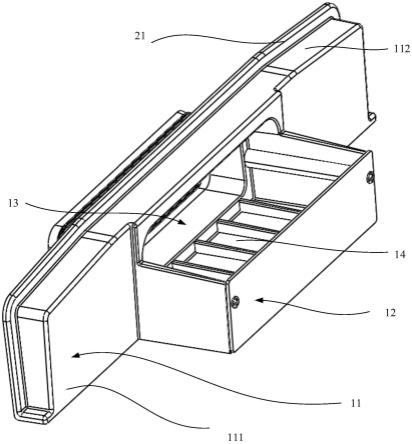
连接器加强结构及包含其的电池箱
1.本技术要求申请日为2021年12月20日的中国专利申请202111567173.8的优先权。本技术引用上述中国专利申请的全文。
技术领域
2.本实用新型涉及车辆换电技术领域,特别涉及一种连接器加强结构及包含其的电池箱。
背景技术:3.电动汽车具有零排放、低噪音、运营和维护性价比高的优点,越来越受到用户的青睐。电动汽车使用的能源为自身搭载的电池包提供的电能,电动汽车在电能使用完后需要充电。电动汽车的电池包设置方式一般分为固定式和可换式,其中,固定式电池包一般是固定在车辆上,在充电时直接以车辆作为充电对象。而可换式的电池包一般通过活动安装的方式被固定在车辆的托架上,电池包可以被取下,以单独进行更换或充电操作,在更换下的电池包充电完毕后,再安装在车辆上。
4.可换式的电池包(快换电池包)都会设有电/液连接器,在电池包与车身连接时用来与车端电/液连接器连接,对电动汽车进行供电;在电池包被从车身上更换下来后,会被送入充电站,与站端电连接连接,进行充电。在可换式的电池包的整个使用寿命中,电/液连接器需要满足连接的可靠性要求,如果连接不可靠或者连接不到位,会造成车辆报警甚至动力中断。因此,快换电池包的电/液连接器处的强度是影响快换电池包使用寿命的一个重要的因素。因此,即使金属材质存在导热系数大、保温性能差等缺点,但是市面上的快换电池包都采用金属材质电池箱,利用金属材质电池箱本身的强度来满足电/液连接器处对于强度的要求。也正是由于快换电池包对电/液连接器处强度要求较高的原因,加工性能和保温性能好、但是强度不如金属材质的非金属复合材料在快换电池包领域的应用遇到了很大的障碍。
技术实现要素:5.本实用新型要解决的技术问题是为了克服现有技术的非金属复合材料箱体在电/液连接器接口处强度低的缺陷,提供一种连接器加强结构及包含其的电池箱。
6.本实用新型是通过下述技术方案来解决上述技术问题:
7.一种连接器加强结构,其用于安装于非金属复合材料的箱体内,所述连接器加强结构包括:第一加强部,所述第一加强部用于环绕于所述箱体的连接器预留口的周侧,并连接所述箱体的内侧表面;第二加强部,所述第二加强部连接于所述第一加强部,至少由所述第二加强部围成空腔,所述空腔用于在所述第一加强部处连通至所述连接器预留口,所述空腔具有朝上设置的开口。
8.在本方案中,通过设置连接器加强结构,将连接器加强结构分为第一加强部和第二加强部,将第一加强部设置在箱体内侧靠近连接器预留口的位置上即将第一加强部环绕
箱体的连接器预留口的周侧上,让第一加强部与箱体连接,可以实现第一加强部和箱体的内侧表面的连接的稳定性和可靠性。能够对连接器安装周围区域进行加强,提升连接器工作的可靠性,促进复合材料非金属电池箱在快换电池包领域的应用。
9.设置第二加强部,并将第二加强部和第一加强部连接,并利用第二加强部和第一加强部共同在连接器预留口处形成一空腔,该空腔用于阻挡箱体内灌注的胶体,能够在靠近箱体的连接器预留口处形成一个连通箱体的连接器预留口的隔离区域,避免对电池箱灌注导热胶(用于促进电池包内部温度均衡,避免热失控)时,胶液流入到空腔内,进而避免了胶体的流动堵塞连接器预留口,并且将该空腔和连接器预留口连通形成一个通道,该隔离区域和该通道可以用于实现后续的电池缆线布置等工作。
10.较佳地,所述空腔由所述第一加强部和所述第二加强部共同围成,所述第一加强部和所述第二加强部通过粘接或焊接的方式与所述箱体连接。
11.在本方案中,采用这种第一加强部和第二加强部共同围设的结构,可以节约连接器加强结构的用料,且可以提高该连接器加强结构的整体强度。而且,通过围设形成的空腔也可以用于装载其他部件,在实现该空腔用于阻挡灌注的胶体时,也能实现将该空腔用于布置后续的电池缆线等工作,可以做到同一个空腔达到两种目的,增大该空腔的利用率,实现一物两用的作用。同时,采用粘接或焊接的方式将箱体分别第一加强部、第二加强部粘接或焊接在一起,相对于其他的连接方式,采用粘接或焊接的方式可以使得第一加强部和第二加强部相对箱体的固定面积更大,进而使得第一加强部和第二加强部与箱体之间相互加强,可以提高整个组合体的结构强度。
12.较佳地,所述开口的边缘高度被设置为高于所述箱体内的灌胶高度。
13.在本方案中,将空腔设置一个具有朝上的开口结构,且将该开口的边缘高度高于箱体内灌注的胶体的高度。通过该结构设计,在往箱体内灌注胶体的过程中,无需考虑胶体会溢流、蔓延至空腔内等可能性。因此,在连接器预留口处设置连接器加强结构的箱体,在实施往箱体内灌注胶体的步骤中,可以有效的降低该步骤的实施难度,并且可以大幅度的提高实施的成功率。
14.较佳地,所述第一加强部包括:背板,所述背板与所述箱体的内侧表面间隔设置;延伸结构,所述延伸结构从所述背板边缘朝向所述箱体的内侧表面延伸,并与所述背板围成开口朝向所述箱体内侧表面的镂空部,所述延伸结构在所述箱体的内侧表面处具有折边,所述折边与所述箱体的内侧表面相贴合,并通过粘接或焊接与所述箱体连接;加强筋,所述加强筋位于所述延伸结构与所述背板围成的所述镂空部内,所述加强筋形成于所述背板的表面,所述加强筋的端部连接于所述延伸结构的表面。
