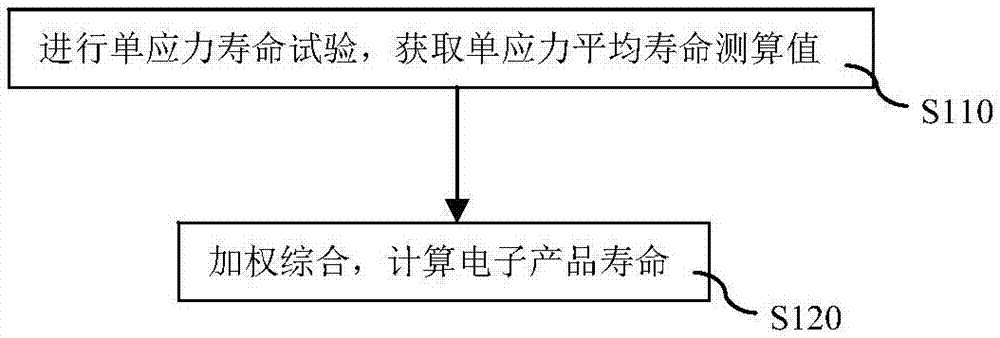
本发明涉及电子
技术领域:
,具体涉及一种电子产品寿命测算方法。
背景技术:
:随着电子技术的不断发展,越来越多的电子产品被应用于人类的日常生产生活中。一般的,电子产品会随着不断使用而老化损坏。随着电子产品的应用范围不断拓宽,一个系统中,单一电子产品的损坏往往会造成一系列的连锁反应。因此,为了维持整个系统的稳定,需要及时监测电子产品的损坏状况并予以更换。然而,即时监测的方式需要消耗大量的资源,并且即时监测也只能在电子产品损坏时才能发现问题并更换,此时,电子产品损坏所造成的连锁反应往往已经发生。因此,在现有技术中,会预先对电子产品的寿命进行测算,以便用户在电子产品寿命到期前及时安排更换操作,从而大大降低电子产品因老化损坏带来的损失。在现有技术中,通常采用在试验环境下模拟电子产品实际的服役环境来测算电子产品的寿命。但是,电子产品在服役过程中通常会经受温度、湿度、振动等多种环境应力的影响,为了更加模拟电子产品实际的服役环境,试验的实施过程中通常会尽量多地覆盖产品实际的环境应力。但是,随着需要模拟的环境应力种类的增多,试验的硬件需求也会增加,试验所需的时间以及工作量也会增加。因此,在实际操作中,试验环境下并不能完美的模拟电子产品实际的服役环境,这就使得获取到的电子产品寿命不准确。技术实现要素:本发明提供了一种电子产品寿命测算方法,所述方法包括:针对影响待测电子产品寿命的不同应力类型分别进行单应力寿命试验,获取每个应力类型对应的单应力平均寿命测算值;对所有的单应力平均寿命测算值进行加权综合,计算所述待测电子产品的寿命。在一实施例中,针对影响待测电子产品寿命的不同应力类型分别进行单应力寿命试验,获取每个应力类型对应的单应力平均寿命测算值,其中:针对影响待测电子产品寿命的不同应力类型分别在极限状态下进行单应力加速寿命试验获取极限状态下的加速寿命试验结果,根据所述加速寿命试验结果获取正常状态下的单应力平均寿命测算值。在一实施例中,所述单应力加速寿命试验的流程包括:确定表征所述待测电子产品寿命与当前单应力加速寿命试验对应的应力类型之间关系的加速模型;针对当前单应力加速寿命试验对应的应力类型试验确定所述待测电子产品的单应力工作极限;基于所述单应力工作极限进行加速应力下的寿命试验,获取加速寿命试验结果;根据所述加速寿命试验结果获取所述待测电子产品加速应力下的平均寿命测算值;根据所述加速模型以及所述加速应力下的平均寿命测算值获取所述待测电子产品正常工作状态下的单应力平均寿命测算值。在一实施例中,所述应力类型包括温度,对应的单应力加速寿命试验流程包括:确定表征所述待测电子产品寿命与温度应力之间的关系的加速模型;试验确定所述待测电子产品的高温工作极限;根据所述高温工作极限设定高温加速寿命试验的试验温度;在所述试验温度下进行高温加速寿命试验,计算高温状态下所述待测电子产品的平均寿命测算值;根据所述加速模型以及高温状态下所述待测电子产品的平均寿命测算值计算常温下所述待测电子产品的平均寿命测算值。在一实施例中,采用arrhenius模型表征所述待测电子产品寿命与温度应力之间的关系。在一实施例中,所述应力类型包括振动,对应的单应力加速寿命试验流程包括:确定表征所述待测电子产品寿命与振动应力之间的关系的加速模型;试验确定所述待测电子产品的振动工作极限;根据所述振动工作极限设定振动加速寿命试验的极限振动程度;在所述极限振动程度下进行振动加速寿命试验,计算极限振动状态下所述待测电子产品的平均寿命测算值;根据所述加速模型以及极限振动状态下所述待测电子产品的平均寿命测算值计算正常振动状态下所述待测电子产品的平均寿命测算值。