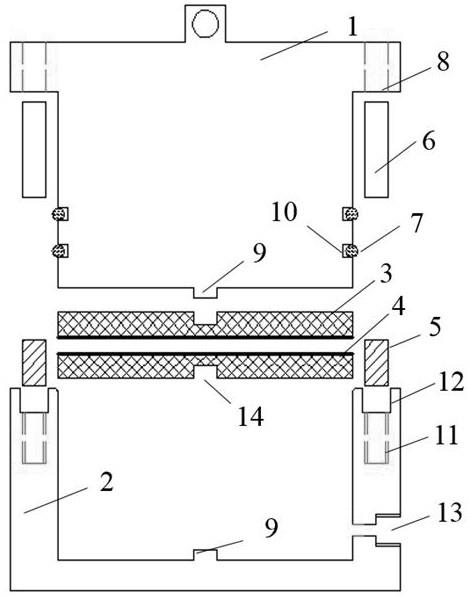
1.本发明属于柔性电子技术领域,具体涉及一种夹芯式薄膜传感器制备过程中所需的真空环境压合装置。
背景技术:2.以压电薄膜为敏感元件的薄膜式压力传感器具有频响宽、动态压力测试范围大、力电转换系数高、柔性和生物界面相容性好等优点,被广泛应用于结构表面、材料内部界面、生物体体表等位置的冲击压力测量。目前压电薄膜类压力计的制作主要采用夹芯式结构,即将具有压电性能的压电薄膜元件采用前后两片柔性电极进行压合封装,柔性电极一般采用柔性印刷电路技术设计制作。当前电极与压电膜的电性连接主要通过导电性粘结剂固定连接、接触式自由连接、金属箔搭接并采用粘结剂固定等方式,在上述电极与压电薄膜元件之间的连接方式中,采用导电或非导电粘结剂固定连接的方式都会影响压电薄膜在面外载荷作用下的变形形式,使得压电薄膜并非处于标定和计算所采用的一维应力状态,从而影响压力计灵敏度的稳定性。采用金属电极直接搭接压电薄膜元件两侧实现电性连接的方式对压电膜元件的应力状态影响较小,同时将压电膜元件周围区域采用相同材质的薄膜垫平从而形成的内部厚度一致、压电膜元件变形自由的夹芯式压力传感器能够具有更为稳定的力电灵敏度响应。然而,目前的薄膜型压力传感器的制作过程中,电极和压电膜元件搭接区域及其内部预设间隙中的气压对压力计测试精度的影响并未考虑。内部间隙残留气压的存在可能导致传感器内压电元件松动、电性连接不稳定,在测量与大气压同一数量级的低压力时更会对测试结果产生较大的干扰。夹芯式压电薄膜型传感器一般由含有压电元件的芯层和含有电极的两侧封装层构成,压制过程复杂,有必要在压力传感器压制过程中维持真空环境,从而提高低压力测量下的电性连接质量和测量精度,同时便于批量化制作个体性差异小的传感器。
技术实现要素:3.本发明为了克服传统夹芯式压电薄膜型传感器压制作过程中内部残留气体对测量精度的影响问题,提供一种可在真空环境下批量制作夹芯式薄膜型传感器的压合装置及方法。
4.本发明采取以下技术方案:一种夹芯式薄膜传感器制备过程中所需的真空环境压合装置,包括压头、套筒、上转模板以及下转模板,压头下部为圆柱体,圆柱体上加工有密封槽,密封槽安装密封圈实现压头和套筒间的密封,所述的套筒为上端开口,下端闭口的空心圆柱体结构,套筒的内径与压头的下部圆柱体直径一致,压头与套筒之间设置有上转模板和下转模板,上转模板的下表面以及下转模板的上表面为转模板正面,用以临时安装、定位批量电极并将其转移至真空密封舱内;套筒侧面开设有阀门孔连接内外环境,所述的阀门孔外侧直径大于内侧直径,阀门孔内侧孔中心与套筒内安装的下转模板的正面平齐。
5.套筒的筒壁上端面周向均匀开设有与压头上部法兰体外圈相同尺寸和数量的筒
壁定位孔,同时筒壁上端面开设有一圈用于放置承压泡沫的内凹槽,所述的压头靠近边缘位置设置有法兰定位孔,法兰定位孔内设置法兰定位杆,法兰定位杆与套筒筒壁定位孔一一对应。
6.压头上部为法兰体结构,下部为直径略小的圆柱体结构。
7.压头下部的圆柱体下表面中心设置有矩形定位凸台,所述的上转模板背面开设有定位凹孔。
8.套筒内底面中心设置矩形定位凸台,下转模板的背面开设有与其对应的定位凹孔。
