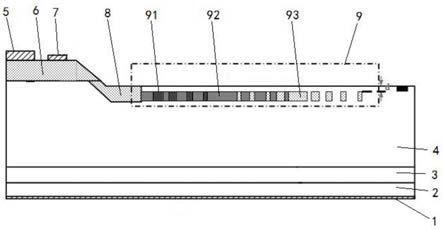
[0001]
本发明属于半导体领域,具体为一种碳化硅器件埋层型终端结构及其制备方法。
背景技术:[0002]
随着电力电子技术的不断发展,功率半导体器件作为核心元器件的地位不断凸显,其广泛应用于电机驱动、新能源发电、智能电网和新能源汽车等。半导体功率器件的耐压性能极其重要,从器件设计的角度上分析,通过优化设计功率半导体器件的终端结构可以充分提高器件的阻断能力。
[0003]
在实际的pn结工艺制造过程中,由于掺杂离子的扩散具有各向同性,杂质离子不仅仅向纵向扩散,而且会在横向扩散。因此在扩散窗口下方形成球面结,其曲率对pn结的击穿特性有很大影响。在器件耐压阶段,随着距离变化的电场强度在结面弯曲处电场更加集中,还未达到理想的耐压时,结面弯曲处的电场就已达到半导体材料的击穿电场。功率半导体器件的终端结构的目的就是缓解元胞边缘的电场强度,使耗尽区向外部扩张,极大的降低主结处的电场集中。目前常用的终端有:场板结构、等间距或变间距场限环结构,场限环结合场板、结终端延伸终端结构等。
[0004]
目前所有的终端结构都会受到终端表面二氧化硅氧化层中固定电荷的影响,由于固定电荷的存在,改变了终端结构中电场的分布,从而使得前期最优化的终端结构的性能大大降低,而且此现象在碳化硅器件上更为严重。因此,亟待需要一种碳化硅器件终端结构及其制备方法,在目前国内工艺能实现的基础上,尽可能充分发挥碳化硅的材料优势,提高器件的耐压性能,并且对表面氧化层电荷的耐受度更高。
技术实现要素:[0005]
本发明的目的是针对以上问题,提供一种碳化硅器件埋层型终端结构及其制备方法,不仅可以避免表面电荷影响,并结合现有的终端结构还可以大大提高终端的性能,同时与现有的制造工艺兼容,减少制作成本。
[0006]
为实现以上目的,本发明采用的技术方案是:一种碳化硅器件埋层型终端结构,包括器件元胞和埋层型终端,所述器件元胞包括:n+ sic衬底;位于所述n+ sic衬底上的p缓冲层;位于所述p缓冲层上的p-漂移区;位于所述p-漂移区上的n基区,在n基区上进行离子注入形成门极区,位于所述n基区上的p+阳极区;所述埋层型终端距离p-漂移区上表面的深度d≧0.3um。
[0007]
进一步的,所述埋层型终端包括台面刻蚀终端延伸结构和离子注入工艺形成的埋层型结终端延伸结构。
[0008]
进一步的,所述埋层型结终端延伸结构距离p-漂移区上表面的深度d≧0.3um。
[0009]
进一步的,所述埋层型结终端延伸结构包括jte1剂量区域和jte2剂量区域,所述jte2剂量区域部分重合在jte1剂量区域上形成埋层型多环调制jte或埋层型三区域jte;所述jte2剂量区域全部重合在jte1剂量区域上形成埋层型场限环jte或埋层型保护环辅助
jte。
[0010]
进一步的,所述台面刻蚀终端延伸结构包括在n基区形成的刻蚀台面和从n基区刻蚀到p-漂移区形成的刻蚀平面。
[0011]
一种碳化硅器件埋层型终端结构的制备方法,(1)清洗碳化硅外延片;(2)在外延片上淀积sio2氧化层,刻蚀形成阳极台面;(3)门极台面刻蚀;(4)门极区域进行离子注入,形成高浓度区域便于形成欧姆接触,随后高温退火处理,激活离子;(5)埋层型终端的制备;i)台面刻蚀,从n基区刻蚀到p-漂移区,最终形成台面刻蚀终端延伸结构(8);ii)对p-漂移区进行第一次离子注入,本次离子区域分成四次不同注入能量和注入剂量,形成均匀分布区域,离子注入深度距上表面的距离d≧0.3um;iii)对p-漂移区进行第二次离子注入,第二次离子注入深度与第一次离子注入深度一致,最终形成埋层型结终端延伸结构,本次离子区域分成四次不同注入能量和注入剂量,形成均匀分布区域,第一次注入剂量是第二次注入剂量的两倍,注入能量一致;iv)退火工艺处理;(6)在外延片上表面进行钝化,形成两层氧化层;(7)刻蚀出阳极接触区,在其表面溅射金属、退火形成p+欧姆接触和n+门极区的欧姆接触;(8)再进行钝化、刻蚀形成接触窗口溅射铝金属;随后在外延片下表面形成阴极欧姆接触。