在一实施例中,采用逆幂律模型表征所述待测电子产品寿命与振动应力之间的关系。在一实施例中,基于公式对所有的单应力加速寿命测试结果进行加权综合,其中:tmean为所述待测电子产品的寿命;n表示n种应力类型;xi%表示第i种应力引起的所述待测电子产品失效比例;ti表示第i种应力加速寿命试验的评估结果,1≤i≤n。在一实施例中,根据前期电子产品历史经验数据确定不同应力类型引起所述待测电子产品失效的比例。在一实施例中,所述应力类型包括温度以及振动,基于公式对温度单应力加速寿命测试结果以及振动单应力加速寿命测试结果进行加权综合,其中:tmean为所述待测电子产品的寿命;x%、y%分别为环境应力温度、振动引起所述待测电子产品失效的比例;t1表示温度单应力加速寿命测试结果;t2表示振动单应力加速寿命测试结果。相较于现有技术,本发明的方法过程简单,硬件需求低,可以获取准确率更高的寿命测算值,具有较高的实用价值以及推广价值。本发明的其它特征或优点将在随后的说明书中阐述。并且,本发明的部分特征或优点将通过说明书而变得显而易见,或者通过实施本发明而被了解。本发明的目的和部分优点可通过在说明书、权利要求书以及附图中所特别指出的步骤来实现或获得。附图说明附图用来提供对本发明的进一步理解,并且构成说明书的一部分,与本发明的实施例共同用于解释本发明,并不构成对本发明的限制。在附图中:图1是根据本发明一实施例的方法执行流程图;图2~图4根据本发明不同实施例的方法部分流程图。具体实施方式以下将结合附图及实施例来详细说明本发明的实施方式,借此本发明的实施人员可以充分理解本发明如何应用技术手段来解决技术问题,并达成技术效果的实现过程并依据上述实现过程具体实施本发明。需要说明的是,只要不构成冲突,本发明中的各个实施例以及各实施例中的各个特征可以相互结合,所形成的技术方案均在本发明的保护范围之内。在现有技术中,通常采用在试验环境下模拟电子产品实际的服役环境来测算电子产品的寿命。但是,电子产品在服役过程中通常会经受温度、湿度、振动等多种环境应力的影响,为了更加模拟电子产品实际的服役环境,试验的实施过程中通常会尽量多地覆盖产品实际的环境应力。但是,随着需要模拟的环境应力种类的增多,试验的硬件需求也会增加,试验所需的时间以及工作量也会增加。因此,在实际操作中,试验环境下并不能完美的模拟电子产品实际的服役环境,这就使得获取到的电子产品寿命不准确。针对上述问题,本发明提出一种电子产品寿命测算方法。在现有技术中,电子产品寿命测算结果不准的主要原因在于:(1)加速模型精度不足,对于电子产品,多应力综合作用的影响并非等效于单个应力作用的简单叠加,各应力之间的耦合效应难以量化;(2)试验设备集成度不够,对于综合应力,传统试验设备难以单独完成,必须利用综合试验设备,然而综合试验设备受制于采购成本、维护成本等,普及度不高。在本发明的方法中,在试验测算电子产品寿命时,并不是综合的同时针对实际服役环境的多种环境应力进行模拟,而是分别针对实际服役环境的每种环境应力进行单独模拟,测算单一环境应力对应的电子产品寿命,然后将多个电子产品寿命测算结果综合以获取实际服役环境下的电子产品寿命。由于针对单一环境应力的模拟的硬件需求以及试验操作难度远远小于同时针对多种环境应力综合模拟的硬件需求;并且,相较与综合环境应力的计算模型,单一环境应力的计算模型的复杂程度小,计算精度高。