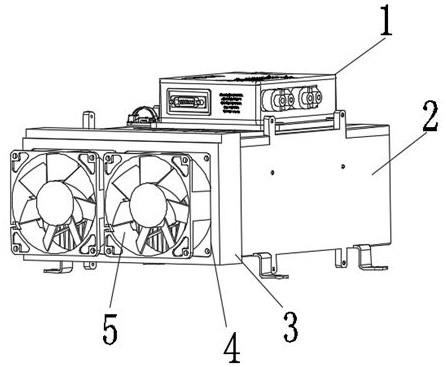
[0001]
本发明属于激光器散热技术领域,具体涉及一种激光器用多层热管散热结构。
背景技术:[0002]
常用的散热方式有水冷、热管、风冷,水冷需要水箱、循环水管、水流驱动,在重量、体积以及成本苛刻的条件下通常不使用,常见于发动机制冷的情况下,这也就是在设备、电子产品中很少见到使用水冷的原因。
[0003]
激光器全负荷工作发热功率175w,热量在尺寸125mm
×
108mm范围内均匀产生。环境温度24
±
2℃,升温值5
±
0.5℃,也就是说,当激光器散热面温度高于31.5℃,会对激光器的工作状况产生不良影响在激光医疗系统中,对散热器的重量、体积都有很高的要求,激光器产生的热量是在125mm
×
108mm的尺寸范围内均匀分布,而散热组件的散热效果是基于热量均匀分布于244mm
×
305mm的尺寸范围内,否则达不到预想的散热效果,造成热量的局部累积,如何使激光器产生的热量从125mm
×
108mm的尺寸范围,快速而相对均匀的分布到244mm
×
305mm的面上是本发明需要解决的问题。
技术实现要素:[0004]
为实现上述目的,本发明提供如下技术方案:一种激光器用多层热管散热结构,包括:激光器,所述激光器通过螺栓连接在散热模组顶部,所述散热模组一侧套接有橡胶连接件,所述橡胶连接件内部通过螺栓固定连接有风机支架,所述风机支架通过螺栓固定连接有风机。
[0005]
为了使得,作为本发明一种优选的,所述散热模组包括散热板,所述散热板顶部横向铣有若干第一凹槽,若干所述第一凹槽内均嵌接有第一热管,所述散热板底部竖向铣有若干第二凹槽,所述散热板还包括鳍片和热管组,所述鳍片表面开设有若干间隔相同的双排连接孔,所述热管组包括第二热管和第三热管,所述第二热管与所述第三热管呈u型,所述第二热管与所述第三热管一侧为圆柱状,一侧为扁平状,所述第二热管和所述第三热管错位设置,若干所述热管组圆柱状与若干所述鳍片上的所述连接孔穿插连接,将若干鳍片与若干热管组穿成一体,若干所述热管组扁平状一侧与鳍片一侧焊接,若干所述热管组扁平状一侧与若干所述第二凹槽嵌接,所述散热板与若干所述鳍片通过金属粉末烧结方式无缝结合,所述侧板与所述底板与所述散热板焊接,所述散热模组与所述激光器通过螺栓连接。
[0006]
为了使得,作为本发明一种优选的,所述散热板顶部铣有的若干第一凹槽深度不得大于0.2mm,所述散热板底部铣有若干所述第二凹槽槽深要铣到所述第一热管外露。
[0007]
为了使得,作为本发明一种优选的,所述第一凹槽尺寸与第一热管尺寸相匹配,所述第二热管与所述第三热管扁平状一侧尺寸与所述第二凹槽尺寸相匹配,所述第二热管与所述第三热管圆柱状一侧尺寸与所述连接孔尺寸相匹配。
[0008]
为了使得,作为本发明一种优选的,所述散热板与所述鳍片材质为铝材质,所述散
热板与所述激光器的接触面光洁度为ra1.6,平整度为0.1mm,所述激光器全负荷工作时发热功率为175w。
[0009]
为了使得,作为本发明一种优选的,所述激光器长度为125mm、宽度为108mm,所述散热板长度为305mm、宽度为244mm、厚度为12.5mm,所述鳍片高度为128.5mm、宽度为5mm,若干所述鳍片24之间间隔为8.28mm。
[0010]
为了使得,作为本发明一种优选的,所述激光器与所述风机均通过外接电源电性连接。
[0011]
