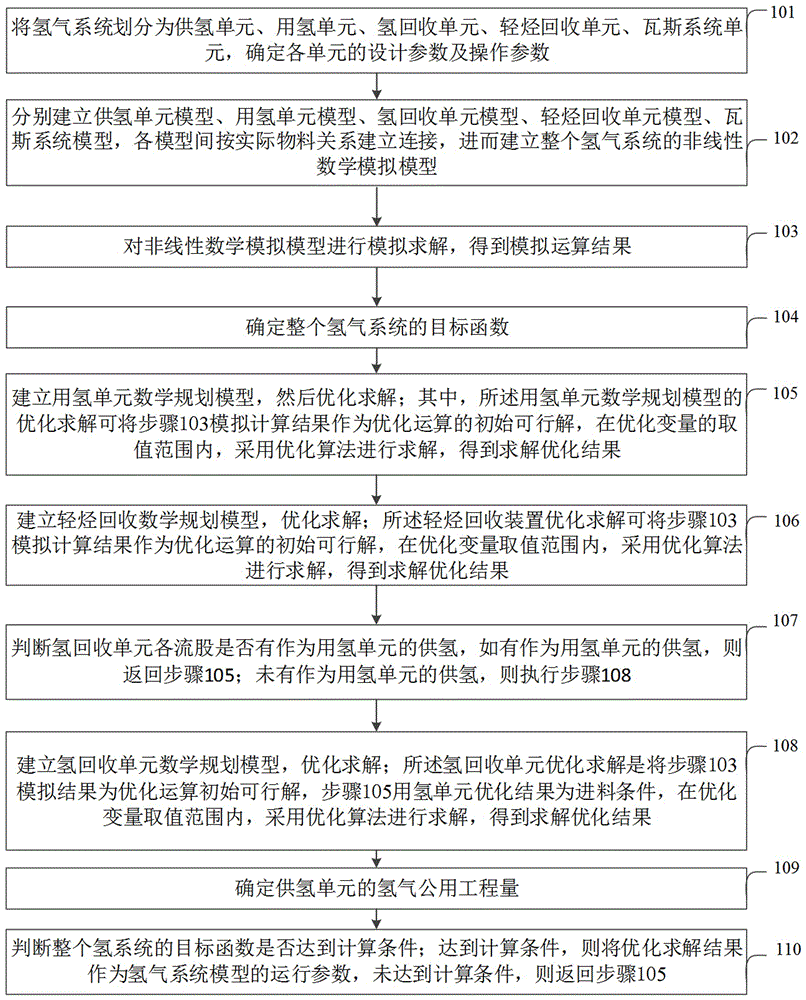
本发明涉及氢气资源优化领域,具体涉及一种炼厂氢气资源的优化方法及系统。
背景技术:
:随着加工原油的重质化、劣质化趋势加剧及产品质量升级要求加强,炼厂对氢气的需求量越来越大,氢气已成为炼油厂原料成本中仅次于原油成本的第二大成本要素。氢气资源优化利用技术是企业实现降本增效的重要手段,已受到企业愈来愈多的重视。目前,氢气资源优化研究主要有夹点分析法及数学规划法,其特点如下:(1)夹点分析法。开展氢气网络夹点分析,首先需得到“氢气体积分数-流股流量”关系的氢源复合曲线及氢阱复合曲线,通过比较氢源复合曲线及氢阱复合曲线在同一氢气纯度下的面积得到氢气剩余曲线图,即为氢气网络的夹点图。氢夹点分析技术优点是简单直观,可以在氢网络设计前得到氢气公用工程量最小需求目标。缺点是夹点分析法仅考虑流股的流量、氢纯度,未考虑压力影响,造成结果是优化的结果可能存在过度优化而无法在实际生产中实施,另一缺点是夹点分析法对于大规模实际问题使用起来比较困难、繁琐;(2)数学规划法。基本原理是将氢气系统优化过程转化成数学建模方程的求解过程,优化目的即为目标函数,根据炼厂实际情况设置约束条件,最后利用易于收敛的求算方法获取目标函数的最优解。优点是处理复杂氢网络优化问题能省却图解法夹点分析的繁琐计算过程。缺点:一是由于氢气系统涉及面广,联立求解方程组较多,因而优化求解的难度较大,此外,诸多设备模型存在非凸非连续的特征,且包含很强的约束条件,造成了优化求解的难度,不容易得到最优解或陷入局域最优解;二是复杂系统下的约束条件不易设定,约束条件增多,计算量增大,优化求解困难,有时难以获得最优解,反之,约束条件减少,优化求解结果的可实施性降低。例如,cn106485341a涉及一种炼油厂氢气系统优化方法。该方法将炼油厂氢气系统收益最大作为目标,对约束条件进行优选,形成了包括轻烃资源优化在内的新的数学规划算法;与现有氢气系统的数学规划算法相比,更切合实际,可获得更大收益以满足炼油厂节氢、增效的需求。缺点:一将整个氢气系统作为优化研究对象,涉及面广,约束限制多,造成优化求解的计算量偏大,有时不易获得系统最优解;二是在优化求解过程中,需要反复调整待优化参数以确保最大收益函数的解趋于最大值,这种在复杂氢气系统中反复试差调整待优化参数的做法必定会降低优化求解的计算效率;三是通过构建数学规划模型,将轻烃回收纳入氢气系统优化研究,进一步扩大了数学模型涵盖范围,增大了优化求解的难度。实际上,氢气系统优化研究最根本问题是氢气的优化研究,氢气优化与轻烃优化之间存在着一种主次且相互影响的关系(如某一含氢流股经过轻烃回收后其氢气相对富集,利于进行氢气回收或直接利用,又如某一含氢流股进行氢气回收后其轻烃相对富集,利于进行轻烃资源回收),因此不能简单地在数学规划建模中将轻烃回收优化与氢气优化进行叠加或求解。因此,如何将现有技术问题加以解决,提供一种新的高效准确的氢气资源优化研究方法,即为本领域技术人员的研究方向所在。技术实现要素:针对现有技术中的缺陷,本发明提供了一种氢气资源的优化方法及系统。本发明方法能够避免复杂系统优化求解常遇到的难收敛、局部最优等问题,可在复杂氢气系统下有效提高氢气系统优化求解的计算效率,获得氢气系统最优解,得到最佳匹配方案,降低炼厂氢耗、提高氢气/轻烃综合回收效益、减少氢公用工程量,解决了氢气、轻烃综合优化造成的数学模型复杂、难收敛等问题。本发明提供了一种氢气资源的优化方法,包括以下步骤:步骤s1:将氢气系统划分为供氢单元、用氢单元、氢回收单元、轻烃回收单元、瓦斯系统单元,确定各单元的设计参数及操作参数;步骤s2:分别建立供氢单元模型、用氢单元模型、氢回收单元模型、轻烃回收单元模型、瓦斯系统模型,各模型间按实际物料关系建立连接,进而建立整个氢气系统的非线性数学模拟模型;步骤s3:对非线性数学模拟模型进行模拟求解,得到模拟运算结果;步骤s4:确定整个氢气系统的目标函数;步骤s5:建立用氢单元数学规划模型,然后优化求解;其中,所述用氢单元数学规划模型的优化求解可将步骤s3模拟计算结果作为优化运算的初始可行解,在优化变量的取值范围内,采用优化算法进行求解,得到求解优化结果;步骤s6:建立轻烃回收数学规划模型,优化求解;所述轻烃回收装置优化求解可将步骤s3模拟计算结果作为优化运算的初始可行解,在优化变量取值范围内,采用优化算法进行求解,得到求解优化结果;步骤s7:判断轻烃回收装置回收轻烃后的贫气及氢回收单元各流股是否有作为用氢单元的供氢,如有作为用氢单元的供氢,则返回步骤s5;没有作为用氢单元的供氢,则执行步骤s8;步骤s8:建立氢回收单元数学规划模型,优化求解;所述氢回收单元优化求解是将步骤s3模拟结果为优化运算初始可行解,步骤s5用氢单元优化结果为进料条件,在优化变量取值范围内,采用优化算法进行求解,得到求解优化结果;步骤s9:确定供氢单元的氢气公用工程量;步骤s10:判断整个氢系统的目标函数是否达到计算条件;达到计算条件,则将优化求解结果作为氢气系统模型的运行参数,未达到计算条件,则返回步骤s5。在所述步骤s1中,所述供氢单元主要涉及水蒸汽裂解制氢、煤制氢、重整副产氢、乙烯装置副产氢、离子膜电解水副产氢中,可以是其中的一类装置或几类装置,所述的供氢单元还可包括焦化装置、催化裂化装置;所述用氢单元包括加氢精制装置、加氢裂化装置中的一种或几种装置;所述氢回收单元包括变压吸附装置、膜分离装置中的一种或几种装置;所述设计参数包括装置的设计数据、催化剂及吸附剂的物化性质;所述操作参数包括装置的操作条件,物料平衡,以及流股的流量、压力、组成。