因此,在有限的硬件条件下,根据本发明的方法可以覆盖更多的实际服役环境的环境应力,从而大大提高寿命测算结果的准确程度。相较于现有技术,本发明的方法过程简单,硬件需求低,可以获取准确率更高的寿命测算值,具有较高的实用价值以及推广价值。接下来基于附图详细描述根据本发明实施例的方法的详细流程,附图的流程图中示出的步骤可以在包含诸如一组计算机可执行指令的计算机系统中执行。虽然在流程图中示出了各步骤的逻辑顺序,但是在某些情况下,可以以不同于此处的顺序执行所示出或描述的步骤。如图1所示,在一实施例中,电子产品寿命测算方法得流程包括:针对影响待测电子产品寿命的不同应力类型分别进行单应力寿命试验,获取每个应力类型对应的单应力平均寿命测算值(步骤s110);对所有的单应力平均寿命测算值进行加权综合,计算待测电子产品的寿命(步骤s120)。进一步的,在本发明的方法流程中,关键点之一在于如何进行单应力寿命试验获取单一应力类型对应的单应力平均寿命测算值。在一实施例中,采用加速寿命试验的方式进行单应力寿命试验。即,针对影响待测电子产品寿命的不同应力类型分别在极限状态下进行单应力加速寿命试验获取极限状态下的加速寿命试验结果,根据加速寿命试验结果获取正常状态下的单应力平均寿命测算值。具体的,如图2所示,在一实施例中,单应力加速寿命试验的流程包括:确定表征待测电子产品寿命与当前单应力加速寿命试验对应的应力类型之间关系的加速模型(步骤s210);针对当前单应力加速寿命试验对应的应力类型试验确定待测电子产品的单应力工作极限(步骤s220);基于单应力工作极限进行加速应力下的寿命试验,获取加速寿命试验结果(步骤s230);根据加速寿命试验结果获取待测电子产品加速应力下的平均寿命测算值(步骤s240);根据加速模型以及加速应力下的平均寿命测算值获取待测电子产品正常工作状态下的单应力平均寿命测算值(步骤s250)。进一步的,在实际应用场景中,影响电子产品寿命的主要环境应力类型之一是温度。在一实施例中,如图3所示,温度对应的单应力加速寿命试验流程包括:确定表征待测电子产品寿命与温度应力之间的关系的加速模型(步骤s310);试验确定待测电子产品的高温工作极限(步骤s320);根据高温工作极限设定高温加速寿命试验的试验温度(步骤s330);在试验温度下进行高温加速寿命试验,计算高温状态下待测电子产品的平均寿命测算值(步骤s340);根据加速模型以及高温状态下待测电子产品的平均寿命测算值计算常温下待测电子产品的平均寿命测算值(步骤s350)。具体的,在一实施例中,采用arrhenius模型表征待测电子产品寿命与温度应力之间的关系。进一步的,在实际应用场景中,影响电子产品寿命的主要环境应力类型还包括振动。在一实施例中,如图4所示,振动对应的单应力加速寿命试验流程包括:确定表征待测电子产品寿命与振动应力之间的关系的加速模型(步骤s410);试验确定待测电子产品的振动工作极限(步骤s420);根据振动工作极限设定振动加速寿命试验的极限振动程度(步骤s430);在极限振动程度下进行振动加速寿命试验,计算极限振动状态下待测电子产品的平均寿命测算值(步骤s440);根据加速模型以及极限振动状态下待测电子产品的平均寿命测算值计算正常振动状态下待测电子产品的平均寿命测算值(步骤s450)。具体的,在一实施例中,采用逆幂律模型表征待测电子产品寿命与振动应力之间的关系。上述实施例分别描述了针对温度以及振动两种环境应力的单应力加速寿命试验流程。需要指出的是,在实际应用场景中,影响电子产品寿命的环境应力有时并仅限于温度以及振动。