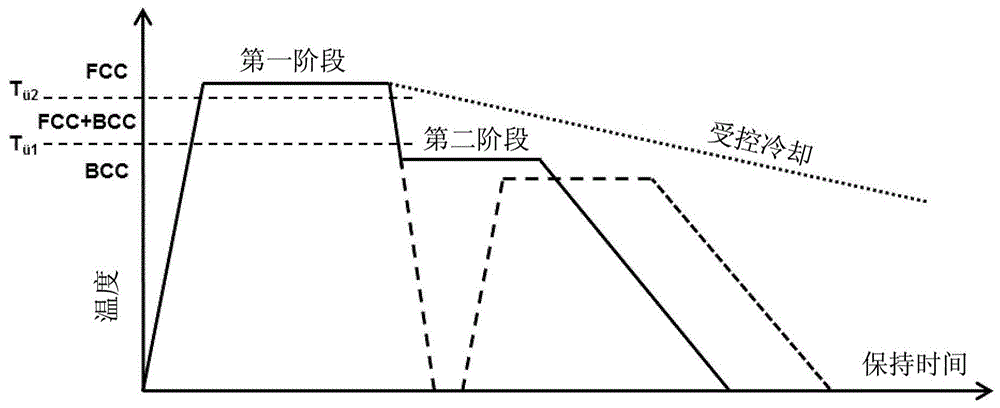
本发明涉及一种软磁合金,特别是一种高磁导率软磁合金。
背景技术:
:具有约3重量%硅的非晶粒取向电工钢(sife)是目前应用最广泛的结晶性软磁材料,其用于电机的板材叠层(叠片铁芯、叠片组,blechpaketen)中。随着电动汽车的发展,需要更有效的、比sife具有更好性能的材料。这意味着,除了具有足够高的电阻,首要期望更高的感应水平以形成高的扭矩和/或较小的结构体积。对于在一些技术如汽车工业和电动汽车中的使用,期望更有效的材料。软磁性钴-铁合金(cofe)由于其极高的饱和感应也被用于电机中。市售cofe合金一般具有49重量%fe、49重量%co和2%v的组成。在这种组成下,在0.4μωm的高电阻率下饱和感应同时达到了约2.35t。然而,期望降低例如由高co含量、额外的生产步骤和废料含量所产生的cofe合金的材料和制造成本。技术实现要素:因此,本文所要解决的问题是提供一种材料成本较低且同时可加工性良好的feco合金,以降低合金直至板材叠层的制造成本,同时实现高功率密度。这是通过独立权利要求的主题解决的。进一步的有利的技术方案是各从属权利要求的主题。根据本发明提供一种软磁合金,特别是一种高磁导率软磁feco合金,其基本上由以下组成:5重量%≤co≤25重量%0.3重量%≤v≤5.0重量%0重量%≤cr≤3.0重量%0重量%≤si≤3.0重量%0重量%≤mn≤3.0重量%0重量%≤al≤3.0重量%0重量%≤ta≤0.5重量%0重量%≤ni≤0.5重量%0重量%≤mo≤0.5重量%0重量%≤cu≤0.2重量%0重量%≤nb≤0.25重量%0重量%≤ti≤0.05重量%0重量%≤ce≤0.05重量%0重量%≤ca≤0.05重量%0重量%≤mg≤0.05重量%0重量%≤c≤0.02重量%0重量%≤zr≤0.1重量%0重量%≤o≤0.025重量%0重量%≤s≤0.015重量%余量为铁,其中cr+si+al+mn≤3.0重量%和最多达0.2重量%的其他杂质。该合金的最大磁导率μmax≥5,000,优选μmax≥10,000,优选μmax≥12,000,优选μmax≥17,000。其他杂质例如为b、p、n、w、hf、y、re、sc、be,除ce外的其他镧系元素。由于本发明合金的co含量较低,所以其原料成本相对于基于49重量%fe、49重量%co、2%v的合金有所降低。根据本发明,制造了一种最大钴含量为25重量%的feco合金,该合金具有更好的软磁性能,特别是比其他最大钴含量为25重量%的feco合金(例如现有的和市售的feco合金,如vacoflux17、afk18或hiperco15)具有显著更高的磁导率。这些现有的和市售的合金的最大磁导率小于5000。根据本发明的合金没有显著的有序调节,因此,不同于具有超过30重量%co的合金,这种合金可以冷轧而不需要上游的淬火过程。淬火过程特别是在大量材料的情况下难以控制,因为很难达到足够快的冷却速率,所以会发生由此导致合金变脆的有序化。在本发明合金中缺省了有序-无序转变,因此简化了大规模生产。明显的有序-无序转变,正如在co含量超过30重量%的cofe合金中的那样,可以通过dsc测量(差示扫描量热法)确定,因为它导致dsc测量中的峰。对于根据本发明合金而言,这种峰在相同条件的dsc测量中测不到。同时,这种新的合金的磁滞损耗比以前已知的和市售的co含量在10至30重量%之间的合金要低得多,以及除了这种合金从未达到的显著较高的磁导率水平之外,还有更高的饱和度。本发明的feco合金也可以成本效益高地大规模制造。本发明的合金由于在诸如电动机的转子或定子之类的应用中具有较高的磁导率,可用于减小转子或定子的尺寸从而减小电动机的尺寸和/或增加功率。例如,在相同的结构尺寸和/或在相同的重量下,可以产生更高的扭矩,这在电动或混合动力车辆中应用时是有利的。除了最大磁导率μmax≥5,000,优选μmax≥10,000,优选μmax≥12,000,优选μmax≥17,000外,该合金还可具有电阻率ρ≥0.25μωm,优选ρ≥0.30μωm,和/或磁滞损耗phys≤0.07j/kg,优选磁滞损耗phys≤0.06j/kg,优选磁滞损耗phys≤0.05j/kg,均在1.5t的振幅,和/或矫顽场强hc≤0.7a/cm,优选矫顽场强hc≤0.6a/cm,优选矫顽场强hc≤0.5a/cm,优选矫顽场强hc≤0.4a/cm,优选矫顽场强hc≤0.3a/cm,和/或优选在100a/cm时的感应b≥1.90t,优选在100a/cm时的感应b≥1.95t,优选在100a/cm时的感应b≥2.00t。磁滞损耗phys通过线性回归法从曲线p/f中的频率f在y轴截距上在1.5t感应的振幅处的反复磁化损耗p测定。线性回归在至少8个测量值上进行,这些测量值大致均匀地分布在50hz至1khz的频率范围上(例如,在50、100、200、300、400、500、600、700、800、900、1,000hz)。在一个实施例中,合金的最大磁导率μmax≥μmax≥10,000,电阻率ρ≥0.28μωm,磁滞损耗phys≤0.055j/kg,振幅为1.5t,矫顽场强hc≤0.5a/cm,100a/cm时的感应b≥1.95t。这种性能的组合对于作为或用于电动机的转子或定子的应用特别有利,以减小转子或定子的尺寸,从而减小电动机和/或增加功率,或在相同结构尺寸和/或相同重量下产生更高扭矩。因此,软磁合金可用于电机,例如作为或用于电动机和/或发电机的定子和/或转子,和/或变压器中和/或电磁致动器中。它可以以板材的形式提供,例如0.5mm到0.05mm的厚度。可以将合金中的若干板材堆叠成用作定子或转子的板材叠层(或叠片铁芯)中。根据本发明的合金,电阻率至少为0.25μωm,优选最小0.3μωm。涡流损耗可以通过选择一个稍低的带材厚度而降低到较低的水平。在进一步的实施例中,更详细地定义了软磁合金的组成,其中10重量%≤co≤20重量%,优选15重量%≤co≤20重量%和0.3重量%≤v≤5.0重量%,优选1.0重量%≤v≤3.0重量%,优选1.3重量%≤v≤2.7重量%和/或0.1重量%≤cr+si≤2.0重量%,优选0.2重量%≤cr+si≤1.0重量%,优选0.25重量%≤cr+si≤0.7重量%。在一个实施例中,更详细地定义了和式,其中0.2重量%≤cr+si+al+mn≤1.5重量%,优选0.3重量%≤cr+si+al+mn≤0.6重量%。软磁合金也可以含有硅,其中0.1重量%≤si≤2.0重量%,优选0.15重量%≤si≤1.0重量%,优选0.2重量%≤si≤0.5重量%。铝和硅可以相互交换,因此在一个实施例中,si和铝(si+al)的总和为0重量%≤(si+al)≤3.0%重量%。根据本发明的合金几乎是无碳的,并且具有最多达0.02重量%的碳,优选≤0.01重量%的碳。这种最高碳含量被认为是不可避免的杂质。在本发明的合金中,只能在最多达0.05重量%的小规模上合金化钙、铍和/或镁以脱氧和脱硫。