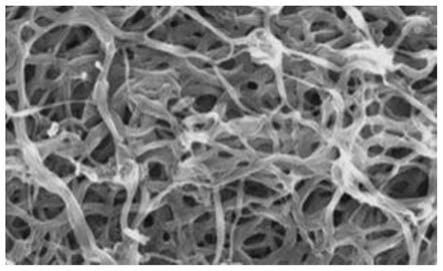
1.本发明涉及燃料电池技术领域,具体涉及一种燃料电池用复合质子交换膜的制备方法。
背景技术:2.燃料电池是一种用于将氢气、天然气或其它碳氢化合物燃料中的电化学能转化为电能的能量转化装置,是氢能的主要利用方式。不同于以储能的方式提供电能的传统蓄电池,燃料电池依靠外部燃料和氧气的稳定供应而持续产生电能。与传统的能源利用方式相比,燃料电池不需要直接燃烧,从而避免了卡诺循环的限制,具有能量转化效率高、污染小、噪声小等诸多优势,被认为是一种潜力巨大的能源利用方式。燃料电池将广泛应用于汽车、飞机、列车等交通工具以及固定电站等方面。
3.膜电极作为燃料电池发电装置和电解水制氢装置的核心零部件,是发生电化学反应的场所、传递电子和质子的介质以及反应气体、尾气和液态水紧密接触的场所。膜电极通常由质子交换膜、阴极催化层、阳极催化层、防水碳层涂敷的气体扩散层这五层组成,通常采用ccm法制备而成。所谓ccm法,是将催化层浆料涂布在质子交换膜的两侧后,再通过热压法将气体扩散层压合到涂覆有催化剂的质子交换膜两侧,由此形成膜电极。此方法具有生产效率高、载铂量低的优点。但是在已成型的质子交换膜上涂覆催化层,使得质子交换膜容易因催化剂浆料溶胀而造成催化剂颗粒分布不均、催化剂容易脱落、附着力差的缺点,并最终降低了燃料电池的使用寿命。为改善此问题,人们通过调整催化剂浆料中溶剂含量及成分、改善涂覆干燥工艺等以期达到改善附着力的效果,也有研究人员通过复合或接枝改性来制备低溶胀质子交换膜,但这些方法均无法很好解决目前产业化过程中质子交换膜涂覆催化剂浆料溶胀的问题。
4.其中,专利cn101942672b介绍了通过“热定型法”将质子交换膜加热到玻璃化温度
±
20℃的范围内,再进行催化剂浆料的流延、印刷或喷涂。催化剂浆料中的溶剂在高温下瞬间挥发,不会造成质子交换膜发生溶胀,且提高了催化剂的附着力。但此方法无法控制膜材的温度均匀性,
±
20℃的温度严重影响膜的均匀性。专利cn111009667b介绍了通过将催化剂涂覆在质子交换膜a面后,催化剂面复合保护膜,继续在质子交换膜上复合b面的方法,但是复合保护膜的方法,仍无法解决催化剂在质子交换膜上的附着力问题。
技术实现要素:5.为了克服现有技术的不足,本发明的目的在于提供一种燃料电池用复合质子交换膜的制备方法,该制备方法可使催化剂均匀分布在质子交换膜的表面上,并有效改善了催化剂颗粒在质子交换膜上的附着力,提高了厚度均匀性。
6.为解决上述问题,本发明所采用的技术方案如下:
7.一种燃料电池用复合质子交换膜的制备方法,其包括以下步骤:
8.s1、全氟磺酸树脂溶液的制备:将f
+
型全氟磺酸树脂颗粒进行h
+
型化处理,使其转
换为h
+
型全氟磺酸树脂后,加入到装有水和高沸点溶剂加热搅拌溶解,制得全氟磺酸树脂溶液;
9.s2、催化剂浆料的制备:取步骤s1制得的全氟磺酸树脂溶液,加入水、高沸点溶剂、表面活性剂和催化剂pt
40
/c
60
,超声分散10-20min,得到催化剂浆料;
10.s3、复合质子交换膜的制备:将步骤s1制得的全氟磺酸树脂溶液涂覆在基材表面上,在50~80℃下预干燥1-3min,以去除水,得到粘弹态质子交换膜;将步骤s2制得的催化剂浆料涂覆在粘弹态质子交换膜的表面上,在50~70℃下进行一次干燥1-3min,以去除水;然后在100~120℃下进行二次干燥3-10min,得到复合质子交换膜。
11.作为本发明优选的实施方式,所述h
+
