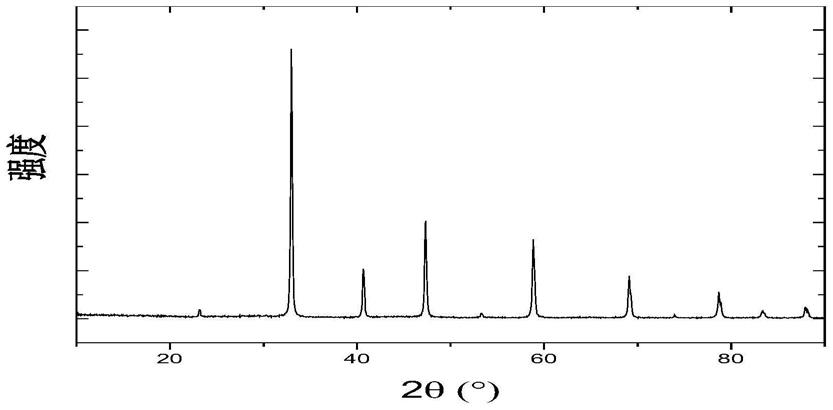
[0001]
本发明涉及二次电池技术领域,具体是一种钙钛矿钒酸盐共混活性材料的电极极片。
背景技术:[0002]
近年来,电动车得到了迅速发展,对锂离子二次电池的要求也越来越高,对高性能锂离子电池负极极片高比容量、快速充电及高功率、使用工作温度范围宽、长的循环寿命和使用年限、突出的安全可靠性的要求日益迫切。
[0003]
目前商用的石墨负极理论容量(372mah/g)无法满足未来400wh/kg的能量密度需求,其极低的工作电压平台0.05~0.1v vs li/li
+
在极端条件下(如低温、大电流快充、过充等)运行时容易产生锂枝晶,安全性能和倍率性能都受到严重限制。而目前开发的硅负极材料虽然具有极高的比容量(理论储锂容量4200mah/g),但其导电性差,在脱嵌锂过程中存在严重的体积效应,体积膨胀接近300~400%,当粉末破碎及脱离集流体时,电子和离子传输就会阻断,循环稳定性在数次循环内就会发生明显衰退,不能满足汽车对数千次循环稳定性的需求。石墨和硅基材料的上述缺陷限制了未来开发高性能二次电池的应用。
[0004]
相比之下,钙钛矿结构的钒酸盐自身具有高电导率(~104s/cm)、高容量及安全且较低的工作电压(0.1~1v vs li/li+),锂离子扩散系数达到~10-8
s/cm,因而具有优异的倍率性能。钒酸盐在嵌入~2个锂离子(~380mah/g比容量)时,体积膨胀系数仅有~2%,低于石墨的~12%,因而具有超长的循环稳定性(>6000次),是一种潜在的商用二次离子电池负极活性材料。钙钛矿结构的碱土钒酸盐作为二次电池负极材料活性物质时,v元素具有多个价态(2
+
、3
+
、4
+
、5
+
价),可以实现多个电子的得失,作为氧化还原活性位点可以贡献高容量。由于v-o键结合能力强,锂离子嵌入时不会将v还原成0价,进而可以保持结构的稳定性。另外,在钙钛矿结构中,[vo6]八面体自身作为刚性结构模型,离子在嵌入时可以保持钙钛矿结构的稳定性,3d的八面体间隙通道又为离子的快速传输提供了3d通道,从而使电极材料具有更高的稳定性和倍率。同时,由于碱土钒酸盐自身具有极高电导率,在实际应用时即使不添加导电剂也可以依靠自身构建起高导电网络框架,从而保证了极片电子和离子传输的同时,尽可能的提高其体积能量密度和质量能量密度。另外,在钙钛矿碱土钒酸盐对碱土金属的空位浓度有很高的容忍度而保持结构稳定性,而碱土金属的空位结构提供了更多的赝电容活性位点,缩短离子的扩散路径,进一步提高比容量和倍率性能。
[0005]
在现有的使用混合材料作为活性物质报道中,如us 3981748使用的ag2cro4和ag3po4混合正极、us 7811707使用的钴酸锂和锰尖晶石共混电极等,通过不同活性物质之间有一定的比容量的协同效应,通过优化成分,可以得到性能更好的电极;但是目前均没有关于钙钛矿结构碱土钒酸盐在电池负极成型材料的相关报道。
技术实现要素:[0006]
本发明的目的在于克服现有技术的不足,提供一种钙钛矿钒酸盐共混活性材料的
电极极片,以至少达到高安全性和高电化学性能的目的。
[0007]
本发明的目的是通过以下技术方案来实现的:
[0008]
一种钙钛矿钒酸盐共混活性材料的电极极片,所述的电极极片包括金属集流体以及涂敷在金属集流体上的负极膜片;所述的负极膜片包括钙钛矿结构碱土钒酸盐活性物质avo3(a=ca,sr,ba)与碳基材料和/或硅基材料共混组成的活性材料。
[0009]
优选的,为了进一步实现高电化学性能的目的,所述的钙钛矿结构碱土钒酸盐活性物质avo3(a=ca,sr,ba)包括标准计量比的钙钛矿结构碱土钒酸盐avo3(a=ca,sr,ba)和非化学计量比x的钙钛矿结构碱土钒酸盐a
x
vo3(a=ca,sr,ba);所述的钙钛矿结构碱土钒酸盐活性物质axvo3(a=ca,sr,ba)包括晶体结构、非晶结构和非晶体以及晶体共存的结构;所述的非化学计量比x=0.3~1.2;通过限定非化学计量比x的取值范围,使非化学计量比x的钙钛矿结构碱土钒酸盐a
x
vo3(a=ca,sr,ba)能够在取值范围内,形成更稳定的结构,同时限定其结构存在形式,从而使制备出的钒酸盐结构稳定,进而间接的提高电化学性能。
[0010]
优选的,为了进一步实现高电学性能的目的,所述的碳基材料选用石墨、硬碳和软碳中的一种及以上,对应的所述的硅基材料选用纳米硅和微米硅、非晶硅和晶体硅、硅碳复合材料中的一种及以上;所述的活性材料包括质量份数为,钙钛矿结构碱土钒酸盐活性物质avo3(a=ca,sr,ba):共混的碳基材料和/或硅基材料=1~99:99~1;通过采用碳基和硅基材料以及两者的混合材料,从而通过控制掺杂的材料组分,控制整体的电极片的比容量、倍率以及导电性能,实现高电化学性能的目的。
[0011]
