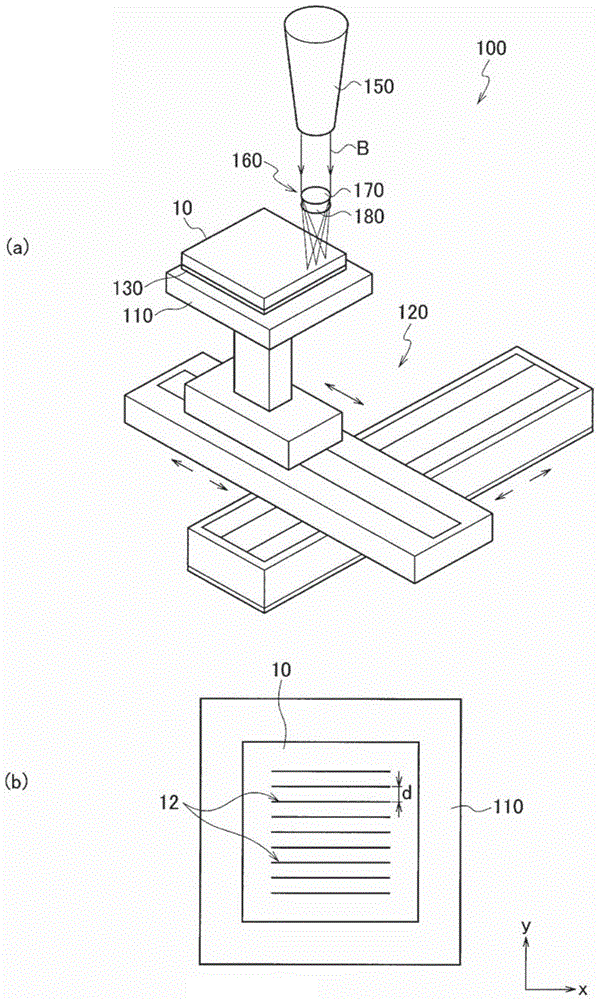
本发明涉及一种剥离基板制造方法,更具体地说,涉及一种对碳化硅、蓝宝石、氮化镓等进行激光加工的剥离基板制造方法。
背景技术:
:以往,在制造以硅(si)晶片为代表的半导体晶片的情况下,将在石英坩埚内熔融的硅熔液凝固得到的圆柱形晶锭切断成适当长度的块,对其周缘部进行磨削以得到目标直径,然后,使用钢丝锯将块化后的晶锭切割成晶片形,从而制造半导体晶片。需要说明的是,在该说明书中,除了另有说明的情况以外,将晶片适当地称为基板。如此操作制造的半导体晶片在前工序中依次实施电路图案的形成等各种处理,并供于后工序,在该后工序中对背面进行背面研磨处理而实现薄片化。另外近年来,硬度大、热导率也高的碳化硅(sic)受到关注,但由于硬度比晶体硅大的关系,不能使用钢丝锯容易地将晶锭切成片,另外,利用背面研磨进行的基板的薄层化也不容易。进一步对于作为难加工材的蓝宝石基板、氮化镓基板,也要求加工技术。另一方面,公开了如下技术:通过使高开口数的聚光透镜与由玻璃板构成的像差增强材组合,对晶片的内部照射脉冲状激光而形成加工层后,将其贴合于刚性基板,利用加工层进行剥离,从而得到薄的剥离基板(参照下述专利文献1)。现有技术文献专利文献专利文献1:日本特开2014-19120号公报技术实现要素:发明要解决的课题然而,为了制作剥离基板,如果想要利用激光对sic、蓝宝石、氮化镓的晶片等晶体材料进行加工,在内部形成加工层,则由于加工导致沿着晶体方向容易产生裂纹,难以形成稳定的加工层。本发明是鉴于上述情况而提供的发明,其课题在于提供一种能够抑制晶体材料中产生裂纹,且能够形成稳定的加工层并进行剥离的剥离基板制造方法。用于解决课题的方法为了解决上述课题,本发明的一个形态涉及的剥离基板制造方法包含基板加工步骤,该步骤具有激光聚光步骤和定位步骤,从而在所述基板上形成加工层,所述激光聚光步骤中,作为基板使用晶体基板,并利用激光聚光器向上述基板的表面照射来自脉冲照射的激光光源的激光,将激光聚光于从上述基板的表面起的基板内部的预定深度,所述定位步骤中,使上述激光聚光器相对于上述基板相对地移动并进行定位的定位。另外,包含基板剥离步骤,即利用上述加工层将通过上述基板加工步骤形成有上述加工层的上述基板剥离,制作剥离基板。而且,上述激光聚光步骤包含激光调节步骤:使用将来自上述激光光源的激光分支成多束分支激光的衍射光学元件,使上述多束分支激光的至少一束按照其强度不同于其他分支激光的方式进行分支。而且,在上述多束分支激光中,利用强度相对高的分支激光使上述加工层伸长而对上述基板进行加工,同时利用强度相对低的分支激光来抑制上述加工层的伸长。在上述激光调节步骤中,可以使上述多束分支激光在上述基板的内部配置成一列或多列或图案状。在上述激光调节步骤中,可以使上述多束分支激光中配置于端部侧的至少一束分支激光的强度低于其他分支激光。在上述激光调节步骤中,优选使上述强度相对高的分支激光的强度相对于上述强度相对低的分支激光的强度以1.1~5.0范围的倍率不同。上述定位步骤中,可以使上述激光聚光器在上述基板的表面沿着相对于上述一列或多列或图案状的方向形成预定角度的扫描方向以预定速度移动。上述定位步骤中,可以隔着使述激光聚光器沿与上述扫描方向正交的方向移位预定距离的动作而重复进行使上述激光聚光器在上述基板的表面沿上述扫描方向以预定速度移动的动作。也可以包含蚀刻步骤:作为蚀刻液使用熔融碱,在含氧的气体气氛下,一边使上述剥离基板中的上述熔融碱的界面位置在上述剥离基板上移动一边进行蚀刻。作为上述熔融碱,可以使用熔融氢氧化钠。可以一边使熔融碱流动一边进行蚀刻。可以通过使用sic基板作为上述基板,从而使上述剥离基板由sic构成。发明的效果根据本发明,能够提供一种能抑制晶体材料中产生裂纹,且能形成稳定的加工层并进行剥离的剥离基板制造方法。附图说明图1中,(a)是表示本发明的一个实施方式中的基板加工装置的斜视图,(b)是表示本发明的一个实施方式中载置在平台上的利用激光进行了加工的基板的平面图。图2中,(a)是说明本发明的一个实施方式中利用激光对载置在平台上的基板进行加工的示意性侧面截面图,(b)是说明本发明的一个实施方式中在基板中形成加工层的侧面截面图。