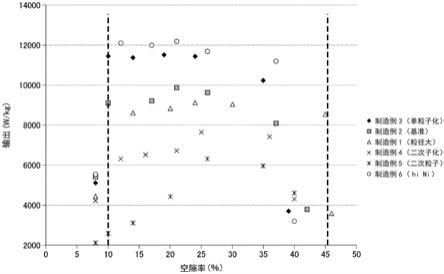
非水系电解质二次电池用电极及具备其的非水系电解质二次电池
本技术是申请号:201780068497.2,pct申请号:pct/jp2017/039698,申请日:2017.11.2,发明名称:“非水系电解质二次电池用电极及具备其的非水系电解质二次电池”的申请的分案申请。
技术领域
本发明涉及非水系电解质二次电池用电极及具备其的非水系电解质二次电池。
背景技术:以往,作为电动汽车等大型动力设备用途,需要具备高输出特性的非水系电解质二次电池用正极活性物质。为了得到高输出特性,有效的是降低构成正极活性物质的二次粒子中的一次粒子数、或利用使一次粒子单分散而成的单粒子构成正极活性物质。但是,若因形成电极时的加压处理或充放电时的膨胀收缩等而使正极活性物质发生破裂,则无法得到高输出特性。因此,提出各种使正极活性物质的耐久性提高的技术。例如提出了具备密度为3.5g/cm3以上的高密度且空隙率为25%以下的正极活性物质的非水二次电池(参照专利文献1)。根据该非水二次电池,通过允许在正极中存在大量空隙,从而尽管密度高,也能避免集电体的断裂,得到高输出特性。另外,例如提出空隙率为30%~50%且细孔径为0.09~0.30μm的二次电池用正极(参照专利文献2)。根据该二次电池用正极,通过使空隙率及细孔径为适合的范围,从而能够改善电极密度,并且能够提高输出特性。另外,例如提出具备细孔径为0.01以上且不足0.1μm的细孔的容积相对于细孔径为0.1~1.0μm的细孔的容积的比值为0.3以下的正极活性物质的二次电池(参照专利文献3)。根据该二次电池,通过使细孔分布为适合的范围,从而能够提高输出特性。现有技术文献专利文献专利文献1:日本特开2009-48876号公报专利文献2:日本特开2010-15904号公报专利文献3:日本特开2012-209161号公报
技术实现要素:发明要解决的课题然而,专利文献1~3的技术均是使用了二次粒子的技术,在实际中正极的压制成型时等,构成正极活性物质的二次粒子发生崩坏,使空穴径变小,电阻变高,结果无法得到高输出特性。尤其是,若正极活性物质发生破裂,则在生成的新的表面上电解液被氧化分解,形成厚的sei,结果无法得到高输出特性。本发明是鉴于上述课题而完成的发明,其目的在于提供能得到高输出特性的非水
系电解质二次电池用电极及具备其的非水系电解质二次电池。用于解决课题的方案为了达成上述目的,本发明提供一种非水系电解质二次电池用电极,其是具备集电体和配置在上述集电体上且包含正极活性物质的正极活性物质层的非水系电解质二次电池用电极,上述正极活性物质含有具有由两种以上的过渡金属所形成的层状结构的化合物粒子而构成,所述化合物粒子基于电子显微镜观察的平均粒径dsem为1~7μm,在基于体积基准的累积粒度分布中的50%粒径d50相对于上述平均粒径dsem的比值(d50/dsem)为1~4,并且在基于体积基准的累积粒度分布中的90%粒径d90相对于在基于体积基准的累积粒度分布中的10%粒径d10的比值(d90/d10)为4以下,上述正极活性物质层的空隙率为10%~45%。上述正极活性物质层的密度优选为2.7~3.9g/cm3。由此,得到更高的输出特性。在二次粒子中,因进行压制而导致发生破裂,未涂布助剂的部分发生表面化,如果是单粒子,则根本不发生破裂,因此输出特性比较高。上述正极活性物质层在空穴分布曲线中的空穴的峰直径优选为0.06~0.3μm。上述正极活性物质层的空穴的平均直径优选为0.03~0.2μm。上述正极活性物质层的上述空穴的峰直径相对于上述空穴的平均直径的比值(峰直径/平均直径)优选为1.1~2.4。上述正极活性物质优选以ni、mn或al为主成分。本发明提供具备上述非水系电解质二次电池用电极的非水系电解质二次电池。发明效果根据本发明,能够提供能得到比以往高的输出特性的非水系电解质二次电池用电极及具备其的非水系电解质二次电池。
附图说明
图1是表示本实施方式涉及的正极活性物质的空穴分布曲线的例子的图。图2是表示由以往的二次粒子构成的正极活性物质的空穴分布曲线的例子的图。图3是表示本实施方式涉及的正极活性物质的dsem与d50/dsem的关系的图。图4是本实施方式涉及的正极活性物质的sem图像。图5是由以往的二次粒子构成的正极活性物质的sem图像。图6是表示实施例及比较例的正极活性物质层的空隙率与输出的关系的图。图7是表示实施例及比较例的正极活性物质层的密度与输出的关系的图。图8是表示实施例及比较例的正极活性物质层的空穴分布曲线中的空穴的峰直径与输出的关系的图。图9是表示实施例及比较例的正极活性物质层的空穴的平均直径与输出的关系的图。图10是表示实施例及比较例的正极活性物质的空穴的峰直径/平均直径与输出的关系的图。
