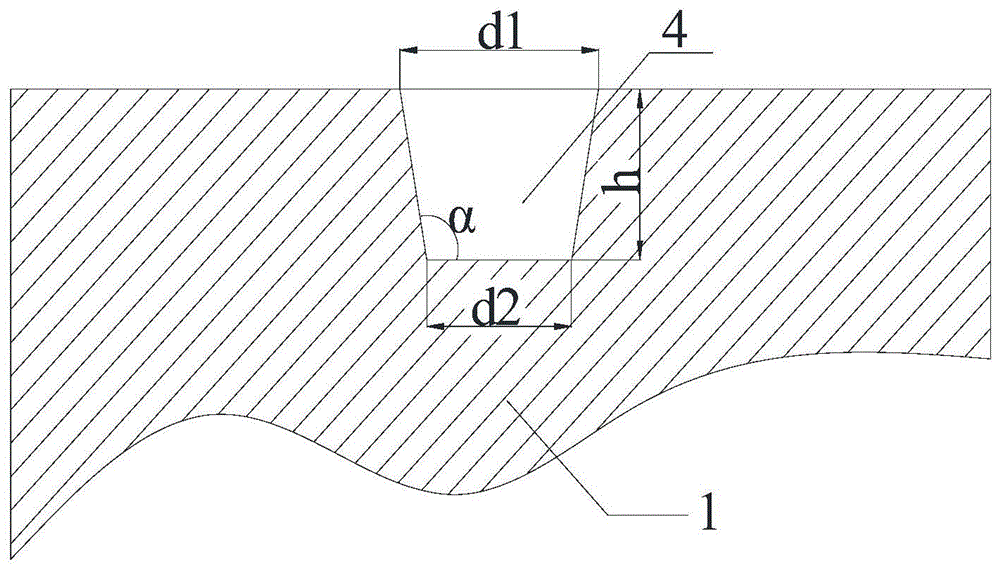
本发明涉及太阳能电池领域,更具体地说,涉及一种太阳能电池片制备方法。
背景技术:
:太阳能电池光伏发电是解决全球能源危机和环境污染问题的重要途径,其中近90%采用的是硅片太阳能电池。金刚石线锯切割技术近年来开始应用于晶体硅片的切割生产,与现行主流的碳化硅磨料砂浆线切割技术相比,它具有切割速率高、环境负荷小、硅片表面机械损伤小、硅锯屑少且容易回收、硅片的弯曲度和总厚度偏差小的优点,金刚石线切割能够大幅度的降低多晶硅片成本。与现行的砂浆线锯切割硅片相比,金刚石线锯切割硅片表面总呈现明显的切割纹及较高的表面反射率。其实金刚石线切割硅片微观粗糙度比砂浆切割硅片小,因此有人认为这些切割纹应该不会影响太阳能电池的性能,但是,光伏市场反映表明,其切割纹足以阻碍其市场发展。理论与实践表明,在各向异性的碱刻蚀制绒过程中,可以完全去除单晶硅片上的金刚石切割纹,因此,金刚石切割技术已在单晶硅片的生产上得到应用。但是,对于金刚石切多晶硅片,采用常规的混酸刻蚀制绒,其反射率均不能减低到现行行业标准,并有明显的线痕等外观缺陷,严重降低了电池效率。如采用碱刻蚀该类多晶硅片,对接近(001)取向的晶粒表面有良好的制绒效果,微观划痕和宏观往复纹能够被彻底去除,但对其他取向的晶粒无效果,并且制备得到的电池效率仍然偏低。为解决金刚石切割硅片的制绒问题,日本一些光伏企业引入喷砂预处理技术,去除金刚石线切割多晶硅片表面切割纹,但其附加的成本高,设备复杂。此外,少数有潜力的金刚线切割硅片制绒技术,如等离子体反应刻蚀(ire)方法,需要比现有产线技术复杂、昂贵的设备,成熟技术转移到产线尚需时日。金属离子辅助制绒(黑硅)技术是近几年发展起来的一种较好的解决金刚线切硅片制绒的方法。该技术是采用au、ag等贵金属离子、过氧化氢和氢氟酸组成联合刻蚀液,在对硅片刻蚀过程中,金属离子被硅还原成纳米粒子并附着在硅片表面,而后金属粒子作为阴极、硅作为阳极,在硅表面构成微电化学反应通道。过氧化氢作用在硅的表面上生成二氧化硅,氢氟酸对二氧化硅进行络和作用,生成可溶于水的络合物,从而在纳米金属粒子下方快速刻蚀形成微纳米孔洞,该孔洞结构具有良好的陷光效应。但在实际生产中,金属离子辅助形成微纳米绒面,虽然表面反射率得到降低,但是电池的效率并没有得到提升,并且外观也存在不良,因此,如何将金属离子辅助制绒(黑硅)技术大规模运用到生产实际中,仍然是当前迫切需要解决的问题。技术实现要素:本发明为了解决现有金属离子辅助制绒技术在实际生产中不能大规模运用的技术问题,提供一种光电转换效率高、外观无明显晶花、能大规模实际生产的太阳能电池片制备方法。本发明的目的是提供上述太阳能电池片的制备方法,步骤包括:在硅基体表面开设开口宽度为500~1200nm、深度为200~500nm的基体孔洞,后经过扩散、附着减反射膜制得太阳能电池片;步骤包括:s11,沉积金属粒子:将硅基体置于含金属离子的盐及氢氟酸的混合液中沉积金属粒子;s21,开微纳米孔:将步骤s11所得硅基体置于含氢氟酸及双氧水的刻蚀液中刻蚀;所述刻蚀液中双氧水的体积:氢氟酸的体积:水的体积=(2~5):1:(5~8);步骤s21中所述双氧水的质量浓度为30~32%;所述氢氟酸的质量浓度为49~50%;s31,削扩微纳米孔:将步骤s21所得硅基体置于含硝酸及氢氟酸的混合酸液中,所述混合酸液中硝酸的体积:氢氟酸的体积:水的体积=(5.0~9.0):1:(7~10);步骤s31中所述硝酸的质量浓度为65~68%;所述氢氟酸的质量浓度为49~50%;s41、除多孔硅及微纳米孔修正:将步骤s31所得硅基体置于碱液中去除多孔硅层及对微纳米孔进行修正;s51、去除金属粒子;s61、扩散;s71、镀减反射膜;s81、制备太阳能电池电极;制得太阳能电池片。