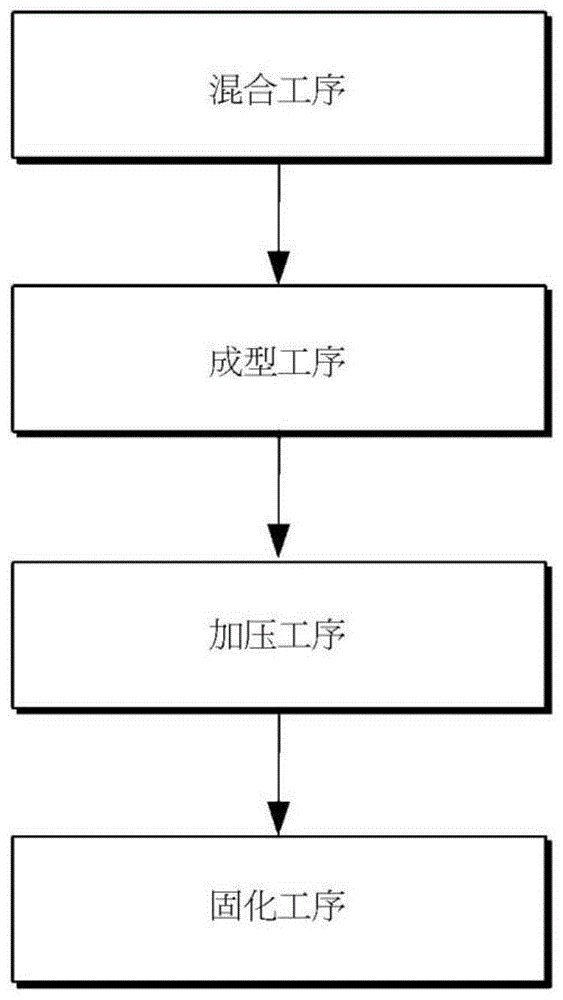
本发明是2017年12月7日所提出的申请号为201780075640.0、发明名称为《电抗器、芯及它们的制造方法、软磁性复合材料及磁芯》的发明专利申请的分案申请。本发明涉及一种适合于称为金属复合物类型的电抗器的软磁性复合材料、使用软磁性复合材料的磁芯、及使用软磁性复合材料的电抗器。
背景技术:
:在办公自动化(officeautomation,oa)机器、太阳能发电系统(solarpowersystem)、汽车、不间断电源(uninterruptiblepowersupply)等各种用途中使用电抗器。电抗器是在例如防止谐波电流向功率输出系统中流出的滤波器(filter)、或使电压升降的电压升降用转换器(converter)等中使用。对于电抗器,根据用途而要求磁导率(magneticpermeability)、电感值(inductancevalue)、铁损(ironloss)等磁特性。例如,电压升降用的转换器中所使用的电抗器由于要求提高能量转换效率,故而要求作为能量损耗的铁损小。另外,为了应对各种用途,也迫切要求将电抗器中所使用的芯成型为任意形状。应对这种迫切要求的电抗器有包括称为金属复合芯的类型的芯的电抗器。金属复合芯(以下也简称为mc芯)是将混合有金属磁性粉末及树脂的材料成型为既定形状,使其固化而成的芯。现有的mc芯的材料为浆料状,在容易向容器中流入所述材料,能够形成既定形状的成型性方面具有优点。称为金属复合物类型的电抗器是指将使用混合有软磁性粉末及树脂的材料的磁芯、以及线圈(coil)一体成型来制造的电抗器。其中,与在磁芯中使用铁氧体(ferrite)的层叠类型的电抗器相比,在高温区域中难以磁饱和等。金属复合物类型的电抗器中所使用的磁芯称为金属复合芯。其是将软磁性粉末与树脂混合来制作软磁性复合材料,通过使所述软磁性复合材料固化而制造。专利文献2中公开了如下方法:通过使用既定的密度比的软磁性粉末,而获得在某种程度上相对磁导率低、饱和磁通密度高的软磁性复合材料。现有技术文献专利文献专利文献1:日本专利特开2012-33727号公报专利文献2:日本专利特开2014-160828号公报技术实现要素:发明所要解决的问题如上所述,由于将磁性粉末与树脂混合而成的材料为浆料状,故而现有的mc芯具有成型性良好的优点。但是,另一方面,当作业者向容器中流入所述材料时,容易将所述材料洒落等,其操作困难,生产性存在问题。另外,现有的mc芯的材料由于树脂的含量多,故而所述材料中的磁性粉末所占的比例减少,导致芯密度的下降,结果使磁特性下降。因此,考虑通过减少树脂量来提高所述材料中所含的磁性粉末的密度。但是,若减少树脂量,则所述材料难以流入至容器内的角落,mc芯的优点即成型性受损。如上所述,现有的mc芯中,难以使成型性、生产性及高密度全部成立。另外,mc芯具有平缓的磁特性。即,与铁氧体芯相比,mc芯难以磁饱和,具有即便增大在线圈中流通的电流,磁导率也难以下降的特性。即,换言之,mc芯具有存在初始磁导率、即在线圈中不流通电流时的磁导率低的倾向的特性。但,作为欲提高磁导率的技术,已知在mc芯制造过程中,从外部施加磁场而使mc芯内的磁性粉末的取向一致的技术(专利文献1)。如上所述的现有技术中,另行设置用以形成电流路径的导电构件,通过对所述导电构件通电而产生磁场,从外部对mc芯的材料施加磁场。这种导电构件例如设置于加入有mc芯材料的容器的外侧,为了成为所需的取向而必须使所述导电构件的设置位置移动。但是,由于所述导电构件的设置条件的制约,难以在实际上欲取向的朝向产生磁通。因此,实际上欲取向的朝向与由导电构件产生的磁通的朝向变得不一致,存在无法获得提高初始磁导率的效果的情况。另外,mc芯中,树脂存在于磁性粉末间,防止磁性粉末彼此的接触。换言之,利用树脂来确保磁性粉末间的绝缘性。若将这种mc芯长时间在高温下使用,则树脂分解,由磁性粉末彼此的接触所引起的磁特性的下降被视为问题。本发明是以下述第一目的、第二目的、第三目的中的至少任一个作为目的。本发明的第一目的在于提供一种不仅获得成型性的优点,而且能够提高生产性及密度的电抗器的制造方法、芯的制造方法、芯及电抗器。本发明的第二目的在于提供一种电抗器的制造方法,其能够获得包括初始磁导率高的芯的电抗器。本发明的第三目的是为了解决如上所述的现有技术的问题点而提出,所述第三目的在于提供一种将在高温下长时间使用时的磁特性恶化加以抑制的复合软磁性复合材料、金属复合芯及金属复合芯的制造方法。解决问题的技术手段为了达成所述第一目的,本发明的电抗器的制造方法是包括包含磁性粉末及树脂的芯、以及安装于所述芯上的线圈的电抗器的制造方法,包括下述结构。(1)混合工序,相对于所述磁性粉末而混合3wt%~5wt%的树脂。(2)成型工序,将所述混合工序中获得的混合物及所述线圈加入至既定的容器中而成型。(3)加压工序,在所述成型工序时挤压所述混合物。(4)固化工序,使所述成型工序中获得的成型体中的树脂固化。本发明的芯的制造方法是包含磁性粉末及树脂的芯的制造方法,包括下述结构。(1)混合工序,相对于所述磁性粉末而混合3wt%~5wt%的树脂。(2)成型工序,将所述混合工序中获得的混合物加入至既定的容器中而成型。(3)加压工序,在所述成型工序时挤压所述混合物。(4)固化工序,使所述成型工序中获得的成型体中的所述树脂固化。本发明的芯为包含磁性粉末及树脂的芯,具有下述结构。(1)所述磁性粉末包含第一磁性粉末、以及平均粒径小于所述第一磁性粉末的第二磁性粉末。(2)所述磁性粉末中的所述第一磁性粉末的添加量为60wt%~80wt%,所述第二磁性粉末的添加量为20wt%~40wt%。(3)所述第一磁性粉末的平均粒径为100μm~200μm,所述第二磁性粉末的平均粒径为3μm~10μm。(4)相对于所述磁性粉末而言的所述树脂的含量为3wt%~5wt%。(5)相对于所述磁性粉末的真密度而言的所述芯的表观密度的比例为超过76.47%。本发明也可理解为包括所述芯的电抗器。为了达成所述第二目的,本发明的电抗器的制造方法为包括包含磁性粉末及树脂的芯、以及安装于所述芯上的线圈的电抗器的制造方法,包括下述结构。(1)混合工序,相对于所述磁性粉末而混合3wt%~5wt%的树脂。(2)成型工序,将所述混合工序中获得的混合物及所述线圈加入至既定的容器中而成型。(3)固化工序,使所述成型工序中获得的成型体中的所述树脂固化。(4)磁场施加工序,在所述固化工序时将所述成型体的所述线圈通电,对所述成型体施加磁场。另外,本发明的电抗器的制造方法为包括包含磁性粉末及树脂的芯、以及安装于所述芯上的线圈的电抗器的制造方法,包括下述结构。(1)混合工序,相对于所述磁性粉末而混合3wt%~5wt%的树脂。(2)成型工序,将所述混合工序中获得的混合物加入至既定的容器中而成型。(3)卷绕工序,在所述成型工序中获得的成型体上卷绕构成所述线圈的导线。(4)固化工序,使卷绕有所述导线的所述成型体中的所述树脂固化。(5)磁场施加工序,在所述固化工序时对所述导线通电,对所述成型体施加磁场。为了达成所述第三目的,本发明的软磁性复合材料为将磁性粉末及树脂混合而成的软磁性复合材料,其中,将所述树脂在220℃的环境中曝露40小时之时的减少率为0.1%以下。所述减少率可设为0.08%以下。所述减少率可设为所述树脂的重量的减少率。所述磁性粉末可包含:既定的平均粒径的第一磁性粉末、以及平均粒径小于所述第一磁性粉末的第二磁性粉末。所述第一磁性粉末的平均粒径可设为100μm~200μm,所述第二磁性粉末的平均粒径可设为5μm~10μm。所述磁性粉末中的所述第一磁性粉末的添加量可设为60wt%~80wt%,所述第二磁性粉末的添加量可设为20wt%~40wt%。所述树脂可设为热固性树脂。所述树脂可设为环氧树脂。包含如上所述的软磁性复合材料的磁芯也是本发明的一实施方式。另外,所述磁性体芯的在155℃的环境中曝露500小时以上时的铁损的变化率可为10%以下。进而,包括所述磁芯的电抗器也是本发明的一实施方式。发明的效果依据本发明,能够提供一种不仅获得成型性的优点,而且可提高生产性及密度的电抗器的制造方法、芯的制造方法、芯及电抗器。依据本发明,能够提供一种电抗器的制造方法,其可获得包括初始磁导率高的芯的电抗器。依据本发明,在软磁性复合材料中,将混合于磁性粉末中的树脂在220℃下曝露40小时之时的减少率设为0.1%以下。由此,在将包含所述软磁性复合材料的磁芯及电抗器长时间曝露于高温下时,也能够抑制存在于磁性粉末间的树脂的消失,其结果为,在本发明的磁芯及电抗器中,能够抑制长时间在高温下使用时的磁特性的下降。附图说明图1是用以对实施方式i的电抗器的制造方法进行说明的流程图。图2是用以对成型工序及加压工序进行说明的图。图3是实施例1~实施例3及比较例1、比较例2的相对于表面压力而言的理论密度的图表。图4是实施例2的芯剖面的扫描电子显微镜(scanningelectronmicroscope,sem)照片(100倍)。图5是比较例1的芯剖面的sem照片(100倍)。