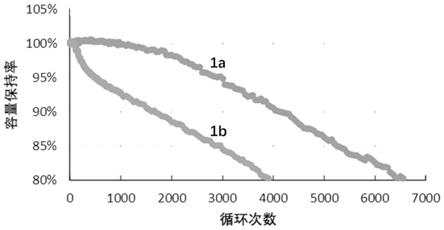
1.本发明涉及一种锂离子电池及其充电方法。
背景技术:2.锂离子电池是一种依靠锂离子在正负极之间来回移动的一种二次电池,在充电过程中,正极中的锂离子脱出,迁移至负极并嵌入负极材料中;放电时则正好相反,锂离子从负极材料中脱出,然后嵌入正极材料中。锂离子电池(lib)是目前综合性能表现最好的电池体系,具有高比能量、高循环寿命、体积小、质量轻、无记忆效应、无污染等独有优势,现阶段已迅速发展成为新一代储能电源,广泛应用于信息技术、电动汽车、航空航天、储能等领域。锂离子电池依据正极材料可以分为三元、磷酸铁锂、锰酸锂等类型。
3.目前锂离子电池设计上,为了防止电芯在充电过程中负极发生析锂,负极可接受锂离子的空位要大于正极可脱出的锂离子量,即要求负极的首次嵌锂容量要高于正极首次脱锂容量,即n/p比》1(也称为cb值)。
4.中国专利cn111008478a中公开了一种锂离子电池最优n/p比的确定方法,通过该专利的设计方法,可以找到锂离子电池设计的最佳n/p比,其中,实施例1确定的锂离子电池最优n/p比为1.2,明显大于1。
5.由于在锂离子电池大规模生产过程中,存在正负极极片涂布重量的波动,正负极材料克容量的波动等问题,为了避免电芯出现析锂现象,目前锂离子电池生产厂家采用的n/p比通常控制在1.04~1.20之间;例如,现有的3c产品一般设计为1.04~1.08;而动力电池类则会更高,一般为1.12~1.20。但是,负极多出的4%~20%的材料,不仅增加了电池的成本,降低了电池的体积能量密度,而且在电池循环过程中也在不断的消耗锂离子,降低了电池的循环寿命,因此,无论从电池成本还是循环寿命上来说都是不利的。
技术实现要素:6.本发明克服了现有技术中锂离子电池存在成本高、能量密度低、循环性能不佳的问题,提供了一种锂离子电池的充电方法。本发明中锂离子电池的充电方法能够保证电芯的安全性,可有效防止充电过程中发生析锂,且本发明中锂离子电池的成本低,能量密度高,显著提高了循环寿命。
7.为了实现上述目的,本发明提供以下技术方案:
8.本发明提供的技术方案之一为:一种锂离子电池的充电方法,所述锂离子电池的n/p比<1.02;所述n/p比为单位面积负极极片容量与单位面积正极极片容量的比值;
9.所述锂离子电池的充电方法为限制充电电压法或限制充电容量法;
10.所述限制充电电压法包括如下步骤:
11.(a1)在所述锂离子电池正极的电压-克容量曲线上,得到所述锂离子电池的正极克容量对应的电压u1;并将所述锂离子电池的充电上限电压设置为u1;
12.(a2)当所述锂离子电池的容量衰减量为c1以上时,或者,当所述锂离子电池的容
量衰减百分比为c2以上时,将所述锂离子电池的充电上限电压由u1切换至u2;其中,u1<u2;
13.所述限制充电容量法包括如下步骤:
14.(b1)将所述锂离子电池的循环电压设置为u2,充电总容量设置为c3,并对所述锂离子电池进行充放电;其中,c3为所述锂离子电池的负极可逆容量
÷
n;
15.(b2)当所述锂离子电池的充电截止电压为u2以上时,解除所述充电总容量设置为c3的设置,并将所述锂离子电池的充电截止电压设置为u2;
16.其中,c1=所述锂离子电池的正极容量-所述锂离子电池的负极容量
÷
n;c2=[1-(n/p)
÷
n]
×
100%;n为所述锂离子电池的安全系数。
[0017]
本发明中,步骤(a1)中,所述锂离子电池正极的电压-克容量曲线可按照本领域常规方法测得,例如,采用扣式电池组装电池正极极片的半电池,并测试电压-克容量曲线。
[0018]
