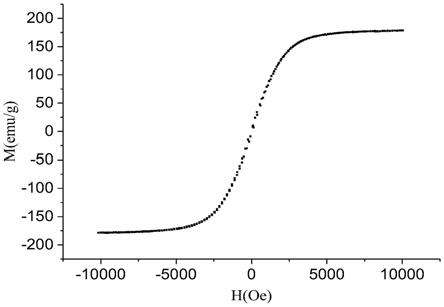
1.本发明属于磁性材料技术领域,具体涉及一种致密软磁复合铁芯材料的制备方法及软磁复合材料。
背景技术:2.软磁粉芯作为电感滤波器、扼流线圈等被广泛应用于电感器、变流器等电子电气元件。随着进入5g高频时代,通讯、计算机以及新能源汽车电子电气器件不断追求小型化、高效化和高频化。这要求软磁粉芯材料具有更高的磁导率以及更低的磁损耗,尤其是高频下具有高磁导率和低损耗。铁氧体和金属合金是构成软磁粉芯最重要的两类软磁材料。软磁铁氧体最大的优点是电阻率高,但其饱和磁化强度一般低于0.5t,这限制了其应用上限,也不符合小型化、高效化的发展趋势。金属软磁材料的饱和磁化强度高达2.2t,但其电阻率(10
‑6~10
‑4ω
·
m)比软磁铁氧体(1~105ω
·
m)低至少4个数量级,成为其在高频领域中应用的最大障碍。目前有各种方法尝试将金属软磁进行绝缘包覆,以得到高磁导率、高饱和磁感应强度和高电阻率的软磁复合材料,如利用氧化物或有机物进行绝缘包覆、钝化或氧化处理进行绝缘包覆等,然而包覆后由于磁稀释作用导致磁体软磁性能下降。为减小这种磁稀释效应的影响,可利用软磁铁氧体粉末进行绝缘包覆。目前有利用湿化学法制备铁氧体颗粒进行绝缘包覆,也有利用机械混合进行绝缘包覆,但如何进行均匀包覆和形成致密高强度块体材料仍非常困难。
技术实现要素:3.有鉴于此,本发明提供一种致密软磁复合铁芯材料的制备方法,可制备出金属软磁/铁氧体复合致密铁芯材料。
4.其技术方案如下:
5.一种致密软磁复合铁芯材料的制备方法,其关键在于按照以下步骤进行:步骤一、分别准备金属软磁粉、软磁铁氧体粉和玻璃助烧剂粉;
6.步骤二、将所述金属软磁粉、软磁铁氧体粉和玻璃助烧剂粉混合得到复混粉末;
7.步骤三、将所述复混粉末进行真空热压处理,得到软磁复合材料;
8.所述金属软磁粉为feco粉、feni粉和fesial粉中的一种;
9.所述软磁铁氧体粉为镍锌铁氧体粉或锰锌铁氧体粉。
10.作为优选,以质量分数计,所述复混粉末中的所述玻璃助烧剂粉含量为0.2
‑
5%,所述软磁铁氧体粉含量为0.5
‑
10%,其余为所述金属软磁粉。
11.作为优选,上述步骤二的具体过程为,先将所述金属软磁粉、软磁铁氧体粉和玻璃助烧剂粉进行球磨,同时加入正硅酸乙酯,无水乙醇为保护介质,接着真空干燥,再在惰性气氛下进一步研磨,得到所述复混粉末。
12.作为优选,上述步骤二中,正硅酸乙酯用量为所述金属软磁粉、软磁铁氧体粉和玻璃助烧剂粉的总质量的0.5
‑
2.5wt.%。
13.作为优选,上述步骤二中,球料比为10:1,球磨转速为100
‑
150rpm,球磨时间6
‑
10h。
14.作为优选,上述步骤三中,将所述复混粉末装入压制模具,将该压制模具放入热压炉中进行真空热压处理;
15.所述热压处理分两段进行:先在600
‑
650℃、300
‑
500mpa条件下保温1
‑
5min,然后降温至450
‑
550℃,于30
‑
50mpa条件下保温5
‑
10min。
16.作为优选,上述步骤一中,取粒径为10
‑
100μm的所述金属软磁粉粉末,进行扁平化处理后备用,所述扁平化处理为湿法球磨。
17.作为优选,上述步骤一中,所述湿法球磨的球料比为5:1
‑
20:1,球磨转速为50
‑
400rpm,球磨时间为4
‑
40h,球磨介质选自无水乙醇、异丙醇、丙三醇或正庚烷。
18.作为优选,上述玻璃助烧剂粉选自如下成份中的一种48.7li2o
‑
36.4b2o3‑
14.9sio2(lbs)、20li2o
‑
30zno
‑
50b2o3(lzb)、30li2o
