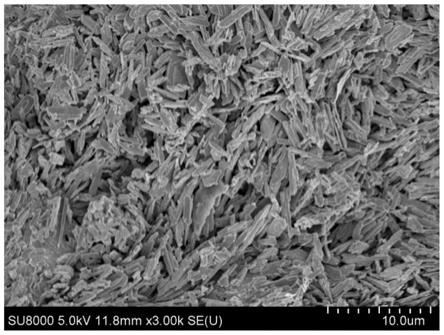
[0001]
本发明涉及铅酸蓄电池技术领域,尤其是涉及一种铅酸蓄电池正极铅膏和制方法。
背景技术:[0002]
阀控式密封铅酸蓄电池是目前的主流铅酸蓄电池产品,基于电池性能与环境友好要求,这类电池一般采用涂膏式极板,正极板栅一般采用铅-钙系合金。通常这类电池的早期失效模式以发生在正极板栅界面的电阻效应(也称为“无锑效应”或pcl-1)和正极活性物质本体软化(pcl-2)最为常见。为了克服“无锑效应”,改善板栅界面与活性物质之间的结合性能,一方面可以在铅-钙合金中添加sn元素,另一方面通常在铅膏中添加sn、sb、bi等元素来改善板栅界面的腐蚀层结构,提高板栅界面腐蚀层的导电性和连接性。正极活性物质在化成前的铅膏一般以三碱式硫酸铅(3bs)为主,3bs为一种约3~5um左右的针状晶体结构,这种结构的铅膏化成后主要形成高容量特性的β-pbo2为主的活性物质结构,但是这种活性物质循环时容易发生软化脱落而导致电池早期失效,循环寿不长。为了抑制活性物质软化,提高活性物质颗粒之间的结合强度,提高循环寿命,通过和膏、固化等工艺获得四碱式硫酸铅(4bs)晶体结构的铅膏是一种有效的措施。4bs晶体呈长棒状,由4bs构成的铅膏内部其棒状晶体交错连接、结构稳定,化成后更容易生成α-pbo2,这种结构的正极活性物质骨架结构机械强度高,循环应用时抗软化能力强。获得4bs铅膏的方法一般采用高温和膏、高温固化等方式。为了更容易获得4bs铅膏,更好的控制4bs晶体的尺寸与形貌,通常在和膏时配方中添加4bs晶种进行诱导引晶。
[0003]
但是通过试验发现,如果在正极铅膏中添加某些特定金属元素(如:sb、bi等)后4bs铅膏难以形成,而这些元素往往又是解决板栅界面效应的有效成分,因此产生了4bs铅膏与克服界面效益不能兼顾的矛盾。为了解决这一矛盾,授权公告号为cn 107331862 b的专利公开了一种利于生成4bs的深循环电池铅膏的和制方法,包括:(1)将铅粉与除三氧化二锑和硫酸亚锡以外的添加剂干混后,加水湿混,再加占总酸量80%以上的硫酸搅拌反应,控制反应温度在65-85℃,获得一次混酸铅膏;(2)将三氧化二锑和硫酸亚锡加入到剩余的硫酸中得到硫酸混合液,再将硫酸混合液混入一次混酸铅膏中进行搅拌反应,降温至小于45℃,获得所述深循环铅膏。又如授权公告号cn 106910872 b的专利公开了一种铅酸蓄电池正极板及其制备方法,所述正极板的铅膏原料包括铅粉、添加剂、水和硫酸,所述添加剂包括三氧化二锑和硫酸亚锡,该发明是先将铅膏的制备分成两部分完成,第一部分的添加剂包含三氧化二锑和硫酸亚锡,控制反应温度不大于50℃,制备出含3bs的第一铅膏,第二部分不包含上述两种添加剂,控制反应温度为80℃-85℃,制备出含4bs的第二铅膏,再进行物理混合,使得正极铅膏中同时含有有效量得3bs和4bs。
[0004]
其不足之处在于,以上方法均可以获得4bs铅膏,但是很难通过和膏条件精确控制4bs的晶体尺寸和含量。cn 106910872 b进行两次和膏,再对两种铅膏进行合并和制,在实际操作上存在一定困难,可操作性差。
技术实现要素:[0005]