9.上转模板和下转模板均为圆形薄板与压头下部圆柱体直径、套筒内径一致,材质为耐压且表面平整度较高的有机玻璃板或聚碳酸酯板,表面粗糙度不大于10nm,转模板的正表面通过激光切割或丝印技术标记若干传感器电极安装工位,用以精确定位传感器的电极,上、下转模板正面电极工位对称设置,合模后上、下工位准确重合。
10.一种夹芯式薄膜传感器制备过程中所需的真空环境压合装置的使用方法,包括以下步骤,s1~在下转模板正面擦拭一层真空脂作为临时固定传感器柔性电极的粘结剂,提供夹芯式薄膜型传感器所用的柔性电极,按照下转模板正面标记的传感器位置依次安装柔性电极,在柔性电极上安装双面覆胶且开设有嵌入孔的绝缘垫平层,将裁剪好的压电膜元件嵌入垫平芯层的嵌入孔内,按照转模板背部定位凹孔的方位将下转模板安装入套筒内部;s2~在上转模板正面擦拭一层真空脂作为临时固定传感器上层柔性电极的粘合剂,按照转模板正面标记的传感器位置依次摆放柔性电极,然后在转模板的背面均匀擦拭一层很薄的真空脂,作为临时粘接上转模板和压头的粘合剂,将上转模板按照背部开设的定位凹孔与压头进行装配贴合;s3~在压头密封槽和密封圈部位均匀涂覆一层真空脂以润滑和密封,采用圆柱形定位销将压头与套筒上下对齐后压入。通过计算适当选取承压泡沫的尺寸、屈服强度和平台应力,在套筒筒壁上端面凹槽内无定位销的地方放置承压泡沫条,将压头缓慢下压,直至压头法兰下表面与泡沫接触,此时上转模板和下转模板间预留有一定高度的间隙,该间隙高度小于承压泡沫高度的二分之一;s4~通过套筒筒壁的阀门孔对上下转模板之间形成的密封舱进行抽真空处理,此时由于套筒内密封舱负压导致的压头下压力由周边承压泡沫条承载,通过泡沫强度和平台应力使之在无额外压力作用时,未达到压溃变形的泡沫始终处于弹性小变形阶段、能够完全支撑压头上作用的大气压载荷,当达到真空环境时停止抽气并关闭阀门保持套筒内部的负压环境;s5~对压头施加载荷,直至承压泡沫条开始进入应力平台变形阶段(压溃大变形),调整加载速度为1mm/min将压头继续缓慢下压,直至上下转模板的正面完全贴合,将压制压力维持一定时间,并保持舱内真空环境,在该过程中承压泡沫被平稳压缩;s6~压制结束后,打开阀门开关,平衡套筒内外压力;将套筒底部固定在工作台上,通过压头上端拉环向上提拉压头,同时通过阀门孔向套筒内部加高压气体,使筒内气压约为150kpa时即可顺利推出压头,分离上下转模板即可获得真空环境下批量压合制成的夹
芯式薄膜传感器。
11.步骤s1中,夹芯式薄膜型传感器柔性电极采用柔性印刷电路技术制作,聚酰亚胺薄膜为基底,厚度28μm,上部采用磁控溅射印刷金属电极及其引线电路厚度12μm;压电膜元件采用极化后的pvdf压电薄膜元件,厚度52μm,直径6mm,绝缘垫平层采用双面覆胶的未极化的pvdf压电薄膜,厚52μm,双面覆胶后的厚度约74μm,上面开设6.1mm直径嵌入孔,pvdf压电膜元件可嵌入其中。
12.承压泡沫条的平台应力为σ,宽a、高b,总布设长度为l,套筒内部直径d,大气压力为p0,则,即承压泡沫在稳定压溃阶段提供的载荷不低于压头因套筒内负压产生的大气压力的2倍,设置密封舱初始高度即上下转模板间距不大于b/2;设压力机最终压制载荷为f,转模板上传感器个数为n,单个传感器受压面积为as,则单个传感器的压制应力为。
