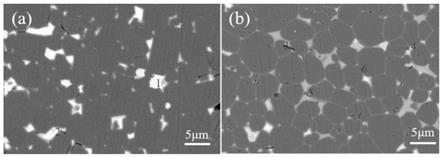
一种高强度r-t-b稀土永磁体及其制备方法
技术领域
1.本发明涉及一种高强度r-t-b稀土永磁体,属于稀土磁体领域。
背景技术:2.r-t-b系稀土永磁体作为一种功能材料,一直以来的研究主要集中在如何进一步提升其磁性能。近些年来随着r-t-b磁体应用领域逐渐扩大,尤其是随着高速马达的发展以及在电动汽车领域的应用,对其力学性能的要求越来越高。
3.r-t-b稀土永磁体是一种脆性材料,在受力时容易发生脆断,这严重的制约了材料的使用环境。造成r-t-b稀土永磁体力学性能较差的原因主要有以下几个方面:首先磁体的主相是一种结构复杂的金属间化物,无法发生滑移或孪生变形,因此受力时容易发生脆断;其次晶界富r相的强度较低,抵抗裂纹传播能力差,因此裂纹很容易沿着晶界富r相传播;最后是r-t-b磁体存在显微结构不均匀的特点,主相晶粒尺寸的不均匀以及晶界富r相分布的不均匀容易导致应力集中。
4.通过细化主相晶粒能够在一定程度上改善磁体的力学性能。但在细化主相晶粒的同时会影响磁体的磁性能,因此在实际生产中的操作难度较大。此外相关的研究表明磁体的断裂类型主要为沿晶断裂,即脆弱的晶界富r相是磁体力学性能较差的主要原因。通过细化主相晶粒尺寸并不能改变晶界富r相强度低的本质,因此现阶段通过提高晶界富r相的强度才是提高磁体力学性能的关键。
5.第二相强化是改善材料力学性能的常用方法,目前已被成熟应用到各个材料体系,因此有望通过引入第二相强化晶界富r相的方法制备高强度的r-t-b稀土永磁体。
技术实现要素:6.针对r-t-b磁体力学性能的不足,本发明提供了一种高强度的r-t-b稀土永磁体。在原材料配比阶段添加一定含量的zr,并合理调控zr与b和t含量的配比,按照sc片制备、sc片高温热处理、氢破、气流磨、气流磨粉末粒度优化、取向成型、等静压、真空烧结和时效的标准工序进行磁体制备。熔炼过程中通过采用1480~1510℃较高的熔炼温度,在1440~1460℃保温浇铸,制备sc片。随后进行将sc片置于900~1030℃氩气环境中保温30min~4h的sc片高温热处理工序,氩气压力为30~50kpa。通过高温热处理会使sc片中zr元素以纤维状zr化物的形式在富r相中析出,结合氢破、气流磨制粉和混粉能够使纤维状的zr化物与磁粉均匀混合。此外通过对sc片的高温热处理诱导zr化物在sc片中析出能够避免烧结过程中zr化物在主相晶粒内部析出。随后压坯烧结时纤维状的zr化物逐渐生长为棒状,并存在于晶界富r相中。通过调整磁体zr含量以及烧结温度、时间等工艺参数能够有效的调控zr化物的形貌、尺寸和分布,实现通过强化晶界富r相的方式提高磁体的力学性能。此外在气流磨过程中采用粉末分级装置对粉末粒度进一步筛分,通过优化粉末粒度分布的方法改善磁体的显微结构均匀性,进一步提高磁体的力学性能,优选以粒度smd处于3.0~6.0μm的粉末颗粒占比95%以上。与传统双合金方法添加第二相颗粒相比本发明采用第二相析出的方法能
够获得更加细小的第二相颗粒,通过调整磁体zr含量、烧结工艺参数可以调节zr化物的形貌、尺寸和分布,同时避免传统双合金法易引入杂质的缺点。
7.本发明采用的技术方案如下:
8.一种高强度r-t-b稀土永磁体,其特征在于磁体成分包括:
9.r:29.0wt.%~33.0wt.%,r由r1、r2和rh组成,r1为稀土元素nd,r2为稀土元素pr,rh为稀土元素dy、tb、ho、gd中的至少一种;r2含量在0.3~10wt.%之间,优选0.5~2wt.%之间;rh含量在0.02~8.5wt.%之间,优选0.1~1wt.%之间;r的余量为r1,
10.b:0.90wt.%~1.1wt.%,
11.m:5.0wt.%以下,其中m由m1、m2、m3组成或由m1、m2、m3和m4组成,m1为元素al,m2为元素cu,m3为元素ga,m4为元素si、zn、sn、ge、ag、au中的至少一种;m1含量在0.1~1.5wt.%之间,优选1~1.2wt.%之间;m2含量在0.01~0.55wt.%之间,优选0.1~0.3wt.%之间;m3含量在0.01~0.6wt.%之间,优选0.05~0.2wt.%之间;当包含m4时,m4含量≤3.0wt.%,
12.zr:0.3wt.%~1.5wt.%,优选为0.5wt.%~1wt.%
13.余量为t以及其他不可避免杂质,其中t为fe和co中的至少一种,t的85wt.%以上为fe,
14.并且满足下式:
15.[zr]/91.22≥0.0025[t]/56
ꢀꢀꢀꢀ
(1),
[0016]
[b]/10.81≥4[zr]/91.22
ꢀꢀꢀꢀ
(2),
[0017]
其中[zr]为以质量分数表示的zr的含量,[b]为以质量分数表示的b的含量,[t]为以质量分数表示的t的含量;
[0018]
其中ti、nb、hf和w等能与b生成析出物的难熔金属元素存在于磁体中时,该类型元素总含量应低于0.01wt.%,
[0019]
所述磁体显微组织由主相r2t14b、晶界富r相和形貌为棒状的zr化物组成,其中棒状zr化物主要分布在磁体晶界富r相中,存在于主相晶粒内部的棒状zr化物数量占总zr化物数量的比例小于2.0%。
[0020]
所述棒状zr化物的长度为0.5μm~2.6μm,长径比为2~10。
[0021]
所述磁体显微组织中zr化物分布面密度为1~6个zr化物/100μm2,优选zr化物分布面密度为2~4个zr化物/100μm2。
[0022]
所述高强度r-t-b稀土永磁体按以下方法制备得到:将所述按照成分配比的高强度r-t-b稀土永磁体的原料通过真空感应熔炼、甩带制备成sc合金片,sc合金片进行高温热处理,氢破和气流磨后制得合金粉末,合金粉末经过粒度优化工序后在取向磁场中模压成型,成型磁体经真空烧结、时效处理制得所述高强度r-t-b稀土永磁体;
[0023]