本发明是为了克服现有技术的铅膏中4bs的晶体尺寸和含量难以控制及可操作性差的问题,提供一种铅酸蓄电池正极铅膏和制方法,以两次加铅粉的方式进行,在保证铅膏配方效果的情况,能够有效的得到一定量的4bs;采用蒸汽加热搅拌控制温度、和膏机转速和时间保证生成4bs的均匀性和含量;固化阶段节省能耗,可得到更多且均匀的4bs。提升极板的物质强度和电池的循环寿命,延长电池的使用寿命;该方法对现有铅膏的和制工艺变化较少、可操作性强、便于生产实施。
[0006]
为了实现上述目的,本发明采用以下技术方案:一种铅酸蓄电池正极铅膏和制方法,包括以下制备步骤:(1)第一步:将部分铅粉与短纤维、石墨及红丹混合均匀,然后加纯水湿混,再加硫酸进行酸混,形成半悬浮浆料,加酸完毕后通入高温蒸汽对半悬浮浆料进行加热并搅拌,得到浆料a;(2)第二步:将锑的氧化物、铋的氧化物、氧化锌及盐类添加剂加入浆料a中,然后搅拌均匀,得到浆料b;(3)第三步:将剩余的铅粉的以边加边搅拌方式逐步加入浆料b中,得到混合均匀的膏体。
[0007]
本发明采用可以克服锑、锡、锌、铝、铋的单质、氧化物、硫酸盐或碳酸盐影响四碱式硫酸铅形成的缺陷。短纤维的作用就是提高铅膏的连接强度,石墨起导电作用,利于化成,红丹也是利于化成的进行;加入水和酸,并通入热蒸汽加热,可以保证温度在80~100℃时,有利于四碱式硫酸铅的生成,温度较低的话,它会生成3bs晶而非4bs晶;铅膏和制完成后,铅膏温度降至45℃以下出膏,然后安照正常生产工艺进行涂板、固化制备正极板。
[0008]
作为优选,步骤(1)中部分铅粉占总铅粉重量的40-80%,短纤维、石墨及红丹分别占总铅粉重量的0.05-0.2%、0.1-0.5%及1-5%。
[0009]
按总铅粉重量比所述的铅粉量占一锅铅粉总量的40-80%,如果过多会导致加水湿混以后不能形成浆料,影响4bs晶种分散的均匀性和生成的4bs的均匀性;如果过少,会导致生成的4bs量少,后续添加铅粉过多,没必要,不仅会造成原料的浪费,也会阻碍4bs晶的生成。
[0010]
作为优选,步骤(1)中所述纯水占总铅粉重量的13.5-16%,加水时间为20-60s,所述的湿混时间为5-25min。
[0011]
加水量和加水时间都是按照实验得出的最优工艺参数进行的,湿混和酸混时间为4bs的生成的时间。时间过长会导致4bs晶体生长过大,不利于后期电池的化成,导致化成困难,电池容量偏低。
[0012]
加水量的控制:加水量过少,困难铅粉都没完全湿润,加水量过多会导致铅膏太稀,根本不能涂敷在板栅上。加酸量的控制:加酸量过少会导致,成品电池初容量过低,不满足出厂要求,加酸过度会导致电池循环寿命缩短。
[0013]
作为优选,硫酸占总铅粉重量的6-10%,硫酸的密度为1.4-1.6g/cm3,所述酸混时间为15-60min。
[0014]
作为优选,步骤(1)中高温蒸汽的温度为80~100℃,搅拌时间为20-30min。
[0015]
引入高温蒸汽的目的是对铅膏进行加热,4bs晶在80-100度范围内,有利于生成,
所以控制在这个温度范围内,搅拌时间是使4bs晶有生长的时间,搅拌时间过短,4bs晶的生成较小,对电池性能没什么效果,过大也会对电池性能造成不利。
[0016]
作为优选,所述短纤维的长度为2-6mm。
[0017]