优选的,为了进一步实现高安全性的目的,所述的负极膜片包括活性材料、导电添加剂以及粘结剂;所述的负极膜片中各组份的质量份数为活性材料:导电添加剂:粘结剂=70~99:0~20:1~10;通过设置不同参数的活性材料、导电添加剂以及粘结剂,从而控制电极片的负极膜片中的各物质的量,防止出现类似锂枝晶的物质生成,从而实现高安全性的目的。
[0012]
优选的,所述的负极膜片的制备方法包括以下步骤:
[0013]
s1将碱土钒酸盐avo3(a=ca,sr,ba)加入到碳基材料和/或硅基材料共混的共混材料中,形成混合活性材料;
[0014]
s2将混合活性材料与导电添加剂、粘结剂按照比例混合均匀,加入溶剂,打浆,得到混合浆料;
[0015]
s3将制备的混合浆料涂布到集流体上,真空下烘干,得到所述的负极膜片。
[0016]
其中,所述的s2中,导电添加剂选自碳材料或mxene导电剂中的至少一种;所述的碳材料包括乙炔黑、科琴黑、super p、碳纳米管、石墨烯中的一种;
[0017]
所述的s2中,粘结剂为水性粘结剂或油性粘结剂;所述的水性粘结剂包括丁苯橡胶、水系丙烯酸树脂、羧甲基纤维素中的至少一种,并以超纯水作为溶剂;
[0018]
所述的油性粘结剂选自聚偏氟乙烯、乙烯-醋酸乙烯酯共聚物、聚乙烯醇中的至少一种,并以n-甲基吡咯烷酮作为有机溶剂。
[0019]
所述的混合活性材料、导电添加剂以及粘结剂按照质量比为70~99:0~20:1~10设置;
[0020]
所述的集流体采用铜箔;所述的真空干燥的温度为80~130℃。
[0021]
本发明的有益效果是:采用钙钛矿结构的钒酸盐avo3(a=ca,sr,ba)与碳基材料
如石墨、硬碳及硅基材料互混作为活性物质,而使用这种活性物质构建电池负极时,电化学性能优异:如与石墨互混时可以提高比容量、倍率、安全性;而与硅基材料互混时可以构建电子网络框架,减少导电炭黑的使用,同时保持高容量和倍率性能,具有极大的商业化潜力。此外,本发明中制备方法工艺简单,成本低廉且绿色环保,适于工业化推广。
附图说明
[0022]
图1为本发明的实施例1的钙钛矿钒酸锶srvo3的x射线衍射光谱图(xrd图);
[0023]
图2为本发明的实施例1的钙钛矿钒酸锶srvo3的扫描电镜图(sem图);
[0024]
图3为本发明的实施例1的石墨的扫描电镜图(sem图);
[0025]
图4为本发明的实施例1的钙钛矿钒酸锶srvo3的电极材料在0.01~3v电位区间内使用未添加导电添加剂的锂离子电池的电压容量图;
[0026]
图5为本发明的实施例1中商用石墨电极片的电化学性能图;
[0027]
图6为本发明的实施例1中,石墨与钙钛矿钒酸锶srvo3按照1:99共混后的电极材料的电化学性能图;
[0028]
图7为本发明的实施例2中,石墨与钙钛矿钒酸锶srvo3按照50:50共混后的电极材料的电化学性能图;
[0029]
图8为本发明的实施例3中,石墨与钙钛矿钒酸锶srvo3按照99:1共混后的电极材料的电化学性能图;
[0030]
图9为本发明的实施例4的钙钛矿钒酸钙cavo3的x射线衍射光谱图;
[0031]
图10为本发明的实施例4的钙钛矿钒酸钙cavo3的扫描电镜图;
[0032]
图11为本发明的实施例4的钙钛矿钒酸钙cavo3的电极材料的电化学性能图;
[0033]
图12为本发明的实施例4中石墨与钙钛矿钒酸钙cavo3按照1:99共混后的电极材料的电化学性能图;
[0034]
图13为本发明的实施例5中,,石墨与钙钛矿钒酸钙cavo3按照50:50共混后的电极材料的电化学性能图;
[0035]
图14为本发明的实施例6中,石墨与钙钛矿钒酸钙cavo3按照99:1共混后的电极材料的电化学性能图;
[0036]
图15为本发明的实施例7的钙钛矿钒酸钡bavo3的x射线衍射光谱图;
[0037]
图16为本发明的实施例7的钙钛矿钒酸钡bavo3的扫描电镜图;
[0038]
图17为本发明的实施例7的钙钛矿钒酸钡bavo3的电极材料的电化学性能图;
[0039]
图18为本发明的实施例7中,石墨与钙钛矿钒酸钡bavo3按照50:50共混后的电极材料的电化学性能图;
[0040]
图19为本发明的实施例8中,硬碳与钙钛矿钒酸锶srvo3按照50:50共混后的电极材料的电化学性能图;
[0041]
图20为本发明的实施例8中商用硬碳电极片的电化学性能图;
[0042]
图21为本发明的实施例9中,软碳与钙钛矿钒酸锶srvo3按照50:50共混后的电极材料的电化学性能图;
[0043]
图22为本发明的实施例10的非化学计量比晶体的钙钛矿钒酸锶sr
0.3
vo3的x射线衍射光谱图;
[0044]
图23为本发明的实施例10的非化学计量比晶体的钙钛矿钒酸锶sr
0.3
vo3的扫描电镜图;
[0045]
图24为本发明的实施例10中,非化学计量比晶体的钙钛矿钒酸锶sr
0.3
vo3与石墨按照99:1共混后的电极材料在0.01~3v电位区间内的电池容量图;