‑
10mgo
‑
60b2o3(lmb)、52.45li2o
‑
31.06b2o3‑
11.99sio2‑
2.25cao
‑
2.25al2o3(lbsca)。
19.本发明的目的之二在于提供一种软磁复合材料。其技术方案如下:
20.一种软磁复合材料,其关键在于采用如上任意一项所述的制备方法制得。
附图说明
21.图1为实施例1中金属软磁粉经球磨处理后的粉末颗粒形貌;
22.图2为实施例1制得样品的静态磁滞回线图;
23.图3为实施例3中金属软磁粉经球磨处理后的粉末颗粒形貌;
24.图4为实施例3制得样品的静态磁滞回线图。
具体实施方式
25.以下结合实施例和附图对本发明作进一步说明。
26.一种致密软磁复合铁芯材料的制备方法,按照以下步骤进行:
27.步骤一、分别准备金属软磁粉、软磁铁氧体粉和玻璃助烧剂粉;
28.所述金属软磁粉为feco粉、feni粉和fesial粉中的一种。取粒径为10
‑
100μm的经雾化制得的金属软磁粉,进行扁平化处理,例如可以采用湿法球磨,湿法球磨的球料比为5:1
‑
20:1,球磨转速为50
‑
400rpm,球磨时间为4
‑
40h,球磨介质选自无水乙醇、异丙醇、丙三醇或正庚烷。
29.所述软磁铁氧体粉为镍锌铁氧体粉或锰锌铁氧体粉的纳米颗粒或微米颗粒。
30.镍锌铁氧体粉的制备过程为:按照镍锌铁氧体化合物中金属元素的原子比在去离子水中加入适量fecl3·
6h2o、zncl2·
6h2o、nicl2·
6h2o,以及分散剂,并搅拌30min以使其溶解。分散剂可以是聚乙二醇,其用量为金属化合物总质量的3wt.%。随后在搅拌的同时以4ml/min的速度向混合液中加入一定浓度的碱溶液作为沉淀剂,使溶液ph值保持在9.5
‑
10,碱溶液可以是naoh溶液。反应完全后,放置8
‑
10h,再利用去离子水清洗,并在干燥箱中干燥24h。随后,将样品研磨,并在管式炉中进行烧结处理,温度为600
‑
800℃,保温1
‑
2h,从而得到镍锌铁氧体粉末。
31.锰锌铁氧体粉的制备同镍锌铁氧体粉,具体过程为:按照锰锌铁氧体化合物中金
属元素的原子比在去离子水中加入适量fecl3·
6h2o、zncl2·
6h2o、mncl2·
4h2o,以及3wt.%聚乙二醇,并搅拌30min,随后在搅拌的同时以4ml/min的速度向混合液中加入一定浓度的naoh溶液,使溶液ph值保持在9.5
‑
10。反应完全后,放置8
‑
10h,再利用去离子水清洗,并在干燥箱中干燥24h。随后,将样品研磨,并在管式炉中进行烧结处理,温度为1100
‑
1200℃,保温1
‑
2h,从而得到锰锌铁氧体粉末。
32.所述玻璃助烧剂粉选自如下成份中的一种48.7li2o
‑
36.4b2o3‑
14.9sio2(lbs玻璃粉)、20li2o
‑
30zno
‑
50b2o3(lzb玻璃粉)、30li2o
‑
10mgo
‑
60b2o3(lmb玻璃粉)、52.45li2o
‑
31.06b2o3‑
11.99sio2‑
2.25cao
‑
2.25al2o3(lbsca玻璃粉),四种玻璃粉中各组份化合物的比例均为摩尔比。
33.根据上述四种玻璃粉的组成,初始原料选自li2co3、sio2、h3bo3,zno、(mgco3)4mg(oh)2·
5h2o、cao、al2o3。采用熔融法制备玻璃粉的过程为:分别按照四种玻璃粉的组份化合物的原子比称取原料,并用球磨机进行球磨处理,以无水乙醇为保护溶剂,球磨4
‑
6h。随后,将球磨后的浆料进行干燥,并加热至900
‑
950℃保温1h,随后进行水淬。将得到的玻璃碎片烘干,并经研磨和湿法球磨20