具体实施方式
参照附图对本发明的一个实施方式进行详细地说明。但是,本发明并不受以下实施方式的限定。另外,在本说明书中,在组合物中存在多种属于各成分的物质的情况下,只要没有特别说明,各成分的含量是指在组合物中存在的该多种物质的合计量。[非水系电解质二次电池用电极]本实施方式涉及的非水系电解质二次电池用电极具备集电体和配置在该集电体上且包含活性物质层的电极活性物质层。本实施方式涉及的非水系电解质二次电池用电极被优选用作非水系电解质二次电池的正极,尤其被优选用作锂离子二次电池的正极。因此,以下,对使用本实施方式涉及的非水系电解质二次电池用电极作为锂离子二次电池的正极的非水系电解质二次电池用正极进行详细地说明。本实施方式涉及的非水系电解质二次电池用正极具备集电体和配置在集电体上且包含正极活性物质的正极活性物质层。作为集电体,可以使用例如铝、镍、不锈钢等。正极活性物质层包含正极活性物质、以及导电助剂、粘结剂等而构成。本实施方式涉及的正极活性物质层的空隙率为10%~45%。如后文所述,本实施方式涉及的正极活性物质层由包含单粒子的正极活性物质构成,因此为了在充分确保锂离子扩散的大通道(通路)的基础上得到更高的输出特性,而将正极活性物质层高密度化,即使将空隙率降低至10%~45%的范围,也不会使正极活性物质层发生破裂。即,不会如以往的包含二次粒子的正极活性物质那样地出现以下情况:因高密度化而发生破裂,从而未被导电助剂被覆(附着)的部分重新表面化(生成新的表面);根据本实施方式,由于由表面整体被导电助剂被覆的单粒子构成,因此得到高输出特性。更优选的空隙率为20%~35%。在此,本实施方式中的空隙率能够利用压汞法进行测定。另外,空隙率能够通过调整正极活性物质的粒径、或调整后述的正极活性物质层的制造方法中的加压条件来进行调整。本实施方式涉及的正极活性物质层的密度优选为2.7~3.9g/cm3。如上所述,本实施方式涉及的正极活性物质层由包含单粒子的正极活性物质构成,因此即使为了得到高输出特性而将正极活性物质层高密度化至2.7~3.9g/cm3的范围,也能将空隙率限制为10%~45%的范围,因此不会使正极活性物质层发生破裂。即,不会如以往的包含二次粒子的正极活性物质那样地出现以下情况:因高密度化而发生破裂,从而未被导电助剂被覆(附着)的部分重新表面化(生成新的表面);根据本实施方式,由于由表面整体被导电助剂被覆的单粒子构成,因此得到高输出特性。更优选的密度为3.0~3.6g/cm3。在此,本实施方式中的密度能够利用密度测定装置进行测定。另外,密度能够通过调整正极活性物质的粒径、或调整后述的正极活性物质层的制造方法中的加压条件来进行调整。本实施方式涉及的正极活性物质层在空穴分布曲线(细孔分布曲线)中的空穴的峰直径优选为0.06~0.3μm。如果正极活性物质层中的空穴的峰直径为该范围内,则能够更可靠地得到如上所述的高输出特性。更优选的空穴的峰直径为0.12~0.25μm。本实施方式中的空穴的峰直径是指:在与上述的空隙率的测定同样地利用采用压汞法的测定得到的空穴分布曲线、更详细而言为log微分细孔容积分布(dv/dlogd)中成为
极大值的细孔的直径d。log微分细孔容积分布(dv/dlogd)是求出微分细孔容积dv除以细孔径的对数处理的微分值dlogd所得的值、并将其相对于平均细孔直径绘制成的曲线。在此,图1是表示本实施方式涉及的正极活性物质的空穴分布(log微分细孔容积分布)曲线的例子的图。另外,图2是表示以往的由二次粒子构成的正极活性物质的空穴分布(log微分细孔容积分布)曲线的例子的图。这些图1及图2中,横轴表示细孔直径d(μm),纵轴表示log微分细孔容积分布(dv/dlogd)。在任一图中均用实线、虚线、单点划线分别表示3个例子。由这些图明确可知:在使用了包含单粒子的正极活性物质的本实施方式中确认到尖锐的峰,与此相对,在使用了包含二次粒子的正极活性物质的以往方案中确认到宽峰。本实施方式涉及的正极活性物质层的空穴的平均直径优选为0.03~0.2μm。如果正极活性物质层中的空穴的平均直径为该范围内,则能够更可靠地得到如上所述的高输出特性。更优选的空穴的平均直径为0.05~0.18μm。需要说明的是,空穴的平均直径利用基于依照与上述的空隙率的测定同样的测定条件的压汞法的测定来得到。另外,本实施方式涉及的正极活性物质层的上述空穴的峰直径相对于上述空穴的平均直径的比值(峰直径/平均直径)优选为1.1~2.4。如果空穴的峰直径相对于空穴的平均直径的比值(峰直径/平均直径)为该范围内,则能够更可靠地得到如上所述的高输出特性。更优选的空穴的峰直径相对于空穴的平均直径的比值(峰直径/平均直径)为1.1~1.8。