图6是实施例1~实施例3及比较例1、比较例2的相对于表面压力而言的磁导率的图表。图7是实施例1~实施例3及比较例1、比较例2的相对于表面压力而言的铁损的图表。图8是实施例4~实施例6及比较例3的相对于表面压力而言的磁导率的图表。图9是实施例4~实施例6及比较例3的相对于表面压力而言的铁损的图表。图10是实施例9~实施例11及比较例6的相对于表面压力而言的磁导率的图表。图11是实施例9~实施例11及比较例6的相对于表面压力而言的铁损的图表。图12是用以对实施方式ii的电抗器的制造方法进行说明的流程图。图13是施加磁场的情况与不施加磁场的情况下的相对于树脂量而言的初始磁导率的图表。图14是相对于树脂量而言的磁导率的变化率的图表。图15是相对于磁场而言的初始电感值的变化率的图表。图16是设为树脂量3wt%而在固化工序中的各施加磁场中制作的电抗器的初始电感值的图表。图17是表示设为树脂量3wt%而在固化工序中的各施加磁场中制作的电抗器的初始电感值的变化率的图表。图18是设为树脂量4wt%而在固化工序中的各施加磁场中制作的电抗器的初始电感值的图表。图19是表示设为树脂量4wt%而在固化工序中的各施加磁场中制作的电抗器的初始电感值的变化率的图表。图20是设为树脂量5wt%而在固化工序中的各施加磁场中制作的电抗器的初始电感值的图表。图21是表示设为树脂量5wt%而在固化工序中的各施加磁场中制作的电抗器的初始电感值的变化率的图表。图22是用以对实施方式iii的金属复合芯的制造方法进行说明的流程图。图23是表示高温放置试验中的放置时间与铁损pcv的关系的图表。符号的说明1:第一磁性粉末2:第二磁性粉末3:树脂4:空隙10:容器20:复合磁性材料30、32:挤压构件40:线圈具体实施方式[1.实施方式i][1-1.结构]本实施方式的电抗器包括芯、及线圈。芯为包含磁性粉末及树脂而构成的金属复合芯。通过将混合有磁性粉末及树脂的粘土状混合物填充于既定的容器,进行加压,能够将芯设为既定的形状。芯的形状可设为例如:环形状芯、i型芯、u型芯、θ型芯、e型芯、eer型芯等各种形状。磁性粉末可使用软磁性粉末,尤其可使用:fe粉末、fe-si合金粉末、fe-al合金粉末、fe-si-al合金粉末(铁硅铝磁合金(sendust))、或者这些两种以上的粉末的混合粉等。fe-si合金粉末例如可使用fe-6.5%si合金粉末、fe-3.5%si合金粉末。软磁性粉末的平均粒径(d50)优选为20μm~150μm。此外,本说明书中所谓“平均粒径”,只要无特别说明,则是指d50,即中值粒径。磁性粉末也可包含平均粒径不同的两种以上的磁性粉末。在此情况下,磁性粉末包含第一磁性粉末、以及平均粒径小于第一磁性粉末的第二磁性粉末,其重量比率优选为设为第一磁性粉末:第二磁性粉末=80:20~60:40。通过设为所述范围,密度提高,磁导率也提高,并且可减小铁损。第一磁性粉末的平均粒径优选为100μm~200μm,第二磁性粉末优选为3μm~10μm。其原因在于,平均粒径小的第二磁性粉末进入第一磁性粉末彼此的间隙,能够实现密度及磁导率的提高及低铁损化。第一磁性粉末及第二磁性粉末优选为球形。第一磁性粉末的圆形度优选为0.93以上,第二磁性粉末的圆形度优选为0.95以上。其原因在于,第一磁性粉末彼此的间隙减少,且更多的第二磁性粉末容易进入所述间隙,能够实现密度及磁导率的提高。此外,第一磁性粉末与第二磁性粉末的种类可相同,也可不同。在不同的情况下也可为3种以上。在利用3种以上的粉末来构成磁性粉末的情况下,也可使各种类的平均粒径不同。第一磁性粉末优选为使用粉碎成分。第二磁性粉末可使用利用水雾化法、气体雾化法、水·气体雾化法来制造的粉末,特别优选为由水雾化法形成的粉末。原因在于,水雾化法在雾化时骤冷,故而粉末难以结晶化。树脂将磁性粉末混合,且将磁性粉末加以保持。在磁性粉末包含平均粒径不同的种类的粉末的情况下,将各粉末以均匀混合的状态来保持。树脂可使用热固性树脂、紫外线固化性树脂、或者热塑性树脂。热固性树脂可使用:酚树脂、环氧树脂、不饱和聚酯树脂、聚氨基甲酸酯、邻苯二甲酸二烯丙酯树脂、硅酮树脂等。紫外线固化性树脂可使用:丙烯酸氨基甲酸酯系、丙烯酸环氧酯系、丙烯酸酯系、环氧系树脂。热塑性树脂优选为使用聚酰亚胺或氟树脂等耐热性优异的树脂。通过添加固化剂而固化的环氧树脂可利用固化剂的添加量等来调整其粘度,因此适合于本发明。也可使用热塑性的丙烯酸系树脂或硅酮树脂。树脂优选为相对于磁性粉末而含有3wt%~5wt%。若树脂的含量少于3wt%,则磁性粉末的接合力不足,芯的机械强度下降。另外,若树脂的含量多于5wt%,则形成于第一磁性粉末间的树脂进入,第二磁性粉末无法填埋所述间隙等,芯的密度下降,磁导率下降。树脂的粘度在与磁性粉末的混合时优选为50mpa·s~5000mpa·s。若粘度小于50mpa·s,则在混合时树脂不会缠绕于磁性粉末,磁性粉末与树脂在容器内容易分离,芯的密度或强度产生不均。若粘度超过5000mpa·s,则粘度过度升高,例如形成于第一磁性粉末间的树脂进入,第二磁性粉末无法填埋所述间隙等,芯的密度下降,磁导率下降。树脂中,可使用sio2、al2o3、fe2o3、bn、aln、zno、tio2等来作为粘度调整材料。作为粘度调整材料的填料的平均粒径宜为第二磁性粉末的平均粒径以下,优选为第二磁性粉末的平均粒径的1/3以下。其原因在于,若填料的平均粒径大,则所获得的芯的密度下降。另外,树脂中,可添加al2o3、bn、aln等高导热率材料。芯的表观密度相对于磁性粉末的真密度的比例优选为超过76.47%,更优选为77.5%以上。若所述比例超过76.47%,则能够提高磁导率。相反,若所述比例为76.47%以下,则由于低密度而成为低磁导率。线圈是已实施绝缘涂覆的导线,可使用铜线或铝线来作为线材。线圈是在芯的至少一部分上卷绕导线而形成或者安装,配置于芯的至少一部分的周围。线圈的卷绕方式或线材的形状并无特别限定。[1-2.电抗器的制造方法]参照附图,对本实施方式的电抗器的制造方法进行说明。本电抗器的制造方法如图1所示,包括(1)混合工序、(2)成型工序、(3)加压工序、及(4)固化工序。(1)混合工序混合工序是将磁性粉末与树脂进行混合的工序。在磁性粉末包含平均粒径不同的两种磁性粉末的情况下,混合工序包括:磁性粉混合工序,将第一磁性粉末、与平均粒径小于第一磁性粉末的第二磁性粉末混合,构成磁性粉末;以及树脂混合工序,相对于磁性粉末,添加3wt%~5wt%的树脂,将磁性粉末与树脂混合。各混合工序的混合可使用既定的混合器,以自动、或者手动来进行。各混合工序的混合时间可适当设定,并无特别限定,例如设为2分钟。通过如上所述的混合工序,能够获得磁性粉末与树脂的混合物(以下也称为复合磁性材料)。此外,混合工序也可在在成型工序中用以将复合磁性材料成型的容器中,填充磁性粉末及树脂来进行混合。由此,不需要将复合磁性材料转移至容器中,能够削减制造工时。(2)成型工序成型工序是将复合磁性粉末加入既定形状的容器中而成型为既定形状的工序。成型工序中,也可将线圈与复合磁性粉末一起加入而成型。作为容器,根据所制造的芯的形状而使用各种形状的容器。在加入线圈的情况下,为了能够从上方插入线圈,容器是使用上表面开口型的箱型或碟形的容器。成型工序中使用的容器也可直接作为收纳芯及线圈的电抗器的包装箱来使用。若使用所述容器来作为包装箱,则具有在复合磁性粉末的固化后不需要将容器取出的优点。在不将容器用作包装箱的情况下,也可利用一个容器来制造多个电抗器。即,也可通过在容器的底部预先形成多个凹部,在所述凹部加入复合磁性材料及线圈,来制造多个电抗器。通过如上所述,以一次的成型工序来完成多个电抗器,因此能够提高制造效率。成型工序中使用的容器可利用树脂成型品来构成其全部或一部分。通过将容器设为树脂制,能够削减制造成本,且可有效利用可形成为mc芯的任意形状的优点。即,由于树脂为比较廉价的材料,故而能够抑制容器的制造成本,并且可通过注射成型等来形成任意形状的芯。树脂成型品的材料例如可使用:不饱和聚酯系树脂、氨基甲酸酯树脂、环氧树脂、块状模塑料(bulkmoldingcompound,bmc)、聚苯硫醚(polyphenylenesulfide,pps)、聚对苯二甲酸丁二酯(polybutyleneterephthalate,pbt)等。另外,也可由铝、镁等导热性高的金属来构成容器的全部或一部分。其原因在于,如后所述,在加压工序中容易将复合磁性材料加温。(3)加压工序加压工序是在成型工序时,利用挤压构件来挤压复合磁性材料的工序。通过利用挤压构件,对加入至容器中的粘土状复合磁性材料进行挤压,而将复合磁性材料扩展为容器的形状,并且使复合磁性材料中所含的空隙减少,提高表观密度及磁导率。在容器中未加入线圈的情况下,通过所述工序,复合磁性材料成为容器内部的形状。即,能够获得包含复合磁性材料的既定形状的成型体。在容器中加入线圈的情况下,如图2所示,在容器10内加入复合磁性材料20,利用挤压构件30,将复合磁性材料20扩展为容器10的形状。