与现有技术相比,本发明的有益效果是:1)通过设有的散热模组,热管导热具有方向性的特点,沿着热管走向,导热效果更好且温差小,位于散热板顶部的第一热管负责x方向导热,位于散热板底部第二热管和第三热管负责y方向导热,同时散热板顶部的第一热管与散热板底部的第二热管和第三热管之间通过金属粉末烧结的方式无缝连接,使得第一热管与第二热管、第三热管之间导热达到最佳效果;2)通过散热板顶部嵌接的第一热管紧贴激光器底部散热面,使得热量在散热板的x轴方向上快速而均匀的分布,通过第二热管和第三热管通过金属粉末烧结的方式与第一热管无缝连接,使得热量通过第一热管沿着第二热管和第三热管快速而均匀的分布,通过第一热管、第二热管、第三热管的排列方式,使得激光器产生的热量通过两层热管的作用快速均匀的分布于散热板面上。
[0012]
3)通过鳍片与散热板之间使用金属粉末烧结的方式进行无缝结合,热管组交错穿插在鳍片上的连接孔中,通过第二热管和第三热管之间交错穿插,将若干鳍片连接成一体,使得激光器缠身的热量能够快速且均匀的分布于整个散热模组中,在通过风机的抽风过程,实现散热模组的高效散热。
附图说明
[0013]
附图用来提供对本发明的进一步理解,并且构成说明书的一部分,与本发明的实施例一起用于解释本发明,并不构成对本发明的限制。在附图中:图1为本发明正面的示意图;图2为本发明侧面结构示意图;图3为本发明散热模组结构示意图;图4为本发明的爆炸图;图5为本发明热管组与鳍片的排列方式示意图;图6为本发明热量仿真示意图。
[0014]
图中:1、激光器;2、散热模组;21、散热板;22、第一凹槽;23、第一热管;24、第二凹槽;25、鳍片;26、热管组;261、第二热管;262、第三热管;27、侧板;28、底板;29、连接孔;3、橡胶连接件;4、风机支架;5、风机。
具体实施方式
[0015]
下面将结合本发明实施例中的附图,对本发明实施例中的技术方案进行清楚、完整地描述,显然,所描述的实施例仅仅是本发明一部分实施例,而不是全部的实施例。基于
本发明中的实施例,本领域普通技术人员在没有做出创造性劳动前提下所获得的所有其他实施例,都属于本发明保护的范围。
[0016]
实施例1请参阅图1-6,本发明提供以下技术方案:一种激光器用多层热管散热结构,包括:激光器1,激光器1通过螺栓连接在散热模组2顶部,散热模组2一侧套接有橡胶连接件3,橡胶连接件3内部通过螺栓固定连接有风机支架4,风机支架4通过螺栓固定连接有风机5。
[0017]
本实施例中,散热模组2包括散热板21,散热板21顶部横向铣有若干第一凹槽22,若干第一凹槽22内均嵌接有第一热管23,散热板21底部竖向铣有若干第二凹槽24,散热板21还包括鳍片25和热管组26,鳍片25表面开设有若干间隔相同的双排连接孔29,热管组26包括第二热管261和第三热管262,第二热管261与第三热管262呈u型,第二热管261与第三热管262一侧为圆柱状,一侧为扁平状,第二热管261和第三热管262错位设置,若干热管组26圆柱状与若干鳍片25上的连接孔29穿插连接,将若干鳍片25与若干热管组26穿成一体,若干热管组26扁平状一侧与鳍片25一侧焊接,若干热管组26扁平状一侧与若干第二凹槽24嵌接,散热板21与若干鳍片25通过金属粉末烧结方式无缝结合,侧板27与底板28与散热板21焊接,散热模组2与激光器1通过螺栓连接。
[0018]