[0046]
图25为本发明的实施例11的非化学计量比晶体的钙钛矿钒酸锶sr
1.2
vo3和杂质sr3v2o3的x射线衍射光谱图;
[0047]
图26为本发明的实施例11的非化学计量比晶体的钙钛矿钒酸锶sr
1.2
vo3和杂质sr3v2o3的扫描电镜图;
[0048]
图27为本发明的实施例11的非化学计量比晶体的钙钛矿钒酸锶sr
1.2
vo3和杂质sr3v2o3的电极材料在0.01~3v电位区间内的锂离子电池的电压容量图;
[0049]
图28为本发明的实施例11中,非化学计量比晶体的钙钛矿钒酸锶sr
1.2
vo3和石墨按照50:50共混后的电极材料在0.01~3v电位区间内的锂离子电池的容量图;
[0050]
图29为本发明的实施例12的非化学计量比非晶体的钙钛矿钒酸锶sr
0.3
vo3的x射线衍射光谱图;
[0051]
图30为本发明的实施例12的非化学计量比非晶体的钙钛矿钒酸锶sr
0.3
vo3的扫描电镜图;
[0052]
图31为本发明的实施例12中,非化学计量比非晶体的钙钛矿钒酸锶sr
0.3
vo3与石墨按照50:50共混后的电极材料在0.01~3v电位区间内的电池容量图;
[0053]
图32为本发明的实施例13的非化学计量比钙钛矿钒酸锶sr
0.3
vo3的非晶体与晶体复合结构的x射线衍射光谱图;
[0054]
图33为本发明的实施例13的非化学计量比钙钛矿钒酸锶sr
0.3
vo3的非晶体与晶体复合结构的扫描电镜图;
[0055]
图34为本发明的实施例13中,非化学计量比钙钛矿钒酸锶sr
0.3
vo3的非晶体与晶体复合结构与石墨按照90:10共混后的电极材料在0.01~3v电位区间内的电池容量图;
[0056]
图35为本发明的实施例14中的硅基材料sio与钙钛矿钒酸锶srvo3按照1:99共混后的电极材料的电化学性能图;
[0057]
图36为本发明的实施例14中的硅基材料sio与钙钛矿钒酸锶srvo3按照1:99
[0058]
共混后的电极材料的循环稳定性图;
[0059]
图37为本发明的实施例15中的硅基材料sio与钙钛矿钒酸锶srvo3按照50:50共混后的电极材料的电化学性能图;
[0060]
图38为本发明的实施例16中的硅基材料sio与钙钛矿钒酸锶srvo3按照99:1共混后的电极材料的电化学性能图
[0061]
图39为本发明的实施例17中硅基材料si与钙钛矿钒酸锶srvo3按照1:99共混后的电极材料的电化学性能图;
[0062]
图40为本发明的实施例17中硅基材料si与钙钛矿钒酸锶srvo3按照1:99共混后的电极材料的循环稳定性能图;
[0063]
图41为本发明的实施例18中,石墨与钙钛矿钒酸锶srvo3按照50:50共混后,再使用20wt%的导电炭黑的电极材料的电化学性能图;
具体实施方式
[0064]
下面结合附图进一步详细描述本发明的技术方案,但本发明的保护范围不局限于以下所述。
[0065]
实施例1
[0066]
采用钙钛矿碱土钒酸锶srvo3与石墨按照99:1比例共混后的电极材料,其中钙钛矿碱土钒酸锶srvo3的物相如图1所示,其xrd图显示为单一物相没有其他杂质,而且其形貌如图2所示,为片状并由纳米颗粒组成;所述的石墨的形貌如图3所示,其表现出片层堆积的形貌。
[0067]
所述的负极膜片的制备步骤具体如下:
[0068]
s1称取9.9g的钒酸锶srvo3与0.1g的石墨,形成混合活性材料;
[0069]
s2将混合活性材料加入到作为有机溶剂的50ml的n-甲基吡咯烷酮有机溶液中,再加入0.1g的pvdf作为粘结剂,使用球磨仪在300r/min的速率下混合5h,得到混合浆料;
[0070]
s3将混合浆料取出使用刮刀涂覆在铜箔上,通过调节刮刀的厚度获得不同面载量的电极片,然后在80℃的温度下烘干24h,即获得所述的负极膜片。
[0071]
将得到的负极膜片按照面载量为2.22mg/cm2裁剪成12mm直径的圆片,随后进行电极片的电化学性能测试:采用半电池2032扣电进行测试,使用金属li作为对电极,使用celgard微膜作为隔膜,使用体积份数之比为ec:dec=50:50与1质量%的lipf6电解液;而半电池电化学性能测试采用0.01~3v的电压测试范围,测试模式采用恒流充放电模式,电流密度依次采用0.2a/g、0.5a/g和1a/g的电流密度。
[0072]
如图4所示,在未添加导电添加剂时,钒酸锶srvo3的电极材料的电极比容量为400mah/g,高于图5所示的商用石墨的实际容量350mah/g;并且其平均工作电压为0.8v,明显高于石墨的0.08v的平均工作电压,因此本发明的实施例1的电极材料在充电时更加安全。
[0073]