‑
40h以及干燥处理,得到试验所用玻璃粉末。
34.步骤二、将所述金属软磁粉、玻璃助烧剂粉和软磁铁氧体粉混合得到复混粉末;
35.以质量分数计,所述复混粉末中的所述玻璃助烧剂粉含量为0.2
‑
5%,所述软磁铁氧体粉含量为0.5
‑
10%,其余为所述金属软磁粉。
36.混合过程为:先按质量比取金属软磁粉、玻璃助烧剂粉和软磁铁氧体粉进行球磨,球料比为10:1,球磨转速为100
‑
150rpm,球磨时间6
‑
10h;同时加入正硅酸乙酯,无水乙醇为保护介质,正硅酸乙酯用量为所述金属软磁粉、玻璃助烧剂粉和软磁铁氧体粉的总质量的0.5
‑
2.5wt.%;接着真空干燥;再在手套箱中,加入硬脂酸锌,于惰性气氛下进一步研磨,把干燥结块的混合粉末粉化,得到所述复混粉末,硬脂酸锌的添加量为所述金属软磁粉、玻璃助烧剂粉和软磁铁氧体粉的总质量的0.3
‑
1wt.%。
37.步骤三、将所述复混粉末装入压制模具,将该压制模具放入热压炉中进行真空热压处理,热压处理分两段进行:先在600
‑
650℃、300
‑
500mpa条件下保温1
‑
5min,以使让磁体致密化,然后降温至450
‑
550℃,于30
‑
50mpa条件下保温5
‑
10min,以使助烧剂充分扩散,并释放部分应力。烧结后将样品在惰性气氛下于400
‑
550℃进行热处理,保温1
‑
4h,以进一步去除内应力,得到软磁复合材料。
38.几种典型软磁复合铁芯材料的详细制备过程如实施例1~3。
39.实施例1
40.步骤一、取金属软磁粉feco雾化粉末,feco雾化粉末中两种元素的质量比为1:1,粉末粒径为30
‑
50μm;其扁平化处理过程为,将10gfeco粉末放入球磨机中,并加入无水乙醇和磨球,球料比为10:1,球磨转速200rpm,时间20h,备用。图1为球磨后的粉末颗粒形貌。
41.按照mn
0.6
zn
0.4
fe2o4化合物中金属元素mn、zn和fe的原子比在去离子水中加入适量fecl3·
6h2o、zncl2·
6h2o、mncl2·
4h2o,以及3wt.%聚乙二醇,并搅拌30
‑
60min,随后在搅拌的同时以4ml/min的速度向混合液中加入一定浓度的naoh沉淀剂,使溶液ph值保持在9.5
‑
10。反应完全后,放置10h,再利用去离子水清洗,然后在干燥箱中干燥24h,温度为80℃。然后将样品研磨10min,并放入管式炉中进行烧结处理。烧结时采用氩气保护,温度1150℃,保温2h。冷却后得到锰锌铁氧体粉,备用。
42.采用熔融法制备lbsca玻璃粉。所用初始原料为li2co3、h3bo3、sio2、cao、al2o3。按照lbsca玻璃粉的组份化合物比例称取原料5g,并在球磨机中进行球磨处理,放入适量无水乙醇作为保护溶剂,球磨4h。随后,将球磨后的浆料进行干燥,并加热至950℃保温1h,随后进行水淬。将得到的玻璃碎片烘干,并经研磨和100目筛子过筛,收集粉末并放入球磨机中,并放入适量无水乙醇和磨球,球料比为10:1,球磨转速为350rpm,球磨时间为20h。随后收集样品,并进行干燥处理,得到玻璃助烧剂粉,备用。
43.步骤二、将经片状化处理的feco金属软磁粉末与lbsca、锰锌铁氧体粉末混合,其中lbsca质量占比为2%,锰锌铁氧体粉质量占比为6%。称取8g混合粉末,将混合粉末放入滚动球磨机中继续球磨,同时加入质量比为2%的正硅酸乙酯以及适量无水乙醇,球料比为10:1,球磨转速为150rpm,球磨时间6h。随后取出样品真空干燥,加入硬脂酸锌,硬脂酸锌的添加量为金属软磁粉、玻璃助烧剂粉和软磁铁氧体粉的总质量的0.3%,并在手套箱中进行进一步研磨,随后装入合金模具。
