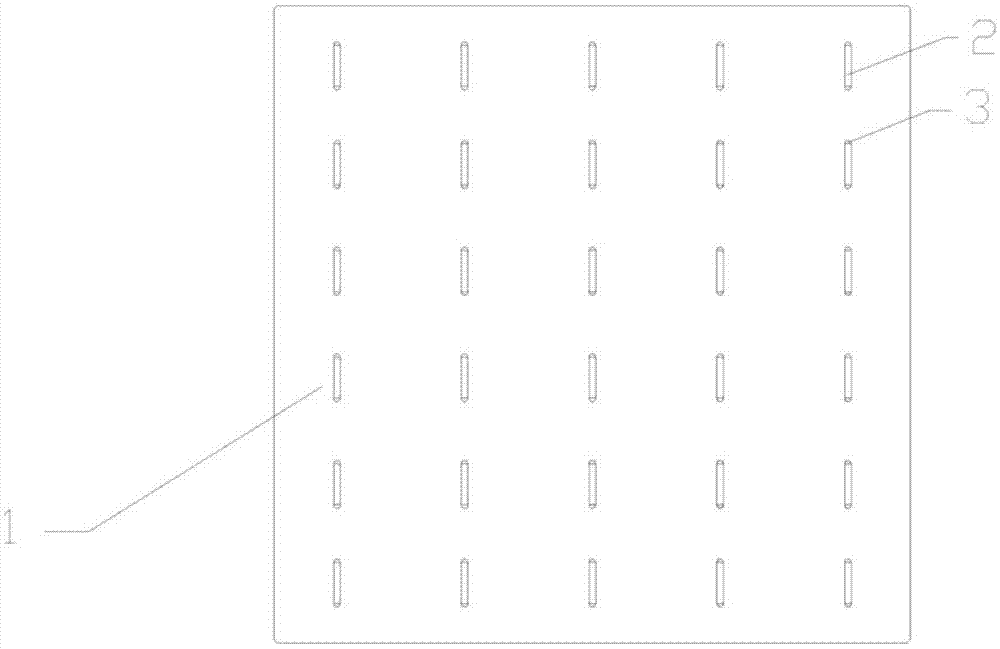
本实用新型属于太阳能电池
技术领域:
,具体涉及一种高抗机械载荷晶硅电池。
背景技术:
:随着人类生活的进步,对于能源的需求迅速增加,然而占据世界上总发电量70%以上的火力发电,由于资源的日渐紧缺以及环境的逐渐恶化已经成为日益引人关注的问题。太阳能作为可再生资源用于发电也越来越受到人们的重视。近年来,随着晶体硅太阳能电池技术的发展,硅片厚度也逐渐减薄以降低光伏发电成本,但硅片减薄随之带来的是组件制作中碎片率的上升和组件本身的抗机械载荷能力下降,特别是PERC(钝化发射极背面电池)工艺的开发,激光开槽环节的增加使电池在组件制作中的碎片率进一步上升,组件本身的抗机械载荷能力也进一步下降。在这种情况下,各种提升组件抗机械载荷能力的方案也逐渐涌现。专利CN104935247A采用在组件边框增加加强筋的方法以提升组件抗机械载荷能力,这种方法有效的降低了组件受压后的电池碎片率和功率损失,但这种方法在组件制作中不仅增加了额外的加强筋,物料成本增加,同时还需要增加额外的工位来实现加强筋安装,工艺步骤繁琐而且增加了额外的人力成本。技术实现要素:本实用新型的目的在于提供一种高抗机械载荷晶硅电池,该晶硅电池通过对背面电极以及激光开槽的结构调整,从而可以避免焊接过程中背面电极位置受力不均匀以及激光损伤加剧背面电极应力作用使电池更容易发生脆性断裂的情况,并从这两个方面来实现降低组件端碎片率以及提升组件抗机械载荷能力。本实用新型的上述目的是通过以下技术方案来实现的:一种高抗机械载荷晶硅电池,所述晶硅电池的背面电极包括多列相平行分布的栅线,每列栅线包括六段或八段相间隔设置的子栅线,每个子栅线的两端与所述背面电场之间设有间隙。背面电极由传统的三段式或者四段式变更为六段式或八段式子栅线结构,背面电极的多段式设计将背面电极烧结过程中产生的应力分布出去,降低了组件在受压过程中应力的影响,从而降低了机械载荷测试过程中的碎片比例以及功率衰减百分比。每个子栅线的两端与所述背面电场之间设有间隙,这样,就避免了焊接过程中焊带在背面电极两端位置由于背面电极、背面电场搭接位置与背面电极的高度差导致的焊接位置受力不均匀从而导致隐裂产生的现象。作为本实用新型的一种改进,本实用新型所述的晶硅电池优选为PERC晶硅电池。当所述的晶硅电池优选为PERC晶硅电池时,所述的PERC晶硅电池的背面设有钝化膜,所述钝化膜上设有激光开槽线,所述激光开槽线在所述背面电极位置处断开。激光开槽线在背面电极位置处断开的设计,由于PERC晶体硅电池的引入使晶体硅电池效率得到了提升,但是激光开槽增加了对硅基体的损伤,特别是在背面电极边缘位置,激光的损伤更是加剧了裂纹的成核,导致电池更容易脆断;因此激光开槽线必须在背电极位置断开。进一步的,所述的钝化膜优选为氧化铝和氮化硅叠层钝化膜。本实用新型的原理是:(1)背面电极两端与背电场连接处间隙设计:避免了焊接过程中焊带在背面电极两端位置由于背面电极、背面电场搭接位置与背面电极的高度差导致的焊接位置受力不均匀从而导致隐裂产生的现象。