通过使用如本实施方式那样包含单粒子的正极活性物质,从而使峰直径/平均直径的值变小而处于上述范围内。因此,粒子彼此的间隙不会变得过小,电解液能够渗透至整体,因此得到高输出特性。正极活性物质层通过将正极合剂涂布于集电体上后进行干燥、加压处理而形成,所述正极合剂是将正极活性物质、导电助剂及粘结剂等与溶剂一同混合而得到的。作为导电助剂,可以使用例如天然石墨、人造石墨、乙炔黑等。作为粘结剂,可以使用例如聚偏二氟乙烯、聚四氟乙烯、聚酰胺丙烯酸类树脂等。接下来,对正极活性物质进行详细地说明。本实施方式涉及的正极活性物质包含具有由两种以上的过渡金属所形成的层状结构的化合物粒子而构成,所述化合物粒子基于电子显微镜观察的平均粒径dsem为1~7μm,在基于体积基准的累积粒度分布中的50%粒径d50相对于上述平均粒径dsem的比值(d50/dsem)为1~4,并且在基于体积基准的累积粒度分布中的90%粒径d90相对于在基于体积基准的累积粒度分布中的10%粒径d10的比值(d90/d10)为4以下。作为具有由两种以上的过渡金属所形成的层状结构的化合物粒子,优选以ni、mn或al为主成分。其中,优选使用具有包含ni的层状结构的锂过渡金属复合氧化物粒子(以下也称作“复合氧化物粒子”。)。dsem为1~7μm且d50/dsem为1~4是指构成正极活性物质的复合氧化物粒子为由单一的粒子构成的单一粒子或者由数量少的一次粒子构成的粒子。即,在本实施方式中,将全部粒子为单一粒子或由数量少的一次粒子构成的粒子的情况统称为“单粒子”。需要说明的是,本实施方式涉及的正极活性物质的单粒子活性物质的比例优选为80%以上。在此,图3是表示本实施方式涉及的正极活性物质的dsem与d50/dsem的关系的图。在图3中,横轴表示dsem(μm),纵轴表示d50/dsem。在图3中,被虚线包围的区域是dsem为1~
7μm且d50/dsem为1~4的区域,其是本实施方式中定义的单粒子的区域。与一次粒子聚集而形成的二次粒子相比,位于上述区域内的单粒子成为一次粒子间的接触晶界少的状态。图4是本实施方式涉及的正极活性物质的sem图像。图5是以往的由二次粒子构成的正极活性物质的sem图像。如图4所示,在本实施方式涉及的构成正极活性物质的单粒子中,粒子未发生聚集,因此导电助剂能够被覆(附着)各粒子的表面整体。因此,能够效率良好地使用导电助剂,并且能够提高输出特性。与此相对,在如图5所示的构成以往的正极活性物质的二次粒子中,一次粒子聚集而形成二次粒子,因此导电助剂不能进入到一次粒子间的间隙中,导电助剂不能被覆(附着)一次粒子的表面整体。因此,不能效率良好地使用导电助剂,并且不能提高输出特性。另外,d90/d10为4以下是指:复合氧化物粒子基于体积基准的累积粒度分布中的分布宽度窄、粒子尺寸一致。通过具备这样的特征,从而得到高耐久性,结果得到高输出特性。在此,与包含一次粒子大量聚集成的二次粒子所构成的锂过渡金属复合氧化物粒子的正极活性物质相比,包含由以往的单粒子构成的锂过渡金属复合氧化物粒子的正极活性物质能够抑制在充放电循环时由基于二次粒子的晶界解离的锂离子导电通路断开所致的容量维持率降低、锂离子的扩散移动阻力增大,因此显示优异的耐久性。另一方面,几乎不形成如由聚集粒子构成的正极活性物质那样的三维晶界网络,无法进行利用了晶界传导的高输出设计,因此存在使输出特性不充分的倾向。为了提高输出特性,考虑通过减小单粒子的粒径(dsem)来改善,但是,若过小,则存在粉体彼此的相互作用增大、极板填充性的恶化变得显著的倾向,并且有时因粉体流动性减少而使操作性显著恶化。另一方面可认为:尤其为了得到实用的能量密度,需要一定程度的粒子尺寸,但在增大粒径的情况下,存在使输出不足变得更显著的倾向。与以往的单粒子相比,本实施方式涉及的锂过渡金属复合氧化物粒子的粒子尺寸更为一致,因此可认为即使在以高电流密度进行充放电的情况下,也可抑制因电流集中于一部分粒子所致的各粒子的充放电深度的不均,因此能够抑制由电流集中所致的电阻增大、并且能够抑制由循环所致的局部劣化。通过进一步使晶界少的锂过渡金属复合氧化物粒子的粒径一致,从而在制作电极时即使在高压下进行压制的情况下,粒子也不会崩坏,因此认为能够将粒子间的空隙均匀化。另外认为:在构成电池的情况下,粒子间的空隙被电解质填充而成为锂离子的扩散路径,通过使该扩散路径的大小一致,从而能够抑制各粒子的充放电不均。由此认为:即使是一次粒子间的接触晶界少的锂过渡金属复合氧化物粒子,也能够担保极板填充性,并且能够达成优异的输出特性。另外,一般在合成单粒子的情况下,为了使粒子生长,热处理温度需要为高温。尤其是,若在ni比率高的组成中进行高温烧成,则有时发生ni元素混入至li位点的、所谓无序化。无序化会阻碍复合氧化物粒子中的li离子的扩散而成阻力,造成在实用电流密度下的充放电容量降低、输出特性降低等影响,因此优选对其进行抑制。通过抑制无序化,从而能够在单粒子中达成更优异的容量及输出特性。在构成正极活性物质的复合氧化物粒子中,从耐久性的观点出发,基于电子显微镜观察的平均粒径dsem为1~7μm。另外,从输出密度及极板填充性的观点出发,在后述的x