44.步骤三、将模具放入热压炉中进行真空热压处理,烧结温度为650℃,保温时间2min,压力300mpa;随后降温至450℃,保温5min,压力30mpa。待模具冷却,经脱模得到致密软磁复合块体。随后将样品在氮气气氛下热处理,450℃条件下保温2h,以进一步除去内应力。
45.由阿基米德法测得样品密度为7.95g/cm3,由振动样品磁强计测得样品饱和磁化强度为179.8emu/g,静态磁滞回线见图2。由软磁材料动态测量装置测量样品磁导率,发现其具有较好频率稳定性,在1khz时为56。
46.实施例2
47.步骤一、取金属软磁粉feco雾化粉末,feco雾化粉末中两种元素的质量比为1:1,粉末粒径为30
‑
50μm;其扁平化处理过程为,将10g的feco粉末放入球磨机中,并加入无水乙醇和磨球,球料比为15:1,球磨转速150rpm,时间8h,备用。
48.按照化合物ni
0.6
zn
0.4
fe2o4中ni、zn和fe的原子比在去离子水中加入适量fecl3·
6h2o、zncl2·
6h2o、nicl2·
6h2o,以及3wt.%聚乙二醇,并搅拌60min,,随后在搅拌的同时以4ml/min的速度向混合液中加入一定浓度的naoh沉淀剂,使溶液ph值保持在9.5
‑
10。反应完全后,放置10h,再利用去离子水反复清洗三次,然后在干燥箱中干燥24h,干燥温度为80℃。接着将样品研磨10min,并放入管式炉中进行烧结处理。烧结时采用氩气保护,温度800℃,保温1h。冷却后得到镍锌铁氧体粉末,备用。
49.采用熔融法制备48.7li2o
‑
36.4b2o3‑
14.9sio2(lbs)玻璃粉,其各成分的比例为原子比。所用初始原料为li2co3、h3bo3、sio2。按照相应比例称取原料5g,并在球磨机中进行球磨处理,放入适量无水乙醇作为保护溶剂,放入30g磨球,球磨转速350rpm,球磨6h。随后,将球磨后的浆料进行干燥,并加热至900℃保温1h,随后进行水淬。将得到的玻璃碎片烘干,并经研磨和100目筛子过筛,收集粉末并放入球磨机中,并放入适量无水乙醇和磨球,球料比为10:1,转速为350rpm,球磨时间为30h。随后收集样品,并进行干燥处理,得到玻璃助烧剂粉,备用。
50.步骤二、将经片状化处理的feco金属软磁粉末与lbs、镍锌铁氧体粉末混合,其中lbs质量占比为4%,镍锌铁氧体粉质量占比为8%。称取8g混合粉末,将混合粉末放入滚动球磨机中继续球磨,同时加入质量比为1.5%的正硅酸乙酯以及适量无水乙醇,球料比为
10:1,球磨转速为150rpm,球磨时间6h。随后取出样品真空干燥,加入硬脂酸锌,硬脂酸锌的添加量为金属软磁粉、玻璃助烧剂粉和软磁铁氧体粉的总质量的0.5%,并在手套箱中进行进一步研磨,随后装入合金模具。
51.步骤三、将模具放入热压炉中进行真空热压处理,烧结温度为600℃,保温时间1min,压力500mpa;随后降温至450℃,保温10min,压力30mpa。待模具冷却,经脱模得到致密软磁复合块体。随后将样品在氮气气氛下热处理,于500℃保温1h,随炉冷却。
52.测得其密度为7.72g/cm3,饱和磁化强度为170.3emu/g,磁导率随频率的增加具有较好频率稳定性。
53.实施例3
54.步骤一、取金属软磁粉fe85si9.5al5.5雾化粉末,fesial中各元素比例为质量比,粉末粒径10
‑
50μm。将fe85si9.5al5.5粉末进行扁平化处理,即湿法球磨,球料比12:1,转速50rpm,时间40h,球磨介质为无水乙醇。扁平化处理后的fe85si9.5al5.5粉末形貌见图3。
55.按照化合物mn
0.6