所述sc合金片的高温热处理是在900~1030℃的氩气环境中保温30min~4h,氩气压力为30~50kpa。
[0024]
所述真空感应熔炼、甩带中的熔炼温度为1480~1510℃,在1440~1460℃保温甩带铸片,制备sc合金片。
[0025]
所述粒度优化工序为采用粉末分级装置对气流磨后的粉末进行筛分,获得粒度smd处于3.0~6.0μm范围内的粉末颗粒占比95%以上的粉末。
[0026]
所述真空烧结的温度为1080~1120℃,保温时间为4~20h。
[0027]
所述时效处理的工艺包括700~900℃保温2~8h的一级时效处理和400~600℃保温2~8h的二级时效处理。
[0028]
本发明还提供了所述高强度r-t-b稀土永磁体的制备方法,所述方法为将所述按照成分配比的高强度r-t-b稀土永磁体的原料通过真空感应熔炼、甩带制备成sc合金片,sc合金片进行高温热处理,氢破和气流磨后制得合金粉末,合金粉末经过粒度优化工序后在取向磁场中模压成型,成型磁体经真空烧结、时效处理制得所述高强度r-t-b稀土永磁体。
[0029]
进一步,所述真空感应熔炼、甩带是在1480~1510℃将原材料熔炼为合金液,在1440~1460℃将熔融合金液通过中间包浇到旋转铜辊上凝固,制得sc合金片。
[0030]
所述sc合金片的高温热处理是在900~1030℃的氩气环境中保温30min~4h,氩气压力为30~50kpa。
[0031]
所述粒度优化工序为采用粉末分级装置对气流磨后的粉末进行筛分,获得粒度smd处于3.0~6.0μm范围内的粉末颗粒占比95%以上的粉末;
[0032]
所述真空烧结的温度为1080~1120℃,保温时间为4~20h。
[0033]
进一步,所述真空感应熔炼、甩带优选按照以下步骤进行,按成分配比取纯度为99.9%以上的原料,依照熔点从高到低的顺序依次放入坩埚中,炉内抽真空直到真空度达10-3
~10-4
pa,露点低于-50℃;之后向炉内充氩气使气压达到30kpa~50kpa,并加热至1480~1510℃,待原材料完全熔化后保温3~5min;之后将合金液温度降至1440~1460℃,将熔融合金液通过中间包浇到旋转铜辊上凝固,制得sc合金片。甩带铸片的工艺一般为:调整铜辊转速为70~75转/分钟,然后按照一定速度转动坩埚,使熔融合金液经过中间包输送到冷却辊上进行凝固随后掉落到水冷盘上降温,制得sc合金片。
[0034]
所述sc合金片高温热处理工序按照以下步骤进行:将熔炼制得的sc合金片放置在钼舟中,然后放置于加热炉内;将炉内真空度抽到10-3
~10-4
pa并加热到900~1030℃,当温度达到目标温度后向炉内充30~50kpa压力的氩气,保温30min~4h;热处理完成后冷却至室温,此过程对冷却速度无要求,既可以采用随炉冷却可以采用风冷。
[0035]
所述氢破和气流磨工序按照以下步骤进行:氢破碎处理时,反应釜内氢气压力一般为0.01~0.09mpa,吸氢反应时,10分钟内反应釜内部压力变化不超过0.5%,代表吸氢结束。吸氢反应结束后,边抽真空边升温至400~600℃之间,保温2~6h,使合金片中的氢气脱出,随后冷却得到氢破碎的粗粉。将得到的粗粉置于气流磨设备中,在惰性气体气氛中,调节喷嘴压力为0.6mpa~0.8mpa之间,通过高速气体带动粗粉相互撞击进行破碎,惰性气体一般为氦气、氮气等惰性气体。控制气流磨设备的分选轮和旋风分离器调控粉末粒度。
[0036]
所述粒度优化工序为采用粉末分级装置对气流磨后得粉末进一步进行筛分,优化粉末粒度。优选以粒度smd处于3.0~6.0μm范围内的粉末颗粒占比95%以上。
[0037]
合金粉末中可加入润滑剂和/或抗氧化剂后再进行模压成型,采用常规市售磁粉保护润滑剂或者抗氧化剂即可。所述润滑剂的添加量可为合金粉末质量的0.01~0.1%,抗氧化剂可为合金粉末质量的0.01~0.14%。
[0038]
所述的合金粉末在取向磁场中的模压成型优选按照以下步骤进行:取向磁场优选为3~6t,成型压力为5~7mpa。取向成型后的压坯再进行冷等静压,压力为150~180mpa。经过取向成型后压坯密度为3.6~4.0g/cm3,冷等静压后压坯密度约为4.5~4.6g/cm3。可根据工艺选择是否在模压后进行冷等静压,本发明选择对取向成型后的压坯进行冷等静压,进
一步消除压坯内部裂纹。
[0039]
所述真空烧结工艺为:10-3
~10-4
pa真空度下,烧结温度为1080~1120℃,保温时间为4~20h。为了防止高温烧结过程中磁体表面层稀土挥发,在升至目标烧结温度后向烧结炉内充30~50kpa的惰性气体,可选惰性气体为氩气和氦气。
[0040]
所述时效处理是在指烧结后的磁体在700~900℃进行2~8h的一级时效处理工艺,然后以不低于20℃/min的速度冷却至低于100℃,再加热至400~600℃进行2~8h的二级时效处理,结束后以不低于30℃/min的速度冷却至低于80℃。
[0041]
第二相对材料的强化作用很大程度上依赖第二相的强度、形貌、尺寸和分布等。向基体粉末中添加第二相粉末颗粒是粉末冶金行业常用的方法,但采用这种方法很难保证第二相分布的均匀性。此外r-t-b类型的稀土永磁体的晶界富r相化学活性较高,易与其他元素发生反应。通过外部添加第二相的方法容易导致第二相完全反应消失或与基体相之间生成高结合力的界面。这种高结合强度的界面对磁体力学性能的提升有限,严重时反而会劣化磁体的力学性能。同时r-t-b磁体的磁性能对各种杂质敏感,通过双合金混粉的方式容易向磁体中引入这类微量杂质,降低磁体磁性能。采用第二相析出强化的方式则能够有效避免上述提到的问题。
[0042]