的范围为0.3≤x<0.6的情况下,优选为1.1μm以上,更优选为1.3μm以上,并且优选为4μm以下,更优选为2μm以下。在x的范围为0.6≤x≤0.95的情况下,优选为1.1μm以上,更优选为1.3μm以上,并且优选为5μm以下,更优选为4μm以下。就基于电子显微镜观察的平均粒径dsem而言,使用扫描型电子显微镜(sem),根据粒径而以1000~10000倍的范围进行观察,选择100个能够确认粒子的轮廓的粒子,使用图像处理软件对所选择的粒子算出球换算直径,以所得的球换算直径的算术平均值的形式求得。复合氧化物粒子在基于体积基准的累积粒度分布中的50%粒径d50相对于基于电子显微镜观察的平均粒径dsem的比值d50/dsem为1~4。在d50/dsem为1的情况下,表示全部为单一粒子,越接近1,表示所构成的一次粒子的数量越少。从耐久性的观点出发,d50/dsem优选为1以上且不足4,从输出密度的观点出发,d50/dsem优选为3以下,特别优选为2.5以下。另外,复合氧化物粒子的50%粒径d50为例如1~21μm,从输出密度的观点出发,优选为1.5μm以上,更优选为3μm以上,并且优选为8μm以下,更优选为5.5μm以下。就50%粒径d50而言,使用激光衍射式粒径分布测定装置在湿式条件下所测定的体积基准的累积粒度分布中,以与从小径侧起的累积50%对应的粒径的形式求得。同样,后述的90%粒径d90及10%粒径d10分别以与从小径侧起的累积90%及累积10%对应的粒径的形式求得。复合氧化物粒子在基于体积基准的累积粒度分布中的90%粒径d90相对于10%粒径d10的比值表示粒度分布的广度,值越小,表示粒子的粒径越一致。d90/d10为4以下,从输出密度的观点出发,优选为3以下,更优选为2.5以下。d90/d10的下限为例如1.2以上。锂过渡金属复合氧化物具有在组成中包含ni的层状结构。作为这样的锂过渡金属复合氧化物,可列举例如锂镍复合氧化物、锂镍钴锰复合氧化物等。其中,锂过渡金属复合氧化物优选具有下述式(1)所示的组成。[化1]lipnixcoym1zo2+α
ꢀꢀꢀ
···
式(1)[式(1)中,p、x、y、z及α满足1.0≤p≤1.3、0.3≤x≤0.95、0≤y≤0.4、0≤z≤0.5、x+y+z=1、-0.1≤α≤0.1,m1表示mn及a1中的至少一者。]锂过渡金属复合氧化物粒子可以掺杂除构成锂过渡金属复合氧化物的元素以外的元素。作为所掺杂的元素,可列举例如b、na、mg、si、p、s、k、ca、ti、v、cr、zn、sr、y、zr、nb、mo、in、sn、ba、la、ce、nd、sm、eu、gd、ta、w及bi。其中,可优选例示mg、ti、w。作为这些元素的掺杂所使用的化合物,可列举包含选自这些元素中的至少1种元素的氧化物及氟化物、以及其li复合氧化物等。掺杂量例如相对于锂过渡金属复合氧化物粒子可以为例如0.005摩尔%以上且10摩尔%以下。另外,锂过渡金属复合氧化物粒子可以为具有包含锂过渡金属复合氧化物的核粒子、和配置在核粒子的表面的附着物的复合氧化物粒子。附着物只要配置在核粒子的表面的至少一部分区域即可,优选配置在核粒子的表面积的1%以上的区域。附着物的组成可以根据目的等进行适当选择,可列举例如包含选自b、na、mg、si、p、s、k、ca、ti、v、cr、zn、sr、y、zr、nb、mo、in、sn、ba、la、ce、nd、sm、eu、gd、ta、w及bi中的至少1种元素的氧化物及氟化物、
以及其li复合氧化物等。附着物的含量例如在锂过渡金属复合氧化物粒子中可以为0.03质量%以上且10质量%以下,优选为0.1质量%以上且2质量%以下。锂过渡金属复合氧化物的组成中包含ni。从非水系电解质二次电池的初始效率的观点出发,锂过渡金属复合氧化物利用x射线衍射法求得的ni元素的无序化优选为4.0%以下,更优选为2.0%以下,进一步优选为1.5%以下。在此,ni元素的无序化是指应该占有本来的位点的过渡金属离子(ni离子)的化学性排列无秩序(chemical disorder)。在层状结构的锂过渡金属复合氧化物中,在以wyckoff符号表示的情况下,具代表性的是应该占有3b所示的位点(3b位点、以下同样)的锂离子和应该占有3a位点的过渡金属离子的替换。