在所述步骤s2中,所述供氢单元模型包括简易供氢模型或详细供氢模型;其中,详细供氢模型包括水蒸汽裂解制氢模型、煤制氢模型,所述详细供氢模型为考虑氢气生产过程中存在的各个反应器的生产工艺过程模型,用于模拟动力学、热效应及催化剂活性,基于变化的进料组成、流量预测产物收率、组成;所述简易供氢模型包括重整副产氢模型及其他供氢装置模型,所述简易供氢模型为仅考虑装置的供氢流量、组成的模型;所述用氢单元模型包括加氢精制处理模型和加氢裂化模型;所述氢回收单元模型包括变压吸附装置模型、膜分离装置模型;所述轻烃回收单元模型包括深冷法轻烃回收装置模型、冷油吸收法轻烃回收装置模型和吸附法轻烃回收装置模型的一种或几种,所述轻烃回收单元模型用于模拟计算轻烃回收量、回收效益、操作成本;所述瓦斯系统模型采用均相管网模型,用于描述氢气系统中部分含氢流股排放至瓦斯管线或直送至燃烧炉的状况。在所述步骤s4中,氢气系统目标目标函数为年总成本最小、总操作成本最少、氢气公用工程量最小或氢气/轻烃综合回收效益最大,优选为氢气/轻烃综合回收效益最大。在所述步骤s5中,在用氢单元数学规划模型进行优化求解时,以新氢流量、循环氢流量为优化变量,以最小化总用氢量为目标函数值,以满足装置最小用氢需求、设备运行的要求为约束条件;所述用氢单元的优化求解采用优化算法进行求解,得到求解优化结果,所述优化算法优选为序列二次规划算法或序贯线性规划算法;所述用氢单元优化求解结果通过物料连接关系传递给下游装置模型。在所述步骤s6中,在轻烃回收数学规划模型进行优化求解时,以步骤s3模拟计算后排放至瓦斯系统的含氢流股为优化变量,以最大化轻烃回收效益为目标函数值,以轻烃回收装置运行负荷、满足燃料气系统总热值最低需求为约束条件;所述轻烃回收装置的优化求解采用优化算法进行求解,得到求解优化结果,所述优化算法优选为序列二次规划算法或序贯线性规划算法。轻烃回收装置的轻烃产品可以是c2乙烯料、液化石油气lpg、轻石脑油中的一种或几种。目标函数:maxflh=∑piflh,i-∑p*cvlh,i-clh其中,flh表示轻烃回收装置回收效益,i表示轻烃回收装置的回收轻烃产品i,pi表示回收轻烃产品i的价格,flh,i表示回收轻烃产品i的流量,p*表示燃料气热值价格,cvlh,i表示回收轻烃产品i的热值,clh表示轻烃回收装置的操作成本,主要涉及压缩机、泵的功耗。约束条件为:轻烃回收装置进出口需满足物料守恒、组分守恒;装置加工负荷受加工能力约束;不能无限制的回收轻烃,需确保轻烃回收后燃料气系统最低总热值需求。式中,rj表示含氢流股rj,表示进入轻烃回收装置的含氢流股rj的流量,表示轻烃回收装置的回收轻烃产品,表示回收轻烃后的贫气,表示含氢流股rj中组分s的含量,表示轻烃回收装置回收轻烃产品中组分s的含量,表示轻烃回收装置回收轻烃后贫气中组分s的含量,表示装置加工能力下限,表示装置加工能力上限,表示回收轻烃产品的热值,表示炼厂弥补因轻烃回收造成瓦斯系统热值损失的最大能力。在所述步骤s7中,含氢流股是否可作为用氢单元新氢的标准为:含氢流股氢纯度大于用氢装置反应器入口氢纯度,ch4体积分数小于ch4设定值,气体杂质含量小于气体杂质设定值,ch4设定值和气体杂质设定值需根据装置工艺要求进行设定。在所述步骤s8中,氢回收单元采用基于协同优化理论的建模方法,将整个氢回收系统作为系统级优化研究对象,从而建立整体系统优化模型;将变压吸附装置、膜分离装置作为氢回收系统下的各子系统优化研究对象,从而建立子系统优化模型;所述系统级优化对象与各子系统通过欲回收的含氢流股相耦合。(a)整体系统优化模型如下:整体系统优化模型的目标函数:式中,f表示氢气回收系统的总回收效益;fi(xi)表示各氢回收装置的回收效益;xi表示模型决策变量;整体系统优化模型的约束条件:氢气回收系统与子系统i等式一致性约束为:…………其中,表示子系统i实际回收处理含氢流股rj的流量,是子系统i传递给系统级的一个常量;表示氢气回收系统中预定的子系统i回收处理含氢流股rj中的流量,是系统级变量,ε表示预设松弛因子,n表示变压吸附单元或膜分离单元中包含的变压吸附装置或膜分离装置的数量;(b)子系统优化模型如下:子系统优化模型的目标函数:其中,表示子系统i实际回收处理含氢流股rj的流量,是子系统i传递给系统级的一个常量;表示氢气回收系统中预定的子系统i回收处理含氢流股rj中的流量,是系统级变量;子系统优化模型的约束条件:式中:、——子系统i的等式不等式约束。在所述步骤s9中,由用氢单元、氢回收单元优化结果经物料衡算确定氢气公用工程量。在所述步骤s10中,所述达到计算条件:若两次目标函数计算相差满足收敛要求,则结束系统计算;若两次目标函数计算相差未达到收敛要求,且迭代次数仍未达到设计上限,则返回步骤s5再进行优化计算;若两次目标函数计算相差未满足收敛要求,但迭代次数达到上限,则停止计算。本发明还提供了一种氢气资源的优化系统,包括以下模块:划分模块、数学模拟模型模块、模拟求解模块、第一确定模块、用氢单元数学规划模型模块、轻烃回收数学规划模型、第一判断模块、氢回收单元数学规划模型模块、第二确定模块和第二判断模块;划分模块,用于将氢气系统划分为供氢单元、用氢单元、氢回收单元、轻烃回收单元、瓦斯系统单元,确定各单元的设计参数及操作参数;数学模拟模型模块,用于分别建立供氢单元模型、用氢单元模型、氢回收单元模型、瓦斯系统模型,各模型间按实际物料关系建立连接,进而建立整个氢系统的非线性的数学模拟模型;模拟求解模块,用于对非线性的数学模拟模型进行模拟求解,得到模拟运算结果;第一确定模块,用于确定整个氢系统的目标函数;用氢单元数学规划模型模块,用于建立用氢单元数学规划模型,然后优化求解;其中,所述用氢单元数学规划模型的优化求解可将模拟求解模块的模拟计算结果作为优化运算的初始可行解,在优化变量的取值范围内,采用优化算法进行求解,得到求解优化结果;轻烃回收数学规划模型,建立轻烃回收数学规划模型,优化求解;所述轻烃回收装置优化求解可将模拟求解模块模拟计算结果作为优化运算的初始可行解,在优化变量取值范围内,采用优化算法进行求解,得到求解优化结果;第一判断模块,判断轻烃回收装置回收轻烃后的贫气及氢回收单元各流股是否有作为用氢单元的供氢,如有作为用氢单元的供氢,则返回用氢单元数学规划模型模块;没有作为用氢单元的供氢,则执行氢回收单元数学规划模型模块;氢回收单元数学规划模型模块,用于建立氢回收单元数学规划模型,优化求解;所述氢回收单元优化求解是将模拟求解模块的模拟结果为优化运算初始可行解,以用氢单元数学规划模型模块的用氢单元优化结果为进料条件,在优化变量取值范围内,采用优化算法进行求解,得到求解优化结果;第二确定模块,用于确定供氢单元的氢气公用工程量;第二判断模块,用于判断整个氢系统的目标函数是否达到计算条件;达到计算条件,则将优化求解结果作为氢气系统模型的运行参数,未达到计算条件,则返回用氢单元数学规划模型模块。