[0012]
进一步的,步骤3中对门极台面反复刻蚀,并通过探针确定刻蚀深度。
[0013]
进一步的,步骤4在门极区域进行氮离子注入,形成高浓度区域便于形成欧姆接触,随后高温退火激活氮离子。
[0014]
进一步的,所述埋层型结终端延伸结构采用两步离子注入,第一步离子注入剂量为4e12cm-2-1.8e13cm-2
,第二步注入剂量为2e12cm-2-9e12cm-2
,第一步离子注入中四次注入的能量和剂量依次递减,第二步离子注入中四次注入的能量和剂量依次递减。
[0015]
进一步的,第一步离子注入的部分为jte1剂量区域,第二步离子注入为jte2剂量区域,所述jte2剂量区域与jte1剂量区域重合部分形成jte1+jte2剂量交错区域。
[0016]
本发明的有益效果:本发明将现有的通过离子注入方式形成的终端结构,向漂移区下表面推进到一定距离处形成埋层型结构,可以完全避免因漂移区上表面区域内的固定电荷对终端结构的影响,充分发挥终端结构的效果,缓解主结处的电场集中,提高器件的耐压能力。无特殊工艺要求,不会增大工艺的难度,可以很好的提高器件的可靠性和稳定性。
[0017]
附图说明
[0018]
图1为本发明为埋层型多环调制jte的结构示意图;
图2为本发明埋层型多环调制jte的制备流程图图3为本发明埋层型多环调制jte的电场分布图;图4为本发明埋层型多环调制jte的静电势分布图;图5为本发明埋层型多环调制jte在不同sio2/sic界面固定电荷影响下的电场分布图;图6为本发明与传统jte在不同sio2/sic界面固定电荷下的阻断耐压能力示意图;图7为本发明为埋层型三区域jte的结构示意图;图8为本发明为埋层型保护环辅助jte的结构示意图;图9为本发明为埋层型场限环jte的结构示意图。
具体实施方式
[0019]
为了使本领域技术人员更好地理解本发明的技术方案,下面结合附图对本发明进行详细描述,本部分的描述仅是示范性和解释性,不应对本发明的保护范围有任何的限制作用。
[0020]
实施例1如图1所示,一种碳化硅器件埋层型终端结构,包括器件元胞和埋层型终端,器件元胞包括:n+ sic衬底2;位于n+ sic衬底2上的p缓冲层3;位于p缓冲层3上的p-漂移区4;位于p-漂移区4上的n基区6,在n基区6上进行离子注入形成门极区7,位于n基区6上的p+阳极区5;埋层型终端距离p-漂移区4上表面的深度d=0.3um。
[0021]
在本实施例中,埋层型终端包括台面刻蚀终端延伸结构8和离子注入工艺形成的埋层型结终端延伸结构9。其中,台面刻蚀终端延伸结构8包括在n基区形成的刻蚀台面和从n基区刻蚀到p-漂移区形成的刻蚀平面;埋层型结终端延伸结构9距离p-漂移区4上表面的深度d=0.3um。
[0022]
在本实施例中,埋层型结终端延伸结构9包括jte1剂量区域92和jte2剂量区域93,jte2剂量区域93部分重合在jte1剂量区域92上形成埋层型多环调制jte。
[0023]