然后,在通过挤压复合磁性材料20而形成的空间中插入线圈40,进而填充复合磁性材料20,利用挤压构件32,将复合磁性材料20与线圈40一起从上方挤压。或者,也可在容器10内加入复合磁性材料20,然后,将线圈40包含其内外周而埋设于所述复合磁性材料20,将复合磁性材料20与线圈40一起从上方挤压。如上所述,通过将复合磁性材料20与线圈40一起挤压,可减少复合磁性材料20中所含的空隙,能够提高表观密度及磁导率。此外,也可避开线圈40所存在的部分,而仅挤压复合磁性材料20。如上所述,通过所述工序,能够获得包含线圈的既定形状的复合磁性材料的成型体。如上所述,加压工序可利用挤压构件来挤压复合磁性材料,将所述材料设为容器的形状,在此情况下,能够将加压工序理解为加压工序及成型工序。挤压复合磁性材料的压力优选为6.3kg/cm2以上。若小于所述值,则挤压的压力小,提高表观密度的效果小。另外,即便是所述值以上,也优选为15.7kg/cm2以下。其原因在于,即便超过所述值来挤压,提高表观密度的效果也小。另外,其原因在于,若超过所述值来挤压,则仅树脂被挤压,磁性粉末间的绝缘性恶化。挤压复合磁性材料的时间能够根据树脂的含量或粘性来适当变更。例如,可设为10秒。加压工序也可将容器或者挤压复合磁性材料的挤压构件设为高于常温(例如25℃)的温度来进行。通过提高容器或者挤压构件的温度,则树脂升温,变得柔软。因此,复合磁性材料容易流入容器内的间隙,能够提高成型性,并且所述材料容易流入复合磁性材料中的空隙,能够提高密度。容器或者挤压复合磁性材料的挤压构件的温度宜高于复合磁性材料中所含的树脂的软化点。其原因在于,能够有效地使树脂变软。加压工序也可在保持容器或者挤压复合磁性材料的挤压构件的温度的状态下进行。另外,加压工序除了预先提高容器或者挤压构件的温度以外,也可将复合磁性材料自身预先加温而挤压所述复合磁性材料。也可保持容器或者挤压复合磁性材料的挤压构件的温度,且将复合磁性材料自身预先加温而挤压。(4)固化工序固化工序是使成型工序中获得的成型体中的树脂固化的工序。在成型体中的树脂通过干燥而固化的情况下,干燥环境可设为大气环境。干燥时间能够根据树脂的种类、含量、干燥温度等来适当变更,例如可设为1小时~4小时,但并不限定于此。干燥温度可根据树脂的种类、含量、干燥时间等而适当变更,例如可设为85℃~150℃,但并不限定于此。此外,干燥温度为干燥环境的温度。另外,树脂的固化并不限定于干燥,根据树脂的种类,固化方法不同。例如,若树脂为热固性树脂,则通过加热而使树脂固化,若树脂为紫外线固化性树脂,则通过对成型体照射紫外线而使树脂固化。固化工序也可将在既定的温度下使成型体固化既定时间的工序反复进行多次。另外,例如在树脂通过干燥而固化的情况下,也可每反复进行多次,而改变干燥温度或干燥时间。[1-3.作用·效果](1)本实施方式的电抗器的制造方法是包括包含磁性粉末及树脂的芯、以及安装于所述芯上的线圈的电抗器的制造方法,其包括:混合工序,相对于磁性粉末而混合3wt%~5wt%的树脂;成型工序,将混合工序中获得的混合物及线圈加入至既定的容器中而成型;加压工序,在成型工序时挤压所述混合物;以及固化工序,使成型工序中获得的成型体固化。由此,能够获得不仅获得成型性的优点,而且提高生产性及密度的芯。即,由于将树脂量设为3wt%~5wt%,故而复合磁性材料成为粘土状而容易操作,能够提高生产性。另外,通过包括加压工序,能够确保可将复合磁性材料的形状成型为既定形状的mc芯的优点,即,成型性的优点,并且通过挤压复合磁性材料,所述材料容易进入复合磁性材料中所含的空隙,能够提高芯的表观密度。(2)加压工序将挤压所述混合物的压力设为6.3kg/cm2以上。由此,能够提高芯的密度。(3)加压工序是将挤压所述混合物的构件或者容器设为高于常温的温度而进行。由此,作为所述混合物的复合磁性材料中的树脂被加温,变得柔软。因此,复合磁性材料容易流入至容器内的角落,能够提高成型性,并且所述材料容易流入复合磁性材料中的空隙,能够提高密度。(4)加压工序是将加温至高于常温的温度的所述混合物加入至所述容器中而进行。由此,能够获得与所述(3)同样的作用效果。(5)磁性粉末是将平均粒径不同的两种磁性粉末混合而成。尤其,磁性粉末是将第一磁性粉末、及平均粒径小于第一磁性粉末的第二磁性粉末混合而成,磁性粉末中的第一磁性粉末的添加量设为60wt%~80wt%,第二磁性粉末的添加量设为20wt%~40wt%。由此,第二磁性粉末进入第一磁性粉末彼此的间隙中,能够实现密度及磁导率的提高及低铁损化。(6)第一磁性粉末将平均粒径设为20μm~150μm,第二磁性粉末将平均粒径设为5μm~20μm。由此,芯的密度、磁导率提高,能够减小铁损。(7)树脂设为环氧树脂、硅酮树脂、或者丙烯酸系树脂。由此,能够使复合磁性材料成为粘土状,操作变得容易,能够提高生产性。[2.实施方式ii][2-1.结构]本实施方式的电抗器由于与实施方式i的电抗器的结构相同,故而省略说明。即,芯、线圈、磁性粉末、树脂是与实施方式i相同。[2-2.电抗器的制造方法]参照附图,对本实施方式的电抗器的制造方法进行说明。本电抗器的制造方法如图12所示,包括(1)混合工序、(2)成型工序、(3)加压工序、(4)固化工序、及(5)磁场施加工序。(1)~(4)的工序由于与实施方式i的电抗器的制造方法基本上相同,故而省略相同的部分,仅对不同的部分进行说明。(3)加压工序加压工序是在成型工序时,利用挤压构件来挤压复合磁性材料的工序。通过利用挤压构件,对加入至容器中的粘土状的复合磁性材料进行挤压,而将复合磁性材料扩展为容器的形状,并且减少复合磁性材料中所含的空隙,提高表观密度、初始磁导率及初始电感值。所谓初始电感值,是指在由本发明所获得的电抗器的线圈中不流通电流时,即固化工序中的施加磁场为0(ka/m)时的电感值。(5)磁场施加工序磁场施加工序是在固化工序时对包含复合磁性材料的成型体所包括的线圈通电,对所述成型体施加磁场的工序。于在成型体中埋设有线圈的情况下,对所述线圈通电。获得成型体后,在所述成型体上卷绕导线而构成线圈的情况下,对所述线圈通电。磁场施加工序只要进行至成型体中的树脂固化为止即可,磁场施加工序可在固化工序前进行。另外,在进行多次固化工序的情况下,磁场施加工序也可在所述固化工序间进行。通过磁场施加工序,成型体中的磁性粉末成为与所施加的磁场的朝向一致而具有取向性,结果,能够获得初始磁导率高的芯。即,磁场施加工序由于在固化工序之间,使用作为电抗器而包括的线圈来作为对成型体施加磁场的元件,故而电抗器制品自身产生的磁通的朝向具有取向性,因此电抗器制品自身产生的磁通与磁性粉末的取向一致。所述取向性的一致程度理想为磁性粉末的磁化容易轴与由电抗器所包括的线圈来产生的磁通的朝向(磁力线的方向)一致,但磁化容易轴也可相对于磁力线而倾斜至45°左右。如上所述,通过磁场施加工序,能够获得初始磁导率高的芯。对成型体施加的磁场优选为2ka/m以上。其原因在于,如后述的实施例所示,获得l0值饱和增加率的一半以上的l0值增加的效果。所谓l0值饱和增加率,是基于下述式(5)而获得的l0值的变化率,式(5)中的l0(h)是施加l0值的提高饱和的磁场而获得固化中的施加磁场的电抗器的初始电感值。另外,若第二磁性粉末被励磁,则具有磁性粉末中的晶粒的磁化方向一致的效果,通过将第二磁性粉末进行励磁,直流重叠特性提高。另外认为,包括包含经励磁而取向的复合磁性材料的芯的电抗器具有涡流损耗下降,由芯产生的热降低的效果。[2-3.作用·效果](1)本实施方式的电抗器的制造方法是包括包含磁性粉末及树脂的芯、以及安装于所述芯上的线圈的电抗器的制造方法,其包括:混合工序,相对于磁性粉末而混合3wt%~5wt%的树脂;成型工序,将混合工序中获得的混合物及线圈加入至既定的容器中而成型;固化工序,使成型工序中获得的成型体中的树脂固化;以及磁场施加工序,在固化工序时将成型体的线圈通电,对成型体施加磁场。由此,能够获得包括初始磁导率高的芯的电抗器。即,现有的mc芯中,相对于磁性粉末而言的树脂的添加量超过5wt%,与此相对,通过设为3wt%~5wt%,能够提高密度及初始磁导率。进而,通过在固化工序时对电抗器自身所包括的线圈通电,而使成型体中的磁性粉末取向为由所述线圈产生的磁通的朝向,故而可取向为所要取向的朝向,因此能够提高初始磁导率。(2)磁场施加工序将所述磁场设为2ka/m以上。由此,能够获得通过磁场施加工序而获得的初始电感值提高效果的大半。(3)包括在成型工序时挤压所述混合物的加压工序。由此,能够提高芯的密度。(4)加压工序是将容器或者挤压所述混合物的构件设为高于常温的温度来进行。由此,所述混合物即复合磁性材料中的树脂被加温,变得柔软。因此,复合磁性材料容易流入至容器内的角落,能够提高成型性,并且所述材料容易流入复合磁性材料中的空隙,能够提高密度。(5)加压工序是将加温至高于常温的温度的所述混合物加入至所述容器中而进行。由此,能够获得与所述(4)相同的作用效果。(6)磁性粉末是将平均粒径不同的两种磁性粉末混合而成。