本发明在合金熔炼阶段向磁体原料中添加一定含量的zr,由于采用熔甩法制备sc片时冷却速度较快,zr化物的析出会被抑制。sc片高温热处理时。zr元素会以纤维状zr化物的形式从富r相中析出,经过氢破、气流磨和混粉后与磁粉均匀的混合到一起。采用第二相析出的方式能够避免外部杂质的引入,因此能够达到比双合金混粉更好的效果。在烧结过程中纤维状的zr化物逐渐生长为棒状,并存在于晶界富r相中。通过调整磁体zr含量以及烧结温度、时间等工艺参数能够有效的调控zr化物的形貌、尺寸,实现通过强化晶界富r相的方式提高磁体的力学性能。同时采用粉末分级装置对气流磨粉末粒度进一步优化,通过提高粉末颗粒均匀性的方法提高磁体显微组织均匀性,进而提高磁体力学性能。
[0043]
通过调节zr与b和t含量的相互关系、控制zr元素的添加量,能够调控zr化物的析出量、形貌与分布。相关研究表明zr元素能够替换主相r2t14b中的部分r元素,当zr添加量较低时无法形成zr化物。本发明通过大量实验发现以t含量衡量主相生成数量时,zr与t元素的含量只有在满足公式(1)时才能保证sc片经过高温热处理后有足够得zr化物析出。但磁体的zr含量并不是越高越好,随着磁体zr含量的升高,即使经过sc片高温热处理工序zr化物的析出也不充分。这些未析出的zr元素则会在烧结时以析出物的形式从主相晶粒内部析出。由于主相与zr化物之间的润湿性较差,两者之间的界面成为了天然的裂纹源,降低磁体力学性能的同时降低磁体的磁性能。在满足公式(1)的条件下合适的zr元素添加量处于0.3wt.%~1.5wt.%之间。
[0044]
此外b元素参与了多种zr化物的形成,因此为了保证zr化物充分生成,b与zr含量需要满足公式(2)。ti、nb、hf和w等元素存在于磁体内部时同样会与b元素反应,消耗了部分b元素。且实验结果表明这些元素与b反应产物的形貌、尺寸和分布难以通过烧结工艺调节,对磁体力学性能的提升有限。因此本发明中优选磁体成分不含ti、nb、hf和w等类型元素,当这类元素以不可避免杂质存在时,这类型元素的总含量应低于0.01wt.%。
[0045]
第二相的尺寸同样会影响其对基体的强化效果,在r-t-b磁体中当第二相尺寸较为细小时,其改变裂纹传播方向的作用较弱,对力学性能的强化效果不明显。当第二相的尺
寸过大时则又会严重阻碍晶界富r相的分布,降低磁体的磁性能。经过sc片高温热处理后析出的zr化物呈细小纤维状,在随着的烧结过程中纤维状的zr化物会逐渐长大为棒状。实验发现在保证磁体烧结致密合格以及平均晶粒尺寸不发生明显变化时通过升高或降低烧结温度能够调控棒状zr化物的尺寸。本发明表明存在于晶界相、长度为0.5μm~2.6μm、长径比2~10的棒状zr析出物能够有效提高磁体的力学性能。
[0046]
分布于磁体晶界富r相中的zr化物会阻碍二级时效过程中晶界富r相的流动,从而使晶界富r相分布均匀性变差,导致磁体矫顽力降低。实验发现采用一定含量的pr替代金属元素nd,同时综合添加al、cu、ga等元素能够显著降低晶界富r相的熔点,增加晶界富r相与主相晶粒的润湿性,改善晶界富r相的分布均匀性,从而提高磁体的矫顽力。
[0047]
优选的,本发明采用粉末分级装置对气流磨粉末进行筛选以获得粒度更为均匀的粉末颗粒,通过调控磁体显微组织的均匀性提高磁体的力学性能。磁体显微组织的不均匀性,尤其是主相晶粒尺寸的不均匀是导致r-t-b磁体力学性能较差的主要原因之一。粉末颗粒中的超细粉在烧结阶段会使周围的晶粒发生异常长大,加剧显微组织不均匀性。磁体中超细粉末熔化或通过合并造成晶粒异常长大时容易将细小的析出物包裹在主相晶粒内部,劣化磁体力学性能。因此通过对气流磨粉末进一步分级去除超细和粗大粉末颗粒能够有效改善主相晶粒尺寸的均匀性,并促进zr化物对磁体力学性能的强化作用。
[0048]
本发明的益处体现在通过对sc片进行高温热处理会使sc片中zr元素以纤维状zr化物的形式在富r相中析出,结合氢破、气流磨制粉和混粉能够使纤维状的zr化物颗粒与磁粉均匀混合。随后压坯烧结时纤维状的zr化物逐渐生长为棒状,并存在于晶界富r相中。实现通过强化晶界富r相的方式提高磁体的力学性能。本发明表明存在于晶界相、长度0.5μm~2.6μm、长径比2~10的棒状zr析出物能够有效的提高磁体的力学性能。结合优化气流磨粉末粒度分布,提高磁体显微组织的均匀性,能够制备高强度的r-t-b磁体,且磁体的磁性能如矫顽力得到保持,不会降低。
附图说明
[0049]
图1(a)和(b)分别为实验no.5和实验no.8磁体的显微组织图。
[0050]
图2(a)和(b)分别为实验no.21和实验no.23磁体的显微组织图。
[0051]
图3为实验no.29磁体的显微组织图。
[0052]
图4(a)和(b)分别为实验no.30和实验no.31的sc片显微组织图。
[0053]
图5为实验no.31磁体显微组织图。
具体实施方式
[0054]
下面结合具体实施例对本发明的技术方案进行进一步说明,但本发明的保护范围不限于此。
[0055]
本发明采用真空感应熔炼、甩带,按成分配比取纯度为99.9%以上的原料,依照熔点从高到低的顺序依次放入坩埚中,炉内抽真空直到真空度达10-3
~10-4
pa,露点低于-50℃。之后向炉内充氩气使气压达到30~50kpa,并加热至1480~1510℃,待原材料完全熔化后保温3~5min。之后将合金液温度降至1440~1460℃,并进行保温、浇铸。调整铜辊转速为70~75转/分钟,然后按照一定速度转动坩埚,使熔融合金液经过中间包输送到冷却辊上进
行凝固随后掉落到水冷盘上降温。
[0056]
对熔炼制备的sc片进行高温热处理。将熔炼制得得合金片放置在钼舟中,置于加热炉内。将炉内真空度抽到10-3
~10-4
pa并加热到900~1030℃,当温度达到目标温度时向炉内充30~50kpa压力得氩气,保温30min~4h。热处理完成后冷却至室温,此过程对冷却速度无要求,既可以采用随炉冷却可以采用风冷。
[0057]