为了达到一个特别好的脱氧效果,可合金化最多达0.05重量%的cer(铈)或cer混合金属。根据本发明,改善的磁性能可以通过与如下组成匹配的热处理来实现。特别地,已经发现,针对所选择的组成的相变温度的测定以及相对于这些测定的相变温度的热处理温度和冷却速率的测定导致改善的磁性能。此外,考虑到钴含量最高为25重量%的根据本发明的合金不具有有序-无序转变,因此在生产过程中不需要淬火来避免有序和由此产生的脆化。cofe合金通常以0.50mm至0.050mm的极薄尺寸范围的带材厚度使用。为了带材加工,通常将材料热轧并且接着冷轧至其最终厚度。冷却时,在热轧后大约在730℃发生脆化的有序调节,因此必须进行特殊的中间退火并随后进行淬火以抑制有序调节,以便能够进行充分的冷轧。该淬火在根据本发明的合金中被省去,因为它没有有序-无序过渡,这简化了生产。为了获得磁性,对cofe合金进行最终热处理,这也称为磁性最终退火。为此,将材料加热到退火温度,在退火温度保持一定时间,然后以规定的速率冷却。在尽可能高的温度和在干燥、纯净的氢气气氛下进行最终退火是有利的,因为首先氢对杂质的还原变得更有效,其次,晶粒结构变得更粗,因此改善了矫顽场强和磁导率等软磁性能。实际上,cofe系统中的退火温度有上限,因为在大约950℃的二元系统中会发生相变,从而将磁性和铁素体bcc相转换为非磁性和奥氏体fcc相。当发生合金化时,在fcc和bcc相之间会形成两相区域,其中两相共存。bcc相与两相或bcc/fcc混合区之间的转变温度为而两相区与fcc相之间的转变温度为其中两相区域的位置和大小还取决于合金化的类型和程度。如果在两相区域或在fcc区域中发生退火,则在冷却和不完全逆转换后,fcc相的残留会损坏磁性。即使进行了完全的逆转换,由于矫顽场强与晶粒直径成反比,所以破坏作用仍然超出了另外产生的晶粒边界。因此,在低于两相区域bcc+fcc的温度对co含量为20重量%的已知的市售合金进行最终退火。例如对于afk18,建议3h/850℃,对于afk1,建议3h/900℃。对于vacoflux17,建议10h/850℃。在如此低的最终退火温度,由于相对较高的磁晶各向异性(在co含量为17重量%时,k1为约45,000j/m3),这些feco合金限制了特别好的软磁性能的潜力。因此,例如使用vacoflux17带材时,仅能达到4,000的最大磁导率,而矫顽场强通常为1a/cm,这限制了应用。与这些已知的最终退火工艺相比,根据本发明的组成能够进行热处理,该热处理产生的磁性能比feco合金通常采用炉冷却的一步退火更好,而与进行一步退火的温度范围无关。选择合金化,使得两相区域的下限和bcc/fcc相变向上移动,以便能够在纯bcc区域中在高温,例如在925℃以上进行退火。使用先前已知的feco合金无法在如此高的温度进行退火。此外,由于根据本发明的组成,两相区域的宽度,即,较低的转变温度和较高的转变温度之间的差值应尽可能地小。因此,与通过两相区域的冷却以及随后的保持时间或在纯bcc区域中的受控冷却相关联,在两相区域之上的最终退火会得到高的最终退火,即去除可能的磁性不利织构、在h2下的清洁效果以及大晶粒的生长的优点,而无fcc相的磁性有害残留物的风险。已经发现,具有在纯bcc区和bcc/fcc混合区之间的相变在较高的温度(如高于925℃)和具有在较窄的两相区(如小于45k)的组成表现出明显的磁性能改善。根据本发明选择具有该相图特征的特定组合的组成,并相应地热处理以确保大于5000或大于10,000的高磁导率。在fe-co合金中,钒被认为是最有效的元素之一,其提高了电阻且同时将两相区转移至较高温度。钴含量较低时,钒提高转变温度更为有效。对于fe-17co合金,通过添加约2%的钒,甚至可以将转变温度提高到二元feco组成的值以上。在fe-co系统中,从约15%的钴开始,bcc/fcc相变的温度在低至居里温度的温度。由于fcc相是顺磁性的,因此磁性相变不再取决于居里温度,而是取决于bcc/fcc相变。足够高的钒含量会移动bcc/fcc相变经过居里温度tc,从而使顺磁性bcc相变得可见。然而,如果钒含量太高,则混合区的宽度增加。这些组成具有较低的最大磁导率值,尽管bcc/fcc混合区和纯bcc区之间的相变是在较高的温度发生的。结果发现,该组成既影响发生相变的温度又影响混合区的宽度,并且在选择组成时应予以考虑。为了获得最高的磁导率值,热处理的温度可以相对于该组成发生相变的温度进行选择。因此发现,当优化生产过程时,对于特定的组成,更精确地测定发生相变的温度是有利的。这些可以通过dsc测量(差示扫描量热法)测定。dsc测量可以用50mg的样品质量和10k/分钟的dsc加热速率进行,因此在样品加热和冷却过程中测定的相变温度可以用来确定热处理的温度。可以添加铬和其他元素以改善电阻或机械性能。铬和大多数其他元素一样,降低了二元fe-17co合金的两相区。因此,除钒以外的合金份额优选地以这样的方式选择,使得与二元feco合金相比,与钒合计增加了两相区。为此,必须尽可能低地保持使奥氏体特别稳定的杂质和元素(如镍)。为了获得良好的磁性能,以下含量已被证明是优选的:钴,5重量%≤co≤25重量%,优选10重量%≤co≤20重量%的含量,特别优选15重量%≤co≤20重量%的含量钒,0.3重量%≤v≤5.0重量%,优选1.0重量%≤v≤3.0重量%的含量和下列和式:0.2重量%≤cr+si+al+mn≤3.0重量%。根据本发明的合金几乎是无碳的,并且具有最多达0.02重量%的碳,优选≤0.01重量%的碳。这种最高碳含量被认为是不可避免的杂质。在根据本发明的合金中,钙、铍和/或镁只能以不超过0.05重量%的少量添加用于脱氧和脱硫。为了实现特别好的脱氧和脱硫,可以合金化至多0.05重量%的cer或cer混合金属。根据本发明的组成实现了进一步的改进。钴在顺磁性bcc相中的扩散系数高于在铁磁性bcc相中的扩散系数。因此,钒通过将两相区域和居里温度tc分开,在更大的温度范围内实现自扩散,从而使该区域中的热处理或由于冷却通过该区域而产生更大的bcc晶粒结构,因此软磁性能更好。此外,两相区域和居里温度tc的分开意味着在冷却时,通过两相区域bcc/fcc的通路以及到纯bcc相的过渡都完全在顺磁状态下发生。这对软磁性能也具有积极作用。根据本发明,提供了一种制造软磁性feco合金的方法,其中该方法具有以下特征。提供了一种预制品,其基本上由以下组成5重量%≤co≤25重量%0.3重量%≤v≤5.0重量%0重量%≤cr≤3.0重量%0重量%≤si≤3.0重量%0重量%≤mn≤3.0重量%0重量%≤al≤3.0重量%0重量%≤ta≤0.5重量%0重量%≤ni≤0.5重量%0重量%≤mo≤0.5重量%0重量%≤cu≤0.2重量%0重量%≤nb≤0.25重量%0重量%≤ti≤0.05重量%0重量%≤ce≤0.05重量%0重量%≤ca≤0.05重量%0重量%≤mg≤0.05重量%0重量%≤c≤0.02重量%0重量%≤zr≤0.1重量%0重量%≤o≤0.025重量%0重量%≤s≤0.015重量%余量为铁,其中cr+si+al+mn≤3.0重量%和最多达0.2重量%的其他熔体相关的杂质。