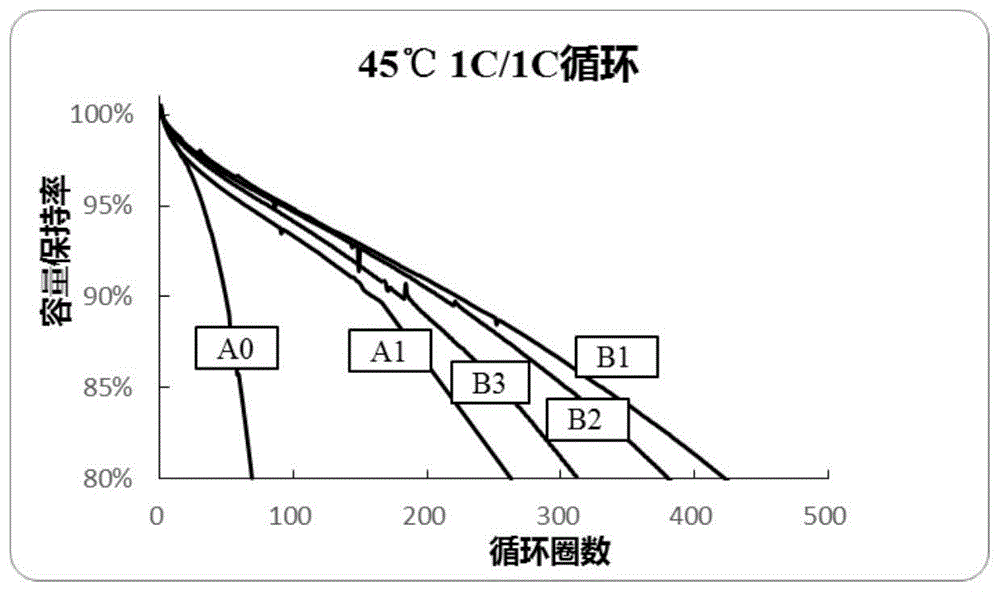
本发明涉及电池
技术领域:
,特别是涉及一种补锂剂、正极极片、隔离膜及锂离子电池。
背景技术:
:锂离子电池目前存在的普遍问题是在首次充电过程中会消耗大量从正极脱出的锂离子来形成负极表面的sei膜。其次,锂离子电池在正常使用过程中也会持续消耗活性锂。以上会导致电芯初始容量降低及电池寿命减少。尤其是硅碳负极锂离子电池中由于硅碳负极首次库伦效率低,首次充放电会有高达40%左右的sei成膜消耗导致的不可逆容量损失。针对锂离子电池负极sei膜消耗活性锂导致电池初始容量降低及寿命减少的现象,目前的解决方案有以下三种:(1)负极富锂方法:包括通过特殊工艺在电池组装之前使得负极sei膜优先形成,或将锂金属辊压到负极极片上以提供额外锂源。此类方法对生产环境要求严苛,工艺流程繁琐,且有一定的安全和性能风险。(2)正极富锂方法:包括提高首次充电电压或正极添加补锂剂以增大正极的首次不可逆的脱锂量。目前通用的正极补锂剂是高克容量的低电压材料,利用这类材料在高电压下脱锂的结构不可逆性,可实现补锂功效。但是由于常规正极活性物质或普通补锂剂的克容量相对较低,正极需要涂覆较多的活性物质才能满足sei成膜所需,对电芯的各项性能会有不利影响。(3)隔离膜的补锂方法:在隔离膜结构上引入补锂添加剂因为补锂剂对环境要求稍高,热稳定性相对较差,而隔离膜的处理工艺相对正负极极片要简单,烘烤温度也远低于正负极极片,具有一定优势,但有可能影响隔膜的li+透过能力,影响电芯的动力学性能,产生首次库伦效率不高和循环寿命恶化等问题。因此,亟需提供一种具有优良综合性能的补锂剂,用于提高锂离子电池的首次库伦效率。技术实现要素:鉴于以上现有技术的缺点,本发明的目的在于提供一种补锂剂、正极极片、隔离膜及锂离子电池,补锂剂适用于正极极片和隔离膜,提高电芯的首次库伦效率及寿命。为实现上述目的及其他相关目的,本发明的一方面提供一种补锂剂,包括内核和有机-无机复合保护层,内核包括富锂化合物,有机-无机复合保护层包括聚合物和含硅氧键的无机化合物。本发明的另一方面提供一种正极极片,正极极片包括集流体和正极活性物质层,正极活性物质层包括正极活性物质和本发明的补锂剂。本发明的另一方面提供一种隔离膜,包括基膜和富锂陶瓷层,富锂陶瓷层包括陶瓷粉体和本发明的补锂剂。本发明的另一方面提供一种锂离子电池,包括正极极片、负极极片、间隔设置于正极极片和负极极片之间的隔离膜、电解液及壳体,所述正极极片为本发明前述的正极极片。本发明的另一方面提供一种锂离子电池,包括正极极片、负极极片、间隔设置于正极极片和负极极片之间的隔离膜、电解液及壳体,所述隔离膜为本发明前述的隔离膜。相对于现有技术,本发明的有益效果为:本发明提供的补锂剂的内核表面包覆有机-无机复合保护层,可起到较好的包覆效果,将内核(富锂化合物)与空气/氧气隔离,使补锂剂能够在储存和料浆制备过程中稳定存在;而当用于制备成极片和隔离膜并组装成电池,在注液化成时,补锂剂表面的有机-无机复合保护层在含有碳酸酯溶剂的电解液中会不断溶解,锂源内核得以暴露,释放活性锂参与负极成膜反应,提高电池的首次循环效率;另外,聚合物和含硅氧键的无机化合物在碳酸酯溶剂中的溶解度不同,从而可以控制补锂速度,达到补锂缓慢释放的效果,减少因传统补锂剂剧烈消耗对电池结构造成不可逆的破坏,提高电池性能;同时,缓慢释放的内核也可成为活性锂,当循环过程中活性锂不足时,这些活性锂能够及时参与到电化学反应中,减少容量的衰减,从而延长电池寿命。此外,内核(例如,li15si4、li4sn等)在更低的电压下就可脱锂,脱锂之后由于正极的对锂电位一直在3.0v以上,电芯放电时内核不会接收锂离子,对正极极片的膨胀特性无恶化,从而改善电芯寿命。