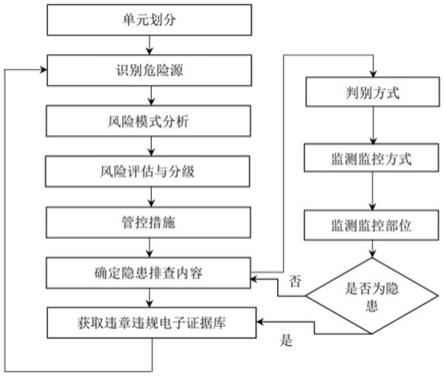
1.本发明属于企业安全风险辨识与评估技术领域,具体涉及一种金属冶炼企业重大 安全风险重大风险辨识与评估方法。
背景技术:2.冶金行业风险辨识评估技术是伴随着安全系统工程的理论发展而来的。通过消化、 吸收国外安全检查表和安全风险的方法,机械、冶金、航天、航空等行业的有关企业开 始应用风险分析评价方法,如安全检查表(scl)、事故树分析(fta)、故障类型及影 响分析(fema)、预先危险性分析(pha)、危险与可操作性研究(hazop)、作业条 件危险性评价(lec)等。
3.由原劳动部劳动保护科学研究所等单位完成的《易燃、易爆、有毒重大危险源辨 识、评价技术研究》项目,将重大危险源评价分为固有危险性评价和现实危险性评价, 反映了人对控制事故发生和事故后果扩大的主观能动作用。该项目在事故严重度评价中 建立了伤害模型库,采用了定量的计算方法,使我国工业安全评价方法的研究从定性评 价进入定量评价阶段。
4.原机械委颁发实施的《机械工厂安全性评价标准》,以检查表打分的办法将评价 内容分为综合管理、危险性和劳动卫生与作业环境三大部分,分别赋予230、600、170 分的权重,以总计得分多少来评定企业的安全水平,是我国实施较早的一个安全性评价 标准。该办法数模结构简单,规定较细,易于推广应用,但也有美中不足之处。
5.(1)评价模型的立论根据、建模原则及有关因素内涵和赋值,还未见严密的科 学论证。
6.(2)评价模型属静态模型。
7.(3)以评估企业宏观安全等级为主要目的。
8.近些年来,不少企业和研究单位也探索提出了许多安全评价、风险评估方法,但 归纳起来,除一部分类似于原机械委的检查表评分方法外,有的混合采用了国外的一些 安全评价方法,有的属模糊评价。模糊评价法虽然对于评定企业安全等级也可发挥一定 的作用,但从系统控制的角度考虑,因其难于提出改进安全工作的参考信息,故也不是 一种理想的方法。
9.根据历年金属冶炼企业事故案例情况,事故主要集中在冶金企业中。冶金是从矿 物中提取金属或其化合物制成金属材料的过程。冶金企业一般包括矿山、烧结、焦化、 耐火、炼铁、炼钢、轧钢、有色金属冶炼及加工、能源动力、氧气、其他辅助配套厂等。
10.冶金企业生产链长、复杂,涉及高温熔融金属、易燃易爆和有毒有害气体、高能 高压设备、危险矿井及尾矿库等很多有较大风险的危险因素,容易引发安全生产事故。
11.国内近年发生的重特大事故表明,以行业为重点预防重特大事故的管理思路已经 不能适应当前安全生产的实际,如何针对重特大事故建立一套具有精准性、前瞻性、系 统性和全面性的防控体系,是亟需解决的一个重大课题。
技术实现要素:12.本发明的目的是针对现有技术存在的不足提供一种金属冶炼企业重大安全风险 重大风险辨识与评估方法。
13.为实现本发明的目的,本发明的技术方案是:一种金属冶炼企业重大安全风险重 大风险辨识与评估方法,步骤在于:s1数据收集,所述收集的数据包括:s1.1金属冶炼企业重、特大事故案例;s1.2金属冶炼企业的涉及的高风险物品、生产工艺水平、设备设施本质化安全状况;s1.3安全评价报告;s1.4金属冶炼相关法规、标准;s1.5隐患电子违章信息采集;s2数据分析,对重、特大事故案例进行分析,分析事故发生的原因、涉及的工艺、设 备、场所,寻找与事故相关的风险因子;s3风险辨识s3.1按金属冶炼工艺划分风险单元,在风险单元内确定风险点进行风险辨识;s3.2编制金属冶炼企业通用风险辨识清单;s3.3按照隐患排查内容、要求查找隐患,并对可能出现的电子违章违规行为、状态、缺 陷,利用在线监测监控系统摄取违章证据,形成金属冶炼企业通用风险与隐患违规证据 