如图6所示,石墨与钒酸锶srvo3共混后的电极材料,在电流密度为0.2a/g,倍率为0.1c时,比容量达到409mah/g,远高于石墨的实际容量349mah/g,并且其在0.5c(0.2a/g)、1c(1a/g)、10c(2a/g)的倍率下能保持353mah/g、295mah/g、264mah/g的高容量,证明了其倍率性能优异;同时采用该电极材料的电池,其平均充电电压提高至0.64v,高于石墨的0.05~0.1v,相比之下更加安全。即证明了本发明制备出的电极材料具有优异的高比容量、倍率、安全性的高电化学性能的特征。
[0074]
实施例2
[0075]
采用钙钛矿碱土钒酸锶srvo3与石墨按照50:50比例共混后的电极材料,其负极膜片的制备包括以下步骤:
[0076]
s1称取4.95g的钒酸锶srvo3与4.95g的石墨,形成混合活性材料;其余步骤同实施例1;
[0077]
将得到的负极膜片按照面载量为2.40mg/cm2裁剪成12mm直径的圆片,随后进行同实施例1的电极片的电化学性能测试。
[0078]
如图7所示,在未添加导电添加剂时,石墨与钙钛矿钒酸锶srvo3共混后的电极材料,在电流密度为0.2a/g,倍率为0.1c时,比容量达到392mah/g,高于如图5所示的商用石墨的实际容量350mah/g;并且其在1c、5c、10c的倍率下能保持305mah/g、265mah/g、196mah/g
的高容量,证明了其倍率性能优异;同时采用该电极材料的电池,其平均充电电压提高至0.27v,高于石墨的0.08v,相比之下更加安全。即证明了本发明制备出的电极材料具有优异的高比容量、倍率、安全性的高电化学性能的特征。
[0079]
实施例3
[0080]
采用钙钛矿碱土钒酸锶srvo3与石墨按照1:99比例共混后的电极材料,其负极膜片的制备包括以下步骤:
[0081]
s1称取0.1的钒酸锶srvo3与9.9g的石墨,形成混合活性材料;其余步骤同实施例1;
[0082]
将得到的负极膜片按照面载量为2.49mg/cm2裁剪成12mm直径的圆片,随后进行同实施例1的电机片的电化学性能测试。
[0083]
如图8所示,在未添加导电添加剂时,石墨与钙钛矿钒酸锶srvo3共混后的电极材料,在电流密度为0.2a/g,倍率为0.1c时,比容量达到361mah/g,高于如图5所示的商用石墨的实际容量350mah/g,并增加了11mah/g的比容量;并且其在0.5c、1c、2c的倍率下能保持301mah/g、227mah/g、146mah/g的高容量,证明了其倍率性能优异;同时采用该电极材料的电池,其平均充电电压提高至0.15v,高于石墨的0.08v,相比之下更加安全。即证明了本发明制备出的电极材料具有优异的高比容量、倍率、安全性的高电化学性能的特征。
[0084]
与实施例1和2对比,在实施例3中虽然钒酸锶srvo3的比例进一步降低(石墨质量比进一步增加),共混电极的倍率性能接近纯石墨的性能,但其倍率性能相比纯石墨还有有一定程度的提高,安全性能也有一定的提升,说明混合极片比石墨单一极片表现出更优的比容量、安全性和倍率性能。
[0085]
实施例4
[0086]
采用钙钛矿碱土钒酸钙cavo3与石墨按照99:1比例共混后的电极材料,其中钙钛矿碱土钒酸钙cavo3的物相如图9所示,其xrd图显示为单一物相没有其他杂质,而且其形貌如图10所示,为片状并由纳米颗粒组成;所述的石墨的形貌如图3所示,其表现出片层堆积的形貌。
[0087]
所述的负极膜片的制备步骤具体如下:
[0088]
s1称取9.9g的钒酸钙cavo3与0.1g的石墨,形成混合活性材料;其余步骤同实施例1;
[0089]
将得到的负极膜片按照面载量为2.17mg/cm2裁剪成12mm直径的圆片,随后进行同实施例1的电机片的电化学性能测试。
[0090]
如图11所示,在未添加导电添加剂时,钒酸钙cavo3的比容量为420mah/g,平均工作电压0.92v。
[0091]
如图12所示,石墨与钙钛矿钒酸钙cavo3共混后的电极材料,在电流密度为0.2a/g,倍率为0.1c时,比容量达到378mah/g,高于如图5所示的商用石墨的实际容量349mah/g,并且其在0.2c、1c的倍率下能保持348mah/g、292mah/g的高容量,证明了其倍率性能优异;同时采用该电极材料的电池,其平均充电电压提高至0.71v,高于石墨的0.05~0.1v,相比之下更加安全。即证明了本发明制备出的电极材料具有优异的高比容量、倍率、安全性的高电化学性能的特征。
[0092]
实施例5
[0093]
采用钙钛矿碱土钒酸钙cavo3与石墨按照50:50比例共混后的电极材料,其负极膜片的制备步骤具体如下:
[0094]
s1称取4.95g的钒酸钙cavo3与4.95g的石墨,形成混合活性材料;其余步骤同实施例1;
[0095]
将得到的负极膜片按照面载量为2.17mg/cm2裁剪成12mm直径的圆片,随后进行同实施例1的电机片的电化学性能测试。
[0096]