附图说明图1是实施例1~3和对比例1~2电芯45℃1c/1c循环容量衰减对比图。图2是实施例1~3和对比例1~2电芯45℃1c/1c循环膨胀力对比图。图3是实施例4基膜ab表面分别先后设置陶瓷层和补锂剂层的隔膜涂布效果图。图4是实施例5基膜a面先后设置陶瓷层和补锂剂层的隔膜涂布效果图。图5是实施例6基膜a面设置富锂陶瓷层的隔膜涂布效果图。图6是对比例3基膜a面仅设置陶瓷层的隔膜涂布效果图。图7是实施例4~6和对比例3涂布效果图的附注说明。具体实施方式下面详细说明根据本发明的补锂剂、正极极片、隔离膜及锂离子电池。本发明第一方面的补锂剂包括内核和有机-无机复合保护层,所述内核包括富锂化合物,所述有机-无机复合保护层包括聚合物和含硅氧键的无机化合物。在内核单独包覆有机保护层或无机保护层,虽然有机保护层柔韧性较好,但是有机骨架间往往存在间隙,包覆难以致密,内核仍然会与周围环境有一定的反应空间;无机保护层虽能致密包覆,但各无机分子间作用力不够,熔沸点较低,在电池制备和烘烤过程中不能保持稳定,包覆可靠性和一致性较差。因而,发明人选择在补锂剂的内核表面包覆有机-无机复合保护层,有机-无机复合保护层和内核(富锂化合物)不发生反应,稳定存在,可起到较好的包覆效果,且有机-无机复合保护层在空气/氧气环境下稳定存在,可以使内核与空气/氧气环境隔离,又可在注液后释放内核参与负极成膜反应。在本发明的一些实施方式中,所述富锂化合物包括金属锂与其他金属或非金属组成的复合材料,所述富锂化合物优选为金属锂与硅、锡、铝、碳等的一种或多种复合化合物,所述富锂化合物更优选为li15si4、li4sn。富锂化合物如(li15si4、li4sn等)与目前通用普通补锂剂相比克容量更高、电压平台更低。富锂化合物做补锂剂优势明显,富锂化合物如(li15si4、li4sn等)在更低的电压下就可脱锂,脱锂之后由于正极的对锂电位一直在3.0v以上,电芯放电时富锂化合物不会接收锂离子,对正极极片的膨胀特性无恶化,电池的膨胀力可维持在无补锂时的水平,不会对模组、电池包的结构强度形成挑战,从而改善电芯寿命。在本发明的一些实施方式中,所述富锂化合物在所述补锂剂中所占的质量百分比为70%~98%。富锂化合物为发挥补锂效果的活性成分,其含量过低时,影响整个补锂剂的活性锂容量,甚至影响电池的容量;而含量过高时,所述有机-无机复合保护层无法形成充分的保护,也无法达到合适的缓释效果。在本发明中,所述富锂化合物在所述补锂剂中所占的质量百分比优选为80%~95%。在本发明的一些实施方式中,所述有机-无机复合保护层的厚度为2nm~3μm。可选的,所述有机-无机复合保护层的厚度为2nm~3μm、5nm~1μm、2nm~5nm、5nm~100nm、100nm~200nm、200nm~500nm、500nm~800nm、800nm~1μm、1μm~3μm。通常情况下,有机-无机复合保护层的厚度低于2nm时,富锂添加剂表面的包覆不完善,内核物质容易发生副反应导致补锂效率低;而有机-无机复合保护层的厚度高于3μm时,包覆层过厚,内核物质中的锂离子不易脱嵌,同样影响补锂效率。作为本发明的一种优选方式,所述有机-无机复合保护层的厚度为5nm~1μm。在本发明的一些实施方式中,所述内核粒径为10nm~30μm。可选地,所述内核粒径为10nm~30μm、500nm~30μm、10nm~30nm、30nm~100nm、100nm~300nm、300nm~500nm、500nm~1μm、1μm~5μm、5μm~10μm、10μm~20μm、20μm~30μm。