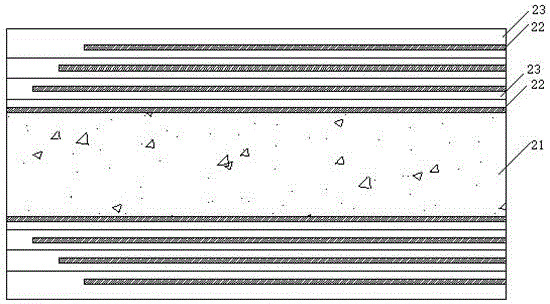
本发明涉及一种绝缘管,特别涉及一种复合绝缘管的制备方法。
背景技术:
:电线电缆的应用主要分为三大类:电力系统、信息传输系统和机械设备以及仪器仪表系统。电线电缆产品主要分为五大类:裸电线及裸导体制品、电力电缆、电气装备用电线电缆、通讯电缆及光纤和电磁线。其中电力电缆的主要特征在导体外挤(绕)包绝缘层,如架空绝缘电缆,或几芯绞合(对应电力系统的相线、零线和地线),如二芯以上架空绝缘电缆,或再增加护套层,如塑料/橡套电线电缆。但是一些行业对电线电缆的耐侯性能以及防脆裂性能要求越来越高,普通多功能线缆采用常规聚氯乙烯、交联聚烯烃等材料作为绝缘和护套材料,而这些材料制成的绝缘管存在整体强度较差,耐候性欠佳等不足。针对上述现象,现一般采用eva与碳黑混合制备成半导电热缩管,再在半导电热缩管外表面通过粘性材料挤包eva绝缘层,最后进行烘干处理,通过这样的方法在生产的过程中,在eva绝缘层与半导电层之间容易存在气泡,造成复合绝缘管的电性能差。技术实现要素:本发明要解决的技术问题是提供一种能够避免产生气泡,提高电性能的复合绝缘管的制备方法。为解决上述技术问题,本发明的技术方案为:一种复合绝缘管的制备方法,其创新点在于:所述制备方法包括如下步骤:步骤1:在内导体上热缩包覆一层长度与内导体长度一致的半导电热缩管;步骤2:在上一步骤形成的半导电热缩管上热缩包覆至少一层长度与内导体长度一致的绝缘热缩管;步骤3:在上一步骤形成的最外层绝缘热缩管上热缩包覆一层长度与绝缘热缩管长度存在一定梯差的半导电热缩管,且该半导电热缩管的长度小于绝缘热缩管的长度;步骤4:在上一步骤形成的半导电热缩管上热缩包覆至少一层长度与内导体长度一致的绝缘热缩管;步骤5:在上一步骤形成的最外层绝缘热缩管上热缩包覆一层长度与上层半导电热缩管长度存在一定梯差的半导电热缩管,且该半导电热缩管的长度小于上层半导电热缩管的长度;步骤6:根据客户要求的产品规格,重复步骤4和步骤5数次,最后在最外层的半导电热缩管上热缩包覆一层长度与内导体长度一致的绝缘热缩管,形成复合绝缘管半成品;步骤7:将步骤6制备成的复合绝缘管半成品放入热压容器内,先加热至75-85℃,至复合绝缘管半成品呈半熔融状态,同时导入氮气,并逐渐加压至0.8-1mpa;步骤8:待热压容器内的压力达标后,再将热压容器加热至175-185℃,保温4-6min,最后仍保持0.8-1mpa的压力进行降温,直至降温至室温,制得复合绝缘管成品。进一步地,所述各半导电热缩管的管壁厚度为0.5-1mm。进一步地,所述相邻两半导电热缩管之间的绝缘热缩管的总管壁厚度达4mm。进一步地,所述热压容器包括热压罐罐体,所述热压罐罐体一端设有封闭端,所述热压罐罐体的另一端设有可打开或关闭的罐门;所述热压罐罐体的上部中心设有电动机,所述电动机的出轴处通过联轴器连接有风机,所述风机的出风口处连接有电加热器,所述电加热器上远离风机一侧连接有冷却器,在距冷却器一定距离的下方的热压罐罐体内壁间设置有隔板,且在隔板的四个端角处设有贯穿隔板且下端与热压罐罐体底面固定连接的导风管;所述导风管的上端开口,各导风管的内侧壁上还均匀分布有出风孔,且导风管的上端开口低于冷却器;所述热压罐罐体的底部设有支撑底座,所述热压罐罐体内底部设有滑动底座,该滑动底座设置在导风管之间;所述滑动底座上设有滑动的滑架车,所述滑架车上设有可打开或关闭的罩体;所述热压罐罐体的上部设有连通热压罐罐体的压力控制阀,所述风机、电加热器、冷却器和压力控制阀均电性连接总控制器。进一步地,所述导风管的上端开口高于隔板或与隔板齐平设置。本发明的优点在于:(1)本发明复合绝缘管的制备方法,先通过热缩工艺制备成复合绝缘管半成品,再将复合绝缘管半成品送至热压容器内进行热压处理,热压处理过程中,先缓慢加热至复合绝缘管半成品呈半熔融状态,再升至高温,避免起始温度过高,破坏复合绝缘管的成分,影响最终产品的质量,通过本发明工艺,可以有效避免复合绝缘管各层之间气泡的产生,进而大大提高复合绝缘管的电性能;(2)本发明复合绝缘管的制备方法,其中,热压容器为确保热压容器有效空间内的温度均匀度,在热压罐罐体内部四周增加导风管,通过导风管将隔板上部的热空气吸入导风管,再由四周的导风管从四周向罩体吹出,进而满足温度均匀度要求。附图说明下面结合附图和具体实施方式对本发明作进一步详细的说明。图1为本发明复合绝缘管的结构示意图。图2为本发明复合绝缘管的制备方法中热压容器的结构示意图。图3为图2中隔板的具体结构示意图。