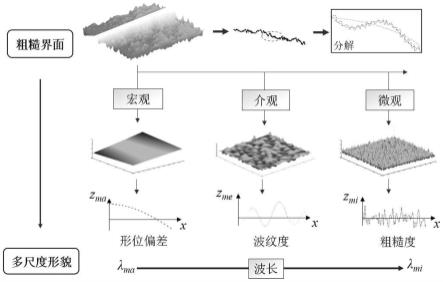
1.本发明涉及典型非连续界面接触分析领域,具体是一种考虑宏微观形貌特征的界面切向接触刚度预测方法。
背景技术:2.非连续界面广泛存在于众多工程领域之中,如螺栓连接、发动机叶片与轮盘连接、机床导轨副连接等。由于制造与工艺限制,接触面是粗糙的且界面的表面形貌包含多尺度轮廓信息,例如宏观尺度上拓扑结构的形位偏差,介观尺度上表面的波纹度,以及微观尺度上的粗糙度等。这些宏观、介观和微观形貌作为界面的几何属性,作用在装配体非连续界面上相互耦合作用,共同决定了装配体间的切向接触特性。而切向刚度直接影响界面接触的黏-滑行为、界面磨损、界面润滑以及整个结构的动力学动态响应等。因此,粗糙界面的切向接触刚度对于界面力学性能和动力学响应至关重要。
3.目前针对单一尺度下的界面接触研究较多,如宏观尺度下基于赫兹理论的弹性接触研究,微观尺度下的基于统计学方法和分形理论的粗糙面接触研究。然而,由于界面各个尺度形貌信息耦合在一起,使得界面切向接触作用机理复杂。单一针对某一尺度下的接触模型难以较好地表征实际非连续界面切向接触刚度,而且多尺度耦合形貌对界面接触的影响尚没有清楚认识,。因此,有必要提出一种考虑界面多尺度形貌的界面切向接触力学模型,对界面切向刚度进行预测。
技术实现要素:4.本发明实施例的目的在于提供一种考虑宏微观形貌特征的界面切向接触刚度预测方法,考虑界面宏观形位制造偏差、介观和微观形貌参数对界面切向接触的耦合作用,预测界面在给定法向载荷下的切向接触刚度,以解决上述技术背景中的问题。
5.本发明实施例是这样实现的,一种考虑宏微观形貌特征的界面切向接触刚度预测方法,该方法包括如下步骤:
6.步骤1:建立单一微观尺度下的微凸体法向接触力学模型,且两个粗糙面接触等效为一个刚性平面和一个粗糙面之间的接触,粗糙面均匀分布着微凸体,微凸体等效半径为r、高度z、微凸体法向变形量ω,以及刚性平面与粗糙面表面轮廓平均高度线之间的间距d;
7.步骤2:基于统计学求和方法将高度随机分布的微凸体的法向载荷与位移关系转变为界面整体法向位移和界面法向载荷之间的关系,建立仅考虑微观形貌的界面法向接触模型;
8.步骤3:将界面宏观形状和位置偏差用线性形状函数sv表征,包括角度偏差和位置偏差;
9.步骤4:将界面宏观形位偏差转变为粗糙界面微凸体高度基准线与等效刚性平面之间的距离变动,并记为d;
10.步骤5:将界面的介观形貌表征为波纹状的形状函数,耦合到粗糙界面微凸体高度
基准线与等效刚性平面之间的距离函数中,以此建立含宏观偏差和介观形貌特征的多尺度粗糙界面法向接触力学模型;
11.步骤6:将单一微凸体切向黏滑行为用非线性弹簧单元来表征;
12.步骤7:将微凸体切向力与位移关系进行无量纲化处理,用统计学求和方法得到基于微凸体切向临界滑移力分布函数表征的整个界面切向力表达方程;
13.步骤8:基于步骤5中已建立的多尺度粗糙界面法向接触力学模型和库伦定律求解界面微凸体切向临界滑移力分布函数ρ
*
(φ);
14.步骤9:通过步骤8中得出的界面微凸体切向临界滑移力分布函数,带入到步骤7中的界面切向力表达方程中,得到含多尺度形貌表征的粗糙界面切向接触力学模型;
15.步骤10:在给定界面法向载荷下,通过施加界面切向位移,得到切向接触力,基于切向力-位移关系得到不同切向位移下的切向接触刚度。
16.本发明的进一步改进在于,在步骤1中,所述微观尺度下的微凸体法向接触力学模型包括微凸体随法向变形量变化的弹性、弹塑性以及塑性阶段变形力关系;
17.其中微凸体弹性变形阶段的力fe、压强pe以及接触面积ae之间的关系表示为:
[0018][0019]
微凸体纯弹性变形临界变形量如下:
[0020][0021]
当法向载荷足够大时,微凸体就会发生全塑性变形,相应的接触力f