型化处理是依次对f
+
型全氟磺酸树脂颗粒碱洗、水洗、酸洗、水洗、烘干而得到h
+
型全氟磺酸树脂。
12.作为本发明优选的实施方式,所述h
+
型化处理具体包括如下步骤:将f
+
型全氟磺酸树脂颗粒置于碱液中在60-100℃下浸泡16-24h进行水解处理,在去离子水中于40~80℃下浸泡5-10h至中性,然后在酸性溶液中浸泡4-8h,重复6~8次,用去离子水洗涤,过滤烘干,即得h
+
型全氟磺酸树脂。
13.作为本发明优选的实施方式,所述步骤s1中水与高沸点溶剂的质量比为5~20:1。
14.作为本发明优选的实施方式,所述步骤s2中各组分的质量份数为:催化剂pt
40
/c
60 1-3份、全氟磺酸树脂溶液2-5份、水40-90份、高沸点溶剂5-15份、表面活性剂0.01-0.2份。
15.作为本发明优选的实施方式,所述全氟磺酸树脂溶液和催化剂浆料中的高沸点溶剂的质量分数均为5~15%。
16.作为本发明优选的实施方式,所述高沸点溶剂为3-甲氧基-3-甲基-1-丁醇(mmb)、二丙酮醇、乳酸乙酯、乙二醇丁醚、丙二醇丁醚、丙二醇丙醚、二丙二醇甲醚、乙二醇苯醚、丙二醇苯醚中的一种。
17.作为本发明优选的实施方式,所述表面活性剂为triton x-45、triton x-100、triton x-140、美国空气化工公司生产的炔二醇类表面活性剂dynol 604和dynol 607、dupont生产的氟碳表面活性剂fso-100和fs-3100中的一种。
18.作为本发明优选的实施方式,所述基材为pet(聚对苯二甲酸乙二酯)膜、pe(聚乙烯)膜、pp(聚丙烯)膜、pvdf(聚偏二氯乙烯)膜、ptfe(聚四氟乙烯)膜中的一种。
19.本发明还提供了一种燃料电池用复合质子交换膜,其是由上述的制备方法制得的。
20.相比现有技术,本发明的有益效果在于:
21.本发明通过在全氟磺酸树脂溶液和催化剂浆料中分别添加高沸点溶剂,并通过低温将水去除,少量残留的高沸点溶剂使得质子交换膜处于粘弹态,将含有高沸点溶剂的催化剂浆料涂覆在质子交换膜表面,低温下继续将水除去,然后高温干燥,形成复合质子交换膜,通过此湿式粘合法,很好地避免了质子交换膜涂覆催化剂浆料制备膜电极过程中产生的溶胀问题,使得催化剂可均匀分布在质子膜表面,并有效改善了催化剂颗粒在质子交换膜上的附着力,提高厚度均匀性。
附图说明
22.图1为本发明实施例1所制得的复合质子交换膜的显微镜图;
23.图2为本发明对比例1所制得的质子交换膜的显微镜图;
24.图3为本发明对比例2所制得的质子交换膜的显微镜图。
具体实施方式
25.下面结合具体实施方式对本发明作进一步详细说明。
26.一种燃料电池用复合质子交换膜的制备方法,其包括以下步骤:
27.s1、全氟磺酸树脂溶液的制备:将f
+
型全氟磺酸树脂颗粒进行h
+
型化处理使其转换为h
+
型全氟磺酸树脂:依次对f
+
型全氟磺酸树脂颗粒碱洗、水洗、酸洗、水洗、烘干。具体步骤如下:将f
+
型全氟磺酸树脂颗粒置于碱液中在60-100℃下浸泡16-24h进行水解处理,在去离子水中于40~80℃下浸泡5-10h至中性,然后在酸性溶液中浸泡4-8h,重复6~8次,用去离子水洗涤,过滤烘干,即得h
+
型全氟磺酸树脂。然后加入到装有水和高沸点溶剂的反应釜中加热搅拌溶解,制得全氟磺酸树脂溶液。
28.以上步骤中,高沸点溶剂为3-甲氧基-3-甲基-1-丁醇(mmb)、二丙酮醇、乳酸乙酯、乙二醇丁醚、丙二醇丁醚、丙二醇丙醚、二丙二醇甲醚、乙二醇苯醚、丙二醇苯醚中的一种。