图3中,(a)是说明本发明的一个实施方式中,对基板照射的三束分支激光的示意性平面图,(b)是说明本发明的一个实施方式中照射于基板的三束分支激光各自聚焦的示意性侧面截面图。图4是说明调节相邻的加工痕迹的间隔的示意性平面图。图5中,(a)~(c)分别是说明本发明的一个实施方式中逐渐蚀刻基板的示意性正视图。图6是图5(b)的局部放大侧视图。图7是表示在本发明的一个实施方式的变形例中,多束分支激光的强度分布的例子的图表图。图8是说明在本发明的一个实施方式的变形例中,配置成多列或图案状的多束分支激光的一个例子的示意性平面图。图9中,(a)是表示实施例1中利用激光形成于基板内部的加工痕迹的通过显微镜得到的照片图,(b)是(a)的局部放大图。图10是说明实施例2的照片图。图11是表示实施例2的剥离面的表面粗糙度的测定结果的照片图。图12是说明实施例3的照片图。图13是表示实施例3的剥离面的表面粗糙度的测定结果的照片图。图14是说明实施例4的照片。图15是表示实施例4的剥离面的表面粗糙度的测定结果的照片图。图16是说明实施例5的照片。图17是表示实施例5的剥离面的表面粗糙度的测定结果的照片图。图18是说明实施例6的照片。图19是表示实施例6的剥离面的表面粗糙度的测定结果的照片图。图20是表示实验例1中蚀刻后的基板面的粗糙度的图表图。图21是表示实验例1中蚀刻后的基板面的非浸渍部的界面附近的照片图。图22是表示实验例1中蚀刻后的基板面的浸渍部的照片图。图23是使用afm对实验例1中蚀刻后的非浸渍部进行拍摄得到的斜视图。图24是表示实验例2中蚀刻温度与蚀刻速率的关系的图表图。图25中,(a)是表示实验例2中浸渍部的蚀刻时间与粗糙度的关系的图表图,(b)是表示实验例2中非浸渍部的界面附近的蚀刻时间与粗糙度的关系的图表图。图26中,(a)是表示实验例2中氮流量与蚀刻速率的关系的图表图,(b)是表示实验例2中氮流量与粗糙度的关系的图表图。图27中,(a)是表示实验例2中空气流量与蚀刻速率的关系的图表图,(b)是表示实验例2中空气流量与粗糙度的关系的图表图。具体实施方式以下,参照附图,对本发明的实施方式进行说明。以下的说明中,对于与已经说明的构成要素相同或类似的构成要素赋予相同或类似的符号,并适当省略其详细说明。另外,以下所示的实施方式是用于将本发明的技术思想具体化的例示,本发明的实施方式并不将构成部件的材质、形状、结构、配置等限定于下述情况。本发明的实施方式可以在不脱离主旨的范围内进行各种变更来实施。图1中,(a)是表示在本发明的一个实施方式中的基板加工装置100的构成的斜视图,(b)是表示在本发明的一个实施方式中载置在平台上的利用激光加工的基板的平面图。本发明的一个实施方式(以下,称为本实施方式)中所使用的基板加工装置100具有:平台110、将平台110以能够在xy方向移动的方式支撑平台支撑部120、配置于平台110上并固定基板10的基板固定工具130。对于该基板10,可以使用作为将晶锭切断得到的晶体材料的碳化硅(sic)晶片。另外,基板加工装置100具有激光光源150和将从激光光源150发出的激光b聚光并向基板10照射的激光聚光部160(激光聚光器)。激光聚光部160具有衍射光学元件(doe)170和物镜180。衍射光学元件170将入射的激光b分支成预定束数的分支激光。分支激光通过物镜180而聚光,且配置为在激光聚光部160的焦点位置处排成一列。需要说明的是,在图中,衍射光学元件170生成三束分支激光,但不限于此。分支激光只要是两束以上的多束分支激光即可。衍射光学元件170按照多束分支激光的强度不同的方式进行调节。这里,按照多束分支激光的强度不同的方式进行调节是指:使多束分支激光的至少一束按照其强度不同于其他分支激光的方式进行分支。因此,分支成三束分支激光的情况中,两束分支激光的强度相同而剩余的一束分支激光的强度与该两束分支激光相比不同的情况是符合的。另外,也相邻的分支激光的强度彼此不同的情况也是符合的。本实施方式中,在多束分支激光中,可以使强度相对高的分支激光的强度相对于强度相对低的分支激光的强度以1.1~5.0范围的倍率不同。