13.与现有技术相比,本发明具有以下有益效果:1.本发明提供的真空环境压合装置能够保证夹芯式薄膜型传感器双侧电极和芯层压合时处于真空状态,有效保证压电薄膜元件和两侧电路的电性连接质量,并消除低应力(与大气压同数量级)测量时压力计结构刚度和内部密封气体对压力信号的干扰。
14.2.本发明提供的压合装置在上下转模板合模之前压头所承受的负压载荷通过具有较大孔隙率的泡沫材料承担。在达到真空环境后,仅需直接对压头施加额外压力即可平稳地将压头压入套筒内实现转模板的合模,由于承压泡沫具有较长的压溃应力稳定区(即应力平台变形阶段),合模过程中泡沫提供的反馈载荷基本恒定,可通过优选承压泡沫的强度和平台应力精确控制传感器的压制压力。
15.3.本发明中采用尺寸和规格完全一致的上下转模板分别转移传感器的上部电极层和芯层/下部电极组合层,并采用压头法兰定位杆、内部定位凸台自上而下地将转模板上的每个传感器进行定位,可精确保证批量制作时各个传感器的上电极
‑
芯层
‑
下电极三层装置上下对齐压合。
16.4.本发明提供的压合装置在压制结束后,可通过压头拉环和套筒阀门反向充气压的方式进行退模,操作简单。
17.5.本发明提供的压制装置和方法便于传感器的批量制作,可精确控制传感器的压合工艺和压力等因素可控可调,能够减小压力计的个体差异性。
附图说明
18.图1是夹芯式薄膜型传感器真空环境压合装置的部分剖视图;图2是本发明提供的传感器真空环境压合方法流程图;图中1
‑
压头,2
‑
套筒,3
‑
上转模板,4
‑
下转模板,5
‑
承压泡沫条,6
‑
法兰定位杆,7
‑
密封圈,8
‑
法兰定位孔,9
‑
定位凸台,10
‑
密封槽,11
‑
筒壁定位孔,12
‑
内凹槽,13
‑
阀门孔,14
‑
定位凹孔。
具体实施方式
19.下面结合附图和实施例对本发明做进一步的详细说明。
20.如附图1所示,本发明提供的一种夹芯式薄膜传感器制备过程中所需的真空环境压合装置,包括压头1、套筒2、上转模板3以及下转模板4,压头1下部为圆柱体,圆柱体上加工有密封槽10,密封槽10安装密封圈7实现压头1和套筒2间的密封,所述的套筒2为上端开口,下端闭口的空心圆柱体结构,套筒2的内径与压头1的下部圆柱体直径一致,压头1与套筒2之间设置有上转模板3和下转模板4,上转模板3的下表面以及下转模板4的上表面为转模板正面,用以临时安装、定位批量电极并将其转移至真空密封舱内;套筒2侧面开设有阀门孔13连接内外环境,所述的阀门孔13外侧直径大于内侧直径,阀门孔13内侧孔中心与套筒2内安装后下转模板4的正面平齐。
21.本发明通过套筒阀门孔既可以对套筒内部抽真空以提供传感器压合所需的负压环境,又可以对套筒内部充高压气体以便于压头和套管的退模分离。本发明通过压力机精确控制压力加载的速度、大小和压力保持时长,从而保证批量化制作工艺参数可控性高、传感器结构个体差异性小。
22.套筒2的筒壁上端面周向均匀开设有与压头1上部法兰体外圈相同尺寸和数量的筒壁定位孔11,同时筒壁上端面开设有一圈用于放置承压泡沫5的内凹槽12,所述的压头1靠近边缘位置设置有法兰定位孔8,法兰定位孔8内设置法兰定位杆6,法兰定位杆6与筒壁定位孔11位置对应。
23.套筒内底面中心设置一长宽不等的矩形定位凸台,形状和规格与压头1的定位凸台9一致,侧面开设有阀门孔13连接内外环境,阀门孔外侧直径大于内侧直径,且门孔内侧孔中心与套筒2内安装后下转模板4的上表面平齐。