p
、接触压力p
p
以及接触面积a
p
如下所示:
[0022]fp
=2πhrω,q
p
=2πrω,p
p
=h
ꢀꢀꢀꢀ
(3);
[0023]
椭圆曲线在弹塑性阶段和塑性阶段的临界点ω2处满足连续性条件和光滑性条件,具体表达式如下:
[0024][0025]
其中p2是在点ω=ω2时的临界接触压力,c1和c2是弹塑性阶段的关系式的常系数,可以表示如下:
[0026][0027][0028]
接触面积a
ep
表达式用指数函数进行表示,如下:
[0029][0030]
弹塑性混合阶段的接触力关系可以表示如下:
[0031]fep
=p
ep
×aep
ꢀꢀꢀꢀꢀꢀꢀꢀꢀꢀꢀ
(9);
[0032]
将式(1)、(3)和(9)相结合,能够得到单个微凸体从弹性阶段到全塑性阶段的法向接触力表达式。
[0033]
本发明的进一步改进在于,在步骤2中,将界面所有微凸体接触力在整个名义接触区间内进行积分,得到整个接触面的法向接触力;微凸体高度概率分布函数φ
*
(z
*
)如下所示:
[0034][0035]
概率密度函数φ
*
(z
*
)可以划分为纯弹性区、弹塑性区以及全塑性区;
[0036]
通过将纯弹性区、弹塑性区以及全塑性区三个变形区的所有微凸体法向变形力相加,可以获得接触界面总的接触力n,具体表达式如下所示:
[0037][0038]
通过公式(11),建立了界面含微观形貌的法向接触基本模型。
[0039]
本发明的进一步改进在于,在步骤3中,由于界面长度和宽度方向的宏观角度偏差α和β的存在以及沿界面法向方向的位置偏差δz的存在,表面轮廓基准线会偏离名义值,表面轮廓基准线与等效刚性平面之间的距离h会发生改变,这里定义界面形状函数sv(x,y)如下:
[0040]
sv(x,y)=-xβ+yα+δz
ꢀꢀꢀꢀꢀꢀꢀ
(13)。
[0041]
本发明的进一步改进在于,在步骤4中,参数d可以表达如下:
[0042]
d(x,y)=d
0-sv(x,y)
ꢀꢀꢀꢀꢀꢀꢀꢀꢀꢀꢀ
(14);
[0043]
通过将式(14)代入式(11)中,得到含宏观形位偏差特性的粗糙面接触力学模型,表达式如下:
[0044][0045]
本发明的进一步改进在于,在步骤5中,介观尺度形貌波长小于宏观尺度形位偏差的波长,且大于微观尺度粗糙形貌的波长,这里用fv(x)表示介观形貌,将其耦合到式(14)的参数d中,得到d的表达式如下:
[0046]dv
(x,y)=d
0-sv(x,y)-fv(x,y)
ꢀꢀꢀꢀꢀꢀꢀꢀꢀꢀ
(16);
[0047]
将上式代入到式(11)中,得到含宏观和介观形貌特征的界面粗糙接触法向力学模型,具体表达式如下:
[0048][0049]
本发明的进一步改进在于,在步骤6中,切向黏滑表示如下:
[0050][0051]
由于微凸体的高度z不同,所受法向载荷不同,导致微凸体发生滑移时的切向力qi不同;当微凸体切向力ti小于临界滑移力qi时,随着δ的增加,ti也相应增加;当ti达到临界滑移力qi时,随着δ的增加,ti保持不变;当微凸体数量足够多时,界面切向力可以表示如下:
[0052][0053]
本发明的进一步改进在于,在步骤7中,通过消去式(19)中的参数k,将参数重新定义为如下:
[0054][0055]
将式(20)代入(19)中,界面切向力可表示为:
[0056][0057]
本发明的进一步改进在于,在步骤8中,当切向位移δ足够大时,切向力t将达到最大值为:
[0058][0059]
基于库伦摩擦定律,滑移状态下法向力与切向力之间关系如下所示:
[0060]
t
max
=μn
ꢀꢀꢀꢀꢀꢀꢀꢀꢀꢀꢀ
(23);
[0061]
综合公式(17)、(22)和(23),切向临界滑移力分布函数ρ
*
(φ)表示如下:
[0062]
本发明的进一步改进在于,在步骤10中,切向接触刚度的计算公式如下:
[0063]
[0064]
与现有技术相比,本发明实施例的有益效果:
[0065]
本发明提供的粗糙界面切向接触刚度预测方法,考虑了界面的宏观形状和位置偏差、介观形貌和微观粗糙特征对界面切向刚度的影响,将不同尺度下的形貌耦合到接触力学模型中,建立了界面多尺度形貌几何量与界面切向接触力学特征物理量之间的映射关系,解决了含多尺度形貌参数下界面切向刚度难以表征的问题;
[0066]
本发明提供的界面切向刚度预测方法,内含多尺度形貌表征的界面法向接触力学模型,可以用于表征粗糙界面法向接触刚度等;
[0067]
本发明提供的界面接触切向刚度预测方法,具有普适性,可用于各种含非连续界面的结构中,如航空发动机枞树型叶片-轮盘装配界面分析、燕尾型叶片切向接触刚度分析、叶片的叶冠接触界面分析以及众多螺栓连接界面的切向接触刚度分析等。
附图说明
[0068]
图1为本发明实施例中典型粗糙界面形貌示意图。
[0069]
图2为本发明实施例中粗糙面等效接触示意图。
[0070]
图3为本发明实施例中粗糙界面微凸体高度分布示意图。
[0071]
图4为本发明实施例中含宏观形位偏差的粗糙面形貌示意图。
[0072]
图5为本发明实施例中含介观形貌特征的粗糙面形貌示意图。
[0073]
图6为本发明实施例中基于非线性弹簧单元表征的粗糙界面微凸体切向接触示意图。
[0074]
图7为本发明实施例中含多尺度形貌特征的粗糙界面切向接触力学建模流程。
[0075]
图8为本发明实施例中随切向位移变化的界面切向接触刚度曲线图。
具体实施方式
[0076]
为了使本发明的目的、技术方案及优点更加清楚明白,以下结合附图及实施例,对本发明进行进一步详细说明。应当理解,此处所描述的具体实施例仅仅用以解释本发明,并不用于限定本发明。
[0077]
以下结合具体实施例对本发明的具体实现进行详细描述。
[0078]
请参阅图1-图8,本发明实施例提供的一种考虑宏微观形貌特征的界面切向接触刚度预测方法,本发明实施例中所描述的对象是典型粗糙界面,可以看到,随着形貌波长不同,可以划分为宏观形位偏差、介观波纹度以及微观粗糙度等,基于界面多尺度形貌特征,建立含多尺度形貌表征的粗糙界面切向接触力学刚度模型,该方法包括如下步骤:
[0079]
步骤1:建立单一微观尺度下的微凸体法向接触力学模型,如图2所示,且两个粗糙面接触等效为一个刚性平面和一个粗糙面之间的接触,粗糙面均匀分布着微凸体,还包括微凸体等效半径为r、高度z、微凸体法向变形量ω,以及刚性平面与粗糙面平均高度线之间的间距d,其中高度z呈高斯分布;该模型包含了微凸体随法向变形量变化的弹性、弹塑性以及塑性阶段变形力关系;
[0080]
具体地,根据赫兹接触理论,微凸体弹性变形阶段的力fe、压强pe以及接触面积ae之间的相互可以表示为:
[0081][0082]
微凸体纯弹性变形临界变形量如下:
[0083][0084]
其中e等效弹性模量,k=0.45+0.41ν,h是两接触面中较软材料的硬度;当法向载荷足够大时,微凸体就会发生全塑性变形,相应的接触力f
p
、接触压力p
p
以及接触面积a
p
如下所示:
[0085]fp
=2πhrω,a
p
=2πrω,p
p
=h
ꢀꢀꢀꢀ
(3);
[0086]
发生全塑性变形时的初始法向变形量定义为ω2=110ω1,当法向变形从纯弹性增加到全塑性阶段时,也即ω1《ω《ω2,微凸体会发生弹塑性混合变形,这里采用低阶椭圆函数插值法以弹性阶段和塑性阶段临界点为边界条件进行差值;椭圆曲线在弹塑性阶段和塑性阶段的临界点ω2处满足连续性条件和光滑性条件,具体表达式如下:
[0087][0088]
其中p2是在点ω=ω2时的临界接触压力,c1和c2是弹塑性阶段的关系式的常系数,可以表示如下:
[0089][0090][0091]