如图13所示,在未添加导电添加剂时,石墨与钙钛矿钒酸钙cavo3共混后的电极材料,在电流密度为0.2a/g,倍率为0.1c时,比容量达到372mah/g,高于如图5所示的商用石墨的实际容量350mah/g,并且其在1c、5c的倍率下能保持311mah/g、267mah/g的高容量,证明了其倍率性能优异;同时采用该电极材料的电池,其平均充电电压提高至0.28v,高于石墨的0.08v,相比之下更加安全。即证明了本发明制备出的电极材料具有优异的高比容量、倍率、安全性的高电化学性能的特征。
[0097]
实施例6
[0098]
采用钙钛矿碱土钒酸钙cavo3与石墨按照1:99比例共混后的电极材料,其负极膜片的制备步骤具体如下:
[0099]
s1称取0.1g的钒酸钙cavo3与9.9g的石墨,形成混合活性材料;其余步骤同实施例1;
[0100]
将得到的负极膜片按照面载量为2.83mg/cm2裁剪成12mm直径的圆片,随后进行同实施例1的电机片的电化学性能测试。
[0101]
如图14所示,在未添加导电添加剂时,石墨与钙钛矿钒酸钙cavo3共混后的电极材料,在电流密度为0.2a/g,倍率为0.1c时,比容量达到355mah/g,比图5所示的商用石墨的实际容量350mah/g增加了5mah/g;并且其在0.5c、2c、10c的倍率下能保持295mah/g、210mah/g、130mah/g的高容量,证明了其倍率性能优异;同时采用该电极材料的电池,其平均充电电压提高至0.11v,高于石墨的0.08v,相比之下更加安全。即证明了本发明制备出的电极材料具有优异的高比容量、倍率、安全性的高电化学性能的特征。
[0102]
实施例7
[0103]
采用钙钛矿碱土钒酸钡bavo3与石墨按照50:50比例共混后的电极材料,其中钙钛矿碱土钒酸钡bavo3的物相如图15所示,其xrd图显示为单一物相没有其他杂质,而且其形貌如图16所示,为微米颗粒组成;所述的石墨的形貌如图10所示,其表现出片层堆积的形貌。
[0104]
所述的负极膜片的制备步骤具体如下:
[0105]
s1称取4.95g的钒酸钡bavo3与4.95g的石墨,形成混合活性材料;其余步骤同实施例1;
[0106]
将得到的负极膜片按照面载量为1.95mg/cm2裁剪成12mm直径的圆片,随后进行同实施例1的电机片的电化学性能测试。
[0107]
如图17所示,在未添加导电添加剂时,钒酸钡bavo3的比容量低于石墨的容量350mah/g,但其较高的平均工作电压还是有助于在与石墨共混时提高其安全性能。
[0108]
如图18所示,石墨与钙钛矿钒酸钡bavo3共混后的电极材料,在电流密度为0.2a/g,倍率为0.1c时,比容量达到321mah/g,略低于图5所示的商用石墨的实际比容量350mah/
g;但是采用该电极材料的电池,其平均充电电压提高至0.54v,高于石墨的0.08v,相比之下更加安全。即证明了本发明制备出的电极材料具有优异的安全性的高电化学性能的特征。
[0109]
实施例8
[0110]
采用钙钛矿碱土钒酸锶srvo3与硬碳按照50:50比例共混后的电极材料,其负极膜片的制备包括以下步骤:
[0111]
s1称取4.95g的钒酸锶srvo3与4.95g的硬碳,形成混合活性材料;其余步骤同实施例1;
[0112]
将得到的负极膜片按照面载量为2.35mg/cm2裁剪成12mm直径的圆片,随后进行同实施例1的电机片的电化学性能测试。
[0113]
如图19所示,在未添加导电添加剂时,硬碳与钙钛矿钒酸锶srvo3共混后的电极材料,在电流密度为0.2a/g,倍率为0.1c时,比容量达到460mah/g,高于如图20所示的商用硬碳的实际容量331mah/g;并且其在0.5c、1c、2c的倍率下能保持381mah/g、280mah/g、224mah/g的高容量,证明了其倍率性能优异;同时采用该电极材料的电池,其平均充电电压为0.6v,高于石墨的0.05~0.1v,相比硬碳的0.75v工作电压有略微的降低,具有较高的安全性。即证明了本发明制备出的电极材料具有优异的高比容量、倍率、安全性的高电化学性能的特征。
[0114]
实施例9
[0115]
采用钙钛矿碱土钒酸锶srvo3与软碳按照50:50比例共混后的电极材料,其负极膜片的制备包括以下步骤:
[0116]
s1称取4.95g的钒酸锶srvo3与4.95g的软碳,形成混合活性材料;其余步骤同实施例1;电流密度采用0.1c和
[0117]
如图21所示,在未添加导电添加剂时,硬碳与钙钛矿钒酸锶srvo3共混后的电极材料,在电流密度为0.2a/g,倍率为0.1c时,比容量达到348mah/g;并且其在0.2c、20c的倍率下能保持308mah/g、150mah/g的高容量,满足动力电池高功率和高容量的需求;同时采用该电极材料的电池,其平均充电电压0.75v,相比软碳的0.70v工作电压有略微的降低,高于石墨的0.05~0.1v,相比之下更加安全。即证明了本发明制备出的电极材料具有优异的高比容量、倍率、安全性的高电化学性能的特征。
[0118]
