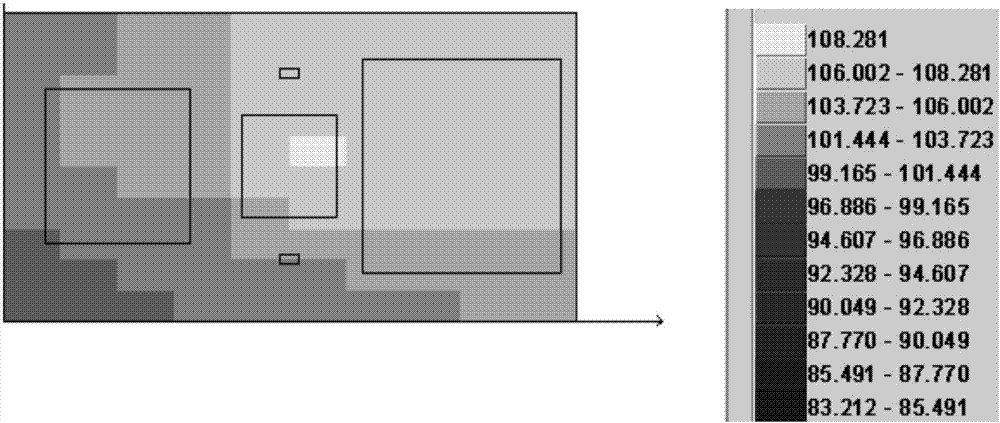
本发明涉及电子
技术领域:
,具体涉及一种电路板寿命预测方法。
背景技术:
:随着电子技术的不断发展,越来越多的电子产品被应用于人类的日常生产生活中。电子产品会随着不断使用而老化损坏。随着电子产品的应用范围不断拓宽,一个系统中,单一电子产品的损坏往往会造成一系列的连锁反应。因此,为了维持整个系统的稳定,需要及时监测电子产品的损坏状况并予以更换。然而,即时监测的方式需要消耗大量的资源,并且即时监测也只能在电子产品损坏时才能发现问题并更换,此时,电子产品损坏所造成的连锁反应往往已经发生。因此,在现有技术中,会预先对电子产品的寿命进行测算,以便用户在电子产品寿命到期前及时安排更换操作,从而大大降低电子产品因老化损坏带来的损失。在电子产品的结构中,一个重要的组成部分就是电路板。在现有技术中,通常采用在试验环境下模拟电路板实际的服役环境来测算电路板的寿命。但是,这种寿命测算方法的执行前提是必须有实物的成品电路板可供试验。这就导致了测试用电路板的生产成本以及生产时间消耗。尤其的,在电路板的研发阶段,由于电路板结果会被多次修改,每次修改后都必须进行测试样品生产的操作,大大增加了研发成本并带来了严重的研发时间浪费。技术实现要素:本发明提供了一种电路板寿命预测方法,所述方法包括:根据目标电路板的板型设计确定所述目标电路板的潜在故障点以及对应的故障机理和故障物理模型;基于所述故障物理模型,综合每个所述潜在故障点对应的所有故障机理,计算获取每个所述潜在故障点的寿命概率密度函数;根据所有所述潜在故障点的寿命概率密度函数,结合竞争失效算法,构建所述目标电路板的寿命概率密度函数,计算获取所述目标电路板的寿命。在一实施例中,针对目标电路板确定潜在故障点以及对应的故障机理和故障物理模型,包括:针对所述目标电路板各个器件进行基于故障模式、机理的影响分析,确定所述目标电路板的潜在故障点以及对应的故障机理和故障物理模型。在一实施例中,所述故障模式包括焊点断裂,所述焊点断裂对应的故障机理包括热疲劳以及振动疲劳,所述热疲劳对应的故障物理模型为柯芬一曼森低循环疲劳和应变疲劳模型,所述振动疲劳对应的物理模型为1阶随机振动疲劳模型。在一实施例中,计算获取每个所述潜在故障点的寿命概率密度函数,包括:分别获取每个所述潜在故障点在单一故障机理下的故障概率密度函数;利用竞争失效算法,根据所述潜在故障点在所有所述故障机理下的故障概率密度函数获取所述潜在故障点的寿命概率密度函数。在一实施例中,分别获取每个所述潜在故障点在单一故障机理下的故障概率密度函数,包括:获取所述目标电路板的材料信息、结构信息以及环境载荷信息;基于所述故障物理模型,结合所述材料信息、所述结构信息,建立所述目标电路板的可靠性分析仿真模型;利用所述可靠性分析仿真模型,结合所述环境载荷信息,分别针对所有的所述故障机理进行应力分析;根据应力分析结果进行仿真,建立概率故障物理模型;根据所述概率故障物理模型获取各个所述潜在故障点在单一故障机理下的故障时间数据,对所述故障时间数据进行拟合,获取所述潜在故障点在所述故障机理下的故障概率密度函数。在一实施例中,根据应力分析结果进行仿真,其中:设置所述材料信息、结构信息以及环境应力信息为随机变量,利用蒙特卡洛随机化方法进行仿真。在一实施例中,设置所述随机变量服从均匀分布,上下容差分别为±5%。在一实施例中,构建所述目标电路板的寿命概率密度函数,其中:以每个所述潜在故障点作为对象,每次从各个所述潜在故障点进行抽样,结合竞争失效算法原则,构建所述寿命概率密度函数。在一实施例中,计算获取所述目标电路板的寿命,其中,计算所述目标电路板的平均首发故障时间。在一实施例中,算获取每个所述潜在故障点的寿命概率密度函数,其中,计算每个所述潜在故障点的平均首发故障时间。本发明的方法过程简单,不需要实体的测试用电路板;相较于现有技术,本发明的方法成本低、具有很高的灵活性,可以大大缩短电路板的开发周期、节约电路板的试验费用。本发明的其它特征或优点将在随后的说明书中阐述。