本发明的发明人通过长期的实践研究发现,由于硅基体的边界效应以及晶向的影响,造成微纳米孔洞的开口大小、方向及深度的不同,为后续扩散、pecvd(等离子体增强化学气相沉积法)等工艺的反应气体进入孔洞形成了障碍。此外,大幅度增加的绒面表面积也会成为载流子的复合中心,造成大规模实际生产的太阳能电池片光电转化效率低。在此基础上,本发明通过特定的金属离子辅助制绒得到特定大小、深度的微纳米孔洞,再经过扩散、镀减反射膜等工序将金刚线切后的多晶硅片制备成表面具有特殊孔洞结构的多晶硅太阳电池片,对于一般太阳能电池片,包括硅基体及附着在硅基体表面的扩散层和减反射膜层,即本发明通过特定的金属离子辅助制绒在硅基体的表面得到特定大小、深度的基体孔洞,位于基体孔洞处的扩散层和减反射膜层附着于基体孔洞的孔壁及底部形成特殊孔洞结构的电池片孔洞,意外发现具有此特殊结构的太阳能电池片的光电转换效率得到显著提升,甚至高于目前常规砂浆切硅片酸制绒得到的电池片,且外观与砂浆切硅片电池片接近,无明显的晶花现象,其原因推测可能是1、本发明特定大小、深度的电池片孔洞具有优异的陷光性能,相比传统的酸制绒砂浆切常规电池片,可以很大程度地降低光的反射损失。2、本发明的基体孔洞使扩散层及减反射膜层在孔洞内分布均匀,对孔洞内的硅表层的钝化效果好,且金属离子辅助制绒的残余纳米金属粒子也容易被清洗出来,消除了载流子的复合中心。特别是制得的具有底面宽度小于开口宽度的特定大小、深度的基体孔洞,孔洞具有倒喇叭形结构,如图1所表示,在电池片的扩散与镀减反射膜工艺过程中,该结构使得工作气体,很容易扩散并覆盖孔洞的壁面与底部,从而制得的扩散层及减反射膜层在孔洞内分布相对比较均匀,并且对孔洞内的硅表层的钝化效果好,能进一步提高太阳能电池的性能。此外,具有该倒喇叭形结构的孔洞,残余的纳米金属粒子也更容易被清洗出来,消除了载流子的复合中心,本发明的太阳电池的光生载流子的收集效果好,电池的短路电流及开路电压高。本发明制备的太阳能电池片不仅较现有的金刚石线锯切割硅片所制备的太阳能电池片效率大幅度提升,甚至与常规砂浆切硅片所制备的电池相比,其平均光电效率的绝对值还可提升0.30%以上。附图说明图1为本发明实施例1所制备的硅基体的微纳米孔洞即基体孔洞的局部放大剖面示意图,d1为微纳米孔洞的开口宽度,d2为微纳米孔洞底面的宽度,h为微纳米孔洞的深度,α为微纳米孔侧面与底面之间的夹角。图2为本发明实施例1所制备的电池片孔洞的局部放大剖面示意图。图3为本发明实施例1所制备的基体孔洞的sem图(放大50000倍)。图4为本发明实施例1所制备的电池片孔洞的sem图(放大20000倍)。图5为本发明对比例1所制备的硅基体表面的微纳米孔洞的sem图(放大50000倍)。图6为本发明对比例4所制备的硅基体表面的微米坑的sem图(放大10000倍)。图7为本发明实施例1所制备的硅基体的实物外观图。图8为本发明对比例1所制备的硅基体的实物外观图。图9为本发明对比例4所制备的硅基体的实物外观图。图10为本发明实施例1所制备的太阳电池片的实物外观图。图11为本发明对比例1所制备的太阳电池片的实物外观图。图12为本发明对比例4所制备的太阳电池片的实物外观图。具体实施方式为了使本发明所解决的技术问题、技术方案及有益效果更加清楚明白,以下结合附图及实施例,对本发明进行进一步详细说明。应当理解,此处所描述的具体实施例仅仅用以解释本发明,并不用于限定本发明。本发明提供一种太阳能电池片,该太阳能电池片的表面具有电池片孔洞,所述电池片孔洞的开口宽度为400~1000nm,所述电池片孔洞的深度为100~400nm。