通常情况下,内核直径低于10nm时,较大的比表面会导致富锂添加剂表面的保护层厚度远大于内核直径,补锂利用率较低;而当内核直径高于30μm时,富锂添加剂尺寸已等同或大于正极活性物质的尺寸,这会对正极材料的加工工艺造成不利影响。作为本发明的一种优选方式,所述内核粒径为500nm~30μm。在本发明的一些实施方式中,所述含硅氧键的无机化合物选自环氧基硅烷、烷基硅烷及硅酸酯等中的一种或多种的组合。所述环氧基硅烷选自kh-560、kh-561、kh-563、kh-564等中的一种或多种的组合;所述烷基硅烷选自甲基三乙氧基硅烷、甲基三甲氧基硅烷、丙基三甲氧基硅烷等中的一种或多种的组合;所述硅酸酯选自正硅酸甲酯、正硅酸乙酯、正硅酸丙酯等中的一种或多种的组合。所述含硅氧键的无机化合物在碳酸酯中25℃时的溶解度不低于15g。可选的,所述含硅氧键的无机化合物在碳酸酯中25℃的溶解度不低于15g、25g、35g、50g、70g、100g;因为补锂剂表面的含硅氧键的无机化合物在碳酸酯溶剂电解液中会不断溶解,可以控制补锂剂在注入电解液进行化成工序时,暴露出活性锂,实现补锂效果。在本发明的一些实施方式中,所述碳酸酯选自线状碳酸酯和/或环状碳酸酯,优选选自碳酸二甲酯(dmc)、碳酸二乙酯(dec)、碳酸甲乙酯(emc)、碳酸甲丙酯(mpc)等中的一种或多种的组合。所述碳酸酯溶剂可溶解所述含硅氧键的无机化合物和聚合物。所述碳酸酯沸点是160℃~250℃,碳酸酯沸点较低可保证补锂剂在60℃~100℃优选温度范围内烘干,避免高温下所述补锂剂的内核材料发生副反应。在本发明的一些实施方式中,所述聚合物在0~150℃时稳定存在,主要考虑涂布和烘烤过程中该聚合物能够保持稳定。所述聚合物与含硅氧键的无机化合物具有较好的相容性,因为聚合物的分子量较高;其在碳酸酯溶剂中的溶解度低于含硅氧键的无机化合物,从而可以控制补锂速度,达到补锂缓慢释放的效果,减少因传统补锂剂剧烈消耗对电池结构造成不可逆的破坏,提高电池性能。所述聚合物选自聚亚烷基碳酸酯、聚亚烷基氧化物、聚烷基硅氧烷、聚丙烯酸烷基酯、聚甲基丙烯酸烷基酯等中的一种或多种的组合。在本发明的一些实施方式中,为控制内核材料中的富锂化合物的释放速率,所述聚合物在有机-无机复合保护层中所占的质量百分比为10%-90%,优选为50%-90%。可选的,所述聚合物在有机-无机复合保护层中所占的质量百分比为10%~90%、50%~90%、10%~20%、20%~30%、30%~50%、50%~70%、70%~90%。作为本发明的一种优选方式,所述聚合物在有机-无机复合保护层中所占的质量百分比为50%~90%。本发明的第二方面提供一种补锂剂的制备方法,包括:提供含硅氧键的无机化合物和聚合物的碳酸酯溶剂,将内核材料分散于所述碳酸酯溶剂中,过滤,干燥固相物。本发明的第三方面提供一种正极极片,所述正极极片包括集流体和正极活性物质层,所述正极活性物质层包括正极活性物质和本发明的补锂剂。在本发明的一些实施方式中,所述正极活性物质层包括均匀混合的正极活性物质和所述补锂剂;和/或,所述正极活性物质层包括正极材料层和补锂剂层,所述正极材料层包括正极活性物质,所述补锂剂层包括所述的补锂剂。通常情况下正极材料层中不包含补锂剂,补锂剂层中不包含正极活性物质。在本发明的一些实施方式中,所述正极极片可以包括以下三种布置方式:所述正极活性物质与补锂剂混合布置在集流体表面;所述补锂剂层布置在集流体表面,所述正极材料层布置在补锂剂层表面;所述正极材料层布置在集流体表面,所述补锂剂层布置在正极材料层表面。在本发明的一些实施方式中,所述正极极片的布置例如可以是将正极活性物质和/或补锂剂搅拌制成浆料后涂覆。在本发明中补锂剂的用量可以依照所需的补锂效果设置,不做特殊限定。