作为优选,步骤(2)中锑的氧化物、铋的氧化物及氧化锌的含量分别为占总铅粉重量的0.1-0.5%、0.05%-0.6%及0.08%-0.3%。
[0018]
作为优选,步骤(2)中盐类添加剂占总铅粉重量的0.1-0.6%,所述盐类添加剂选自硫酸锌、碳酸锌及硫酸铝中的一种。
[0019]
作为优选,步骤(2)中搅拌时间为搅拌时间1~5min。
[0020]
作为优选,步骤(3)的加料时间1~5min,全部加完后搅拌2-10min。
[0021]
该步的加料时间和搅拌时间的控制是为了增加4bs晶的分散均匀,以增加最终铅膏的一致性,同时也是为了增加工艺的简单易加工性能。
[0022]
因此,本发明具有如下有益效果:本发明具有的有益效果:(1)本发明的铅膏和制方法,以两次加铅粉的方式进行,将对4bs有抑制作用的锑、锡、锌、铝、铋的单质、氧化物、硫酸盐或碳酸盐等配方在第二次铅粉中加入,既不影响铅膏配方效果,又能有效的得到一定量的4bs;(2)采用蒸汽加热搅拌控制温度、和膏机转速和时间保证生成4bs的均匀性和含量;后续固化阶段采用正常固化,节省固化阶段能源损耗即可得到更多且均匀的4bs,提升极板的物质强度和电池的循环寿命。
[0023]
(3)该方法对现有铅膏的和制工艺变化较少、可操作性强、便于生产实施。
附图说明
[0024]
图1是实施例1加剩余铅粉前的铅膏sem。
[0025]
图2是实施例1加入剩余铅粉以后铅膏的sem图。
[0026]
图3是实施例2加剩余铅粉前的铅膏sem。
[0027]
图4是实施例2加入剩余铅粉以后铅膏的sem图。
[0028]
图5是对比例1最终的铅膏的sem图。
[0029]
图6是实施例1-3及对比例1-2的12v/12ah的试验电池的循环测试数据图(实施例1对应曲线543,实施例2对应曲线544,实施例3对应曲线545,对比例1对应曲线546,对比例2对应曲线547)。
[0030]
图7是对比例3最终铅膏的sem图。
具体实施方式
[0031]
下面结合具体实施方式对本发明做进一步的描述。
[0032]
总实施例一种铅酸蓄电池正极铅膏和制方法,包括以下制备步骤:(1)第一步:将占总铅粉重量40-80%的部分铅粉与占总铅粉重量0.05-0.2%的短纤维(短纤维的长度为2-6mm)、占总铅粉重量0.1-0.5%的石墨及占总铅粉重量1-5%的红丹混合均匀,然后20-60s加占总铅粉重量13.5-16%的纯水,加水后湿混5-25min,再加占总铅粉
重量6-10%的硫酸(硫酸的密度为1.4-1.6g/cm3)进行酸混,酸混时间为15-60min,形成半悬浮浆料,加酸完毕后通入80~100℃的高温蒸汽对半悬浮浆料进行加热并搅拌20-30min,得到浆料a;(2)第二步:将占总铅粉重量0.1-0.5%的锑的氧化物、占总铅粉重量0.05%-0.6%的铋的氧化物、占总铅粉重量0.08%-0.3%的氧化锌及占总铅粉重量0.1-0.6%的盐类添加剂(硫酸锌、碳酸锌及硫酸铝)加入浆料a中,然后搅拌均匀,搅拌时间1~5min,得到浆料b;(3)第三步:将剩余的铅粉的以边加边搅拌方式逐步加入浆料b中,加料时间1~5min,全部加完后搅拌2-10min,得到混合均匀的膏体。
[0033]