通过氢破和气流磨将合金片制备呈合金粉末。氢破碎处理时,反应釜内氢气压力一般为0.01~0.09mpa,吸氢反应时,10分钟内反应釜内部压力变化不超过0.5%,代表吸氢结束。吸氢反应结束后,边抽真空边升温至400~600℃之间,保温2~6h,使合金片中的氢气脱出,随后冷却得到氢破碎的粗粉。将得到的粗粉置于气流磨设备中,调节喷嘴压力为0.6mpa~0.8mpa之间,通过高速气体带动粗粉相互撞击进行破碎,惰性气体一般为氦气、氮气等惰性气体。控制气流磨设备的分选轮和旋风分离器调控粉末粒度。
[0058]
采用粉末分级装置对气流磨后得粉末进一步进行筛分,优化粉末粒度。优选以粒度smd处于3.0~6.0μm范围内的粉末颗粒占比95%以上。
[0059]
向合金粉末中加入润滑剂和/或抗氧化剂后,在取向磁场进行模压成型,采用常规市售磁粉保护润滑剂或者抗氧化剂即可。所述润滑剂的添加量可为合金粉末质量的0.01~0.1%,抗氧化剂可为合金粉末质量的0.01~0.14%。
[0060]
取向磁场优选为3-6t,成型压力为5-7mpa。取向成型后的压坯再进行冷等静压,压力为150~180mpa。经过取向成型后压坯密度为3.6~4.0g/cm3,冷等静压后压坯密度约为4.6g/cm3。
[0061]
采用真空烧结工艺将磁体烧结致密。所述真空烧结工艺为:10-3
~10-4
pa真空度下,烧结温度为1080~1120℃,保温时间为4~20h。为了防止高温烧结过程中磁体表面层稀土挥发,在升至目标烧结温度后向烧结炉内充30~50kpa的惰性气体,可选惰性气体为氩气和氦气。
[0062]
烧结后的磁体需进行两级时效工艺,首先在700~900℃进行2~8h的一级时效处理工艺,然后以不低于20℃/min的速度冷却至低于100℃,再加热至400~600℃进行2~8h的二级时效处理,结束后以不低于30℃/min的速度冷却至低于80℃。
[0063]
将磁体破碎后在中心取样,利用icp-ms检测磁体成分。采用sem观察磁体显微组织,通过epma分析磁体微区成分。采用内圆切片机、双面磨的方式制备三点弯曲样品,样品尺寸长
×
宽
×
高为25(
±
0.01)mm
×
6(
±
0.01)mm
×
5(
±
0.01mm),样品高度方向平行于磁体取向方向。按照gb/t31967.2-2015规定采用三点弯曲的方法测量磁体的抗弯强度,每组实验测量10只样品并计算平均值。三点弯曲压头为直径5mm的圆柱,两支撑柱的直径为5mm,支点之间的跨距为14.5mm,压头的下压速度为0.1mm/min。采用线切割、双面磨和端面磨的方法制备磁性能测量样品,样品为φ10mm
×
10mm圆柱,利用nim设备测量磁体磁性能。
[0064]
实施例一:
[0065]
对于低熔点金属以纯度为99.9wt.%以上的纯金属作为原料,对于熔点高于纯铁的元素则以该元素与铁的合金作为原料。依照熔点从高到低的顺序依次放入坩埚中,炉内抽真空直到真空度达10-4
pa,露点低于-50℃。之后向炉内充氩气使气压达到30kpa,并加热至1490℃,待原材料完全熔化后保温3min。之后将合金液温度降至1450℃,并进行浇铸。调整铜辊转速为70转/分钟,然后按照一定速度转动坩埚,使熔融合金液经过中间包输送到冷
却辊上进行凝固随后掉落到水冷盘上降温,得到厚度为0.25
±
0.05mm的合金片。
[0066]
对熔炼制备的sc片进行高温热处理。将熔炼制得得合金片放置在钼舟中,置于加热炉内。将炉内真空度抽到10-4
pa并加热到1000℃,当温度达到目标温度时向炉内充30kpa压力的氩气,保温2h。热处理完成后随炉冷却至室温。
[0067]
合金片在0.09mpa氢气压力下进行吸氢反应,吸氢反应结束后边抽真空边升温至550℃,保温4h使合金片中的氢气脱出,随后冷却得到氢破碎的粗粉。冷却后向粗粉中加入0.05wt.%硬脂酸锌并混合3h,利用氮气气流磨对粗粉进一步破碎得到细粉,气体压力为0.6mpa。将气流磨后的细粉采用粉末分级装置进一步进行筛分,使smd处于3.0~6.0μm范围内的粉末颗粒占比95%以上。
[0068]
在细粉中添加0.03wt.%的有机润滑剂(天津市悦圣新材料研究所生产磁粉保护润滑剂3#)并混合3h。混合均匀后的细粉在磁场下取向成型,取向磁场为3.5t的静磁场,压制压力为5mpa,压制后磁体密度为3.9~4.0g/cm3。之后进行冷等静压,压制压力为160mpa,压制后磁体密度大于4.6g/cm3。
[0069]
采用真空烧结工艺将磁体烧结致密。所述真空烧结工艺为在10-4
pa真空度下,以7.53g/cm3作为烧结磁体的最低要求,烧结温度为1080~1120℃,在4~20h内调整保温时间。为了防止高温烧结过程中磁体表面层稀土挥发,在升至目标烧结温度后向烧结炉内充30kpa的氩气。
[0070]
烧结后的磁体需进行两级时效工艺,磁体首先在860℃进行3h的一级时效处理工艺,然后以不低于20℃/min的速度冷却至低于100℃,再加热至520℃进行3h的二级时效处理,结束后以不低于30℃/min的速度冷却至低于80℃。
[0071]
将磁体破碎后在中心取样,利用icp-ms检测磁体成分。采用sem观察磁体显微组织,通过epma分析磁体微区成分。按照gb/t31967.2-2015规定采用三点弯曲的方法测量磁体的抗弯强度。每组实验测量10只样品并计算平均值。
[0072]
各实验组磁体成分采用质量分数表示,具体如表1所示:
[0073]
表1
[0074]
no.ndprfealdycocugabzrtinb公式(1)公式(2)130.60.5bal10.50.10.150.10.960////230.60.5bal10.50.10.150.10.960.05//不满足满足330.60.5bal10.50.10.150.10.960.1//不满足满足430.60.5bal10.50.10.150.10.960.28//满足满足530.60.5bal10.50.10.150.10.960.30//满足满足630.60.5bal10.50.10.150.10.960.5//满足满足730.60.5bal10.50.10.150.10.960.6//满足满足830.60.5bal10.50.10.150.10.961//满足满足930.60.5bal10.50.10.150.10.961.5//满足满足1030.60.5bal10.50.10.150.10.962//满足满足1130.60.5bal10.50.10.150.10.962.5//满足不满足1230.60.5bal10.50.10.150.10.963//满足不满足1330.60.5bal10.50.10.150.10.960.50.002/满足满足1430.60.5bal10.50.10.150.10.960.50.2/满足满足