进一步优选,电池片孔洞的开口宽度为500~800nm,所述电池片孔洞的深度为150~300nm。能显著提高太阳能电池的光电转换效率且制备的太阳能电池片外观无明显晶花。优选,电池片孔洞的底面宽度小于开口宽度。例如倒喇叭形结构,如附图2所示的,d2小于d1,可以很大程度地降低光的反射损失。一般太阳能电池片,包括硅基体及附着在硅基体表面的扩散层和减反射膜层,可通过在硅基体表面开设此种形状的基体孔洞,再制备均匀的扩散层和减反射膜层可得到此类太阳能电池片。本发明的太阳电池的光生载流子的收集效果好,电池的短路电流及开路电压高,与常规砂浆切硅片所制备的电池相比,其平均光电效率的绝对值可提升0.30%以上。进一步优选,如附图2所示,电池片孔洞的侧面与底面的夹角α为100°~135°,进一步优选,电池片孔洞的侧面与底面的夹角为110°~120°,进一步优化孔洞结构,特定的开口宽度、倾斜度及深度得到的太阳能电池片性能更优。太阳能电池片一般包括硅基体及附着在硅基体表面的扩散层和减反射膜层,所述硅基体的表面具有基体孔洞,位于基体孔洞处的扩散层和减反射膜层附着于基体孔洞的侧面和底面即孔壁和底部形成上述电池片孔洞。优选,基体孔洞的开口宽度为500~1200nm,优选为600~1000nm;基体孔洞的深度为200~500nm,优选为300~400nm。使扩散层及减反射膜层在孔洞内分布均匀,对孔洞内的硅表层的钝化效果好,且金属离子辅助制绒的残余纳米金属粒子也容易被清洗出来,消除了载流子的复合中心。优选,减反射膜层的厚度为80~90nm。本发明同时提供了一种太阳能电池片的制备方法,步骤包括:在硅基体表面开设开口宽度为500~1200nm、深度为200~500nm的基体孔洞,后经过扩散、附着减反射膜制得太阳能电池片。具体步骤可以包括:s11,沉积金属粒子:将硅基体置于含金属离子的盐及氢氟酸的混合液中沉积金属粒子;具体可以为将硅基体置于含金属离子的盐(如agno3)及氢氟酸的混合液槽中,使金属离子被硅还原成纳米金属粒子并沉积在硅基体表面。优选,此步骤s11中,含金属离子的盐及氢氟酸的混合液中金属离子的浓度为10~100ppm,氢氟酸在混合液中的体积浓度为0.5~10%;其中,所述氢氟酸的质量浓度为49~50%;进一步优化生成的纳米金属粒子粒径,及在硅基体表面的分布。优选,此步的反应温度为20~30℃,反应时间为50~150s。一般反应完成后可以用去离子水清洗120~240s。优选,步骤s11前还包括对硅基体进行前处理,前处理本发明没有限制可以为本领域技术人员公知的各种前处理,本发明优选为:s01,碱初抛;优选,具体为采用氢氧化钠或氢氧化钾溶液,在一定温度下,将多晶体硅基体进行初始抛光,以去除硅表面的油污及损伤层,使硅基体表面形成相对平整的微米绒面,然后过去离子水清洗120~240s。在此阶段中,强碱的质量浓度可以控制在2.0~15wt%,温度可以控制在60~90℃,反应时间可以为1.0~5.0min,平均减重量可以在0.20~0.35g,能更优的去除金刚线切割硅片留下的损伤层。s02,酸清洗;优选,具体可以为将步骤s01所得硅基体采用体积浓度为0.2~2.0%的稀硝酸清洗硅基体上残留的强碱,清洗温度可以为常温,清洗时间为50~100秒,然后再过去离子水清洗120~240s。s21,开微纳米孔:将步骤s11所得硅基体置于含氢氟酸及双氧水的刻蚀液中刻蚀;所述刻蚀液中双氧水的体积:氢氟酸的体积:水的体积=(2~5):1:(5~8),此步骤s21中上述双氧水的质量浓度为30~32%;氢氟酸的质量浓度为49~50%;即采用此质量浓度的双氧水、氢氟酸按上述体积比配置刻蚀液。