实施例1一种铅酸蓄电池正极铅膏和制方法,包括以下制备步骤:(1)第一步:将占总铅粉重量60%的部分铅粉与占总铅粉重量0.15%的短纤维(短纤维的长度为4mm)、占总铅粉重量0.3%的石墨及占总铅粉重量2.5%的红丹混合均匀,然后40s加占总铅粉重量14.5%的纯水,加水后湿混18min,再加占总铅粉重量8%的硫酸(硫酸的密度为1.5g/cm3)进行酸混,酸混时间为40min,形成半悬浮浆料,加酸完毕后通入90℃的高温蒸汽对半悬浮浆料进行加热并搅拌25min,得到浆料a;(2)第二步:将占总铅粉重量0.3%的锑的氧化物、占总铅粉重量0.3%的铋的氧化物、占总铅粉重量0.15%的氧化锌及占总铅粉重量0.3%的盐类添加剂硫酸锌加入浆料a中,然后搅拌均匀,搅拌时间3min,得到浆料b;(3)第三步:将剩余的铅粉的以边加边搅拌方式逐步加入浆料b中,加料时间3min,全部加完后搅拌6min,得到混合均匀的膏体。
[0034]
实施例2一种铅酸蓄电池正极铅膏和制方法,包括以下制备步骤:(1)第一步:将占总铅粉重量40%的部分铅粉与占总铅粉重量0.05%的短纤维(短纤维的长度为6mm)、占总铅粉重量0.1%的石墨及占总铅粉重量5%的红丹混合均匀,然后20s加占总铅粉重量13.5%的纯水,加水后湿混5min,再加占总铅粉重量10%的硫酸(硫酸的密度为1.4g/cm3)进行酸混,酸混时间为15min,形成半悬浮浆料,加酸完毕后通入80℃的高温蒸汽对半悬浮浆料进行加热并搅拌30min,得到浆料a;(2)第二步:将占总铅粉重量0.1%的锑的氧化物、占总铅粉重量0.6%的铋的氧化物、占总铅粉重量0.08%的氧化锌及占总铅粉重量0.6%的盐类添加剂(硫酸锌、碳酸锌及硫酸铝)加入浆料a中,然后搅拌均匀,搅拌时间2min,得到浆料b;(3)第三步:将剩余的铅粉的以边加边搅拌方式逐步加入浆料b中,加料时间3min,全部加完后搅拌4min,得到混合均匀的膏体。
[0035]
实施例3一种铅酸蓄电池正极铅膏和制方法,包括以下制备步骤:(1)第一步:将占总铅粉重量80%的部分铅粉与占总铅粉重量0.05%的短纤维(短纤维的长度为4mm)、占总铅粉重量0.4%的石墨及占总铅粉重量5%的红丹混合均匀,然后20s加占总铅粉重量16%的纯水,加水后湿混5min,再加占总铅粉重量10%的硫酸(硫酸的密度为1.4g/cm3)进行酸混,酸混时间为60min,形成半悬浮浆料,加酸完毕后通入80℃的高温蒸汽对半悬浮浆料进行加热并搅拌30min,得到浆料a;
(2)第二步:将占总铅粉重量0.1%的锑的氧化物、占总铅粉重量0.6%的铋的氧化物、占总铅粉重量0.08%的氧化锌及占总铅粉重量0.6%的盐类添加剂(硫酸锌、碳酸锌及硫酸铝)加入浆料a中,然后搅拌均匀,搅拌时间5min,得到浆料b;(3)第三步:将剩余的铅粉的以边加边搅拌方式逐步加入浆料b中,加料时间1min,全部加完后搅拌10min,得到混合均匀的膏体。
[0036]