15.在本方案中,在箱体的内侧表面上朝向箱体的内部延伸,在延伸一段距离后设立背板阻止其继续延伸,以此从箱体的内侧表面延伸出的这段结构为延伸结构,所以背板和箱体的内侧表面之间延伸的距离便是延伸结构延伸出的长度,也就是上述所述的背板与箱体的内侧表面间隔设置。将该延伸结构朝向箱体的内侧表面设置为镂空部,可以在节约用料的同时增强延伸结构的整体强度,且将延伸结构与箱体的内侧表面的连接处设置成折边结构,该折边与箱体的内侧表面相贴合,可增大延伸结构和箱体的内侧表面的接触面积,并将折边采用粘接或焊接的方式实现延伸结构和箱体的内侧表面连接,使得第一加强部与箱体之间的连接相互加强,进而可以提高整个组合体的结构强度。同时,将延伸结构朝向箱体
的内侧表面设置为镂空部,且在镂空部内设置加强筋,该加强筋设置在背板朝向箱体内侧表面上,加强筋的一端和箱体的内侧表面连接,另一端和背板连接。在节省用料的同时,可以加强延伸结构在与箱体的内侧表面连接时的变形度,且增强了与其连接的稳定性和可靠性。所以,将第一加强部采用上述结构形式,不仅能提高第一加强部和箱体的连接强度,也能进一步提高自身的整体强度。
16.较佳地,所述第二加强部具有围板,所述围板用于在所述箱体的内侧将所述连接器预留口包围,所述围板的顶端高度高于所述箱体内的灌胶高度,且所述围板的底端延伸至所述箱体内部的底面。
17.在本方案中,将连接器预留口设置在箱体的侧面,并采用第二加强部将连接器预留口包围起来,第二加强部与第一加强部之间形成空腔,连接器预留口和空腔连通,避免阻挡后续电池缆线等工作。第二加强部是通过设置围板将第一加强部围挡起来形成空腔的,设置为围板的好处是,可以增强第二加强部连接的稳定性和可靠性。在往箱体内进行灌注胶体的过程中,胶体具有流动性,会蔓延至连接器预留口处,并堵塞住连接器预留口,所以将围板顶端的高度高于箱体的灌注胶体的高度,并将围板的底端延伸至箱体内的底面上,到后续需要灌注胶体时,围板则可以有效的阻挡住胶体的蔓延和流动,避免胶体流动到空腔内。也无需考虑到胶体是否会溢流至空腔内并堵塞连接器预留口等问题。因此,对于采用该连接器加强结构的箱体,在实施朝向箱体内灌注胶体的步骤时,可有效降低该步骤的实施难度,提高实施成功率。
18.较佳地,所述围板包括:两块侧板,两块所述侧板靠近所述箱体的内侧表面的一端分别连接于所述第一加强部,所述侧板的另一端朝向所述箱体的内部并在所述箱体内延伸;端板,所述端板的两端分别连接两块所述侧板朝向所述箱体的内部并在所述箱体内延伸的一端。
19.在本方案中,围板包括两侧的侧板和中间的端板,两块侧板和中间的端板共同与第一加强部连接围成空腔。两块侧板靠近箱体的内侧表面的一端与第一加强部连接,两块侧板的另一端即朝向箱体的内部的一端共同与端板连接。采用这种结构形式,可以更好的组成封闭式空腔,进一步隔离胶体的蔓延。且这种端板和两块侧板采用可拆卸连接的方式,降低了端板和侧板的加工难度,且便于工作人员更换端板和侧板。
20.较佳地,所述第二加强部还包括:底板,所述底板位于两块所述侧板的下方,所述底板的一侧表面分别与两块所述侧板连接,所述底板的另一侧表面用于与所述箱体的底面连接。
21.在本方案中,通过在两块侧板的下方设置底板,使得底板的下表面和箱体的底面连接,则第二加强部和箱体的下表面为多点连接,通过增大第二加强部和箱体下表面的接触面积,不仅可以实现自身结构的强度增加,也能增强整个连接器加强结构和箱体连接的稳定性和牢固性。
22.较佳地,所述连接器加强结构还包括第三加强部,所述第三加强部与所述第一加强部连接,所述第三加强部围成用于穿过所述连接器预留口的通道,所述通道与所述空腔连通。
23.在本方案中,第三加强部插入连接器预留口中,且将第三加强部和第一加强部连接,则第三加强部与连接器预留口形成通道,并将该通道与空腔连通,可以使得箱体内部的
电池缆线可以从箱体内部自由伸出至空腔内,再从空腔内穿过该通道伸出至箱体的外部。设置空腔的目的如上所述,不仅可以用来阻挡灌注的胶体的蔓延,还可以用于放置或排布箱体内部的电池缆线等。所以通过该结构设置,可以实现对电池缆线从箱体的内部伸出至箱体的外部的过程中的进一步保护。同时,将第三加强部和第一加强部连接,可以增强连接器加强结构的自身整体的结构强度以及与箱体连接的强度。
24.较佳地,所述第三加强部与所述第一加强部一体成型。
25.在本方案中,将第三加强部和第一加强部设置成一体成型的结构,通过增大第一加强部和第三加强部连接的接触面积,可以使得增大整个连接器加强结构的结构强度与刚性,也进而提高了整个连接器加强结构和箱体连接的强度与刚性,可以更好的实现连接器加强结构在连接器预留口处的连接强度,则可以更加有效的保护箱体内部的电池缆线向箱体外部的自由延伸。同时,第三加强部和连接器预留形成的通道的长度方向与第一加强部内的镂空部上的加强筋方向一致,均为箱体的内侧表面的径向垂直方向,更加便于在该通道内进行抽芯,从而可以使得第三加强部与第一加强部的一体成型结构在成型工艺上更加方便。
26.较佳地,所述连接器加强结构还包括保温材料,所述保温材料设置于所述空腔内。