29.s2、催化剂浆料的制备:取步骤s1制得的全氟磺酸树脂溶液,加入催化剂pt
40
/c
60
、水、高沸点溶剂和表面活性剂,超声分散,得到催化剂浆料。其中,各组分的质量份数为:催化剂pt
40
/c
60 1-3份、全氟磺酸树脂溶液2-5份、水40-90份、高沸点溶剂5-15份、表面活性剂0.01-0.2份。表面活性剂为triton x-45、triton x-100、triton x-140、美国空气化工公司生产的炔二醇类表面活性剂dynol 604和dynol 607、dupont生产的氟碳表面活性剂fso-100和fs-3100中的一种。
30.步骤s1和s2中全氟磺酸树脂溶液和催化剂浆料中的高沸点溶剂的质量分数均为5~15%。
31.s3、复合质子交换膜的制备:将步骤s1制得的全氟磺酸树脂溶液涂覆在基材表面上,在50~80℃下预干燥1-3min,以去除水,得到粘弹态质子交换膜;将步骤s2制得的催化剂浆料涂覆在粘弹态质子交换膜的表面上,在50~70℃下进行一次干燥1-3min,以去除水;然后在100~120℃下进行二次干燥3-10min,得到复合质子交换膜。
32.步骤s3中所用的基材为pet(聚对苯二甲酸乙二酯)膜、pe(聚乙烯)膜、pp(聚丙烯)膜、pvdf(聚偏二氯乙烯)膜、ptfe(聚四氟乙烯)膜中的一种。
33.实施例1:
34.一种燃料电池用复合质子交换膜的制备方法,其包括以下步骤:
35.s1、全氟磺酸树脂溶液的制备:
36.①
将f+型全氟磺酸树脂颗粒料于质量分数为15%的氢氧化钾水溶液中,在90℃浸泡20小时,进行水解处理,得到k+型全氟磺酸树脂颗粒料。之后用去离子水在60℃浸泡5小时至中性,再投入到2mol/l的盐酸水溶液中,浸泡4小时,重复6次。用去离子水洗涤颗粒料,过滤烘干,得到h+型全氟磺酸树脂(pfsa);
37.②
将上述颗粒料与由水和mmb按8:1的质量比放入密闭高压釜中,150℃下加热搅拌溶解4小时,冷却后得到质量分数为25%的全氟磺酸树脂(pfsa)溶液。
38.s2、催化剂浆料的制备
39.取部分上述质量分数为25%的pfsa溶液,按pt
40
/c
60
:pfsa:水:mmb:triton x-45
=2:3:40:5:0.1的质量比加入水、mmb、催化剂pt
40
/c
60
,超声分散2h,得到固体含量为10%的催化剂浆料。
40.s3、复合质子交换膜的制备
41.a.将上述质量分数为25%的全氟磺酸树脂(pfsa)溶液涂覆在光学级pet基材上,使用鼓风式烘箱在60℃预干燥2min以除去水,得到厚度为25um的粘弹态质子交换膜;
42.b.将催化剂浆料涂覆在粘弹态质子交换膜表面,使用鼓风式烘箱在60℃一次干燥2min除去水,最后在110℃下二次干燥5min,以形成干厚为1um的催化剂层,即得复合质子交换膜。
43.实施例2~6:
44.实施例2~6与实施例1的区别在于:步骤s3中的预干燥温度不同,具体组分如表1所示,其他组分、步骤及参数均相同。
45.表1实施例1~6步骤s3的干燥温度
46.项目预干燥温度一次干燥温度二次干燥温度实施例160℃60℃100℃实施例240℃60℃100℃实施例350℃60℃100℃实施例470℃60℃100℃实施例580℃60℃100℃实施例690℃60℃100℃
47.实施例7~10:
48.实施例7~10与实施例1的区别在于:步骤s3中的一次干燥温度不同,具体见表2,其他组分、步骤及参数均相同。
49.表2实施例7~10步骤s3的干燥温度