1530.60.5bal10.50.10.150.10.960.50.5/满足满足1630.60.5bal10.50.10.150.10.960.5/0.002满足满足1730.60.5bal10.50.10.150.10.960.5/0.2满足满足1830.60.5bal10.50.10.150.10.960.5/0.5满足满足1930.60.5bal10.50.10.150.10.960.50.20.2满足满足
[0075]
采用三点弯曲的方法测试磁体的抗弯强度,每组测量10个数据并计算平均值。在sem的背散模式下统计面积为1000μm
×
1000μm范围内的尺寸、形貌,计算晶界富r相中析出物占比和析出物的分布密度(100μm2范围内析出物的数量),具体如下表2所示:
[0076]
表2
[0077][0078]
使用sem观察磁体的显微组织,如图1(a)和(b)所示,从图中可以看出当磁体zr含量为0.3wt.%时,在磁体的晶界相发现了zr化物。但由于zr元素的添加量较低导致磁体中zr化物的数量较少。而当磁体zr含量增加到1.0wt.%时晶界富r相中的zr化物数量明显增多。
[0079]
采用epma点扫描的方法分析磁体的微区成分。实验no.5和实验no.8磁体析出物成分如表3所示:
[0080]
表3
[0081][0082]
从析出物的成分可以看出zr化物的zr含量较高,在20~85wt.%之间。由于zr元素能够取代主相中的r元素,因此当磁体内部zr浓度较低时能够参与形成析出物的zr含量不足,导致sc片在高温热处理时无法析出zr化物。因此在本发明中只有当磁体中zr含量超过
一定浓度时才能够明显促进zr化物的形成。
[0083]
结合各实验组的数据可以得出当磁体的zr含量不满足公式(1)时磁体内部不存在zr化物。当磁体的zr含量满足公式(1)但是zr元素含量低于0.3wt.%时仅会形成极少量细纤维状的zr化物。由于析出物的分布密度低且尺寸太过细小,磁体受力时这些细小的析出物易随晶界富r相断裂,因此对磁体力学性能的提升有限。随着合金中zr元素增加到推荐范围内(0.3wt.%~1.5wt.%)时析出物的分布密度和析出物的平均长度逐渐增加,且经过烧结后再sc片高温热处理阶段析出的纤维状zr化物会生长为棒状。由于棒状的析出物能够承受更高的载荷,因此改变裂纹的传播方向,从而起到强化磁体晶界相的作用。同时棒状析出物受力时的拔出效应也能够消耗更多的断裂能,因此综合两方面的作用能够有效的提高磁体的抗弯强度。
[0084]
磁体的b含量同样会影响zr化物的析出过程,如实验no.11和实验no.12所示当b元素含量不满足公式(2)时,sc片高温热处理后析出的zr化物呈块状,经过烧结后生长为粗大块状。这些粗大的块状析出物的zr含量均高于85wt.%,一般分布于晶界富r相,且与主相晶粒直接接触。由于这种粗大析出物与主相晶粒的润湿性较差,其与主相晶粒的界面结合力较差容易导致应力集中,降低磁体的力学性能。
[0085]
ti、nb等能与b生成析出物的元素存在于磁体中时会影响zr化物的析出过程。由实验no.13~no.19可以看出随着磁体中ti、nb等元素含量的增加,zr化物的平均长度下降、抗弯强度随之降低。ti、nb等元素与b元素反应,影响sc片高温热处理时zr化物的析出以及烧结时zr化物的进一步生长过程,从而改变zr化物的尺寸和析出量。实验结果表明添加了ti、nb后的磁体内部不但zr化物的平均长度降低,同时随着ti和nb含量的升高,zr化物逐渐由棒状转变为块状。导致析出物对晶界富r相的强化效果减弱,磁体的抗弯强度降低。因此ti、nb、hf和w这类元素以不可避免杂质存在时,这类型元素的总含量应低于0.01wt.%。
[0086]
实施例二:
[0087]
对于低熔点金属以纯度为99.9wt.%以上的纯金属作为原料,对于熔点高于纯铁的元素则以该元素与铁的合金作为原料。依照熔点从高到低的顺序依次放入坩埚中,炉内抽真空直到真空度达10-4
pa,露点低于-50℃。之后向炉内充氩气使气压达到30kpa,并加热至1490℃,待原材料完全熔化后保温3min。之后将合金液温度降至1450℃,并进行浇铸。调整铜辊转速为70转/分钟,然后按照一定速度转动坩埚,使熔融合金液经过中间包输送到冷却辊上进行凝固随后掉落到水冷盘上降温,得到厚度为0.25
±
0.05mm的合金片。
[0088]
对熔炼制备的sc片进行高温热处理。将熔炼制得得合金片放置在钼舟中,置于加热炉内。将炉内真空度抽到10-4
pa并加热到1000℃,当温度达到目标温度时向炉内充30kpa压力的氩气,保温2h。热处理完成后随炉冷却至室温。
[0089]
合金片在0.09mpa氢气压力下进行吸氢反应,吸氢反应结束后边抽真空边升温至550℃,保温4h使合金片中的氢气脱出,随后冷却得到氢破碎的粗粉。冷却后向粗粉中加入0.05wt.%硬脂酸锌并混合3h,利用氮气气流磨对粗粉进一步破碎得到细粉,气体压力为0.6mpa。将气流磨后的细粉采用粉末分级装置进一步进行筛分,使smd处于3.0~6.0μm范围内的粉末颗粒占比95%以上。
[0090]
在细粉中添加0.03wt.%的有机润滑剂(天津市悦圣新材料研究所生产磁粉保护润滑剂3#)并混合3h。混合均匀后的细粉在磁场下取向成型,取向磁场为3.5t的静磁场,压
