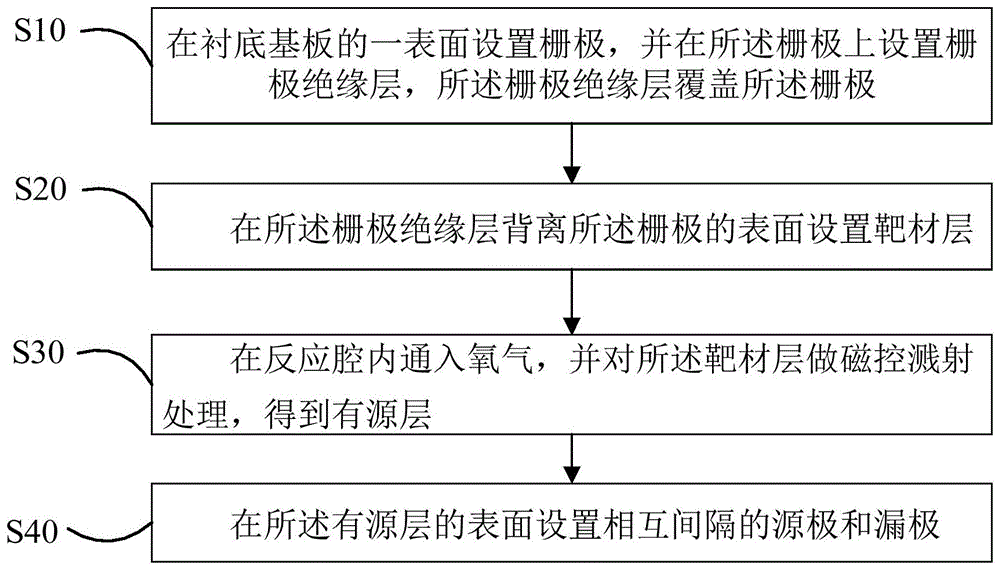
本发明涉及显示
技术领域:
,特别涉及一种阵列基板的制作方法、阵列基板和显示面板。
背景技术:
:目前的lcd(liquidcrystaldisplay,液晶显示面板)因其电压低,功耗低,方便携带的优势,使之成为显示技术的主流技术。但近几年发展的oled(organiclight-emittingdiode,有机发光半导体)技术具有比lcd更显著的优势,如亮度更高,色彩更逼真,对比度更高,还不需要背光源,因此是未来显示技术的发展方向。通常液晶显示面板包括(colorfilter,cf,彩膜基板)、薄膜晶体管、(thinfilmtransistor,tft,阵列基板)、及设于cf基板与tft阵列基板之间的液晶(liquidcrystal)。通过对tft阵列基板供电与否来控制液晶分子改变方向,将背光模组的光线投射到cf基板产生不同色彩显示。tft阵列基板的性能特征和运行特性很大程度上取决于设置tft阵列基板的半导体元件特性。现有的tft阵列基板通常采用非晶硅(a-si)材料来制作半导体层,然而,随着液晶显示装置朝着大尺寸(75寸以上)和高分辨率(8k4k)的方向发展以及源漏极中金属铜(cu)的使用,传统的a-si仅有1cm2/(vs)左右的迁移率已经无法满足要求,以铟镓锌氧化物(igzo,indiumgalliumzincoxide)为代表的金属氧化物材料具备超过15cm2/(vs)以上的迁移率。而有源层在制作过程中,一般不在反应腔内通氧,导致有源层薄膜的性能不稳定,影响元器件的性能。技术实现要素:本发明的主要目的是提供一种阵列基板的制作方法,旨在使有源层在制作过程中具有一定的氧气体积流量,保证有源层的性能稳定和元器件的性能稳定。为实现上述目的,本发明提供一种阵列基板的制作方法,该阵列基板的制作方法包括:在衬底基板的一表面设置栅极,并在所述栅极上设置栅极绝缘层,所述栅极绝缘层覆盖所述栅极;在所述栅极绝缘层背离所述栅极的表面设置靶材层;在反应腔内通入氧气,并对所述靶材层做磁控溅射处理,得到有源层;在所述有源层的表面设置相互间隔的源极和漏极。可选地,所述在反应腔内通入氧气,并对所述靶材层做磁控溅射处理,得到有源层的步骤包括:打开氧气流量控制开关;控制在所述反应腔内通入氧气的氧气体积流量为:0.5sccm-2sccm;将铟镓锌的原子比为0.4:0.25:1的铟镓锌氧化物薄膜作为靶材层;对铟镓锌氧化物薄膜进行磁控溅射处理;在退火温度为350℃至450℃的温度下,对所述铟镓锌氧化物薄膜进行退火处理,得到有源层。可选地,在所述反应腔内通入氧气的氧气体积流量为:0.8sccm-1.5sccm。可选地,所述在退火温度为350℃至450℃的温度下,对所述铟镓锌氧化物薄膜进行退火处理的步骤包括:将所述铟镓锌氧化物薄膜的温度升高至退火温度,所述退火温度的范围为:350℃至450℃;预设退火时长为10min-90min;根据所述退火时长,将所述铟镓锌氧化物的温度自退火温度降回常温。可选地,所述对铟镓锌氧化物薄膜进行磁控溅射处理的步骤包括:将铟镓锌氧化物薄膜放置于反应腔内;预设磁控溅射时长为:100s-120s;根据所述磁控溅射时长对所述铟镓锌氧化物薄膜进行进行磁控溅射。可选地,其特征在于,所述铟镓锌氧化物薄膜经过磁控溅射后的厚度h为:20nm-40nm。