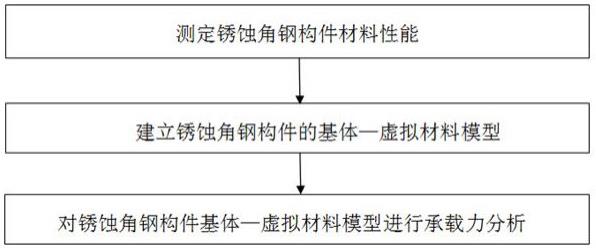
1.本发明所涉及电力工程领域,尤其涉及到一种基于虚拟材料的锈蚀角钢构件承载力评估方法。
背景技术:2.近年来,随着我国经济水平的不断提高和发展,电力工业作为各行各业的发展的基础行业之一,进入了快速发展的时期。高压与超高压输电技术的投用以及一系列有关线路的建成和使用,标志着我国电力工业的发展水平已经进入世界领先的行列。输电线路网络承担着将电力能源将发电端到用电端的传输任务,输电线路网的安全可靠运行是国家经济发展的重要一环,同时也是关乎国家安全的重要事业。作为输电线路的主要组成部分,输电铁塔是整个输电线路中最为重要的电力工程设施,其安全有效的工作是电网系统正常运作的基本保障,输电铁塔的安全可靠运行对于保证整个电力可靠输送至关重要。然而从人民电力一直发展至今,输电铁塔结构发生失稳倒塌的事故频频发生,这极大影响了我国电力供给的稳定性、可靠性和安全性,同时也会对国家经济产生巨大的损失。因而,应加大对输电铁塔的结构安全性的关注度,减少或避免铁塔倒塌事故的发生,才能令输电线路的正常运行加以保障。
3.输电铁塔长期暴露在自然环境中,在其服役过程中,除了受塔线自重、张力以及风雨载荷之外,还会经常性地受到雨、雪、潮湿大气、工业大气等外界因素的影响。这些外界的影响因素长期作用于铁塔结构,加速输电铁塔构件的锈蚀现象,会使得铁塔构件腐蚀破损、承载能力下降,导致铁塔结构局部出现缺陷,进而使得铁塔的整体结构的受力性能下降。除去人为无法控制的极端天气或其他自然灾害的影响,比如台风或暴雪,这种极端环境会令塔线结构的外载荷大幅上升,使铁塔结构产生严重的变形,甚至出现倒塔的情况;在正常的工况下,外界因素则会令构件出现锈蚀等缺陷,令角钢构件材性变化、穿孔、截面削弱甚至断裂等,从而降低输电铁塔的结构安全性、可靠性,影响铁塔的服役寿命。出于对输电铁塔安全性的考虑,应有针对性的对其发生锈蚀的构件进行检测评估,以此为指导对其采取合理的应对措施,确保输电铁塔的正常使用,减少输电铁塔破坏或者倒塌事故发生。
4.根据以上分析,为了确保输电铁塔安全可靠的工作,对现有铁塔结构的锈蚀情况进行检测,分析已锈蚀构件的蚀余承载力,研究铁塔结构在服役期中的锈蚀现状显得很有必要。以科学、实用的方法对铁塔锈蚀构件的承载力进行评估,能为铁塔的维修改造工作提供一定的指导,对提高输电线路的安全等级,保障电网运行有着积极作用。
技术实现要素:5.本发明要解决的技术问题是提供一种基于虚拟材料的锈蚀角钢构件承载力评估方法,该方法是基于材性试验,通过在基体材料表面添加虚拟材料层,对锈蚀构件进行仿真分析,考虑锈蚀作用对构件表面性能影响的一种评估方法,该方法主要适用于对输电铁塔上的锈蚀构件进行承载力评估。
6.为解决上述技术问题,本发明所采取的技术方案是:一种基于虚拟材料的锈蚀角钢构件承载力评估方法,其特征在于包括如下步骤:依据锈蚀角钢构件的材料性能参数,建立锈蚀角钢构件的基体—虚拟材料模型,其中,所述基体为原金属,所述虚拟材料为锈蚀部分的虚拟材料层;对锈蚀角钢构件的基体—虚拟材料模型进行屈曲分析,得到所述锈蚀角钢构件的基体—虚拟材料模型的载荷位移曲线,根据载荷位移曲线评估所述锈蚀角钢构件承载力。