步骤(a1)中,所述正极克容量可为本领域常规,例如,所述正极克容量=锂离子电池的负极容量
÷n÷
正极活性物质质量,其中,n为锂离子电池的安全系数;所述n的范围可为本领域常规,优选为>1.02,更优选为1.04~1.2。
[0019]
本发明中,步骤(a2)中,优选地,当所述锂离子电池的容量衰减量为c1时,或者,当所述锂离子电池的容量衰减百分比为c2时,将所述锂离子电池的充电上限电压由u1切换至u2;其中,u1<u2。
[0020]
本发明中,步骤(b1)中,所述锂离子电池的负极可逆容量可为本领域常规,例如,所述锂离子电池的负极可逆容量=负极极片的可逆克容量
×
负极极片的面密度
×
正极极片的长度
×
正极极片的宽度
÷
n,其中,n为锂离子电池的安全系数;所述n的范围可为本领域常规,优选为>1.02,更优选为1.04~1.2。
[0021]
本发明中,步骤(a2)、步骤(b1)和步骤(b2)中,所述u2可为本领域常规的电池充电上限电压,例如3~5v。一般地,磷酸铁锂电池的充电上限电压可为3.6~3.7v,优选为3.65v;三元电池充电上限电压可为4.2~4.35v,优选为4.25v;锰酸锂电池充电上限电压可为4.2~4.35v,优选为4.2v。
[0022]
本发明中,步骤(b2)中,一般可为在充放电循环过程中,所述锂离子电池的充电截止电压大于u2时,解除所述充电总容量设置为c3的设置,并将所述锂离子电池的充电截止电压设置为u2。
[0023]
步骤(b2)中,优选地,当所述锂离子电池的充电截止电压大于u2时,所述锂离子电池的充电总容量c3的衰减量可为c1以上,或者,所述锂离子电池的充电总容量衰减百分比为c2以上;所述c1和c2如前所述。
[0024]
本发明中,所述n/p比的计算方法可为本领域常规。例如:
[0025]
当正负极极片未经过充电或者放电时,n/p比的计算方法为(负极材料首次嵌锂容量
÷
负极活性物质含量
×
负极极片面密度)
÷
(正极极材料首次脱锂容量
÷
正极活性物质含量
×
正极极极片面密度);
[0026]
当正负极极片经过充电或者放电时,n/p比的计算方法为(负极材料可逆脱嵌锂容量
÷
负极活性物质含量
×
负极极片面密度)
÷
(正极极材料可逆脱嵌锂容量
÷
正极活性物质含量
×
正极极极片面密度)。
[0027]
其中,所述正负极极片经过充电或者放电可为本领域常规,例如从经过化成后的电芯中拆出的正负极极片。
[0028]
其中,所述n/p比的计算方法中,正负极材料的首次容量和可逆容量可采用扣式电池的测试方法,例如用金属锂片作为对电极,以正极或者负极极片作为工作电极进行容量测试。
[0029]
本发明中,所述锂离子电池的n/p比优选为0.8~1.02;更优选为0.85~1.0;例如0.9、0.95或0.98。
[0030]
其中,当正负极极片未经过充电或者放电时,所述锂离子电池的n/p比优选为0.85~1.02;更优选为0.9~1.0。
[0031]
当正负极极片经过充电或者放电时,所述锂离子电池的n/p比优选为0.8~1.0;更优选为0.85~0.98。
[0032]
本发明提供的技术方案之二为:一种锂离子电池,其充电方法如前所述。
[0033]
本发明中,所述锂离子电池的n/p比优选为0.8~1.02;更优选为0.85~1.0;例如0.9、0.95或0.98。
[0034]
本发明中,所述锂离子电池包括正极片、负极片、隔离膜和电解液。
[0035]
其中,所述正极片可为本领域常规,例如三元正极片、磷酸铁锂正极片或锰酸锂正极片。
[0036]
所述负极片可为本领域常规,例如石墨负极极片。