信息清单;s3.4风险点从高风险物品、高风险工艺、高风险设备、高风险场所、高风险作业辨识高 危风险因子;s3.5将每个风险点的高风险物品风险因子、高风险工艺风险因子、高风险设备风险因子、 高风险场所风险因子、高风险作业风险因子辨识结果整理汇编成单元固有风险清单;s4风险评估s4.1采用风险矩阵法对通用风险清单中的风险点进行初步评估;s4.2以冶炼工艺为单元,以重点防控风险点为评估主线,划分风险评估单元;s4.3建立金属冶炼企业高危风险固有风险指标体系,通过建立的金属冶炼企业评估模型, 计算风险点的固有危险指数;s4.4单元固有风险评估,单元内每个风险点固有危险指数的危险暴露加权累计值;s4.5确定单元风险频率,以单元安全生产标准化得分百分比的倒数作为单元风险频率指 标;s4.6单元初始高危安全风险评估,单元风险管控频率与单元固有危险指数的聚合;s4.7动态风险因子辨识s4.7.1单元动态风险因子辨识,单元动态风险因子包括高危风险动态监测因子、安全生 产基础管理动态因子、自然环境动态因子、物联网大数据动态因子、特殊时期动态
因子;s4.7.2单元动态风险清单编制;s4.8动态风险因子辨识,不同动态风险因子形成的现实风险动态修正指标分别实时修正 风险点固有危,险指数和单元初始高危安全风险;s4.9单元风险聚合到企业整体风险。
14.根据本发明实施例,所述步骤s3.1按金属冶炼工艺划分风险单元包括炼铁单元、 炼钢单元、黑色金属铸造单元、铁合金冶炼单元、铜冶单元炼、铅锌冶炼单元、镍钴冶 炼单元、锡冶炼单元、锑冶炼单元、铝冶炼单元、镁冶炼单元、其他稀有金属冶炼单元、 有色金属合金制造单元、有色金属铸造单元;所述步骤s3.1在风险单元内确定风险点 包括高炉坍塌事故风险点。
15.根据本发明实施例,所述步骤s4.3金属冶炼企业评估模型包括风险点固有危险 指数、单元固有危险指数、现实风险动态修正指数、风险点固有风险指标动态修正、单 元固有危险指数动态修正、单元风险频率指标、单元初始高危风险、单元现实风险;所述单元现实风险由r
n
表示,包括单元安全生产基础管理、安全生产标准化和单元内 各风险点的高风险设备、高风险工艺、高风险物质、高风险场所、高风险作业以及监测 监控指标报警因素构成,金属冶炼企业单元高危现实风险评估模型为:式中:r
n
——单元现实风险b
s
——安全生产基础管理动态指标v——安全生产标准化自评/评审分值h
si
——单元内第i个风险点的高风险设备指数m——物质危险系数e——场所人员暴露指数l
i
——单元内第i个风险点监测监控设施失效率的平均值t
i
——单元内第i个风险点涉及高风险作业种类数k
3i
——单元内第i个风险点高危风险动态监测特征指标报警信号修正系数e
i
——单元内第i个风险点场所人员暴露指数f——单元内各风险点场所人员暴露指数累计值n——单元内风险点数。
16.根据本发明实施例,所述金属冶炼企业单元高危现实风险评估模型应用在金属 冶炼企业的风险单元,依据试算结果的可比性原则,制定单元风险分级标准为: 17.根据本发明实施例,所述单元风险分级标准应用企业整体风险标准化分,以单元 内最高风险等级风险点为单元整体风险,单元整体风险级别划分标准为:
18.根据本发明实施例,所述单元风险分级标准应用企业整体风险标准化分,采用兼 顾极值或称突出最大值的计权型多因子环境质量指数的方法来计算企业的整体风险,对 于一个企业,只需计算出它的整体综合风险指数,再对照单元风险分级标准,按照内梅 罗指数的基本计算公式,企业整体风险等级r为:式中:max(rni)为企业各单元现实风险值中最大值ave(r
ni
)为企业各单元现实风险值的平均值。
19.根据本发明实施例,所述单元风险分级标准应用企业整体风险标准化分,企业整 体风险等级r由企业内单元现实风险最大值max(r