具体实施方式下面的实施例可以使本专业的技术人员更全面地理解本发明,但并不因此将本发明限制在所述的实施例范围之中。实施例本实施例复合绝缘管的制备方法,以110kv的变压器套管为例,如图1所示,具体包括如下步骤:步骤1:在管径为72mm的内导体21上热缩包覆一层长度与内导体21长度一致的管壁厚为0.5mm的半导电热缩管22。步骤2:在上一步骤形成的半导电热缩管22上热缩包覆两层长度与内导体长度一致的绝缘热缩管23,且保证两层绝缘热缩管23的总管壁厚度达4mm。步骤3:在上一步骤形成的最外层绝缘热缩管23上热缩包覆一层长度与绝缘热缩管23长度存在梯差为50mm的管壁厚为0.5mm的半导电热缩管22,且该半导电热缩管22的长度小于绝缘热缩管23的长度。步骤4:在上一步骤形成的半导电热缩管22上热缩包覆两层长度与内导体长度一致的绝缘热缩管23,且保证两层绝缘热缩管23的总管壁厚度达4mm。步骤5:在上一步骤形成的最外层绝缘热缩管23上热缩包覆一层长度与上层半导电热缩管长度存在梯差为50mm的半导电热缩管22,且该半导电热缩管22的长度小于上层半导电热缩管22的长度。步骤6:根据客户要求的产品规格,重复步骤4和步骤5两次,得到4层半导电热缩管22,最后在最外层的半导电热缩管22上热缩包覆一层长度与内导体长度一致的厚度为4mm的绝缘热缩管,形成复合绝缘管半成品。步骤7:将步骤6制备成的复合绝缘管半成品放入热压容器内,该热压容器如图2所示,包括热压罐罐体1,热压罐罐体1一端设有封闭端2,热压罐罐体1的另一端设有可打开或关闭的罐门15。热压罐罐体1的上部中心设有电动机4,电动机4的出轴处通过联轴器连接有风机5,风机5的出风口处连接有电加热器6,电加热器6上远离风机5一侧连接有冷却器7,在距冷却器7一定距离的下方的热压罐罐体1内壁间设置有隔板3,且在隔板3的四个端角处设有贯穿隔板3且下端与热压罐罐体1底面固定连接的导风管12;导风管12的上端开口,各导风管12的内侧壁上还均匀分布有出风孔13,且导风管12的上端开口低于冷却器7,导风管12的上端开口与隔板3齐平设置。热压罐罐体1的底部设有支撑底座8,热压罐罐体1内底部设有滑动底座9,该滑动底座9设置在导风管12之间;滑动底座9上设有滑动的滑架车10,滑架车10上设有可打开或关闭的罩体11;热压罐罐体1的上部设有连通热压罐罐体1的压力控制阀14,风机5、电加热器6、冷却器7和压力控制阀14均电性连接总控制器16。将需要热压容器成型的复合绝缘管半成品放在罩体11内,固定在滑架车10上,将滑架车10滑动推送进热压罐罐体1内,关闭罐门15,工作人员调节总控制器16,控制风机5、电加热器6、冷却器7和压力控制阀14,依次实现升温、加压、保温和降温过程,具体地,先加热至75-85℃,至复合绝缘管半成品呈半熔融状态,同时导入氮气,并逐渐加压至0.8-1mpa。步骤8:待热压容器内的压力达标后,再将热压容器加热至175-185℃,保温4-6min,最后仍保持0.8-1mpa的压力进行降温,直至降温至室温,制得复合绝缘管成品。对比例本对比例复合绝缘管的制备方法,以110kv的变压器套管为例,具体包括如下步骤:步骤1:绕带:首先,取一管径为72mm的金属管型导体,在导体的一端具有一注脂口,另一端具有一排气口,在导体的表面缠绕数层玻璃纤维布带和半导体适形材料,且玻璃纤维布带和半导体适形材料交错缠绕;步骤2:装套:在缠绕有布带的导体的外侧壁上套装一热缩套管,然后,再对热缩套管与导体之间进行抽真空处理,使得热缩套管紧贴在导体的外侧壁上;步骤3:注脂:在真空度在-90—-100kpa的真空的状态下,从导体上的注脂口处向热缩套管与导体之间的腔体内灌注环氧树脂,直至树脂充满;步骤4:固化:对环氧树脂进行固化处理,在固化的过程中,将热缩套管与导体之间多余的环氧树脂以及气体排出。将实施例和对比例制备成的复合绝缘管成品进行电性能测试,其测试结果见下表:110kv变压器套管对比例实施例局放10pc3pc工频耐压230kv276kv介质损耗0.0070.003雷电冲击550kv660kv由上表可以看出,通过本发明复合绝缘管的制备方法制备出的复合绝缘管电性能优于传统制备方法制备出的复合绝缘管电性能。以上显示和描述了本发明的基本原理和主要特征以及本发明的优点。本行业的技术人员应该了解,本发明不受上述实施例的限制,上述实施例和说明书中描述的只是说明本发明的原理,在不脱离本发明精神和范围的前提下,本发明还会有各种变化和改进,这些变化和改进都落入要求保护的本发明范围内。本发明要求保护范围由所附的权利要求书及其等效物界定。当前第1页1 2 3