并且,本发明的部分特征或优点将通过说明书而变得显而易见,或者通过实施本发明而被了解。本发明的目的和部分优点可通过在说明书、权利要求书以及附图中所特别指出的步骤来实现或获得。附图说明附图用来提供对本发明的进一步理解,并且构成说明书的一部分,与本发明的实施例共同用于解释本发明,并不构成对本发明的限制。在附图中:图1以及图4是根据本发明不同实施例的方法执行流程图;图2以及图3是根据本发明不同实施例的方法部分流程图;图5是根据本发明一实施例的目标电路板cca模型示意图;图6是根据本发明一实施例的目标电路板热应力云图;图7是根据本发明一实施例的目标电路板冲击条件下位移云图;图8是根据本发明一实施例的目标电路板1阶模态位移图;图9是根据本发明一实施例的目标电路板1阶振型图;图10是根据本发明一实施例的目标电路板寿命概率密度函数图。具体实施方式以下将结合附图及实施例来详细说明本发明的实施方式,借此本发明的实施人员可以充分理解本发明如何应用技术手段来解决技术问题,并达成技术效果的实现过程并依据上述实现过程具体实施本发明。需要说明的是,只要不构成冲突,本发明中的各个实施例以及各实施例中的各个特征可以相互结合,所形成的技术方案均在本发明的保护范围之内。在电子产品的结构中,一个重要的组成部分就是电路板。在现有技术中,通常采用在试验环境下模拟电路板实际的服役环境来测算电路板的寿命。但是,这种寿命测算方法的执行前提是必须有实物的成品电路板可供试验。这就导致了测试用电路板的生产成本以及生产时间消耗。尤其的,在电路板的研发阶段,由于电路板结果会被多次修改,每次修改后都必须进行测试样品生产的操作,大大增加了研发成本并带来了严重的研发时间浪费。针对上述现有技术中存在的问题,本发明提出了一种电路板寿命预测方法。在本发明的方法中,不需要对实体的电路板进行试验测算,而是根据电路板的板型设计来计算构造物理模型,基于物理模型进行仿真来计算获取电路板的寿命。这样在电路板的研发阶段,每次修改电路板设计时只需对应修正其物理模型就能计算获取其寿命测算值。本发明的方法过程简单,不需要实体的测试用电路板;相较于现有技术,本发明的方法成本低、具有很高的灵活性,可以大大缩短电路板的开发周期、节约电路板的试验费用。具体的,由于电路板是由多个元器件组合构成的结构,在实际服役环境中,电路板上存在多个可能会发生故障的位置点。因此,在本发明的方法中,对电路板上的多个故障点首先分别进行寿命分析,然后综合所有故障点的寿命分析结果来分析整个电路板的寿命。进一步的,通常,针对单一故障点,引发其故障的原因(故障机理)也不止一个。例如,针对一引脚焊点,导致其断裂的原因可能是温度疲劳,也可能是振动疲劳。因此,在本发明的方法中,针对每个故障点,还要对可能导致其故障的每个故障机理进行分别分析,综合所有的故障机理的分析结果来分析该故障点的寿命。接下来基于附图详细描述根据本发明实施例的方法的详细流程,附图的流程图中示出的步骤可以在包含诸如一组计算机可执行指令的计算机系统中执行。虽然在流程图中示出了各步骤的逻辑顺序,但是在某些情况下,可以以不同于此处的顺序执行所示出或描述的步骤。如图1所示,在一实施例中,电路板寿命预测方法包括以下步骤:根据目标电路板的板型设计确定目标电路板的潜在故障点以及对应的故障机理和故障物理模型(s110);基于故障物理模型,综合每个潜在故障点对应的所有故障机理,计算获取每个潜在故障点的寿命概率密度函数(s120);根据所有潜在故障点的寿命概率密度函数,结合竞争失效算法,构建目标电路板的寿命概率密度函数,计算获取目标电路板的寿命(s130)。具体的,在一实施例中,在步骤s110中,采用影响分析(fmmea)方法确定目标电路板的潜在故障点以及对应的故障机理和故障物理模型。具体的,根据电路板可能发生的所有故障模式针对目标电路板各个器件进行基于故障模式、机理的影响分析,从而确定目标电路板的潜在故障点以及对应的故障机理和故障物理模型。进一步的,在一实施例中,电路板可能发生的故障模式包括焊点断裂,焊点断裂对应的故障机理包括热疲劳以及振动疲劳,热疲劳对应的故障物理模型为coffin-mason模型,振动疲劳对应的物理模型为1阶随机振动疲劳模型。