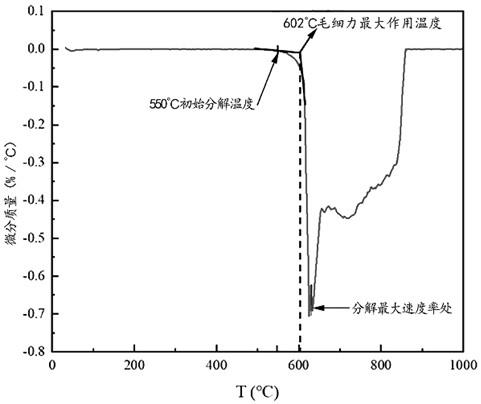
1.本发明涉及锂离子电池领域,具体而言,本发明涉及一种低温固相再生锂离子电池正极材料的方法及由此得到的锂离子电池正极材料。
背景技术:2.随着新能源行业的不断发展、锂离子电池的广泛应用,退役电池的数量亦将迎来爆发式增长。对锂离子电池正负极材料进行回收再生,实现资源再利用,对于环保以及整个行业的可持续发展具有重要意义。
3.对于锂离子电池正极材料而言,在经过长期充放电循环后,部分锂将残留在负极中无法脱嵌形成死锂,导致正极材料中锂“缺失”,因此再生正极材料时通常需要补锂,以使再生的正极材料能够用于锂离子电池。
4.cn110277552a公开一种废旧电池中镍钴锰三元正极材料的修复再生方法,包括除胶、除导电剂的步骤1;除集电体的步骤2;补镍钴锰的步骤3;及补锂的步骤4,其中补锂之后需要在700-900℃的下进行煅烧。这种高温固相法再生法,不仅工艺繁复、耗能,而且补锂效果不佳。
5.此外,镍钴锰系(ncm)锂离子电池正极材料的原始结构为层状结构,锂缺失导致材料结构中出现锂空位,锂空位又导致层状结构塌陷和锂镍混排。这种内部结构破坏严重的正极材料,一般无法通过高温固相法实现结构还原和结构缺陷完全恢复,再生之后内部结构中仍存在锂空位,导致补锂不均匀,使得再生的正极材料难以恢复初始的容量水平。
6.因而,仍需进一步改进锂离子电池正极材料,特别是三元正极材料的再生方法,提高补锂均匀性,进而使再生正极材料恢复较高的容量水平,并降低工艺能耗,提高再生效率及成本效益。
技术实现要素:7.为解决上述问题,本发明人进行了深入研究和大量实验,提出了一种在较低温度下固相再生锂离子电池正极材料的方法。该方法在除杂过程中,巧妙地利用在较低的温度下除去碳质导电剂(如导电炭黑)的过程中,通过碳质导电剂缓慢分解为二氧化碳,在正极材料中形成毛细孔道,使得在该温度下已经熔化的锂源借助于毛细作用进入正极材料的内部。由于导电剂在正向制造过程中已分散的十分均匀,因而在缓慢热分解过程可产生均匀分布的孔道,进而为补锂的锂源提供均匀的位点,使得补锂更加均匀高效。
8.具体而言,一方面,本发明提供一种低温固相再生锂离子电池正极材料的方法,包括以下步骤:(1)收集锂离子电池正极极片并分离出集电体,得到其中含有导电剂和正极活性物质的锂离子电池正极材料;(2)按配锂量li/tm为1~1.1的量,将得自步骤(1)的锂离子电池正极材料与固态锂源充分混合并干燥,得到一混合物,
式li/tm中,li是所述固态锂源中li的摩尔数,tm是得自步骤(1)的锂离子电池正极材料中所含有的每种金属元素的摩尔数之和;(3)将得自步骤(2)的混合物在氧气或空气氛围中,于温度t下进行热处理,该温度t满足:max(t1,t2)《t《t3,得到再生锂离子电池正极材料,式max(t1,t2)《t《t3中,t1为导电剂开始分解的温度,t2为固态锂源开始熔化的温度,t3为导电剂分解速率最大的温度,max(t1,t2)表示t1和t2中较大的一个。
9.另一方面,本发明还提供一种根据前述方法再生的锂离子电池正极材料。
10.相比于现有高温固相再生正极材料的方法,本发明的再生方法巧妙地利用已存在的均匀分散的碳质导电剂于较低温度下的缓慢分解,在正极材料中形成毛细孔道,并借助孔道的毛细作用实现精确、深度和均匀的补锂;同时也简化了工艺并降低了能耗。
附图说明
11.图1是导电炭黑(sp)的热重曲线;及图2是导电炭黑(sp)的热重微分曲线。
具体实施方式
12.下面通过实施例对本技术进一步详细说明。通过这些说明,本技术的特点和优点将变得更为清楚明确。
13.此外,下面所描述的本技术不同实施方式中涉及的技术特征只要彼此之间未构成冲突即可相互结合。