小结:由于软碳与硬碳、石墨均属于c的异构体,以软碳、硬碳或者石墨与钙钛矿结构碱土钒酸锶srvo3共混时,既可以充分发挥碳材料的低电压优势,又可以发挥钙钛矿结构碱土钒酸盐的高容量、高倍率、高安全性的优势,从而得以调控能量密度、功率密度和安全性。与实施例1和8相比,实施例9的软碳在不同的倍率下具有更高的容量,这是由于其具有更多的缺陷和更大的比表面积所引起的。
[0119]
因此整体上,碳材料与钙钛矿结构碱土钒酸盐共混使用时,电极的容量与二者的质量比及容量呈现相关性,通过更换不同的碳材料同样可以获得更优电化学性能的混合电极。
[0120]
实施例10
[0121]
采用非化学计量数x=0.3的晶体结构sr
0.3
vo3与石墨按照99:1共混的电极材料,其中非化学计量数比的钙钛矿碱土钒酸锶sr
0.3
vo3的物相如图22所示,其xrd图显示为单一物相没有其他杂质,而且其形貌如图23所示,为片状并由纳米颗粒组成;所述的石墨的形貌
如图3所示,其表现出片层堆积的形貌。
[0122]
所述的负极膜片的制备包括以下步骤:
[0123]
s1称取9.9g的非化学计量比晶体结构的酸锶sr
0.3
vo3与0.1g的石墨,形成混合活性材料;其余步骤同实施例1;
[0124]
将得到的负极膜片按照面载量为2.01mg/cm2裁剪成12mm直径的圆片,随后进行同实施例1的电极片的电化学性能测试。
[0125]
如图24所示,在未添加导电添加剂时,石墨与非化学计量数比晶体结构的钙钛矿钒酸锶sr
0.3
vo3共混后的电极材料,在电流密度为0.1a/g,倍率为0.1c时,比容量达到449mah/g,高于如图5所示的商用石墨的实际容量350mah/g;并且其在0.1c、0.2c的倍率下能保持387mah/g、322mah/g的高容量,证明了其倍率性能优异;同时采用该电极材料的电池,其平均充电电压提高至0.54v,高于石墨的0.08v,相比之下更加安全。即证明了本发明制备出的电极材料具有优异的高比容量、倍率、安全性的高电化学性能的特征。
[0126]
实施例11
[0127]
采用非化学计量数x=1.2的晶体结构sr
1.2
vo3与石墨按照99:1共混的电极材料,其中非化学计量数比的钙钛矿碱土钒酸锶sr
1.2
vo3的物相如图25所示,其xrd图显示为含有少量的sr3v2o8杂质相,而且杂质相形貌如图26所示,为片状并由纳米颗粒组成;
[0128]
所述的负极膜片的制备包括以下步骤:
[0129]
s1称取9.9g的非化学计量比晶体结构的酸锶sr
1.2
vo3与0.1g的石墨,形成混合活性材料;其余步骤同实施例1;
[0130]
将得到的负极膜片按照面载量为2.01mg/cm2裁剪成12mm直径的圆片,随后进行同实施例1的电机片的电化学性能测试。
[0131]
如图27-28所示,在未添加导电添加剂时,石墨与非化学计量数比晶体结构的钙钛矿钒酸锶sr
1.2
vo3共混后的电极材料,在电流密度为0.1a/g,倍率为0.05c时,比容量达到308mah/g,低于如图5所示的商用石墨的实际容量350mah/g;但其在0.5c、2c和8c的倍率下能保持287mah/g、201mah/g、146mah/g的高容量的高容量,证明了其倍率性能优异;同时采用该电极材料的电池,其平均充电电压提高至0.70v,高于石墨的0.08v,相比之下更加安全。即证明了本发明制备出的电极材料具有优异安全性的高电化学性能的特征。
[0132]
实施例12
[0133]
采用非化学计量数x=0.3的非晶体结构sr
0.3
vo3与石墨按照50:50共混的电极材料;其中非化学计量数比的非晶体结构的钙钛矿碱土钒酸锶sr
1.2
vo3的物相如图29所示,其xrd图显示为单一相,没有其他杂质;而且其形貌如图30所示,为片状并由纳米颗粒组成;
[0134]
所述的负极膜片的制备包括以下步骤:
[0135]
s1称取4.95g的非化学计量比晶体结构的酸锶sr
0.3
vo3与4.95g的石墨,形成混合活性材料;其余步骤同实施例1;
[0136]
将得到的负极膜片按照面载量为2.22mg/cm2裁剪成12mm直径的圆片,随后进行同实施例1的电机片的电化学性能测试。
[0137]
如图31所示,在未添加导电添加剂时,石墨与非化学计量数比晶体结构的钙钛矿钒酸锶sr
0.3
vo3共混后的电极材料,在电流密度为0.1a/g,倍率为0.1c时,比容量达到461mah/g,高于如图5所示的商用石墨的实际容量350mah/g;并且其在0.5c、1c和2c的倍率
下能保持367mah/g、295mah/g、264mah/g的高容量,证明了其倍率性能优异;同时采用该电极材料的电池,其平均充电电压提高至0.64v,高于石墨的0.05~0.1v,相比之下更加安全。即证明了本发明制备出的电极材料具有优异的高比容量、倍率、安全性的高电化学性能的特征。
[0138]
实施例13
[0139]