具体可以为将硅基体放置于含氢氟酸及双氧水的刻蚀液槽中。步骤s11沉积在硅基体表面的纳米金属粒子作为阴极、硅作为阳极,在硅基体表面构成微电化学反应通道,过氧化氢和氢氟酸联合作为刻蚀液,过氧化氢作用在硅上生成二氧化硅,氢氟酸对二氧化硅进行络和作用,生成可溶于水的络合物,从而在纳米金属粒子下方快速刻蚀形成微纳米孔洞结构,因刻蚀的各向异性,形成的微纳米孔的开口形状与晶向有关,在(100)晶向一般形成四边形微纳米孔,在(111)晶向一般形成六边形微纳米孔等。对于同一晶向,除去晶体边界,刻蚀液对该晶向的硅的刻蚀作用大致相同,因此,同一晶向的孔的形状、宽度(指的是四边形或六边形两平行边的距离)、深度是基本相同的。对于不同的晶向,可通过调整刻蚀液的浓度、温度或时间来控制开孔的大小与深度。本发明通过双氧水的体积:氢氟酸的体积:水的体积=(2~5):1:(5~8),进一步优选双氧水的体积:氢氟酸的体积:水的体积=(3~5):1:(5~8),从而制得独特大小、深度的基体孔洞。进一步优选,此步反应温度为30~40℃,刻蚀时间为200~300s。合适的孔洞,不仅能避免后续电池工艺的难度增加,而且避免陷光效应,优化电池片的效率。一般,开孔完成后,将硅基体过去离子水清洗120~240s。s31,削扩微纳米孔:将步骤s21所得硅基体置于含硝酸及氢氟酸的混合酸液中,所述混合酸液中硝酸的体积:氢氟酸的体积:水的体积=(5.0~9.0):1:(7~10);步骤s31中所述硝酸的质量浓度为65~68%;所述氢氟酸的质量浓度为49~50%;即采用此质量浓度的硝酸、氢氟酸按上述体积比配置混合酸液。具体可以为将硅基体放置于含硝酸及氢氟酸的混合酸液槽中,通过硝酸及氢氟酸对硅基体表面刻蚀形成的微纳米孔进行联合刻蚀,采用高浓度及高富硝酸的混合酸液来刻蚀所开的微纳米孔,可以降低微纳米孔的孔深,同时,进一步优化微纳米孔,优化微纳米孔的开口形状与大小,意外发现高浓度及高富硝酸的混合酸液使原来的四边形或六边型的棱角钝化形成圆弧角,使微纳米微孔的开口由原来的四边形或六边形变成准圆形(本发明的准圆形指其类似圆形,因原多边形的棱边未被刻蚀,仅棱角被刻蚀成圆弧,准圆形的宽度指的是通过中心点的径向宽度),同时可以进一步扩孔。由于微纳米孔的深度较深,混合酸液进入孔洞内需要一定的时间,因此微纳米孔洞的外表面边缘及壁面优先被刻蚀,在高浓度及高富硝酸的混合酸液体系下,刻蚀液对硅基体具有很高的刻蚀速度,从而将余下的微纳米孔洞上(其上已经被削掉一层微纳米孔洞)刻蚀形成外宽里窄,具有倒喇叭形状(从硅表面的外向里观察)的准圆台形的微纳米孔,如图3所示。本发明优选硝酸的体积:氢氟酸的体积:水的体积=(6.0~8.0):1:(8~9),本发明采用含特定的硝酸与氢氟酸浓度的混合酸液从而制得特定形状的孔洞结构,优选硝酸与氢氟酸的浓度比值γ为5~9,进一步优选6~8,在同样的总酸浓度下。如果γ小,则反应速度迟缓,则微孔的顶部与底部刻蚀速度接近,即不能形成倒喇叭形状的孔,此时孔的倾斜面与底面的夹角α为90°或接近90°(α=90°即为准圆柱形孔),如图5所示。γ越大,反应速度越快,准圆台形微纳米孔洞的顶面(开口)宽度d1与底面宽度d2相差就越大,即孔的夹角α就越大,光线入射后反射出孔洞的量就越多,反射率也越大,对后续的扩散与镀膜工艺也就越有利。当然γ也不能太大,否则孔的α太大,光线容易被反射出,陷光效应变差,失去了微纳孔相比常规微米坑的优势。优选,此步反应温度为8~13℃,最优为9~11℃,反应时间为80~180s,最优为100~150s。进一步优化微纳米孔结构,避免平均反射率增加及产生晶花现象,同时简化工艺。