ni
)确定,即 r=max(r
ni
)。
20.根据本发明实施例,所述步骤s3.5中,所述高危风险动态监测因子从企业现有的监测系统提取,包括温度、压力、冷却水,高 危风险动态监测因子作为对风险点固有危险指数动态修正;所述安全生产基础管理动态因子包括事故隐患、生产安全事故2项指标;所述自然环境动态因子从气象系统获取,选取对本单元事故发生有影响的气象和地质灾 害数据;所述物联网大数据动态因子从国家安全大数据平台提取,选取与本单元风险相关的同类 型事故数据;所述特殊时期动态因子从政务网、国家日历获取。
21.一种电子设备,包括:一个或多个处理器;存储装置,用于存储一个或多个程序;当所述一个或多个程序被一个或多个处理器执行,使得一个或多个处理器实现一种金属 冶炼企业重大安全风险重大风险辨识与评估方法。
22.一种计算机可读介质,其上存储有计算机程序,所述程序被处理器执行时实现一 种金属冶炼企业重大安全风险重大风险辨识与评估方法。
23.本发明的有益技术效果是:(1)提出由单元到风险点的金属冶炼企业重大风险 辨识方法;(2)编制汇总金属冶炼企业的单元高危风险清单,为后期的风险评价提供依 据和参考;(3)高危风险防控模型运用安全科学原理,构建系统的事故防控模型;(4) 对照高危风险清单,确定分析对象,减少对重大安全风险管控的盲目性,实现靶向感知, 避免受从业人员对法规标准和有关知识、经验的局限;(5)集合高危险事故的诱发因素、 后果严重性、
社会承载能力、安全隐患、事故的大数据建立风险分析模型,计算出风险 值;高危险风险值也是动态变化的,如大幅提高某一高风险设备的管理水平,其风险值 也随之降低;但如果社会承载能力减小,即便管理水平有所提高,其风险值也是上升的; (6)根据高危险风险值和风险系数,建立统一的风险等级体系和预警值;(7)根据冶 金企业调研的有关技术资料和现场调查、类比分析结果,在辨识分析的基础上对风险点 风险严重度(固有风险)评估;通过典型金属冶炼企业使用本评估模型进行应用,验证 了评估模型的可行性;(8)以提高金属冶炼企业的本质安全程度和安全管理水平,预防 重特大事故,减轻事故危害后果为目的,为金属冶炼企业安全风险管控提供理论与技术 指导。
附图说明
24.图1是单元风险分级评估与隐患违章电子库流程图。
25.图2是金属冶炼企业重大安全风险重大风险辨识与评估方法流程图。
26.具体实施方式
27.以下结合附图及实施例对本发明做进一步详细的说明。
28.如图1,本发明提供一种金属冶炼企业重大安全风险重大风险辨识与评估方法, 步骤在于:s1数据收集,所述收集的数据包括:s1.1金属冶炼企业重、特大事故案例;s1.2金属冶炼企业的涉及的高风险物品、生产工艺水平、设备设施本质化安全状况;s1.3安全评价报告;s1.4金属冶炼相关法规、标准;s1.5隐患电子违章信息采集;s2数据分析,对重、特大事故案例进行分析,分析事故发生的原因、涉及的工艺、设 备、场所,寻找与事故相关的风险因子;s3风险辨识s3.1按金属冶炼工艺划分风险单元,在风险单元内确定风险点进行风险辨识;s3.2编制金属冶炼企业通用风险辨识清单;s3.3按照隐患排查内容、要求查找隐患,并对可能出现的电子违章违规行为、状态、缺 陷,利用在线监测监控系统摄取违章证据,形成金属冶炼企业通用风险与隐患违规证据 信息清单;s3.4风险点从高风险物品、高风险工艺、高风险设备、高风险场所、高风险作业辨识高 危风险因子;s3.5将每个风险点的高风险物品风险因子、高风险工艺风险因子、高风险设备风险因子、 高风险场所风险因子、高风险作业风险因子辨识结果整理汇编成单元固有风险清单;s4风险评估