在所述划分模块中,所述供氢单元包括水蒸汽裂解制氢、煤制氢、重整副产氢、乙烯装置副产氢、离子膜电解水副产氢、焦化装置、催化裂化装置中的一种或几种装置,所述用氢单元包括加氢精制装置、加氢裂化装置中的一种或几种装置;所述氢回收单元包括变压吸附装置、膜分离装置中的一种或几种装置;所述设计参数包括装置的设计数据、催化剂及吸附剂的物化性质;所述操作参数包括装置的操作条件,物料平衡,以及流股的流量、压力、组成。所述数学模拟模型模块中,所述供氢单元模型包括简易供氢模型或详细供氢模型;其中,详细供氢模型包括水蒸汽裂解制氢模型、煤制氢模型,所述详细供氢模型为考虑氢气生产过程中存在的各个反应器的生产工艺过程模型,用于模拟动力学、热效应及催化剂活性,基于变化的进料组成、流量预测产物收率、组成;所述简易供氢模型包括重整副产氢模型及其他供氢装置模型,所述简易供氢模型为仅考虑装置的供氢流量、组成的模型;所述用氢单元模型包括加氢精制处理模型和加氢裂化模型;所述氢回收单元模型包括变压吸附装置模型、膜分离装置模型;所述轻烃回收单元模型包括深冷法轻烃回收装置模型、冷油吸收法轻烃回收装置模型和吸附法轻烃回收装置模型的一种或几种,所述轻烃回收单元模型用于模拟计算轻烃回收量、回收效益、操作成本;所述瓦斯系统模型采用均相管网模型,用于描述氢气系统中部分含氢流股排放至瓦斯管线或直送至燃烧炉的状况。在所述第一确定模块中,氢气系统的目标目标函数为年总成本最小、总操作成本最少、氢气公用工程量最小或氢气/轻烃综合回收效益最大,优选为氢气/轻烃综合回收效益最大。所述用氢单元数学规划模型模块中,在用氢单元数学规划模型进行优化求解时,以新氢流量、循环氢流量为优化变量,以最小化总用氢量为目标函数值,以满足装置最小用氢需求、设备运行的要求为约束条件;所述用氢单元的优化求解采用优化算法进行求解,得到求解优化结果,所述优化算法优选为序列二次规划算法或序贯线性规划算法;所述用氢单元优化求解结果通过物料连接关系传递给下游装置模型。在所述轻烃回收数学规划模型中,在轻烃回收数学规划模型进行优化求解时,以模拟求解模块模拟计算后排放至瓦斯系统的含氢流股为优化变量,以最大化轻烃回收效益为目标函数值,以轻烃回收装置运行负荷、满足燃料气系统总热值最低需求为约束条件;所述轻烃回收装置的优化求解采用优化算法进行求解,得到求解优化结果,所述优化算法优选为序列二次规划算法或序贯线性规划算法;优化地,目标函数为:maxflh=∑piflh,i-∑p*cvlh,i-clh,其中,flh表示轻烃回收装置回收效益,i表示轻烃回收装置的回收轻烃产品i,pi表示回收轻烃产品i的价格,flh,i表示回收轻烃产品i的流量,p*表示燃料气热值价格,cvlh,i表示回收轻烃产品i的热值,clh表示轻烃回收装置的操作成本,主要涉及压缩机、泵的功耗;优化地,约束条件为:式中,rj表示含氢流股rj,表示进入轻烃回收装置的含氢流股rj的流量,表示轻烃回收装置的回收轻烃产品,表示回收轻烃后的贫气,表示含氢流股rj中组分s的含量,表示轻烃回收装置回收轻烃产品中组分s的含量,表示轻烃回收装置回收轻烃后贫气中组分s的含量,表示装置加工能力下限,表示装置加工能力上限,表示回收轻烃产品的热值,表示炼厂弥补因轻烃回收造成瓦斯系统热值损失的最大能力。所述第一判断模块中,含氢流股是否可作为用氢单元新氢的标准为:含氢流股氢纯度大于用氢装置反应器入口氢纯度,ch4体积分数小于ch4设定值,气体杂质含量小于气体杂质设定值,ch4设定值和气体杂质设定值需根据装置工艺要求进行设定。所述氢回收单元数学规划模型模块中,氢回收单元采用基于协同优化理论的建模方法,将整个氢回收系统作为系统级优化研究对象,从而建立整体系统优化模型;将变压吸附装置、膜分离装置作为氢回收系统下的各子系统优化研究对象,从而建立子系统优化模型;所述系统级优化对象与各子系统通过欲回收的含氢流股相耦合;优先地,整体系统优化模型如下:整体系统优化模型的目标函数:式中,f表示氢气回收系统的总回收效益;fi(xi)表示各氢回收装置的回收效益;xi表示模型决策变量;整体系统优化模型的约束条件:氢气回收系统与子系统i等式一致性约束为:…………其中,表示子系统i实际回收处理含氢流股rj的流量,是子系统i传递给系统级的一个常量;表示氢气回收系统中预定的子系统i回收处理含氢流股rj中的流量,是系统级变量,ε表示预设松弛因子,n表示变压吸附单元或膜分离单元中包含的变压吸附装置或膜分离装置的数量;优先地,子系统优化模型如下:子系统优化模型的目标函数:其中,表示子系统i实际回收处理含氢流股rj的流量,是子系统i传递给系统级的一个常量;表示氢气回收系统中预定的子系统i回收处理含氢流股rj中的流量,是系统级变量;子系统优化模型的约束条件:式中:、——子系统i的等式不等式约束。所述第二确定模块中,由用氢单元、氢回收单元优化结果经物料衡算确定氢气公用工程量。