需要根据电子产品的具体服役环境确定试验所需要模拟的应力类型。进一步的,在本发明的方法流程中,关键点还包括如何对所有的单应力平均寿命测算值进行加权综合。具体的,在一实施例中,基于公式对所有的单应力加速寿命测试结果进行加权综合,其中:tmean为所述待测电子产品的寿命;n表示n种应力类型;xi%表示第i种应力引起的所述待测电子产品失效比例;ti表示第i种应力加速寿命试验的评估结果,1≤i≤n。具体的,在一应用场景中,影响待测电子产品的环境应力类型为温度以及振动,对应的,基于公式对温度单应力加速寿命测试结果以及振动单应力加速寿命测试结果进行加权综合,其中:tmean为待测电子产品的寿命;x%、y%分别为环境应力温度、振动引起待测电子产品失效的比例;t1表示温度单应力加速寿命测试结果;t2表示振动单应力加速寿命测试结果。进一步的,在一实施例中,在对所有的单应力加速寿命测试结果进行加权综合的过程中,根据前期电子产品历史经验数据确定不同应力类型引起待测电子产品失效的比例。接下来针对一具体应用场景来详细描述本发明方法的实施过程。针对某控制板,影响其寿命的环境应力为温度以及针对,测算该控制板的寿命的流程如下:s1:单应力温度加速寿命试验。s1.1:高温工作极限摸底试验。从60度开始升温,当温度小于80℃时,步长为10℃,当温度大于等于80℃时,步长为5℃,每个温度点停留1个小时,全程温变率为设备的最大能力,在每个温度点停留30min后开始检测。如果控制板发生故障,将应力降低至上一应力水平,若控制板恢复正常工作,则判定故障应力水平为控制板的工作极限;若控制板无法恢复正常工作,则判定故障应力水平减去一个步长的值为工作极限。s1.2:高温加速寿命试验方案制定。根据s1.1工作极限摸底试验的结果,高温工作极限为95度,分别设置90度和85度两个温度点,开展试验,具体试验方案如表1所示:编号温度t(℃)试验样本量试验时间1(s1)905400小时2(s2)855400小时表1s1.2.1:试验截止条件。采用定时截尾和定数截尾相结合的方式,每组试验中,关联故障样本量达到3个及以上便可停止试验;或者达到试验停止时间400小时。s1.2.2:试验数据记录。对于每组应力水平的试验,每隔2小时对汽车控制板进行性能检测,判断是否故障,如果控制板发生了故障记录故障时的试验时间其中1≤i≤2,表示第i组试验,km表示每组试验的故障数,1≤m≤3。s1.3:加速模型确定。采用arrhenius模型表征该控制板的寿命与温度应力之间的关系:ξ=aee/kt(3)其中,ξ表示特征寿命,a为正常数,e表示激活能,k是玻尔兹曼常数,为8.617×10-5ev/℃,t为绝对温度。对式(3)进行对数变化,得到:lnξ=a+b/t(4)其中,a=lna,b=e/k,均为未知系数。s1.4:加速应力下平均寿命的点估计。s1.4.1:各组试验下总的试验时间。各组试验下总的试验时间ti′为:其中,i表示第i组试验,表示每组试验的故障数,tij表示第i组试验第j个故障控制板的故障时间,ni=5,表示第i组试验的样本数,φi=400,表示第i组试验的截尾时间。s1.4.2:各组试验下控制板平均寿命的点估计。各组试验下控制板平均寿命t的点估计为:s1.5:回归分析。将第i组试验的应力值ti,i=1,2以及s1.4.2各组试验下控制板平均寿命的点估计值带入式(4),可以求解2个未知系数a、b的取值。s1.6:正常应力下平均寿命的评估。将正常使用应力水平45℃带入式(4),可计算该控制板的寿命t1为35727.66小时,约8.157年。