可选地,所述铟镓锌氧化物经薄膜过磁控溅射后的厚度h为30nm;且/或,所述退火温度为400℃。本发明还提出一种阵列基板,包括该阵列基板采用上述任一项所述的阵列基板的制作方法制作,该阵列基板包括:衬底基板;栅极,所述栅极设于所述衬底基板的一表面;栅极绝缘层,所述栅极绝缘层设于所述栅极背离所述阵列基板的一侧,并覆盖所述栅极;有源层,所述有源层设于所述栅极绝缘层背离所述栅极的表面,所述有源层包括在通氧状态下磁控溅射处理的靶材层;源极,所述源极设于所述有源层背离所述栅极绝缘层的表面;以及漏极,所述漏极设于所述有源层背离所述栅极绝缘层的表面,并与所述源极间隔设置。本发明还提出一种显示面板,包括彩膜基板和上述所述的阵列基板,所述彩膜基板与所述阵列基板相对设置,所述显示面板还包括液晶层,所述液晶层设置于所述彩膜基板和所述阵列基板之间。本发明的技术方案通过在衬底基板的一表面设置栅极,并在所述栅极上设置栅极绝缘层,所述栅极绝缘层覆盖所述栅极;并在所述栅极绝缘层背离所述栅极的表面设置靶材层;再对所述靶材层进行通氧并做磁控溅射处理,得到有源层,由于在制作有源层时通入氧气,而氧气能使磁控溅射时靶材层的设置氧化膜,从而有源层表面缺陷态密度降低,并减少有源层载流子浓度,保证了栅压对沟道电流的调控能力,最后在所述有源层的表面设置相互间隔的源极和漏极,从而便于对液晶进行控制。如此,本发明的技术方案可以使有源层在制作过程中具有一定的氧气体积流量,保证有源层的性能稳定和元器件的性能稳定。附图说明为了更清楚地说明本发明实施例或现有技术中的技术方案,下面将对实施例或现有技术描述中所需要使用的附图作简单地介绍,显而易见地,下面描述中的附图仅仅是本发明的一些实施例,对于本领域普通技术人员来讲,在不付出创造性劳动的前提下,还可以根据这些附图示出的结构获得其他的附图。图1为本发明阵列基板的制作方法一实施例的流程示意图;图2为本发明阵列基板的制作方法另一实施例的流程示意图;图3为本发明阵列基板的制作方法又一实施例的流程示意图;图4为本发明阵列基板的制作方法再一实施例的流程示意图;图5为本发明阵列基板一实施例的结构示意图。附图标号说明:标号名称标号名称100阵列基板70有源层10衬底基板80源极30栅极90漏极50栅极绝缘层本发明目的的实现、功能特点及优点将结合实施例,参照附图做进一步说明。具体实施方式下面将结合本发明实施例中的附图,对本发明实施例中的技术方案进行清楚、完整地描述,显然,所描述的实施例仅仅是本发明的一部分实施例,而不是全部的实施例。基于本发明中的实施例,本领域普通技术人员在没有作出创造性劳动前提下所获得的所有其他实施例,都属于本发明保护的范围。需要说明,本发明实施例中所有方向性指示(诸如上、下、左、右、前、后……)仅用于解释在某一特定姿态(如附图所示)下各部件之间的相对位置关系、运动情况等,如果该特定姿态发生改变时,则该方向性指示也相应地随之改变。另外,在本发明中涉及“第一”、“第二”等的描述仅用于描述目的,而不能理解为指示或暗示其相对重要性或者隐含指明所指示的技术特征的数量。由此,限定有“第一”、“第二”的特征可以明示或者隐含地包括至少一个该特征。另外,各个实施例之间的技术方案可以相互结合,但是必须是以本领域普通技术人员能够实现为基础,当技术方案的结合出现相互矛盾或无法实现时应当认为这种技术方案的结合不存在,也不在本发明要求的保护范围之内。