24.上转模板3和下转模板4均为圆形薄板与压头下部圆柱体直径、套筒内径一致。优选的,转模板材质为耐压且表面平整度较高的有机玻璃或聚碳酸酯板。上、下转模板形制、材质和规格完全一致,仅安装位置不同。
25.上转模板3和下转模板4的正面为传感器电极粘贴面,上面采用激光刻蚀的方式标记有传感器阵列的精确摆放位置,背面开设有定位凹孔14,孔边长宽高与压头1、套筒2上定位凸台9的尺寸一致,孔高度为板厚度一半。
26.承压泡沫5为具有一定强度和平台应力的轻质弹性泡沫,为矩形长条状;优选的,弹性eva发泡泡沫孔隙率高、回弹性好、可重复使用,且承压泡沫在稳定压溃阶段提供的载荷不低于压头因套筒内负压产生的大气压力的2倍。无额外压力作用时,承压泡沫稳定支撑压头并在上下转模板之间提供一定高度的密封舱。当压头施加额外压力时,承压泡沫屈服压缩变形并产生稳定的反馈载荷,直至上转模板3和下转模板4压合。
27.如图2所示,本发明基于芯式薄膜传感器真空环境压合装置的方法包括以下步骤:s1:在下转模板正面擦拭一层很薄的真空脂作为临时固定传感器柔性电极的粘结剂,提供夹芯式薄膜型传感器所用的柔性电极,按照下转模板正面标记的传感器位置依次安装柔性电极,在柔性电极上安装双面覆胶且开设有嵌入孔的绝缘垫平层,将裁剪好的压电膜元件嵌入垫平芯层的嵌入孔内,按照转模板背部定位凹孔的方位将下转模板安装入套筒内部。
28.优选的转模板采用透明有机玻璃板,厚度10mm,正面采用激光划线,标注所有传感器的摆放位置,背面中心开设长5mm、宽3mm、深5mm的定位凹孔。
29.优选的,夹芯式薄膜型传感器柔性电极采用柔性印刷电路技术制作,聚酰亚胺薄
膜为基底,厚度28μm,上部采用磁控溅射印刷金属电极及其引线厚度12μm。
30.优选的,压电膜元件采用极化后的pvdf压电薄膜元件,厚度52μm,直径6mm,绝缘垫平层采用双面覆胶的未极化的pvdf压电薄膜,厚52μm,双面覆胶后的厚度74μm,上面开设6.1mm直径的嵌入孔,pvdf压电膜元件可嵌入其中。
31.s2:在上转模板正面擦拭一层很薄的真空脂作为临时固定传感器上层柔性电极的粘合剂,按照转模板正面标记的传感器位置依次摆放柔性电极,然后在转模板的背面均匀擦拭一层很薄的真空脂,作为临时粘接上转模板和压头的粘合剂,将上转模板按照背部开设的定位凹孔与压头进行装配贴合。
32.s3:在压头密封槽和密封圈部位均匀涂覆一层真空脂以润滑和密封,采用圆柱形定位销将压头与套筒上下对齐后压入,在套筒筒壁上端面凹槽内无定位销的地方放置承压泡沫条,将压头缓慢下压,直至压头法兰下表面与泡沫接触,此时上下转模板间预留有一定高度的间隙。
33.承压泡沫为通孔或闭孔型金属基、高聚物基泡沫材料,孔隙率不小于80%,在压缩是具有典型的弹性小变形(应力
‑
应变线性关系)、应力平台(应力随应变基本保持不变)和致密化(应力随应变迅速增长)三个典型变形阶段,其中平台阶段泡沫应力基本保持不变。优选的,高聚物基体弹性和弹塑性泡沫的屈服强度和平台应力较为接近,便于预设泡沫强度并计算最终的压制载荷。