本领域的技术人员可以根据需要获得的补锂容量,通过计算正负极的理论容量,选择合适用量的补锂剂,再经简单调整以达到效果。本发明的第四方面提供一种隔离膜,所述隔离膜包括基膜和富锂陶瓷层,所述富锂陶瓷层包括陶瓷粉体和本发明的补锂剂。在本发明的一些实施方式中,所述富锂陶瓷层位于隔离膜的至少一个外表面上。在本发明的一些实施方式中,所述富锂陶瓷层包括均匀混合的陶瓷粉体和补锂剂;和/或,所述富锂陶瓷层包括陶瓷层和补锂剂层,所述陶瓷层包括陶瓷粉体,所述补锂剂层包括补锂剂。通常情况下陶瓷层中不包含补锂剂,补锂剂层中不包含陶瓷粉体。在本发明的一些实施方式中,所述富锂陶瓷层可以是含有所述陶瓷粉体和所述补锂剂的单层结构,也可以是由含有所述陶瓷粉体的陶瓷层和含有所述补锂剂的补锂剂层组成的双层结构。更具体地,所述隔离膜可以包括两种布置方式:方式一是补锂剂与陶瓷粉体混合布置在所述基膜表面;方式二是陶瓷层布置在所述基膜表面,补锂剂层布置在所述陶瓷层表面。方式二的布置方式是为了避免补锂剂在后续充放电过程中堵塞所述基膜。在本发明的一些实施方式中,所述隔离膜的布置例如可以是将陶瓷粉体和/或补锂剂搅拌制成浆料后涂覆。在本发明的一些实施方式中,所述基膜包括a面和b面,例如,所述补锂剂和/或陶瓷粉体可以涂覆在基膜的a面和/或b面。在本发明的一些实施方式中,所述基膜选自聚烯烃类隔离膜,优选地,所述基膜选自聚乙烯(pe)、聚丙烯(pp)、聚酰胺(pa),聚四氟乙烯(ptfe)、聚偏氟乙烯(pvdf)、聚氯乙烯(pvc)等中的一种或多种的组合。更优选地,所述基膜包括聚乙烯、聚丙烯和聚偏氟乙烯等中的一种或多种的组合。在本发明的一些实施方式中,所述基膜的厚度为5μm~50μm,可选的,所述基膜的厚度为5μm~10μm、10μm~20μm、20μm~30μm、30μm~40μm、40μm~50μm。在本发明的一些实施方式中,所述陶瓷粉体选自三氧化二铝、二氧化硅、二氧化钛、二氧化锆、二氧化锡、氧化锌、氧化钙、氧化镁、碳酸钙、碳酸钡、硫酸钡、钛酸钡、氮化铝、氮化镁等中的一种或多种的组合。作为本发明的一种优选方式,所述陶瓷粉体为三氧化二铝。在本发明中补锂剂的用量可以依照所需的补锂效果设置,不做特殊限定。本领域的技术人员可以根据需要获得的补锂容量,通过计算正负极的理论容量,选择合适用量的补锂剂,再经简单调整以达到效果。本发明的第五方面提供一种锂离子电池,包括正极极片、负极极片、间隔设置于正极极片和负极极片之间的隔离膜、电解液及壳体,所述正极极片为本发明前述的正极极片。本发明的第六方面提供一种锂离子电池,包括正极极片、负极极片、间隔设置于正极极片和负极极片之间的隔离膜、电解液及壳体,所述隔离膜为本发明前述的隔离膜。在本发明的一些实施方式中,所述负极极片中的活性物质为可脱嵌锂离子的各种无机或有机物质。作为本发明的一种优选方式,负极极片的活性物质选自钛酸锂、单质硅及其化合物、单质锡及其化合物、过渡金属及其化合物、锂化物、石墨、软碳、硬碳等中的一种或多种的组合。在本发明的一些实施方式中,所述电解液的溶质锂盐包括六氟磷酸锂(lipf6)、四氟硼酸锂(libf4)、高氯酸锂(liclo4)、双(氟磺酰)亚胺锂(lin(so2f)2)、双(三氟甲基磺酰)亚胺锂(lin(cf3so2)2)、双草酸硼酸锂(libob)、二氟草酸硼酸锂(lidfob)等中的一种或多种的组合。电解液中电解质的摩尔浓度为0.5m~2m。在本发明的一些实施方式中,所述电解液溶剂包括碳酸丁烯酯(bc)、碳酸二甲酯(dmc)、碳酸二乙酯(dec)、碳酸甲乙酯(emc)、碳酸甲丙酯(mpc)等中的一种或多种的组合。为保证电解液溶质及所述补锂剂有机-无机复合保护层的溶解性,所述电解液溶剂也可加入适量碳酸乙烯酯(ec)、碳酸丙烯酯(pc)。