尤其,磁性粉末是将第一磁性粉末、及平均粒径小于第一磁性粉末的第二磁性粉末混合而成,磁性粉末中的第一磁性粉末的添加量设为60wt%~80wt%,第二磁性粉末的添加量设为20wt%~40wt%。由此,第二磁性粉末进入第一磁性粉末彼此的间隙,能够实现密度及磁导率的提高及低铁损化。(7)第一磁性粉末将平均粒径设为20μm~150μm,第二磁性粉末将平均粒径设为5μm~20μm。由此,芯的密度、磁导率提高,能够减小铁损。(8)树脂设为环氧树脂、硅酮树脂、或者丙烯酸系树脂。由此,可使复合磁性材料成为粘土状,操作变得容易,能够提高生产性。[3.实施方式iii][3-1.结构]本实施方式的软磁性复合材料是包含磁性粉末及树脂而构成。软磁性复合材料中所含的树脂是使用在220℃的环境中曝露40小时之时的减少率(以下称为加热减量)为0.1%以下的树脂。树脂通过长时间曝露于高温的环境中,体积或重量变化。加热减量是表示曝露于高温前后的树脂的重量或体积的变化率的值,加热减量是基于曝露于高温前后的树脂的重量或体积来算出。以下,虽基于树脂的重量变化来算出加热减量,但也可基于体积变化来算出。即便是基于重量变化及体积变化来算出加热减量的情况,本实施方式中,也使用在220℃的环境中曝露40小时之时的加热减量为0.1%以下的树脂。本实施方式中,通过将磁性粉末及树脂混合而获得粘土状的软磁性复合材料。另外,本实施方式中,通过将粘土状的软磁性复合材料填充于既定的容器中,进行加压而将磁芯设为既定的形状。磁芯的形状可设为例如环形状芯、i型芯、u型芯、θ型芯、e型芯、eer型芯等各种形状。(磁性粉末)磁性粉末也可使用平均粒径不同的多种磁性粉末。例如,也可包含平均粒径不同的两种磁性粉末。以下,以将两种软磁性粉末混合而成的混合粉末为例进行说明。但,也可未必为将两种粉末混合而成的粉末。例如,可使用1种软磁性粉末,也可将3种以上的软磁性粉末进行混合。在将两种磁性粉末混合的情况下,磁性粉末包含第一磁性粉末、及平均粒径小于第一磁性粉末的第二磁性粉末。第一磁性粉末及第二磁性粉末的重量比率优选为设为第一磁性粉末:第二磁性粉末=80:20~60:40。通过设为所述范围,密度提高,磁导率也提高,并且能够减小铁损。第一磁性粉末的平均粒径优选为100μm~200μm,第二磁性粉末优选为5μm~10μm。通过将平均粒径不同的两种磁性粉末混合,则平均粒径小的第二磁性粉末进入第一磁性粉末彼此的间隙。由此,能够实现密度及磁导率的提高及低铁损化。第一磁性粉末及第二磁性粉末可使用软磁性粉末,尤其可使用fe粉末、fe-si合金粉末、fe-al合金粉末、fe-si-al合金粉末(铁硅铝磁合金)、这些两种以上的粉末的混合粉、或者非晶质软磁性合金粉末等。作为fe-si合金粉末,例如可使用fe-6.5%si合金粉末、fe-3.5%si合金粉末。软磁性粉末的平均粒径(d50)优选为20μm~150μm。此外,本说明书中所谓“平均粒径”,只要无特别说明,则是指d50、即中值粒径。第一磁性粉末及第二磁性粉末优选为球形。第一磁性粉末的圆形度优选为0.90以上,第二磁性粉末的圆形度优选为0.94以上。其原因在于,第一磁性粉末彼此的间隙减少,且更多的第二磁性粉末容易进入所述间隙,能够实现密度及磁导率的提高。此外,第一磁性粉末与第二磁性粉末的种类可相同,也可不同。在将3种以上的软磁性粉末混合的情况下,也可将分别不同的磁性粉末混合3种以上。第一磁性粉末及第二磁性粉末可使用以气体雾化法或水雾化法、或者水气体雾化法来制造的粉末。利用这些方法来形成的粒子的平均圆形度理想为设为0.90以上,在仅利用各种雾化法而无法形成平均圆形度为0.90以上的粉末的情况下,也可进而实施提升粒子的平均圆形度的加工。例如,由气体雾化法形成的软磁性粉末为大致球状的粒子。因此,可将利用气体雾化法而形成的粉末不进行加工而直接使用。另一方面,利用水雾化法来制造的软磁性粉末是在其表面形成有凹凸的非球状粒子。在此情况下,能够通过使用球磨机(ballmill)、机械合金化(mechanicalalloying)、喷射磨机(jetmill)、磨碎机(attritor)或者表面改质装置,使表面的凹凸平整,从而使粒子的平均圆形度上升。(树脂)树脂混合于混合粉末,具有在第一粉末与第二粉末均匀混合的状态下加以保持的功能。树脂与磁性粉末混合,将所混合的磁性粉末加以保持。在磁性粉末包含平均粒径不同的种类的粉末的情况下,将各粉末以均匀混合的状态来保持。树脂是使用在220℃下加热40小时之时的加热减量为0.1%以下、理想为0.08%以下的树脂。树脂可使用固化性树脂。若加热减量为0.1%以下,则树脂可使用热固性树脂、紫外线固化性树脂、或者热塑性树脂。热固性树脂可使用酚树脂、环氧树脂、不饱和聚酯树脂、聚氨基甲酸酯、邻苯二甲酸二烯丙酯树脂、硅酮树脂等。紫外线固化性树脂可使用丙烯酸氨基甲酸酯系、丙烯酸环氧酯系、丙烯酸酯系、环氧系的树脂。热塑性树脂优选为使用聚酰亚胺或氟树脂等耐热性优异的树脂。通过添加固化剂而固化的环氧树脂能够通过固化剂的添加量等来调整其粘度,因此适合于本发明。也可使用热塑性的丙烯酸系树脂或硅酮树脂。树脂优选为相对于磁性粉末而含有3wt%~5wt%。若树脂的含量少于3wt%,则磁性粉末的接合力不足,芯的机械强度下降。另外,若树脂的含量多于5wt%,则形成于第一磁性粉末间的树脂进入,第二磁性粉末无法填埋所述间隙等,芯的密度下降,初始磁导率μ0下降。树脂的粘度在与磁性粉末的混合时优选为50mpa·s~5000mpa·s。若粘度小于50mpa·s,则在混合时,树脂不会缠绕于磁性粉末,在容器内磁性粉末与树脂容易分离,芯的密度或强度产生不均。若粘度超过5000mpa·s,则粘度过度升高,例如形成于第一磁性粉末间的树脂进入,第二磁性粉末无法填埋所述间隙等,芯的密度下降,初始磁导率μ0下降。树脂中,可使用sio2、al2o3、fe2o3、bn、aln、zno、tio2等来作为粘度调整材料。作为粘度调整材料的填料的平均粒径宜为第二磁性粉末的平均粒径以下,优选为第二磁性粉末的平均粒径的1/3以下。其原因在于,若填料的平均粒径大,则所获得的芯的密度下降。另外,树脂中可添加al2o3、bn、aln等高导热率材料。芯的表观密度相对于磁性粉末的真密度而言的比例优选为超过76.47%,更优选为77.5%以上。若所述比例超过76.47%,则能够提高磁导率。相反,若所述比例为76.47%以下,则由于低密度而成为低磁导率。(线圈)线圈为已实施绝缘涂覆的导线,可使用铜线或铝线来作为线材。线圈是在芯的至少一部分上卷绕导线而形成或者安装,配置于芯的至少一部分的周围。线圈的卷绕方式或线材的材料、形状并无特别限定。[3-2.金属复合芯的制造方法]参照附图,对本实施方式的金属复合芯的制造方法进行说明。本金属复合芯的制造方法如图22所示,包括(1)混合工序、(2)成型工序、(3)加压工序、及(4)固化工序。(1)混合工序混合工序为将磁性粉末及树脂混合的工序。混合工序包括:磁性粉混合工序,将第一磁性粉末、与平均粒径小于第一磁性粉末的第二磁性粉末进行混合,构成磁性粉末;以及树脂混合工序,相对于磁性粉末而添加3wt%~5wt%的树脂,将磁性粉末及树脂混合。各混合工序的混合可使用既定的混合器,以自动、或者手动来进行。各混合工序的混合时间可适当设定,并无特别限定,例如设为2分钟。通过如上所述的混合工序,能够获得磁性粉末与树脂的混合物(以下也称为复合磁性材料)。此外,混合工序也可在在成型工序中用以将复合磁性材料成型的容器中,填充磁性粉末及树脂而混合。由此,不需要将复合磁性材料转移至容器中,能够削减制造工时。(2)成型工序成型工序是将复合磁性粉末加入至既定形状的容器中而成型为既定形状的工序。在成型工序中,也可将线圈与复合磁性粉末一起加入而成型。作为容器,根据所制造的芯的形状而使用各种形状的容器。在加入线圈的情况下,为了能够从上方插入线圈,容器是使用上表面开口型的箱型或碟形的容器。成型工序中所使用的容器也可直接作为收纳芯及线圈的金属复合芯的包装箱来使用。若将所述容器用作包装箱,则具有在复合磁性粉末的固化后不需要将容器取出的优点。在不将容器用作包装箱的情况下,也可利用一个容器来制造多个金属复合芯。即,也可通过在容器的底部预先形成多个凹部,在所述凹部加入复合磁性材料及线圈,来制造多个金属复合芯。通过如上所述,以一次的成型工序来完成多个金属复合芯,因此能够提高制造效率。成型工序中使用的容器可利用树脂成型品来构成其全部或一部分。通过将容器设为树脂制,能够削减制造成本,且可有效利用可形成为mc芯的任意形状的优点。即,由于树脂为比较廉价的材料,故而能够抑制容器的制造成本,并且能够通过注射成型等来形成任意形状的芯。另外,也可利用铝、镁等导热性高的金属来构成容器的全部或一部分。其原因在于,如后所述,在加压工序中容易将复合磁性材料加温。(3)加压工序加压工序是在成型工序时利用挤压构件来挤压复合磁性材料的工序。通过利用挤压构件,将加入至容器中的粘土状复合磁性材料进行挤压,而将复合磁性材料扩展为容器的形状,并且减少复合磁性材料中所含的空隙,提高表观密度、及初始磁导率。