ni元素的无序化越小,初始效率越提高,故优选。锂过渡金属复合氧化物中的ni元素的无序化可以利用x射线衍射法求得。对于锂过渡金属复合氧化物,利用cukα射线测定x射线衍射光谱。将组成模型设为li1-dnidmeo2(me为锂过渡金属复合氧化物中的除ni以外的过渡金属),基于所得的x射线衍射光谱,利用rietveld分析进行结构优化。将作为结构优化的结果所算出的d的百分率设为ni元素的无序化的值。在锂过渡金属复合氧化物具有式(1)所示的组成的情况下,在本发明的一个实施方式中,有时对应于式(1)中的x的值而使a的范围、dsem、d50、d90及d10所示的粒径的范围以及ni元素的无序化的更优选的范围发生变动,以下对它们进行例示。在式(1)中,在x满足0.3≤x<0.8的情况下,从输出密度的观点出发,d50/dsem优选为1以上且2以下。在式(1)中,在x满足0.3≤x<0.6的情况下,从输出密度的观点出发,优选满足以下方式中的至少之一。(i)从充放电容量的观点出发,锂过渡金属复合氧化物粒子利用x射线衍射法求得的ni元素的无序化优选为1.5%以下。(ii)d90/d10优选为3.0以下,更优选为2.5以下。(iii)从极板填充性的观点出发,d50优选为1μm以上且5.5μm以下,更优选为1μm以上且3μm以下。(iv)式(1)中的a优选满足1.1<a<1.2。在式(1)中,在x满足0.6≤x<0.8的情况下,从输出密度的观点出发,优选满足以下的方式中的至少之一。(i)从充放电容量的观点出发,锂过渡金属复合氧化物粒子利用x射线衍射法求得的ni元素的无序化优选为2.0%以下。(ii)d90/d10优选为2.3以下。(iii)从极板填充性的观点出发,d50优选为1μm以上且5.5μm以下。在式(1)中,在x满足0.8≤x<0.95的情况下,从输出密度的观点出发,优选满足以下的方式中的至少之一。(i)从充放电容量的观点出发,锂过渡金属复合氧化物粒子利用x射线衍射法求得的ni元素的无序化优选为4.0%以下。(ii)d90/d10优选为3.0以下。(iii)从极板填充性的观点出发,d50优选为1μm以上且5.5μm以下。
本实施方式涉及的正极活性物质中所含的锂过渡金属复合氧化物粒子可以利用包括以下步骤的制造方法来制造:将锂化合物和具有所期望的组成的氧化物混合而得到原料混合物;将所得的原料混合物进行热处理。对在热处理后所得的热处理物,可以进行破碎处理,也可以利用水洗等进行除去未反应物、副产物等的处理。另外,也可以进一步进行分散处理、分级处理等。作为得到具有所期望的组成的氧化物的方法,可列举:按照目标组成将原料化合物(氢氧化物、碳酸化合物等)混合,利用热处理分解为氧化物的方法;将可溶于溶剂的原料化合物溶解于溶剂,按照目标组成利用温度调整、ph调整、络合剂投入等得到前体的沉淀,将这些前体进行热处理而得到氧化物的共沉淀法等。以下,以锂过渡金属复合氧化物以式(1)表示的情况为例,对正极活性物质的制造方法的一例进行说明。得到原料混合物的方法优选包括:利用共沉淀法得到包含ni、co和选自mn及al中的至少一者的复合氧化物;将所得的复合氧化物与碳酸锂、氢氧化锂等锂化合物混合。利用共沉淀法得到复合氧化物的方法可以包括:晶种生成工序,以所期望的构成调整包含金属离子的混合水溶液的ph等而得到晶种;晶析工序,使所生成的晶种生长而得到具有所期望的特性的复合氢氧化物;和将所得的复合氢氧化物进行热处理而得到复合氧化物的工序。关于得到复合氧化物的方法的详细情况,可以参照日本特开2003-292322号公报、日本特开2011-116580号公报等。利用共沉淀法得到的复合氧化物的成为粒度分布的指标的d90/d10为例如3以下,优选为2以下。另外,d50为例如12μm以下,优选为6μm以下,更优选为4μm以下,另外,为例如1μm以上,优选为2μm以上。复合氧化物中的ni、co和mn及al的含有比ni/co/(mn+al)可以为例如1/1/1、6/2/2、8/1/1等。原料混合物优选在复合氧化物的基础上还包含锂化合物。作为锂化合物,可列举碳酸锂、氢氧化锂、氧化锂等。所使用的锂化合物的粒径以d50计为例如0.1~100μm,优选为2~20μm。原料混合物中的锂的含量以例如li/(ni+co+mn+al)计为1.0以上,并且可以为1.3以下,优选为1.2以下。复合氧化物与锂化合物的混合例如可以使用高速剪切混合机等来进行。通过将所得的原料混合物进行热处理,从而可以得到锂过渡金属复合氧化物粒子。热处理的温度为例如700℃~1100℃。热处理可以在单一的温度下进行,也可以在多个温度下进行。当在多个温度下进行热处理的情况下,例如可以以700~925℃的范围进行第一热处理、接着以930~1100℃的范围进行第二热处理。也可以进一步以700~850℃的范围追加进行第三热处理。热处理的时间为例如1~40小时,当在多个温度下进行热处理的情况下,可以分别为1~10小时。热处理的气氛可以为大气中,也可以为氧气气氛。可以对热处理物进行破碎处理、分散处理、分级处理等。由此可以得到所期望的锂过渡金属复合氧化物粒子。另外,也可以在对热处理物进行破碎处理、分散处理、分级处理等后进一步混合锂化合物而得到混合物,再进行追加的热处理。在进一步混合锂化合物的情况下,混合物中的