7.对上述方案作进一步说明,所述锈蚀角钢构件的材料性能参数通过如下方法获得:对锈蚀角钢构件进行材性试验得到锈蚀角钢构件名义应力应变曲线,依据所述名义应力应变曲线,确定锈蚀角钢构件的材料性能参数。
8.对上述方案作进一步说明,所述对锈蚀角钢构件进行材性试验得到锈蚀角钢构件名义应力应变曲线包括:对锈蚀角钢构件切割为标准拉伸试样,对标准拉伸试样进行常温金属拉伸试验,得到其名义应力应变曲线。
9.对上述方案作进一步说明,所述锈蚀角钢构件的材料性能参数包括杨氏模量、泊松比和/或屈服强度。
10.对上述方案作进一步说明,在建立锈蚀角钢构件的基体—虚拟材料模型之前还包括:在锈蚀角钢构件的材料性能参数的基础上,建立用于有限元分析的二维基体—虚拟材料模型,设定所述二维基体—虚拟材料模型中的虚拟材料层的厚度,并对所述二维基体—虚拟材料模型进行拉伸分析,得到所述二维基体—虚拟材料模型的名义应力应变曲线,通过对比所述二维基体—虚拟材料模型的名义应力应变曲线与所述锈蚀角钢构件名义应力应变曲线,确定虚拟材料层的厚度。
11.对上述方案作进一步说明,所述基体-虚拟材料模型中基体与虚拟材料层厚度的比值为9:1。
12.对上述方案作进一步说明,所述建立锈蚀角钢构件的基体—虚拟材料模型包括:以金属层为基体,在所述基体表面添加所述虚拟材料层建立角钢模型,设定虚拟材料层的厚度,以及虚拟材料层杨氏模量、泊松比、屈服强度,建立锈蚀角钢构件的基体—虚拟材料模型。
13.对上述方案作进一步说明,所述屈曲分析包括:对锈蚀角钢构件的基体—虚拟材料模型进行特征值屈曲分析后,将所得一阶模态1%的变形量作为初始缺陷,施加到锈蚀角钢构件的基体—虚拟材料模型上;使用弧长法对所述基体—虚拟材料模型进行非线性屈曲分析,得到锈蚀角钢构件的载荷位移曲线,依据所述载荷位移曲线评估所述锈蚀角钢构件的承载力。
14.对上述方案作进一步说明,所述特征值屈曲分析包括:以基体—虚拟材料模型的端面的形心点为第二耦合点,对第二耦合点施加位移载荷约束,对锈蚀角钢构件的基体—虚拟材料模型进行特征值屈曲分析。
15.对上述方案作进一步说明,所述屈曲分析还包括:计算所述载荷位移曲线线性段的曲线斜率获得所述锈蚀角钢构件的刚度。
16.与现有常用的对于锈蚀构件的评估方法对比,本发明具有以下优点:(1)本发明是通过建立基体—虚拟材料模型来模拟锈蚀后角钢构件的材料特性,解决了在对锈蚀构件进行仿真时,通过改变整体材料的屈服强度等力学特性以表征锈蚀对
材料的影响。因此,本发明基于锈蚀件内部材料不被影响的观测结果进行建模,能对锈蚀构件的蚀余承载力进行更有效仿真评估。
17.(2)本发明首先对锈蚀构件进行取样并测试其材料特性,并以此为依据调整虚拟材料的材料特性参数,进行分析。因此本发明准确度高、适用范围广,同时成本低、实用性强。
附图说明
18.下面结合附图和具体实施方式对本发明作进一步详细的说明。