如图2所示,一种碳化硅器件埋层型终端结构的制备方法,一种碳化硅器件埋层型终端结构的制备方法,(1)清洗碳化硅外延片;(2)在外延片上淀积sio2氧化层,刻蚀形成阳极台面;(3)门极台面刻蚀;(4)门极区域进行离子注入,形成高浓度区域便于形成欧姆接触,随后高温退火处理,激活离子;(5)埋层型终端的制备;i)台面刻蚀,从n基区刻蚀到p-漂移区,最终形成台面刻蚀终端延伸结构8;ii)对p-漂移区进行第一次离子注入,本次离子区域分成四次不同注入能量和注入剂量,形成均匀分布区域,离子注入深度距上表面的距离d=0.3um;iii)对p-漂移区进行第二次离子注入,第二次离子注入深度与第一次离子注入深度一致,最终形成埋层型结终端延伸结构9,本次离子区域分成四次不同注入能量和注入剂量,形成均匀分布区域,第一次注入剂量是第二次注入剂量的两倍,注入能量一致;iv)退火工艺处理;
(6)在外延片上表面进行钝化,形成两层氧化层;(7)刻蚀出阳极接触区,在其表面溅射金属、退火形成p+欧姆接触和n+门极区的欧姆接触;(8)再进行钝化、刻蚀形成接触窗口溅射铝金属;随后在外延片下表面形成阴极欧姆接触。
[0024]
在本实施例中,步骤3中对门极台面反复刻蚀,并通过探针确定刻蚀深度;步骤4在门极区域进行氮离子注入,形成高浓度区域便于形成欧姆接触,随后高温退火激活氮离子。
[0025]
在本实施例中,第一步离子注入的部分为jte1剂量区域92,第二步离子注入为jte2剂量区域93,jte2剂量区域93与jte1剂量区域92重合部分形成jte1+jte2剂量交错区域91,其中,jte1剂量区域92与台面刻蚀终端延伸结构8连接,jte1剂量区域92内穿插设置多个jte1+jte2剂量交错区域91,jte2剂量区域93与jte1剂量区域92连接,形成埋层型多环调制jte。
[0026]
在本实施例中,埋层型多调制环结终端延伸结构采用两步离子注入,第一步离子注入剂量为4e12cm-2
,第二步注入剂量为2e12cm-2
,第一步离子注入中四次注入的能量和剂量依次递减,第二步离子注入中四次注入的能量和剂量依次递减。
[0027]
如图3、图4所示,阻断状态下的静电势分布以及电场分布,随着深度的递增静电势均匀缓慢的下降,在深度为0.3um时电场分布已趋于平缓,最大电场在1.6mv/cm左右,提高了终端的耐压能力,且终端的稳定性和可靠性更高。
[0028]
实施例2一种碳化硅器件埋层型终端结构,包括器件元胞和埋层型终端,器件元胞包括:n+ sic衬底2;位于n+ sic衬底2上的p缓冲层3;位于p缓冲层3上的p-漂移区4;位于p-漂移区4上的n基区6,在n基区6上进行离子注入形成门极区7,位于n基区6上的p+阳极区5;埋层型终端距离p-漂移区4上表面的深度d=0.5um。
[0029]
在本实施例中,埋层型终端包括台面刻蚀终端延伸结构8和离子注入工艺形成的埋层型结终端延伸结构9。其中,台面刻蚀终端延伸结构8包括在n基区形成的刻蚀台面和从n基区刻蚀到p-漂移区形成的刻蚀平面;埋层型结终端延伸结构9距离p-漂移区4上表面的深度d=0.5um。
[0030]
在本实施例中,埋层型结终端延伸结构9包括jte1剂量区域92和jte2剂量区域93,jte2剂量区域93部分重合在jte1剂量区域92上形成埋层型多环调制jte。
[0031]
一种碳化硅器件埋层型终端结构的制备方法,(1)清洗碳化硅外延片;(2)在外延片上淀积sio2氧化层,刻蚀形成阳极台面;(3)门极台面刻蚀;(4)门极区域进行离子注入,形成高浓度区域便于形成欧姆接触,随后高温退火处理,激活离子;(5)埋层型终端的制备;i)台面刻蚀,从n基区刻蚀到p-漂移区,最终形成台面刻蚀终端延伸结构8;ii)对p-漂移区进行第一次离子注入,本次离子区域分成四次不同注入能量和注入剂量,形成均匀分布区域,离子注入深度距上表面的距离d=0.5um;