优选,单片硅基体在此工序前后的减重量控制在0.06~0.15g,最佳范围为0.08~0.12g,进一步优化太阳能电池片的性能。一般,削扩微纳米孔后还将硅基体过去离子水清洗120~240s。s41、除多孔硅及微纳米孔修正:将步骤s31所得硅基体置于碱液中去除多孔硅层及对微纳米孔进行修正。优选,所述碱液为质量浓度0.2~5.0%的氢氧化钠或氢氧化钾溶液,置于碱液中的时间为5.0~30s。具体可以为将硅基体放置在含氢氧化钠或氢氧化钾溶液的槽中进行刻蚀,低浓度的强碱迅速除去硅外表层的疏松的多孔硅结构,露出具有本发明特征的准圆台形微纳米孔洞形成的绒面。优选,反应温度为常温,反应时间为5.0~30s,本步骤中削扩微纳米孔后的微纳米孔不会被破坏,形状与体积不会有大的变化。一般,反应完成后,将硅基体过去离子水清洗120~240s。s51、去除金属粒子。优选为将步骤s41所得硅基体置于含氨水与过氧化氢的溶液中。具体可以为将步骤s41所得硅基体放入含氨水与双氧水的混合液槽中,氨水的体积:双氧水的体积:水的体积=1:(1~4):(40~50);此步骤s41中所述氨水的质量浓度为25~28%,所述双氧水的质量浓度为30~32%;即采用上述质量浓度的氨水和双氧水按如上体积配置混合液,过氧化氢为氧化剂,将前序清洗未除去的纳米金属(如银)粒子氧化,采用氨水为络合剂,使其形成银胺络离子而溶于水被除去。优选,反应的温度为常温,反应的时间为50~300s,一般,反应完后可将硅基体过去离子水清洗120~240s。所述步骤s51后还包括:s52,混酸清洗。具体可以为将步骤s51所得硅基体放置于含氢氟酸与盐酸的酸溶液中清洗,以除去其他微量金属杂质(如铁、镍等金属杂质),含氢氟酸与盐酸的酸溶液中物质体积分数比为盐酸:氢氟酸:水=(2~3):1:(5~6),此步骤s52中所述盐酸的质量浓度为35~38%,所述氢氟酸的质量浓度为49~50%。优选,反应的温度为常温,清洗时间为50~300s。一般反应后,可将硅基体过去离子水清洗120~240s。s53,慢提拉。具体可以为将步骤s52所得硅基体采用热的去离子水清洗120~240s,水温为60~80℃,然后缓慢提拉,将硅基体提出水面。提拉时间为5~20s。一般可控制槽中水的残余离子浓度,采用电导率仪测试该槽中去离子水的电阻值,控制其在70±2℃下电导率值≤1.0μs/cm。s54,干燥,具体可以为将步骤s53所得硅基体热烘干,烘干温度为100~150℃,时间为5~15min。优选,干燥后所得硅基体表面金属原子或离子的浓度≤50ppb,采用电感耦合等离子体质谱仪(icp-ms)测试。本发明特殊结构的硅基体由于表面特殊结构的基体孔洞使残余纳米金属粒子少,消除了载流子的复合中心,能提高光电转化效率。具体实施上述步骤后,即得到对金刚线切割硅基体进行制绒后的硅基体,如图7所示可以看出,该硅基体表面制绒均匀,无晶界现象,采用绒面反射率仪检测,在400~1100nm波段内,其平均光反射率14~22%,优选,16~20%。在扫描电子显微镜(sem)下,观察本发明制备的硅基体的绒面,可以看出,该绒面由具有一定开口宽度、倾斜角度、及孔深度的微纳米孔洞构成。s61、扩散。扩散工艺本发明没有限制,可以采用本领域技术人员公知的各种扩散工艺,在此不再赘述。在制备具有本发明特征绒面的硅基体后,使其进入扩散炉中经过磷扩散制pn结,扩散工艺与常规酸制绒的砂浆切硅片大致相同。因本发明的准圆台形微纳米孔洞具有倒喇叭形结构,在扩散过程中,磷源气很容易扩散并覆盖孔洞的壁面与底部,这样使得n型扩散层沿孔洞分布均匀,n层收集载流子的效果好,电池的开路电压及短路电流高。