进一步的,在一实施例中,利用竞争失效算法来综合同一潜在故障点上的所有的故障机理的分析结果。具体的,如图2所示,首先分别获取每个潜在故障点在单一故障机理下的故障概率密度函数(s210);然后利用竞争失效算法,根据潜在故障点在所有故障机理下的故障概率密度函数获取潜在故障点的寿命概率密度函数(s220)。进一步的,在一实施例中,采用仿真计算方法获取每个潜在故障点在单一故障机理下的故障概率密度函数。具体的,如图3所示,首先获取目标电路板的材料信息、结构信息以及环境载荷信息(s310);然后基于故障物理模型,结合目标电路板的材料信息、结构信息,建立目标电路板的可靠性分析仿真模型(s320);接着利用可靠性分析仿真模型,结合环境载荷信息,分别针对所有的故障机理进行应力分析(s330);根据应力分析结果进行仿真,建立概率故障物理模型(ppof,probabilisticphysicsoffailure)(s340);根据概率故障物理模型获取各个潜在故障点在单一故障机理下的故障时间数据,对故障时间数据进行拟合,获取潜在故障点在所述故障机理下的故障概率密度函数(s350)。具体的,在一实施例中,在根据应力分析结果进行仿真的过程中,设置目标电路板的材料信息、结构信息以及环境应力信息为随机变量,利用蒙特卡洛随机化方法进行仿真。进一步的,在一实施例中,设置随机变量服从均匀分布,上下容差分别为±5%。进一步的,在一实施例中,利用calcepwa软件建立可靠性分析仿真模型(cca)。进一步的,在一实施例中,在构建目标电路板的寿命概率密度函数的过程中,以每个潜在故障点作为对象,每次从各个潜在故障点进行抽样,结合竞争失效算法原则,构建寿命概率密度函数。进一步的,为了简单的获取直观的寿命测算结果,在一实施例中,在最后计算获取目标电路板的寿命时,计算目标电路板的平均首发故障时间。对应的,在一实施例中,在获取每个潜在故障点的寿命概率密度函数的过程中,计算每个潜在故障点的平均首发故障时间。接下来基于一具体应用实例来详细说明本发明方法的执行流程。以一特定板型设计的电路板为对象进行电路板寿命测算,其执行流程如下(如图4所示):s1:故障物理模型识别。利用故障模式、机理及其影响分析(fmmea)的方法,找到潜在故障点处的故障机理以及故障物理模型。针对测算对象的潜在故障点进行了fmmea,表1列举部分元件的fmmea数据信息,其中最后1列为潜在故障点处可能存在的故障物理模型。表1对于潜在故障点u3,其故障模式为焊点断裂,该故障模式所对应的故障机理有两种,分别是热疲劳和振动疲劳。热疲劳所对应的故障物理模型为柯芬一曼森低循环疲劳和应变疲劳(coffin-mason)模型,如式(1)所示;式(1)中:nf表示器件平均失效前的循环次数;δυ表示焊点所受剪切应力的范围,其值由热应力分析得到;ξf表示疲劳延伸系数,由具体材料决定,比如,对于lead.5sn95pb材料,其值为0.325;c表示温度循环应力强度指数,其表达式为:式(2)中,tme表示温度循环的平均温度,td表示高温浸泡时间。振动疲劳所对应的故障物理模型为1阶随机振动疲劳模型,如式(3)所示。。式(3)中,nf为器件的疲劳寿命;b为疲劳强度指数;c是与振动类型相关的常数,比如随机振动,其值2e+7;x和y为器件坐标;z1和z2分别表示与产品结构相关的参数和与振动应力强度相关的参数,具体的取值分别如式(4)和式(5)所示:式(4)中,c表示与器件封装类型相关的系数;t表示电路板厚度;l表示器件长度;b表示器件四条边到电路板四条边的距离中最大的值。式(5)中,fn表示最小自然频率,psdmax为经过振动分析后得到的最大功率谱密度值。s2:器件寿命评估。根据目标电路板的材料信息、结构信息、环境载荷信息并结合应力分析的结果,得到目标电路板失效的主故障机理、设计薄弱环节并计算各故障机理的故障时间和分布等,最终得到目标电路板上各器件故障预计信息矩阵,从而完成器件寿命评估工作。s2.1:材料库、结构库、应力库。