锂的含量以例如li/(ni+co+mn+al)计可以为1.05~1.3,优选为1.1~1.2。另外,追加的热处理的温度可以为850~1000℃的范围,优选为870~950℃的范围,优选为比原料混合物的热处理温度低的温度。追加的热处理的热处理时间可以为例如2~15小时。也可以在进行追加的热处理后进行破碎处理、分散处理、分级处理等。[非水系电解质二次电池]本实施方式涉及的非水系电解质二次电池具备上述的非水系电解质二次电池用电极作为正极。另外,本实施方式涉及的非水系电解质二次电池被构成为在具备以往公知的非水系电解质二次电池用负极作为负极的基础上还包含非水系电解质、间隔件等。关于非水系电解质二次电池用负极、非水系电解质、间隔件等,例如可以适当采用日本特开2002-075367号公报、日本特开2011-146390号公报、日本特开2006-12433号公报等中记载的非水系电解质二次电池用负极、非水系电解质、间隔件等,其制造方法也可以使用这些公报中记载的制造方法。需要说明的是,本发明并不受上述实施方式的限定,在能够达成本发明的目的的范围内的变形、改良包含在本发明内。实施例
[0073]
接下来,对本发明的实施例进行说明。但是,本发明并不受以下的实施例的限定。《正极活性物质的制造例1》(晶种生成工序)首先,在反应槽内,一边加入10kg水进行搅拌,一边以使铵离子浓度变为1.8质量%的方式进行了调整。将槽内温度设定为25℃,使氮气流通,将反应槽内空间的氧浓度保持为10体积%以下。向该反应槽内的水中添加25质量%氢氧化钠水溶液,将槽内的溶液的ph值调整为13.5以上。接着,将硫酸镍溶液、硫酸钴溶液及硫酸锰溶液混合,制备以摩尔比计为1∶1∶1的混合水溶液。加入上述混合水溶液直至溶质变为4摩尔的量为止,一边利用氢氧化钠溶液将反应溶液中的ph值控制为12.0以上,一边进行晶种生成。(晶析工序)上述晶种生成工序后,直至晶析工序结束之前,将槽内温度维持为25℃以上。另外,准备溶质1200摩尔的混合水溶液,将其与氨水溶液一起,一边将溶液中的铵离子浓度维持为2000ppm以上,一边以不使反应槽内发生新的晶种生成的方式用5小时以上同时投入。在反应中用氢氧化钠溶液以使反应溶液中的ph值维持为10.5~12.0的方式进行控制。在反应中进行逐次取样,在复合氢氧化物粒子的d50变为约4.5μm时结束投入。接着,使生成物进行水洗、过滤、干燥而得到复合氢氧化物粒子。将所得的氢氧化物前体在大气气氛下以300℃进行20小时热处理,得到具有ni/co/mn=0.33/0.33/0.33组成比率、d10=3.4μm、d50=4.5μm、d90=6.0μm、d90/d10=1.8的复合氧化物。(合成工序)将所得的复合氧化物和碳酸锂按照使li/(ni+co+mn)=1.15的方式进行混合,得到原料混合物。将所得的原料混合物在大气中以925℃进行7.5小时烧成后,以1030℃烧成6小时,得到烧结体。将所得的烧结体破碎,利用树脂制球磨机进行10分钟的分散处理,过干
式筛,得到粉状体。将所得的粉状体用干式分级机分级为大中小3个部分,分取中粒子。相对于分级前,分级后中粒子的比例为46wt%。综上得到基于电子显微镜观察的平均粒径dsem为3.6μm、d10=3.7μm、d50=5.1μm、d90=6.7μm、d50相对于平均粒径dsem的比值d50/dsem为1.4、粒度分布中的比值d90/d10为1.8、ni无序化量为0.3%、组成式:li
1.15
ni
0.33
co
0.33
mn
0.33