iii)对p-漂移区进行第二次离子注入,第二次离子注入深度与第一次离子注入深度一致,最终形成埋层型结终端延伸结构9,本次离子区域分成四次不同注入能量和注入剂量,形成均匀分布区域,第一次注入剂量是第二次注入剂量的两倍,注入能量一致;iv)退火工艺处理;(6)在外延片上表面进行钝化,形成两层氧化层;(7)刻蚀出阳极接触区,在其表面溅射金属、退火形成p+欧姆接触和n+门极区的欧姆接触;(8)再进行钝化、刻蚀形成接触窗口溅射铝金属;随后在外延片下表面形成阴极欧姆接触。
[0032]
在本实施例中,步骤3中对门极台面反复刻蚀,并通过探针确定刻蚀深度;步骤4在门极区域进行氮离子注入,形成高浓度区域便于形成欧姆接触,随后高温退火激活氮离子。
[0033]
在本实施例中,第一步离子注入的部分为jte1剂量区域92,第二步离子注入为jte2剂量区域93,jte2剂量区域93与jte1剂量区域92重合部分形成jte1+jte2剂量交错区域91,其中,jte1剂量区域92与台面刻蚀终端延伸结构8连接,jte1剂量区域92内穿插设置多个jte1+jte2剂量交错区域91,jte2剂量区域93与jte1剂量区域92连接,形成埋层型多环调制jte。
[0034]
如图3、图4所示,阻断状态下的静电势分布以及电场分布,随着深度的递增静电势均匀缓慢的下降,在深度为0.3um时电场分布已趋于平缓,在深度为0.5um的情况下,最大电场在1.6mv/cm左右,提高了终端的耐压能力,且终端的稳定性和可靠性更高。
[0035]
实施例3一种碳化硅器件埋层型终端结构,包括器件元胞和埋层型终端,器件元胞包括:n+ sic衬底2;位于n+ sic衬底2上的p缓冲层3;位于p缓冲层3上的p-漂移区4;位于p-漂移区4上的n基区6,在n基区6上进行离子注入形成门极区7,位于n基区6上的p+阳极区5;埋层型终端距离p-漂移区4上表面的深度d=0.8um。
[0036]
在本实施例中,埋层型终端包括台面刻蚀终端延伸结构8和离子注入工艺形成的埋层型结终端延伸结构9。其中,台面刻蚀终端延伸结构8包括在n基区形成的刻蚀台面和从n基区刻蚀到p-漂移区形成的刻蚀平面;埋层型结终端延伸结构9距离p-漂移区4上表面的深度d=0.8um。
[0037]
在本实施例中,埋层型结终端延伸结构9包括jte1剂量区域92和jte2剂量区域93,jte2剂量区域93部分重合在jte1剂量区域92上形成埋层型多环调制jte。
[0038]
一种碳化硅器件埋层型终端结构的制备方法,(1)清洗碳化硅外延片;(2)在外延片上淀积sio2氧化层,刻蚀形成阳极台面;(3)门极台面刻蚀;(4)门极区域进行离子注入,形成高浓度区域便于形成欧姆接触,随后高温退火处理,激活离子;(5)埋层型终端的制备;i)台面刻蚀,从n基区刻蚀到p-漂移区,最终形成台面刻蚀终端延伸结构8;ii)对p-漂移区进行第一次离子注入,本次离子区域分成四次不同注入能量和注入剂
量,形成均匀分布区域,离子注入深度距上表面的距离d=0.8um;iii)对p-漂移区进行第二次离子注入,第二次离子注入深度与第一次离子注入深度一致,最终形成埋层型结终端延伸结构9,本次离子区域分成四次不同注入能量和注入剂量,形成均匀分布区域,第一次注入剂量是第二次注入剂量的两倍,注入能量一致;iv)退火工艺处理;(6)在外延片上表面进行钝化,形成两层氧化层;(7)刻蚀出阳极接触区,在其表面溅射金属、退火形成p+欧姆接触和n+门极区的欧姆接触;(8)再进行钝化、刻蚀形成接触窗口溅射铝金属;随后在外延片下表面形成阴极欧姆接触。
[0039]