该倍率优选为1.2~3.0的范围,更优选为1.5~2.5的范围,进一步优选为1.8~2.2的范围。本实施方式中,通过按照使由衍射光学元件170分支的多束分支激光的强度不同的方式进行调节,从而能够控制在基板10的内部形成加工痕迹时产生的裂纹。即,利用多束分支激光中的强度相对高的分支激光,形成裂纹以相对于激光的照射方向成直角的方式伸长(扩展)的能够剥离的加工状态。而且,利用强度相对低的分支激光形成裂纹不伸长的加工层,起到防止利用强度高的分支激光形成的裂纹沿着晶体方向与意图相反地伸长(扩展)的阻止层的作用。图2中,(a)是说明利用激光对载置于平台上的基板进行加工的示意性侧面截面图,(b)是说明在基板中形成加工层的侧面截面图。基板10由平台110上的基板固定工具130保持。基板固定工具130通过设置于其上面的固定台125来固定基板10。固定台125可以应用通常的粘着层、机械卡盘、卡盘等。聚光并照射到基板10的激光b在距基板10表面的预定深度处形成聚光点f(激光聚光步骤),在距基板表面的预定深度位置形成预定形状的加工痕迹12。需要说明的是,本实施方式中,加工痕迹12伴随平台110的移动、即基板10的移动而排成列状。该加工痕迹12通过使激光聚光部160相对于保持在平台110上的基板10相对地移动来进行定位(定位步骤),从而在基板10的内部以预定的图案形成。例如,通过隔着沿与扫描方向形成预定角度θ(参照图4)的方向(例如90°(与扫描方向正交的方向)、45°)使聚光点f移位预定距离d(参照图1(b))的动作而重复进行沿预定的扫描方向使聚光点f以预定速度移动的动作,从而能够形成将直线状的加工痕迹12配置为二维状所得到的加工层14。(基板加工步骤)在基板加工装置100中,激光b通过激光聚光部160的衍射光学元件170和物镜180向基板10照射,分支光束分别聚光于基板10内部的聚光点f,在聚光点f形成加工痕迹12。激光聚光部160按照使基板10的预定深度的范围t内的分支激光的直径实质上缩小的方式进行聚光,以确保形成使加工痕迹12连接而成的加工层14所需的能量密度。图中示出了利用从基板10的表面侧入射的分支激光,在包含聚光点f的预定深度的范围t内形成的加工层14。加工层14是使利用各分支激光形成的加工痕迹12连接而成的层。如此形成的加工层14由于相邻的分支激光为预定间隔,因此具有预定的周期结构。图3中,(a)是基板10的示意性平面图,(b)是说明照射于基板的三束分支激光各自聚焦的示意性侧面截面图。向基板10的表面照射的三束分支激光ba、bb、bc在基板10的表面形成配置成一列的三个光束斑点ra、rb、rc并入射至基板10,并在基板10的内部形成三个聚光点fa、fb、fc。利用这些聚光点fa、fb、fc分别形成加工痕迹12a、12b、12c(参照图4)。由于基板10是sic等晶体基板,因此具有在形成聚光点fa、fb、fc时容易沿晶体方向产生裂纹的性质。在这种分支成三束分支激光ba、bb、bc的情况下,例如通过使中央的分支激光bb的强度大于两侧(即两端部侧)的分支激光ba、bc的强度(激光调节步骤),从而即使在利用中央的聚光点fb形成加工痕迹12时产生的裂纹向两侧的聚光点fa、fc的方向伸长,也能够通过利用两侧的聚光点fa、fc所形成的加工痕迹12来阻止裂纹的伸长。这时,分支激光ba、bc的强度设定为不会使加工痕迹从聚光点fa、fc沿晶体方向伸长(扩展)程度的强度,即能够得到剥离基板所需的加工痕迹的最小强度。关于三束分支光束的强度,可以按照相差1.1~5.0范围的倍率的方式设定中央的分支激光bb的强度相对于两侧的分支激光ba、bc的强度的倍率。该倍率优选为1.2~3的范围,更优选为1.5~2.5的范围,进一步优选为1.8~2.2的范围。图4是说明调节形成于基板10的相邻的加工痕迹12a~c的间隔的图。在基板10的表面,通过从光聚光部16供给的三束分支激光ba、bb、bc而形成有配置成一列的三个光束斑点ra、rb、rc。三束分支激光经由这些光束斑点ra、rb、rc而聚光于基板10内部的聚光点fa、fb、fc,在聚光点fa、fb、fc处分别形成加工痕迹。三个光束斑点ra~c沿预定的扫描方向以预定速度扫描。