在容器中未加入线圈的情况下,通过所述工序,复合磁性材料成为容器内部的形状。即,能够获得包含复合磁性材料的既定形状的成型体。在容器中加入线圈的情况下,如图2所示,在容器10内加入复合磁性材料20,利用挤压构件30而将复合磁性材料20扩展为容器10的形状。然后,在通过挤压复合磁性材料20而形成的空间中插入线圈40,进而填充复合磁性材料20,利用挤压构件32,将复合磁性材料20与线圈40一起从上方挤压。或者,也可在容器10内加入复合磁性材料20,然后,将线圈40埋设于所述复合磁性材料20,将复合磁性材料20与线圈40一起从上方挤压。如上所述,通过将复合磁性材料20与线圈40一起挤压,而减少复合磁性材料20中所含的空隙,能够提高表观密度及磁导率。此外,也可避开线圈40所存在的部分,而仅挤压复合磁性材料20。如上所述,通过所述工序,能够获得包含线圈的既定形状的复合磁性材料的成型体。如上所述,加压工序也可利用挤压构件来挤压复合磁性材料,将所述材料设为容器的形状,在此情况下,能够将加压工序理解为加压工序及成型工序。挤压复合磁性材料的压力优选为2.0kg/cm2以上。若小于所述值,则挤压的压力小,提高表观密度的效果小。另外,即便为所述值以上,也优选为10.0kg/cm2以下。其原因在于,即便超过所述值来挤压,提高表观密度的效果也小。挤压复合磁性材料的时间可根据树脂的含量或粘性而适当变更。例如可设为10秒。加压工序也可将容器或者挤压复合磁性材料的挤压构件设为高于常温(例如25℃)的温度来进行。通过提高容器或者挤压构件的温度,树脂被加温而变得柔软。因此,复合磁性材料容易流入容器内的间隙,能够提高成型性,并且所述材料容易流入复合磁性材料中的空隙,能够提高表观密度。容器或者挤压复合磁性材料的挤压构件的温度宜高于复合磁性材料中所含的树脂的软化点。其原因在于,能够有效地使树脂变软。加压工序也可在将容器或者挤压复合磁性材料的挤压构件的温度加以保持的状态下进行。另外,加压工序除了预先提高容器或者挤压构件的温度以外,也可将复合磁性材料自身预先加温来挤压所述复合磁性材料。也可将容器或者挤压复合磁性材料的挤压构件的温度加以保持,且将复合磁性材料自身预先加温来挤压。(4)固化工序固化工序是使成型工序中获得的成型体中的树脂固化的工序。在通过成型体中的树脂的干燥而固化的情况下,干燥环境能够设为大气环境。固化工序中,通过基于树脂的干燥状态来控制干燥温度及时间的干燥分布,而使树脂固化。干燥时间可根据树脂的种类、含量、干燥温度等而适当变更,例如可设为1小时~4小时,但并不限定于此。干燥温度可根据树脂的种类、含量、干燥时间等而适当变更,例如可设为85℃~150℃,但并不限定于此。此外,干燥温度为干燥环境的温度。另外,树脂的固化并不限定于干燥,固化方法根据树脂的种类而不同。例如若树脂为热固性树脂,则通过加热而使树脂固化,若树脂为紫外线固化性树脂,则通过对成型体照射紫外线而使树脂固化。固化工序也可将在既定的温度下使成型体固化既定时间的工序反复进行多次。另外,例如,在树脂通过干燥而固化的情况下,也可每反复进行多次,而改变干燥温度或者干燥时间。[3-3.作用·效果](1)作为本实施方式的磁芯中所使用的树脂,是设为将所述树脂在220℃的环境中曝露40小时之时的减少率为0.1%以下、理想为0.08%以下的树脂。减少率是将树脂曝露于高温下的环境中的情况下的重量的减少率。利用本实施方式的软磁性复合材料来制作的磁芯中,即便在长时间在高温下使用的情况下,也可抑制磁芯内部的磁性粉末彼此的接触。磁芯中,产生与内部所含的软磁性粉末的大小相应的涡流。若将磁芯长时间曝露于高温下,则在磁芯中所含的树脂的减少率超过0.1%的情况下,树脂由于热的影响而分解、消失。通过由树脂隔开的磁性粉末彼此由于树脂的消失而接触,产生更大的涡流。(2)本实施方式的磁性粉末是使用平均粒径不同的多种磁性粉末。例如,第一磁性粉末的平均粒径设为100μm~200μm,第二磁性粉末的平均粒径设为5μm~10μm。另外,将磁性粉末的比例设为:第一磁性粉末的添加量为60wt%~80wt%,所述第二磁性粉末的添加量为20wt%~40wt%。由此,第二磁性粉末进入第一磁性粉末彼此的间隙,能够实现密度及磁导率的提高及低铁损化。(3)树脂可利用热固性树脂、紫外线固化性树脂、或者热塑性树脂,但可使用热固性树脂。其中优选为利用环氧树脂。环氧树脂不仅玻璃转移点高、耐热性优异,而且在固化时不会副产生挥发物质,因此成形品的尺寸变化少。另外,由于富有流动性,即使在比较低压下也可成形,故而可实现工序的简易化。(4)使用本实施方式的软磁性复合材料来制作的磁芯即便在长时间曝露于155℃的环境中的情况下,也能够将铁损的变化率抑制为小。进而理想为,使用可制作在155℃的环境中曝露500小时以上时的铁损的变化率成为10%以下的磁芯的软磁性复合材料。此种磁性粉末的芯即便在155℃的环境中曝露1000小时以上,树脂也不会由于热的影响而分解、消失。换言之,这可根据经过500小时的时刻的铁损的变化率来预测经过1000小时的时刻的铁损的变化率,由此也可实现高温放置试验的时间的缩短。[4.实施例][4-1.实施例i]以下参照表1~表4及图3~图11,对本发明的实施例i进行说明。(1)测定项目测定项目为密度、磁导率及铁损。对于所制作的各芯的样品,利用φ2.6mm的铜线,实施40圈的卷线来制作电抗器。各芯的样品的形状设为外径为35mm、内径为20mm、高度为11mm的环形形状。另外,以下述条件来算出所制作的电抗器的磁导率及铁损。<密度>芯的密度为表观密度。即,测量各芯的样品的外径、内径、及高度,根据这些值,基于π×(外径2-内径2)×高度来算出样品的体积(cm3)。而且,测定样品的质量,将所测定的质量除以所算出的体积来算出芯的密度。<磁导率及铁损>磁导率及铁损的测定条件设为频率20khz、最大磁通密度bm=30mt。磁导率设为在测定铁损pcv时设定最大磁通密度bm时的振幅磁导率。关于铁损,使用作为磁性测量机器的bh分析仪(岩通计测股份有限公司:sy-8232)来算出。所述计算是通过根据铁损的频率曲线,以下述(1)式~(3)式,利用最小平方法来算出磁滞损耗系数、涡流损耗系数而进行。pcv=kh×f+ke×f2……(1)phv=kh×f……(2)pev=ke×f2……(3)pcv:铁损kh:磁滞损耗系数ke:涡流损耗系数f:频率phv:磁滞损耗pev:涡流损耗本实施例中,各粉末的平均粒径及圆形度是使用下述装置而采取3000个的平均值,是在玻璃基板上分散粉末,利用显微镜来拍摄粉末照片,从图像中自动测定每一个。公司名:马尔文(malvern)装置名:粒度粒形分析仪(morphologi)g3s比表面积是利用布鲁诺-埃梅特-特勒(brunauer-emmett-teller,bet)法来测定。(2)样品的制作方法芯的样品是如下所述,从(a)加压工序中的压制表面压力、(b)树脂量、(c)容器的温度的差异的观点来制作。下述依次示出这些制作方法及其结果。(a)加压工序中的压制表面压力首先,作为混合工序,将平均粒径为123μm的fe-6.5%si合金粉末(圆形度为0.943)、及平均粒径为5.1μm的fe-6.5%si合金粉末(圆形度为0.908),以重量比率70:30在v型混合机中混合30分钟而构成磁性粉末。然后,在铝杯中加入所述磁性粉末,相对于所述磁性粉末,添加3.5wt%的环氧树脂,使用刮刀来手动混合2分钟。由此,获得作为磁性粉末与树脂的混合物的复合磁性材料。继而,将混合工序中获得的复合磁性材料填充于具有环形形状的空间的树脂制容器中,使用油压机,将容器内的复合磁性材料以表1的压制压来挤压10秒,制作环形形状的成型体。在所述挤压期间,容器的温度保持为25℃。将如上所述通过加压工序及成型工序而获得的成型体在大气中,在85℃下干燥2小时,然后在120℃下干燥1小时,进而在150℃下干燥4小时,制作成为样品的环形芯。[表1]pcv[20khz30mt]在表1及图3~图7中示出由各压制压所获得的实施例1~实施例3、比较例1、比较例2中的芯的密度、磁导率、铁损的结果。实施例1~实施例3将压制压设为400n、600n、1000n,比较例1无压制,比较例2将压制压设为100n。压制面均相同。表1中的“理论密度”是根据芯的表观密度/磁性粉末的真密度来算出的比例。此处,第一磁性粉末、第二磁性粉末均使用fe-6.5%si合金粉末,将其真密度设为7.63g/cm3而算出理论密度。图3是实施例1~实施例3以及比较例1、比较例2的相对于表面压力而言的理论密度的图表。如表1及图3所示,可知实施例1~实施例3、比较例1、比较例2的相对于表面压力而言的理论密度存在如下倾向:较不进行加压工序的比较例1而言,进行加压工序的比较例2及实施例1~实施例3的理论密度高,且随着表面压力上升而升高。表面压力为1.6kg/cm2的比较例2中,理论密度与无加压的比较例1相比,基本上无变化,但在表面压力为6.3kg/cm2以上的实施例1~实施例3中,理论密度达到77.5%以上,成为高于比较例1、比较例2的值。