zn
0.4
fe2o4中mn、zn和fe的原子比在去离子水中加入适量fecl3·
6h2o、zncl2·
6h2o、mncl2·
4h2o,以及3wt.%聚乙二醇,并搅拌30
‑
60min,随后在搅拌的同时以4ml/min的速度向混合液中加入一定浓度的naoh沉淀剂,使溶液ph值保持在9.5
‑
10。反应完全后,放置10h,再利用去离子水清洗,然后在干燥箱中干燥24h,温度为80℃。接着将样品研磨10min,并放入管式炉中进行烧结处理。烧结时采用氩气保护,温度1150℃,保温2h。冷却后得到锰锌铁氧体粉末。
56.采用熔融法制备52.45li2o
‑
31.06b2o3‑
11.99sio2‑
2.25cao
‑
2.25al2o3(lbsca)玻璃粉,其各成分的比例为原子比。所用初始原料为li2co3、h3bo3、sio2、cao、al2o3。按照四种玻璃的相应比例称取原料5g,并在球磨机中进行球磨处理,放入适量无水乙醇作为保护溶剂,球磨4h。随后,将球磨后的浆料进行干燥,并加热至950℃保温1h,随后进行水淬。将得到的玻璃碎片烘干,并经研磨和100目筛子过筛,收集粉末并放入球磨机中,并放入适量无水乙醇和磨球,球料比为10:1,转速为350rpm,球磨时间为20h。随后收集样品,并进行干燥处理,得到玻璃助烧剂粉,备用。
57.步骤二、将经片状化处理的fesial金属软磁粉末与lbsca、锰锌铁氧体粉末混合,其中lbsca质量占比为2.5%,锰锌铁氧体粉末质量占比为5%。称取8g混合粉末,将混合粉末放入滚动球磨机中继续球磨,同时加入质量比为2%的正硅酸乙酯以及适量无水乙醇,球料比为10:1,球磨转速为150rpm,球磨时间6h。随后取出样品真空干燥,加入硬脂酸锌,硬脂酸锌的添加量为金属软磁粉、玻璃助烧剂粉和软磁铁氧体粉的总质量的0.5%,并在手套箱中进行进一步研磨,随后装入合金模具。
58.步骤三、将模具放入热压炉中进行真空热压处理,烧结温度为650℃,保温时间1min,压力500mpa;随后降温至450℃,保温10min,压力30mpa。待模具冷却,经脱模得到致密软磁复合块体。随后将样品在氮气气氛下热处理,500℃条件下保温1h,随炉冷却。
59.测得其密度为6.05g/cm3,饱和磁化强度为78.2emu/g,静态磁滞回线图见图4。测得样品磁导率为84.6(100khz),磁损耗为51.6w/kg(f=100khz,bm=100mt)。
60.对照例1
61.采用如实施例2中的材料和工艺方法,不同之处在于,不加入玻璃助烧剂lbs,仅使用经片状化处理的feco金属软磁粉末与镍锌铁氧体粉末制备磁体。经检测,制得样品的磁
体密度约为6.5g/cm3,并且易粉化碎裂,无法准确测得磁性能。
62.本发明的方法具有如下优点:(1)使用玻璃助烧剂,其作用在于,由于其熔点低,在烧结过程中呈液态,起到润滑作用,有助于致密化和混合粉末的均匀分布,增加密度,同时也可增大电阻,并有利于提高机械强度;(2)步骤一中,金属软磁粉进行扁平化处理,可以提高粉末电阻率,增加高频性能;(3)将金属软磁粉、软磁铁氧体粉和玻璃助烧剂粉进行球磨过程中,加入正硅酸乙酯,能够对原料粉末进行包覆,经混合均匀和烧结,覆盖在粉末表面,起到提高电阻率的作用。
63.与现有技术相比,本发明的有益效果:能够制得密度高、饱和磁化强度高同时磁导率高、磁损耗低的复合铁芯材料,具有较好的应用前景。
64.最后需要说明的是,上述描述仅仅为本发明的优选实施例,本领域的普通技术人员在本发明的启示下,在不违背本发明宗旨及权利要求的前提下,可以做出多种类似的表示,这样的变换均落入本发明的保护范围之内。