14.如前所述,本发明提供一种低温固相再生锂离子电池正极材料的方法,包括以下步骤:(1)收集锂离子电池正极极片并分离出集电体,得到其中含有导电剂和正极活性物质的锂离子电池正极材料;(2)按配锂量li/tm为1~1.1的量,将得自步骤(1)的锂离子电池正极材料与固态锂源充分混合并干燥,得到一混合物,式li/tm中,li是所述固态锂源中li的摩尔数,tm是得自步骤(1)的锂离子电池正极材料中所含有的每种金属元素的摩尔数之和;(3)将得自步骤(2)的混合物在氧气或空气氛围中,于温度t下进行热处理,该温度t满足:max(t1,t2)《t《t3,得到再生锂离子电池正极材料,式max(t1,t2)《t《t3中,t1为导电剂开始分解的温度,t2为固态锂源开始熔化的温度,t3为导电剂分解速率最大的温度,max(t1,t2)表示t1和t2中较大的一个。
15.在根据本发明的方法的一个实施方案中,步骤(3)中所述的氧气或空气的流速为0.1~2.5ml/(g
·
min)。
16.在根据本发明的方法的一个实施方案中,所述导电剂为选自导电炭黑、导电石墨、科琴黑和气相生长碳纤维vgcf中的一种或多种;所述固态锂源为氢氧化锂。
17.在根据本发明的方法的一个实施方案中,所述导电剂为导电炭黑,且步骤(3)中所述温度t为550-625℃,优选为550-602℃。
18.在根据本发明的方法的一个实施方案中,所述导电剂在所述锂离子电池正极材料
中的重量含量为1.1~3%,且其粒度为30~50nm。
19.在根据本发明的方法的一个实施方案中,步骤(3)中所述的热处理进行4~15h。
20.在根据本发明的方法的一个实施方案中,步骤(1)中所述分离是利用极性溶剂处理正极极片,使得正极材料与集电体相分离,其中所述极性溶剂为选自下列中的一种或多种:n-甲基吡咯烷酮(nmp),二甲亚砜(dmso),n,n-二甲基甲酰胺(dmf),n,n-二甲基乙酰胺(dmac),及丙酮。
21.在根据本发明的方法的一个实施方案中,还包括在步骤(1)之后和步骤(2)之前,对所述锂离子电池正极材料进行碱洗,以除去该锂离子电池正极材料中残留的集电体的步骤。
22.在根据本发明的方法的一个实施方案中,所述碱洗所用的碱可以是氢氧化钠或者氢氧化锂。
23.在根据本发明的方法的一个实施方案中,进一步包括在碱洗之后进行醇洗,以除去碱洗过程中残留的碱的步骤。
24.在根据本发明的方法的一个实施方案中,所述锂离子电池正极材料为选自下列中的一种或多种:licoo2;limn2o4;linio2;lini
0.5
mn
1.5
o4;lini
x
coyal
1-x-y
o2,式中0<x<1,0<y<1,0<x+y<1;lini
x
coymn
1-x-y
o2,式中0<x<1,0<y<1,0<x+y<1。
25.另外,本发明还提供一种根据前述的方法得到的锂离子电池正极材料。
26.在根据本发明的方法中,为了保证碳质导电剂分解能够形成毛细孔道,不仅要控制热处理的温度,还需要控制步骤(3)中热处理时的氧气或空气的流速,即每分钟通过每克要再生的正极材料的氧气或者空气的体积,为0.1~2.5ml/(g
·
min)。通氧速率过慢,导电碳材料分解过慢,补锂时间过长;通氧速率过快,导电碳材料分解过快,无法形成充分的毛细作用。
27.在根据本发明的方法中,锂离子电池正极极片与集电体的分离采用极性溶剂溶出法,即利用诸如n-甲基吡咯烷酮等极性溶剂,溶出正极极片中所含的粘结剂如聚偏二氟乙烯(pvdf),从而使正极活性物质层与集电体相分离,然后通过例如筛分法去除集电体(通常为铝质),得到其中含有导电剂和正极活性物质的锂离子电池正极材料。
28.作为一种选择,由于溶剂溶出脱附以及筛分过程中可能导致与集电体分离的正极材料中仍残留少量的正极集电体铝,可在补锂之前,采用三段碱洗或过量碱洗的方式处理正极材料以除去残余的集电体铝。