从激光光源150供给脉冲激光,通过脉冲照射使光束斑点ra~c在扫描方向以预定间隔形成。该扫描方向的间隔可以任意设定。另外,通过调节配置有三个光束斑点ra~c的列的方向,能够调节通过光束斑点ra~c形成的三条加工痕迹12a~c的间隔。图4(a)示出了将配置有三个光束斑点ra~c的列的方向设定为与扫描方向正交的情况。这时,对于与扫描方向正交的方向,三个光束斑点ra~c的相邻距离为最大,因此通过三个光束斑点ra~c形成的加工痕迹12a~c的间隔(彼此相邻的间隔)也最大。图4(b)示出了将配置有三个光束斑点ra~c的列的方向d设定为与扫描方向的正交方向形成预定角度θ的情况。图4(b)中,作为一例,描绘了形成θ=45°的角度的情况。预定角度θ不限于45°,θ越小,则光束斑点ra~c在与扫描方向正交的方向上的相邻距离越短,因此通过光束斑点ra~c形成的加工痕迹12a~c的间隔也变得越短。需要说明的是,将该θ设为90°、即将预定角度设为90°的情况为图4(a)所示的状态。本实施方式中,通过将形成有加工层14的基板10在加工层14处割断,并在加工层14处剥离基板10,从而能够制作剥离基板(基板剥离步骤)。由于在加工层14中加工痕迹相连接,因此基板10能够容易地沿着加工层14割断并进行剥离。因此,对于作为晶体材料的碳化硅(sic)晶片的基板10,能够抑制裂纹产生并形成稳定的加工层14。而且在本实施方式中,后续,对从加工层14剥离的剥离基板10p(从碳化硅晶片剥离的基板)进行碱蚀刻,使剥离基板10p的基板面10ps镜面化(蚀刻步骤)。图5(a)~(c)分别是说明通过本发明的一个实施方式(以下,称为本实施方式)涉及的蚀刻方法逐渐蚀刻基板的示意性正视图。图6是图5(b)的局部放大侧视图。在该蚀刻中,在含氧的气体气氛下使剥离基板10p中的熔融碱的界面位置在剥离基板上逐渐移动。本实施方式中,使剥离基板10p从上方以固定速度慢慢下降至装入至容器200的熔融碱al中来进行浸渍(参照图5(a)~(c))。其结果,剥离基板10p中的熔融碱al的界面位置g(熔融碱al的液面位置)从基板下端向上方逐渐移动。这里,如图5、图6所示,本说明书中界面位置g为与熔融碱al的液面位置相同的位置。在剥离基板10p的非浸渍部nim的界面附近v,在蚀刻反应时吸入气体气氛中的氧而促进氧化,高速地进行良好的蚀刻。因此,通过这样操作使剥离基板10p中的熔融碱al的界面位置g向基板上方逐渐移动,从而即使是由作为高硬度且为难加工材料的sic(碳化硅)构成的剥离基板10p,也能够在基板面10ps上以宽范围且高速地形成良好的镜面。更详细地说明的话,在液面的边界区域,熔融碱因表面张力而沿sic面向上爬,形成薄的熔融碱液的膜。而且,由于该膜薄,因此容易将空气中的氧供给至sic面,使氧化变得活跃。然后由熔融碱除去该氧化膜,将这样的循环活跃地反复进行。因此,可高效地促进镜面化(各向同性蚀刻)。因此,即与将剥离基板10p全部浸渍于熔融碱al中(整个基板成为浸渍部)相比,能够在非常的短时间内在剥离基板10p整面形成该良好的镜面。剥离基板10p的下降速度根据熔融碱的种类、温度、气体气氛中的氧浓度等以能够进行良好的蚀刻的方式决定。需要说明的是,关于蚀刻,可以进行各向同性蚀刻。为此,可以通过将剥离基板10p的氧化速度设为氧化被膜的溶解速度以上,以避免未被氧化的阶段的基板材料(sic)被蚀刻,从而即使在基板材料中产生缺陷(晶体缺陷),也可以在该缺陷被氧化后,也就是说成为氧化被膜后进行蚀刻。其结果,对剥离基板10p进行各向同性蚀刻。另外,通过将剥离基板10p浸渍于熔融碱al中,并使剥离基板10p从熔融碱al中以固定速度慢慢提起,从而即使使剥离基板10p中的熔融碱al的界面位置g(熔融碱al的液面位置)向基板下方逐渐移动,也能够在剥离基板10p的基板面10ps上以宽范围且高速地形成良好的镜面。作为熔融碱,可列举熔融氢氧化钠(naoh)、熔融氢氧化钾(koh)等,在对si面进行蚀刻时,从高效地除去si面(蚀刻速度的高速化)而进行镜面化的观点考虑,优选熔融氢氧化钠shl(参照图5、图6)。在这种情况下,如果使用处于650℃以上的熔融氢氧化钠,则容易进行这种高速且良好的蚀刻。如果温度低于650℃,则蚀刻速度(蚀刻速率)容易变低。