即,可知通过将表面压力设为6.3kg/cm2以上,所述材料遍布至复合磁性材料中所含的空隙、或容器的角落,由此密度提高。另外,可知若表面压力成为6.3kg/cm2以上,则理论密度大致一定。图4是实施例2的芯剖面的sem照片(100倍)。图5是比较例1的芯剖面的sem照片(100倍)。图4及图5中,符号1表示第一磁性粉末,符号2表示第二磁性粉末。符号3表示树脂,符号4表示空隙。此外,空隙4是在sem照片中以深黑表示的部分,与此相对,以比较淡的黑来表示的部分为树脂3。如图4、图5所明示,可知图4所示的实施例2较图5所示的比较例1而言,复合磁性材料中的空隙4的数量减少,空隙4自身的大小也可减小。磁导率为振幅磁导率,是通过使用所述的阻抗分析仪,由20khz、1.0v的各磁场的强度的电感来算出。表1中的“μ0”表示不使直流重叠的状态、即磁场的强度为0h(a/m)时的初始磁导率。表1中的“μ12000”表示磁场的强度为12kh(ka/m)时的磁导率。图6是实施例1~实施例3以及比较例1、比较例2的相对于表面压力而言的磁导率的图表。如表1及图6所示,可知,与未加压的比较例1相比,加压的实施例1~实施例3的磁导率升高。例如可知,与比较例1相比,实施例1的初始磁导率μ0上升约8.7%。可知在加压的比较例2中,与未加压的比较例1相比,磁导率也升高,但对于芯的密度上升的帮助小。图7是实施例1~实施例3以及比较例1、比较例2的相对于表面压力而言的铁损的图表。如表1及图7所示,可知,关于铁损,与未加压的比较例1相比,加压的实施例1~实施例3的铁损降低。尤其可知,存在通过增大表面压力,而磁滞损耗(phv)下降的倾向。可知在加压的比较例2中,与未加压的比较例1相比,铁损减少,但实施例1~实施例3的铁损更减少。可知若表面压力达到6.3kg/cm2以上,则存在磁导率及铁损均成为大致一定,且由加压所引起的对磁特性的效果饱和的倾向。换言之,可知,在表面压力为6.3kg/cm2~15.7kg/cm2的范围内,可获得由于包括加压工序而引起的密度、磁导率的提高及低铁损化的效果。(b)树脂量将实施例2的树脂量设为表2所示的条件,以与实施例2相同的顺序来制作芯的样品(实施例4~实施例8以及比较例3~比较例5)。在表2及图8、图9中示出实施例4~实施例8以及比较例3~比较例5的密度、磁导率、铁损的结果。此外,表2的μ0、μ12000是与表1相同的含义。[表2]pcv[20khz30mt]图8是实施例4~实施例8以及比较例3~比较例5的相对于树脂量而言的磁导率的图表。图9是实施例4~实施例8以及比较例3~比较例5的相对于树脂量而言的铁损的图表。如表2及图8、图9所示,若树脂量相对于复合磁性材料而小于3wt%,则芯所包含的空隙增多,密度下降。其结果为,成为磁导率的下降以及磁滞损耗增加的原因。另外,若树脂量小于3wt%,则磁性粉末彼此容易进行点接触,成为涡流损耗增加的原因。另一方面,若树脂量相对于复合磁性材料而超过5wt%,则密度的下降变得显著。其结果为,磁滞损耗增大。(c)容器的温度改变容器的温度来制作芯的样品。如所述(a)所述,实施例1~实施例3及比较例1中,容器的温度设为25℃。另外,将容器的温度设为70℃,且除了容器的温度以外设为与所述(a)中进行的工序相同,将由此获得的样品作为实施例9~实施例11及比较例6。在表3及图10、图11中,示出实施例1~实施例3、实施例9~实施例11及比较例1、比较例2、比较例6的密度、磁导率、铁损的结果。此外,表3的理论密度、μ0、μ12000是与表1相同的含义。[表3]pcv[20khz30mt]图10是实施例9~实施例11及比较例6的相对于表面压力而言的磁导率的图表。图11是实施例9~实施例11及比较例6的相对于表面压力而言的铁损的图表。如表3及图6、图7、图10、图11所示,可知,较将容器的温度设为25℃的实施例1~实施例3、比较例2而言,将容器的温度设为70℃的实施例9~实施例11、比较例6存在密度、理论密度增加的倾向,且存在铁损减少的倾向。磁导率表现出根据表面压力而增减的结果。另外可知,将容器的温度设为70℃,在提高温度的期间,实施例9~实施例11的理论密度达到77.9%以上,通过提高表面压力而高于比较例6。如上所述,通过将容器加温至高于常温(25℃),复合磁性材料中的树脂变得柔软,所述材料容易流入所述材料中的空隙,由此认为,表观密度提高,理论密度提高。作为其结果,可知获得低铁损化的效果。(d)树脂的粘度测定对本实施例中使用的树脂的粘度进行说明。本实施例中使用的树脂的粘度是通过如下所述,测定载置于复合磁性材料上的砝码的沉入深度,来作为树脂的粘度。即,首先,将树脂的添加量设为表4所示的条件,以与所述(a)的混合工序相同的方式制作复合磁性材料。继而,将所获得的复合磁性材料,以厚度成为3mm的方式投入直径为5mm的铝制容器中,在所述复合磁性材料上的中央载置日本工业标准(japaneseindustrialstandard,jis)的10g砝码。接着,载置砝码后经过10秒,然后去除砝码,测定由砝码的重量所形成的复合磁性材料的凹坑的深度。将其结果示于表4中。[表4]树脂量[wt%]深度[mm]30.26440.48950.558如表4所示,可知,树脂的添加量越多,凹坑的深度越深,复合磁性材料的粘性低,砝码容易沉入。[4-2.实施例ii]以下,参照表5~表11及图13~图21,对本发明的实施例ii进行说明。(1)测定项目测定项目为密度、磁导率、铁损、及电感值(l值)。对于所制作的各芯的样品,利用φ2.6mm的铜线,实施40圈的卷线来制作电抗器。各芯的样品的形状设为外径为35mm、内径为20mm、高度为11mm的环形形状。另外,以下述条件来算出所制作的电抗器的磁导率、铁损及电感值。<密度>芯的密度为表观密度。即,测量各芯的样品的外径、内径、及高度,根据这些值,基于π×(外径2-内径2)×高度来算出样品的体积(cm3)。而且,测定样品的质量,将所测定的质量除以所算出的体积来算出芯的密度。<磁导率及铁损>磁导率及铁损的测定条件设为频率20khz、最大磁通密度bm=30mt。磁导率设为在测定铁损pcv时设定最大磁通密度bm时的振幅磁导率。关于铁损,使用作为磁性测量机器的bh分析仪(岩通计测股份有限公司:sy-8232)来算出。所述计算是通过根据铁损的频率曲线,以下述(1)式~(3)式,利用最小平方法来算出磁滞损耗系数、涡流损耗系数而进行。pcv=kh×f+ke×f2……(1)phv=kh×f……(2)pev=ke×f2……(3)pcv:铁损kh:磁滞损耗系数ke:涡流损耗系数f:频率phv:磁滞损耗pev:涡流损耗<电感值>电感值是通过对所制作的芯的样品实施1次卷线(20圈),在20khz、1.0v的条件下使用阻抗分析仪(安捷伦科技(agilenttechnology)公司:4294a)来测定。此外,本实施例中,各粉末的平均粒径及圆形度是使用下述装置而采取3000个的平均值,在玻璃基板上分散粉末,利用显微镜来拍摄粉末照片,从图像中自动测定每一个。公司名:马尔文(malvern)装置名:粒度粒形分析仪(morphologi)g3s比表面积是利用bet法来测定。(2)样品的制作方法芯的样品是如下所述,从(a)施加磁场的有无、(b)施加磁场的大小、(c)加压工序的有无的观点来制作。下述依次示出这些制作方法及其结果。(a)施加磁场的有无首先,作为混合工序,将平均粒径为123μm的fe-6.5%si合金粉末(圆形度为0.943)、与平均粒径为5.1μm的fe-6.5%si合金粉末(圆形度为0.908),以重量比率70:30在v型混合机中混合30分钟而构成磁性粉末。然后,在铝杯中加入所述磁性粉末,相对于所述磁性粉末,以表5所示的条件来添加环氧树脂,使用刮刀来手动混合2分钟。由此,获得作为磁性粉末与树脂的混合物的复合磁性材料。继而,将混合工序中获得的复合磁性材料填充于具有环形形状的空间的树脂制容器中,使用油压机,将容器内的复合磁性材料以600n的压制压(表面压力9.4kg/cm2)挤压10秒,来制作环形形状的成型体。在所述挤压期间,容器的温度保持为25℃。然后,对所获得的成型体,将所述铜线卷绕40圈而形成线圈,制作成为基础的电抗器。然后,将所述电抗器在大气中,在85℃下干燥2小时,然后在120℃下干燥1小时,进而在150℃下干燥4小时而使树脂固化,制作成为样品的环形芯。此时,以在各温度下的干燥时间中成为4.85ka/m的方式对线圈通电,获得实施例12~实施例16的样品。实施例12~实施例16的差异为树脂的添加量,分别为3.0wt%~5.0wt%。另外,制作在树脂的固化中未施加磁场而制作的环形线圈,获得比较例7~比较例11的样品。[表5]图13是施加磁场的情况与不施加的情况下的相对于树脂量而言的初始磁导率的图表。如表5及图13所示,可知,在各树脂量下,在固化工序中施加磁场者的初始磁导率提高。图14是相对于树脂量而言的磁导率的变化率的图表。表5及图14中所示的“变化率”是各树脂量下的施加磁场的情况与不施加磁场的情况下的初始磁导率μ0的变化率,是以式(4)算出而获得的值。