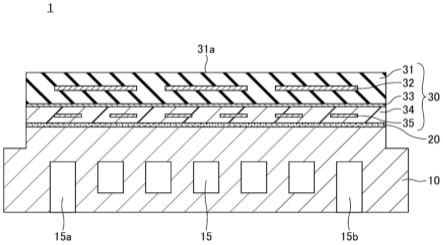
1.本发明涉及一种静电吸盘及其制造方法、以及基板固定装置。
背景技术:2.在现有技术中,在制造诸如ic、lsi等半导体器件时使用的成膜装置(例如cvd装置、pvd装置等)或等离子体蚀刻装置具有用于在真空处理室内准确地保持晶片的载物台。
3.作为这样的载物台,例如,提出了一种基板固定装置,该基板固定装置构造为通过安装在底板上的静电吸盘来吸附并保持作为吸附目标对象的晶片。静电吸盘例如具有发热体和用于使来自发热体的热量均匀化的金属层。
4.引文列表
5.专利文献
6.ptl 1:jp-a-2020-88304
技术实现要素:7.然而,近年来,要求进一步改善静电吸盘的均热性,并且现有技术的结构难以满足改善均热性的要求。
8.本发明是鉴于上述情况而完成的,其目的在于提供一种具有进一步改善的均热性的静电吸盘。
9.本公开的实施例涉及一种静电吸盘。该静电吸盘包括:
10.基体,其具有放置吸附目标对象的放置表面;
11.热扩散层,其直接形成在基体的与放置表面相反的表面上;
12.绝缘层,其在热扩散层的与基体相反的一侧布置成与热扩散层接触;以及
13.发热体,其埋入在绝缘层中,
14.其中,热扩散层由热导率高于绝缘层的材料形成。
15.根据所公开的技术,能够提供一种具有进一步改善的均热性的静电吸盘。
附图说明
16.图1是简化和例示根据本实施例的基板固定装置的截面图。
17.图2a至图2c是例示根据本实施例的基板固定装置的制造过程的视图。
18.图3a至图3c是例示根据本实施例的基板固定装置的制造过程的视图。
19.图4a和图4b是例示根据本实施例的基板固定装置的制造过程的视图。
具体实施方式
20.以下,将参照附图描述本发明的各实施例。应当注意,在各图中,用相同的附图标记表示具有相同构造的部分,并且可以省略重复的描述。
21.[基板固定装置的结构]
[0022]
图1是简化和例示根据本实施例的基板固定装置的截面图。参照图1,基板固定装置1具有的主要构成元件为:底板10、粘合层20和静电吸盘30。
[0023]
底板10是用于安装静电吸盘30的构件。底板10的厚度例如可以设定为约20mm至50mm。底板10例如由铝形成,并且还可以用作控制等离子体的电极等。通过向底板10供给预定的高频电力,能够控制用于使生成的等离子体状态的离子等与吸附在静电吸盘30上的基板碰撞的能量,并且能够有效地进行蚀刻处理。
[0024]
在底板10中设有水通道15。水通道15的一端具有冷却水引入部15a,并且另一端具有冷却水排出部15b。水通道15连接到设置在基板固定装置1外部的冷却水控制装置(未示出)。该冷却水控制装置(未示出)构造成将冷却水从冷却水引入部15a引入到水通道15中并从冷却水排出部15b排出冷却水。通过使冷却水在水通道15中循环来冷却底板10,从而能够冷却被吸附到静电吸盘30上的基板。底板10除了水通道15之外,还可以设置有气体通道等,气体通道用于引入惰性气体以用于冷却被吸附到静电吸盘30上的晶片。
[0025]
静电吸盘30是构造为吸附并保持作为吸附目标对象的晶片的部分。静电吸盘30的平面形状例如可以是圆形。作为静电吸盘30的吸附目标对象的晶片的直径例如可以为8英寸、12英寸或18英寸。
[0026]
静电吸盘30通过粘合层20安装在底板10的一个表面上。作为粘合层20,例如可以使用有机硅粘合剂。例如,可以将粘合层20的厚度设定为约2mm。粘合层20的热导率优选设定为2w/mk以上。粘合层20可以具有堆叠多个粘合层的分层结构。例如,当粘合层20由具有高热导率的粘合剂和具有低弹性模量的粘合剂组合的两层结构构成时,获得了减小由于与由铝制成的底板的热膨胀差异而产生的应力的效果。
[0027]
静电吸盘30具有基体31、静电电极32、热扩散层33、绝缘层34和发热体35。静电吸盘30例如是约翰逊
·
拉别克型(johnsen-rahbeck)静电吸盘。然而,静电吸盘30也可以是库仑力型静电吸盘。
[0028]
基体31是电介质,并且具有放置吸附目标对象的放置表面31a。作为基体31,例如,可以使用诸如氧化铝(al2o3)和氮化铝(aln)等陶瓷。基体31的厚度例如可以设定为约1mm至10mm,并且基体31的相对介电常数(khz)例如可以设定为约9至10。