第二判断模块,所述达到计算条件:若两次目标函数计算相差满足收敛要求,则结束系统计算;若两次目标函数计算相差未达到收敛要求,且迭代次数仍未达到设计上限,则返回用氢单元数学规划模型模块再进行优化计算;若两次目标函数计算相差未满足收敛要求,但迭代次数达到上限,则停止计算。与现有技术相比,本发明的氢气资源的优化方法及系统具有如下优点:(1)本发明的氢气资源的优化方法,先建立整个氢系统的非线性的数学模拟模型、确定整个氢系统目标函数,将整个氢气系统的数学规划模型的求解问题,简化为具有序贯连接关系的各子单元优化求解,然后在各子单元优化求解过程中与整个氢系统非线性的数学模拟模型建立联系,从而不再简单地将整个氢气系统作为优化研究对象,而是充分研究考虑了氢气系统内部单元的逻辑关联,将整个氢气系统的优化研究问题简化为耗氢单元、氢回收单元、供氢单元各子系统的优化研究,避免了复杂系统优化求解常遇到的难收敛、局部最优等问题,可在复杂氢气系统下有效提高氢气系统优化求解的计算效率,获得氢气系统最优解,得到最佳匹配方案、操作方案,显著降低炼厂氢耗、提高氢气回收效率、减少氢公用工程量,进而提高企业经济效益,提升企业综合实力。(2)本发明在氢气优化研究基础上将轻烃回收纳入氢气系统优化研究,并非简单的将轻烃回收优化与氢气优化交给数学规划建模求解,而是充分考虑了轻烃回收与氢气系统优化、瓦斯系统平衡的关联耦合,建立了供氢、耗氢、轻烃回收、氢回收等序贯连接关系的数学模型,进一步扩大了氢气系统优化数学模型涵盖范围,解决了氢气、轻烃综合优化造成的数学模型复杂、难收敛等问题。(3)本发明从系统角度出发,考虑了供氢、耗氢、氢回收、轻烃回收单元间及各单元内部装置间的协同优化,充分发挥了整个氢气系统优化节氢的潜力,可有效提高氢气系统的操作水平,最小化装置用氢,最大化氢回收,提高氢气/轻烃综合回收效益。附图说明为了更清楚地说明本发明实施例或现有技术中的技术方案,下面将对实施例或现有技术描述中所需要使用的附图作简单地介绍,显而易见地,下面描述中的附图是本发明的一些实施例,对于本领域技术人员来讲,在不付出创造性劳动的前提下,还可以根据这些附图获得其他的附图。图1是本发明一实施例提供的炼厂氢气资源的优化方法的流程图;图2为一炼厂氢气系统的氢气管网的示意图;图3为蒸汽裂解制氢装置模型结构的示意图;图4为炼厂氢系统在优化后氢气管网的示意图;图5是本发明另一实施例提供的炼厂氢气资源的优化系统的示意图。具体实施方式为使本发明实施例的目的、技术方案和优点更加清楚,下面将结合本发明实施例中的附图,对本发明实施例中的技术方案进行清楚、完整的描述,显然,所描述的实施例是本发明一部分实施例,而不是全部的实施例。基于本发明中的实施例,本领域技术人员在没有作出创造性劳动前提下所获得的所有其他实施例,都属于本发明保护的范围。本发明一实施例提供了一种炼厂氢气资源的优化方法,参见图1所示的流程图,该方法包括以下步骤:步骤101:将氢气系统划分为供氢单元、用氢单元、氢回收单元、轻烃回收单元、瓦斯系统单元,确定各单元的设计参数及操作参数。在本步骤中,供氢单元主要涉及水蒸汽裂解制氢、煤制氢、重整副产氢、乙烯装置副产氢、离子膜电解水副产氢,可以是其中的一类装置或几类装置。供氢单元还可包括焦化装置、催化装置。用氢单元主要涉及汽油加氢、航煤加氢、柴油加氢、蜡油加氢、渣油加氢、润滑油加氢等各类炼油加氢精制装置及加氢裂化装置,可以是其中的一类装置或几类装置。氢回收单元主要涉及变压吸附装置、膜分离装置,可以是其中一类装置或几类装置。氢回收装置还包括与上述氢回收装置相关联的轻烃回收装置、脱硫装置。设计参数主要涉及装置的基础设计数据、催化剂及吸附剂的基础物化性质。操作参数主要涉及装置的操作条件、物料平衡及流股的流量、压力、组成。例如,图2为一炼厂氢气系统示意图,表1为炼厂氢气系统划分的三单元装置构成,表2为部分装置设计参数及操作参数汇总。表1氢气系统三单元装置构成项目装置供氢单元1#天然气制氢装置、2#天然气制氢装置、连续重整装置、外购高纯氢、延迟焦化、催化裂化用氢单元1#、2#柴油加氢装置、航煤加氢装置、szorb装置、加氢裂化装置、蜡油加氢装置氢回收单元1#制氢装置psa、2#制氢装置psa、连续重整氢psa、轻烃回收装置表2部分装置设计参数及操作参数汇总蜡油加氢加氢裂化2#柴油加氢1#柴油加氢航煤加氢szorb氢油比≥500≥700≥500≥450约45mol≥0.26氢分压,mpa≥8≥12.0(循环氢纯度≥80%)≥6.4入口压力7.0入口压力2.00.61反应器设计/操作压力,mpa12/11.015.7/14.09.3/98.0/7.12.3/2.02.38/2.7新氢压缩机入/出口压力,mpa2→122→15.72→9.32→7.21.4→2.31.8→3.5新氢压缩机设计/最大气量,nm3/h34000/4000038500/4500027835/3300010000/150001500/100003500/8000新氢压缩机类型容积式往复式往复式往复式往复式往复式循环氢入/出口压力,mpa9.5→1213.3→15.37.1→9.16.59→7.83-2.2→3.5压缩机设计/最大气量,nm3/h200000/250000370000/480000207000/25000040000/50000--压缩机类型离心式离心式离心式离心式--热高分设计/操作温度,℃-280/225280/220280/230/129热高分设计/操作压力,mpa-15/138.8/8.16.8/6.5-/2.72热低设计/操作温度,℃-300/240280/220280/225--热低分设计/操作压力,mpa-3.3/2.73.0/2.42.5/2.2--冷高分设计/操作温度,℃140/49150/55150/50150/50150/45-冷高分设计/操作压力,mpa11.5/9.514.9/138.65/7.456.8/6.32.5/1.95-冷低分设计/操作温度,℃100/51170/40150/50150/50150/40-冷低分设计/操作压力,mpa2.5/23.2/2.63/2.43/2.22.5/1.7-注:szorb的氢油比按摩尔氢油比,其它均按体积氢油比。