所述变化率表示施加磁场的效果的程度。变化率=μ0(h)/μ0(0)-1……(4)μ0(h):施加磁场的情况下的初始磁导率μ0(0):不施加磁场的情况下的初始磁导率如图14所示,树脂量越多,变化率越大。其原因在于,树脂量越多,利用所施加的磁场,磁性粉末越容易取向。可知在树脂量为3.3wt%~5.0wt%的范围内,变化率为10%以上,初始磁导率提高的效果高。(b)施加磁场的大小将树脂量分别设为3wt%、4wt%、5wt%,将施加磁场设为如表6所述,且将除了树脂量及施加磁场以外设为与所述(a)相同的工序,来制作电抗器的样品。然后,对于各样品,如所述“(1)测定项目”中所示般测定电感值。另外,根据所测定的电感值l0基于式(5),算出l0值变化率。将其结果示于表6中。[表6]l0值变化率=l0(h)/l0(0)-1……(5)l0(h):在固化工序中的各施加磁场h中所制作的电抗器的初始电感值l0(0):将固化工序中的施加磁场设为0而制作的电抗器的初始电感值图15是固化工序中的相对于施加磁场而言的l0值变化率的图表,是将表6图表化而成。如表6及图15所示,可知,存在树脂量越多,l0值变化率越大的倾向。l0值变化率在磁场小的区域容易上升,在磁场大的区域难以上升。即,在施加磁场为10ka/m前后,l0值提高开始饱和。表7是表示关于各树脂量的l值饱和增加率及l值饱和增加率的半值磁场的表。所谓l值饱和增加率,是将固化工序中的施加磁场设为14.56ka/m而制作的样品的l0值变化率,所谓l值饱和增加率的半值磁场,是获得l值饱和增加率的一半的l0值变化率的固化工序中的施加磁场的值。[表7]如表7、图15所示,可知,当树脂量为3wt%时,施加磁场为3.0ka/m以上,获得充分的l0值的提高效果。当树脂量为4wt%~5wt%时,施加磁场为2ka/m以上,获得充分的l0值的提高效果。根据这些情况,通过施加磁场设为2ka/m以上,可获得由固化中的磁场施加所带来的效果饱和时的一半以上的l0值变化率。(c)加压工序的有无在挤压复合磁性材料的情况、及不挤压的情况下,在树脂量3wt%~5wt%下,如下所述制作样品,针对所获得的初始电感值(l0)的差异来调查。(c-1)树脂量为3wt%的情况<有加压工序>将树脂量相对于磁性粉末而设为3wt%,以与所述(a)相同的工序来制作电抗器的样品。但,固化工序时的施加磁场设为如表8所示。<无加压工序>将树脂量相对于磁性粉末而设为3wt%,以与所述(a)相同的工序来制作电抗器的样品。但,不进行复合磁性材料的压制。即,将混合工序中获得的复合磁性材料填充于具有环形形状的空间的树脂制容器中,不压制而制作环形形状的成型体。在此期间,容器的温度保持为25℃。[表8]继而,对于所制作的样品,在有加压工序的情况、及无加压工序的情况下,分别算出初始电感值(l0)。另外,根据所算出的电感值(l0),基于式(5)来算出其变化率。将其结果示于表8及图16、图17中。图16是在硬化工序中的各施加磁场中来制作的电抗器的初始电感值的图表。如图16所示,可知,l0是在有加压工序的情况下高。认为其主要原因在于,通过将复合磁性材料压制,所述材料中的空隙被挤碎,空隙的数量减少,或者空隙的大小减小,由此,芯的表观密度提高,结果为初始磁导率提高。图17是表示在固化工序中的各施加磁场中制作的电抗器的初始电感值的变化率的图表。如图17所示,可知,在固化工序中的施加磁场低至5ka/m左右的情况下,在加压工序的有无方面未看到差异,但若磁场高于此,则有加压工序的情况下的l0的变化率升高。尤其可知,若达到9.27ka/m以上,则由加压工序引起的效果显著出现。(c-2)树脂量为4wt%的情况在有加压工序的情况及无加压工序的情况下制作样品的工序除了将树脂量设为4wt%以外,与所述(c-1)树脂量为3wt%的情况相同。另外,以与所述(c-1)相同的方式算出初始电感值(l0)。根据所算出的电感值(l0),基于式(5)来算出其变化率。将其结果示于表9及图18、图19中。[表9]图18是在固化工序中的各施加磁场中制作的电抗器的初始电感值的图表。如图18所示,可知,有加压工序的情况下的l0高。认为其主要原因在于,通过将复合磁性材料压制,所述材料中的空隙被挤碎,空隙的数量减少,或者空隙的大小减小,由此,芯的表观密度提高,结果为初始磁导率提高。图19是表示在固化工序中的各施加磁场中制作的电抗器的初始电感值的变化率的图表。如图19所示,可知,在l0的变化率的方面,也是有加压工序的情况下的变化率升高。(c-3)树脂量为5wt%的情况在有加压工序的情况及无加压工序的情况下制作样品的工序除了将树脂量设为5wt%以外,与所述(c-1)树脂量为3wt%的情况相同。另外,以与所述(c-1)相同的方式算出初始电感值(l0)。根据所算出的电感值(l0),基于式(5)来算出其变化率。将其结果示于表10及图20、图21中。[表10]图20是在固化工序中的各施加磁场中制作的电抗器的初始电感值的图表。图21是表示在固化工序中的各施加磁场中制作的电抗器的初始电感值的变化率的图表。如图20、图21所示,可知,初始电感值及其变化率均为与无加压工序的情况相比,在有加压工序的情况下升高。但其差小。认为其与如下效果抵消,即,通过树脂量增多,在复合磁性材料中所占的树脂的比例提高,进行加压而表观密度提高,由此带来的初始磁导率提高的效果。如图21所示,可知,固化工序中的施加磁场越高,与无加压工序的情况相比,l0的变化率在有加压工序的情况下越高。认为其主要原因在于,通过包含大量的树脂量,利用所施加的磁场,磁性粉末的取向性容易一致。(d)树脂的粘度测定对本实施例中使用的树脂的粘度进行说明。本实施例中使用的树脂的粘度是通过如下所述,测定载置于复合磁性材料上的砝码的沉入深度来作为树脂的粘度。即,首先,将树脂的添加量设为表11所示的条件,以与所述(a)的混合工序相同的方式制作复合磁性材料。继而,将所获得的复合磁性材料,以厚度成为3mm的方式投入直径为5mm的铝制容器中,在所述复合磁性材料上的中央载置jis标准的10g砝码。接着,载置砝码后经过10秒,然后去除砝码,测定由砝码的重量所形成的复合磁性材料的凹坑的深度。将其结果示于表11中。[表11]树脂量[wt%]深度[mm]30.26440.48950.558如表11所示,可知,树脂的添加量越多,凹坑的深度越深,复合磁性材料的粘性低,砝码容易沉入。[4-3.实施例iii]以下,参照表12~表14及图23,对本发明的实施例iii进行说明。<树脂(关于加热减量)>准备加热减量不同的4种树脂a~树脂d,使用树脂a~树脂d来制作成为样品的试验片,进行各树脂的加热减量的测定。树脂的加热减量是利用以下方法来测定。树脂的加热减量根据样品的尺寸而不同,因此进行比较的树脂的样品的尺寸必须统一。本实施例中,使用“直径40×高度10(mm)”的圆柱样品来测量树脂a~树脂d的加热减量。(1)加热减量的测定方法(a)试验片的准备首先,准备具有既定尺寸的内径的模具或容器。本实施例中,将既定尺寸设为具有“直径40×高度10(mm)”的内径的模具。将成为树脂a~树脂d的材料的成形材料投入模具内部,将模具加热至150℃。通过所施加的热,成形材料熔解,然后发生化学反应,根据模具的形状而固化。样品制作时的树脂a~树脂d的加热时间设为4小时。(b)加热前的质量测定将固化的树脂a~树脂d从模具中取出,作为试验片a~试验片d。测量所述试验片a~试验片d的质量至1mg。将所述值设为m0。(c)高温放置试验将试验片a~试验片d加热至220℃。加热时间设为20小时或40小时。(d)加热后的质量测定将经过既定时间的试验片a~试验片d取出,散热后,测量质量至1mg。将所述值设为m1。(e)加热减量的计算利用以下的式子来计算加热减量。(m0-m1)÷m0×100=加热减量(%)[表12]表12是表示将树脂a~树脂d在220℃的环境下实施20小时或40小时的高温放置试验时的加热减量的图表。如表12所示,树脂a的曝露20小时之时的加热减量为0.09%,曝露40小时之时的加热减量为0.12%,树脂b的曝露20小时之时的加热减量为0.07%,曝露40小时之时的加热减量为0.08%,树脂c的曝露20小时之时的加热减量为0.05%,曝露40小时之时的加热减量为0.05%,树脂d的曝露20小时之时的加热减量为0.08%,曝露40小时之时的加热减量为0.10%。[第一特性比较(由加热减量的差异所引起的对铁损的影响的比较)]第一特性比较中,将使用加热减量不同的树脂a~树脂d来制作的电抗器的特性进行比较。(2)测定项目测定项目为铁损。对于所制作的各芯的样品,利用φ1.2mm的铜线,实施1次卷线40圈、2次卷线3圈的卷线来制作电抗器。各芯的样品的形状设为外径为35mm、内径为20mm、高度为11mm的环形形状。另外,以下述的条件来算出所制作的电抗器的铁损。<铁损>铁损的测定条件设为频率20khz、最大磁通密度bm=30mt。铁损是使用作为磁性测量机器的bh分析仪(岩通计测股份有限公司:sy-8232)来算出。