[0029]
静电电极32是薄膜电极,并且埋入在基体31中。静电电极32连接到设置在基板固定装置1外部的电源,并且当从电源施加预定电压时通过静电在静电电极和晶片之间产生吸力。由此,能够将晶片吸附并保持在静电吸盘30的基体31的放置表面31a上。施加在静电电极32上的电压越高,吸附保持力越强。静电电极32可以具有单极形状或双极形状。作为静电电极32的材料,例如可以使用钨、钼等。
[0030]
热扩散层33直接形成在位于基体31的放置表面31a的相反侧的背面上。具体地,热扩散层33在没有粘合层等的情况下与基体31的背面接触。热扩散层33是用于使发热体35产生的热量均匀化并扩散的层,并且由热导率高于绝缘层34的材料形成。热扩散层33的热导率优选为400w/mk以上。作为具有这种热导率的材料,可以例举诸如铜(cu)、铜合金、银(ag)和银合金等金属、碳纳米管等。
[0031]
热扩散层33优选地形成在基体31的整个背面上。具体地,热扩散层33优选地以实心形状形成在基体31的背面上,并且优选地不具有图案或开口。通过这样做,热扩散层33可以充分地呈现改善均热性的效果。热扩散层33的厚度例如可以设定为约几nm至几百μm。热
扩散层33的下表面与绝缘层34的上表面接触。
[0032]
应当注意,在现有技术的静电吸盘中,由于作为热扩散层发挥作用的金属层等经由粘合层而固定于基体,或者金属层被图案化为预定的形状,因此无法充分地实现均热性。
[0033]
绝缘层34在热扩散层33的与基体31相反的一侧布置成与热扩散层33接触。绝缘层34是用于使热扩散层33和发热体35绝缘的层。作为绝缘层34,例如,可以使用具有高热导率和高耐热性的环氧树脂、双马来酰亚胺三嗪树脂等。绝缘层34的热导率优选设定为3w/mk以上。当绝缘层34中包含诸如氧化铝和氮化铝等填料时,可以提高绝缘层34的热导率。另外,绝缘层34的玻璃化转变温度(tg)优选设定为250℃以上。此外,绝缘层34的厚度优选地设定为约100μm至150μm,并且绝缘层34的厚度偏差优选地设定为
±
10%以下。
[0034]
发热体35埋入在绝缘层34中。发热体35的周围被绝缘层34覆盖,从而免受外部影响。发热体35构造成通过从基板固定装置1的外部施加电压而发热,并且构造成加热以使得基体31的放置表面31a变为预定温度。发热体35能够将基体31的放置表面31a的温度加热至例如约250℃至300℃。作为发热体35的材料,可以使用铜(cu)、钨(w)、镍(ni)、康铜(cu/ni/mn/fe合金)等。发热体35的厚度例如可以设定为约20μm至100μm。发热体35例如可以被图案化成同心形状。
[0035]
应当注意,为了提高发热体35与绝缘层34在高温下的粘合性,优选使发热体35的至少一个表面(上表面和下表面中的一者或两者)粗糙化。也可以使发热体35的上表面和下表面都粗糙化。在这种情况下,可以对发热体35的上表面和下表面使用不同的粗糙化方法。粗糙化方法没有特别的限制,并且粗糙化方法的实例包括利用蚀刻的方法、使用偶联剂系统的表面改性技术的方法、使用通过波长为355nm以下的uv-yag激光器的点处理(dot processing)的方法等。
[0036]
[基板固定装置的制造方法]
[0037]
图2a至图4b是例示根据本实施例的基板固定装置的制造过程的视图。下面参照图2a至图4b描述基板固定装置1的制造过程,重点描述形成静电吸盘的过程。应当注意,图2a至图4a示出了相对于图1被上下翻转的状态。
[0038]
首先,在图2a所示的过程中,通过已知的制造方法制造其中埋入有静电电极32的基体31,已知的制造方法包括对生片进行通孔加工的过程、在通孔中填充导电膏的过程、形成成为静电电极的图案的过程、堆叠并烧制其它生片的过程、使表面平坦化的过程等。
[0039]
然后,在图2b所示的过程中,将热扩散层33直接形成在基体31的一个表面上。热扩散层33可以例如使用诸如铜和银等金属通过溅射法、无电镀敷法、喷涂法等直接形成在基体31的一个表面上。热扩散层33优选形成在基体31的一个表面的整个表面上。当通过溅射法形成热扩散层33时,热扩散层33的厚度为约10nm以上且500nm以下。通过溅射法形成的热扩散层33具有均匀的膜厚度,这在改善均热性方面是非常有效的。这里,均匀的膜厚度指的是热扩散层33的最厚部分和最薄部分之间的差为10%以下的情况。