本发明提出一种阵列基板的制作方法。参照图1至图4,本发明技术方案提出的阵列基板的制作方法包括:步骤s10,在衬底基板10的一表面设置栅极30,并在所述栅极30上设置栅极绝缘层50,所述栅极绝缘层50覆盖所述栅极30;步骤s20,在所述栅极绝缘层50背离所述栅极30的表面设置靶材层;步骤s30,在反应腔内通入氧气,并对所述靶材层做磁控溅射处理,得到有源层70;步骤s40,在所述有源层70的表面设置相互间隔的源极80和漏极90。本发明的技术方案通过在衬底基板10的一表面设置栅极30,并在所述栅极30上设置栅极绝缘层50,所述栅极绝缘层50覆盖所述栅极30;并在所述栅极绝缘层50背离所述栅极30的表面设置靶材层;再对所述靶材层进行通氧并做磁控溅射处理,得到有源层70,由于在制作有源层70时通入氧气,而氧气能使磁控溅射时靶材层的设置氧化膜,从而有源层70表面缺陷态密度降低,并减少有源层70载流子浓度,保证了栅压对沟道电流的调控能力,最后在所述有源层70的表面设置相互间隔的源极80和漏极90,从而便于对液晶进行控制。如此,本发明的技术方案可以使有源层70在制作过程中具有一定的氧气体积流量,保证有源层70的性能稳定和元器件的性能稳定。在本申请的一实施例中,该阵列基板100包括的衬底基板10可以是玻璃、塑料或者其它透明材料,只要能为显示面板的各部件进行支撑,方便用户使用即可。该衬底基板10上可阵列分布多个该薄膜晶体管。同时,该薄膜晶体管可以是底栅型薄膜晶体管或顶栅型薄膜晶体管,以下仅以底栅型薄膜晶体管为例进行说明。在本申请的一实施例中,所述在衬底基板10的一表面设置栅极30的步骤包括:在所述衬底基板10上沉积第一金属薄膜;采用光刻过程对第一金属层进行图案化处理,得到栅极30。具体地,采用光刻过程对第一金属层进行图案化处理包括:在第一金属薄膜上光阻;在光阻上设置光罩,该光罩包括透光区和遮光区,将光罩对准光阻后,用光源照射光罩,使部分光通过透光区,照射在光阻上曝光;用显影液使未被光照射的部显影;用酸性气体对光阻和第一金属薄膜进行蚀刻;用去光阻液对光阻进行清洗,从而得到栅极30。可以理解的是,该栅极30的材料包括钼(mo)、铝(al)、铜(cu)、钛(ti)、铬(cr)中的一种或多种。均能使栅极30较好地控制阴极表面电场强度从而改变阴极发射电子或捕获二次放射电子的作用。在本申请的一实施例中,还可采用溅射(sputter)工艺沉积形成栅极30,具体而言,可以选用al、al/mo或al的合金类靶材通入氩气进行溅射而形成栅极30,栅电极层的厚度可以为300nm~400nm,但不以此为限。然后,可通过掩膜光刻工艺形成掩膜图形,最后,可采用湿法刻蚀工艺形成栅极30的图案。当然,在本公开的其它实施方式中,也可以通过真空镀膜等其它工艺形成栅极30,在此不再详述。在本申请的一实施例中,可以通过化学气相沉积方法获得栅极绝缘层50,以栅极绝缘层50为sinx为例,可使用等离子体增强化学的气相沉积(pecvd)在栅极30上面沉积sinx膜层,具体而言,以sih4、nh3、n2等气体作为反应气体,反应温度约350℃,完成sinx膜层的沉积,膜厚约300nm~400nm。当然,在本公开的其它实施方式中,也可以通过真空镀膜等其它工艺形成栅极绝缘层50,在此不再详述。