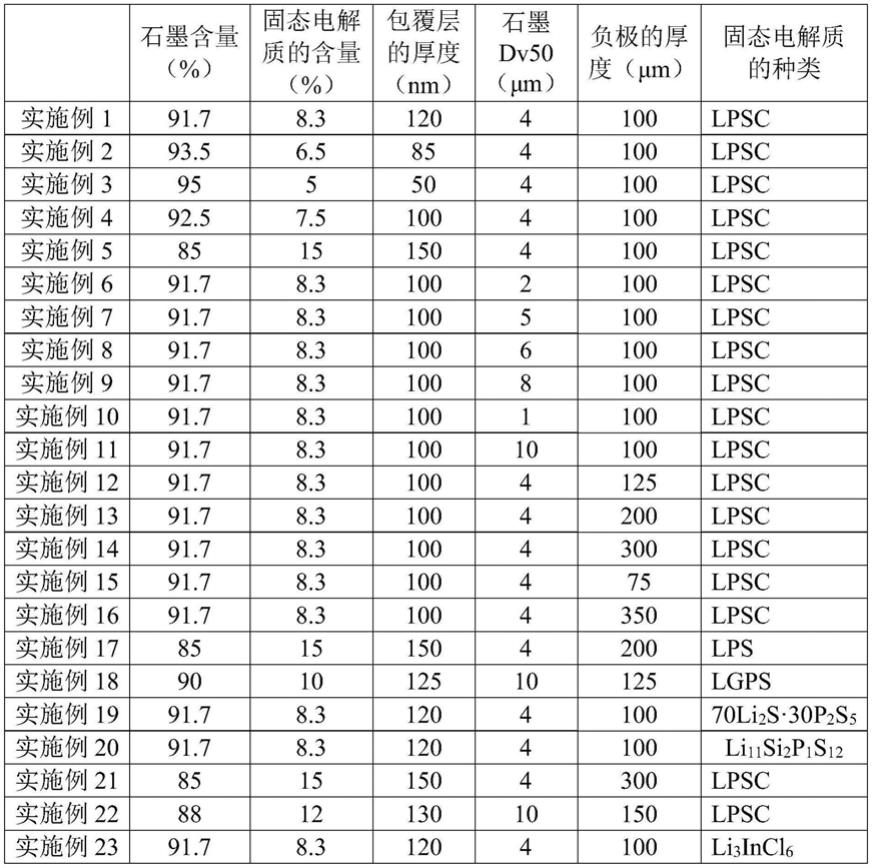
p-s玻璃陶瓷、硫银锗矿型li6ps5x、li
11-cm2-c
p
1+cs12
,其中,20≤x≤80,x选自cl、br和i中至少一种,m选自ge、sn和si中的至少一种,c为0~5。
13.上述的复合材料中,所述硫化物固态电解质可选自li6ps5cl、li3ps4、70li2s
·
30p2s5、li
11
si2p1s
12
和li
10
gep2s
12
中的至少一种。
14.本技术中,制备所述li6ps5cl按照如下方法:将原料li2s、p2s5和licl根据摩尔比进行500~600rpm/min球磨,然后高温500~600℃烧结,即合成li6ps5cl;
15.制备所述li3ps4按照如下方法:将原料li2s、p2s5和licl根据摩尔比进行500-600rpm/min球磨,然后高温300~450℃烧结,即合成li3ps4;
16.制备所述70li2s
·
30p2s5按照如下方法:将原料li2s、p2s5根据摩尔比进行500-600rpm球磨,然后高温200~350℃烧结,即合成70li2s
·
30p2s5;
17.制备所述li
11
si2p1s
12
按照如下方法:将原料li2s、p2s5、sis2根据摩尔比进行500-600rpm球磨,然后高温400~600℃烧结,合成得到所述li
11
si2p1s
12
;
18.制备所述li
10
gep2s
12
,按照如下方法:将原料li2s、p2s5、ges2根据摩尔比进行500-600rpm球磨,然后高温400~600℃烧结,合成得到所述li
11
si2p1s
12
。
19.上述的复合材料中,所述石墨的形状为粒状、磷片状、片状和块状中的至少一种;
20.所述固态电解质在所述石墨表面以面包覆和/或点包覆的形式存在。
21.上述的复合材料中,基于所述复合材料的质量,所述石墨的含量可为85%~95%,所述固态电解质的含量可为5~15%。
22.本技术第二方面提供了上述的复合材料的制备方法,包括如下步骤:将所述固态电解质、石墨加入第一溶剂中,经过分散、加热处理,获得所述复合材料。
23.上述的制备方法中,所述将固态电解质、石墨加入第一溶剂中,经过分散、烘干处理,获得所述复合材料的步骤包括:
24.将所述固态电解质加入到第一溶剂中,得到第一混合溶液;
25.将所述石墨加入所述第一混合溶液中,进行分散处理,得到第二混合溶液;
26.将所述第二混合溶液在第一预设温度下进行加热,蒸干所述第一溶剂,得到所述复合材料。
27.上述制备方法中,所述第一溶剂包括无水乙醇和/或n-甲基吡咯烷酮,所述第一预设温度为70~85℃。
28.本技术中,每0.1克所述固态电解质与每1-20ml所述第一溶剂的混合。
29.本技术中,所述处理采用超声。
30.本技术第三方面提供了一种负极,所述负极包括粘接剂、导电剂、第一硫化物固态电解质以及上述的复合材料。
31.本技术中,所述负极包括如下质量百分含量的组分制成,以负极质量的总量为100%计:
32.复合材料占85%~95%;
33.粘结剂占0.5%~2%;
34.导电剂占3%~10%;
35.余量为第一固态电解质。
36.上述的负极中,所述粘结剂选自ptfe、sbr、nbr和pvdf中的至少一种,优选为ptfe;
37.所述导电剂选自superp、乙炔黑、科琴黑、炭黑、碳纳米管、石墨烯和碳纤维中的至少一种。
38.本技术中,所述负极具体由如下质量百分含量的组分制成,以总量为100%计:
39.所述复合材料90%;
40.所述粘结剂1%;
41.导电剂4%;
42.固态电解质5%。
43.本技术中,所述负极的厚度可为100~300μm,具体可为100μm、150μm、200μm、300μm、100~150μm、150~200μm、200~300μm、100~200μm或150~300μm。