其他杂质可包括例如元素b、p、n、w、hf、y、re、sc、be、除ce以外的镧系元素中的一种或多种。在一些实施例中,预制品具有冷轧织构或纤维织构。对预制品或由预制品制成的部件进行热处理。在一个实施例中,预制品在温度t1加热,然后从t1冷却到室温。在另一个备选实施例中,预制品在温度t1冷却,然后在高于室温的温度t2冷却,并在t2的温度进一步热处理,其中t1>t2。只有在温度t2的热处理后,预制品才冷却到室温。预制物具有从bcc相区朝向bcc/fcc混合区到fcc相区的相变,其中在升温时,bcc相区与bcc/fcc混合区之间的相变发生在第一转变温度而在升温时,bcc/fcc混合区与fcc相区之间的相变发生在第二转变温度其中温度t1高于温度t2低于转变温度和取决于预制品的组成。借助dsc测量可以确定相变温度和其中在加热过程中确定相变温度在冷却过程中确定相变温度在一个实施例中,在样品质量为50mg和dsc加热速率为10k/分钟时,转变温度高于900℃,优选高于920℃,优选高于940℃。在一个实施例中,在选择温度t1和t2时考虑了预制品的固相线温度。在一个实施例中,900℃≤t1<tm,优选930℃≤t1<tm,优选940℃≤t1<tm,优选960℃≤t1<tm,且700℃≤t2≤1050℃且t2<t1,其中tm是固相线温度。在一个实施例中,和之间的差值小于45k,优选小于25k。在一个实施例中,至少在t1至t2温度范围上的冷却速率为10℃/h至50,000℃/h,优选10℃/h至900℃/h,优选20℃/h至1,000℃/h,优选20℃/h至900℃/h,优选25℃/h至500℃/h。这种冷却速率可用于上述两种热处理。在一个实施例中,之间的差值小于45k,优选小于25k,t1高于t2低于其中940℃≤t1<tm,700℃≤t2≤1050℃和t2<t1,其中tm为固相线温度,并且冷却速率在至少从t1至t2的温度范围上为10℃/h至900℃/h。该合金的性能,即和与热处理的温度t1和t2的这种组合可用于达到特别高的磁导率值。在一个实施例中,将预制品在高于热处理超过30分钟的时间,然后冷却至t2。在一个实施例中,预制品在t1热处理一段时间t1,其中15分钟≤t1≤20小时,然后从t1冷却至t2。在一个实施例中,预制品从t1冷却至t2,在t2热处理一段时间t2,其中30分钟≤t2≤20小时,然后从t2冷却至室温。在将预制品从t1冷却至室温的实施例中,然后可将预制品从室温加热至t2,并根据本文所述的一个实施例在t2进行热处理。由于合金没有有序无序转变,所以在800℃至600℃的温度范围上省略了淬火。例如,800℃至600℃的冷却速率范围可以为100℃/h至500℃/h。然而,原则上也可以选择更慢的冷却速率。上述的冷却速率也可以没有问题地进行到室温。预制品可以从10℃/h至50,000℃/h,优选从10℃/h至1,000℃/h,优选从10℃/h至900℃/h,优选从25℃/h至900℃/h,优选25℃/h至500℃/h的速率从t1冷却至室温。从t2到室温的冷却速率对磁性能的影响较小,因此预制品从t2到室温的可以10℃/h到50,000℃/h、优选100℃/h到1000℃/h的速率冷却。在另一个备选实施例中,将预制品从t1冷却至室温,冷却速率为10℃/h至900°h。在具有从t1到室温的缓慢冷却的实施例中,例如冷却速率小于500℃/h,优选小于200℃/h,也可以避免在温度t2的进一步热处理。经过热处理后,软磁合金可具有下列性能组合之一:最大磁导率μmax≥5,000,和/或电阻率ρ≥0.25μωm,和/或在1.5t的振幅的磁滞损耗phys≤0.07j/kg,矫顽场强hc≤0.7a/cm,在100a/cm的感应b≥1.90t,或最大磁导率μmax≥10,000,和/或电阻率ρ≥0.25μωm,和/或在1.5t的振幅的磁滞损耗phys≤0.06j/kg,和/或矫顽场强hc≤0.6a/cm,优选hc≤0.5a/cm和/或在100a/cm的感应b≥1.95t,或最大磁导率μmax≥12,000,优选μmax≥17,000和/或电阻率ρ≥0.30μωm,和/或在1.5t振幅下的磁滞损耗phys≤0.05j/kg,和/或矫顽场强hc≤0.5a/cm,优选hc≤0.4a/cm,优选hc≤0.3a/cm和/或在100a/cm时的感应b≥2.00t。在一些实施例中,软磁合金具有以下性能组合之一:最大磁导率μmax≥5,000,电阻率ρ≥0.25μωm,在1.5t振幅下的磁滞损耗phys≤0.07j/kg,矫顽场强hc≤0.7a/cm,在100a/cm的感应b≥1.90t,或最大磁导率μmax≥10,000,电阻率ρ≥0.25μωm,在1.5t振幅下的磁滞损耗phys≤0.06j/kg,矫顽场强hc≤0.6a/cm,在100a/cm的感应b≥1.95t,或最大磁导率μmax≥12,000,电阻率ρ≥0.28μωm,在1.5t振幅下的磁滞损耗phys≤0.05j/kg,矫顽场强hc≤0.5a/cm,在100a/cm的感应b≥2.00t。最大磁导率μmax≥17,000,电阻率ρ≥0.30μωm,在1.5t振幅下的磁滞损耗phys≤0.05j/kg,矫顽场强hc≤0.4a/cm,优选hc≤0.3a/cm,在100a/cm的感应b≥2.00t。在一个实施例中,平行于轧制方向测量、与轧制方向成对角线(45°)测量或垂直于轧制方向测量的热处理后的矫顽场强hc的最大差为最大6%,优选为最大3%。换句话说,平行于轧制方向测得并与轧制方向成对角线(45°)测得的矫顽场强hc的最大差为最大6%,优选为最大3%,和/或平行于轧制方向测得并垂直于轧制方向测得的矫顽场强hc的最大差与为最大6%,优选为最大3%,和/或与轧制方向成对角线(45°)测量或垂直于轧制方向测得的在这两个方向之间的矫顽场强hc的最大值为最大6%,优选最大值为3%。对于软磁性feco合金来说,这种极低的各向异性导致在转子或定子应用中沿圆周具有均匀的特性,因此,无需为每层薄板扭曲转子或定子板材层,以确保板材叠层中足够的磁性能各向同性。热处理可以在含氢气氛下进行,也可以在惰性气体下进行。在一个实施例中,在t1的固定炉中进行热处理,并在t2的固定炉或连续炉中进行热处理。在另一个实施例中,在t1的连续炉中和在t2的固定炉或连续炉中进行热处理。预制品在热处理前可能有冷轧织构或纤维织构。预制品可以带材的形式提供。通过冲压、激光切割或水射流切割,可以从带材制造至少一层片材。在一个实施例中,对由带材料制成的冲压、激光切割、腐蚀或水射流切割的板材段进行热处理。在一个实施例中,热处理后,通过绝缘粘合剂将若干板材粘合成板材叠层,或表面氧化以调节绝缘层,并接着将其粘合或激光焊接成板材叠层,或涂覆无机-有机混合涂层,然后继续加工成板材叠层上。