34.在套筒内部抽真空阶段,压头通过承压泡沫在弹性小变形阶段(工程应变小于5%)提供的支撑载荷与套筒保持稳定间距从而在上下转模板之间形成真空密封舱,真空密封舱的高度不大于承压泡沫高度的50%,从而保证在传感器压制时承压泡沫仍处于应力平台变形阶段;在压合阶段又可以通过压力机加载精密控制压缩位移或载荷的施加速率对传感器进行压合和保压处理,此时承压泡沫进入应力平台阶段并提供稳定的支撑载荷,传感器的压制载荷为压力机施加载荷与泡沫压溃载荷之差;在退模阶段压头通过压头上作用的拉伸载荷和舱内反充的高压协同分离装置。
35.设承压泡沫条的平台应力为σ,宽a、高b,总布设长度为l,套筒内部直径d,大气压力为p0,则,即承压泡沫在稳定压溃阶段提供的载荷不低于压头因套筒内负压产生的大气压力的2倍,设置密封舱初始高度即上下转模板间距不大于b/2。设压力机最终压制载荷为f,转模板上传感器个数为n,单个传感器受压面积为as,则单个传感器的压制应力为。
36.优选的,密封槽宽度为5mm,深度为4mm,选用线径5.5mm、外径为(d
‑
10)mm的硅橡胶密封圈。
37.s4:通过套筒筒壁的阀门孔对上下转模板之间形成的密封舱进行抽真空处理,此时由于套筒内密封舱负压导致的压头下压力由周边承压泡沫条承载,通过优选泡沫强度和平台应力使之在无额外压力作用时,未达到压溃变形的泡沫能够完全支撑压头上作用的大气压载荷,当达到真空环境时停止抽气并关闭阀门保持套筒内部的负压环境。
38.s5:将压头继续缓慢下压,直至上下转模板的正面完全贴合,将压制压力维持一定时间,并保持舱内真空环境,在该过程中承压泡沫被压缩。
39.s6:压制结束后,打开阀门开关,平衡套筒内外压力;将套筒底部固定在工作台上,通过压头上端拉环向上提拉压头,同时通过阀门孔向套筒内部加高压气体,使筒内气压约
为150kpa即可顺利推出压头,分离上下转模板即可获得真空环境下批量压合制成的夹芯式薄膜传感器。
40.本发明提供的装置即可实现夹芯式传感器两侧电极封装时的真空环境,又可以在真空环境中的传感器施加一定载荷,且压制的载荷可通过施加在压头上的力和承压泡沫压溃支撑力进行计算,压制工艺可控性强。
41.本实施例的压头和套筒之间通过密封槽和密封圈实现真空环境的密封,在抽真空时上下转模板之间的密封舱负压引起的压头下压载荷由周边设置的承压泡沫支撑,承压泡沫的平台应力和填充长度可通过预先计算设定。高孔隙率弹性泡沫的使用即能保证筒内负压密封舱的稳定存在,又能够保证在上下转模板压合过程中泡沫提供的反馈载荷恒定,从而便于通过加载压力和反馈载荷确定传感器的压制压力。
42.本实施例的压头和套筒之间采用多个定位孔和定位杆进行连接装配,内部上下转模板分别采用定位凸台和定位凹孔进行定位装配,可精确保证批量制作传感器时上转模板正面安装的柔性电极与下转模板安装的芯层/柔性电极组合层位置一一对齐压合。
43.本实施例提供的压合装置在退模过程中,可通过向套筒内反向充一定高压气体的作用协助压头与套筒的分离,减小了因密封摩擦力导致的压头退模的难度。
44.本实施例采用了批量制作的柔性电极、压电膜元件和等厚度垫平层,同时采用表面平整有机玻璃转模板为压合面,且压力可控,可以精确控制各工艺参数的前提下批量制作薄膜型传感器,从而减小传感器的个体差异性。
45.以上仅为本发明的较佳实施例而已,并不用以限制本发明,凡在本发明的精神和原则之内所作的任何修改、等同替换和改进等,均应包含在本发明的保护范围之内。