采用非化学计量数x=0.3的晶体与非晶体复合结构的sr
0.3
vo3与石墨按照99:1共混的电极材料;其中非化学计量数比的晶体与非晶体复合结构的钙钛矿碱土钒酸锶sr
0.3
vo3的物相如图32所示,其xrd图含有晶体相及在30度附近明显的非晶鼓包相,而且形貌如图33所示,为片状并由纳米颗粒组成;
[0140]
所述的负极膜片的制备包括以下步骤:
[0141]
s1称取9.9g的非化学计量比晶体和非晶体复合结构的酸锶sr
0.3
vo3与0.1g的石墨,形成混合活性材料;其余步骤同实施例1;
[0142]
将得到的负极膜片按照面载量为2.22mg/cm2裁剪成12mm直径的圆片,随后进行同实施例1的电机片的电化学性能测试。
[0143]
如图34所示,在未添加导电添加剂时,石墨与非化学计量数比晶体结构的钙钛矿钒酸锶sr
0.3
vo3共混后的电极材料,在电流密度为0.1a/g,倍率为0.1c时,比容量达到451mah/g,高于如图5所示的商用石墨的实际容量350mah/g;并且其在0.5c、2c和5c的倍率下能保持390mah/g、242mah/g、184mah/g的高容量,证明了其倍率性能优异;同时采用该电极材料的电池,其平均充电电压提高至0.47v,高于石墨的0.08v,相比之下更加安全。即证明了本发明制备出的电极材料具有优异的高比容量、倍率、安全性的高电化学性能的特征。
[0144]
实施例14
[0145]
采用钙钛矿碱土钒酸锶srvo3与硅基材料sio按照99:1比例共混后的电极材料,其负极膜片的制备包括以下步骤:
[0146]
s1称取9.9g的钒酸锶srvo3与0.1g的sio,形成混合活性材料;其余步骤同实施例1;
[0147]
将得到的负极膜片按照面载量为2.02mg/cm2裁剪成12mm直径的圆片,随后进行同实施例1的电机片的电化学性能测试。
[0148]
如图35所示,在未添加导电添加剂时,sio与钙钛矿钒酸锶srvo3共混后的电极材料,在电流密度为0.2a/g,倍率为0.1c时,比容量达到491mah/g,高于图6中石墨与钙钛矿钒酸锶srvo3按照1:99共混后的电极材料的实际容量461mah/g,因sio材料自身比石墨具有较高的比容量;并且其在0.5c、1c、2c、5c的倍率下能保持442mah/g、315mah/g、238mah/g、196mah/g的高容量,证明了其倍率性能优异;同时采用该电极材料的电池,其平均充电电压提高至0.56v,高于sio的~0.3v,相比之下更加安全。即证明了本发明制备出的电极材料具有优异的高比容量、倍率、安全性的高电化学性能的特征。
[0149]
如图36所示,在未添加导电剂时,sio与钙钛矿钒酸锶srvo3共混后的电极材料,在10c的倍率下保持良好的循环稳定性,在50次循环内保持196mah/g的容量没有衰退,说明复合电极具有优异的稳定性,说明复合电极比sio电极具有更优的循环稳定性。
[0150]
实施例15
[0151]
采用钙钛矿碱土钒酸锶srvo3与硅基材料sio按照50:50比例共混后的电极材料,
其负极膜片的制备包括以下步骤:
[0152]
s1称取4.95g的钒酸锶srvo3与4.95g的sio,形成混合活性材料;其余步骤同实施例1;
[0153]
将得到的负极膜片按照面载量为2.13mg/cm2裁剪成12mm直径的圆片,随后进行同实施例1的电机片的电化学性能测试。
[0154]
如图37所示,在未添加导电添加剂时,sio与钙钛矿钒酸锶srvo3共混后的电极材料,在电流密度为0.2a/g,倍率为0.1c时,比容量达到660mah/g,高于图35中sio与钙钛矿钒酸锶srvo3按照1:99共混后的电极材料的实际容量490mah/g,说明随着sio含量的增加,样品的比容量可以有效的提高;并且其在0.5c、1c的倍率下能保持307mah/g、120mah/g的高容量,证明了其倍率性能优异;同时采用该电极材料的电池,其平均充电电压提高至0.46v,高于石墨的0.08v及sio的~0.3v,相比之下更加安全。即证明了本发明制备出的电极材料具有优异的高比容量、倍率、安全性的高电化学性能的特征。
[0155]
从上述中可以得出,在不添加导电剂,由于添加的sio含量较多,构建电极时导电框架有一定的降低,混合电极的电导率有一定的降低,高电流密度下无法快速的传输电子,从而使其在高倍率10c下仅保存~14mah/g的低容量。但混合电极在低倍率下0.1c还是保持660mah/g的高容量,对于提高能量密度具有很大的优势。因此商用时,通过增加一定质量比的导电剂1wt%~20wt%,还可以进一步提高其倍率性能。
[0156]
实施例16
[0157]
采用钙钛矿碱土钒酸锶srvo3与硅基材料sio按照1:99比例共混后的电极材料,其负极膜片的制备包括以下步骤:
[0158]
s1称取0.1的钒酸锶srvo3与9.8的sio,形成混合活性材料;其余步骤同实施例1;