27.在本方案中,保温材料可以至少包括保温棉或保温毡,或者类似物等柔性轻质保温材料,填充于空腔内。通过在空腔内设置保温材料,可以提高整个连接器加强结构的保温隔热效果。
28.一种电池箱,其包括非金属复合材料的箱体,所述电池箱还包括如上任一项所述的连接器加强结构。
29.在本方案中,将连接器加强结构安装在电池箱上,当电池箱的内部进行灌注胶体,灌注胶体的目的是:通过胶体在电池箱内的流动和蔓延,使得各个电池芯的受热均匀,减小了各个电池芯之间的温度差异,降低了电池芯受到较大的温度影响。为了阻挡胶体在箱体的内部蔓延时堵塞住连接器预留口,所以在连接器预留口处设置连接器加强结构,以此来阻挡胶体蔓延至连接器预留口处堵塞住连接器预留口。连接器加强结构在连接器预留口朝向箱体内部处形成一空腔,不仅实现了利用该空腔对胶体流动蔓延的阻挡,也对后续箱体内电池缆线伸出连接器预留口等的布置工作提供了空间。
30.较佳地,所述连接器加强结构还包括第三加强部,所述第三加强部与所述第一加强部连接,所述第三加强部围成用于穿过所述连接器预留口的通道,所述通道与所述空腔连通,所述第三加强部通过粘接或焊接与所述连接器预留口连接。
31.在本方案中,第三加强部插入连接器预留口中,且将第三加强部和第一加强部连接,则第三加强部与连接器预留口形成通道,并将该通道与空腔连通,可以使得箱体内部的电池缆线可以从箱体内部自由伸出至空腔内,再从空腔内穿过该通道伸出至箱体的外部。设置空腔的目的如上所述,不仅可以用来阻挡灌注的胶体的蔓延,还可以用于放置或排布箱体内部的电池缆线等,所以通过该结构设置,可以实现对电池缆线从箱体的内部伸出至箱体的外部的过程中的进一步保护。同时,第三加强部和第一加强部连接,可以增强连接器加强结构的整体结构强度以及与箱体的连接强度。而且,将第三加强部通过粘接或焊接的方式与连接器预留口连接,通过增大第三加强部和连接器预留口的接触面积,可以增强粘接的稳固性,也提高了整个连接器加强结构与箱体的结构强度。
32.较佳地,所述箱体包括相对层叠的内箱壳体与外箱壳体,所述连接器预留口贯穿所述内箱壳体和外箱壳体设置;所述第一加强部连接于所述内箱壳体,所述第三加强部至少连接于所述外箱壳体,并覆盖所述内箱壳体和所述外箱壳体在所述连接器预留口处的接缝。
33.在本方案中,采用上述结构设置,将箱体设置成具有多层层叠的结构,可以提高箱体内部的保温效果。在由内箱壳体与外箱壳体层叠组合形成箱体的情况下,通过第三加强部覆盖内箱壳体和外箱壳体在连接器预留口处的接缝,可以进一步提高箱体在接缝处的密封效果,保证箱体在连接器预留口处的隔热保温性能。
34.较佳地,所述箱体包括相对组合的上箱体单元和下箱体,所述箱体的连接器预留口开设于所述下箱体上。
35.在本方案中,将连接器预留口设置在下箱体上,可以便于复合材料零件的加工。
36.较佳地,第三加强部通过焊接的方式与所述下箱体连接,并连接在所述连接器预留口处。
37.在本方案中,相比于将第三加强部安装于上箱体和下箱体的中间部分,将第三加强部与下箱体连接,可以更加方便上箱体和下箱体的注塑成型的制作,且方便第三加强部和下箱体的连接。同时,采取粘接或焊接的方式将第三加强部与下箱体固定连接,可以增强连接的稳固性,也提高了整个连接器加强结构自身整体的结构强度。并且,如上述所述,将第三加强部与连接器预留口固定连接,加强了第三加强部与连接器预留口的连接,且便于第三加强部的拆卸和安装,同时提高了第三加强部和连接器预留口之间的密封性。
38.较佳地,所述电池箱还包括电连接器,所述电连接器通过与固定于箱体外的连接板相连,设置于所述连接器预留口处。在本方案中,电池箱的箱体包括内箱壳体和外箱壳体,外箱壳体包覆在内箱壳体的外侧表面上,外箱壳体又由连接板包覆,即箱体由连接板包覆。连接器加强结构的第一加强部和第二加强部在内箱壳体的内侧表面上连接,第三加强部贯穿连接器预留口,其一端和连接板连接,其另一端在内箱壳体的内侧表面上和第一加强部连接。电池箱还包括电连接器,该电连接器设置在连接器预留口处,即电连接器与箱体外侧表面的连接板连接,并插入连接器预留口与内部元件连接。
39.本实用新型的积极进步效果在于:该连接器加强结构及包含其的电池箱通过设置连接器加强结构,并将连接器加强结构分为第一加强部和第二加强部,将第一加强部设置在箱体内侧靠近连接器预留口的位置上即将第一加强部环绕箱体的连接器预留口的周侧上,让第一加强部与箱体连接,可以实现第一加强部和箱体的内侧表面的连接的稳定性和可靠性,能够对连接器安装周围区域进行加强,提升连接器工作的可靠性,促进复合材料非金属电池箱在快换电池包领域的应用;设置第二加强部,并将第二加强部和第一加强部连接,且与第一加强部围成一个空腔,该空腔用于阻挡箱体内灌注的胶体,能够在靠近箱体的连接器预留口处形成一个连通箱体的连接器预留口的隔离区域,避免胶体的流动堵塞连接器预留口,并且将该空腔和连接器预留口连通,可以用于实现后续的电池缆线布置等工作。
附图说明
40.图1为本实用新型一较佳实施例电池箱的整体结构示意图。
41.图2为本实用新型一较佳实施例电池箱另一视角的整体结构示意图。
42.图3为本实用新型一较佳实施例下箱体带连接器加强结构的结构示意图。