实施例4一种铅酸蓄电池正极铅膏和制方法,包括以下制备步骤:(1)第一步:将占总铅粉重量50%的部分铅粉与占总铅粉重量0.1%的短纤维(短纤维的长度为3mm)、占总铅粉重量0.2%的石墨及占总铅粉重量2%的红丹混合均匀,然后30s加占总铅粉重量14.5%的纯水,加水后湿混10min,再加占总铅粉重量7%的硫酸(硫酸的密度为1.45g/cm3)进行酸混,酸混时间为25min,形成半悬浮浆料,加酸完毕后通入90℃的高温蒸汽对半悬浮浆料进行加热并搅拌22min,得到浆料a;(2)第二步:将占总铅粉重量0.2%的锑的氧化物、占总铅粉重量0.2%的铋的氧化物、占总铅粉重量0.15%的氧化锌及占总铅粉重量0.2%的盐类添加剂(硫酸锌、碳酸锌及硫酸铝)加入浆料a中,然后搅拌均匀,搅拌时间2min,得到浆料b;(3)第三步:将剩余的铅粉的以边加边搅拌方式逐步加入浆料b中,加料时间4min,全部加完后搅拌4min,得到混合均匀的膏体。
[0037]
实施例5一种铅酸蓄电池正极铅膏和制方法,包括以下制备步骤:(1)第一步:将占总铅粉重量70%的部分铅粉与占总铅粉重量0.18%的短纤维(短纤维的长度为5mm)、占总铅粉重量0.4%的石墨及占总铅粉重量4%的红丹混合均匀,然后50s加占总铅粉重量15%的纯水,加水后湿混20min,再加占总铅粉重量8%的硫酸(硫酸的密度为1.5g/cm3)进行酸混,酸混时间为50min,形成半悬浮浆料,加酸完毕后通入95℃的高温蒸汽对半悬浮浆料进行加热并搅拌28min,得到浆料a;(2)第二步:将占总铅粉重量0.4%的锑的氧化物、占总铅粉重量0.45%的铋的氧化物、占总铅粉重量0.25%的氧化锌及占总铅粉重量0.5%的盐类添加剂(硫酸锌、碳酸锌及硫酸铝)加入浆料a中,然后搅拌均匀,搅拌时间4min,得到浆料b;(3)第三步:将剩余的铅粉的以边加边搅拌方式逐步加入浆料b中,加料时间3.5min,全部加完后搅拌7min,得到混合均匀的膏体。
[0038]
对比例1(与实施例1的区别在于,采用常规步骤和制铅膏。)一种铅酸蓄电池正极铅膏和制方法,包括以下制备步骤:将铅粉与占铅粉重量0.15%的短纤维(短纤维的长度为4mm)、占铅粉重量0.3%的石墨、占铅粉重量2.5%的红丹、占总铅粉重量0.3%的锑的氧化物、占总铅粉重量0.15%的氧化锌及占总铅粉重量0.3%的硫酸锌、碳酸锌混合均匀,然后40s加占铅粉重量14.5%的纯水,加水后湿混18min,再加占铅粉重量8%的硫酸(硫酸的密度为1.5g/cm3)进行酸混,酸混时间为40min,形成半悬浮浆料,加酸完毕后通入90℃的高温蒸汽对半悬浮浆料进行加热并搅拌35min,得到混合均匀的膏体。
[0039]
对比例2(与实施例1的区别在于,通入高温蒸汽的温度为50℃。)一种铅酸蓄电池正极铅膏和制方法,包括以下制备步骤:(1)第一步:将占总铅粉重量25%的部分铅粉与占总铅粉重量0.15%的短纤维(短纤维
的长度为4mm)、占总铅粉重量0.3%的石墨及占总铅粉重量2.5%的红丹混合均匀,然后40s加占总铅粉重量14.5%的纯水,加水后湿混18min,再加占总铅粉重量8%的硫酸(硫酸的密度为1.5g/cm3)进行酸混,酸混时间为40min,形成半悬浮浆料,加酸完毕后通入90℃的高温蒸汽对半悬浮浆料进行加热并搅拌25min,得到浆料a;(2)第二步:将占总铅粉重量0.3%的锑的氧化物、占总铅粉重量0.3%的铋的氧化物、占总铅粉重量0.15%的氧化锌及占总铅粉重量0.3%的盐类添加剂硫酸锌加入浆料a中,然后搅拌均匀,搅拌时间3min,得到浆料b;(3)第三步:将剩余的铅粉的以边加边搅拌方式逐步加入浆料b中,加料时间3min,全部加完后搅拌6min,得到混合均匀的膏体。