化学气相沉积是一种化工技术,该技术主要是利用含有薄膜元素的一种或几种气相化合物或单质、在衬底表面上进行化学反应生成薄膜的方法。化学气相淀积是近几十年发展起来的制备无机材料的新技术。化学气相淀积法已经广泛用于提纯物质、研制新晶体、淀积各种单晶、多晶或玻璃态无机薄膜材料。这些材料可以是氧化物、硫化物、氮化物、碳化物,也可以是iii-v、ii-iv、iv-vi族中的二元或多元的元素间化合物,而且它们的物理功能可以通过气相掺杂的淀积过程精确控制。从而获得性能稳定的栅极绝缘层50。在得到对所述靶材层做磁控溅射处理和得到有源层70的步骤之间,还可以通过光刻和湿法刻蚀形成氧化物有源层70的图形。当然,在本公开的其它实施方式中,也可以通过真空镀膜等其它工艺形成氧化物有源层70,在此不再详述。此外,在形成氧化物有源层70的图形后,还可对氧化物有源层70进行退火处理,对氧化物有源层70的膜层致密性进行改善,降低栅极绝缘层50的表面自由能,减少接触界面的陷阱和缺陷,同时,对氧化物有源层70内的氧空位浓度进行平衡,实现优化和稳定前沟道电子迁移率的效果。源漏极90层包括源极80和漏极90,举例而言,可使用al或cu/monb的靶材通入氩气进行溅射沉积得到源漏金属膜层,膜厚可为300nm~400nm,但不限于该范围;通过光刻和湿法刻蚀形成源极80和漏极90的图形。当然,在本公开的其它实施方式中,也可以通过其它工艺形成源漏极90层,在此不再详述。在本实施例中,将源极80和漏极90的材料设置为铝,把铝作为源极80和漏极90是因为铝的价格便宜,而且镀膜工艺简单,大大降低生产成本,对设备的要求低。参照图2,在本申请的一实施例中,所述在反应腔内通入氧气,并对所述靶材层做磁控溅射处理,得到有源层70的步骤包括:步骤s31,打开氧气流量控制开关;步骤s32,控制在所述反应腔内通入氧气的氧气体积流量为:0.5sccm-2sccm;步骤s33,将铟镓锌的原子比为0.4:0.25:1的铟镓锌氧化物薄膜作为靶材层;步骤s34,对铟镓锌氧化物薄膜进行磁控溅射处理;步骤s35,在退火温度为350℃至450℃的温度下,对所述铟镓锌氧化物薄膜进行退火处理,得到有源层70。在本实施例中,该流量控制开关可以为流量控制传感器,可以理解的是,该反应腔还设有压力传感器,从而保证在一定的压强下对有源层70进行制作。在本申请的一实施例中,靶材层的设置同样可以采用溅射工艺形成,该靶材层包括铟镓锌原子,其中靶材层的铟镓锌各成分的比例可为in:ga:zn=0.4:0.25:1,再通入体积流量为0.5sccm-2sccm的氧气,以及通入稀有气体进行溅射工艺,当氧气通入反应腔的体积流量小于0.5sccm时,会导致有源层70的膜层致密度不足,载流子的浓度较高,不利于元器件的使用;当氧气体积流量高于2sccm时,会导致有源层70对电子的俘获和散射作用增强,从而导致栅压对沟道电流的调控能力变差,器件性能恶化。当氧气体积流量的范围为0.5sccm-2sccm时,可以较好地保证有源层70的表面缺陷态密度降低,改善有源层70膜层的致密性,并较好地减少载流子的浓度,此时元器件的迁移率、阈值电压、开关比和亚阈值摆幅的数值较佳,便于元器件工作。可以理解的是,氧气的体积流量还可以为0.6sccm、0.7sccm、1.6sccm、1.7sccm、1.8sccm、1.9sccm等,均能较好地保证有源层70的表面缺陷态密度降低,改善有源层70膜层的致密性,并较好地减少载流子的浓度。