所述电解液溶剂可确保锂离子电池注液之后所述补锂剂的有机-无机复合保护层能够溶解,如此,所述补锂剂的内核材料,即富锂化合物,便可得以释放,在后续充电过程中可参与锂离子电池负极的sei成膜过程,提高锂离子电池的首次库伦效率。以下结合实施例进一步说明本发明的有益效果。为了使本发明的发明目的、技术方案和有益技术效果更加清晰,以下结合实施例进一步详细描述本发明。但是,应当理解的是,本发明的实施例仅仅是为了解释本发明,并非为了限制本发明,且本发明的实施例并不局限于说明书中给出的实施例。实施例中未注明具体实验条件或操作条件的按常规条件制作,或按材料供应商推荐的条件制作。此外应理解,本发明中提到的一个或多个方法步骤并不排斥在所述组合步骤前后还可以存在其他方法步骤或在这些明确提到的步骤之间还可以插入其他方法步骤,除非另有说明;还应理解,本发明中提到的一个或多个设备/装置之间的组合连接关系并不排斥在所述组合设备/装置前后还可以存在其他设备/装置或在这些明确提到的两个设备/装置之间还可以插入其他设备/装置,除非另有说明。而且,除非另有说明,各方法步骤的编号仅为鉴别各方法步骤的便利工具,而非为限制各方法步骤的排列次序或限定本发明可实施的范围,其相对关系的改变或调整,在无实质变更技术内容的情况下,当亦视为本发明可实施的范畴。在下述实施例中,所使用到的试剂、材料以及仪器如没有特殊的说明,均可商购获得。一、用于测试的电池的制备实施例1(1)补锂剂的制备将正硅酸甲酯和聚甲基丙烯酸乙酯按照1:3的重量比加入到碳酸二乙酯中,控制温度在45℃,充分搅拌使其完全溶解,形成正硅酸甲酯质量浓度为2%、聚甲基丙烯酸乙酯质量浓度为6%的溶液。待溶液冷却至室温后,将平均粒径为1μm的li15si4颗粒加入到所述溶液中,充分搅拌使锂颗粒均匀分散,过滤,将滤渣在真空箱中进行80℃干燥,得到补锂剂,其中有机无机复合保护层的厚度为10nm。(2)正极极片的制备正极活性物质为镍钴锰三元材料,将活性物质、补锂剂、导电碳、粘结剂按照重量比92.5%:4.5%:1.5%:1.5%溶于n-甲基吡咯烷酮(nmp)中,经搅拌获得均匀的正极浆料,将正极浆料单面涂覆在铝箔基材表面,面密度为15.58mg/cm2,烘干辊压后裁剪成所需宽度及形状的正极极片。(3)负极极片的制备将负极活性物质硅氧化物、导电碳superp、粘结剂pvdf按照重量比95%:2%:3%溶于n-甲基吡咯烷酮(nmp)中,经搅拌获得均匀的负极浆料。将负极浆料均匀涂覆在铜箔基材表面,浆料单面涂覆,面密度为2.11mg/cm2,经120℃烘箱烘干膜片,经辊压成所需要的厚度,裁剪成所需宽度及形状的负极极片。(4)隔离膜的制备隔膜制备为常规技术,基膜为pe隔膜,表面涂覆陶瓷层,根据需要裁剪成所需的形状。(5)电池的制备将上述得到的负极极片、正极极片及隔离膜进行卷绕得到jellyroll,然后装配、注液,所述电解液溶剂比例dmc:dec:ec=1:1:1,溶质锂盐是lipf6,其摩尔浓度为1m。化成分容后可得所需的锂离子电池,编号为b1。实施例2(1)补锂剂的制备制备方法与实施例1相同,不同之处是li15si4的粒径是3μm,有机-无机复合保护层的厚度为500nm。(2)正极极片的制备正极活性物质为镍钴锰三元材料,将活性物质、导电碳、粘结剂按照重量比97%:1.5%:1.5%溶于n-甲基吡咯烷酮(nmp)中,经搅拌获得均匀的正极浆料,将正极浆料单面涂覆在铝箔基材表面,面密度为14.87mg/cm2。后将上述补锂剂、导电碳superp、粘结剂pvdf按照重量比95%:2%:3%溶于n-甲基吡咯烷酮(nmp)中,经搅拌获得均匀的补锂剂浆料。