需要说明的是,在不是对si面而是对c面进行蚀刻时,从高效地除去c面(蚀刻速度的高速化)而进行镜面化的观点考虑,优选使用熔融氢氧化钾。另外,可以一边使熔融碱al流动一边进行蚀刻。由此,能够防止因蚀刻而劣化的熔融碱滞留在基板面10ps附近。(变形例)需要说明的是,在上述实施方式中,作为多束分支激光的例子,例示了三束分支激光,但本发明不限于此。多束分支激光只要为两束以上的分支激光且强度不同即可。例如,如图7所示,可以为9束分支激光。多束分支激光配置成一列,图7(a)中两端的分支激光的强度小,中央的分支激光的强度大于两端的分支激光的强度。图7(b)中两端和中央的分支激光的强度小。需要说明的是,由于会影响剥离,因此为了加工层的稳定化,优选多束分支激光中包含相同强度的分支激光。另外,在上述实施方式中,例示了将多束分支激光在基板的内部配置成一列的情况,但本发明不限于此。可以使多束分支激光在基板的内部配置成多列或图案状。无论是一列、多列、还是图案状,都能够均等地形成加工层,能够在抑制裂纹产生的同时形成稳定的加工层。图8是表示照射于基板10的分支激光的光束斑点配置成多列或图案状的状态的一个例子的示意性平面图。分支激光在图中沿着与一点划线所表示的扫描方向正交的方向形成第1列的四个光束斑点r11、r12、r13、r14,第2列的四个光束斑点r21、r22、r23、r24,第3列的四个光束斑点r31、r32、r33、r34,第4列的四个光束斑点r41、r42、r43、r44。这些光束斑点形成由从第1列到第4列共计4列构成的多列配置。另外,还形成由在扫描方向的4列、在与扫描方向正交的方向的4列的共计4×4的16个光束斑点构成的图案。在这些光束斑点中,中央的四个光束斑点r22、r23、r32、r33与包围它们的其他光束斑点r11、r12、r13、r14、r21、r24、r31、r34、r41、r42、r43、r44相比强度相对大,例如可以处于1.1~5.0倍率的范围。需要说明的是,光束斑点所形成的多列只要是2列以上即可,光束斑点的图案只要是三个以上光束斑点所形成的特定图案即可。(实施例和实验例)以下,说明实施例(使用图1~图6说明的实施方式的实施例)和实验例。[实施例1]本实施例中,基板加工装置100的激光光源150使用innolighttechnologycorporation制halogn35k-100的激光振荡器。该激光光源150可以供给如表1所示的激光b。[表1]波长515nm脉冲能量100μj重复频率35khz最大平均输出功率3.5w脉冲宽度1.5nsm2(光束质量因子)约1.3衍射光学元件170使用从激光b分支成强度1∶2∶1的三束分支激光ba~c的古河机械金属工业制衍射光学元件。物镜180使用lcpln100×ir。基板10使用表面经镜面抛光的晶体结构4h的sic基板。而且,为了阐明加工痕迹12的性质,在表2所示的条件下对基板10进行加工。表2中,衍射光学元件的角度是由与扫描方向正交的方向和配置成一列的三个光束斑点ra、rb、rc的方向所形成的角度。另外焦点的深度为从相当于聚光点f的焦点起到基板10表面的深度。[表2]衍射光学元件的角度0°输出功率233mw扫描速度10mmps照射间隔0.29μm焦点的深度略低于100μm图9是表示通过如此加工而形成于基板10的加工痕迹12a~c的显微镜照片。图9(a)是从透明sic基板10的上表面进行观察而得到的照片,示出了通过三个光束斑点ra~c分别形成的三条加工痕迹12a~c。这里,由于衍射光学元件170生成强度1∶2∶1的三束分支激光ba、bb、bc,因此中央的加工痕迹12b稍微粗,而两侧的加工痕迹12a、12c稍微细。图9(b)是在与加工痕迹12的延伸方向大致垂直的截面中,观察形成于基板10上的加工痕迹12而得到的图片,示出了三条加工痕迹12a~c。这里,观察到裂纹从各加工痕迹沿横向方向伸长(扩展),从中央的加工痕迹12b伸长(扩展)的裂纹cp、cq分别伸长(扩展)至两侧的加工痕迹12a、12c,但分别被两侧的加工痕迹12a、12c阻止。因此可知,这三条加工痕迹12a~c通过裂纹cp、cq而连接,并且裂纹cp、cq的进一步伸长(扩展)得以抑制。