制压力为5mpa,压制后磁体密度为3.9~4.0g/cm3。之后进行冷等静压,压制压力为160mpa,压制后磁体密度大于4.6g/cm3。
[0091]
采用真空烧结工艺将磁体烧结致密。所述真空烧结工艺为:在10-4
pa真空度下,以7.53g/cm3作为烧结磁体的最低要求,不同实验组烧结工艺如表5所示。为了防止高温烧结过程中磁体表面层稀土挥发,在升至目标烧结温度后向烧结炉内充30kpa的氩气。
[0092]
烧结后的磁体需进行两级时效工艺,磁体首先在860℃进行3h的一级时效处理工艺,然后以不低于20℃/min的速度冷却至低于100℃,再加热至520℃进行3h的二级时效处理,结束后以不低于30℃/min的速度冷却至低于80℃。
[0093]
采用sem观察磁体的显微组织,并在sem的背散模式下统计析出物的尺寸、数量和主相晶粒尺寸。将磁体破碎后在中心取样,利用icp-ms检测磁体成分。各实验组磁体成分采用质量分数表示,具体如表4所示:
[0094]
表4
[0095]
no.ndprfealdycocugabzrtinb公式(1)公式(2)20~2330.60.5bal10.50.10.150.10.960.6//满足满足2430.60.5bal10.50.10.150.10.96/0.6///2530.60.5bal10.50.10.150.10.96//0.6//2630.60.5bal10.50.10.150.10.96/0.30.3//2730.60.5bal10.50.10.150.10.96/0.25///
[0096]
不同实验组采用的烧结工艺如表5所示:
[0097]
表5
[0098]
no.烧结温度/℃保温时间/h201060122110807221100523113042411005251100526110052711005
[0099]
采用三点弯曲的方法测试磁体的抗弯强度,每组测量10个数据并计算平均值和标准层。在sem的背散模式下统计面积为1000μm
×
1000μm范围内析出物的尺寸与数量,并计算析出物的平均长度和长径比,具体结果如表6所示。
[0100]
表6
[0101][0102]
由于实验no.20~no.23磁体中包含了较高浓度的zr元素,低温烧结时磁体难以烧结致密。实验no.20的样品在1060℃保温12h后密度仍不达标,因此本发明的磁体需要在较高温度下进行烧结。
[0103]
分析发现通过改变烧结温度能够调节在sc片高温热处理阶段析出zr化物的长度。实验no.20~no.23采用了不同的烧结温度,在保证磁体密度合格的条件下使不同实验组磁体的平均晶粒尺寸差值在0.5μm范围内。分析不同温度烧结磁体的zr化物尺寸以及磁体的力学性能,发现随着烧结温度的升高磁体中zr化物的长度增加。从实验no.23的显微组织(图2的(b)图)可以看出当烧结温度为1130℃时,出现了长度为6.14μm的zr化物。在本实验组中磁体的抗弯强度随zr化物的长度增加先增大后降低,其中当zr化物的平均长度为0.89μm时磁体的抗弯强度存在最大值。适当尺寸的棒状zr化物分布于晶界相时能够强化晶界富r相,改变裂纹的传播方向。同时棒状析出物在受力时的拔出效应能够吸收更多的断裂能,因此可以有效的改善磁体的力学性能。磁体中尺寸较长的zr化物会穿插在几个主相晶粒间,与主相直接接触。由于zr化物与主相的润湿性较差,两相之间的界面会成为裂纹源,因此当析出相的尺寸太大时反而会降低磁体的力学性能。
[0104]
本实施例在保证磁体密度合格的前提下控制不同温度的烧结时间,使各实验组的晶粒尺寸不存在明显变化,排除了主相晶粒尺寸对磁体力学性能的影响。实验表明只有zr化物长度在0.5~2.6μm,长径比在2~10范围内时才能对磁体的力学性能起到较好的强化效果。
[0105]
nb和ti等元素单独添加到磁体中时同样会与b元素生成析出物。但是实验发现nb、ti等元素与zr生成的化物的形貌种类较多,存在纤维状、棒状和块状几种类型,当这类元素的添加量较少时还会出现颗粒状的析出物。此外通过烧结工艺调控很难调控nb、ti析出物的尺寸和不同形貌析出物的占比。这些析出物存在于磁体中时虽然也能够在一定程度上强化晶界富r相、提高磁体的抗弯强度,但由于不同析出物存在形貌和尺寸的差异,导致磁体不同部位力学性能的一致性较差,体现为这类磁体抗弯强度的标准差要明显高于单独添加zr的磁体。因此为了保证磁体力学性能的一致性应尽量降低这类元素在磁体中所占比例,当这类元素以不可避免的杂质存在时其含量应低于0.01wt.%。
[0106]
实施例三:
[0107]
对于低熔点金属以纯度为99.9wt.%以上的纯金属作为原料,对于熔点高于纯铁的元素则以该元素与铁的合金作为原料。依照熔点从高到低的顺序依次放入坩埚中,炉内抽真空直到真空度达10-4
pa,露点低于-50℃。之后向炉内充氩气使气压达到30kpa,并加热至1490℃,待原材料完全熔化后保温3min。之后将合金液温度降至1450℃,并进行浇铸。调整铜辊转速为70转/分钟,然后按照一定速度转动坩埚,使熔融合金液经过中间包输送到冷
却辊上进行凝固随后掉落到水冷盘上降温,得到厚度为0.25
±
0.05mm的合金片。
[0108]
对熔炼制备的sc片进行高温热处理。将熔炼制得得合金片放置在钼舟中,置于加热炉内。将炉内真空度抽到10-4
pa并加热到1000℃,当温度达到目标温度时向炉内充30kpa压力得氩气,保温2h。热处理完成后随炉冷却至室温。
[0109]
合金片在0.09mpa氢气压力下进行吸氢反应,吸氢反应结束后边抽真空边升温至550℃,保温4h使合金片中的氢气脱出,随后冷却得到氢破碎的粗粉。冷却后向粗粉中加入0.05wt.%硬脂酸锌并混合3h,利用氮气气流磨对粗粉进一步破碎得到细粉,气体压力为0.6mpa。将气流磨后的部分细粉采用粉末分级装置进一步进行筛分,使smd处于3.0~6.0μm范围内的粉末颗粒占比95%以上。不经过粉末分级装置处理的粉末smd处于3.0~6.0μm范围内的粉末颗粒占比为82%。