43.图4为本实用新型中图3中a处的局部放大图。
44.图5为本实用新型一较佳实施例下箱体的结构示意图。
45.图6为本实用新型一较佳实施例下箱体另一视角的结构示意图。
46.图7为本实用新型中图6中b处的局部放大图。
47.图8为本实用新型一较佳实施例连接器加强结构的整体结构示意图。
48.图9为本实用新型一较佳实施例连接器加强结构另一视角的整体结构示意图。
49.图10为本实用新型一较佳实施例连接器加强结构的仰视视角的整体结构示意图。
50.图11为本实用新型一较佳实施例下箱体的剖视图。
51.图12为本实用新型一较佳实施例下箱体另一视角的剖视图。
52.图13为本实用新型一试验例的上箱盖的结构示意图。
53.图14为本实用新型一试验例的下箱体的结构示意图。
54.附图标记说明:
55.连接器加强结构1
56.第一加强部11
57.背板111
58.延伸结构112
59.镂空部113
60.加强筋114
61.折边115
62.第二加强部12
63.围板121
64.侧板1211
65.端板1212
66.底板122
67.螺钉123
68.第三加强部13
69.空腔14
70.箱体2
71.箱体的内侧表面21
72.连接器预留口22
73.上箱体单元23
74.箱盖外壳231
75.隔热层232
76.保护层233
77.下箱体24
78.内箱壳体25
79.外箱壳体26
80.加强结构261
81.凹陷部262
82.加强筋263
83.连接板27
84.电池箱3
85.电连接器4
具体实施方式
86.下面举个较佳实施例,并结合附图1-12来更清楚完整地说明本实用新型。
87.实施例
88.具体如图2-3所示,本实用新型提供一种连接器加强结构1,将其用于安装在非金属复合材料的箱体2的内侧。
89.该连接器加强结构1具体包括第一加强部11和第二加强部12,本实施例中的第一加强部11和第二加强部12为一体成型的结构,两者无缝隙连接,共同组成上述的连接器加强结构1。且第一加强部11和第二加强部12分别通过粘接或焊接的方式与箱体2连接,即将整个连接器加强结构1通过粘接或焊接的方式和箱体的内侧表面21固定连接。
90.具体在本实施方式中,择优选择采用粘接的方式分别将第一加强部11和第二加强部12相对箱体2进行固定连接。相对于其他的连接方式,采用粘接的方式可以使得第一加强部11和第二加强部12相对箱体2的固定面积更大,进而使得第一加强部11和第二加强部12与箱体2之间相互加强,可以提高整个组合体连接器加强结构1的结构强度,同时在箱体采用非金属复合材料的情况下,采用粘接实现连接的连接可靠性也更高。同时,采用粘接的连接方式,对于发生粘接位置不当或粘接错误等问题时,便于工作人员的整改,方便拆卸。对于连接器加强结构1和箱体2的具体连接方式,可以按需设置。
91.如图3-4所示,第一加强部11位于箱体的内侧表面21上,且第一加强部11环绕连接在连接器预留口22的周侧,可以实现第一加强部11和箱体的内侧表面21的连接的稳定性和可靠性。
92.如图5所示,第二加强部12和第一加强部11无缝隙连接,第二加强部12和第一加强部11共同围成一个空腔14。该空腔14位于连接器预留口22靠近箱体2内侧的正前方,且该空腔14与连接器预留口22连通。
93.为了均衡箱体2内各电芯(图中未示出)之间的温度差异,后续会往箱体2内灌注胶体,胶体具有流动性,它会在箱体2内进行流动和蔓延,以此实现降低箱体2内各电芯之间的温度差异。所以当胶体在箱体2内流动蔓延时,胶体会流动蔓延至连接器预留口22处,并将连接器预留口22堵塞,则连接器预留口22无法正常后续的工作。
94.所以,在本实施方式中,设置空腔14的目的在于:用于阻挡箱体2内灌注的胶体,能够在靠近箱体2的连接器预留口22处形成一个连通箱体2的连接器预留口22的隔离区域,避免胶体流入到空腔14内,进而避免了胶体的流动堵塞连接器预留口22,并且将该空腔14和连接器预留口22连通形成一个通道,该隔离区域和该通道可以用于实现后续的电芯的缆线布置等工作。且设置空腔14的好处在于:在能提高该连接器加强结构1的整体强度时,也能节约连接器加强结构1的用料。而且,通过围设形成的空腔14也可以用于装载其他部件,在实现该空腔14用于阻挡灌注的胶体时,也能实现将该空腔14用于布置后续的电芯的缆线等
工作,可以做到同一个空腔14实现两种作用,增大箱体2空间的利用率,实现一物两用的作用。
95.并且,如图5所示,将空腔14朝上设置,在空腔14上设置一个具有朝上的开口结构,并且将组成空腔14的第二加强部12上的各个挡板的边缘高度高于箱体2内灌注胶体的高度。通过该结构设计,在往箱体2内灌注胶体的过程中,无需考虑胶体会溢流、蔓延至空腔14内等可能性。因此,在连接器预留口22处设置连接器加强结构1的箱体2,在实施往箱体2内灌注胶体的步骤中,可以有效的降低该步骤的实施难度,并且可以大幅度的提高实施的成功率。
96.其中,将连接器加强结构1安装在至少为非金属复合材料的箱体2内。所以本实施方式中,就是将连接器加强结构1安装在非金属复合材料内。而连接器加强结构1也可以按需设置在其他材质上,例如安装在铸铁等材料上。