在本实施例中,步骤3中对门极台面反复刻蚀,并通过探针确定刻蚀深度;步骤4在门极区域进行氮离子注入,形成高浓度区域便于形成欧姆接触,随后高温退火激活氮离子。
[0040]
在本实施例中,第一步离子注入的部分为jte1剂量区域92,第二步离子注入为jte2剂量区域93,jte2剂量区域93与jte1剂量区域92重合部分形成jte1+jte2剂量交错区域91,其中,jte1剂量区域92与台面刻蚀终端延伸结构8连接,jte1剂量区域92内穿插设置多个jte1+jte2剂量交错区域91,jte2剂量区域93与jte1剂量区域92连接,形成埋层型多环调制jte。
[0041]
如图3、图4所示,阻断状态下的静电势分布以及电场分布,随着深度的递增静电势均匀缓慢的下降,在深度为0.3um时电场分布已趋于平缓,在深度为0.8um的情况下,最大电场在1.6mv/cm左右,提高了终端的耐压能力,且终端的稳定性和可靠性更高。
[0042]
如图5所示,在不同界面固定电荷的情况下,4500v阻断电压时的电场分布,可见采用埋层型终端提高了终端的稳定性,峰值电场均有较大幅度的改善。
[0043]
如图6所示,在不同界面固定电荷密度下的最大击穿电压,随着固定电荷的增多,最大击穿电压逐渐减小,但采用埋层型终端结构对比于传统结构具有很好的稳定性和可靠性。最大击穿电压减小的幅度相对较小且最大击穿电压有明显的提升。
[0044]
实施例4如图7所示,一种碳化硅器件埋层型终端结构,包括器件元胞和埋层型终端,器件元胞包括:n+ sic衬底2;位于n+ sic衬底2上的p缓冲层3;位于p缓冲层3上的p-漂移区4;位于p-漂移区4上的n基区6,在n基区6上进行离子注入形成门极区7,位于n基区6上的p+阳极区5;埋层型终端距离p-漂移区4上表面的深度d=0.6um。
[0045]
在本实施例中,埋层型终端包括台面刻蚀终端延伸结构8和离子注入工艺形成的埋层型结终端延伸结构9。其中,台面刻蚀终端延伸结构8包括在n基区形成的刻蚀台面和从n基区刻蚀到p-漂移区形成的刻蚀平面;埋层型结终端延伸结构9距离p-漂移区4上表面的深度d=0.6um。
[0046]
在本实施例中,埋层型结终端延伸结构9包括jte1剂量区域92和jte2剂量区域93,jte2剂量区域93部分重合在jte1剂量区域92上形成埋层型三区域jte。
[0047]
埋层型三区域jte在制备步骤5中,第一步离子注入的部分为jte1剂量区域92,第二步离子注入为jte2剂量区域93,其中,jte2剂量区域93与jte1剂量区域92叠加部分形成jte1+jte2剂量交错区域91。
[0048]
如图7所示,最终形成结构为:jte1+jte2剂量交错区域91与斜面刻蚀工艺形成的结终端延伸结构8连接,jte1剂量区域92与jte1+jte2剂量交错区域91连接,jte2剂量区域93与jte1剂量区域92连接。
[0049]
如图6所示,在不同界面固定电荷密度下的最大击穿电压,随着固定电荷的增多,最大击穿电压逐渐减小,但采用埋层型终端结构对比于传统结构具有很好的稳定性和可靠性。最大击穿电压减小的幅度相对较小且最大击穿电压有明显的提升。
[0050]
实施例5如图8所示,一种碳化硅器件埋层型终端结构,包括器件元胞和埋层型终端,器件元胞包括:n+ sic衬底2;位于n+ sic衬底2上的p缓冲层3;位于p缓冲层3上的p-漂移区4;位于p-漂移区4上的n基区6,在n基区6上进行离子注入形成门极区7,位于n基区6上的p+阳极区5;埋层型终端距离p-漂移区4上表面的深度d=0.6um。
[0051]