[实施例2]接着,利用在基板10的整个表面所形成的加工痕迹12而制作加工层14后,通过利用加工层14割断基板10而进行剥离,从而制作剥离基板,并调查剥离基板的剥离面的性质。实施例2中,在表3的实施例2的栏中所示的条件下形成加工层14。除了表3所示的条件以外,使用与实施例1相同的条件。例如,基板10使用晶体结构4h的多晶体的sic基板,衍射光学元件170使用分支成三束分支激光的衍射光学元件。需要说明的是,表3中也同时示出了后述的实施例3~6的条件。[表3]图10(a)和图10(b)是表示实施例2中形成于基板10上的划线前和划线后的加工痕迹的显微镜照片。图10(c)是使用激光显微镜观察得到的基板10的截面的显微镜照片,图10(d)是将图10(c)的框内放大了的放大显微镜照片。根据图10(c)和图10(d),观察到在与基板10的表面平行的方向即图中横向方向形成有加工痕迹12连接而成的加工层14。图10(e)是表示使用拉伸试验机在加工层14处割断得到的剥离基板的剥离面的照片。该实施例2中,在相对于剥离基板的整个表面的90%部分形成了剥离面。接着,测定剥离基板的剥离面的表面粗糙度。在朝向激光聚光部160的激光照射侧的上表面,对于ra(μm)成为了图11(a)那样的形状,对于rz(μm)成为了图11(b)那样的形状,得到了如表4所示的结果。在该表4中,示出了表面粗糙度的3点测定值和它们的平均值。以下也同样。需要说明的是,表4中“扫描方向”的粗糙度表示在扫描激光的方向上的粗糙度,“偏移方向”的粗糙度表示在相对于扫描方向成90°的方向上形成于分支光束间的粗糙度。在后述的表5~表7中也同样。另外,在载置在平台110的一侧的下表面,对于ra(μm)成为了图11(c)那样的形状,对于rz(μm)成为了图11(d)那样的形状,得到了如表5所示的结果。[表4]激光照射侧[表5]平台侧[实施例3]图12(a)和(b)分别是表示实施例3中形成于基板10上的划线前和划线后的加工痕迹的显微镜照片。图12(c)是使用激光显微镜观察得到的基板10的截面的显微镜照片,图12(d)是将图12(c)的框内放大了的放大显微镜照片。实施例3中,在表3的实施例3的栏中所示的条件下形成加工层14。除了表3中所示的条件以外,在与实施例2相同的条件下进行。该实施例3中,在剥离基板表面的50%形成了剥离面。关于剥离基板的剥离面的表面粗糙度,在激光照射侧的上表面,对于ra(μm)成为了图13(a)那样的形状,对于rz(μm)成为了图13(b)那样的形状,得到了如表6所示的结果。另外,在平台侧的下表面,对于于ra(μm)成为了图13(c)那样的形状,对于rz(μm)成为了图13(d)那样的形状,得到了如表7所示的结果。[表6]激光照射侧[表7]平台侧[实施例4]图14(a)和(b)分别是表示实施例4中形成于基板10上的划线前和划线后的加工痕迹的显微镜照片。图14(c)是使用激光显微镜观察得到的基板10的截面的显微镜照片,图14(d)是将图14(c)的框内放大了的放大显微镜照片。实施例4中,在表3的实施例4的栏中所示的条件下形成加工层14。除了表3中所示的条件以外,在与实施例2相同的条件下进行。该实施例4中,在剥离基板表面的30%形成了剥离面。关于剥离基板的剥离面的表面粗糙度,在激光照射侧的上表面,对于ra(μm)成为了图15(a)那样的形状,对于rz(μm)成为了图15(b)那样的形状,得到了如表8所示的结果。另外,在平台侧的下表面,对于ra(μm)成为了图15(c)那样的形状,对于rz(μm)成为了图15(d)那样的形状,得到了如表9所示的结果。[表8]激光照射侧[表9]平台侧[实施例5]图16(a)和(b)分别是表示实施例5中形成于基板10上的划线前和划线后的加工痕迹的显微镜照片。图16(c)是使用激光显微镜观察得到的基板10的截面的显微镜照片,图16(d)是将图16(c)的框内放大了的放大显微镜照片。实施例5中,在表3的实施例6的栏中所示的条件下形成加工层14。除了表3中所示的条件以外,在与实施例2相同的条件下进行。该实施例5中,在剥离基板表面的98%形成了剥离面。