97.如图6所示,在第一加强部11朝向箱体的内侧表面21处具有凹槽,该凹槽用于容纳与箱体的内侧表面21连接的粘接胶。相比于其他方案直接在第一加强部11和箱体的内侧表面21上设置粘接胶,可以增强粘接的稳固性,避免粘接的两端产生相对滑动,进而避免粘接胶的相对滑动降低粘接的效果,也降低粘接的可靠性,进而提高了整个连接器加强结构1与箱体2的结构强度。并且,设置凹槽容纳粘接胶,可以有效的避免了粘接胶溢出等问题。
98.如图5-6所示,第一加强部11包括背板111和延伸结构112。其中,背板111设置在与箱体的内侧表面21的间隔处上。在箱体的内侧表面21上朝向箱体2的内部延伸,在延伸一段距离后设立背板111阻止其继续延伸,以此从箱体的内侧表面21延伸出的这段结构即为延伸结构112,所以背板111和箱体的内侧表面21之间延伸的距离便是延伸结构112延伸出的长度,也即背板111与箱体的内侧表面21间隔设置。
99.其中,延伸结构112的一侧面为背板111,另一侧面朝向箱体的内侧表面21处具有开口结构,将背板111设置成朝向箱体的内侧表面21的延伸结构112为镂空部113,即延伸结构112内设置成镂空部113,采用这种结构的目的在于:可以在节约用料的同时增强延伸结构112的整体强度。
100.如图6所示,在上述镂空部113的内部,设置多个沿相同方向延伸的加强筋114。该加强筋114设置在背板111的表面,加强筋114延伸至整个延伸结构112,加强筋114从背板111的表面延伸至箱体的内侧表面21上,即加强筋114的长度与延伸结构112度的宽度保持一致。也就是说,加强筋114的一端和箱体的内侧表面21连接,其另一端和背板111连接。设置加强筋114并采取这样的结构形式的目的是:在节省用料的同时,可以降低延伸结构112在与箱体的内侧表面21连接时的变形度,且增强了第一加强部11和箱体2连接的稳定性和可靠性。
101.当然,在其他实施例中,加强筋114可以在延伸结构112的内部设置成:
102.第一种,沿箱体的内侧表面21径向垂直方向延伸,在延伸结构112内依次等间距交错排列设置;
103.第二种,沿箱体的内侧表面21径向垂直方向延伸,在延伸结构112内交叉设置。
104.上述结构设置方案均能够实现加强稳定性和可靠性的目的,因此可根据事实需要自由选择。
105.如图6所示,在本实施方式中,择优选择第一种。可以使得各加强筋114之间通过相
互交错连接的形式加强延伸结构112的稳定性和与箱体的内侧表面21连接的可靠性以及降低了延伸结构112的变形性。相比于其他方案中,在不增加背板111或延伸结构112的厚度的情况下,或不采用刚度较强的材料的情况下,采用加强筋114交错布置的结构形式,可以稳定提高延伸结构112的稳定性。
106.其中,如图6所示,在延伸结构112与箱体的内侧表面21的连接处设置有折边115,折边115朝向延伸结构112所在的反方向延伸,即将折边115朝向远离箱体2的下表面延伸设置和/或朝向连接器预留口22的反方向延伸设置,该折边115与箱体的内侧表面21相贴合,即第一加强部11通过折边115实现与箱体的内侧表面21的无缝隙连接。设置折边115这一结构,可增大延伸结构112和箱体的内侧表面21的接触面积,并将折边115采用粘接或焊接的方式实现延伸结构112和箱体的内侧表面21连接,使得第一加强部11与箱体2之间的连接相互加强,进而可以提高整个组合体的结构强度。所以,将第一加强部11采用上述结构形式,不仅能提高第一加强部11和箱体2的连接强度,也能进一步提高自身的整体强度。
107.如图7所示,本实施例中的第二加强部12包括围板121和底板122。围板121用于在箱体2的内侧将连接器预留口22包围,即围板121与第一加强部11共同在连接器预留口22朝向箱体2内部处围成一个空腔14。且围板121的顶端高度高于箱体2内的灌胶高度,围板121的底端延伸至箱体2内部的底面上。设置围板121的好处是,可以增强第二加强部12连接的稳定性和可靠性。
108.其中,围板121包括两块侧板1211和中间的端板1212,两块侧板1211和中间的端板1212共同与第一加强部11连接围成空腔14。两块侧板1211靠近箱体的内侧表面21的一端与第一加强部11连接,两块侧板1211的另一端即朝向箱体2的内部的一端共同与端板1212连接。采用这种结构形式,可以更好的组成封闭式空腔14,进一步隔离胶体的蔓延。且这种端板1212和两块侧板1211采用可拆卸连接的方式,降低了端板1212和侧板1211的加工难度,且便于工作人员更换端板1212和侧板1211。
109.同时,在本实施方式中,两块侧板1211和第一加强部11呈一体成型结构。因为空腔14是用来阻挡胶体的流动蔓延至连接器预留口22,还会用来布置后续缆线等作业。所以,将两块侧板1211和第一加强部11连接成一体结构,只需要将端板1212设置成可拆卸连接的状态即可,当有需要维修或更换时,只需要拆卸端板1212,便可解决问题。不需要工作人员依次将两块侧板1211和端板1212分别拆卸下来,增加了工作人员的工作量,且操作繁琐。同时,通过一体成型的工艺,增加两块侧板1211与第一加强部11之间的连接面积,以提高第二加强部12在该处连接的强度与刚性。