[0040]
应当注意,优选在形成热扩散层33之前对基体31进行表面处理。例如,表面处理是进行清洗或反向溅射处理(reverse sputter treatment)。例如,通过浸入纯水中、超声波清洗、用ipa置换和真空干燥来进行清洗。此外,例如,在即将进行溅射之前,通过使用ar气的反向溅射除去基体31的一个表面上的诸如碳等污垢,然后进行溅射过程。
[0041]
然后,在图2c所示的过程中,将绝缘树脂膜341直接布置在热扩散层33的与基体31
相反的一侧的表面(图2c中的上表面)上。绝缘树脂膜341是合适的,因为它可以抑制在真空中层压时夹杂空隙。绝缘树脂膜341在未固化的情况下保持半固化状态(b阶段)。绝缘树脂膜341通过处于半固化状态的绝缘树脂膜341的粘合力而临时固定在热扩散层33上。
[0042]
作为绝缘树脂膜341,例如,可以使用具有高热导率和高耐热性的环氧树脂、双马来酰亚胺三嗪树脂等。绝缘树脂膜341的热导率优选设定为3w/mk以上。当绝缘树脂膜341中包含诸如氧化铝和氮化铝等填料时,可以提高绝缘树脂膜341的热导率。另外,绝缘树脂膜341的玻璃化转变温度(tg)优选地设定为250℃以上。此外,从增强热导率性能(提高热导率)的观点来看,绝缘树脂膜341的厚度优选地设定为60μm以下,并且绝缘树脂膜341的厚度偏差优选地设定为
±
10%以下。
[0043]
然后,在图3a所示的过程中,将金属箔351布置在绝缘树脂膜341上。由于金属箔351是最终成为发热体35的层,因此金属箔351的材料与已经例举的发热体35的材料类似。考虑到通过蚀刻的布线可成形性,金属箔351的厚度优选设定为100μm以下。金属箔351通过处于半固化状态的绝缘树脂膜341的粘合力而临时固定在绝缘树脂膜341上。
[0044]
应当注意,在布置在绝缘树脂膜341上之前,优选使金属箔351的至少一个表面(上表面和下表面中的一者或两者)粗糙化。也可以使金属箔351的上表面和下表面都粗糙化。在这种情况下,可以对金属箔351的上表面和下表面使用不同的粗糙化方法。粗糙化方法没有特别的限定,并且粗糙化方法的实例包括利用蚀刻的方法、使用偶联剂系统的表面改性技术的方法、使用通过波长为355nm以下的uv-yag激光器的点处理的方法等。
[0045]
另外,在使用点处理的方法中,可以选择性地使金属箔351的必要区域粗糙化。因此,在使用点处理的方法中,不需要使金属箔351的整个区域粗糙化,并且至少,使留下作为发热体35的区域粗糙化就足够了(即,不需要使要通过蚀刻去除的区域粗糙化)。
[0046]
然后,在图3b所示的过程中,将金属箔351图案化以形成发热体35。例如,发热体35可以被图案化成同心形状。具体地说,例如,在金属箔351的整个表面上形成抗蚀剂,通过对该抗蚀剂进行曝光、显影,形成仅覆盖留下作为发热体35的部分的抗蚀剂图案。然后通过蚀刻除去未被抗蚀剂图案覆盖的部分的金属箔351。例如,在金属箔351的材料为铜的情况下,氯化铜蚀刻液、氯化铁蚀刻液等可以用作去除金属箔351的蚀刻液。
[0047]
然后,通过剥离液剥离抗蚀剂图案,从而在绝缘树脂膜341的预定位置形成发热体35(光刻法)。发热体35通过光刻法形成,使得可以减小发热体35在宽度方向上的尺寸偏差,从而改善发热分布。应当注意,通过蚀刻形成的发热体35的截面形状可以为例如大致梯形。在这种情况下,与绝缘树脂膜341接触的表面和相反表面之间的布线宽度的差可以设定为例如约10μm到50μm。通过使发热体35的截面形状为简单的大致梯形形状,可以改善发热分布。
[0048]
然后,在图3c所示的过程中,在绝缘树脂膜341上布置用于覆盖发热体35的绝缘树脂膜342。绝缘树脂膜342是合适的,因为它可以抑制在真空中层压时夹杂空隙。绝缘树脂膜342的材料可以与例如绝缘树脂膜341的材料类似。然而,绝缘树脂膜342的厚度可以在发热体35能够被覆盖的范围内适当地确定,并且不必要求与绝缘树脂膜341的厚度相同。
[0049]