具体的,为了使得散热效果达到最好,在散热板21顶部铣有第一凹槽22,将第一热管23使用油压机压入第一凹槽22内,散热板21底部铣有第二凹槽24,热管组26中第二热管261与第三热管262呈u型,第二热管261与第三热管262一侧通过机压成扁平状,同时第二热管261与第三热管262交错穿插在鳍片25的连接孔29中,将若干个鳍片25连接成一体,扁平状一侧的第二热管261和第三热管262与第二凹槽24嵌接,散热板21与若干鳍片25形成的组合体通过金属粉末烧结的方式无缝连接在一起,侧板27和底板28与散热板21焊接在一起,使得整个散热模组2结构更加稳定牢固。
[0019]
本实施例中,散热板21顶部铣有的若干第一凹槽22深度不得大于0.2mm,散热板21底部铣有若干第二凹槽24槽深要铣到第一热管23外露。
[0020]
具体的,首先散热板21顶部铣有深度不大于0.2mm的第一凹槽22,然后通过油压机将第一热管23压入第一凹槽22内,散热板21底部铣有可使得第一热管23外露的第二凹槽24,第二热管261和第三热管262嵌在第二凹槽24内,第二热管261和第三热管262通过金属烧结的方式与第一热管23紧密连接,使得激光器1产生的热量通过第一热管23沿着第二热管261和第三热管262快速均匀的分布。
[0021]
本实施例中,第一凹槽22尺寸与第一热管23尺寸相匹配,第二热管261与第三热管262扁平状一侧尺寸与第二凹槽24尺寸相匹配,第二热管261与第三热管262圆柱状一侧尺寸与连接孔29尺寸相匹配。
[0022]
具体的,第一热管23通过机压成扁平状,散热板21顶部铣有的第一凹槽22与第一热管23尺寸匹配,通过油压机将第一热管23压入第一凹槽22内,使得第一热管23与散热板21之间结合的更加紧固,第二热管261与第三热管262一侧通过机压成扁平状,散热板21底部铣有第二凹槽24,第二凹槽24尺寸与第二热管261、第三热管262扁平状一侧尺寸相匹配,通过金属粉末烧结的方式将第一热管23与第二热管261和第三热管262之间无缝连接在一起,使得第一热管23与第二热管261、第三热管262之间导热效果达到最好,从而实现激光器1产生的热量通过热管均匀的分布在散热板21上。
[0023]
本实施例中,散热板21与鳍片25材质为铝材质,散热板21与激光器1的接触面光洁度为ra1.6,平整度为0.1mm,激光器1全负荷工作时发热功率为175w。
[0024]
具体的,因为铝的导热性更好,所以散热板21和鳍片25都采用铝材质,激光器1全负荷工作时发热功率175w,当环境温度24
±
2℃,升温值5
±
0.5℃,也就是说,激光器1散热面温度不得高于31.5℃,通过热管的分层交错排列,使得激光器1产生的热量可以快速均匀的分布在散热板21面上,通过风机5的抽风,对整个散热模组2进行散热。
[0025]
本实施例中,激光器1长度为125mm、宽度为108mm,散热板21长度为305mm、宽度为244mm、厚度为12.5mm,鳍片25高度为128.5mm、宽度为5mm,若干鳍片25之间间隔为8.28mm。
[0026]
本实施例中,激光器1与风机5均通过外接电源电性连接。
[0027]
具体的,如图6所示,激光器1在全负荷工作时,热量激光器1散热面均匀分布,通过散热模组2中热管组26的排列组合方式和风机5的紧密配合下,将热量快速且均匀的分布到散热板21上,使得激光器1散热面的最高温度不超过31.5℃,从而使得激光器1的工作状态不受到影响。
[0028]
最后应说明的是:以上所述仅为本发明的优选实施例而已,并不用于限制本发明,尽管参照前述实施例对本发明进行了详细的说明,对于本领域的技术人员来说,其依然可以对前述各实施例所记载的技术方案进行修改,或者对其中部分技术特征进行等同替换。凡在本发明的精神和原则之内,所作的任何修改、等同替换、改进等,均应包含在本发明的保护范围之内。