110.如图7所示,底板122位于两块侧板1211的下方,即底板122的一侧表面分别与两块侧板1211连接,底板122相对的另一侧表面用于与箱体2的底面连接。则第二加强部12和箱体2的下表面为多点连接,通过增大第二加强部12和箱体2下表面的接触面积,不仅可以实现自身结构的强度增加,也能增强整个连接器加强结构1和箱体2连接的稳定性和牢固性。
111.本实施例中,在底板122的表面设置螺钉123,即将端板1212垂直安装在箱体2的内部,并且安装在底板122朝向箱体2内部的侧表面时,使得端板1212和底板122的该处侧表面完全贴合之后,在端板1212和底板122的重合面上安装螺钉123,将底板122和端板1212紧固连接在一起。
112.第二加强部12具体的安装顺序和方法可以按需设置。设置螺钉123实现两者连接
的好处在于可以提高连接器加强结构1在该处的连接强度和刚度,且在箱体2灌注胶体的过程中,保证连接器加强结构1的自身强度能够大于胶体对连接器加强结构1外表面承受胶体的作用力。
113.如图5-6所示,连接器加强结构1还包括第三加强部13。
114.将第三加强部13插入连接器预留口22中,则第三加强部13与连接器预留口22形成通道,使得第三加强部13和第一加强部11连接,并将该通道与空腔14连通,可以使得箱体2内部的电芯的缆线可以从箱体2内部自由伸出至空腔14内,再从空腔14内穿过该通道伸出至箱体2的外部。设置空腔14的目的如上,不仅可以用来阻挡灌注的胶体的蔓延,还可以用于放置或排布箱体2内部的电芯的缆线等。所以通过该结构设置,可以实现对电芯的缆线从箱体2的内部伸出至箱体2的外部的过程中的进一步保护。同时,将第三加强部13和第一加强部11连接,可以增强连接器加强结构1的自身整体的结构强度以及与箱体2连接的强度。
115.在本实施方式中,如图5-6所示,将第一加强部11和第三加强部13设置成一体成型结构。通过增大第一加强部11和第三加强部13连接的接触面积,可以使得增大整个连接器加强结构1的结构强度与刚性,也进而提高了整个连接器加强结构1和箱体2连接的强度与刚性,可以更好的实现连接器加强结构1在连接器预留口22处的连接强度,则可以更加有效的保护箱体2内部的电芯的缆线向箱体2外部的自由延伸。同时,第三加强部13和连接器预留形成的通道的长度方向与第一加强部11内的镂空部113上的加强筋114方向一致,均为箱体的内侧表面21的径向垂直方向,更加便于在该通道内进行抽芯,从而可以使得第三加强部13与第一加强部11的一体成型结构在成型工艺上更加方便。
116.其中,第三加强部13通过粘接或焊接的方式与连接器预留口22连接。在本实施方式中,如图6所示,加强部通过粘接的方式与连接器预留口22连接,且第三加强部13朝向连接器预留口22的表面具有凹槽,该凹槽用于容纳与连接器预留口22连接的粘接胶。相比于其他方案直接在第三加强部13和连接器预留口22上设置粘接胶,可以增强粘接的稳固性,可以避免粘接的两端产生相对滑动,进而避免了粘接胶的滑动降低粘接的效果,降低粘接的可靠性,则第三加强部13和连接器预留口22采用粘接的方式提高了整个连接器加强结构1与箱体2的结构强度。并且,设置凹槽容纳粘接胶,可以有效的避免了粘接胶溢出等问题。将第三加强部13和连接器预留口22的连接方式可以按需设置,例如需要将第三加强部13和连接器预留口22紧固连接在一起的时候,而且在无需将二者拆卸的情况下,便可以采取焊接等紧固方式,增强连接器预留口22和第三加强部13连接的紧固性和可靠性。
117.在本实施方式中,连接器加强结构1还包括保温材料(图中未示出),保温材料填充在空腔14内,可以提高连接器加强结构1的保温隔热效果。
118.择优选择,保温材料可以至少包括保温棉或保温毡,或者类似物等柔性轻质保温材料,填充于空腔内。不仅可以提高箱体2在连接器预留口22处具有保温作用,也可以提高空腔14内的保温隔热效果。
119.如图1所示,为一种电池箱3,电池箱3包括非金属复合材料的箱体2,且该电池箱3包括上述的连接器加强结构1。
120.如上,为了达到电池箱3内各电芯之间温度差异降低的目的,会往箱体2内灌注胶体,而胶体具有流动性,所以蔓延流动的胶体会堵塞住连接器预留口22,使得连接器预留口22不能正常工作,将箱体2内部的电芯缆线等输出线通过连接器预留口22输送出去,所以在
连接器预留口22处设置连接器加强结构1,以此避免胶体流动堵塞连接器预留口22。连接器加强结构1在连接器预留口22朝向箱体2内部处形成一空腔14,不仅实现了利用该空腔14对胶体流动蔓延的阻挡,也对后续箱体2内电芯缆线伸出连接器预留口22等的布置工作提供了空间。
121.连接器加强结构1包括第三加强部13,第三加强部13和第一加强部11连接。将第三加强部13插入连接器预留口22中,则第三加强部13与连接器预留口22形成通道,使得第三加强部13和第一加强部11连接,并将该通道与空腔14连通,可以使得箱体2内部的电芯的缆线可以从箱体2内部自由伸出至空腔14内,再从空腔14内穿过该通道伸出至箱体2的外部。设置空腔14的目的如上,不仅可以用来阻挡灌注的胶体的蔓延,还可以用于放置或排布箱体2内部的电芯的缆线等。所以通过该结构设置,可以实现对电芯的缆线从箱体2的内部伸出至箱体2的外部的过程中的进一步保护。同时,将第三加强部13和第一加强部11连接,可以增强连接器加强结构1的自身整体的结构强度以及与箱体2连接的强度。