[0110]
在细粉中添加0.03wt.%的有机润滑剂(天津市悦圣新材料研究所生产磁粉保护润滑剂3#)并混合3h。混合均匀后的细粉在磁场下取向成型,取向磁场为3.5t的静磁场,压制压力为5mpa,压制后磁体密度为3.9~4.0g/cm3。之后进行冷等静压,压制压力为160mpa,压制后磁体密度大于4.6g/cm3。
[0111]
本实施例中所有实验组的成分均与实验no.7相同,将压坯在真空烧结炉中烧结致密。所述真空烧结工艺为在10-4
pa真空度下,烧结温度为1100℃,为了防止高温烧结过程中磁体表面层稀土挥发,在升至目标烧结温度后向烧结炉内充30kpa的氩气,保温时间为6h。
[0112]
烧结后的磁体需进行两级时效工艺,磁体首先在860℃进行3h的一级时效处理工艺,然后以不低于20℃/min的速度冷却至低于100℃,再加热至520℃进行3h的二级时效处理,结束后以不低于30℃/min的速度冷却至低于80℃。
[0113]
通过万能材料试验机三点弯曲测试方法测量烧结态磁体的抗弯强度。采用sem观察磁体的显微组织,并在sem背散模式下统计面积为1000μm
×
1000μm区域内析出物的尺寸、数量以及主相晶粒尺寸。
[0114]
不同实验组磁体的工艺特点、析出物尺寸和分布情况、主相晶粒尺寸以及磁体的力学性能如表7所示:
[0115]
表7
[0116][0117]
对比上述实验数据可知实验no.28的晶粒尺寸更加均匀,说明采用粉末分级处理气流磨粉末能够显著降低超细粉和粗大粉末颗粒所占比例,提高烧结后磁体晶粒尺寸的一致性,对磁体力学性能有明显的提升效果。此外粉末粒度的均匀性能够影响析出物的分布情况。当粉末颗粒包含较多的超细粉时,超细粉末颗粒在烧结阶段通过熔化或与周围的大晶粒合并造成晶粒生长时容易将zr化物包裹在主相晶粒内部,如图3磁体显微组织所示。从析出物的分布情况可以看出,未经过粉末筛选的磁体晶界相中析出物所占比例明显降低,即分布于主相内部的析出物数量增加。这些存在于主相晶粒内部的析出物会在主相晶粒内部造成裂纹,从而降低磁体的力学性能。采用粉末筛选首先能够保证磁体主相晶粒的一致性,其次可以避免超细粉末颗粒使邻近晶粒长大时包裹析出物的情况,因此更能发挥出析出物对磁体力学性能强化的优势。
[0118]
实施例四:
[0119]
对于低熔点金属以纯度为99.9wt.%以上的纯金属作为原料,对于熔点高于纯铁的元素则以该元素与铁的合金作为原料。依照熔点从高到低的顺序依次放入坩埚中,炉内抽真空直到真空度达10-4
pa,露点低于-50℃。之后向炉内充氩气使气压达到30kpa,并加热至1490℃,待原材料完全熔化后保温3min。之后将合金液温度降至1450℃,并进行浇铸。调整铜辊转速为70转/分钟,然后按照一定速度转动坩埚,使熔融合金液经过中间包输送到冷却辊上进行凝固随后掉落到水冷盘上降温,得到厚度为0.25
±
0.05mm的合金片。
[0120]
对部分熔炼制备的sc片进行高温热处理,部分sc片不进行高温热处理作为对比。将熔炼制得得合金片放置在钼舟中,置于加热炉内。将炉内真空度抽到10-4
pa并加热到1000℃,当温度达到目标温度时向炉内充30kpa压力得氩气,保温2h。热处理完成后随炉冷却至室温。
[0121]
合金片在0.09mpa氢气压力下进行吸氢反应,吸氢反应结束后边抽真空边升温至550℃,保温4h使合金片中的氢气脱出,随后冷却得到氢破碎的粗粉。冷却后向粗粉中加入0.05wt.%硬脂酸锌并混合3h,利用氮气气流磨对粗粉进一步破碎得到细粉,气体压力为0.6mpa。将气流磨后的部分细粉采用粉末分级装置进一步进行筛分,使smd处于3.0~6.0μm范围内的粉末颗粒占比95%以上。不经过粉末分级装置处理的粉末smd处于3.0~6.0μm范围内的粉末颗粒占比为82%。
[0122]
在细粉中添加0.03wt.%的有机润滑剂(天津市悦圣新材料研究所生产磁粉保护润滑剂3#)并混合3h。混合均匀后的细粉在磁场下取向成型,取向磁场为3.5t的静磁场,压制压力为5mpa,压制后磁体密度为3.9~4.0g/cm3。之后进行冷等静压,压制压力为160mpa,压制后磁体密度大于4.6g/cm3。
[0123]
本实施例中所有实验组的成分均与实验no.7相同,将压坯在真空烧结炉中烧结致密。所述真空烧结工艺为在10-4
pa真空度下,烧结温度为1100℃,为了防止高温烧结过程中磁体表面层稀土挥发,在升至目标烧结温度后向烧结炉内充30kpa的氩气,保温时间为6h。
[0124]
烧结后的磁体需进行两级时效工艺,磁体首先在860℃进行3h的一级时效处理工艺,然后以不低于20℃/min的速度冷却至低于100℃,再加热至520℃进行3h的二级时效处理,结束后以不低于30℃/min的速度冷却至低于80℃。
[0125]
采用sem观察磁体显微组织,图4(a)和(b)分别为经过高温热处理和未经过高温热处理sc片的显微组织。从图中可以发现未经过高温热处理的sc片的组织不存在zr化物,当sc片经过1000℃
×
2h的高温热处理后在富r相中出现了团簇的细纤维状zr化物。这些zr化物会在随后的制粉工艺中破碎并与磁粉均匀混合,起到类似双合金粉末混合的效果。
[0126]
采用三点弯曲的方法测试磁体的抗弯强度,每组测量10个数据并计算平均值。在sem的背散模式下统计面积为1000μm
×
1000μm范围内析出物的数量与分布,具体结果如表8所示。
[0127]
表8
[0128]
实验no.sc片是否经过高温热处理抗弯强度(mpa)分布于主相晶粒内部析出物占比(%)30是6150.2531否4809.5
[0129]
图5为实验no.31磁体的显微组织,结合表8数据可以发现经过sc片高温热处理工
序的磁体中zr化物主相分布在晶界相中,而未经过sc片高温热处理的磁体中相当大比例的zr化物分布在主相晶粒内部。同时实验no.30磁体的抗弯强度要明显高于实验no.31的磁体。