步骤102:分别建立供氢单元模型、用氢单元模型、氢回收单元模型、轻烃回收单元模型、瓦斯系统模型,各模型间按实际物料关系建立连接,进而建立整个氢气系统的非线性数学模拟模型。(1)供氢单元模型在步骤102中,供氢单元模型包括简易供氢模型或详细供氢模型;其中,详细供氢模型包括水蒸汽裂解制氢模型、煤制氢模型,详细供氢模型为考虑氢气生产过程中存在的各个反应器的生产工艺过程模型,用于模拟动力学、热效应及催化剂活性,基于变化的进料组成、流量预测产物收率、组成。简易供氢模型包括重整副产氢模型、蒸汽裂解制氢装置模型及其他供氢装置模型,简易供氢模型为仅考虑装置的供氢流量、组成的模型,不涉及产氢工艺过程的模拟。蒸汽裂解制氢装置模型结构示意如图3所示,转化炉管内反应可描述如下:上述反应对应的动力学方程分别为:式中:、、表示反应速率;、、表示反应动力学速率常数;、、表示平衡常数。中温变换反应器中反应可如下描述:(2)用氢单元模型用氢单元模型为严格反应动力学模型,精确描述原料经反应器后的油品质量变化及轻端组分变化过程。油品质量主要通过油品馏程数据、相对密度表示。轻端组分包括h2、nh3、h2s、n2、o2、h2o、co、co2、c1~c5轻烃等。用氢单元模型能模拟当前工况下的生产状况,也能预测反应器进料性质变化或工艺条件变化后的产物分布情况。工艺条件主要涉及反应器温度、压力、氢油比及高低压分离器的温度、压力。用氢单元模型仅涉及新氢压缩机、反应器、高低压分离器、循环氢压缩机模拟计算,不涉及后续分离工艺装置的核算。反应器入口进料形式为新氢、循环氢、原料油混合物,进料性质主要涉及气相物料的组成、流量、杂质含量及原料油性质。反应器出口为转化后的生成油与轻端组分的混合物,经高低压分离器分离成循环氢、低分气、干气及液相油品。用氢单元模型可以包括加氢精制处理模型和加氢裂化模型。其中,加氢精制处理模型主要涉及汽油加氢、航煤加氢等各类别加氢精制处理装置模型,加氢精制处理模型要呈现以下几种转化反应,包括加氢脱硫反应、加氢脱氮反应、加氢脱氧反应、烯烃加氢饱和反应及芳烃加氢饱和反应。加氢裂化模型主要涉及各类别加氢裂化装置模型,加氢裂化模型要呈现以下几种转化反应,包括加氢脱硫反应、加氢脱氮反应、烃类裂化反应。下面以加氢精制处理模型、加氢裂化模型为例进行详细阐述:对于加氢精制处理模型,以测定给定加氢处理反应器给定反应机理i的反应动力学公式可表示如下:式中:表示反应机理i下的反应速率;-j个反应动力学模型混合;表示速率常数;表示反应氢分压;、表示相应指数;表示组分浓度。用以上方程式分别对加氢脱硫反应、加氢脱氮反应、加氢脱氧反应、烯烃加氢饱和反应及芳烃加氢饱和反应求解,对各反应氢耗速率求和,即可求得该装置总化学氢耗速率。对于加氢裂化装置模型,除必须考虑上述的脱硫、脱氮等反应外,还必须考虑烃类裂化消耗的氢。模型将反应器进出口油品按每15℃划分虚拟组分,采用下述反应动力学模型测定其相应参数,进而建立加氢裂化装置的反应动力学模型。式中:表示虚拟组分i反应速率;表示校正参数;表示速率常数;、表示相应指数;表示反应氢分压;表示虚拟组分i浓度。对于轻烃组分的预测,可采用下式计算,式中:表示轻端产率;表示产物中h2s分压;表示相关系数。轻烃组分分布如表3所示。表3用氢装置反应产生轻烃组成分布组成摩尔分率ch4x1c2h6x2c2h4x3c3h8x4c3h6x5c4h10x6c4h8x7c5h12x8c5h10x9∑1.0(3)氢回收单元模型氢回收单元模型分为变压吸附装置模型、膜分离装置模型。本发明方法中,变压吸附装置模型要能够模拟当前工况下的分离状况,还要能预测进料流量、组成变化后的吸附分离情况。本发明方法中,在变压吸附装置模型中,从吸附床底至顶,按装填吸附剂类别不同划分不同的微元段,假设压力及温度恒定不变,流动模型采用轴向分散活塞流模型,由总物质平衡计算吸附引起的流速变化,传质速率方程采用线性推动力模型(ldf),吸附平衡方程采用扩展的兰格缪尔模型描述。变压吸附装置数学模型如下:微元体积中气体组分i的传质平衡方程为:其中,dl表示床层轴向扩散系数;ci表示组分i气相总浓度;表示气流速度;ρp表示吸附压力p下气相密度;ε表示分子吸附床孔隙率;表示组分i吸附平衡浓度,z表示微元段轴向距离;t表示时间;总传质平衡方程为:其中,dl表示床层轴向扩散系数;c表示床层气相浓度;ρp表示吸附压力p下气相密度,ci表示组分i气相总浓度;v表示气流速度;表示组分i吸附平衡浓度;ε表示分子吸附床孔隙率;z表示微元段轴向距离,t表示时间;传质速率方程:其中,表示气固传质系数;表示组分i吸附床气相浓度;表示组分i吸附平衡浓度;吸附平衡方程为:;其中,θi表示待吸附的混合气体中,某层吸附剂上气体组分i的覆盖率;pi表示待吸附的混合气体中,气体组分i的分压;bi表示气体组分i在该层吸附剂上的兰格缪尔吸附常数;qi表示i组分的吸附量,qmax,i表示混合气分中i组分的最大吸附量。本发明方法中,膜分离装置模型要能够模拟当前工况下的分离状况,还要能预测进料流量、组成变化后的吸附分离情况。本发明方法中,在膜分离装置模型中,忽略膜两侧流体的流动阻力,假设原料侧气体组成呈线性变化,渗透侧为全混合形式,组分i气体渗透量的数学模型如下:式中:——组分i渗透气量;——渗透系数;——膜面积;——原料侧膜表面压力;——原料气中组分i的浓度;——渗余气中组分i的浓度;——渗透气压力;——渗透气中组分i的浓度。