将补锂剂浆料均匀涂覆在上述膜片表面,浆料单面涂覆,面密度为0.71mg/cm2,经120℃烘箱烘干膜片,烘干辊压后裁剪成所需宽度及形状的正极极片。(3)负极极片的制备与实施例1相同(4)隔离膜的制备与实施例1相同(5)电池的制备与实施例1相同,得到的电池编号为b2。实施例3(1)补锂剂的制备将环氧基硅烷kh-560和聚丙烯酸乙基酯按照1:4的重量比加入到碳酸二甲酯中,控制温度在45℃,充分搅拌使其完全溶解,形成环氧基硅烷kh-560质量浓度为2%、聚丙烯酸乙基酯质量浓度为8%的溶液。待溶液冷却至室温后,将平均粒径为4μm的li4sn颗粒加入到所述溶液中,充分搅拌使li4sn颗粒均匀分散,过滤,将滤渣在真空箱中进行80℃干燥,得到补锂剂,其中有机-无机复合保护层的厚度为750nm。(2)正极极片的制备正极活性物质为镍钴锰三元材料,将上述补锂剂、导电碳superp、粘结剂pvdf按照重量比95%:2%:3%溶于n-甲基吡咯烷酮(nmp)中,经搅拌获得均匀的补锂剂浆料。将补锂剂浆料均匀涂覆在铝箔基材表面,面密度为14.87mg/cm2。后将活性物质、导电碳、粘结剂按照重量比97%:1.5%:1.5%溶于n-甲基吡咯烷酮(nmp)中,经搅拌获得均匀的正极浆料,将正极浆料均匀涂覆在上述膜片表面,浆料单面涂覆,面密度为0.71mg/cm2,经120℃烘箱烘干膜片,烘干辊压后裁剪成所需宽度及形状的正极极片。(3)负极极片的制备与实施例1相同(4)隔离膜的制备与实施例1相同(5)电池的制备与实施例1相同,得到的电池编号为b3。实施例4(1)补锂剂的制备将聚乙烷基硅氧烷和kh-561加入到碳酸二乙酯中,形成质量浓度为15%的溶液,充分搅拌使其完全溶解,将平均粒径为0.5μm的li15si4颗粒加入到所述溶液中,充分搅拌使锂颗粒均匀分散,过滤,将滤渣在真空箱中进行80℃干燥,得到补锂剂,其中有机无机复合保护层的厚度为30nm。(2)正极极片的制备正极活性物质为镍钴锰三元材料,活性物质的固含量为97%,正极浆料单面涂覆在铝箔基材表面,面密度为15.58mg/cm2,烘干辊压后裁剪得正极极片。(3)负极极片的制备将负极活性物质硅氧化物、导电碳superp、粘结剂pvdf按照重量比95%:2%:3%溶于n-甲基吡咯烷酮(nmp)中,经搅拌获得均匀的负极浆料。将负极浆料均匀涂覆在铜箔基材表面,浆料单面涂覆,面密度为2.57mg/cm2,经120℃烘箱烘干膜片,经辊压成所需要的厚度,裁剪成负极极片。(4)隔离膜的制备隔离膜包括基膜和双面涂布的陶瓷层、补锂剂层(图3和图7)。基膜为pp隔离膜陶瓷层和补锂剂层对称设置在基膜两侧。陶瓷层和补锂剂层的厚度分别为4μm和6μm。陶瓷层的制备:将陶瓷粉体tio2(粒径0.2μm)、粘结剂pvdf按照90%:10%的比例加入到nmp溶剂中,混合均匀得到陶瓷浆料,涂布到上述pp基膜ab两面,烘干。补锂剂层的制备:将补锂剂、粘结剂pvdf按照85%:15%的比例加入到nmp溶解中,混合均匀后得到富锂材料浆料,涂布到上述烘干的陶瓷层上,烘干。(5)电池的制备将上述得到的负极极片、正极极片及隔离膜用叠片工艺进行装配,用铝塑膜进行预封装,注入5g电解液,所述电解液溶剂比例dmc:dec:ec=1:1:1,溶质锂盐是lipf6,其摩尔浓度为1m。化成分容后可得所需的锂离子电池,编号为b4。实施例5(1)补锂剂的制备制备方法与实施例4相同,不同之处是把kh-561替换为正硅酸甲酯,li15si4的粒径是4μm,有机无机复合保护层的厚度为300nm。(2)正极极片的制备与实施例4相同(3)负极极片的制备与实施例4相同(4)隔离膜的制备隔离膜包括基膜和仅涂布a面的陶瓷层、补锂剂层(图4和图7)。基膜为pvdf隔离膜,陶瓷层设置在基膜的表面,然后在陶瓷层上设置所述补锂剂层。