19.图1是本发明中评估方法的流程图;图2为锈蚀角钢构件边缘锈蚀部分截面金相图;图3为锈蚀角钢构件基体部分截面金相图;图4和图5分别为锈蚀角钢构件拉伸试验试件端面和长度方向视图;图6为基体—虚拟材料模型;其中:1、虚拟材料,2、基体;图7为基体—虚拟材料模型的网格划分示意图;图8为基体—虚拟材料模型的边界条件示意图;图9为q235材料模型与基体—虚拟材料模型的应力应变曲线图;图10为q235材料与基体—虚拟材料建立的角钢构件模型对比图;图11为q235材料与基体—虚拟材料角钢模型的载荷—位移曲线图。
具体实施方式
20.下面结合附图和具体实施方式对本发明作进一步详细的说明。
21.本发明为一种能对输电铁塔中锈蚀角钢构件的蚀余承载力进行评估的方法。该方法以锈蚀构件的材料拉伸试验为基础,结合金属材料锈蚀后截面的特征,设计了虚拟材料,考虑建立材料锈蚀层的基体—虚拟材料模型来表征锈蚀后金属材料的力学性能,并以此对锈蚀后角钢构件力学性能进行评估的一种方法。
22.如附图1所示,基于虚拟材料的锈蚀角钢构件承载力评估方法,包括以下步骤:第一步:测定锈蚀构件的材料性能。
23.为了得到锈蚀后构件的材料性能,首先需要对进行评估的锈蚀角钢构件,进行材性试验,如附图4和5所示,可采用如图4、图5方式对取样的锈蚀构件进行切割,再加工成标准拉伸试样。参考的国家标准《gb/t 228-2002金属材料室温拉伸试验方法》,对所制作的拉伸试样进行常温金属拉伸试验,得到锈蚀角钢构件名义应力应变曲线。通过对名义应力应变曲线进行进一步的分析,可以得到锈蚀后金属材料的杨氏模量、泊松比、屈服强度以及抗拉强度等力学性能指标,从而确定角钢构件锈蚀后的材料性能参数。
24.第二步:建立锈蚀角钢构件的基体—虚拟材料模型。
25.锈蚀角钢构件的基体—虚拟材料模型包括以金属层为基体,在基体表面添加虚拟材料层。基体—虚拟材料模型中需要设定虚拟材料层的厚度,以及虚拟材料层杨氏模量、泊松比、屈服强度等材料性能参数,其中材料形成参数由第一步中材性试验得到,下面来说明确定虚拟材料层的厚度的方法。
26.在建立锈蚀角钢构件的基体—虚拟材料模型之前,先建立二维基体—虚拟材料模
型,二维基体—虚拟材料模型如图6、图7所示,该模型以原金属为基体,在其表面加上虚拟材料层。通过设置不同虚拟材料层的厚度,对该二维基体—虚拟材料模型进行拉伸分析,并对比分析不同虚拟材料层厚度的二维基体—虚拟材料模型的名义应力应变曲线与锈蚀角钢构件材性试验的名义应力应变曲线,观察两者近似程度,从而确定虚拟材料层的厚度。
27.具体包括,在锈蚀角钢构件的材料性能参数的基础上,建立用于有限元分析的二维基体—虚拟材料模型,设定二维基体—虚拟材料模型中的虚拟材料层的厚度,并对二维基体—虚拟材料模型进行拉伸分析,得到二维基体—虚拟材料模型的名义应力应变曲线,通过对比所述二维基体—虚拟材料模型的名义应力应变曲线与所述锈蚀角钢构件名义应力应变曲线,确定虚拟材料层的厚度。其中设定所述二维基体—虚拟材料模型中的虚拟材料层的厚度可以为设定不同的厚度,通过设定不同的虚拟材料层的厚度,可以使得二维基体—虚拟材料模型的名义应力应变曲线与所述锈蚀角钢构件名义应力应变曲线最接近,从而使二维基体—虚拟材料模型更接近实际的锈蚀角钢构件,将二维基体—虚拟材料模型的名义应力应变曲线与所述锈蚀角钢构件名义应力应变曲线最接近的二维基体—虚拟材料模型对应的厚度确定为虚拟材料层的厚度。其中,拉伸分析过程是对基体—虚拟材料模型施加固定载荷,进行静力学分析,在分析中增加1000个载荷步,利用不同载荷步对应的变形,绘制材料的载荷位移曲线。在上述的非线性屈曲分析和拉伸分析中,拉伸试件在拉伸的过程中,一般经历弹性、屈服、强化、颈缩4个阶段。