s2:单应力振动加速寿命试验。s2.1:振动工作极限摸底试验。初始振动量级为1grms,频率在5hz~150hz之间,振动步长为0.2grms,在每个振动台阶停留10min开始检测。如果控制板发生故障,将应力降低至上一应力水平,若控制板恢复正常工作,则判定故障应力水平为控制板的工作极限;若控制板无法恢复正常工作,则判定故障应力水平减去一个步长的值为工作极限。s2.2:振动加速寿命试验方案制定。根据s2.1工作极限摸底试验的结果,振动工作极限为2.8grms,分别设置2.4grms和2.2grms两个振动点,开展试验,具体试验方案如表2所示:编号振动v(grms)试验样本量试验时间1(s1)2.45400小时2(s2)2.25400小时表2s2.2.1:试验截止条件。采用定时截尾和定数截尾相结合的方式,每组试验中,关联故障样本量达到3个及以上便可停止试验;或者达到试验停止时间400小时。s2.2.2:试验数据记录。对于每组应力水平的试验,每隔2小时对汽车控制板进行性能检测,判断是否故障,如果控制板发生了故障记录故障时的试验时间其中1≤i≤2,表示第i组试验,km表示每组试验的故障数,1≤m≤3。s2.3:加速模型确定。采用逆幂律模型表征该控制板的寿命与振动应力之间的关系:ξ=av-c(7)其中,ξ表示特征寿命,a,c表示未知参数,v为振动应力。对式(7)进行对数变化,得到:lnξ=a+blnv(8)其中a=lna,b=-c,均为未知系数。s2.4:加速应力下平均寿命的点估计。s2.4.1:各组试验下总的试验时间。各组试验下总的试验时间ti′为:其中,i表示第i组试验,表示每组试验的故障数,tij表示第i组试验第j个故障控制板的故障时间,ni=5,表示第i组试验的样本数,φi=400,表示第i组试验的截尾时间。s2.4.2:各组试验下控制板平均寿命的点估计。各组试验下控制板平均寿命t的点估计为:s2.5:回归分析。将第i组试验的应力值vi,i=1,2以及s2.4.2各组试验下控制板平均寿命的点估计值带入式(8),可以求解2个未知系数a、b的取值。s2.6:正常应力下平均寿命的评估。将正常使用应力水平0.25grms带入式(8),可计算该控制板的寿命t2为28605.78小时,约6.531年。s3:综合应力下平均寿命评估。s3.1:温度、振动环境应力引起产品失效比例的历史数据。根据前期积累的电子产品历史经验数据,得到环境应力温度、振动等引起电子产品失效的比例x%,y%;s3.2:温度-振动综合应力下控制板的寿命评估。根据单应力温度、振动的加速寿命试验评估结果,结合s3.1的失效比例,可以根据式(2)计算控制板在温度、振动综合应力下的平均寿命tmean为33056.96小时,约7.547年。本发明的电子产品寿命评估方法,首先开展单应力加速寿命试验,利用单应力加速模型计算电子产品在单应力下的平均寿命;然后根据环境应力引起电子产品失效比例数据,开展加权综合计算,从而计算电子产品在多应力综合作用下的平均寿命指标。本发明一方面规避了多应力加速模型耦合度不足导致的加速寿命试验精度差的问题,另一方面不需采用集成度较高的综合试验设备,便可完成综合应力的寿命评估,节约试验成本。虽然本发明所公开的实施方式如上,但所述的内容只是为了便于理解本发明而采用的实施方式,并非用以限定本发明。本发明所述的方法还可有其他多种实施例。在不背离本发明实质的情况下,熟悉本领域的技术人员当可根据本发明做出各种相应的改变或变形,但这些相应的改变或变形都应属于本发明的权利要求的保护范围。当前第1页12