所述陶瓷层和富锂材料层的厚度分别为4μm和8μm。所述陶瓷层和补锂剂层与实施例4相同。(5)电池的制备与实施例4相同,得到的电池编号为b5。实施例6(1)补锂剂的制备制备方法与实施例4相同,不同之处是把kh-561替换为甲基三乙氧基硅烷,li15si4的粒径是30μm,有机无机复合保护层的厚度为1μm。(2)正极极片的制备与实施例4相同(3)负极极片的制备与实施例4相同(4)隔离膜的制备隔离膜包括基膜和仅涂布a面的富锂陶瓷层(图5)。基膜为pvdf隔离膜,富锂陶瓷层的厚度为12μm。富锂陶瓷层的制备:将陶瓷粉体al2o3(粒径0.4μm)、补锂剂、粘结剂pvdf按照30%:60%:10%的比例加入到nmp溶剂中,混合均匀得到富锂陶瓷浆料,涂布到上述pvdf基膜a面,烘干。(5)电池的制备与实施例4相同,得到的电池编号为b6。对比例1不添加补锂剂(1)正极极片的制备正极活性物质为镍钴锰三元材料,将活性物质、导电碳、粘结剂按照重量比97%:1.5%:1.5%溶于n-甲基吡咯烷酮(nmp)中,经搅拌获得均匀的正极浆料,将正极浆料单面涂覆在铝箔基材表面,面密度为15.58mg/cm2。烘干辊压后裁剪成所需宽度及形状的正极极片。(2)负极极片的制备与实施例1相似,不同之处是面密度为2.22mg/cm2。(3)隔离膜的制备与实施例1相同。(4)电池的制备与实施例1相同,得到的电池编号为a0。对比例2(1)补锂剂的制备与实施例1相比,不同之处是li15si4粒径是3μm,有机-无机复合保护层的厚度是1μm。(2)正极极片的制备与对比例1相同(3)负极极片的制备将负极活性物质硅氧化物、补锂剂、导电碳superp、粘结剂pvdf按照重量比73%:22%:2%:3%溶于n-甲基吡咯烷酮(nmp)中,经搅拌获得均匀的负极浆料。将负极浆料均匀涂覆在铜箔基材表面,浆料单面涂覆,面密度为2.88mg/cm2,经120℃烘箱烘干膜片,经辊压成所需要的厚度,裁剪成所需宽度及形状的负极极片。(4)隔离膜的制备与实施例1相同(5)电池的制备与实施例1相同,得到的电池编号为a1。对比例3不添加补锂剂(1)正极极片的制备与实施例6相同(2)负极极片的制备与实施例6相同(3)隔离膜的制备隔离膜包括基膜和仅涂布a面的陶瓷层(图6和图7)。所述基膜为pp隔离膜,所述陶瓷层的厚度为3μm。隔离膜经分切裁剪后编号为隔离膜7。陶瓷层的制备:将陶瓷粉体zro2(粒径0.5μm)、粘结剂pvdf按照80%:20%的比例加入到nmp溶剂中,混合均匀得到陶瓷浆料,涂布到上述pp基膜a面,烘干。(4)电池的制备与实施例4相同,得到的电池编号为a2。表1是实施例1~3和对比例1、2中补锂剂及正极极片的重要特征表表2是实施例4~6和对比例3中补锂剂及隔离膜的重要特征表二、电池性能测试按照实施例1~6和对比例1~3制备出电池后,上述电池的化成流程如下:先以0.02c充电至3.0v,再以0.1c充电至3.4v,最后以0.2c充电至4.2v,放电时以0.2c放电至2.8v。首次库伦效率等于首次放电容量除以首次充电容量。实施例1~3是将补锂剂用在正极极片,对比例1正极极片没有添加补锂剂,对比例2是将补锂剂用在负极极片。实施例1~3、对比例1~2的测试结果见表3。表3实施例1~3、对比例1~2的电池性能测试结果组别首次充电容量/ah首次放电容量/ah首次库伦效率b141.4140.6498%b241.4340.0997%b341.1840.5198%a043.4231.2672%a143.4240.1492%如表3所示是电芯首次充放电容量及库伦效率,可以看出:由于对比例1(电池a0)中硅氧化物的首次成膜时消耗大量的锂离子,因此a0的首次库伦效率仅有72%,对比例2(电池a1)、实施例1(电池b1)、实施例2(电池b2)、实施例3(电池b3)因为都有补锂剂,补锂剂表面的有机-无机复合保护层在碳酸酯溶剂电解液中会不断溶解,暴露的富锂化合物可以较容易地参加电化学反应。