28.此时,基体—虚拟材料层模型的力学性能与试验所得的锈蚀构件相近,此时认为,调试后的虚拟材料能有效表征材料锈蚀层的力学特性,可以利用该二维基体—虚拟材料模型中基体与虚拟材料的厚度比例,来建立锈蚀角钢构件的基体—虚拟材料模型进行下一步的力学性能分析。
29.第三步:对锈蚀角钢构件基体—虚拟材料模型进行承载力分析。
30.对锈蚀角钢构件的基体—虚拟材料模型进行屈曲分析,得到所述锈蚀角钢构件的基体—虚拟材料模型的载荷位移曲线,根据载荷位移曲线评估所述锈蚀角钢构件承载力。
31.对锈蚀角钢构件的基体—虚拟材料模型进行屈曲分析。根据所得载荷位移曲线,利用材料力学中计算过程,对所得数据进行处理后,能有效评估构件的蚀余承载力、蚀余刚度以及蚀余极限拉力等力学性能指标。
32.具体地,屈曲分析包括:对锈蚀角钢构件的基体—虚拟材料模型进行特征值屈曲分析后,将所得一阶模态1%的变形量作为初始缺陷,施加到锈蚀角钢构件的基体—虚拟材料模型上;使用弧长法对所述基体—虚拟材料模型进行非线性屈曲分析,得到锈蚀角钢构件的载荷位移曲线,依据所述载荷位移曲线评估所述锈蚀角钢构件的承载力。
33.在上述步骤中,对基体—虚拟材料模型进行特征值屈曲分析和非线性屈曲分析,均是利用有限元软件对材料变形进行模型,获取材料载荷位移曲线。非线性屈曲分析过程是,首先对基体—虚拟材料模型施加载荷,进行静力学分析,逐步地在该模型上,按照约束施加一个恒定的荷载增量,直到解开始发散为止。尤其重要的是,要一个足够小的荷载增量,来使荷载达到预期的临界屈曲荷载。
34.本发明的原理说明如下:对于锈蚀引起的钢构件力学性能变化的作用机理目前并未由统一的认识,现有存
在认为是锈蚀作用导致了钢构件的平均截面积减小以及锈坑引起的应力集中的影响,也有研究认为锈蚀改变了钢结构的物理、化学性能。影响金属力学性能的因素可分为包括金属晶格类型、晶粒大小等的内在因素,以及包括温度、应变速率和应力状态等的外在因素。由于本评估方法主要以仿真的方法对构件的力学性能进行评估,因而主要关注锈蚀对金属内在因素的影响。根据有关对锈蚀金属材料的金相分析试验研究表明,锈蚀的钢构件内部的金属组织未受到锈蚀作用的影响,其金相组织与锈蚀前并无差异,如附图2和3所示。因而认为金属锈蚀后材料性能的变化,主要来源于其表面锈蚀层的影响。因此本发明通过建立基体—虚拟材料模型来模拟锈蚀后角钢构件的材料特性,解决了在对锈蚀构件进行仿真时,通过改变整体材料的屈服强度等力学特性以表征锈蚀对材料的影响。本发明基于锈蚀件内部材料不被影响的观测结果进行建模,能对锈蚀构件的蚀余承载力进行更有效仿真评估。
35.下面通过一个更具体的实施例,对本发明加以说明。