122.而且,如上,将第三加强部13通过粘接或焊接的方式与连接器预留口22连接,通过增大第三加强部13和连接器预留口22的接触面积,可以增强粘接的稳固性,也提高了整个连接器加强结构1与箱体2的结构强度。
123.其中,箱体2包括相对层叠的内箱壳体25与外箱壳体26,内箱壳体25和外箱壳体26上下覆盖共同组成箱体2,采用上述在内箱壳体25和外箱壳体26的连接处即接缝处设置连接器加强结构1这一结构设置,可以提高箱体2内部的保温效果。且连接器预留口22贯穿内箱壳体25和外箱壳体26设置,可以将箱体2内部的电芯的缆线等输出线通过连接器预留口22输送出来。
124.其中,第一加强部11连接于内箱壳体25,第一加强部11位于箱体2的内侧,即位于内箱壳体25上。第三加强部13至少连接于外箱壳体26,并覆盖内箱壳体25和外箱壳体26在连接器预留口22处的接缝,可以进一步提高箱体2在接缝处的密封效果,保证箱体2在连接器预留口22处的隔热保温性能。所以,通过整个连接器加强部可以实现箱体2内、外的接通。
125.如图1-2所示,箱体2包括上箱体单元23和下箱体24,上箱体单元23和下箱体24上下包覆,共同组成一个箱体2。
126.其中,在本实施方式中,连接器预留口22开设于下箱体24上,可以便于复合材料零件的加工。若连接器预留口22横穿在上箱体单元23和下箱体24之间,则在加工箱体2时,会增加加工程序,操作繁琐。
127.其中,第三加强部13与下箱体24连接,相比于将第三加强部13安装于上箱体23和下箱体24的中间部分,将第三加强部13与下箱体24连接,可以更加方便上箱体23和下箱体24的注塑成型的制作,且方便第三加强部13和下箱体24的连接。同时,采取粘接或焊接的方式将第三加强部13与下箱体24固定连接,本实施方式中,择优选择将第三加强部13和下箱体24之间采取焊接的连接方式,可以增强连接的稳固性,也提高了整个连接器加强结构1自身整体的结构强度。并且,如上述所述,将第三加强部13与连接器预留口22固定连接,加强了第三加强部13与连接器预留口22的连接,且便于第三加强部13的拆卸和安装,同时提高了第三加强部13和连接器预留口22之间的密封性。
128.如图所示,电池箱3的箱体2包括内箱壳体25和外箱壳体26,外箱壳体26包覆在内箱壳体25的外侧表面上,外箱壳体26的外侧周面又由金属材质的连接板27进行包覆连接,
即箱体2的周圈方向由连接板27完成环绕包覆。连接器加强结构1的第一加强部11和第二加强部12在内箱壳体25的内侧表面上连接,第三加强部13贯穿连接器预留口22,其末端和连接板27接触并连接。
129.本实施例中的电池箱3还包括电连接器4,该电连接器4设置在连接器预留口22处,即电连接器4与位于箱体2外侧表面的连接板27固定连接。连接板27的结构如图3所示,为截面呈“l”形的金属板状件,通过安装在材质为非金属复合材料的箱体2外周侧表面上,实现对箱体2的加固,同时,连接板27提供的外侧表面用来安装快换单元。其中,连接板27相对箱体2的连接方式,可采用螺钉螺母连接,并进一步可以采用粘接的固定方式。
130.设置在连接板27上的快换单元包括但不限于:电/液冷连接器、锁止机构等,锁止机构包括螺纹锁止机构(通过多个螺栓把电池箱与车身进行固定的锁止机构)、锁销锁止机构(通过锁销锁止方式把电池箱与车身进行固定的锁止机构)、旋转锁止机构(通过旋转锁止方式把电池箱与车身进行固定的锁止机构)、翻转锁止机构(通过翻转锁止方式把电池箱与车身进行固定的锁止机构)、顶压锁止机构(通过顶压锁止方式把电池箱与车身进行固定的锁止机构)、错齿锁止机构(通过错齿锁止方式把电池箱与车身进行固定的锁止机构)、插销锁止机构(通过插销锁止方式把电池箱与车身进行固定的锁止机构)、推拉锁止机构(通过推拉锁止方式把电池箱与车身进行固定的锁止机构)。本实施例设置在连接板27上的快换单元是由锁轴和导向块构成的错齿锁止机构。
131.本实施例中,电连接器4的内侧表面与插入连接器预留口22内与电芯的线缆对接,实现将电芯的线缆引出的目的。
132.试验例
133.某快换电动汽车目前使用钣金材质电池包(使用云母片作为保温材料),其重量为371.5kg。准备与上述钣金材质电池包具有相同的尺寸规格(外部尺寸以及电池箱内部空间尺寸)非金属复合材质电池包。
134.钣金材质电池包和非金属复合材质电池包均具有由上箱盖和下箱体组合形成的电池箱。
135.如图13所示,非金属复合材质电池箱的上箱盖(上箱体单元23)采用具有以下结构:上箱盖包括箱盖外壳231、隔热层232和保护层233,隔热层232和保护层233依次覆盖并固定在箱盖外壳231朝向下的一侧。并且箱盖外壳231采用smc材质模压成型,轻质柔性的隔热层232采用5mm厚的气凝胶毡,保护层233的材质为防火布,箱盖外壳231与隔热层232之间以及隔热层232与保护层233之间均采用结构胶粘接连接的方式连接,并在箱盖外壳231设置凹凸结构231a以增加强度。