在一些实施例中,预制品具有板材叠层的形状,并且板材叠层根据本文所述的一个实施例进行热处理。因此,热处理可以在由板材段制成的冲压或焊接板材叠层上进行。预制品可按如下方法生产。熔体可通过真空感应熔融、电渣重熔或真空电弧重熔等方式提供,其中熔体主要由以下组成:5重量%≤co≤25重量%0.3重量%≤v≤5.0重量%0重量%≤cr≤3.0重量%0重量%≤si≤3.0重量%0重量%≤mn≤3.0重量%0重量%≤al≤3.0重量%0重量%≤ta≤0.5重量%0重量%≤ni≤0.5重量%0重量%≤mo≤0.5重量%0重量%≤cu≤0.2重量%0重量%≤nb≤0.25重量%0重量%≤ti≤0.05重量%0重量%≤ce≤0.05重量%0重量%≤ca≤0.05重量%0重量%≤mg≤0.05重量%0重量%≤c≤0.02重量%0重量%≤zr≤0.1重量%0重量%≤o≤0.025重量%0重量%≤s≤0.025重量%余量为铁,其中cr+si+al+mn≤3.0重量%和最多达0.2重量%的其他杂质。其他杂质可以是b、p、n、w、hf、y、re、sc、be、除ce以外的镧系元素中的一种或多种。熔体凝固成铸块,铸块转化成最终尺寸的预制品,通过热轧和/或锻造和/或冷成型进行成型。在一个实施例中,铸块通过在900℃和1300℃之间的温度下热轧以形成厚度d1的板坯,然后通过冷轧形成厚度d2的带材,其中1.0mm≤d1≤5.0mm,0.05mm≤d2≤1.0mm,其中d2<d1。通过冷轧的冷变形度可达>40%,优选>80%。在一个实施例中,铸块通过在900℃至1300℃之间的温度热轧成坯料而形成,然后通过冷拉拔转变成线材。通过冷拉拔的冷变形度可达>40%,优选>80%。为了减少硬化并因此设定所需的冷变形度,可以在连续炉或固定炉中进行中间尺寸的中间退火。在选择温度t1和/或t2时,可以考虑合金的居里温度。例如,其中tc是居里温度,且tc≥900℃。在一个实施例中,选择在两相区与居里温度tc分离的组成中,存在另一个具有较高自扩散的温度范围,从而通过在该范围进行热处理或通过该范围冷却,可以获得较大的bcc晶粒结构,从而获得较好的软磁性能。此外,两相区和居里温度tc的分离使得在冷却时穿过两相区bcc/fcc和转变到纯bcc相区都在完全顺磁状态下进行。随着温度t2的选择使得软磁性能进一步改善。在一个实施例中,最终退火后的平均晶粒尺寸为至少100μm,优选至少200μm,优选至少250μm。在一个实施例中,退火合金的测量密度比以下密度低超过0.10%:该密度为由合金的金属元素的平均原子量、从对应二元feco合金的金属元素的平均原子量和从退火二元feco合金的测量密度根据比例法计算的密度。由于热处理,成品合金中的硫含量可小于熔体中的硫含量。例如,熔体中的硫含量上限可为0.025重量%,而成品软磁合金中的硫含量上限为0.015重量%。在一个实施例中,用于电绝缘的预制品产品还涂覆有氧化物层。例如,如果在板材叠层中使用预产品,则可以应用此实施例。板材段或板材叠层可涂覆有氧化物层。该预制品可涂覆甲醇镁层或优选丙醇锆层,该层在热处理期间转化为绝缘氧化物层。预制品可以在含氧或含水蒸汽的气氛中进行热处理以形成电绝缘层。在一个实施例中,从预制品冲压、激光切割或腐蚀的板材段还经受最终退火,然后借助绝缘粘合剂将退火的单个板材粘合成板材叠层上,或者将经退火的单个板材表面氧化以调节绝缘层并接着粘合、焊接或激光焊接成板材叠层,或者将经退火的单个板材涂覆无机-有机混合涂层,如remisol-c5,并接着继续加工成板材叠层。根据前述实施例之一的软磁合金可在本文所述的方法中生产,可用于电机,例如电动机和/或发电机的定子和/或转子中,和/或在变压器中和/或在电磁致动器中。附图说明现在将参考附图和以下实施例更详细地解释本发明的实施例。图1示出了根据本发明热处理的三个变化方案的示意图(不成比例)。图2以批次930423为例示出了相变时dsc加热和冷却曲线的典型过程。图3示出了对于加热(dsc)和冷却(dsc),与二元fe-17co熔体相比,根据本发明的fe-17co-cr-v合金随着v含量增加的相变的第一起始温度的示意图。相对于第二y轴绘制的是最大磁导率μmax的走向。图4示出了根据多线性回归的感应值b的系数。图5示出了根据多线性回归的电阻系数。图6示出了批次930329(fe-17co1.5v-0.5cr)的矫顽场强hc作为往复晶粒直径d的倒数对于不同退火的函数。图7对于不同批次示出了具有不同v含量的fe-17co特殊熔体的转变温度和以及达到的最佳矫顽场强hc。这些合金还含有总和最多达0.6重量%的cr和/或si。表29示出了图7的数据,包括各个退火的细节。图8示出了第一退火阶段的分步退火后的最大磁导率和矫顽场强。图9示出了在高于相变的4h1000℃的第一退火阶段后在低于相变的第二退火阶段的分步退火后的最大磁导率和矫顽场强。图10示出了批次930329(fe-17co-0.5cr-1.5v)和930330(fe-17co-2.0v)依赖于冷变形度的矫顽场强hc。图11示出了批次93/0330(fe-17co-2v)的(200)-极图。a)冷变形:左上。b)在910℃最终退火10小时后:中上。c)最后在1050℃最终退火4小时后:右上。d)在1050℃最终退火4h和910℃最终退火10h后:下。图12示出了,对于规定的退火,批次930330(fe-17co-2v)与轧制方向平行(纵向)、与轧制方向成45°、与轧制方向垂直(横向)测量的矫顽场强hc。图13示出了,对于规定的退火,批次930335(fe-23co-2v)与轧制方向平行(纵向)、与轧制方向成45°、与轧制方向垂直(横向)测量的矫顽场强hc。图14示出了,与典型的sife(trafopermn4)和典型的feco合金相比,根据本发明的批次930329(fe-17co-1.5v-0.5cr)、930505(fe-17co-1.4v-0.4si)和930330(fe-17co-2v)在最佳退火后的新曲线。图15示出了,与典型的sife(trafopermn4)和典型的feco合金相比,根据本发明的批次930329(fe-17co-1.5v-0.5cr)、930505(fe-17co-1.4v-0.4si)和930330(fe-17co-2v)在最佳退火后的磁导率。图16示出了,与典型的sife(trafopermn4)和feco合金相比,根据本发明的批次930329(fe-17co-1.5v-0.5cr)和930330(fe-17co-2v)在最佳退火后在1.5t的感应振幅(induktionsamplitude)时的损耗。板材厚度分别为0.35mm。图17示出了,对于来自表25的数据,最大磁导率作为基于fe-17co合金的相对密度差δρ的函数的图。