搜集产品材料、结构等设计信息、三维模型信息及环境应力载荷信息等,对于目标电路板,其部分信息库如表2-表5所示,其中,表2、表3为元器件数据信息,表4为板层信息,表5为环境载荷信息。元件id元件类型封装横坐标(mm)纵坐标(mm)导电孔数量r1电阻res120650.840.642u1集成电路pqfp16020.3225.4160u3集成电路bga35281.2825.4352表2表3位置层层材料厚度(mm)金属材料金属化率1layer_1pwb.epoxyf0.03556pwb.cu502layer_2pwb.epoxyf0.635pwb.cu03layer_3pwb.epoxyf0.03556pwb.cu504layer_4pwb.epoxyf0.635pwb.cu05layer_5pwb.epoxyf0.03556pwb.cu506layer_6pwb.epoxyf0.635pwb.cu0表4表5s2.2:cca(calcepwa)模型建立。根据目标电路板元器件及板层的材料、尺寸、功率等数据,在calcepwa软件中建立电路板的cca模型,其中器件以三维实体简化表示,以功率值表示器件散热,通过电路互联结构实现热传递,具体如图5所示。s2.3:应力分析。首先进行热应力分析,得到的热应力云图如图6所示。由图6所示结果可得,温度最大值出现在u2处,最高温度达到1080c;此外,器件u3的表面温度也较高。针对目标电路板cca模型,开展振动应力分析,得到冲击应力条件下,单板位移云图如图7所示。由图7所示结果可得,位移较大区域发生在单板的中间区域,最大值达到3.964e-2mm;在随机振动应力作用下,单板的1阶模态位移如图8所示,1阶固有频率为416.2hz;1阶振型如图9所示。s2.4:ppof模型建立。设置表2-表4中的材料、结构等信息为随机变量,利用蒙特卡洛随机化方法,随机变量服从均匀分布,上下容差分别为±5%;在calcepwa软件设置蒙特卡洛(montecarlo)仿真,仿真次数为1000,从而建立ppof模型。s2.5:故障点分布拟合。根据s2.4的仿真结果,得到各个潜在故障点在某一故障物理模型下的大量故障时间数据。对这些故障数据进行拟合,得到在该故障机理下的故障概率密度函数fi(x),i表示第i个故障机理。s2.6:故障点分布融合。利用竞争失效的算法,得到该潜在故障点的寿命概率密度函数hj(x),j表示第j个潜在故障点,根据式(6)计算各个潜在故障点的平均首发故障时间式(6)中,k表示第k个潜在故障点。部分潜在故障点的平均首发故障时间如表6所示:名次故障模式主故障机理平均首发故障时间1u3焊点开裂1阶热疲劳模型(pbga)5.30年2r1焊点开裂1阶热疲劳模型(ll)9.26年3c1焊点开裂1阶热疲劳模型(ll)17.10年4u1互连开路1阶振动疲劳模型(rm)30年5镀通孔电学开路calce_pth热疲劳模型30年表6s3:系统寿命评估。以每个潜在的故障点作为对象,每次从各个潜在故障点进行抽样,结合竞争失效算法原则,构建整个电路板的寿命概率密度函数f(t),最终得到,在95%置信度水平下,可以认为f(t)数据服从3参数威布尔分布,其中尺寸参数a=27178.2,形状参数b=2.078,位置参数c=18314,仿真数据和拟合的曲线如图10所示。目标电路板的寿命概率密度函数如公式所示:基于式(7)可以计算,目标电路板的平均首发故障时间tlife为:假定产品不能维修,目标电路板的平均寿命为42388.45小时,约4.84年。根据本发明的方法,基于失效物理的思想去完成某型电路板的寿命预测工作,可以在研发样机阶段定性暴露该产品的设计薄弱环节,定量评估寿命指标,大大缩短了产品的研发周期,节约了产品的试验费用。虽然本发明所公开的实施方式如上,但所述的内容只是为了便于理解本发明而采用的实施方式,并非用以限定本发明。本发明所述的方法还可有其他多种实施例。在不背离本发明实质的情况下,熟悉本领域的技术人员当可根据本发明做出各种相应的改变或变形,但这些相应的改变或变形都应属于本发明的权利要求的保护范围。当前第1页12