[0130]
对于实验no.30的磁体,sc片在氢破前经过了高温热处理,促使zr化物在sc片中析出,在后续的合金粉末制备过程中这些zr化物会发生一定程度的破碎并与磁粉均匀的混合起来。这个过程类似与双合金粉末混合的效果,但本方法得到的粉末存在zr化物的形态一致性高、尺寸均匀,并且无杂质引入的优势。在后续的烧结过程中这些zr化物会发生长大,由纤细的纤维状长呈棒状并存在于磁体晶界相中,通过强化磁体晶界富r相的方法提高磁体的力学性能。
[0131]
对于实验no.31的磁体,由于没有经过sc片的高温热处理,zr化物只能在烧结阶段从磁体中析出,这个阶段的zr化物析出过程伴随着磁体致密和主相晶粒长大,在此阶段析出的zr化物容易被包裹在主相晶粒内部。因此实验no.31磁体中存在于主相晶粒内部的析出物比例要远高于实验no.30的情况。这些存在于主相晶粒内部的析出物会在主相晶粒内部造成裂纹,从而降低磁体的力学性能。
[0132]
实施例五:
[0133]
对于低熔点金属以纯度为99.9wt.%以上的纯金属作为原料,对于熔点高于纯铁的元素则以该元素与铁的合金作为原料。依照熔点从高到低的顺序依次放入坩埚中,炉内抽真空直到真空度达10-4
pa,露点低于-50℃。之后向炉内充氩气使气压达到30kpa,并加热至1490℃,待原材料完全熔化后保温3min。之后将合金液温度降至1450℃,并进行浇铸。调整铜辊转速为70转/分钟,然后按照一定速度转动坩埚,使熔融合金液经过中间包输送到冷却辊上进行凝固随后掉落到水冷盘上降温,得到厚度为0.25
±
0.05mm的合金片。
[0134]
对熔炼制备的sc片进行高温热处理。将熔炼制得得合金片放置在钼舟中,置于加热炉内。将炉内真空度抽到10-4
pa并加热到1000℃,当温度达到目标温度时向炉内充30kpa压力得氩气,保温2h。热处理完成后随炉冷却至室温。
[0135]
合金片在0.09mpa氢气压力下进行吸氢反应,吸氢反应结束后边抽真空边升温至550℃,保温4h使合金片中的氢气脱出,随后冷却得到氢破碎的粗粉。冷却后向粗粉中加入0.05wt.%硬脂酸锌并混合3h,利用氮气气流磨对粗粉进一步破碎得到细粉,气体压力为0.6mpa。将气流磨后的细粉采用粉末分级装置进一步进行筛分,使smd处于3.0~6.0μm范围内的粉末颗粒占比95%以上。
[0136]
在细粉中添加0.03wt.%的有机润滑剂(天津市悦圣新材料研究所生产磁粉保护润滑剂3#)并混合3h。混合均匀后的细粉在磁场下取向成型,取向磁场为3.5t的静磁场,压制压力为5mpa,压制后磁体密度为3.9~4.0g/cm3。之后进行冷等静压,压制压力为160mpa,压制后磁体密度大于4.6g/cm3。
[0137]
采用真空烧结工艺将磁体烧结致密。所述真空烧结工艺为在10-4
pa真空度下,以7.53g/cm3作为烧结磁体的最低要求,烧结温度为1100℃,为了防止高温烧结过程中磁体表面层稀土挥发,在升至目标烧结温度后向烧结炉内充30kpa的氩气,保温时间为6h。
[0138]
烧结后的磁体需进行两级时效工艺,磁体首先在860℃进行3h的一级时效处理工艺,然后以不低于20℃/min的速度冷却至低于100℃,再加热至520℃进行3h的二级时效处理,结束后以不低于30℃/min的速度冷却至低于80℃。
[0139]
将磁体破碎后在中心取样,利用icp-ms检测磁体成分。采用内圆切片机、双面磨的方式制备三点弯曲样品,按照gb/t31967.2-2015规定采用三点弯曲的方法测量磁体的抗弯强度。每组实验测量10只样品并计算平均值。采用线切割、双面磨和端面磨的方法制备磁性能测量样品,样品为φ10mm
×
10mm圆柱,利用nim设备测量磁体磁性能。
[0140]
各实验组磁体成分采用质量分数表示,具体如表9所示:
[0141]
表9
[0142]
no.ndprfealdycocugabzr3230.60.5bal10.50.10.150.10.96/3330.60.5bal10.50.10.150.10.960.63431.1/bal10.50.10.150.10.960.63531.60.5bal/0.50.10.150.10.960.63630.750.5bal10.50.1/0.10.960.63730.70.5bal10.50.10.15/0.960.6
[0143]
磁体力学性能及矫顽力如表10所示:
[0144]
表10
[0145]
no.抗弯强度(mpa)矫顽力(koe)3236020.133361820.093460219.653561318.243659619.803762019.74
[0146]
本实施例中通过对磁体的成分进行调整,选择性不添加pr、al、cu、ga中的某些元素,未添加的量以同等重量百分比的nd取代。结合磁体成分以及力学性能和矫顽力数据可知对于zr含量为0.6wt.%的磁体,pr、al、cu和ga等元素含量的变化并不会影响磁体的抗弯强度,但是会在较大程度上影响磁体的磁性能。对于添加0.6wt.%zr的磁体,如果磁体综合添加了al、ga、cu、pr元素,则磁体的矫顽力与未添加zr的磁体基本相同。而这四种元素中某一种元素的缺失都会导致磁体的矫顽力有较大的降低。因此本实验通过zr化物增强磁体力学性能时必须综合添加这四种元素以保证磁体的矫顽力不发生降低。
[0147]
本发明中形貌呈棒状的zr化物分布于晶界富r中,通过强化晶界富r相的方法提高磁体的力学性能。但是棒状的zr化物分布于晶界相中时会阻碍二级时效过程中晶界相的流动与分布,因此会降低磁体的矫顽力。文献表明在r-t-b磁体中使用一定量的pr替代nd后,pr元素主要分布在晶界相中。结合低熔点元素al、cu、ga的综合添加能够显著的降低晶界相的熔点,增强晶界相与主相的润湿性,从而改善二级时效过程中晶界相的分布能力,提高磁体的矫顽力。