本发明中,调节扩散的温度或磷源量,使扩散后的硅片的平均方阻在80~100ω/□,最优在85~90ω/□,这样的方阻范围与本发明特征的绒面具有较好的匹配度。优选,步骤s61后还包括:s62、去磷硅玻璃。一般为二次清洗去磷硅玻璃,去除磷硅玻璃层和刻蚀硅基体周边,该工艺本发明没有限制,可以采用本领域技术人员公知的各种刻蚀工艺,在此不再赘述。s71、镀减反射膜。pecvd镀sinx减反射膜。镀膜工艺本发明没有限制,可以采用本领域技术人员公知的各种镀膜工艺,在此不再赘述。上述制备的特殊结构的基体孔洞使硅烷气和氨气可以顺利进入孔洞内部,使得镀膜过程中原子氢对孔洞壁与底部都有良好的钝化效果,大大减少了由于刻蚀制绒过程中孔洞内硅产生的悬挂键,降低了复合中心数目,电池的开路电压和短路电流都得到一定的提升,优选,减反射膜层的厚度80~90nm,平均折射率2.00~2.20。s81、制备太阳能电池电极。一般为印刷电极并金属化制成受光面电极及背光面电极用于引出电流,受光面电极及背光面电极可以采用各种电极结构,例如,可以在背面印刷背铝浆、背银浆,正面印刷正银浆,经过烧结炉后,得到具有正、负电极的太阳能电池片。本发明同时提供了一种太阳能电池,包括上述太阳能电池片。太阳能电池的其他结构为公知,在此不再赘述。为了使本发明所解决的技术问题、技术方案及有益效果更加清楚明白,以下结合实施例,对本发明进行进一步详细说明。应当理解,此处所描述的具体实施例仅用以解释本发明,并不用于限定本发明。实施例1本实施例所采用的原材料物质等级、浓度分别为:氢氧化钾,电子级,质量浓度为45%;硝酸:电子级,质量浓度为65~68%,氢氟酸:电子级,质量浓度为49~50%;硝酸银:分析纯,固体,纯度为99.9%;氨水:电子级,质量浓度为25~28%;双氧水,电子级,质量浓度为30~32%;盐酸:电子级,质量浓度为35~38%;采用金刚线切割的156×156多晶硅片,测试其电阻率数值范围为1.20~2.50ω·cm,符合硅片的电阻率要求。测试其少子寿命数值范围为1.10~1.60μs,符合硅片的少子寿命要求。每次采用200片(2个花篮,每个篮子100片)做实验,实验结果取平均值,各工艺槽容积体积均为120升左右。整个制绒过程的工艺步骤为下:a(碱初抛):在初抛槽中加入15l氢氧化钾溶液,加入105l的水,得到质量浓度为7.83%的氢氧化钾溶液,将溶液升温到80℃,将硅片放入其中,刻蚀时间为4.0min。刻蚀完成后,将硅片过去离水清洗150s,得到去油污及损伤层的多晶硅片。电子称称量该工序的减重量为0.282g/片。b(酸清洗):将上步骤的硅片放入清洗槽中,该槽中的清洗液为用体积浓度1%的稀硝酸,清洗时间为2min,将硅片过去离水清洗150s。c(沉积金属粒子):将上步骤的硅片放入沉积金属粒子槽中,该沉积金属粒子槽中所加入氢氟酸为4l,水116l,再加入4g的硝酸银晶体,得到硝酸银的浓度为33.4ppm,加热槽中溶液的温度至20±1℃,反应时间为60s。反应完成后,将硅片过去离水清洗10s以除去浮银粒子。d(开微纳米孔):将上步骤的硅片放置开孔槽中,该槽加入氢氟酸10l,双氧水40l,去离子水70l,双氧水的体积:氢氟酸的体积:水的体积=4:1:7;将温度升到35℃,反应时间为240s,反应完成后,将硅片过去离水清洗150s。e(削扩微纳米孔):将上步骤的硅片放置在削扩微纳米孔槽中,槽中硝酸及氢氟酸的物质体积比为硝酸:氢氟酸:水=7:1:9,混合酸液的温度为10℃,反应时间为120秒,反应完成后取出硅片,将硅片过去离水清洗150s,用电子称称量该工序的减重量为0.103g/片。