具体实施方式根据本发明,提供一种软磁合金,其主要由以下组成:5重量%≤co≤25重量%0.3重量%≤v≤5.0重量%0重量%≤cr≤3.0重量%0重量%≤si≤3.0重量%0重量%≤mn≤3.0重量%0重量%≤al≤3.0重量%0重量%≤ni≤0.5重量%0重量%≤mo≤0.5重量%0重量%≤ta≤0.5重量%0重量%≤cu≤0.2重量%0重量%≤nb≤0.1重量%0重量%≤ti≤0.05重量%0重量%≤ce≤0.05重量%0重量%≤ca≤0.05重量%0重量%≤mg≤0.05重量%0重量%≤c≤0.02重量%0重量%≤zr≤0.1重量%0重量%≤o≤0.025重量%0重量%≤s≤0.015重量%余量为铁,和最多为0.2重量%的其他熔融导致的杂质。例如,杂质可以是元素b、p、n、w、hf、y、re、sc、be、除ce以外的镧系元素中的一种或多种。为了提高电阻,除了合金元素钒之外,还可以在一定程度上合金化cr、si、al和mn中的一种或多种,其中满足以下和式:0.05重量%≤cr+si+al+mn≤3.0重量%根据本发明的合金优选在真空感应炉中熔融。但真空电弧重熔和电渣重融也是可行的。熔体首先凝固成去除氧化皮的块体(或铸锭、铸块),然后在900℃至1300℃之间的温度锻造或热轧。可替代的,氧化皮的去除也可以首先在锻造或热轧的杆材上进行。需要的尺寸可以通过带材、坯料或杆材的热成型来实现。热轧材料可以通过喷砂、磨光或剥落去除表面氧化物。然而,有利的最终尺寸也可以通过带材、杆材或线材的冷成型来实现。在冷轧带材的情况下,可以进行磨光工艺以去除热轧工艺中的氧化物。如果冷成型后硬化度过高,则可以在400℃至1300℃之间的温度进行一次或多次中间退火以恢复和重结晶。中间退火的厚度或直径应当如此选择,使得优选达到冷变形>40%直到最终厚度,特别是>80%的冷变形。最后一个加工步骤是在700℃和固相线温度tm(通常最大为1200℃)之间的温度进行热处理,这也称为磁最终退火。最终退火优选在纯净干燥的氢气气氛下进行。还可以在保护气体或在真空中进行退火。图1示出了根据本发明热处理的关于相变、特别是fcc、fcc+bcc和bcc区域的三个变化方案的示意图。对于在图1中以实线表示的方案1,在fcc区中的第一退火阶段之后直接进行在bcc区中的第二退火阶段。第二退火阶段是可选的,可以用来进一步改善软磁性能,特别是磁导率和磁滞损耗。对于在图1中以线虚线表示的方案2,在fcc区中的第一退火阶段首先冷却到室温。在bcc区中的第二退火阶段在稍后的时间点发生。对于在图1中以点虚线表示的方案3,从在fcc区中的退火阶段受控地冷却到室温。这种类型的受控冷却也可以在方案1中在从第一阶段到第二阶段的冷却中进行(图1中未显示)。因此,根据本发明,退火可以分两个阶段进行,或者通过从高于上转变温度的温度进行受控冷却来进行。受控冷却是指存在定义的冷却速率来优化地调节软磁特性。无论如何,其中一个退火阶段发生在fcc区。根据本发明的退火可以在连续炉中或在固定炉中进行。在本发明的退火中,在900℃(如果则高于)和tm之间高于的温度,在奥氏体fcc区对合金进行至少一次退火以产生大晶粒,利用氢的清洁作用,并去除可能的对磁性不利的织构。高于的最终退火阶段在固定退火或在连续炉中进行。备选地,该阶段的热处理也可以在连续炉中在带材上进行。接着在bcc区中以每小时10-50,000℃、优选以每小时20-1,000℃的速率将合金冷却至室温或在700℃-1,000℃之间的温度。第二退火阶段可在铁素体bcc区中通过加热或通过在700℃与1000℃(如果则低于)之间的温度保持来进行,以除去fcc相的可能残留。然后,在磁性最终退火后,以每小时10至50,000℃的速率、优选以每小时20至1,000℃的速率,从退火温度冷却合金。根据本发明的合金具有从bcc相区到bcc/fcc混合区的相变,并且在稍高一些的温度还具有从bcc/fcc混合区到fcc相区的相变,其中随着温度升高,bcc相区和bcc/fcc混合区之间的相变发生在第一转变温度处,以及随着温度进一步升高,bcc/fcc混合区和fcc相区之间的相变发生在第二转变温度处,如图2所示。从bcc相区向bcc/fcc混合区的相变、从bcc/fcc混合区向fcc相区的相变发生的温度可以通过dsc测量来确定。以批次930423为例,图2示出了一个相变时的典型的dsc加热和冷却曲线的过程。相变的居里温度和第一起始温度也示于图2中。下图示出了使用netzsch公司的动态热流差示量热计实施的dsc测量的结果。在一个炉子中有两个相同的刚玉坩埚(al2o3),其中一个装有实际样品,另一个装有用作参考的校准样品。两个坩埚都经历了相同的温度程序,可以包括加热、冷却或等温段的组合。通过测量样品与参考样品在定义的导热路径处的温差,定量获得热流差。dsc测量中确定的各种极大值和极小值(峰)可以根据它们的曲线形状分配给特定类型的相变。绘制了典型的曲线,但材料特性曲线也取决于测量条件,特别是样品质量以及加热速率和冷却速率。为了保证测量的可比性,将测量仪器的加热速率和冷却速率以及这里所研究样品的样品质量选择为相同的。本实验采用的加热速率和冷却速率分别为10k/min,样品质量分别为50mg。通过以规定的加热速率加热规定质量的样品来借助dsc测量测定转变温度和在该测量中,转变温度由第一起始来表示。在din51005(“热分析”)中定义的此参数也称为外推峰起始温度,它代表相变的开始,并且被定义为外推初始基线与通过上升或下降的峰侧缘的线性部分的切线的交点。该参数的优点在于它与样品质量以及加热速率或冷却速率无关。第一起始温度之间的差值定义为两相区域的宽度:组成对转变温度和的影响借助用dsc法进行测定。图3示出了与二元fe-17co合金(正方形)相比,具有增加的v含量的fe-17co-cr-v合金(圆圈)的相变对于加热的(实心符号)和冷却(空心符号)的第一起始温度。合金的组成在表1至表4中给出。加热(dsc)和冷却(dsc)的峰-居里温度tc以菱形表示。对于具有较低v含量的特定熔体,tc对应于相变温度。在副轴上绘制了最高的最大磁导率μmax(三角形)。v含量在1-3重量%之间在这里可以实现最高的最大磁导率。图3表明,随着v含量的增加,相变以及发生在高温下,并且两相区bcc+fcc的宽度(即,)增加。为了调节软磁性能实施最终退火。在本实验中,这始终是在h2保护气氛下进行。所用的h2质量始终为氢3.0(或工业级氢气),h2含量>99.9%,其中h2o≤40ppm-mol,o2≤10ppm-mol,n2≤100ppm-v。使用由重5kg的铸块制成的带材研究了合金的磁性。合金在真空下熔融,然后倒入约1500℃的扁平模具中。从各个铸块上磨掉氧化皮后,在从约1000℃至1300℃的温度将这些铸块热轧成3.5毫米厚的带材。然后将所得的热轧带材酸洗以除去氧化物皮,然后冷轧至0.35mm的厚度。为了表征磁性能,将样品环从带材上冲出,并切割电阻条。在电阻条上确定电阻ρ。在室温下以退火状态生产的样品环上测量了最大磁导率μmax,矫顽场强hc,场强20、25、50、90、100和160a/cm的感应b,剩磁br和磁滞损耗physt。磁滞损耗是通过在不同频率下以1.5t的感应振幅测量损耗来确定的。