o2所示的锂过渡金属复合氧化物粒子。《正极活性物质的制造例2》除了将制造例1的晶析工序中的混合水溶液的投入结束时机变更为复合氢氧化物粒子的d50变为约3.0μm时以外,在相同的条件下进行操作,得到具有ni/co/mn=0.33/0.33/0.33组成比率、d10=2.2μm、d50=3.0μm、d90=4.1μm、d90/d10=1.9的复合氧化物。将所得的复合氧化物和碳酸锂按照使li/(ni+co+mn)=1.05的方式进行混合,得到原料混合物。将所得的原料混合物在大气中以925℃烧成7.5小时后,以1030℃烧成6小时,得到烧结体。将所得的烧结体破碎,用树脂制球磨机进行30分钟的分散处理,过干式筛,得到粉状体。将所得的粉状体和碳酸锂按照使li/(ni+co+mn)=1.17的方式进行混合,在大气中以900℃烧成10小时,得到烧结体。将所得的烧结体破碎,用树脂制球磨机进行30分钟的分散处理,过干式筛,得到粉状体。综上得到平均粒径dsem为1.2μm、d10=1.5μm、d50=3.3μm、d90=5.1μm、d50相对于平均粒径dsem的比值d50/dsem为2.8、粒度分布中的d90/d10比为3.4、ni无序化量为0.9%、组成式:li
1.17
ni
0.33
co
0.33
mn
0.33
o2所示的锂过渡金属复合氧化物粒子。《正极活性物质的制造例3》在与制造例2相同的条件下得到复合氧化物。将所得的复合氧化物和碳酸锂按照使li/(ni+co+mn)=1.05的方式进行混合,得到原料混合物。将所得的原料混合物在大气中以925℃烧成7.5小时后,以1030℃烧成6小时,得到烧结体。将所得的烧结体破碎,用树脂制球磨机进行30分钟的分散处理,过干式筛,得到粉状体。将所得的粉状体和碳酸锂按照使li/(ni+co+mn)=1.17的方式进行混合,在大气中以900℃烧成10小时,得到烧结体。将所得的烧结体破碎,使用喷射磨机,以不粉碎一次粒子的方式调整为供给压0.4mpa、粉碎压0.55mpa,进行2次分散处理,过干式筛,得到粉状体。综上得到平均粒径dsem为1.4μm、d10=1.1μm、d50=1.9μm、d90=2.8μm、d50相对于平均粒径dsem的比值d50/dsem为1.4、粒度分布中的d90/d10比为2.5、ni无序化量为1.0%、组成式:li
1.17
ni
0.33
co
0.33
mn
0.33
o2所示的锂过渡金属复合氧化物粒子。《正极活性物质的制造例4》在与制造例2相同的条件下得到复合氧化物。将所得的复合氧化物和碳酸锂按照使li/(ni+co+mn)=1.05的方式混合,得到原料混合物。将所得的原料混合物在大气中以925℃烧成7.5小时后,以1030℃烧成6小时,得到烧结体。将所得的烧结体破碎,用树脂制球磨机进行10分钟的分散处理,过干式筛,得到粉状体。将所得的粉状体和碳酸锂按照使li/(ni+co+mn)=1.14的方式进行混合,在大气中以900℃烧成10小时,得到烧结体。将所得的烧结体破碎,用树脂制球磨机进行10分钟的分散处理,过干式筛,得到粉状体。综上得到平均粒径dsem为1.25μm、d10=2.7μm、d50=4.5μm、d90=6.7μm、d50相对于一次粒子的平均粒径dsem的比值d50/dsem为3.6、粒度分布中的d90/d10比为2.5、ni无序
化量为1.0%、组成式:li
1.14
ni
0.33
co
0.33
mn
0.33
o2所示的锂过渡金属复合氧化物粒子。《正极活性物质的制造例5》在与制造例2相同的条件下得到复合氧化物。将所得的复合氧化物和碳酸锂按照使li/(ni+co+mn)=1.15的方式进行混合,得到原料混合物。将所得的原料混合物在大气中以950℃烧成15小时,得到烧结体。将所得的烧结体破碎,用树脂制球磨机进行10分钟的分散处理,过干式筛,得到粉状体。综上得到平均粒径dsem为0.49μm、d10=3.0μm、d50=4.4μm、d90=7.6μm、d50相对于平均粒径dsem的比值d50/dsem为9.0、粒度分布中的d90/d10比为2.5、ni无序化量为0.9%、组成式:li
1.15
ni
0.33
co
0.33
mn
0.33
o2所示的锂过渡金属复合氧化物粒子。《正极活性物质的制造例6》将制造例1中的硫酸镍溶液、硫酸钴溶液及硫酸锰溶液的混合比以摩尔比计变更为8∶1∶1,得到混合水溶液,并且将晶析工序中的混合水溶液的投入结束时机变更为复合氢氧化物粒子的d50变为3.2μm时,除此以外,在相同的条件下进行操作,得到具有ni/co/mn=0.80/0.10/0.10组成比率、d
10
=2.2μm、d
50
=2.9μm、d
90
=4.0μm、d
90
/d
10
=1.8的复合氧化物。将所得的复合氧化物和氢氧化锂一水合物按照使li/(ni+co+mn)=1.04的方式混合,得到原料混合物。将所得的原料混合物在氧气流中以780℃烧成5小时后,以900℃烧成10小时,再以780℃烧成5小时,得到烧结体。将所得的烧结体破碎,用树脂制球磨机进行10分钟的分散处理,得到粉状体。再在旋转叶片式的高速搅拌混合机中加入粉状体和相对于粉状体为10质量%的水,以2000rpm进行搅拌,由此使晶界的残留碱溶出,进行分散处理,以350℃干燥后,过干式筛,得到粉状体。综上得到平均粒径dsem为1.5μm、d10=2.2μm、d50=3.6μm、d90=6.0μm、d50相对于平均粒径dsem的比值d50/dsem为2.4、粒度分布中的d90/d10比为2.7、ni无序化量为1.6%、组成式:li