在本实施例中,埋层型终端包括台面刻蚀终端延伸结构8和离子注入工艺形成的埋层型结终端延伸结构9。其中,台面刻蚀终端延伸结构8包括在n基区形成的刻蚀台面和从n基区刻蚀到p-漂移区形成的刻蚀平面;埋层型结终端延伸结构9距离p-漂移区4上表面的深度d=0.6um。
[0052]
在本实施例中,埋层型结终端延伸结构9包括jte1剂量区域92和jte2剂量区域93,jte2剂量区域93全部重合在jte1剂量区域92上形成埋层型保护环辅助jte。
[0053]
埋层型保护环辅助jte在制备步骤5中,第一步离子注入的部分为jte1剂量区域92,第二步离子注入为jte2剂量区域93,其中,jte2剂量区域93全部叠加在jte1剂量区域92上,形成jte1+jte2剂量交错区域91。
[0054]
如图8所示,最终形成结构为:jte1剂量区域92与斜面刻蚀工艺形成的结终端延伸结构8连接,jte1剂量区域92中穿插设置多个jte1+jte2剂量交错区域91。
[0055]
如图6所示,在不同界面固定电荷密度下的最大击穿电压,随着固定电荷的增多,最大击穿电压逐渐减小,但采用埋层型终端结构对比于传统结构具有很好的稳定性和可靠性。最大击穿电压减小的幅度相对较小且最大击穿电压有明显的提升。
[0056]
实施例6如图9所示,一种碳化硅器件埋层型终端结构,包括器件元胞和埋层型终端,器件元胞包括:n+ sic衬底2;位于n+ sic衬底2上的p缓冲层3;位于p缓冲层3上的p-漂移区4;位于p-漂移区4上的n基区6,在n基区6上进行离子注入形成门极区7,位于n基区6上的p+阳极区5;埋层型终端距离p-漂移区4上表面的深度d=0.6um。
[0057]
在本实施例中,埋层型终端包括台面刻蚀终端延伸结构8和离子注入工艺形成的埋层型结终端延伸结构9。其中,台面刻蚀终端延伸结构8包括在n基区形成的刻蚀台面和从n基区刻蚀到p-漂移区形成的刻蚀平面;埋层型结终端延伸结构9距离p-漂移区4上表面的深度d=0.6um。
[0058]
在本实施例中,埋层型结终端延伸结构9包括jte1剂量区域92和jte2剂量区域93,所述jte2剂量区域93全部重合在jte1剂量区域92上形成埋层型场限环jte。
[0059]
埋层型场限环jte在制备步骤5中,第一步离子注入的部分为jte1剂量区域92,第二步离子注入为jte2剂量区域93,其中,jte2剂量区域93全部叠加在jte1剂量区域92上,形成jte1+jte2剂量交错区域91。
[0060]
如图9所示,最终形成结构为:jte1+jte2剂量交错区域91与台面刻蚀终端延伸结构8连接,并且全部为jte1+jte2剂量交错区域91。
[0061]
如图6所示,在不同界面固定电荷密度下的最大击穿电压,随着固定电荷的增多,最大击穿电压逐渐减小,但采用埋层型终端结构对比于传统结构具有很好的稳定性和可靠性。最大击穿电压减小的幅度相对较小且最大击穿电压有明显的提升。
[0062]
需要说明的是,在本文中,术语“包括”、“包含”或者其任何其他变体意在涵盖非排他性的包含,从而使得包括一系列要素的过程、方法、物品或者设备不仅包括那些要素,而且还包括没有明确列出的其他要素,或者是还包括为这种过程、方法、物品或者设备所固有的要素。
[0063]
本文中应用了具体个例对本发明的原理及实施方式进行了阐述,以上实例的说明只是用于帮助理解本发明的方法及其核心思想。以上所述仅是本发明的优选实施方式,应当指出,由于文字表达的有限性,而客观上存在无限的具体结构,对于本技术领域的普通技术人员来说,在不脱离本发明原理的前提下,还可以做出若干改进、润饰或变化,也可以将上述技术特征以适当的方式进行组合;这些改进润饰、变化或组合,或未经改进将发明的构思和技术方案直接应用于其它场合的,均应视为本发明的保护范围。