f(除多孔硅及微纳米孔修正):将上步骤的硅片放入添加有氢氧化钠的槽中进行修正反应,其中氢氧化钠的质量浓度为2.0%。反应温度为20℃,反应时间为15s,反应完成后,将硅片过去离水清洗150s。g(去除金属粒子):将上步骤的硅片放入添加有氨水与过氧化氢的混合液槽中进行清洗纳米银粒子,槽中氨水的体积浓度为3%,过氧化氢的体积浓度为5%。溶液的温度为20℃,清洗时间为200秒,而后将硅片过去离水清洗150s。h(混酸清洗):将上步骤后的硅片放置在氢氟酸和盐酸混合酸溶液中清洗,混合液中氢氟酸的体积浓度为10%,盐酸体积浓度为20%,溶液的温度为20℃,酸洗时间为200s,而后将硅片过去离水清洗150s。i(慢提拉):将上步骤清洗后的硅片采用热的去离水清洗150s,水的温度为70℃,然后缓慢提拉,将硅片提出水面,提拉时间为10s,采用电导率仪测试该槽中去离子水在69℃时的电导率值在0.50~0.70μs/cm。j(干燥):将上步骤清洗后的硅片使用热烘干,烘干温度为120℃,时间为10min。实施上述步骤后,即得到本实施例所制得的硅基体1样品sa1,采用扫描电镜(sem)观察sa1,放大50000倍,结果如图3。sa1的外观如图7。采用icp-ms仪器测试其表面的残余银粒子的浓度为17.30ppb。k(扩散):将上步骤烘干后的硅基体1样品sa1进入扩散炉中经过磷扩散制pn结。l(去磷硅玻璃):将上步骤经过扩散的硅片经过二次清洗以刻蚀去除磷硅玻璃及四周扩散层。m(镀减反射膜)将上步骤经过扩散的硅片经过两次清洗后pecvd镀sinx减反射膜,减反射膜的平均厚度为82nm,平均折射率为2.10。n(制备太阳能电池电极):将上步骤镀膜后的硅片背面印刷背铝浆、背银浆,正面印刷正银浆,过烧结炉后得到本发明的多晶硅太阳电池片样品ss1,如图2所示,制得的太阳能电池片包括硅基体1及附着在硅基体1表面的扩散层2和减反射膜层3,所述硅基体1的表面具有基体孔洞4,位于基体孔洞4处的扩散层2和减反射膜层3附着于基体孔洞4的侧面和底面即孔壁和底部形成电池片孔洞5,本实施例在镀减反射膜过程中在扩散层2表面形成有氢钝化层6即在扩散层2和减反射膜层3还有氢钝化层6。采用扫描电镜观察ss1,放大20000倍,结果如图4。ss1的外观如图10。实施例2采用与实施例1相同的方法步骤制备太阳能电池样品ss2,不同的是步骤e(削扩微纳米孔)中硝酸及氢氟酸的物质体积比改为硝酸:氢氟酸:水=5:1:10,制得硅基体样品sa2。实施例3采用与实施例1相同的方法步骤制备太阳能电池样品ss3,不同的是步骤e(削扩微纳米孔)中硝酸及氢氟酸的物质体积比改为硝酸:氢氟酸:水=9:1:9,制得硅基体样品sa3。实施例4采用与实施例1相同的方法步骤制备太阳能电池样品ss4,不同的是步骤e(削扩微纳米孔)中硝酸及氢氟酸的物质体积比改为硝酸:氢氟酸:水=8:1:7,制得硅基体样品sa4。实施例5采用与实施例1相同的方法步骤制备太阳能电池样品ss5,不同的是步骤e(削扩微纳米孔)的反应时间为150s,制得硅基体样品sa5。实施例6采用与实施例1相同的方法步骤制备太阳能电池样品ss6,不同的是步骤d(开微纳米孔)中双氧水的体积:氢氟酸的体积:水的体积=3:1:8,制得硅基体样品sa6。对比例1采用与实施例1相同的方法步骤制备太阳能电池样品dss1,不同的是步骤e(削扩微纳米孔)中硝酸及氢氟酸的物质体积比改为硝酸:氢氟酸:水=4:1:10,制得硅基体样品dsa1,采用扫描电镜观察dsa1,放大50000倍,结果如图5。dsa1的外观如图8。dss1的外观如图11。对比例2采用与实施例1相同的方法步骤制备太阳能电池样品dss2,不同的是步骤e(削扩微纳米孔)的反应时间为200s,制得硅基体样品dsa2。