化成充电时添加剂中的富锂化合物得以在负极表面形成sei膜,减小了正极的不可逆锂消耗,故其补锂容量都比较高,首次库伦效率也都在92%以上。实施例1~3、对比例1~2得到的电池在45℃下进行循环测试,充放电条件如下:以1c电流充电至4.2v后继续恒压充电至0.05c,后以1c电流放电至2.8v。如此充放电循环直至最后一次放电容量衰减为第一次放电容量的80%,测试结果见图1和图2。如图1、图2所示分别为实施例1~3和对比例1~2电芯45℃1c/1c循环容量衰减及膨胀力的对比图,可以看出:硅氧化物体系添加补锂剂后,电池容量衰减速度明显降低,寿命得以延长。这是因为补锂剂释放富锂化合物一方面能够参与sei成膜,另一方面也可成为活性锂,当循环过程中活性锂不足时,这些储备的活性锂能够及时参与到电化学反应中,减少容量的衰减,从而延长电池寿命。比较对比例2(电池a1)、实施例1(电池b1)、实施例2(电池b2)、实施例3(电池b3)可以发现,电池b1、b2、b3的循环性能要优于电池a1,这一方面是因为电池b1、b2、b3中补锂剂的量高于电池a1,前者的首次库伦效率高于后者(92%),前者有更多的活性锂;另一方面,前者的补锂剂在正极,富锂化合物脱出后不会再回嵌到正极,因此正负极的膨胀特性不会恶化,而后者的补锂剂在负极,在电芯循环过程中,因为负极电位低,充放电过程中所述内核也会嵌脱锂,从而消耗活性锂,引起其本身的成膜及膨胀,恶化负极的膨胀,电芯整体膨胀力增大,这对循环性能是不利的。实施例4~6是将补锂剂用在隔离膜,对比例3隔离膜没有添加补锂剂。实施例4~6和对比例3的测试结果见表4。表4实施例4~6和对比例3的电池性能测试结果如表4所示是实施例4~6和对比例3中锂离子电池的首次库伦效率和循环性能,可以看出:由于对比例3(电池a2)中硅氧化物的首次成膜时消耗大量的锂离子,因此电池a2的首次库伦效率仅有73.0%,实施例4~6中因为隔膜上都有富锂材料,补锂剂表面的有机-无机复合保护层在碳酸酯溶剂电解液中会不断溶解,暴露的锂源可以较容易地参加电化学反应。化成充电时隔膜中的锂源得以在负极表面形成sei膜,减小了正极的不可逆锂消耗,故其补锂容量都比较高,首次库伦效率也都在91%以上。上述得到的电池在25℃下进行循环测试,充放电条件如下:以1c电流充电至4.2v后继续恒压充电至0.05c,后以1c电流放电至2.8v。如此充放电循环直至200圈,测试结果见表4。从表4所有编号电池的循环性能数据可以看出,硅氧化物体系添加隔离膜补锂剂后,电池在200圈时的容量保持率从81%(对比例3)提升至85%以上,说明容量衰减速度明显降低,寿命得以延长。这是因为富锂隔膜释放锂源一方面能够参与sei成膜,另一方面也可成为活性锂,当循环过程中活性锂不足时,这些储备的活性锂能够及时参与到电化学反应中,减少容量的衰减,从而延长电池寿命。以上所述,仅为本发明的较佳实施例,并非对本发明任何形式上和实质上的限制,应当指出,对于本
技术领域:
的普通技术人员,在不脱离本发明方法的前提下,还将可以做出若干改进和补充,这些改进和补充也应视为本发明的保护范围。凡熟悉本专业的技术人员,在不脱离本发明的精神和范围的情况下,当可利用以上所揭示的技术内容而做出的些许更动、修饰与演变的等同变化,均为本发明的等效实施例;同时,凡依据本发明的实质技术对上述实施例所作的任何等同变化的更动、修饰与演变,均仍属于本发明的技术方案的范围内。当前第1页12