通过线性回归确定的曲线p/f对f的截距给出了磁滞损耗。从铸块上锯出圆盘以分析元素。分析结果见表1至表4。表1显示了金属元素的湿化学分析法,以确定其基本组成。余量为铁,未给出<0.01%的其他元素,其中数据以重量%计。表2显示了通过热气提取对表1的批次中的非金属杂质的分析,其中数据以重量%计。表3示出了金属元素的湿化学分析,以微调基本组成并限制组成范围和杂质。余量为铁,未指定<0.01%的其他元素。数据以重量%计。在批次930502和930503中,使用了杂质程度更高的铁原料。表4显示了通过热气提取对表3的批次中的非金属杂质的分析,数据以重量%计。表3继续显示对两个大型熔体的金属元素的分析。余量为铁,76/4988大熔体的p-含量为0.003重量%,76/5180大熔体的p含量为0.002重量%,未给出<0.01%的其他元素。表4还示出了通过热气提取对表3的两个大型熔体的非金属杂质的分析,数据为重量%。图4和图5示出了借助多线性回归,对主要合金元素钴、钒和铬对最佳退火的感应值和电阻的影响的统计评估。图4示出了根据多线性回归的感应值b的系数。b值后面的数字(如b20)表示场强(a/cm)。条形图表明添加1重量%时的感应值变化。仅显示回归值大于回归误差的那些元素。图5示出了多线性回归后的电阻系数。条形图表明合金化有1重量%的各元素的电阻的变化。从这些图可以看出,钒比铬降低了低感应。为此,在饱和度(b160)相同的情况下,铬比钒增加了更多的电阻。co增加了饱和度(b160),但对低感应值和电阻影响很小。表7示出了与不是本发明的退火方案相比,带材厚度为0.35mm的批次93/0330的根据本发明的退火方案,参见图1。除非另有规定,冷却速率为150℃/h。在测量前未进行去磁处理。图6示出了对于不同退火而言,批次930329(fe-17co1.5v-0.5cr)的矫顽场强hc作为晶粒直径d的倒数的函数。表5显示在规定退火后的平均晶粒尺寸d和矫顽场强hc以及最大磁导率μmax,见图4。冷却速率为150℃/h。表6示出了dsc转变温度和居里温度tc。单位为℃。#nv意味着在dsc测量中不能检测到任何信号。fe-co合金具有非常好的软磁性能的原因之一是异常大的晶粒结构,这是在fcc区域退火后实现的。将批次93/0330(fe-17co-2v)在1050℃下短暂退火4小时后,确定晶粒大小为354-447μm。持续退火几天后,只有在bcc区域进行退火才能获得相似大小的晶粒。图6借助批次930329示意性示出了矫顽场强hc与晶粒尺寸的倒数的关系。示出了线性关系。为了比较上述退火方案,以示例方式检测了批次930330。表8示出了第一退火阶段的分步退火后的结果(批次93/0330),见图6。冷却速率为150℃/h。只要第一次退火发生在较低的fcc区(这里在1050℃),所有退火方案都显示出非常好的软磁性能,比在纯bcc区退火要好得多。在前一次fcc区的第一退火阶段后在较高bcc区的第二退火阶段进一步改善了上述值。图7示出了不同v含量的fe-17co特定熔体的转变温度和作为所实现的最佳矫顽场强hc的函数。这些标签反映了v的含量。图7显示v含量对软磁性能的调节是决定性的。如果v含量太低,就不会增加。如果v含量太高,则随着钒使两相区变宽,软磁性能恶化,另见图3和表6。这在约1.4至2重量%钒时导致矫顽场强hc的最小值。为了寻找最佳退火温度,在不同的退火温度对样品进行退火,然后进行测量。如果必要的退火次数大于可用的样品数目,则同一样品组通常在不同的温度退火。在这种所谓的“分步退火”中,从较低的起始温度开始,并在较高的温度逐步退火。可以使用分步退火例如追踪对磁性有直接影响的消除区域(ausscheidungsbereiche)、重结晶温度或相变。图8示出了第一退火阶段分步退火后的最大磁导率和矫顽场强。表9示出了,在先前的高于相变的第一退火阶段4h1000℃后,批次93/0330在低于相变的分步退火的结果。冷却速率为150℃/h。可以看到大约1000℃的扩展最大值。还显示了相应的dsc测量值,用于与相位位置进行比较。图9示出了,在先前的高于相变的第一退火阶段4h1000℃(菱形)后,低于相变的第二退火阶段的分步退火后的最大磁导率和矫顽场强(圆形)。在测量静态值之前不要去磁。可见最大值在950℃。在1000℃分步退火的最后退火之后,样品再在950℃退火10h(三角形)。在950℃分步退火的原始值已不复存在。再次穿过两相区bcc+fcc将损坏软磁特性。对不同组成的合金测量了在不同退火后的磁性能。结果总结于表10至表24中。给出了值b20、b25、b50、b90、b100、b160(t)hc(a/cm)、μmax、br(t)和physt1.5t(ws/kg)。表10示出了所选批次以150℃/h的冷却速率在850℃退火4h后的结果。这些实施例不是根据本发明的。表11示出了所选批次以150℃/h的冷却速率在910℃退火10h后的结果。在测量静态值之前未去磁。这些实施例不是根据本发明的。表12示出了在所选批次在910℃退火10h且冷却至室温后再接着在930℃退火70h之后的结果。冷却速率为150℃/h。在测量静态值之前未去磁。这些实施例不是根据本发明的。表13示出了所选批次在1000℃退火4h后的结果。冷却速率为150℃/h。在测量静态值之前未去磁。表14示出了所选批次在第一退火阶段于1000℃退火4h且冷却至室温并接着在第二退火阶段于910℃退火10h的结果。冷却速率为150℃/h。在测量静态值之前未去磁。表15示出了所有fe-co-v-cr批次在1050℃退火4h后的结果。冷却速率为150℃/h。在测量静态值之前未去磁。在850℃下退火4h后测量了批次930322至930339的电阻。对于富v的批次930422和930423,略低于1050℃。可在表18中找到调整的退火阶段。表16示出了所有fe-co-v-cr批次在第一退火阶段中在1050℃退火4h且冷却至室温并接着在第二退火阶段于910℃退火10h之后的结果。冷却速率为150℃/h。测量前去磁。对于灰色标记的批次,高于910℃不够多,或高于910℃太多。可在表17中找到调整的退火阶段。表17示出了调整这些批次的退火后的结果,其中dsc测量的转变温度(表6)根据本发明与4h1050℃+10h910℃的退火(表15和16)不一致,或仅略微不一致。冷却速率为150℃/h。对于4h1050℃的退火,在测量前未去磁,而对于所有其他退火,在测量前均进行去磁。表18示出了批次930423在不同相区中退火后的结果,以阐明铁磁性bcc区和顺磁性bcc对磁性能的影响,另见图2。冷却速率为150℃/h。对于4h1050℃退火,在测量前未去磁,而对于所有其他退火,在测量前均去磁。表19示出了所选批次在1050℃退火4h接着以50℃/h缓慢冷却至室温后的结果。在测量静态值之前未去磁。表20示出了在所选批次在1050℃退火4h且以50℃/h缓慢冷却至室温以及在910℃10h且以约150℃/h炉冷的第二退火阶段之后的结果。在测量静态值之前未去磁。