关于剥离基板的剥离面的表面粗糙度,在激光照射侧的上表面,对于ra(μm)成为了图17(a)那样的形状,对于rz(μm)成为了图17(b)那样的形状,得到了如表10所示的结果。另外,在平台侧的下表面,对于ra(μm)成为了图17(c)那样的形状,对于rz(μm)成为了图17(d)那样的形状,得到了如表11所示的结果。[表10]激光照射侧[表11]平台侧[实施例6]图18(a)和(b)分别是表示实施例6中形成于基板10上的划线前和划线后的加工痕迹的显微镜照片。图18(c)是使用激光显微镜观察得到的基板10的截面的显微镜照片,图18(d)是将图18(c)的框内放大了的放大显微镜照片。实施例6中,在表3的实施例6的栏中所示的条件下形成加工层14。除了表3中所示的条件以外,在与实施例2相同的条件下进行。该实施例6中,在剥离基板表面的10%形成了剥离面。关于剥离基板的剥离面的表面粗糙度,在激光照射侧的上表面,对于ra(μm)成为了图19(a)那样的形状,对于rz(μm)成为了图19(b)那样的形状,得到了如表12所示的结果。另外,在平台侧的下表面,对于ra(μm)成为了图19(c)那样的形状,对于rz(μm)成为了图19(d)那样的形状,得到了如表13所示的结果。[表12]激光照射侧[表13]平台侧根据以上的实施例2~6可知,使用分割成三束分支激光的衍射光学元件170,在由晶体结构4h的sic制成的基板10上形成加工层14,利用加工层14进行割断并进行剥离,从而能够容易地制作剥离基板。另外,根据表面粗糙度的测定可知,在剥离基板上形成了光滑的剥离面。这里,在实施例2~6中,未观察到对加工速度、激光强度的明确依赖性。故此推测:通过利用分支光束抑制了加工层的伸长,从而不易受到加工条件的影响。另外,在实施例1~6中,使用了晶体结构4h的sic的基板10,但不限于此,也可以同样地应用于晶体结构6h的sic的基板。另外,不限于sic的基板,也可以同样地应用于蓝宝石的基板等。另外,在实施例2~6中,在基板10的表面仅平行地形成了一层加工层14,但通过利用激光聚光部160适当地设定聚光点f的深度,也可以形成两层以上的加工层14,利用这些加工层14割断基板10并进行剥离。需要说明的是,在实施例2~6中,在制作剥离基板后,使用熔融碱对该剥离基板进行蚀刻的情况下,优选通过对基板面进行金刚石研磨等作为前处理来调节基板面的表面粗糙度后进行蚀刻。由此,容易得到镜面化的良好蚀刻面。<实验例1(通过湿蚀刻确认高速镜面化现象)>本实验例中,通过将sic晶片在naoh(熔融氢氧化钠)中浸渍一半左右,从而在产生有浸渍于naoh溶液的浸渍部im和未浸渍于naoh溶液的非浸渍部nim的状态下进行蚀刻。(实验条件和实验方法)本发明人等向ni(镍)制的坩埚中放入约5g固体的naoh,使用电炉进行加热使其成为750℃的熔融状态,将用ni线固定的sic晶片(sic基板)在已熔融的naoh溶液中浸渍一半左右,进行20分钟的蚀刻。所使用的晶片为偏角4°、10mm见方的4h-sic晶片。作为前加工,使用金刚石砂轮(sd#1000)实施磨削。蚀刻速率的评价由蚀刻前后的厚度差来求出。粗糙度测定使用触针式粗糙度测定机(taylorhobson公司制pgi840)。(蚀刻面的外观和形状)图20示出了蚀刻后的sic晶片表面的形状。在用于得到图20的测量中,测量基板面上沿着直线的表面的高度。从图20可知,与浸渍部im相比,非浸渍部nim更被蚀刻除去。特别是在非浸渍部nim中,在距界面位置g1mm的区域,比浸渍部im多被除去了60μm。(蚀刻表面的详细观察)另外,使用激光显微镜图像观察并拍摄浸渍部im和非浸渍部nim(也包含界面附近v)。将拍摄结果分别示于图21、图22中。在浸渍部im中观察到蚀刻坑的产生(参照图22),在非浸渍部nim确认到其是无蚀刻坑的平滑面(参照图21)。进一步将使用afm测量1μm×1μm非浸渍部nim而得到的结果示于图23中。该测量的结果,确认了其是粗糙度为0.54nmra、8.7nmrz的镜面。<实验例2(蚀刻的基础特性的调查)>本实验例中,进行实验以调查蚀刻的特性如何受温度、气体气氛等的影响。(温度对于到达表面粗糙度和蚀刻速率的影响)以实验例1的实验方法为基础,进行将实验时间设为20~120分钟、将温度设为600~750℃的蚀刻实验。