在对有源层70进行磁控溅射处理之后和退火处理之前,还可以通过光刻和湿法刻蚀形成有源层70的图形,从而便于有源层70的使用。在形成有源层70之后,再对有源层70进行退火处理。通过退火,可以对有源层70的膜层表面的致密性进行改善,并且降低栅极绝缘层50的表面自由能,减少接触界面的缺陷。同时,可以对有源层70内的氧空位浓度进行平衡,实现优化和稳定前沟道电子迁移率的效果。本申请可选的实施例中,可以将退火温度设置在350℃至450℃之间,有源层70的退火环境可以处于纯氧环境下或氧气/氮气的环境下,从而使有源层70的膜层表面的表面粗糙度较小,降低沟道处表面缺陷态密度,提高元器件性能。在本申请的一实施例中,在所述反应腔内通入氧气的氧气体积流量为:0.8sccm-1.5sccm。当氧气体积流量的范围为0.8sccm-1.5sccm时,可以最好地保证有源层70的表面缺陷态密度降低,改善有源层70膜层的致密性,并最好地减少载流子的浓度,此时元器件的迁移率、阈值电压、开关比和亚阈值摆幅的数值最佳,便于元器件工作。当然,该氧气的体积流量的取值还可以是0.9sccm、1sccm、1.1sccm、1.2sccm、1.3sccm、1.4ccm等,均能便于元器件工作。参照图3,在本申请的一实施例中,所述在退火温度为350℃至450℃的温度下,对所述铟镓锌氧化物薄膜进行退火处理的步骤包括:步骤s351,将所述铟镓锌氧化物薄膜的温度升高至退火温度,所述退火温度的范围为:350℃至450℃;步骤s352,预设退火时长为10min-90min;步骤s353,根据所述退火时长,将所述铟镓锌氧化物的温度自退火温度降回常温。在本实施例中,对铟镓锌氧化物薄膜进行加热,使其温度升高至350摄氏度至450摄氏度之间,当温度低于350摄氏度时,温度较低,不利于有源层70和栅极绝缘层50沟道处的连接;当温度低于450摄氏度时,温度较高,有源层70和栅极绝缘层50沟道处反应较快,不利于形成平整的有源层70;当退火温度位于350摄氏度至450摄氏度时,可以使有源层70和栅极绝缘层50沟道处平滑过渡,可以较好的降低有源层70的膜层表面粗糙度,可以理解的是,该退火温度还可以为360℃、370℃、380℃、390℃、400℃、410℃、420℃、430℃、440℃等均可以使有源层70和栅极绝缘层50沟道处平滑过渡,可以较好的降低有源层70的膜层表面粗糙度。并且设置退火时间控制退火过程,该退火处理的退火时间可以为10min-90min,当退火时间小于10min时,有源层70和栅极绝缘层50的沟道处缺陷反应时间较短,不利于形成较好的平整度;当退火时间大于90min时,反应时间过长,此时的沟道处缺陷已经较小,不利于降低生产成本,当退火时间的范围位于10min-90min内时,有源层70和栅极绝缘层50沟道处的缺陷具有足够长的时间进行平整化连接,从而减小有源层70的膜层表面粗糙度。可以理解的是,该退火时间还可以为15min、20min、30min、40min、50min、60min、70min、75min、85min均可使有源层70和栅极绝缘层50沟道处的缺陷具有足够长的时间进行平整化连接,从而减小有源层70的膜层表面粗糙度。