然后,在图4a所示的过程中,在将绝缘树脂膜341和342按压在基体31上的同时,将绝缘树脂膜341和342加热到固化温度以上以进行固化。由此,绝缘树脂膜341和342被一体化为绝缘层34,从而形成直接结合到热扩散层33的绝缘层34。另外,发热体35的周围被绝缘
层34覆盖。考虑到恢复到室温时的应力,绝缘树脂膜341和342的加热温度优选设定为200℃以下。通过以上步骤,完成静电吸盘30。
[0050]
应当注意,通过在将绝缘树脂膜341、342按压在基体31上的同时加热并固化绝缘树脂膜341、342,可以使因发热体35的有无的影响而导致的绝缘层34的上表面(不与静电吸盘30接触的一侧的面)的凹凸(unevenness)减小并平坦化。绝缘层34的上表面的凹凸优选地设定为7μm以下。绝缘层34的上表面的凹凸设定为7μm以下,使得在下一过程中可以防止气泡被包括在绝缘层34和粘合层20之间。也就是说,可以防止绝缘层34和粘合层20之间的粘合性降低。
[0051]
然后,在图4b所示的过程中,制备预先形成有水通道15等的底板10,并且在该底板10上形成粘合层20(未固化)。然后,将图4a所示的静电吸盘30上下翻转,并且隔着粘合层20布置在底板10上,并且随后使粘合层20固化。由此,完成了其中静电吸盘30隔着粘合层20堆叠在底板10上的基板固定装置1。
[0052]
这样,在静电吸盘30中,由于在基体31的背面直接形成有热扩散层33,因此能够容易地将发热体35产生的热量均匀地传递到基体31。具体地,与在基体和金属层等之间夹置有粘合层等的现有技术的结构相比,在静电吸盘30中,能够进一步改善均热性。
[0053]
另外,热扩散层33形成在基体31的整个背面上,使得由发热体35产生的热量可以均匀地扩散到整个基体31上。此外,热扩散层33的热导率设定为400w/mk以上,使得热量可以在基体31的水平方向上快速扩散。由热扩散层33均匀扩散的热量可以均匀地加热基体31。
[0054]
此外,与通过粘贴金属箔来制造热扩散层的情况不同,直接形成在基体31的背面上的热扩散层33具有均匀的膜厚度。因此,改善均热性的效果很好。
[0055]
此外,其中埋入有发热体35的绝缘层34被布置成与热扩散层33接触,使得由发热体35产生的热量能够被有效地传递到热扩散层33。
[0056]
尽管已经详细描述了优选实施例等,但是本发明不限于上述实施例等,并且在不脱离权利要求所限定的范围的情况下,可以对上述实施例等进行各种改变和替换。
[0057]
例如,作为本发明的基板固定装置的吸附目标对象,除了半导体晶片(硅晶片等)以外,还可以例示在液晶面板等的制造过程中使用的玻璃基板等。
[0058]
本公开还涵盖例如下面描述的各种示例性实施例。
[0059]
[1]一种静电吸盘,包括:
[0060]
基体,其具有放置吸附目标对象的放置表面;
[0061]
热扩散层,其直接形成在基体的与放置表面相反的表面上;
[0062]
绝缘层,其在热扩散层的与基体相反的一侧布置成与热扩散层接触;以及
[0063]
发热体,其埋入在绝缘层中,
[0064]
其中,热扩散层由热导率高于绝缘层的材料形成。
[0065]
[2]根据[1]所述的静电吸盘,其中,热扩散层形成在基体的与放置表面相反的一侧的整个表面上。
[0066]
[3]根据[1]或[2]所述的静电吸盘,其中,热扩散层的热导率为400w/mk以上。
[0067]
[4]根据[1]至[3]中任一项所述的静电吸盘,其中,热扩散层的材料为铜、铜合金、银或银合金。
[0068]
[5]一种静电吸盘的制造方法,该制造方法包括:
[0069]
在基体的一个表面上直接形成热扩散层;
[0070]
在热扩散层的与所述基体相反的表面上直接布置第一绝缘树脂膜;
[0071]
在第一绝缘树脂膜上布置金属箔;
[0072]
对金属箔进行图案化以形成发热体;
[0073]
在第一绝缘树脂膜上布置用于覆盖发热体的第二绝缘树脂膜;以及
[0074]
固化第一绝缘树脂膜和第二绝缘树脂膜以形成直接结合到热扩散层的绝缘层,
[0075]
其中,热扩散层由热导率高于绝缘层的材料形成。
[0076]
[6]一种基板固定装置,包括:
[0077]
底板;以及
[0078]
根据[1]至[4]中任一项所述的静电吸盘,该静电吸盘安装在底板的一个表面上。