对比例3采用与实施例1相同的方法步骤制备太阳能电池样品dss3,不同的是步骤d(开微纳米孔)中双氧水的体积:氢氟酸的体积:水的体积=6:1:7,制得硅基体样品dsa3。对比例4采用砂浆切的156×156多晶硅片,采用传统的混酸在rena链式机上制备多晶硅绒面(即一次清洗工艺),得到硅基体样品dsa4,采用扫描电镜观察dsa4,放大10000倍,结果如附图6;dsa4的外观如图9;经实施例1相同的k(扩散)、l(去磷硅玻璃)、m(镀减反射膜)、n(制备太阳能电池电极)的制备步骤得太阳电池片样品dss4。dss4的外观如图12。性能测试硅基体sa1-sa6及dsa1-dsa4的表征:在扫描电子显微镜(sem)下,观察并测试硅基体sa1-sa6及dsa1-dsa4的微纳米孔洞,其形状参数有:顶面开口宽度(d1,单位:nm)、侧面与底面之间的夹角(α,单位:度)、孔洞的深度(h,单位:nm)。采用绒面反射率仪检测所制得到的硅基体,在400~1100nm波段内的平均光反射率(单位:%)。电池片电性能参数:采用太阳电池片专用测试仪器,如单次闪光模拟器进行测试。测试条件为标准测试条件(stc):光强:1000w/m2;光谱:am1.5;温度:25。测试方法按照iec904-1进行。电池片的主要电性能参数:光电转化效率(eta,单位:%)、短路电流(isc,单位:a)、开路电压(voc,单位:v)、(填充因子(ff,单位:%)、漏电流(irev2,单位:a)、串联电阻(rs,单位:mω)、并联电阻(rsh,单位:ω)。硅基体的表征参数测试结果如表1:表1电池片电性能参数测试结果如表2。表2样品etaiscvocffirev2rsrshss119.089.10550.632480.740.30980.00105556.673ss218.858.94810.631880.510.27530.00119414.774ss318.908.98420.631780.760.32670.00110573.820ss418.978.99910.631580.570.27500.00109402.778ss518.928.96710.631680.720.30670.00121512.820ss618.808.95210.631980.650.48210.00110237.000dss118.498.84250.630580.700.54790.00130386.774dss218.568.83720.631980.870.33360.00114277.572dss318.278.75740.629380.680.34780.00094229.732dss418.448.78210.631180.730.43700.00180299.042从表2结果可以看出,本发明实施例所制备的电池片的短路电流相比传统的砂浆片电池(对比例dss4)得到了较大的幅度提升,均在150ma以上,其开路电压也有一定范围的提升,因此电池的转换效率得到了明显的提升,均在0.30%以上。对比例所制得的电池片效率较低,不采用本发明特殊结构的电池片孔洞的电池片开路电压出现明显的下降(例如dss3的开路电压下降了3mv以上)。以上所述仅为本发明的较佳实施例而已,并不用以限制本发明,凡在本发明的精神和原则之内所作的任何修改、等同替换和改进等,均应包含在本发明的保护范围。本领域技术人员容易知道,以上所述仅为本发明的较佳实施例而已,并不用以限制本发明,凡在本发明的精神和原则之内所作的任何修改、等同替换和改进等,均应包含在本发明的保护范围之内。本发明的保护范围由权利要求书确定。当前第1页1 2 3