有风险辨识评估单元,一般以车间划分。该单元的划分原则兼顾了单元安全风险管控能 力与安全生产标准化管控体系的无缝对接。风险点是在单元区域内,以可能诱发的本单 元重特大事故点作为风险点。
37.将金属冶炼行业按工艺特点划分评估单元,见表1。
38.表1安全评估单元划分
39.结合典型金属冶炼行业安全风险辨识与评估和事故案例统计分析结果,参照法 律法规及行业标准等,结合所划分单元,重点关注危险部位及关键作业岗位,辨识与研 判金属冶炼行业潜在风险模式,参照《企业职工伤亡事故分类》识别事故后果类别,分 析事故后果严重程度,并提出与风险模式相对应的管控对策。
40.此外,按照隐患排查内容、要求查找隐患,并对可能出现的电子违章违规行为、 状态、缺陷等,利用在线监测监控系统摄取违章证据,最终形成安全风险与隐患违章信 息表。
41.综合考虑可能出现的事故类型与事故后果,运用风险矩阵对每一项进行评估,确 定风险等级。与风险辨识信息表制作的关键术语的释义。
42.危险部位:各评估单元具有潜在能量和物质释放危险的、可造成人员伤害、在一 定的触发因素作用下发生事故的部位。
43.风险模式:即风险的表现形式,风险的出现方式或风险对操作的影响。
44.事故类别:参照《企业职工伤亡事故分类标准》(gb 6441
‑
1986)事故类别与定 义。如,溃坝在标准中事故类别为其他。
45.事故后果:某种事件对目标影响的结果。事件导致的最严重的潜在后果,以人员 伤害程度、财产损失、系统或设备设施破坏、社会影响力加以度量。
46.风险等级:单一风险或组合风险的大小,以后果和可能性的组合来表达。
47.风险管控措施:与参考依据一一对应,主要依据国家标准和行业规范,针对每一 项风险模式从标准或规范中找出对应的管控措施列出来。如:《炼铁安全规程》、《炼钢 安全规程》、《工业企业煤气安全规程》、《铜冶炼安全生产规范》、《铜及铜合金熔铸安全 生产规范》等。
48.隐患违规电子证据:按照隐患排查内容、要求查找隐患,并对可能出现的电子违 章违规行为、状态、缺陷等,利用在线监测监控系统摄取违章证据,为远程执法提供证 据。
49.判别方式:根据排查的内容,判别是否出现的违章违规行为、状态、管理缺陷等。
50.监测监控方式:捕获隐患的信息化手段,主要有在线监测、监控、无人机摄取、 日常隐患或分析资料的上传等。
51.监测监控部位:在重点部位或事故易发部位安装监测监控设备进行实时在线展示 的现状部位。
52.构建冶金熔融金属、冶金企业煤气、铸造、铁合金、铜冶炼、有色金属铸造等单 元通用风险辨识与评估清单,形成通用安全风险与隐患违规电子证据信息,覆盖各类型 金属冶炼安全重大风险点运行中的潜在安全风险。
53.通用风险辨识与评估清单,见表2
‑
表15。
54.表2冶金熔融金属安全风险、隐患信息表(高炉基础)
55.表3冶金熔融金属安全风险、隐患信息表(高炉风口及平台)
56.表4冶金熔融金属安全风险、隐患信息表(高炉炉壳)
57.表5冶金熔融金属安全风险、隐患信息表(高炉炉缸)
58.表6冶金熔融金属安全风险、隐患信息表(干渣坑)
59.表7冶金熔融金属安全风险、隐患信息表(铸铁区)
60.表8冶金熔融金属安全风险、隐患信息表(铁水罐、钢水罐、中间包(罐)、渣 罐)罐)
61.表9冶金熔融金属安全风险、隐患信息表(起重机)
62.表10冶金熔融金属安全风险、隐患信息表(混铁炉)表11冶金熔融金属安全风险、隐患信息表(铁水预处理区)
63.表11冶金熔融金属安全风险、隐患信息表(转炉)
64.表12冶金熔融金属安全风险、隐患信息表(电炉)
65.表13冶金熔融金属安全风险、隐患信息表(炉外精炼区)
数、安全生产基础管理动态修正系数、特殊时期指标、高危风险物联网指标、自然环境 等方面分析指标要素与特征值来构建指标体系。