29.三段式碱洗是指采用高中低三种浓度的碱依次进行洗涤。碱洗可采用氢氧化钠溶液或氢氧化锂溶液。通过碱洗,不仅可以除去残留的集电体铝,也可以除去可能情况下正极材料表面的氧化铝包覆层,便于后续的补锂,使得锂源更顺利地到达正极材料结构的内部。过量碱洗是指,相对于正极材料可能的含铝量,采用过量氢氧化钠溶液或氢氧化锂溶液进行处理。
30.在根据本发明的方法中,配锂量li/tm是指为补锂而要加入的固态锂源中锂的摩尔数(li)与经测量而确定的已经与集电体分离的正极材料中所含各种金属的总摩尔数(tm)之比。例如,正极材料为lini
0.5
mn
1.5
o4时,可通过电感耦合等离子体(icp)发射光谱测量其中li、ni、mn各自的摩尔数,三者之和即为tm。
31.在根据本发明的方法中,配锂量li/tm为1~1.1。当li/tm低于1时,锂的化学计量比
不足1,再生的正极材料仍为失锂状态;当li/tm大于1.1时,添加的锂源过量,会导致再生的正极材料表面残留lioh,影响再生正极材料的容量恢复。
32.在根据本发明的方法中,将分离出集电体而得到的正极材料与固态锂源混合成均匀的混合物,然后将该混合物在一定温度t下进行热处理,以同时实现正极材料中所含导电剂如导电石墨缓慢分解和固态锂源处于熔化状态。因而该温度t应当满足:max(t1,t2)《t《t3,式中t1为导电剂开始分解的温度,t2为固态锂源开始熔化的温度,t3为导电剂分解速率最大的温度。
33.图1是导电炭黑(sp)的热重曲线,如图所示,当导电剂sp的质量开始变化时,表明其开始分解,可以产生毛细作用,对应的温度即导电剂开始分解的温度t1,大约550℃;当重量变化达到99%的时候,表明导电剂sp已经完全分解,导电剂sp无法再发挥产生毛细力的作用,此时对应的温度称为导电剂完全分解的温度。容易理解的是,只要控制合适的热处理时间,完全可以实现碳质导电剂在热处理温度范围max(t1,t2)《t《t3完全分解。
34.在根据本发明的方法中,使用氢氧化锂作为固态锂源,其熔点即固态锂源开始熔化的温度t2为450℃;所以max(t1,t2)=t1,即导电剂开始分解的温度。
35.如图2所示,当导电剂sp的质量损失率达到最大值,对应热重微分曲线到达第一个峰值,此时导电剂sp分解速率最大,对应的温度即为导电剂分解速率最大的温度t3,大约625℃;当分解速率到达最大分解速率1/2时,此时分解速率适中,毛细作用最强,对应的具体温度可以通过在分解速率达到1/2时对热重微分曲线做切线获得,所得温度大约602℃,作为热处理温度的优选上限。
36.现有的锂离子电池的正极材料中,通常包含正极活性物质、导电剂和粘结剂。当通过溶剂去除粘结剂之后,在通过分出集电体而得到的锂离子电池正极材料中,导电剂的重量含量一般为1.1~3%,且其粒度为30~50nm。根据本发明的方法适用于这样的正极材料的再生。如果导电剂的含量过低,则无法产生持续的毛细作用;如果导电碳材料含量过大,则影响电池的容量。另外,若果导电剂的粒度过大,则前述的毛细作用变弱。
37.在根据本发明的方法中,步骤(3)中的热处理进行4~15h,取决于实际的热处理温度选择;当热处理温度较低时,导电碳材料分解速度慢,需要较长热处理时间;当热处理温度较高时,碳材料分解相对较快,热处理时间较短。
38.试验表明,当氧气或空气的流速为0.1~2.5ml/(g
·
min),热处理温度t为550-625℃时,热处理的时间一般为4~15h。这种条件下,待再生的锂离子电池正极材料中所含有的导电剂可以缓慢分解并形成微细孔道。
39.在根据本发明的方法中,作为一种选择,当进行碱洗之后,还可以对分离出集电体的正极材料进行醇洗,以除去碱洗过程中残留的碱。用于醇洗的醇可以为例如无水乙醇,对此没有特殊的限制。
40.适合利用本发明的方法进行再生的锂离子电池正极材料可以是licoo2;limn2o4;linio2;lini