(4)轻烃回收单元模型本发明方法中,轻烃回收单元模型还可以采用固定特定组分回收率的方法进行简化处理,回收率可通过实际轻烃回收装置运行数据进行拟合求得,也可通过常规流程模拟软件进行建模计算求得,如aspenplus、proii等,还可以人为根据经验设定。轻烃回收单元模型的主要用途用于模拟计算轻烃回收量、回收效益、操作成本。本发明方法中,脱硫装置模型可以采用固定脱硫率、脱co2率的方法进行简化处理,脱硫率、脱co2率由人为设定。瓦斯系统模型采用均相管网模型,用于描述氢气系统中部分含氢流股排放至瓦斯管线或直送至燃烧炉的状况。本发明方法中,氢气系统模型由上述建立的供氢单元模型、用氢单元模型、氢回收单元模型及瓦斯系统模型,依据实际物流关系,采用物料连接线连接而成。物料连接线仅代表两物理装置物料的连接关系,优选的,可根据需要能进行管线压降、流速的计算。步骤103:对非线性的数学模拟模型进行模拟求解,得到模拟运算结果。步骤104:确定整个氢系统的目标函数。本发明方法中,步骤104中氢气系统目标函数为年总成本最小、总操作成本最少、氢气公用工程量最小或氢气/轻烃综合回收效益最大,优选的为氢气/轻烃综合回收效益最大优化目标函数。其中,年总成本=设备年均投资费用+设备操作费用+外购成本+公用工程消耗-外卖收益-燃料价值。总操作成本=∑fi×pi,即总操作成本等于流入设备的气体总量×单位气体流量的操作费用。氢气公用工程量指水蒸汽裂解制氢及煤制氢的量。氢气/轻烃综合回收效益=氢公用工程减少带来的效益+轻烃回收效益。优选的目标函数:maxf=fh2+flh式中,f表示氢气系统氢气/轻烃综合回收效益,fh2表示氢气系统氢公用工程减少带来的效益,flh表示轻烃回收带来的效益。氢气系统优化研究本质是氢气综合利用的优化,因此以氢气/轻烃综合回收效益最大为目标函数进行的系统优化,需在氢气综合利用最优基础上,再进行轻烃回收优化。步骤105:建立用氢单元数学规划模型,然后优化求解;其中,所述用氢单元数学规划模型的优化求解可将步骤103模拟计算结果作为优化运算的初始可行解,在优化变量的取值范围内,采用优化算法进行求解,得到求解优化结果。在步骤105中,用氢单元优化求解采用序列二次规划算法、序贯线性规划算法。用氢单元优化求解结果通过物料连接关系传递给下游装置模型。在步骤105中,用氢单元数学优化模型的目标函数可以为总用氢最小,调节参数为新氢流量、循环氢流量(即氢分压、氢油比)参数,约束条件为满足装置最小用氢需求(最小氢油比、氢分压、装置耗氢)、关键设备运行要求。例如,用氢装置优化需满足:反应器入口氢分压不小于工艺要求值,氢油比不小于工艺要求值,新氢中纯氢补给量不小于装置化学氢耗,循环氢氢纯度不小于工艺要求值,反应器进口需满足物料平衡。式中:表示未反应器入口氢纯度;表示反应器入口压力;表示工艺要求或许可的反应器入口最小氢分压;表示反应器入口氢气体积;表示反应器入口液相油品体积;表示工艺要求或许可的反应器入口最小氢油比;表示补充氢流量;表示补充氢纯度;表示装置化学氢耗;表示循环氢流量;表示循环氢纯度;表示工艺要求或许可的循环氢最小氢纯度;表示反应器入口总量;表示反应器出口总量。步骤s106:建立轻烃回收数学规划模型,优化求解;所述轻烃回收装置优化求解可将步骤s3模拟计算结果作为优化运算的初始可行解,在优化变量取值范围内,采用优化算法进行求解,得到求解优化结果;步骤s106中,在轻烃回收数学规划模型进行优化求解时,以步骤s3模拟计算后排放至瓦斯系统的含氢流股为优化变量,以最大化轻烃回收效益为目标函数值,以轻烃回收装置运行负荷、满足燃料气系统总热值最低需求为约束条件;所述轻烃回收装置的优化求解采用优化算法进行求解,得到求解优化结果,所述优化算法优选为序列二次规划算法或序贯线性规划算法。轻烃回收装置的轻烃产品可以是c2乙烯料、液化石油气lpg、轻石脑油中的一种或几种。目标函数:maxflh=∑piflh,i-∑p*cvlh,i-clh其中,flh表示轻烃回收装置回收效益,i表示轻烃回收装置的回收轻烃产品i,pi表示回收轻烃产品i的价格,flh,i表示与基础研究工况相比多回收轻烃产品i的流量,p*表示燃料气热值价格,cvlh,i表示回收轻烃产品i的热值,clh表示轻烃回收装置增加的操作成本,主要涉及压缩机、泵的功耗。约束条件为:轻烃回收装置进出口需满足物料守恒、组分守恒;装置加工负荷受加工能力约束;不能无限制的回收轻烃,需确保轻烃回收后燃料气系统最低总热值需求。具体公式如下:式中,rj表示含氢流股rj,表示进入轻烃回收装置的含氢流股rj的流量,表示轻烃回收装置的回收轻烃产品,表示回收轻烃后的贫气,表示含氢流股rj中组分s的含量,表示轻烃回收装置回收轻烃产品中组分s的含量,表示轻烃回收装置回收轻烃后贫气中组分s的含量,表示装置加工能力下限,表示装置加工能力上限,表示回收轻烃产品的热值,表示炼厂弥补因轻烃回收造成瓦斯系统热值损失的最大能力。步骤107:判断氢回收单元各流股是否有作为用氢单元的供氢,如有作为用氢单元的供氢,则返回步骤105;没有作为用氢单元的供氢,则执行步骤108;在步骤107中,含氢流股是否可作为用氢单元新氢的标准如下:含氢流股氢纯度大于某用氢装置反应器入口氢纯度,ch4体积分数小于某一设定值,杂质含量(co、o2、n2等)小于某一设定值,上述的设定值需根据装置工艺要求进行设定。例如用氢单元新氢的标准可设定如下:若含氢流股氢纯度大于88.0%,ch4体积分数小于4%,杂质含量(co、o2、n2等)小于50ppm,可将该流股送至对氢气质量要求不太高的用氢装置,如汽油加氢、航煤加氢、szorb等装置;若含氢流股氢纯度>93%,ch4体积分数小于2%,杂质含量(co、o2、n2等)小于50ppm,除可将该流股上述装置外,还可送至柴油加氢、蜡油加氢及部分加氢裂化装置。步骤108:建立氢回收单元数学规划模型,优化求解;氢回收单元优化求解是将步骤103模拟结果为优化运算初始可行解,步骤105用氢单元优化结果为进料条件,在优化变量取值范围内,采用优化算法进行求解,得到求解优化结果。