88.固有风险指标重点将高风险物品(如铁水、钢水、熔渣、煤气)、高风险工艺(如 高炉系统、转炉系统、冷却水系统)、高风险设备(如高炉本体、转炉、煤气柜)、高风 险场所(如高炉区域、转炉区域)、高风险作业(如起重机械作业、检修作业等)作为 指标体系的五个风险因子,分析指标要素与特征值,构建固有风险指标体系。
89.表16炼铁单元固有风险指标(高炉坍塌事故风险点)
90.风险管控指标:将企业安全管理现状整体安全程度表征单元高危风险管控频率指 标。安全生产标准化是企业安全管控水平的重要衡量。《企业安全生产标准化基本规范》(gb/t 33000
‑
2016)指出企业根据自身安全生产实际,从目标职责、制度化管理、教 育培训、现场管理、安全风险管控及隐患排查治理、应急管理、事故管理、持续改进8 个要素内容实施标准化管理。
91.风险动态调整指标:安全状态是动态变化的,会随着监测指标、管控状态、外部 自然环境以及事故大数据分析结果而变化,动态风险指标体系重点从高危风险监测特征 指标、安全生产基础管理动态指标、特殊时期指标、高危风险物联网指标、自然环境等 方面分
析指标要素与特征值,构建指标体系参见下表17。
92.表17金属冶炼行业重大安全风险动态指标体系(高炉坍塌事故风险点)
93.固有风险指标计量模型:风险点风险严重度(固有风险)指标,即风险点事故风 险的固有危险指数(h)受下列因素影响:a.设备本质安全化水平;b.监测监控失效率水平(体现工艺风险);c.物质危险性;d.场所人员风险暴露;e.高风险作业危险性。
94.高风险设备(hs),固有危险指数以风险点设备设施本质安全化水平作为赋值依 据,表征风险点生产设备设施防止事故发生的技术措施水平,在申请人建立的工业企业 动态安全评价模型中风险点本质安全化水平指数采用分类、赋值的方式作为hs。
95.此赋值因素繁杂,且赋值的数值最大相差大道9倍,会造成模型计算结果相差 巨
大,不利于分级。
96.因此,经过研究、试算后,申请人认为既方便计算机实现,又不会造成模型计算 结果差不巨大,在原来的原理基础上,首先将赋值类型由原来的13项缩减为5项, 即“危险隔离(替代)”、“故障安全
‑
失误安全”、“故障安全
‑
失误风险”、“故障风险
‑
失 误安全”、“故障风险
‑
失误风险”等来表征设备设施本质化安全水平,取值范围变为 1.1~1.7,具体取值按表18进行。
97.表18风险点固有危险指数(hs)
98.高风险物品(m)主要指具有爆炸性、易燃性、放射性、毒害性、腐蚀性的物品。
99.高风险物品因其特有的物理、化学性质,作用于承载体导致事故的可能性和严重 性都会较大。
100.在申请人建立的工业企业动态安全评价模型中物质的危险系数是按照风险点所 涉及的危险物质在《建筑设计防火规范》(gb50016)中有关“生产的火灾危险性分类
”ꢀ
中所提出的物质进行分类取值,取值见表19。
101.表19物质危险系数赋值表
102.虽然该取值方式是按照物质的火灾危险性来进行分类、取值,只是对具有易燃、 易爆等特性的物质有了取值规则,但是对于涉及到的毒物特性的物质没有取值规则。
103.为了表征风险点所有物质的风险特性,那么就需要对火灾、爆炸、毒性、能量等 特性的所有物质都要进行考虑。
104.申请人参照《危险化学品重大危险源辨识》的理念来表征风险点高风险物品的危 险指数。
105.m值由风险点高风险物品的火灾、爆炸、毒性、能量等特性确定,采用高风险 物品的实际存在量与临界量的比值及对应物品的危险特性修正系数乘积的m值作为分 级指标,根据分级结果确定m值。
106.风险点高风险物品m值的计算方法如下:式中:q1,q2,
…
,q
n