[0037]
所述隔离膜根据本领域常规一般位于正极片和负极片之间。
[0038]
在符合本领域常识的基础上,上述各优选条件,可任意组合,即得本发明各较佳实例。
[0039]
本发明所用试剂和原料均市售可得。
[0040]
本发明的积极进步效果在于:
[0041]
(1)本发明针对n/p比相对于现有技术大幅度降低的锂离子电池(n/p比<1.02),提供的充电方法可明显提升锂离子电池循环寿命,循环性能提升10%~80%;
[0042]
(2)本发明中n/p比<1.02的锂离子电池,在负极使用量降低的同时,降低了锂离子电池的生产成本,同时,可提高能量密度;
[0043]
(3)本发明中锂离子电池的充电方法能够保证电芯的安全性,可有效防止充电过程中发生析锂。
附图说明
[0044]
图1为实施例1与对比例1的常温(25℃)循环性能图;
[0045]
图2为实施例2与对比例2的常温(25℃)循环性能图。
具体实施方式
[0046]
下面通过实施例的方式进一步说明本发明,但并不因此将本发明限制在所述的实施例范围之中。下列实施例中未注明具体条件的实验方法,按照常规方法和条件,或按照商品说明书选择。
[0047]
实施例1
[0048]
以磷酸铁锂作为正极活性材料,全电池使用电压范围为2.5~3.65v,通过扣式电池测试,在电压范围2.0~3.75v,倍率为0.1c时,测试其首次脱锂克容量为160mah/g,首次
嵌锂克容量为157mah/g。
[0049]
以石墨作为负极材料,通过扣式电池测试,在电压范围0.005~2v,倍率为0.1c时,测试其首次嵌锂克容量为360mah/g,首次脱锂克容量为340mah/g。
[0050]
基于上述正负极材料,设计锂离子电池,其n/p比为0.9。
[0051]
计算上述锂离子电池的负极可逆容量:负极可逆容量=负极极片的可逆克容量
×
负极极片的面密度
×
正极极片的长度
×
正极极片的宽度
÷
n,计算得340mah/g
×
30.6mg/cm2×
5809mm
×
180mm
÷
1.1=98.9ah。
[0052]
对该电池进行循环测试,测试温度为25℃,测试流程如下:
[0053]
(b1)将上述锂离子电池静置30min后,设置锂离子电池的循环电压为u2(u2为3.65v),设置锂离子电池的1c充电总容量为c3(c3为98.9ah);静置30min后;1c放电至2.5v;
[0054]
(b2)
①
循环步骤(b1)的操作,直至上述锂离子电池的充电截止电压≥3.65v;其中,锂离子电池的容量衰减量为c1,c1=锂离子电池的正极容量-锂离子电池的负极容量
÷
n,120.9ah-98.9ah
÷
1.1=22.0ah;锂离子电池的容量衰减百分比为c2,c2=[1-(n/p)
÷
n]
×
100%,[1-0.9
÷
1.1]
×
100%=18.2%。
[0055]
②
静置30min;1c充电至3.65v,恒压至0.05c;静置30min;1c放电至2.5v;
[0056]
循环步骤
②
的操作,直至电池容量衰减到80%。
[0057]
对比例1
[0058]
采用与实施例1相同的材料和生产工艺制得锂离子电池,仅将n/p比调整为1.1。对制得的锂离子电池进行循环测试,测试温度为25℃,测试流程如下:
[0059]
(1)将上述锂离子电池静置30min后,1c充电至3.65v,恒压至0.05c;静置30min,1c放电至2.5v;
[0060]
(2)循环上述步骤(1)的操作,直至电池容量衰减到80%。
[0061]
实施例2
[0062]