在步骤108中,对于氢回收单元数学规划模型的建立,采用基于协同优化理论的建模方法,将整个氢回收系统作为系统级优化研究对象,将变压吸附装置、膜分离装置作为氢回收系统下的各子系统优化研究对象;系统级优化对象与各子系统通过欲回收的含氢流股相耦合。本发明方法中,系统级优化求解、子系统优化求解采用常规的优化算法,可以是遗传算法、多目标优化求解法、既约梯度法等。(a)整个氢回收系统级优化模型对于整个氢回收系统,目标函数为最大化氢气回收,约束条件为各子系统优化目标函数,整体系统优化模型的目标函数:式中,表示氢气回收系统的总回收效益;表示各氢回收装置的回收效益;表示模型决策变量;整体系统优化模型的约束条件:氢气回收系统与子系统i等式一致性约束为:…………其中,表示子系统i实际回收处理含氢流股rj的流量,是子系统i传递给系统级的一个常量;表示氢气回收系统中预定的子系统i回收处理含氢流股rj中的流量,是系统级变量,ε表示预设松弛因子。可以理解的是,这里的子系统i表示变压吸附单元或膜分离单元。n表示变压吸附单元或膜分离单元中包含的变压吸附装置或膜分离装置的数量。(b)子系统优化模型本发明方法中,子系统为各变压吸附装置、膜分离装置,子系统优化目标函数为各装置子系统变量与系统级变量偏差最小,约束条件为各系统的相应的等式及不等式约束,子系统i的优化模型如下:子系统优化模型的目标函数:其中,表示子系统i实际回收处理含氢流股rj的流量,是子系统i传递给系统级的一个常量;表示氢气回收系统中预定的子系统i回收处理含氢流股rj中的流量,是系统级变量。子系统优化模型的约束条件:式中:、为子系统i的等式不等式约束。步骤109:确定供氢单元的氢气公用工程量;在步骤109中,须由用氢单元、氢回收单元优化结果经物料衡算确定氢气公用工程量。例如,供氢单元氢气公用工程量可以通过下述关系式确定:氢公用工程=用氢装置用氢+排放至瓦斯系统的氢-副产氢-回收氢在确定氢公用工程量基础上,计算氢气优化带来的经济效益,如下:fh2=ph2f氢公用工程减少量-∑p*cvh2-ch2式中,fh2表示氢气系统氢公用工程减少带来的效益,表示氢公用工程价格,表示与基础研究工况相比系统减少的氢公用工程用量,表示燃料气热值价格,表示氢气优化带来的燃料气热值损失,表示氢气优化带来的增加操作成本步骤110:判断整个氢系统的目标函数是否达到计算条件;达到计算条件,则将优化求解结果作为氢气系统模型的运行参数,未达到计算条件,则返回步骤105。本发明方法中,步骤110达到计算条件主要涉及判断目标函数计算是否收敛及迭代次数是否达到上限:若两次目标函数计算相差满足一定要求,则结束系统计算;若两次目标函数计算相差未达到设计要求,且迭代次数仍未达到设计上限,则返回步骤105再进行优化计算;若两次目标函数计算相差满足一定要求,但迭代次数达到上限,则停止计算。系统级迭代最大次数优选为5~50。图4为炼厂氢系统在优化后氢气管网的示意图,表4为优化前后氢回收系统整体性能对比。从结果可看出,优化后系统多回收氢气6425nm3/h,进而减少制氢装置制氢6425nm3/h,减少了能源消耗及co2排放,具有显著的经济效益。表4优化前后氢回收系统整体性能对比优化前优化后氢气总供纯氢,nm3/h8298775970装置总用氢,nm3/h6313862546排放至瓦斯系统的纯氢,nm3/h1984913424psa回收氢气,nm3/h-6425系统氢气利用率,%76.0882.33轻烃轻烃装置多回收轻烃,t/h-0.8氢气/轻烃综合回收效益增加,元/h-10510如图5所示,本发明还提供了一种氢气资源的优化系统,包括以下模块:划分模块21、数学模拟模型模块22、模拟求解模块23、第一确定模块24、用氢单元数学规划模型模块25、轻烃回收数学规划模型26、第一判断模块27、氢回收单元数学规划模型模块28、第二确定模块29和第二判断模块30;划分模块21,用于将氢气系统划分为供氢单元、用氢单元、氢回收单元、轻烃回收单元、瓦斯系统单元,确定各单元的设计参数及操作参数;数学模拟模型模块22,用于分别建立供氢单元模型、用氢单元模型、氢回收单元模型、瓦斯系统模型,各模型间按实际物料关系建立连接,进而建立整个氢系统的非线性的数学模拟模型;模拟求解模块23,用于对非线性的数学模拟模型进行模拟求解,得到模拟运算结果;第一确定模块24,用于确定整个氢系统的目标函数;用氢单元数学规划模型模块25,用于建立用氢单元数学规划模型,然后优化求解;其中,所述用氢单元数学规划模型的优化求解可将模拟求解模块23的模拟计算结果作为优化运算的初始可行解,在优化变量的取值范围内,采用优化算法进行求解,得到求解优化结果;轻烃回收数学规划模型26,用于建立轻烃回收数学规划模型,优化求解;所述轻烃回收装置优化求解可将模拟求解模块23模拟计算结果作为优化运算的初始可行解,在优化变量取值范围内,采用优化算法进行求解,得到求解优化结果;第一判断模块27,用于判断轻烃回收装置回收轻烃后的贫气及氢回收单元各流股是否有作为用氢单元的供氢,如有作为用氢单元的供氢,则返回用氢单元数学规划模型模块25;没有作为用氢单元的供氢,则执行氢回收单元数学规划模型模块28;氢回收单元数学规划模型模块28,用于建立氢回收单元数学规划模型,优化求解;所述氢回收单元优化求解是将模拟求解模块23的模拟结果为优化运算初始可行解,以用氢单元数学规划模型模块25的用氢单元优化结果为进料条件,在优化变量取值范围内,采用优化算法进行求解,得到求解优化结果;第二确定模块29,用于确定供氢单元的氢气公用工程量;第二判断模块30,用于判断整个氢系统的目标函数是否达到计算条件;达到计算条件,则将优化求解结果作为氢气系统模型的运行参数,未达到计算条件,则返回用氢单元数学规划模型模块25。