——每种高风险物品实际存在(在线)量(单位:吨)
q1,q2,
…
,q
n
——与各高风险物品相对应的临界量(单位:吨)β1,β2…
,β
n
——与各高风险物品相对应的校正系数。
107.金属冶炼企业风险点涉及的高风险物品主要有铁水、钢水、熔渣、煤气、煤粉等, 根据其危险特性规定了临界量。金属冶炼工艺涉及高风险物品相对应的临界量见表20。
108.表20高风险物品临界量(qn)取值表
109.校正系数β的取值见表21。
110.表21高风险物品校正系数(βn)取值表
111.根据计算出来的α值,按表21确定金属冶炼行业风险点高风险物品的级别,确 定相应的物质指数(m),取值范围1~9。
112.表22风险点高风险物品r值和物质指数(m)的对应关系
113.高风险场所(e)指致害物相对较多或较大能量意外释放的可能性相对较大的场 所。这种场所因其致害物多、能量大,而且意外释放的可能性大,导致对系统的控制难 度增大,一旦发生事故,后果严重。
114.金属冶炼企业涉及的高风险场所主要有高炉区域、转炉区域、铸造区域、煤气泄 漏影响区域等,高风险场所中最重要的就是在该场所内进行操作、检修以及受事故影响 范围内的其他人员,为此,以风险点内暴露人数p来衡量高风险场所的风险指数,高 风险场所(e)按表23取值,取值范围1~9。
115.表23风险点暴露人员指数赋值表
116.高风险工艺(k1)指生产流程中由于工艺本身的状态和属性相对容易发生变化, 从而改变旧有的安全风险平衡体系,引起风险增加,可能导致严重事故发生的工艺过程。
117.这类工艺的特点表现为相对难以控制,系统中能量大,致害物多。
118.影响工艺的特征指标主要是针对工艺的控制系统及其联锁保护系统,而工艺的控 制系统及其联锁保护系统最重要的就是对工艺过程的监测、监控设施,监测、监控设施 的可靠性、完好性直接影响对工艺过程控制的效率和联锁保护的有效性。
119.因此,针对高风险工艺的指标我们采用工艺过程中监测、监控设施的有效性来表 征。
120.由监测监控设施失效率修正系数k1表征:k1=i+l式中:1——监测监控设施失效率的平均值。
121.高风险作业(k2)包括了风险点中涉及的特种作业人员、特种设备操作人员以及 危险作业涉及的人员。因此,以风险点中某个时间段内涉及的所有高风险作业种类数量 来表征高风险人员的危险性系数。
122.由危险性修正系数k2表征:k2i+0.05t式中:t——风险点涉及高风险作业种类数。
123.实施例:以某钢铁企业为例使用该方法进行风险辨识与评估,将炼铁和炼钢作为 整个系统的两个单元进行评估。
124.炼铁单元重大风险评估。
125.1、高危固有风险指标量化:将高炉坍塌事故、熔融金属事故、煤气事故、粉爆 事故等4个风险点作为高危固有风险辨识与评估的重点。
126.(1)高炉坍塌事故风险点。
127.高风险设备设施—高炉本体,以高炉设备设施本质安全化水平作为赋值依据,表 征高炉坍塌事故风险点生产设备设施防止事故发生的技术措施水平,取值范围1.1~1.7。
128.高炉目前运行平稳,本质安全化水平较高,各项安全联锁正常投入使用,按“失 误安全”赋值,取hs=1.3。
129.高风险工艺,高炉坍塌事故风险点高风险工艺有软水密闭循环系统和高炉系统两 个。其中,软水密闭循环系统特征值取冷却壁系统水量监测失效率和炉底系统水量监测 失效率;高炉系统特征值取炉身、炉腰、炉腹冷却壁温度监测失效率、炉基温度监测失 效率、视频监控失效率等。
130.由监测监控设施失效率修正系数k1表征:k1=1+l(1
‑
监测监控设施失效率的平 均值)。
131.高炉工艺比较普遍,较为成熟,各项特征值失效率较低,取k1=1.01。