50.项目预干燥温度一次干燥温度二次干燥温度实施例160℃60℃100℃实施例760℃40℃100℃实施例860℃50℃100℃实施例960℃70℃100℃实施例1060℃80℃100℃
51.实施例11~14:
52.实施例11~14与实施例1的区别在于:步骤s3中的二次干燥温度不同,具体见表3,其他组分、步骤及参数均相同。
53.表3实施例11~14中步骤s3的干燥温度
54.项目预干燥温度一次干燥温度二次干燥温度实施例160℃60℃100℃实施例1160℃60℃90℃实施例1260℃60℃110℃实施例1360℃60℃120℃
实施例1460℃60℃130℃
55.实施例15:
56.本实施例与实施例1的区别在于:将实施例1中的mmb全部替换为丙二醇丁醚,其他组分、步骤及参数均相同。
57.实施例16:
58.本实施例与实施例1的区别在于:将实施例1中的mmb全部替换为二丙酮醇,其他组分、步骤及参数均相同。
59.对比例1:
60.本对比例与实施例1的区别在于:将实施例1中的mmb全部替换为乙醇,其他组分、步骤及参数均相同。
61.对比例2:
62.一种质子交换膜的制备方法,其包括以下步骤:
63.按照现有ccm工艺,使用催化剂浆料,对市售的质子交换膜(厚度25um),直接进行涂覆加工,制得质子交换膜。
64.性能对比实验:
65.对实施例1~16及对比例1~2进行附着力测试和厚度测试,并测定催化剂的分布均匀性。其中,具体测定方法如下:
66.附着力测试方采用胶带剥离法,用3m610胶带测试催化剂层与质子交换膜的附着力,并判断催化剂层脱落百分比;
67.催化分布均匀性通过显微镜进行观察判断,并对实施例1与对比例1~2的质子交换膜进行对比,结果如图1~图3所示。
68.厚度均匀性测试方法参照:gb/t 20042.5-2009质子交换膜燃料电池第5部分:膜电极测试方法中进行。
69.结果表4所示。
70.表4实施例1~16及对比例1~2性能对比实验结果
71.[0072][0073]
由表4可知,实施例1~6的预干燥温度在60℃及以上时,催化剂层附着力脱落均可不超过5%,但温度高于60℃时候厚度偏差会提高至1um。同样的,实施例7~10的一次干燥温度在60℃及以上时,催化剂层附着力脱落均不超过5%,但温度高于60℃时候厚度偏差会提高至1um。实施例11~14的二次干燥温度在100℃及以上时,催化剂层附着力脱落均不超过5%,但温度高于100℃时候厚度偏差会提高至1um。实施例15~16采用了与实施例1不同的高沸点溶剂,虽然附着力或厚度偏差不如实施例1好,但在催化剂分布上也同样仍比对比例1和2分布均匀。由图1~图3可知,实施例1的质子交换膜中催化剂分布均匀,其均匀性优于对比例1和2:对比例1中的高沸点溶剂mmb替换为低沸点溶剂乙醇,但仍具有较好的催化剂分散性,可见使用本发明工艺仍能有效改善催化剂分散性;而对比例3中,按照传统的工艺技术,催化剂颗粒团聚明显。由此可证,本发明的制备方法使得催化剂可均匀分布在质子膜表面,并有效改善了催化剂颗粒在质子交换膜上的附着力,提高厚度均匀性。
[0074]
综上所述,本发明通过湿式粘合法将催化剂层复合在粘弹态质子交换膜上,有效改善了催化剂分布均匀性和厚度均匀性,提高了催化剂颗粒的附着力,很好地避免了质子交换膜涂覆催化剂浆料制备膜电极过程中产生的溶胀问题。
[0075]
上述实施方式仅为本发明的优选实施方式,不能以此来限定本发明保护的范围,本领域的技术人员在本发明的基础上所做的任何非实质性的变化及替换均属于本发明所要求保护的范围。