在所述划分模块21中,所述供氢单元包括水蒸汽裂解制氢、煤制氢、重整副产氢、乙烯装置副产氢、离子膜电解水副产氢、焦化装置、催化裂化装置中的一种或几种装置,所述用氢单元包括加氢精制装置、加氢裂化装置中的一种或几种装置;所述氢回收单元包括变压吸附装置、膜分离装置中的一种或几种装置;所述设计参数包括装置的设计数据、催化剂及吸附剂的物化性质;所述操作参数包括装置的操作条件,物料平衡,以及流股的流量、压力、组成。所述数学模拟模型模块22中,所述供氢单元模型包括简易供氢模型或详细供氢模型;其中,详细供氢模型包括水蒸汽裂解制氢模型、煤制氢模型,所述详细供氢模型为考虑氢气生产过程中存在的各个反应器的生产工艺过程模型,用于模拟动力学、热效应及催化剂活性,基于变化的进料组成、流量预测产物收率、组成;所述简易供氢模型包括重整副产氢模型及其他供氢装置模型,所述简易供氢模型为仅考虑装置的供氢流量、组成的模型;所述用氢单元模型包括加氢精制处理模型和加氢裂化模型;所述氢回收单元模型包括变压吸附装置模型、膜分离装置模型;所述轻烃回收单元模型包括深冷法轻烃回收装置模型、冷油吸收法轻烃回收装置模型和吸附法轻烃回收装置模型的一种或几种,所述轻烃回收单元模型用于模拟计算轻烃回收量、回收效益、操作成本;所述瓦斯系统模型采用均相管网模型,用于描述氢气系统中部分含氢流股排放至瓦斯管线或直送至燃烧炉的状况。在所述第一确定模块24中,氢气系统的目标目标函数为年总成本最小、总操作成本最少或氢气公用工程量最小或氢气/轻烃综合回收效益最大,优选为氢气/轻烃综合回收效益最大。所述用氢单元数学规划模型模块25中,在用氢单元数学规划模型进行优化求解时,以新氢流量、循环氢流量为优化变量,以最小化总用氢量为目标函数值,以满足装置最小用氢需求、设备运行的要求为约束条件;所述用氢单元的优化求解采用优化算法进行求解,得到求解优化结果,所述优化算法优选为序列二次规划算法或序贯线性规划算法;所述用氢单元优化求解结果通过物料连接关系传递给下游装置模型。在所述轻烃回收数学规划模型26中,在轻烃回收数学规划模型26进行优化求解时,以模拟求解模块23模拟计算后排放至瓦斯系统的含氢流股为优化变量,以最大化轻烃回收效益为目标函数值,以轻烃回收装置运行负荷、满足燃料气系统总热值最低需求为约束条件;所述轻烃回收装置的优化求解采用优化算法进行求解,得到求解优化结果,所述优化算法优选为序列二次规划算法或序贯线性规划算法;优化地,目标函数为:maxflh=∑piflh,i-∑p*cvlh,i-clh,其中,flh表示轻烃回收装置回收效益,i表示轻烃回收装置的回收轻烃产品i,pi表示回收轻烃产品i的价格,flh,i表示回收轻烃产品i的流量,p*表示燃料气热值价格,cvlh,i表示回收轻烃产品i的热值,clh表示轻烃回收装置的操作成本,主要涉及压缩机、泵的功耗;优化地,约束条件为:式中,rj表示含氢流股rj,表示进入轻烃回收装置的含氢流股rj的流量,表示轻烃回收装置的回收轻烃产品,表示回收轻烃后的贫气,表示含氢流股rj中组分s的含量,表示轻烃回收装置回收轻烃产品中组分s的含量,表示轻烃回收装置回收轻烃后贫气中组分s的含量,表示装置加工能力下限,表示装置加工能力上限,表示回收轻烃产品的热值,表示炼厂弥补因轻烃回收造成瓦斯系统热值损失的最大能力。所述第一判断模块27中,含氢流股是否可作为用氢单元新氢的标准为:含氢流股氢纯度大于用氢装置反应器入口氢纯度,ch4体积分数小于ch4设定值,气体杂质含量小于气体杂质设定值,ch4设定值和气体杂质设定值需根据装置工艺要求进行设定。所述氢回收单元数学规划模型模块28中,氢回收单元采用基于协同优化理论的建模方法,将整个氢回收系统作为系统级优化研究对象,从而建立整体系统优化模型;将变压吸附装置、膜分离装置作为氢回收系统下的各子系统优化研究对象,从而建立子系统优化模型;所述系统级优化对象与各子系统通过欲回收的含氢流股相耦合;优先地,整体系统优化模型如下:整体系统优化模型的目标函数:式中,f表示氢气回收系统的总回收效益;fi(xi)表示各氢回收装置的回收效益;xi表示模型决策变量;整体系统优化模型的约束条件:氢气回收系统与子系统i等式一致性约束为:…………其中,表示子系统i实际回收处理含氢流股rj的流量,是子系统i传递给系统级的一个常量;表示氢气回收系统中预定的子系统i回收处理含氢流股rj中的流量,是系统级变量,ε表示预设松弛因子,n表示变压吸附单元或膜分离单元中包含的变压吸附装置或膜分离装置的数量;优先地,子系统优化模型如下:子系统优化模型的目标函数:其中,表示子系统i实际回收处理含氢流股rj的流量,是子系统i传递给系统级的一个常量;表示氢气回收系统中预定的子系统i回收处理含氢流股rj中的流量,是系统级变量;子系统优化模型的约束条件:式中:、——子系统i的等式不等式约束。所述第二确定模块29中,由用氢单元、氢回收单元优化结果经物料衡算确定氢气公用工程量。第二判断模块30,所述达到计算条件:若两次目标函数计算相差满足收敛要求,则结束系统计算;若两次目标函数计算相差未达到收敛要求,且迭代次数仍未达到设计上限,则返回用氢单元数学规划模型模块25再进行优化计算;若两次目标函数计算相差未满足收敛要求,但迭代次数达到上限,则停止计算。需要说明的是,在上述具体实施方式中所描述的各个具体技术特征,可以通过任何合适的方式进行任意组合,其同样落入本发明所公开的范围之内。另外,本发明的各种不同的实施方式之间也可以进行任意组合,只要其不违背本发明的思想,其同样应当视为本发明所公开的内容。以上结合附图详细描述了本发明的优选实施方式,但是,本发明并不限于上述实施方式中的具体细节,在本发明的技术构思范围内,可以对本发明的技术方案进行多种简单变型,这些简单变型均属于本发明的保护范围。当前第1页12