[0040]
对比例3(与实施例1的区别在于,第一步加入的铅粉含量占总铅粉重量25%。)一种铅酸蓄电池正极铅膏和制方法,包括以下制备步骤:(1)第一步:将占总铅粉重量25%的部分铅粉与占总铅粉重量0.15%的短纤维(短纤维的长度为4mm)、占总铅粉重量0.3%的石墨及占总铅粉重量2.5%的红丹混合均匀,然后40s加占总铅粉重量14.5%的纯水,加水后湿混18min,再加占总铅粉重量8%的硫酸(硫酸的密度为1.5g/cm3)进行酸混,酸混时间为40min,形成半悬浮浆料,加酸完毕后通入90℃的高温蒸汽对半悬浮浆料进行加热并搅拌25min,得到浆料a;(2)第二步:将占总铅粉重量0.3%的锑的氧化物、占总铅粉重量0.3%的铋的氧化物、占总铅粉重量0.15%的氧化锌及占总铅粉重量0.3%的盐类添加剂硫酸锌加入浆料a中,然后搅拌均匀,搅拌时间3min,得到浆料b;(3)第三步:将剩余的铅粉的以边加边搅拌方式逐步加入浆料b中,加料时间3min,全部加完后搅拌6min,得到混合均匀的膏体。
[0041]
图1是实施例1加剩余铅粉前的铅膏sem;图2是实施例1加入剩余铅粉以后铅膏的sem图。由图1和图2可以看出:铅膏中具有尺寸均匀的晶体,长度大小为2-6um之间,图2中可以看出晶体尺寸未发生变化,分散较均匀。
[0042]
图3是实施例2加剩余铅粉前的铅膏sem;图4是实施例2加入剩余铅粉以后铅膏的sem图。由图3和图4可以看出:铅膏中具有尺寸均匀的晶体,长度大小为3um左右。图2中可以看出晶体尺寸未发生变化,分散较均匀。
[0043]
图5是对比例1最终的铅膏的sem图。图5为正常的和膏工艺制备的铅膏的sem图片,铅膏呈块状结构,仅存在少量的晶体。
[0044]
图6是实施例1-3及对比例1-2的12v/12ah的试验电池的循环测试数据图。
[0045]
由于6可以看出:4bs在化成以后转化为骨架铅结构,有利于保持正极活性物质结构稳定性,延缓活性物质的坍塌,延长电池使用寿命。一次混合投入及温度较低都不利于4bs的形成,电池化成以后会使活性物质结构连接松疏,抗软化能力弱,结合循环曲线来看实施例1和实施例2的循环寿命较低。
[0046]
图7是对比例3最终铅膏的sem图。图中的颗粒为不规则块状,只有极少的4bs晶体,第一次投放铅粉量较少不利于4bs的形成,电池化成以后会使活性物质结构连接松疏,抗软化能力弱。
[0047]
由实施例1-5以及对比例1-7的数据可知,只有在本发明权利要求范围内的方案,才能够在各方面均能满足上述要求,得出最优化的方案,得到最优的铅酸蓄电池正极铅膏,
各工艺参数才能使得材料利用、回收率最大化。而对于配比的改动、原料的替换/加减,或者加料顺序的改变,均会带来相应的负面影响。
[0048]
本发明中所用原料、设备,若无特别说明,均为本领域的常用原料、设备;本发明中所用方法,若无特别说明,均为本领域的常规方法。
[0049]
以上所述,仅是本发明的较佳实施例,并非对本发明作任何限制,凡是根据本发明技术实质对以上实施例所作的任何简单修改、变更以及等效变换,均仍属于本发明技术方案的保护范围。