(2)背面电极由传统的三段式子栅线或者四段式子栅线变更为六段式子栅线或八段式子栅线设计:背面电极的多段式子栅线设计将背面电极烧结过程中产生的应力分布出去,降低了组件在受压过程中应力的影响,从而降低了机械载荷测试过程中的碎片比例以及功率衰减百分比。(3)激光开槽线在背面电极位置断开设计:PERC工艺的引入使晶硅电池效率得到了提升,但是激光开槽增加了对硅基体的损伤,特别是在背面电极边缘位置,激光的损伤更是加剧了裂纹的成核,导致电池更容易脆断,因此激光开槽线必须在背面电极位置断开。与现有技术相比,本实用新型具有以下优点:(1)本实用新型中的高抗机械载荷晶硅电池降低了组件焊接过程中隐裂的产生,从而降低了组件端碎片率;(2)本实用新型中的高抗机械载荷晶硅电池不需要添加任何辅助备件,即可实现PERC电池组件端机械载荷测试合格;(3)本实用新型中的高抗机械载荷晶硅电池的制备方法工艺简单,与现有产线兼容性好,不需要增加特殊环节,工业化可行性强,适合大规模推广使用。附图说明图1是本实用新型实施例1中的多晶硅的背面电极结构示意图;图2是本实用新型实施例2中的多晶硅的背面电极结构示意图;图3是本实用新型实施例3中的单晶硅的背面电极和激光开槽线结构示意图;图4是本实用新型实施例4中的单晶硅的背面电极和激光开槽线结构示意图。具体实施方式以下列举具体实施例对本实用新型进行说明:实施例1如图1所示,本实施例提供的高抗机械载荷晶硅电池,晶硅电池的背面电极包括多列相平行分布的栅线1,每列栅线包括六段相间隔设置的子栅线2,每个子栅线的两端与所述背面电场之间设有间隙3。其中晶体硅电池采用p型多晶硅片。该高抗机械载荷晶硅电池的制备方法,包括以下步骤:(1)选取电阻率在0.1~6Ω·cm的轻掺杂的p型多晶硅片,将硅片基体置于制绒机中进行损伤层去除和绒面制备,制绒采用的化学溶液为氢氟酸、硝酸、盐酸及其它常规添加剂的一种或多种混合水溶液。(2)对硅片表面进行清洗,采用化学溶液进行清洗,化学溶液可以为氢氟酸、硝酸、盐酸及其它常规添加剂的一种或多种混合水溶液,清洗时间为0.5~10分钟,温度为20~30℃。(3)将硅片置于800~1000℃的炉管中进行磷(P)扩散,在硅片表面形成n-型扩散层,扩散后硅片方块电阻为60~90Ω/sq。(4)将扩散后的硅片置于湿法刻蚀机中,采用化学溶液刻蚀掉周边的P/N结,同时去除磷硅玻璃,化学溶液可以为氢氟酸、硝酸、盐酸、硫酸及其它常规添加剂的一种或多种混合水溶液,刻蚀时间为0.5~10分钟,温度为5~20℃。(5)将湿刻后多晶硅片正面镀氧化硅或者氮化硅的一种或几种。(6)背面印刷银背面电极以及铝背场,背面电极采用本实用新型的六段式设计(即背面电极包括多列相平行设置的栅线1,每个栅线由六段相间隔设置的子栅线2组成),背面电极和背面电场连接处两端漏硅设计(即背面电极的每个子栅线2的两端与背面电场相连接处设有间隙3,可以露出硅片的表面,造成背面电极和背面电场连接处的断开)。(7)印刷正面电极栅线,烧结。如表1所述,按照上述实例结果表明多晶硅电池组件端碎片率下降0.2%以上。