以镍钴锰酸锂作为正极活性材料,全电池使用电压范围为2.8~4.3v,通过扣式电池测试,在电压范围2.5~4.35v,倍率为0.1c时,测试其首次脱锂克容量为218mah/g,首次嵌锂克容量为194mah/g。
[0063]
以石墨作为负极材料,通过扣式电池测试,在电压范围0.005~2v,倍率为0.1c时,测试其首次嵌锂克容量为370mah/g,首次脱锂克容量为350mah/g。
[0064]
基于上述正负极材料,设计锂离子电池,其n/p比为0.95。
[0065]
计算正极克容量:正极克容量=负极容量
÷n÷
正极活性物质质量,计算得159.1ah
÷
1.06
÷
838.5g=179mah/g;采用扣式电池组装电池正极极片的半电池,并测试电压-克容量曲线,确定正极克容量为179mah/g时,对应的充电电压u1为4.2v。
[0066]
对上述锂离子电池进行循环测试,测试温度为25℃,测试流程如下:
[0067]
(a1)将上述锂离子电池静置30min后,1c充电至4.2v,恒压至0.05c;静置30min,1c放电至2.8v;
[0068]
(a2)
①
循环步骤(a1)的操作,直至电池的容量衰减量c1达到7.0ah;其中,电池的容量衰减量c1=锂离子电池的正极容量-锂离子电池的负极容量
÷
n,计算得c1为159.1ah-161.2ah
÷
1.06=7.0ah;
[0069]
②
将上述锂离子电池静置30min后,1c充电至4.3v,恒压至0.05c;静置30min,1c放
电至u2(2.8v);循环步骤
②
的上述操作,直至电池容量衰减到80%。
[0070]
对比例2
[0071]
采用与实施例2相同的材料和生产工艺制得锂离子电池,仅将n/p比调整为1.1,对制得的锂离子电池进行循环测试,测试温度为25℃,测试流程如下:
[0072]
(1)将上述锂离子电池静置30min后,1c充电至4.3v,恒压至0.05c;静置30min,1c放电至2.8v;
[0073]
(2)循环上述步骤(1)的操作,直至电池容量衰减到80%。
[0074]
效果实施例
[0075]
实施例与对比例电芯的循环测试数据如图1和图2所示。
[0076]
图1中,1a为实施例1中锂离子电池在25℃条件下的循环衰减曲线;1b为对比例1中锂离子电池在25℃条件下的循环衰减曲线。
[0077]
由图1中的循环数据结果可以看出,实施例1中n/p比为0.9的锂离子电池,相比于对比例1中n/p比为1.1的锂离子电池,其循环性能得到了明显的提升,由4000次提升至6500次,寿命提升62.5%,即(6500-4000)/4000
×
100%=62.5%。
[0078]
图2中,2a为实施例2中锂离子电池在25℃条件下的循环衰减曲线;2b为对比例2中锂离子电池在25℃条件下的循环衰减曲线;由图2中的循环数据结果可以看出,实施例2中n/p比为0.95的锂离子电池,相比于对比例2中n/p比为1.1的锂离子电池,其循环性能得到了明显的提升,由2300次提升至2740次,寿命提升19.13%,即(2740-2300)/2300
×
100%=19.13%。
[0079]
此外,发明人经大量研究发现:对于n/p比<1.02的锂离子电池,当锂离子电池的容量衰减量为c1以上时,或者,当锂离子电池的容量衰减百分比为c2以上时,若不不采用本技术中将锂离子电池的充电上限电压由u1切换至u2的充电方式;电池会出现异常,例如,电池发生安全事故;或者,负极析锂,从而导致电池循环性能快速衰减。
[0080]
而且,由上述实施例可知,本技术在锂离子电池的生产制造过程中,并未增加任何额外的工序、材料和设备;充电方法操作简单、易行,适用于所有锂离子电池生产商。