[0159]
将得到的负极膜片按照面载量为2.13mg/cm2裁剪成12mm直径的圆片,随后进行同实施例1的电机片的电化学性能测试。
[0160]
如图38所示,在未添加导电添加剂时,sio与钙钛矿钒酸锶srvo3共混后的电极材料,在电流密度为0.2a/g,倍率为0.1c时,比容量达到850mah/g,高于图37中sio与钙钛矿钒酸锶srvo3按照50:50共混后的电极材料的实际容量660mah/g,说明随着sio含量的增加,样品的比容量可以有效的提高;并且其在0.2c、1c、5c的倍率下能保持400mah/g、101mah/g、45mah/g的高容量;可以看出,srvo3在使用量降低至1wt%时,在低倍率sio的增加进一步提高了比容量,srvo3在低倍率下还是可以有效的作为导电剂提供电子网络框架,但在高倍率5c下比容量还是降低至45mah/g的低容量。
[0161]
以上可以看出,随着sio含量的增加,混合电极的在低倍率下的比容量增加明显,但在高倍率下的比容量有明显的降低。这主要是由于sio自身半导体特性和较高的比容量影响。
[0162]
实施例17
[0163]
采用钙钛矿碱土钒酸锶srvo3与硅基材料si按照99:1比例共混后的电极材料,因与与sio相比,si具有更高的比容量,但同时其体积膨胀较大,作为半导体材料,需要一定量的导电剂作为电子传输网络框架。
[0164]
所述的负极膜片的制备包括以下步骤:
[0165]
s1称取9.9g的钒酸锶srvo3与0.1g的si,形成混合活性材料。
[0166]
s2将混合活性材料加入到作为有机溶剂的50ml的n-甲基吡咯烷酮有机溶液中,再加入0.5g的pvdf作为粘结剂;其余同实施例1;
[0167]
将得到的负极膜片按照面载量为1.85mg/cm2裁剪成12mm直径的圆片,随后进行同实施例1的电机片的电化学性能测试。
[0168]
如图39所示,在未添加导电剂时,si与钙钛矿碱土钒酸锶srvo3共混后的电极材料,在电流密度为0.2a/g,倍率为0.1c时,比容量达到600mah/g,高于图14中sio与钙钛矿钒酸锶srvo3按照1:99共混后的电极材料的实际容量491mah/g,也远高于图6中石墨与钙钛矿钒酸锶srvo3按照1:99共混后的电极材料的实际容量421mah/g,说明当使用srvo3与其他材料互混使用时,srvo3不仅可以有效的发挥高比容量的活性物质特点,也可以为其他高比容量的半导体活性物质提供电子网络框架,从而获得更高的比容量;并且,si与钙钛矿碱土钒酸锶srvo3共混后的电极材料在0.2c的倍率下能保持561mah/g的高容量,证明了其倍率性能优异;说明了本发明制备的电极材料兼具高比容量和高倍率特性。
[0169]
同时如图40所示,si与钙钛矿碱土钒酸锶srvo3共混后的电极材料表现出优异的循环稳定性,在50次循环内使用5c的倍率下可以保持稳定,没有容量衰退,说明共混极片具有优异的循环稳定性。即证明了本发明制备出的电极材料具有优异的高比容量、倍率、安全性的高电化学性能的特征。
[0170]
实施例18
[0171]
采用非化学计量数x=0.3的晶体与非晶体复合结构的sr
0.3
vo3与石墨按照50:50共混的电极材料;
[0172]
所述的负极膜片的制备包括以下步骤:
[0173]
s1称取0.35g的非化学计量比晶体和非晶体复合结构的酸锶sr
0.3
vo3与0.35g的石墨,并加入0.2g的导电炭黑,形成混合活性材料;其余步骤同实施例1;
[0174]
将得到的负极膜片按照面载量为1.68mg/cm2裁剪成12mm直径的圆片,随后进行同实施例1的电机片的电化学性能测试。
[0175]
如图41所示,在导电剂质量份数为20%时,石墨与非化学计量数比晶体结构的钙钛矿钒酸锶sr
0.3
vo3共混后的电极材料,在电流密度为0.1a/g,倍率为0.1c时,比容量达到543mah/g,高于如图5所示的商用石墨的实际容量350mah/g,也高于图24中不采用导电剂的非化学计量比晶体的钙钛矿钒酸锶sr
0.3
vo3与石墨按照90:10共混后的电极材料的450mah/g;说明了在添加使用导电剂后,导电剂同时贡献一部分容量,同时构建了更高效的导电框架,因而具有更高的比容量。但导电剂比表面积大,导致极片的厚度大,因而使用质量份数为20%的导电剂会导致体积能量密度下降40%。因而,合理使用导电剂含量,可以进一步优化性能。
[0176]
综上所述,本发明制备的电极材料具有优异的高比容量、倍率、安全性的高电化学性能的特征。
[0177]
以上所述仅是本发明的优选实施方式,应当理解本发明并非局限于本文所披露的形式,不应看作是对其他实施例的排除,而可用于各种其他组合、修改和环境,并能够在本文所述构想范围内,通过上述教导或相关领域的技术或知识进行改动。而本领域人员所进行的改动和变化不脱离本发明的精神和范围,则都应在本发明所附权利要求的保护范围内。