并且,可以在反应腔内设置温度传感器,以实时检测反应腔内的退火状况,进一步减小有源层70的膜层表面粗糙度。参照图4,在本申请的一实施例中,所述对所述靶材层做磁控溅射处理的步骤包括:步骤s341,将铟镓锌氧化物薄膜放置于反应腔内;步骤s342,预设磁控溅射时长为:100s-120s;步骤s343,根据所述磁控溅射时长对所述铟镓锌氧化物薄膜进行磁控溅射。当磁控溅射的时长小于100s时,有源层70的膜厚较低,不利于在退火过程中改善与栅极绝缘层50沟道处的平滑度;当磁控溅射的时长大于120s时,导致膜厚较大,提高了生产成本,当磁控溅射的时长在100-120s时,有源层70的膜厚适中,并且生产成本较低,此时元器件的迁移率、阈值电压、开关比、亚阈值摆幅达到最佳值。该时长的控制可以通过计时器控制,通过计时器与磁控溅射开关进行连接,控制磁控溅射的反应时间。在本申请的一实施例中,所述铟镓锌氧化物薄膜经过磁控溅射后的厚度h为:20nm-40nm。将该铟镓锌氧化物薄膜的厚度h设置在20nm-40nm的范围可以使元器件的迁移率、阈值电压、开关比、亚阈值摆幅达到最佳值。可以理解的是,该铟镓锌氧化物薄膜的厚度h还可以为23nm、25nm、27nm、30nm、33nm、35nm、37nm、39nm等均能使元器件的迁移率、阈值电压、开关比、亚阈值摆幅达到最佳值。参照图5,本发明还提出一种阵列基板100,该阵列基板100包括:衬底基板10;栅极30,所述栅极30设于所述衬底基板10的一表面;栅极绝缘层50,所述栅极绝缘层50设于所述栅极30背离所述阵列基板100的一侧,并覆盖所述栅极30;有源层70,所述有源层70设于所述栅极绝缘层50背离所述栅极30的表面,所述有源层70包括在通氧状态下磁控溅射处理的靶材层;源极80,所述源极80设于所述有源层70背离所述栅极绝缘层50的表面;以及漏极90,所述漏极90设于所述有源层70背离所述栅极绝缘层50的表面,并与所述源极80间隔设置。在通氧状态下磁控溅射处理的靶材层在形成有源层70时,有源层70的表面会形成致密的氧化膜,并且退火处理后,有源层70与栅极绝缘层50的沟道处平滑连接,大大降低了有源层70的表面粗糙度,从而保证了元器件的迁移率、阈值电压、开关比、亚阈值摆幅达到最佳值。由于本阵列基板100采用了上述所有实施例的全部技术方案,因此至少具有上述实施例的技术方案所带来的所有有益效果,在此不再一一赘述。本发明还提出一种显示面板,包括彩膜基板和上述所述的阵列基板100,所述彩膜基板与所述阵列基板100相对设置,所述显示面板还包括液晶层,所述液晶层设置于所述彩膜基板和所述阵列基板100之间。在通氧状态下磁控溅射处理的靶材层在形成阵列基板100的有源层70后,有源层70的表面会形成致密的氧化膜,并且退火处理后,有源层70与栅极绝缘层50的沟道处平滑连接,大大降低了有源层70的表面粗糙度,从而保证了元器件的迁移率、阈值电压、开关比、亚阈值摆幅达到最佳值,从而该显示面板具有较好的显示功能。由于本显示面板采用了上述所有实施例的全部技术方案,因此至少具有上述实施例的技术方案所带来的所有有益效果,在此不再一一赘述。以上所述仅为本发明的可选实施例,并非因此限制本发明的专利范围,凡是在本发明的发明构思下,利用本发明说明书及附图内容所作的等效结构变换,或直接/间接运用在其他相关的
技术领域:
均包括在本发明的专利保护范围内。当前第1页12