其中p1是在点ω=ω1时的临界接触压力;
[0092]
接触面积a
ep
表达式用指数函数进行表示,如下:
[0093][0094]
弹塑性混合阶段的接触力关系可以表示如下:
[0095]fep
=p
ep
×aep
ꢀꢀꢀꢀꢀꢀꢀꢀꢀꢀꢀꢀ
(9);
[0096]
将式(1)、(3)和(9)相结合,便可得到单个微凸体从弹性阶段到全塑性阶段的法向接触力表达式。
[0097]
步骤2、基于统计学求和方法将高度随机分布的微凸体的法向载荷与位移关系转变为界面整体法向位移和界面法向载荷之间的关系,建立仅考虑微观形貌的界面法向接触模型;
[0098]
具体地,如图3所示,粗糙界面微凸体高度分布,将界面所有微凸体接触力在整个名义接触区间内进行积分,可以得到整个接触面的法向接触力等;这里微凸体高度分布假定为服从高斯正态分布,高度概率分布函数φ
*
(z
*
)如下所示:
[0099]
[0100]
其中,σs是微凸体高度分布的标准差,σ是粗糙面高度的标准差,z
*
=z/σ是无量纲化的微凸体高度,β=ησr是粗糙度参数,η是微凸体在界面上的分布密度;在一定的分离距离d下,粗糙面的微凸体会发生变形,相应的接触力f大小取决于微凸体高度。根据微凸体高度大小,概率密度函数φ
*
(z
*
)可以划分为三个区域,分别是纯弹性区、弹塑性区以及全塑性区,如图3所示,当微凸体高度z》d+ω2时,倾向于发生塑性变形,而当高度z《d+ω1时则容易产生弹性变形;
[0101]
通过将纯弹性区、弹塑性区以及全塑性区三个变形区的所有微凸体相加,可以获得接触界面总的接触力n,具体表达式如下所示:
[0102][0103]
其中a0表示名义接触区域面积,上标*表示经过σ无量纲化后的参数,通过公式(11),建立了界面含微观形貌的法向接触基本模型;
[0104]
具体地,式(11)中的微观形貌参数η、σ和r可以通过实际轮廓测量数据得到,具体并如下:
[0105][0106]
式中e[.]代表着计算数据的数学期望;当接触面轮廓是各向异性时,上标max和min表示在正交方向上最大和最小轮廓高度斜率所对应的轮廓数据,上标s1、s2和comb分别表示两个接触面以及等效后的粗糙面,m0、m2和m4分别是粗糙轮廓的零阶、二阶和四阶谱矩。
[0107]
步骤3:将界面宏观形状和位置偏差用线性形状函数sv表征,包括角度偏差和位置偏差,如图4所示,由于宏观角度θ和位置δz的存在,表面轮廓基准线会偏离名义值,表面轮廓基准线与等效刚性平面之间的距离h会发生改变,这里定义界面的宏观偏差为关于接触界面长度和宽度方向的函数sv(x,y):
[0108]
步骤4:将界面宏观形位偏差转变为粗糙界面微凸体高度基准线与等效刚性平面之间的距离变动,参数d可以表达如下:
[0109]
d(x,y)=d
0-sv(x,y)
ꢀꢀꢀꢀꢀꢀꢀ
(14);
[0110]
式中d0是微凸体高度基准线与等效刚性平面之间距离d的名义值,通过将式(14)代入式(11)中,得到含宏观形位偏差特性的粗糙面接触力学模型,表达式如下:
[0111][0112]
步骤5:将界面的介观形貌表征为波纹状的形状函数,耦合到粗糙界面微凸体高度基准线与等效刚性平面之间的距离函数中,以此建立含宏观偏差和介观形貌特征的多尺度粗糙界面法向接触力学模型;
[0113]
具体地,如图5所示,介观尺度形貌波长小于宏观尺度形位偏差的波长,且大于微观尺度粗糙形貌的波长,这里用fv(x)表示介观形貌,相应的,将fv(x)代入式(14)的参数d中,得到d的表达式如下:
[0114]dv
(x,y)=d
0-sv(x,y)-fv(x,y)
ꢀꢀꢀꢀꢀꢀꢀꢀꢀꢀꢀ
(16);
[0115]
将上式代入到式(11)中,得到含宏观和介观形貌特征的界面粗糙接触法向力学模型,具体表达式如下:
[0116][0117]