表21示出了所选批次在1100℃下退火4h后的结果。冷却速率为150℃/h。除批次930422和930423外,在测量静态值之前未去磁。表22示出了在所选批次在第一退火阶段中在1100℃退火4h且冷却至室温以及在910℃10h的第二退火阶段之后的结果。冷却速率为150℃/h。在测量静态值之前未去磁。表23示出了所选批次在1150℃下退火4h后的结果,冷却速率为150℃/h。除批次930442外,在测量静态值之前未去磁。表24示出了在所选批次在第一退火阶段中在1150℃退火4h且冷却至室温以及在910℃10h的第二退火阶段之后的结果。冷却速率为150℃/h。在测量静态值之前未去磁。表25示出了具有各种添加剂的各种fe-17co合金组成的最大磁导率和密度的数据。从二元合金fe-16.98co(其测量密度为7.942g/cm3,其平均原子量为56.371g/mol(根据金属合金元素的分析的含量计算))开始,对于添加了v、cr、mn、si、al和其他金属元素的fe-17co合金,借助其平均原子量计算其虚拟密度,并将其与测得的密度进行比较。例如对于fe-17.19co-1.97v合金(批次93/0330),平均原子量为56.281g/mol。现在可以根据比例法(7.942g/cm3×56.281/56.371=7.929g/cm3)来计算出该fe-17.19co-1.97v合金应具有的虚拟密度,若其晶格常数与二元fe-16.98co合金保持不变。然而,实际上,在该合金上测得的密度为7.909g/cm3,比虚拟密度7.929g/cm3低-0.26%。这意味着该合金的晶格常数必须比二元合金的晶格常数大大约0.085%。表26示出了所选批次和退火的数据,这些数据同时显示出特别高的最大磁导率和低的磁滞损耗,并且在100a/cm时显示出感应b(b100)水平非常高。表27示出了所选批次和退火的杂质c和s的数据,以ppm为单位。通过在1050℃在氢气下退火,这些杂质被有效地减少。表28示出了两种大型熔体76/4988和76/5180的磁值。记号a或b的意思是来自铸块a或铸块b——熔体分别倒入两个模具中。批次76/4988的电阻率为0.306μωm,批次76/5180的电阻率为0.318μωm。表29示出了对于不同批次由具有不同v含量的fe-17co特殊熔体获得的转变温度和以及最佳矫顽场强hc,包括相应的退火处理的细节。这些合金还含有总和最多达0.6重量%的cr和/或si。这些数据的图示于图7。图8和图9表明,在根据本发明的合金930330中存在的bcc/fcc相变对最大磁导率和矫顽场强有很大的影响。在第一退火阶段(图8),第一次冷却开始(两相区下边界)与μmax的增加一致,在第一次加热开始(两相区上边界)时,μmax变为最大值或hc变为最小值)。在fcc区中温度较高时,磁性会再次变差。在第二退火阶段(图9),μmax在以下变为最大值,并随着进入两相区而下降。如果越过两相区并在(此处为950℃)下再次退火,则不再达到μmax的最大值,这可能是由于该样品已经穿过bcc+fcc混合区两次以及由此产生的晶界引起的。总之,可以确定,如果第一退火阶段发生高于而第二退火阶段发生小于则可获得最佳的磁性能。研究了冷变形程度对磁性能的影响。图10示出了批次930329(fe-17co-0.5cr-1.5v)和930330(fe-17co-2.0v)依赖于冷变形度的矫顽场强hc。在“无中间退火”时,热轧厚度相当于0%的kv,在“具有中间退火”时,中间退火的厚度相当于0%的kv。最终厚度为d2的带材的冷变形程度kv定义为,由于轧制时的宽度可以忽略不计,因此相对于非冷变形的初始厚度d1的厚度减小的百分比。例如,非冷变形的初始厚度d1可以通过热轧或通过中间退火(zgl)实现。kv[%]=[(d1-d2)/d1]x100在图10中,例如从矫顽场强hc可以看出,当kv增加(通过在不同的d1=1.3mm;1.0mm;0.60mm和相同的最终厚度d2=0.35mm的情况下进行中间退火来实现)时,磁学性质改善了最大约90%kv。若从3.5mm的恒定d1(热轧厚度)出发,并且以0.20mm和0.10mm的高的轧制度实现冷成型,则hc会再次增加,如虚线所示。这可以通过以下来解释:在最高的冷变形度下,晶粒的成核点太多,并且晶粒在退火过程中相互干扰生长。在t1=1000℃下进行4h和在t2=910℃进行10h的最终退火后,无需中间退火,即可制备批次930329(fe-17co-0.5cr-1.5v)的合金(均以重量%计),最终厚度为0.35mm时平均粒度为0.25mm,最终厚度为0.20mm时平均粒度为0.21mm,最终厚度0.10mm时平均粒度为0.15mm。因此,存在最佳的冷变形度,约为90%。为了研究织构的形成是否对磁性起决定性作用,通过在50mm×45mm的片材上通过x射线衍射来确定织构。图11显示了批次93/0330(fe-17co-2v)的(200)极图。左侧的结果是具有轧制织构的未退火板材的结果。中间的板材的结果是在910℃退火10h且具有仅非常弱的织构。右侧的板材的结果是在1050℃退火4h且没有织构。下侧的板材的结果是在1050℃退火4h且在910℃退火10h且没有织构。在此,根据角度将cu-kα=0.154059295nm照射到样品上,并用2mm的带孔板测量衍射强度。具有2°角度范围和能量分散操作的lynxexe半导体带状检测器用作检测器。如(200)极图所示,在未经退火的硬轧状态下出现轧制织构,在fcc区在h2中在1050℃退火4h后,轧制织构已完全溶解。缺少织构也与方向相关的hc的测量一致。为此,从相对于轧制方向的各个方向(纵向=0°,对角线=45°,横向=90°)上取五个hc带,每个带的尺寸为50mm×10mm,并在-koerzimaten中进行测量。图12示出了,对于规定的退火,批次930330(fe-17co-2v)与轧制方向平行(纵向)、与轧制方向成45°、与轧制方向垂直(横向)测量的矫顽场强hc。每个点是5次测量的平均值。误差条代表标准偏差。图13示出了,对于规定的退火,批次930335(fe-23co-2v)与轧制方向平行(纵向)、与轧制方向成45°、与轧制方向垂直(横向)测量的矫顽场强hc。每个点是5次测量的平均值。误差条代表标准偏差。在910℃4h退火后,平均值显示出各向异性,但是考虑到统计误差,该各向异性并不明显。然而,这种轻微的各向异性与来自相应极图的织构的残留相重合(图11中上方的中间图)。在4h1050℃和4h1050℃+10h910℃退火后,hc的平均值几乎相同。在1050℃的fcc区的退火会完全消除现有的织构,随后在910℃的bcc区的第二退火阶段不会产生新的织构。在下文中,根据本发明的合金的磁性示例性借助本发明的批次930329(fe-17co-1.5v-0.5cr)和930330(fe-17co-2.0v)与比较合金进行比较。