36.实施例一:以肢宽为100mm、肢厚为10mm的等边角钢为研究对象,采取两端铰接的约束形式,取其长细比λ为100。对比研究未受锈蚀的角钢模型与锈蚀模型的受压承载力。
37.第一步,选定角钢材质为q235钢,参考的标准《gb/t 228-2002金属材料室温拉伸试验方法》,对锈蚀后的q235钢材料参数进行测定。
38.未受锈蚀时,角钢整体材料均为q235钢;对于锈蚀模型,假定其表面由于金属锈蚀的影响,产生锈蚀层,该锈蚀层占肢厚的10%。锈蚀后的材料性能设定如表1。
39.表1 锈蚀层的材料性能第二步,建立二维的基体—虚拟材料模型,见附图6和7。对于该模型,虚拟材料与基体材料的厚度分别占材料总厚度的10%、90%,如表2所示。该材料由于锈蚀作用导致表层材料性能下降,该锈蚀层通过厚度占比为10%的虚拟材料层(附图6中的区域1)进行模拟,同时材料内部的性能不变,因此保持与原材料一致且厚度占比为90%(附图6中的区域2)。在进行对二维的基体—虚拟材料模型拉伸分析时,通过对材料一端进行固定,另一端施加拉伸载荷实现。考虑到材料两端受集中力作用时,依据圣维南原理,材料两端受力部分会出现应力集中的现象,影响分析的精度。为尽可能消除应力集中现象的影响,分析中令材料的长宽比为10:1,同时为避免集中力直接施加到材料的端面,将材料的端面与端面的中点进行运动耦合,把端面中点作为第一耦合点,通过第一耦合点完成拉伸载荷的施加,见附图8。
40.在不考虑锈蚀层的情况下,建立q235钢的二维模型,采用与二维的基体—虚拟材料模型类似的约束方式,如图8所示,对比研究两种模型的材性差异。通过对第一耦合点提取位移、载荷数据,分别绘制q235材料模型与基体—虚拟材料模型的载荷位移曲线,在进行数据处理后,得到两模型的名义应力应变曲线,对比见附图9。由图可知q235材料模型的屈
服强度为270mpa,在虚拟材料层的影响下,材料的屈服强度下降为250mpa;材料应力应变曲线的斜率并未发生较大变化,即材料的模量所受影响不大。
41.第三步,在进行了对材料性能的分析后,分别基于两种材料建立角钢模型,对比分析构件的受压承载力。附图10分别为基于q235材料模型与基体—虚拟材料模型建立的角钢构件模型。以角钢其中一个端面的形心点为第二耦合点,对角钢端面进行耦合,对该耦合点施加位移载荷,对角钢构件模型进行特征值屈曲分析。将屈曲分析所得的一阶模态1%的变形量作为构件的初始缺陷施加在模型上,再使用弧长法对构件模型进行非线性屈曲分析。通过对该耦合点的进行数据提取,绘制模型的载荷位移曲线,如图11,整理得到表3。
42.由表3可知,以基体—虚拟材料建立的锈蚀模型与未锈蚀模型相比,角钢构件的受压极限承载力下降约8%,同时由其载荷位移曲线的斜率下降可知,锈蚀构件的刚度也受到一定程度的削弱。同时若结合锈蚀构件的材料试验结果,调整所用虚拟材料层的厚度、屈服强度、刚度等参数,能更有效对锈蚀构件的承载力性能进行准确评估。
43.本发明通过建立基体—虚拟材料模型来模拟锈蚀后角钢构件的材料特性,解决了在对锈蚀构件进行仿真时,通过改变整体材料的屈服强度等力学特性以表征锈蚀对材料的影响。本发明基于锈蚀件内部材料不被影响的观测结果进行建模,能对锈蚀构件的蚀余承载力进行更有效仿真评估。