表1本实施例制备的多晶硅电池组件与常规电池组件的性能对比电池片组件开盒碎机损EL隐裂合计产量碎片率本实施例02681110.12%常规电池341118990.34%实施例2如图与实施例1不同的是,采用的是p型多晶硅片,背面电极包括多列相平行设置的栅线,每个栅线由八段相间隔设置的子栅线组成。如表2所示,按照上述实例结果表明多晶硅电池组件端碎片率下降0.2%以上。表2本实施例制备的多晶硅电池组件与常规电池组件的性能对比电池组件开盒碎机损EL隐裂合计产量碎片率本实施例12361300.08%常规电池141015800.31%实施例3如图3所示,本实施例提供的高抗机械载荷晶硅电池,晶硅电池的背面电极包括多列相平行分布的栅线1,每列栅线包括八段相间隔设置的子栅线2,每个子栅线的两端与所述背面电场之间设有间隙3。该晶体硅片为p型PERC单晶硅片。该PERC晶硅电池的背面设有钝化膜,钝化膜上设有激光开槽线4,激光开槽线4在背面电极位置处断开。钝化膜优选为氧化铝和氮化硅叠层钝化膜。该高抗机械载荷晶硅电池的制备方法,包括以下步骤:(1)选取电阻率在0.1~6Ω·cm的轻掺杂的p型单晶硅片,将硅片基体置于制绒槽中进行损伤层去除和绒面制备,在质量百分含量为0.5~5%的氢氧化钠去离子水溶液中,在温度为75~90℃的条件下进行表面织构化形成绒面结构;(2)对硅片表面进行清洗,采用化学溶液进行清洗,化学溶液可以为氢氟酸、硝酸、盐酸及其它常规添加剂的一种或多种混合水溶液,清洗时间为0.5~10分钟,温度为20~30℃;(3)将硅片置于800~1000℃的炉管中进行磷(P)扩散,在硅片表面形成n-型扩散层,扩散后硅片方块电阻为60-90Ω/sq;(4)将扩散后的硅片置于湿法刻蚀机中,采用化学溶液刻蚀掉周边的P/N结,同时去除磷硅玻璃,化学溶液可以为氢氟酸、硝酸、盐酸、硫酸及其它常规添加剂的一种或多种混合水溶液,刻蚀时间为0.5~10分钟,温度为5~20℃;(5)将湿刻后硅片背面镀氧化铝以及氮化硅薄膜后进行激光开槽工艺,激光开槽图形设计采用本实用新型的背面电极位置处断开设计;(6)背面印刷银背极以及铝背场,背电极采用本实用新型的八段式设计,背极背场连接处两端漏硅设计(由于此处背面沉积了背面叠层钝化膜氧化铝和氮化硅,此处露出的表面是该叠层模);(7)印刷正电极栅线,烧结后经过光衰处理设备进行光衰减处理。如表3所示,按照上述设计的测试结果表明:PERC电池组件端机械载荷测试PL值由原来的5%以上降低为1%以下,判定为合格:表3本实施例制备的单晶硅电池组件与常规电池组件的性能对比实施例4如图4所示,与实施例3不同的是,每列栅线包括六段相间隔设置的子栅线。按照上述设计的测试结果表明:PERC电池组件端机械载荷测试PL值由原来的6%以上降低为2%左右,判定为合格:表4本实施例制备的单晶硅电池组件与常规电池组件的性能对比上面列举一部分具体实施例对本实用新型进行说明,有必要在此指出的是以上具体实施例只用于对本实用新型作进一步说明,不代表对本实用新型保护范围的限制。其他人根据本实用新型做出的一些非本质的修改和调整仍属于本实用新型的保护范围。当前第1页1 2 3