作为比较合金,有典型的elektroblechtrafopermn4(fe-2.5si-al-mn)和三种feco合金vacoflux17(fe-17co-2cr-mo-v-si)、vacoflux48(fe-49co-1.9v)和hypocore特殊熔体。hypocore特殊熔体根据carpentertechnologies公司发布的组成进行熔融(fe-5co-2.3si-1mn-0.3cr,数据以重量%给出)。图14示出了,与sife(trafopermn4)和feco比较合金相比,根据本发明的批次930329(fe-17co-1.5v-0.5cr)、930505(fe-17co-1.4v-0.4si)和930330(fe-17co-2v)在最佳退火后的新曲线。图15示出了,与ρsife(trafopermn4)和feco比较合金相比,根据本发明的批次930329(fe-17co-1.5v-0.5cr)、930505(fe-17co-1.4v-0.4si)和930330(fe-17co-2v)在最佳退火后的磁导率。图16示出了,与sife(trafopermn4)和feco比较合金相比,根据本发明的批次930329(fe-17co-1.5v-0.5cr)和930330(fe-17co-2v)在最佳退火后在1.5t的振幅时的损耗。930329、930330和trafopermn4的磁滞损耗(y截距)相似。板材厚度分别为0.35mm。图17示出了基于fe-17co的合金的最大磁导率与相对密度差δρ的关系(表25中的数据)。可以看出,相对密度差为-0.10%至-0.35%的合金可获得较高的最大磁导率,相对密度差为-0.20%至-0.35%的合金可获得特别高的最大磁导率。二元fe-17co合金的相对密度差最终意味着,这些合金的晶格常数必须比二元合金的晶格常数大一些。较大的晶格常数意味着,由于晶格中的原子距离较大,用于换位过程的活化能较低,因此扩散性更好。这也有助于晶粒长大,因此有助于降低矫顽场强或提高磁导率。为了在生产规模上研究根据本发明的合金的性能,在正常生产中进行了两个大的熔融。为此,在真空感应炉中将2.2t所需的组成熔化,并在设定和分析精确的组成后,将其倒入两个直径340mm的圆形模具中。固化并冷却后,将圆块从模具中取出,并在燃气回转炉中加热至1170℃的温度进行热轧。接着将充分加热的块体在初轧轧辊上热轧成横截面为231x96mm2的板坯。然后将这些板坯的所有面磨成226x93mm2的尺寸以去除氧化皮。从批次76/4988将由此获得的两个板坯在热轧机上轧制成热轧带材。为此,首先将板坯在1130℃的温度加热,然后在充分加热后轧制成热轧带材。带材的最终厚度为2.6mm。该带材的最终轧制温度为900℃,卷轴温度为828℃。另一带材的最终厚度选为1.9mm。该带材的最终轧制温度为871℃,卷轴温度为718℃。然后对两个热轧带材进行喷砂处理,以去除氧化皮。将部分热轧带带材在h2保护气体气氛下于750℃中间退火1小时。将热轧带材的另一部分在h2保护气体气氛下于1050℃中间退火1小时。热轧带材的其余部分保持原样,而不经中间退火。随后轧制至最终厚度,其中使带材均在中间厚度从两侧去除氧化物。在带材热轧之前,另外从板坯上锯下15mm厚度的段,并且通过热轧(厚度3.5mm)成带材,酸洗所获得的热轧带材,然后在技术中心进行冷轧,由此生产带材。列出所获得的结果用于比较。从批次76/5180两端的两个板坯上分别锯下15mm厚的圆片。在1200℃加热这些圆片,然后热轧成3.5mm厚的带材。对由此获得的热轧带材进行酸洗以去除氧化物。然后将其冷轧至0.35mm的厚度。由此获得的所有带材制成冲压环,并经历最终退火处理。表28示出了磁值的结果。批次76/4988的电阻率是0.306μωm,批次76/5180的电阻率是0.318μωm。从表28中可以看出,与vacoflux17相比,co含量小于30重量%的市售合金所测得的大型熔体样品的磁性能更好。对于76/5180b的大型熔体样品测量的最大磁导率大于20,000。因此,根据本发明的合金适合于大规模工业生产具有改善的磁性的带状材料。根据本发明的合金对于每种场强均显示比vacoflux17更高的感应。在高于断点的感应,新的合金位于trafopermn4和vacoflux48之间。接近磁饱和的在场强为400a/cm时的经空气气流校正的感应b对于两个批次为2.264t(这对应于2.214t的极化j)。因此,在典型的电动机和发电机的工作区域中,新合金的扭矩将比vacoflux17和trafopermn4更高。从930329和930330的比较中可以看出,钒与上述热处理相结合,可以增加磁滞回线的矩形度,并达到一定程度,根据合金的不同,最大磁导率几乎与vacoflux48的磁导率一样大。这是令人惊讶且极其出人意料的,因为在约50%co时,各向异性常数k1会过零,而在17%co时则不存在。相反,当17%co时,fe-co体系中的各向异性常数k1非常高。在与trafopermn4的磁滞损耗水平相当的磁滞损耗下,也表现出很好的软磁性能。但随着频率的增加,由于新合金的电阻较高,在相同的带材厚度,trafopermn4的损耗增加比新的合金少很多。然而,这种效果可以通过选择稍低的带材厚度和相应较低的涡流损耗来弥补。总之,提供了一种具有更好的软磁性能的高磁导率的软磁合金,例如,具有比现有的和市售的feco合金显著更高的磁导率和更低的磁滞损耗,同时提供了更高的饱和度。同时,这种新的合金提供了比之前已知的和市售的co含量在10至30重量%之间的合金显著更低的磁滞损耗,尤其是这种合金还从未达到的显著更高的磁导率水平。本发明的合金也可以工业规模且廉价地生产。表1批次93/cson03220.00500.00120.00160.001203230.00450.00100.01500.001103240.00380.00100.01300.000903250.00310.00110.01000.001103260.00320.00110.00850.001203270.00320.00110.00970.001103280.00290.00110.01000.001303290.00280.00120.00930.001303300.00240.00110.00920.001403310.00300.00110.00870.001103320.00220.00110.00680.001203330.00400.00110.00140.001103340.00360.00100.00220.001303350.00340.00100.01200.001603360.00400.00100.00880.001403370.00390.00100.00580.001203380.00360.00110.00820.001203390.00250.00090.00260.0010表2表3表4表5表6表7表8表9表10表11表12表13表14表15表16表17表18表19表20表21表22表23表24表25表26表27表28表29当前第1页12