0.5
mn
1.5
o4;lini
x
coyal
1-x-y
o2,式中0<x<1,0<y<1,0<x+y<1;lini
x
coymn
1-x-y
o2,式中0<x<1,0<y<1,0<x+y<1中的一种或多种。
41.需要说明的是,本发明的收集锂离子电池正极极片并分离出集电体,不能采用高温脱附,因为高温脱附无法去除粘结剂pvdf,而且会导致pvdf分解出hf(氢氟酸)并与材料中的li和al反应,生成lif和alf3。lif和alf3残留在正极材料中难以去除。
42.作为一种选择,在采用溶剂法分离集电体和正极材料时,可先将破碎的正极碎片在极性溶剂中实施超声处理,接着用筛网滤除集电体,前述极性溶剂为非质子极性溶剂;前述超声处理可在20~50℃温度下进行5~60 min;所使用的筛网网孔尺寸,依据正极碎片的尺寸,一般可以为70~400目,优选为100~200目。
43.另外,通过筛网滤除集电体之后,可通过过滤法(例如陶瓷板过滤)除去所述极性溶剂,进而得到除去集电体的锂离子电池正极材料。
44.以下通过实施例对本发明进行进一步说明。
45.实施例1将回收lini
0.56
co
0.12
mn
0.32
o2(ncm562)正极极片破碎至5mm2大小,送入nmp超声池中,于50℃超声20min后,采用300目筛网过滤去除集电体铝箔,而后进一步采用陶瓷滤板过滤,同时去除回收正极材料中的集电体铝箔和粘结剂pvdf,得到三元正极湿料。接着,先后采用高(3mol/l)、中(1mol/l)、低(0.2mol/l)三种浓度的氢氧化钠碱液分段冲洗,去除正极材料表面包覆层氧化铝,最后再用无水乙醇清洗,去除表面残碱,烘干后得到纯化除杂后的回收三元正极材料,回收的正极材料包括活性物质和导电炭黑,导电碳黑含量1.5%,导电碳黑粒度粒度分布范围40-50nm。
46.对除杂后的ncm562材料进行icp测试,得到li/tm(锂与镍钴锰之和的摩尔数之比),添加lioh作为锂源直至li/tm为1.02,将ncm与lioh采用高速混合机混合均匀,送入管式炉中升温至600℃持续通氧9h,通氧速率2.0ml/(g
·
min),得到再生的三元正极材料。
47.实施例2按照实施例1的工艺步骤进行低温固相补锂,不同之处在于通氧速率0.1ml/(g
·
min)。
48.实施例3按照实施例1的工艺步骤进行低温固相补锂,不同之处在于通氧速率2.5ml/(g
·
min)。
49.实施例4按照实施例1的工艺步骤进行低温固相补锂,不同之处升温至550℃通氧9h。
50.实施例5按照实施例1的工艺步骤进行低温固相补锂,不同之处升温至625℃通氧9h。
51.实施例6按照实施例1的工艺步骤进行低温固相补锂,不同之处在于导电碳黑含量3.0%,导电碳黑粒度粒度分布范围30-35nm。
52.实施例7按照实施例1的工艺步骤进行低温固相补锂,不同之处在于加入lioh调整li/tm为1.10。
53.对比例1按照实施例1的工艺步骤进行低温固相补锂,不同之处升温至500℃通氧9h。
54.对比例2按照实施例1的工艺步骤进行除杂,不同之处在于直接在700℃下通氧12h。
55.对比例3
按照实施例1的工艺步骤进行除杂,不同之处在于导电碳材料是碳纳米管,锂源是氢氧化锂,在500℃下通氧12h。
56.对比例4按照实施例1的工艺步骤进行除杂,不同之处在于导电碳材料粒度范围在60-80nm。
57.对比例5按照实施例1的工艺步骤进行除杂,不同之处在于通氧速率0.08ml/(g
·
min)。
58.对比例6按照实施例1的工艺步骤进行除杂,不同之处在于通氧速率2.8ml/(g
·
min)。