1.04
ni
0.80
co
0.10
mn
0.10
o2所示的锂过渡金属复合氧化物粒子。《评价》以如上述那样得到的各制造例的锂过渡金属复合氧化物作为正极活性物质,利用以下的步骤制作评价用电池。首先,使如上述那样得到的各正极活性物质96质量份、乙炔黑3质量份及聚偏二氟乙烯(pvdf)1质量份分散于n-甲基-2-吡咯烷酮(nmp)中,制备成正极合剂。将所得的正极合剂涂布在作为集电体的铝箔上,干燥后用辊压机进行压缩成型,之后,裁切成规定的尺寸,由此制作成正极。在如上述那样得到的正极和作为负极的石墨上分别安装引线电极后,在正极与负极之间配置间隔件,将它们收纳于袋状的层压袋中。作为间隔件,使用厚度为16μm的pe间隔件。接着,使其在65℃下真空干燥,除去吸附于各构件的水分。之后,在氩气气氛下向层压袋内注入电解液,进行密封。将这样得到的电池放入25℃的恒温槽中,以微弱电流进行老化。作为电解液,使用如下的电解液:将碳酸亚乙酯(ec)、碳酸甲乙酯(emc)和碳酸二甲酯(dmc)以体积比3∶3∶4混合后,添加1.5质量%的碳酸亚乙烯酯(vc),之后,溶解六氟化磷酸锂(lipf6),使其浓度为1.2mol/l。
关于各正极活性物质的d10、d50及d90,使用激光衍射式粒径分布测定装置((株)岛津制作所制sald-3100),测定体积基准的累积粒度分布,对应于从小径侧起的累积而求得各自的粒径。关于各正极活性物质的dsem,在使用扫描型电子显微镜(sem)以1000~10000倍观察得到的图像中,选择100个能够确认粒子的轮廓的粒子,使用图像处理软件(imagej)对所选择的粒子算出球换算直径,以所得的球换算直径的算术平均值的形式求得。关于镍元素的无序化的值(ni无序化量),利用x射线衍射法按照以下的步骤求得。对于所得的锂过渡金属复合氧化物粒子,利用cukα射线测定x射线衍射光谱。基于所得的x射线衍射光谱,将组成模型设为li
1-d
nidmeo2(me为锂过渡金属复合氧化物中的除镍以外的过渡金属),利用rietveld分析对锂过渡金属复合氧化物进行结构优化。将结构优化的结果所算出的d的百分率作为ni无序化量。使用压汞法,测定空隙率、空穴的峰直径、空穴的平均直径。将直径超过约5μm的直径区域推测为测定上的噪音,进行截断。密度由电极重量和电极体积求得。另外,对如上述那样得到的评价用电池评价了输出密度。具体而言,将评价用电池放电,设定为soc50%的状态,在25℃的环境下保持2小时。接着,从soc50%的状态进行恒定电流放电,测定第10秒的直流电阻,算出输出密度。需要说明的是,放电下限电压设为2.7v。将结果示于表1中。[表1]
另外,将各评价结果归纳示于图6~图10中。图6是表示本实施例及比较例的正极活性物质层的空隙率与输出的关系的图。图7是表示本实施例及比较例的正极活性物质层的密度与输出的关系的图。图8是表示本实施例及比较例的正极活性物质层的空穴分布曲线中的空穴的峰直径与输出的关系的图。图9是表示本实施例及比较例的正极活性物质层的空穴的平均直径与输出的关系的图。图10是表示本实施例及比较例的正极活性物质的空穴的峰直径/平均直径与输出的关系的图。如表1所示可以确认:与比较例1~12相比,实施例1~29具有较高的输出密度。
在图6中,横轴表示空隙率(%),纵轴表示输出(w/kg)。由该图6可以确认:通过使正极活性物质层的空隙率为10%~45%,从而得到高输出特性。在图7中,横轴表示密度(g/cm3),纵轴表示输出(w/kg)。由该图7可以确认:通过使正极活性物质层的密度为2.7~3.9g/cm3,从而得到高输出特性。在图8中,横轴表示峰直径(μm),纵轴表示输出(w/kg)。由该图8可以确认:通过使在空穴分布曲线中的空穴的峰直径为0.06~0.3μm,从而得到高输出特性。在图9中,横轴表示平均直径(μm),纵轴表示输出(w/kg)。由该图9可以确认:通过使空穴的平均直径为0.03~0.2μm,从而得到高输出特性。在图10中,横轴表示空穴峰直径/空穴平均直径,纵轴表示输出(w/kg)。由该图10可以确认:通过使空穴的峰直径相对于空穴的平均直径的比值(峰直径/平均直径)为1.1~2.4,从而得到高输出特性。产业上的可利用性具备使用了本发明的正极活性物质的非水系电解质二次电池用电极的非水系电解质二次电池具有优异的输出密度和耐久性,因此能够适合利用于电动汽车等大型动力设备中。