132.高风险场所,高炉坍塌事故风险点高风险场所主要是高炉区域,以“人员风险暴 露”作为特征值,即根据事故风险模拟计算结果,暴露在高炉坍塌事故影响范围内的所 有人员(包含作业人员及周边可能存在的人员)。
133.以风险点内暴露人数p来衡量,按照表23取值,取值范围1~9。
134.炼铁厂在岗员工133人,高炉当班人数理应介于10~29人之间,取e=5。
135.高风险物品,高炉坍塌事故风险点高风险物品主要是铁水和高温炉料等高温熔融 物。
136.采用高风险物品的实际存在量与临界量的比值及对应物品的危险特性修正系数 乘积的m值作为分级指标,根据分级结果确定m值。
137.依据风险点高风险物品m值的计算方法,高温熔融物临界量q取150t,校正系 数β取1,根据计算出来的m值,按照表22确定金属冶炼行业风险点高风险物品的级 别,确定相应的物质指数(m),取值范围1~9。
138.高炉容积为2600m3,按炉内铁水和高温炉料等高温熔融物在3000t左右估算,对 应m=5。
139.高风险作业,高炉坍塌事故风险点高风险作业主要有危险作业、特种设备操作、 特种作业等,由危险性修正系数k2表征:k2=1+0.05t(t
‑
风险点涉及高风险作业种类 数)。
140.取k2=1.15。
141.风险点典型事故风险的固有危险指数,将风险点危险指数h定义为:h=h
s
mek1k2风险点危险指数为:h1=1.3
×5×5×
1.01
×
1.15=37.75。
142.风险点动态危险指数,将风险点动态危险指数h定义为:h
′
=hk3。
143.其中k3为高危风险动态监测特征指标报警信号修正系数。
144.用高危风险动态监测特征指标报警信号系数(k3)修正风险点固有危险指数(h)。 在线监测项目实时报警分一级报警(低报警)、二级报警(中报警)和三级报警(高报 警)。
145.当在线监测项目达到3项一级报警时,记为1项二级报警;当监测项目达到2项 二级报警时,记为1项三级报警。由此,设定一、二、三级报警的权重分别为1、3、6, 归一化处理后的系数分别为0.1、0.3、0.6,即报警信号修正系数,公式描述为:k3=1+0.1a1+0.3a2+0.6a3式中:k3——高危风险动态监测特征指标报警信号系数a1——黄色报警次数a2——橙色报警次数a3——红色报警次数现实报警次数为动态数据,暂先以理想状况无监测报警的情况下,进行测算,取k3=1, 即h
′
13
=h1=37.75。
146.(2)熔融金属事故风险点。
147.按以上高炉坍塌事故风险点固有危险指数测算过程,对熔融金属事故风险点 的固有危险指数进行测算,结果如下:h2=1.3
×3×3×
1.01
×
1.15=14.8。
148.以理想状况无监测报警的情况下,进行风险点动态危险指数测算,取k3=1,即 h2=h2=14.8。
149.(3)煤气事故风险点。
150.按以上高炉坍塌事故风险点固有危险指数测算过程,对煤气事故风险点的固有危 险指数进行测算,结果如下:h3=1.3
×1×3×
1.01
×
1.2=4.73。
151.考虑到煤气报警器在实际生产中报警比较普遍,取低报3次,中报1次,高报1 次,进行风险点动态危险指数测算,取k3=2.2,即h
′3=h3×
2.2=10.41。
152.(4)粉爆事故风险点。
153.按以上高炉坍塌事故风险点固有危险指数测算过程,对粉爆事故风险点的固有危 险指数进行测算,结果如下:h4=1.3
×5×3×
1.01
×
1.15=22.65。
154.以理想状况无监测报警的情况下,进行风险点动态危险指数测算,取k3=1,即: h4=h4=22.65。
155.(5)炼铁单元固有危险指数。
156.根据安全控制论原理,单元固有危险指数为若干风险点动态危险指数的场所人员 暴露指数加权累计值。