59.对以上实施例和对比例中再生处理得到的三元正极材料的容量水平进行测试:在25℃下,将得自实施例和对比例的再生正极材料,按94%正极材料+3%导电碳sp+3%pvdf于nmp中进行正极合浆,单面涂布,组装成纽扣电池。以最大充电倍率充电、以1c倍率放电,进行满充满放循环测试,直至电池的容量减至初始容量的80%,记录容量保持率,并将测试结果以及各实施例和对比例中具体情况总结于下面的表中。
60.需要说明的是,用于本发明的物料的来源如下:物料名称简称来源导电碳
ꢀꢀꢀꢀꢀꢀꢀꢀꢀꢀꢀꢀꢀꢀꢀ
sp
ꢀꢀꢀꢀꢀꢀꢀꢀꢀꢀꢀꢀꢀꢀꢀꢀ
卡博特聚偏氟乙烯
ꢀꢀꢀꢀꢀꢀꢀ
pvdf
ꢀꢀꢀꢀꢀꢀꢀꢀꢀꢀꢀꢀꢀꢀ
苏威碳纳米管
ꢀꢀꢀꢀꢀꢀꢀꢀꢀꢀꢀ
cnts
ꢀꢀꢀꢀꢀꢀꢀꢀꢀꢀꢀꢀꢀꢀ
天奈氢氧化钠
ꢀꢀꢀꢀꢀꢀꢀꢀꢀꢀꢀꢀ
naoh
ꢀꢀꢀꢀꢀꢀꢀꢀꢀꢀꢀꢀꢀꢀ
麦克林n-甲基吡咯烷酮
ꢀꢀꢀꢀꢀꢀꢀ
nmp
ꢀꢀꢀꢀꢀꢀꢀꢀꢀꢀꢀꢀꢀꢀꢀ
天奈对以上实施例和对比例中再生处理得到的三元正极材料的容量水平进行测试,结果如下表所示:
样品锂源导电剂粒度范围nmli/tm升温模式通氧速率ml/(g
·
min)初始克容量(mah/g)实施例1lioh导电炭黑40-501.02600℃9h2.0189.1实施例2lioh导电炭黑40-501.02600℃9h0.1188.4实施例3lioh导电炭黑40-501.02600℃9h2.5188.7实施例4lioh导电炭黑40-501.02550℃9h2.0187.9实施例5lioh导电炭黑40-501.02625℃9h2.0188.1实施例6lioh导电炭黑30-351.02600℃9h2.0187.1实施例7lioh导电炭黑40-501.10600℃9h2.0188.5对比例1lioh导电炭黑40-501.02500℃9h2.0166.5对比例2lioh导电炭黑40-501.02700℃12h2.0170.1对比例3lioh碳纳米管40-501.02500℃12h2.0160.1对比例4lioh导电炭黑60-801.02600℃9h2.0172.1对比例5lioh导电炭黑40-501.02600℃9h0.08170.3对比例6lioh导电炭黑40-501.02600℃9h2.8176.4
结合实施例1,4,5和对比例1可知,当温度低于550℃时,虽然已经达到氢氧化锂熔融温度,但未达到导电剂的分解温度,无法通过导电剂分解产生二氧化碳,利用二氧化碳逸出形成的空位内部相应产生的毛细力吸入锂,导致材料的克容量相对偏低;结合实施例1,4,5和对比例2相比,当温度高于625℃时,导电碳分解速率达到最大值,分解速率过快,无法产生毛细作用。
61.从对比例3中可以看出,在导电碳材料的完全分解温度小于锂源熔融温度时,虽温度达到锂源熔融温度,但此时导电碳材料碳纳米管已经完全分解,无法利用毛细作用进行补锂。
62.结合对比例1和对比例4可知,导电剂粒度大于50nm时,由于粒度较大,毛细作用减弱,导致电池克容量减少。
63.结合实施例1-3与对比例5和6可知,当通氧速率低于0.1 ml/(g
·
min)时,通氧速率过慢,影响导电碳分解速率,导致电池初始克容量减小;当通氧速率高于2.5 ml/(g
·
min),通氧速率过快,毛细作用减弱,导致电池初始克容量减小。
64.综上所述,根据本发明的方法实现了在较低温度进行固相补锂/结构修复;并将除杂(如除去导电剂)和补锂工艺相结合,简化了正极材料的再生流程,同时又实现了比较理想的补锂效果。因为正向制造过程中已分散十分均匀的导电剂缓慢分解为二氧化碳,该二氧化碳逸出时在材料内部形成毛细孔道,并借助于毛细力吸入因熔化而离解的锂,进而实现了更加均匀高效的补锂,使得通过本发明的方法再生正极材料具有较高的克容量。
65.以上结合优选实施方式对本技术进行了说明,然而这些实施方式仅为范例性起到说明性的作用。在此基础上,可以对本技术进行多种替换和改进,均落入本技术保护范围内。