步骤6:将单一微凸体切向黏滑行为用非线性弹簧单元来表征;
[0118]
具体地,如图6所示,切向黏滑表示如下:
[0119][0120]
由于微凸体的高度z不同,所受法向载荷不同,导致微凸体发生滑移时的切向力qi不同;当微凸体切向力ti小于临界滑移力qi时,随着δ的增加,ti也相应增加;当ti达到临界滑移力qi时,随着δ的增加,ti保持不变;当微凸体数量足够多时,界面切向力可以表示如下:
[0121][0122]
步骤7:将微凸体切向力与位移关系进行无量纲化处理,用统计学求和方法得到基于微凸体切向临界滑移力分布函数表征的整个界面切向力表达方程;
[0123]
具体地,首先需要消去式(19)中的参数k,这里采用无量纲化方法,将参数重新定义为如下:
[0124][0125]
其中δ
*
是无量纲化的切向位移,φ是无量纲化的临界滑移力,ρ
*
(φ)是滑移力φ的分布函数,σ是粗糙面轮廓标准差,将式(20)代入(19)中,界面切向力可表示为:
[0126][0127]
步骤8:基于步骤5中已建立的多尺度粗糙界面法向接触力学模型和库仑定律求解界面微凸体切向临界滑移力分布函数;
[0128]
具体地,当δ
*
→
∞时,上式的右侧第二项将趋近于零,此时所有的微凸体将发生滑移接触,同时,切向力t将达到最大值:
[0129][0130]
基于库伦摩擦定律,滑移状态下法向力与切向力之间关系如下所示:
[0131]
t
max
=μn
ꢀꢀꢀꢀꢀꢀꢀꢀꢀꢀꢀ
(23);
[0132]
其中μ是摩擦系数,n是非连续界面法向接触载荷;
[0133]
比较公式(17)、(22)和(23),切向临界滑移力分布函数ρ
*
(φ)可以表示如下:
[0134][0135]
步骤9:将式(24)中的微凸体切向临界滑移力分布函数代入式(21)中的界面切向力方程,得到含多尺度形貌表征的粗糙界面切向接触力学模型,表达式如下:
[0136][0137]
其中φe和φ
p
分别等于无量纲化的变量和粗糙面切向接触力方程式是关于切向位移δ
*
的分段函数,在给定切向位移后,可以根据该模型得到切向力t的值以及计算处于不同接触状态下的各个切向力成分。
[0138]
步骤10:在给定界面法向载荷下,通过施加界面切向位移,得到切向接触力,基于切向力-位移关系得到不同切向位移下的切向接触刚度,计算公式如下:
[0139][0140]
上述建立多尺度形貌界面切向接触刚度预测模型的具体流程如图7所示;
[0141]
在本实施例中采用如下的形貌参数和材料属性对界面切向刚度进行计算,e1=e2=207gpa,ν1=ν2=0.29,h=1.96gpa,σ/r=1.144
×
10-3
,β=0.0541,a0=0.0012m2,d0=7.5μm;
[0142]
界面宏观形状函数定义如下:
[0143]
sv(x,y)=x(5
×
10-5
)
[0144]
界面介观形貌函数fv=0。刚性平面与粗糙面平均高度线之间的间距d(x)的定义如下:
[0145]
d(x,y)=d
0-x(5
×
10-5
)
ꢀꢀꢀꢀꢀꢀꢀ
(27);
[0146]
基于已建立的多尺度形貌表征的界面切向接触力学模型,可以得到不同切向位移下的切向刚度,如图8所示;
[0147]
通过本实施例所述的含多尺度形貌参数界面切向接触力学模型,可以对界面切向力与位移关系、切向刚度与位移关系进行计算,需要说明的是,通过本实施例中的式(17),也可以对法向接触刚度进行计算;
[0148]
本实施例中所采用的多尺度形貌参数仅仅作为分析和计算演示,对于不同大小和材质以及加工工艺的接触界面,可以根据实际表面形貌的测量结果进行计算。
[0149]
以上所述仅为本发明的较佳实施例而已,并不用以限制本发明,凡在本发明的精神和原则之内所作的任何修改、等同替换和改进等,均应包含在本发明的保护范围之内。