157.h
′
定义如下:式中:h
′
i
——单元内第i个风险点动态危险指数e
i
——单元内第i个风险点场所人员暴露指数f——单元内各风险点场所人员暴露指数累计值n——单元内风险点数。
158.炼铁单元区域内的4个风险点,e1=5,e2=3,e3=3,e4=3,f=14,故:h=37.75
ꢀ×
(5/14)+14.8
×
(3/14)+10.41
×
(3/14)+22.65
×
(3/14)=23.73。
159.初始高危风险管控频率指标量化,单元初始高危风险管控频率指标从企业安全生 产管控标准化程度来衡量,即采用单元安全生产标准化分数考核办法来衡量单元固有风 险初始引发事故的概率。
160.以单元安全生产标准化得分的倒数作为单元高危风险管控频率指标。
161.则计量单元初始高危风险管控频率为:g=100/v式中:g——单元初始高危风险管控频率v——安全生产标准化自评/评审分值炼铁厂安全生产标准化达标等级为二级,暂定取值75分。计算出炼铁单元初始高危风 险管控频率指标(g)为1.33。
162.单元初始高危安全风险评估,将单元高危风险管控频率(g)与固有风险指数聚 合:r0=gh
′
式中:r0——单元初始安全风险值g——单元风险管控频率指数值h——单元固有危险指数值。
163.炼铁单元初始高危安全风险值r0=1.33
×
23.73=31.56。
164.单元现实高危安全风险评估,单元现实风险(rn)为现实风险动态修正指数对 单元初始高危安全风险(r0)进行修正的结果。
165.安全生产基础管理动态指标(b
s
)对单元初始高危安全风险值(r0)进行修正; 特殊时期指标、高危风险物联网指标和自然环境指标对单元风险等级进行调档。
166.单元现实风险(r
n
)为:
r
n
=r0b
s
式中:r
n
——单元现实风险r0——单元初始高危安全风险值b
s
——安全生产基础管理动态指标。
167.安全生产基础管理动态指标主要包括事故隐患评估(i1)、隐患等级(i2)、隐患 整改情况(i3)及生产安全事故指标(i4)等4项指标。b
s
=i1w1+i2w2+i3w3+i4w4168.参考钢厂炼铁单元安全管理基本情况,测算其安全生产基础管理动态指标: b
s
=0.15
×
1+0.15
×
2+0.20
×
0+0.50
×
0.45=0.675。
169.即钢厂炼铁单元现实高危安全风险值:r
n
=31.56
×
0.675=21.30。
170.依据单元安全风险分级标准,钢厂炼铁单元现实高危安全风险等级为iv级。
171.炼钢单元高危风险指标的辨识与评估,将熔融金属事故、煤气事故2个风险点作 为高危固有风险辨识与评估的重点。
172.下面以130t转炉作为测算对象,对各风险点进行评估。
173.按上述炼铁单元重大风险评估的计算过程,对炼钢单元重大风险进行测算评估, 结果如下:h
′
=8.34,g=1.33,r0=11.09,r
n
=18.32。
174.依据单元安全风险分级标准,炼钢单元现实高危安全风险等级也为iv级。
175.应用对象整体风险,同上计算出钢厂所有金属冶炼单元的r
n
见表20。
176.表24钢厂所有金属冶炼单元现实高危安全风险值r
ni
表
177.钢厂金属冶炼单元整体综合风险为:r=max(r
ni
)=24.57按照金属冶炼行业高危风险等级划分标准,钢厂整体风险值为24.57,整体风险等级即 为iv级,预警信号为蓝色。
178.本发明不局限于上述实施方式,对于本领域的普通技术人员来说,在不脱离本发 明原理的前提下,还可以做出若干改进和润饰,这些改进和润饰也视为本发明的保护范 围之内。本说明书未做详细描述的内容属于本领域专业技术人员公知的现有技术。