136.如图14所示,非金属复合材质电池箱的下箱体采用上述实施例中的下箱体(下箱体24)。该下箱体包括叠放设置的外壳体(外箱壳体26)和内壳体(内箱壳体25),且外壳体侧壁向外延展形成加强结构261,加强结构261设置凹陷部262在保证强度的同时实现减重,内壳体与外壳体之间设置有纵横交错的加强筋263,加强筋263形成于外壳体的上表面(及外壳体上朝向内壳体的表面),并通过粘接于内壳体连接,通过加强筋263将内壳体与外壳体之间隔成成若干腔室,形成腔室结构。外壳体与内壳体之间的腔室结构的高度(即外壳体与内壳体相对的表面之间的距离)为5mm,外壳体和内壳体均由smc模压成型。
137.当腔室结构内不放置气凝胶时形成的下箱体记为非金属复合材料下箱体a,当腔
室结构内放置气凝胶时形成的下箱体记为非金属复合材料下箱体b,非金属复合材料下箱体a和非金属复合材料下箱体b分别采用卡扣扣合的方式与上箱盖组合,形成非金属复合材料电池箱,分别记作非金属复合材料电池箱a和非金属复合材料电池箱b,分别装入电池模组及必要的电气元件后形成非金属复合材质电池包a和非金属复合材质电池包b。
138.上箱盖与下箱体之间采用u型密封的方式进行密封,上箱盖的侧面设有凹陷部,与设置于下箱体侧面的凸起部配合,形成卡扣连接,上箱盖与下箱体一次模压,实现卡扣连接结构的扣合。
139.对相同尺寸规格的非金属复合材质电池包a、非金属复合材质电池包b以及钣金材质电池包进行测试。
140.重量测试方面,非金属复合材料下箱体b的质量为45kg,而相同尺寸规格的钣金材质下箱体(使用云母片作为保温材料)其质量为60.4kg。相较于钣金材质下箱体,非金属复合材质下箱体b减重达到25.5%。非金属复合材料电池箱b的重量为57.8kg,钣金材质电池箱的重量为70.772kg,非金属复合材质电池箱重量优势明显。非金属复合材料下箱体a,相较于非金属复合材料下箱体b,缺少了在腔室结构中放置的气凝胶毡,由于气凝胶毡的密度较小,而使用量不大,因此,非金属复合材料下箱体a的质量与非金属复合材料下箱体b相当,略有降低(几乎可以忽略)。在电池包总体重量方面,非金属复合材料电池包a和非金属复合材料电池包b的总体重量相较于钣金材质电池包,总体重量减少2-3%,重量优势明显。
141.强度测试方面,非金属复合材质下箱体a和非金属复合材质下箱体b,以及用于与二者组合形成复合材料非金属电池箱的非金属复合材料上盖均满足gb/t 31467.3-2015《电动汽车用锂离子动力蓄电池包和系统第3部分:安全性要求与测试方法》所规定的强度等方面的要求(实际测试中可达到标准的1.5倍)。能够用于电动汽车。
142.保温性能和隔热性能方面:初始包内温度在20-30℃,并放置在7-9℃的环境中经历600min,非金属复合材质电池包a的包内电芯单体的累计温度变化率(累计降温速率)低于钣金材质电池包的50%(电芯单体温度通过光纤测量),非金属复合材质电池包b的包内电芯单体的累计温度变化率更是仅有钣金材质电池包的约40%。在更低温度下,这个优势更加明显,在北方寒冷地区使用,能够保证电芯的温度处于较佳的运行温度下。而且经过测试,非金属复合材料电池包a和非金属复合材料电池包b可耐1000℃高温,在模拟电池起火的试验中,即使电池完全燃烧,非金属复合材料箱体在整个试验过程中基本保持完好,仅出现过冒烟而没有明火。
143.非金属复合材质电池包a和非金属复合材质电池包b的电芯放置腔内灌注导热胶(导热胶灌注高度为电池高度的1/3左右),一来增加电芯之间的温度均一性,避免由于个别电芯温度异常导致的热失控。二来也使得电池箱内部的各电芯(或者由电芯形成的电池模组)形成一个整体,增加了电池包的整体强度。上述情况下的非金属复合材料电池包b与上述钣金材料电池包相比,在相同的环境中,以40a的充电电流充电(soc从0-100%)时,钣金材质电池包比非金属复合材质电池包b累计温升高5℃以上,非金属复合材质电池包b相较于钣金材质电池包充电容量高5%以上,且复合材料非金属电池包的箱体内部最大温差(通过记录所有正负极耳温度获得)均匀性维持在1.5-2℃。这不仅与使用了导热胶有关,还与smc的比热容及保温性能高于钣金材料有关,上述因素使得本技术的非金属复合材料电池包在避免热失控方面较钣金材质电池包更具优势。
144.上述试验例所使用到的部分原料性能如下:
145.smc满足以下性能要求:材料级(无序玻纤状态)拉伸强度≥70mpa(gb/t 1447-2005),弯曲强度≥160mpa(gb/t 1449-2005),冲击韧性≥55kj/m2(gb/t 1451-2005),断裂延伸率≥1.3%(gb/t 1447-2005)。
146.气凝胶毡的密度为约0.16mg/cm3。
147.结构胶剪切强度(阳极氧化铝-阳极氧化铝)≥6mpa,拉伸强度≥5mpa,阻燃等级v0。
148.上述smc、气凝胶毡和结构胶可以是符合以上性能要求的市售产品或自制产品,其余材料为市售产品。