所述计算是通过根据铁损的频率曲线,以下述(1)式~(3)式,利用最小平方法来算出磁滞损耗系数、涡流损耗系数而进行。pcv=kh×f+ke×f2……(1)phv=kh×f……(2)pev=ke×f2……(3)pcv:铁损kh:磁滞损耗系数ke:涡流损耗系数f:频率phv:磁滞损耗pev:涡流损耗此外,本实施例中,各粉末的平均粒径及圆形度是使用下述装置而采取3000个的平均值,在玻璃基板上分散粉末,利用显微镜来拍摄粉末照片,从图像中自动测定每一个。公司名:马尔文(malvern)装置名:粒度粒形分析仪(morphologi)g3s比表面积是利用bet法来测定。(3)样品的制作方法芯的样品是使用平均粒径为123μm的fe6.5si来作为第一磁性粉末。继而,准备平均粒径为5.1μm的fe6.5si来作为第二磁性粉末。然后,将第一磁性粉末与第二磁性粉末以重量比率70:30的比例加以混合,获得平均粒径不同的两种磁性粉末的混合物。然后,在铝杯中加入所述磁性粉末,对所述磁性粉末添加树脂a~树脂d,使用刮刀来手动混合2分钟。由此,获得作为磁性粉末与树脂的混合物的复合磁性材料。继而,将混合工序中获得的复合磁性材料填充于具有环形形状的空间的树脂制容器,使用油压机,将容器内的复合磁性材料以600n的压制压(表面压力9.4kg/cm2)挤压10秒,来制作环形形状的成型体。在所述挤压期间,容器的温度保持为25℃。然后,将所述成型体在大气中,在85℃下干燥2小时,然后在120℃下干燥1小时,进而在150℃下干燥4小时而使树脂固化,制作成为样品的环形芯,获得使用树脂a的样品(比较例12)、使用树脂b的样品(实施例17)、使用树脂c的样品(实施例18)、使用树脂d的样品(实施例19)。然后,对于所获得的环形芯,利用所述铜线,实施1次卷线40圈、2次卷线3圈的卷线而制作成为基础的电抗器。(4)耐热试验继而,使用实施例17~实施例19及比较例12的样品来进行高温放置试验。高温放置试验是将实施例17~实施例19以及比较例12的样品在155℃的环境下曝露24小时~1000小时,测定其后的铁损pcv。[表13]pcv的变化率(%)表13是表示对实施例17~实施例19及比较例12的样品实施高温放置试验时的铁损(pcv)的变化率的表。所谓铁损(pcv)的变化率,是设为试验开始时的铁损(pcv0)及经过既定时间后的铁损(pcv1),利用以下的式子来算出。(pcv1-pcv0)÷pcv0×100=pcv的变化率(%)图23是基于表13来制作的图表。图23的纵轴表示铁损(pcv)的变化率,横轴表示高温放置试验中的经过时间。如图23所示,若将实施例17~实施例19及比较例12的样品曝露于155℃,则从试验开始起至试验开始后24小时为止之间,在所有样品中,铁损(pcv)的变化率大幅度上升。实施例17~实施例19及比较例12的样品的从试验开始起经过24小时之时的铁损(pcv)的变化率为6.3%~9.3%。这是无论树脂的加热减量如何都会发生的现象,通过将树脂加热而再次使树脂固化,此时产生的应力对(pcv)造成影响。从试验开始起至试验开始后400小时为止之间,在所有样品中,铁损(pcv)的变化率未大幅度变化。然而,在试验开始后经过400小时的时刻,比较例12的样品(树脂a)的铁损(pcv)的变化率变大。另一方面,在试验开始后经过400小时的时刻,实施例17~实施例19的样品(树脂b~树脂d)的铁损(pcv)的变化率并无大的变化。其原因在于,比较例12的样品中所含的树脂由于热而分解或消失,磁性粉末彼此接触,涡流损耗pev上升,与此相对,实施例17~实施例19的样品中所含的树脂未产生分解或消失。进而,若试验开始后经过500小时,则实施例19的样品(树脂d)的铁损(pcv)的变化率(%)变大。认为其原因在于,与40小时的加热减量为0.08%的树脂b、或40小时的加热减量为0.05%的树脂相比较,在40小时的加热减量稍高的树脂d中,由于热而使树脂开始分解或消失。另一方面,使用在155℃下加热40小时之时的加热减量为0.08%以下的树脂b、树脂c的实施例17及实施例18的样品中,即便从试验开始起经过1000小时,铁损(pcv)的变化率(%)也未出现大的变化。其原因在于,实施例17及实施例18的样品中所含的树脂不会由于热而分解或消失,确保磁性粉末彼此的绝缘,因此抑制涡流损耗pev上升。根据以上,通过使用在220℃的环境中曝露40小时之时的加热减量为0.1%以下的树脂,即便在将磁芯在155℃的环境中曝露超过400小时的情况下也能够抑制铁损(pcv)的变化。进而,通过使用在220℃的环境中曝露40小时之时的加热减量为0.08%以下的树脂,即便在将磁芯在155℃的环境中曝露超过1000小时的情况下也能够抑制铁损(pcv)的变化。(关于详细的铁损pcv的变化)铁损pcv为磁滞损耗phv与涡流损耗pev的合计的值。在表12及图23中的高温放置试验中,作为铁损pcv上升的原因,列举涡流损耗pev。以下,列举使用树脂a的比较例12及实施例18的样品为例,对pcv的变化率(%)的上升、与磁滞损耗phv及涡流损耗pev的变化量进行验证。表14是表示使用树脂a的比较例12的样品、以及使用树脂c的实施例18的样品的从试验开始起至试验开始后1000小时为止的铁损pcv、磁滞损耗phv、以及涡流损耗pev的值的表。[表14]如表14所示,比较例12的样品中,从试验开始起试验开始后经过400小时后的涡流损耗pev为6.2,与此相对,从试验开始起试验开始后经过1000小时后的涡流损耗pev成为9.0。此时的涡流损耗pev的变化率根据(9.0-6.2)/6.2×100而为45%。另一方面,从试验开始起试验开始后经过400小时后的磁滞损耗phv为21.3,与此相对,从试验开始起试验开始后经过1000小时后的磁滞损耗phv成为23.1。可知此时的磁滞损耗phv变化率根据(23.1-21.3)/21.3×100,约为8.5%。即,在表14及图23中可知,在pcv的变化率大幅度变化的情况下,涡流损耗pev大幅度变化。另一方面,实施例18的样品中,从试验开始起试验开始后经过400小时后的涡流损耗pev为6.0,与此相对,从试验开始起试验开始后经过1000小时后的涡流损耗pev成为6.1。涡流损耗pev的变化率根据(6.1-6.0)/6.0×100而为1.7%。另一方面,从试验开始起试验开始后经过400小时后的磁滞损耗phv为20.1,与此相对,从试验开始起试验开始后经过1000小时后的磁滞损耗phv成为20.2。磁滞损耗phv的变化率根据(20.2-20.1)/20.1×100而为约0.5%。表14中,实施例18的样品中,涡流损耗pev、及磁滞损耗phv均未大幅度变化。因此,表14及图23中也可知,铁损pcv的变化率(%)也少。(结论)根据以上可知,由包含在220℃下加热40小时之时的加热减量为0.1%以下的树脂的软磁性复合材料来制作的磁芯即便在155℃下长时间使用,铁损pcv的变化率(%)也可抑制为小。其原因在于,在220℃下加热40小时之时的加热减量小的树脂即便在高温的环境下长时间曝露,树脂也不会分解或消失,因此能够抑制磁性粉末彼此的接触,由此可实现低涡流损耗。[5.其他实施方式]本发明并不限定于所述实施方式,在实施阶段,能够在不脱离其要旨的范围内将构成要素变形而具体化。另外,通过所述实施方式中所公开的多个构成要素的适当组合,能够形成各种发明。例如,也可从实施方式所示的全部构成要素中削除若干构成要素。进而,也可将不同的实施方式中的构成要素适当组合。例如,实施方式ii中,作为在电抗器中设置线圈的方法,已对在成型工序中将线圈加入容器中而埋设于复合磁性材料的方法加以说明,但也可采用包括如下卷绕工序的方法,即,预先成形包含复合磁性材料的既定形状的成型体,在所述成型体上卷绕构成线圈的导线。另外,实施方式iii中,作为在电抗器中设置线圈的方法,已对在成型工序中将线圈加入容器中而埋设于复合磁性材料的方法加以说明,但也可采用包括如下卷绕工序的方法,即,预先成型包含复合磁性材料的既定形状的成型体,在所述成型体上卷绕构成线圈的导线。另外,磁芯是通过在本实施方式iii中,将预先混合有软磁性粉末及树脂的软磁性复合材料流入容器中来制作,但也可利用以下方法来制作。在容器内填充第一粉末与第二粉末的混合粉末后,使容器整体振动,由此提高容器内的混合粉末的密度。然后,对于通过振动而提高密度的混合粉末渗透树脂,利用根据树脂种类的固化法而固化。作为振动的方法,也可为如下方法:对容器整体,利用马达或凸轮等而使其上下或/及前后左右地振动,或轻敲,或者利用锤状的构件轻轻敲击容器。也可利用超声波振子使容器整体振动。进而,本实施方式iii中,在成型工序与固化工序之间,包含利用挤压构件来对容易进入的复合磁性材料进行挤压的加压工序,但也可省略加压工序。根据所使用的磁性粉末或树脂的种类、或成型工序的方法,即便省略加压工序,也可将磁特性优异的磁芯成型。在此情况下,能够出于减少工序数量或成本的目的而省略加压工序。当前第1页12