本实验例中,对于浸渍部im和非浸渍部nim的界面附近v调查蚀刻温度和蚀刻速率的关系。将实验结果示于图24中。可知:浸渍部im、界面附近v均存在温度越高则蚀刻速率越大的倾向,且增大的比例两者均为相同程度。而且,在界面附近v的蚀刻速率比浸渍部im高2~3倍程度。特别是在750℃时成为高达289μm/h的值。另外,图25(a)示出了浸渍部im的蚀刻面的粗糙度,图25(b)示出了非浸渍部nim的界面附近v的蚀刻面的粗糙度。在浸渍部im中观察到粗糙度一度增大,然后减少的倾向。根据蚀刻面的观察结果来思考,推测是因为:在蚀刻初期出现由金刚石磨削造成的潜伤,然后慢慢变得平滑。另外认为:在浸渍部im中蚀刻速率低,在120分钟的实验中没有足够的时间减少浸渍部im的粗糙度。但是认为,由于观察到蚀刻坑逐渐增加的倾向,因此难以适用于镜面化。另一方面可知:在非浸渍部nim中,如果为700℃以上,则到达表面粗糙度达到1.4nmra。而且,根据蚀刻面的观察结果,在任何条件下均未观察到蚀刻坑的产生。关于该蚀刻坑,根据在蚀刻速率低于23μm/h的处理条件即600℃120分钟的蚀刻处理后的观察结果,也没有观察到蚀刻坑的产生。(气氛对于粗糙度和蚀刻速率的影响)基于实验例1的实验条件,将实验时间设为30分钟,在气体气氛为大气的情况和氮气(用于排除氧气而制成非活性的气体)的情况下分别进行实验,调查其影响。(氮气气氛的影响)一边使氮气流入电炉内一边进行蚀刻。对于浸渍部im和非浸渍部nim的界面附近v,分别将氮流量与蚀刻速率的关系示于图26(a)中,将氮流量与粗糙度的关系示于图26(b)中。需要说明的是,图26(a)中氮流量0l/min是指没有使氮气流入因而电炉内为大气气氛的状态。关于蚀刻速率,浸渍部im、界面附近v在氮流量10l/min均大大降低,在其以上的流量下没有观察到进一步的变化。另一方面,关于粗糙度,浸渍部im、界面附近v均存在氮流量越增加则越增大的倾向。因此推测,蚀刻时首先会露出由磨削造成的潜伤,然后消失,从而成为镜面。根据蚀刻面的观察结果,浸渍部im、界面附近v均观察到潜伤,认为粗糙度的增大倾向是因为蚀刻速率的降低而导致了镜面工艺的钝化。(大气的影响)接着,进行了用于调查大气影响的蚀刻。对于浸渍部im和非浸渍部nim的界面附近v,分别将空气流量与蚀刻速率的关系示于图27(a)中,将空气流量与粗糙度的关系示于图27(b)中。浸渍部im、界面附近v均无论空气流量如何,蚀刻速率基本上都没有变化。然而可知,在相同的蚀刻时间内,在浸渍部im中,空气流量越增加则潜伤越被除去。另外在空气流量为20l/min时,在界面附近v会形成膜状的凹凸,粗糙度显著增大。通过以上的实验结果、推测可知,空气对蚀刻起作用。因此认为,在非浸渍部nim中,在碱蒸气或通过表面张力形成的熔融碱液的薄膜与sic反应时,吸入大气的氧而促进氧化。<实验例1、2的汇总>如以上所说明,根据实验例1、2,在使用naoh溶液对sic基板的湿蚀刻中,发现了非浸渍部的sic晶片面的高效镜面化现象。根据用于调查其基础特性的实验可知,通过750℃、20分钟的蚀刻,到达表面粗糙度成为1.4nmra,通过750℃、45分钟的蚀刻,蚀刻速率达到最大的304μm/h。进一步可知在蚀刻气氛中,空气发挥作用。本申请主张基于2017年2月16日申请的日本专利申请第2017-027121号的优先权,这些申请的全部内容通过参照而被引入本说明书中。产业上的可利用性根据本发明,由于能够高效地较薄地形成剥离基板,因此能够用于半导体领域、显示器领域、能量领域等广泛的领域,例如,如果是作为单晶体基板的si基板(硅基板),则能应用于太阳能电池,另外,如果是gan系半导体器件等蓝宝石基板等,则能应用于发光二极管、激光二极管等,如果是sic等,则能应用于sic系功率器件等,也能够适用于透明电子产品领域、照明领域、混合动力/电动汽车领域等广泛的领域。符号说明10:基板(晶体基板、sic基板),10p:剥离基板,14:加工层,150:激光光源,160:激光聚光部(激光聚光器),170:衍射光学元件,al:熔融碱,b:激光,ba~c:分支激光,shl:熔融氢氧化钠,θ:预定角度。当前第1页12