44.本技术第四方面提供了上述负极的制备方法,包括如下步骤:1)将所述复合材料、所述粘结剂、所述导电剂、所述第一固态电解质按照比例进行球磨混合,得到球磨后的混合原料;
45.2)对所述球磨后的混合原料进行辊压,即得到所述负极。
46.上述的制备方法中,步骤1)中所述球磨的转速可为200-350rpm/min,球磨时间可为30-60min;
47.所述球磨在氧化锆球磨罐中采用直径可为2-10mm的氧化锆球进行;
48.步骤2)中,所述辊压在辊压机进行;
49.所述辊压的条件如下:
50.所述辊压机的上辊与下辊之间的间距可可为100μm~300μm;
51.辊速可为1-3m/min。
52.本技术第五方面提供了一种固态电池,包括正极、第一固态电解质层和上述负极。
53.本技术第六方面提供了一种用电设备,该用电设备包括上述的固态电池,其中固态电池作为用电设备的供电电源。
54.本技术具有以下有益效果:
55.1、本技术复合材料用于制备负极,由于固态电解质是包覆在石墨表面,因此有利于固态电解质与石墨的充分接触,促进了负极活性材料(石墨)容量的发挥,从而提高电池的首效以及提升电池循环性能;其次,柔性的石墨负极与固态电解质层更有效的接触,降低了界面电阻,促进界面处的锂离子传输。
56.2、采用复合材料制备负极的方法利用粘结剂在高速剪切力作用下容易纤维化易于成膜,原料混合辊压即能形成微米级厚度的自支撑负极;制备方法简单,无需使用有毒溶剂形成负极,规避了有毒溶剂干燥与溶剂后处理的步骤,大大减少了负极制备的步骤,规避了负极制备过程中,有毒溶剂对环境与人的危害。
57.3、负极结构有利于离子与电子的传输,且无需使用铜箔作为集流体,用作固态电池的负极时,能降低固态电池的整体重量,节约成本。
附图说明
58.图1为本技术实施例1复合材料颗粒的结构示意图,其中a为石墨,b为具有固态电解质包覆石墨的复合材料。
59.图2为本技术实施例1固态电池的示意图。
60.图2中各个标记如下:
61.1负极;2固态电解质层;3正极。
具体实施方式
62.下述实施例中所使用的实验方法如无特殊说明,均为常规方法。
63.下述实施例中所用的材料、试剂等,如无特殊说明,均可从商业途径得到。
64.本技术首先提供了一种复合材料,包括内核和设置在所述内核表面的包覆层;
65.所述内核包含石墨;
66.所述包覆层的材料包括固态电解质。
67.本技术利用固态电解质对石墨进行包覆,从而可以提高固态电解质与石墨表面的接触性能,有效的将固态电解质“浸润”到石墨中,进而有利于活性材料容量的发挥。
68.进一步的,为了提高电解质在电极中浸润性,同时避免石墨粒径过大或过小导致接触不充分,从而影响界面处的锂离子传输,所述石墨的粒径dv50可包括2~8μm;
69.所述包覆层的厚度可包括50~150nm,具体可包括50nm、125nm、130nm、150nm。
70.固态电解质包括硫化物固态电解质、聚合物固态电解质、卤化物固态电解质、金属氧化物固态电解质中的一种或多种。其中卤化物固态电解质包括li3incl6、li3ycl6、li3tbcl6、li3ercl6;金属氧化物固态电解质包括lialo2、li2zro3、li4ti5o
12
。由于硫化物固态电解质具有优良的电导率,因此本技术采用硫化物固态电解质作为包覆材料。
71.进一步的,为了促进电子的传输,且无需使用铜箔作为集流体,以降低负极制备固态电池的重量,同时节约成本,硫化物固态电解质可包括li6ps5cl、li3ps4、70li2s
·
30p2s5、li
10
gep2s
12
、li
11
si2p1s
12
。
72.下述实施例中,制备所述li6ps5cl按照如下方法:将原料li2s、p2s5和licl根据摩尔比进行500-600rpm/min球磨,然后高温500~600℃烧结,即合成li6ps5cl;
73.制备所述li3ps4按照如下方法:将原料li2s、p2s5和licl根据摩尔比进行500-600rpm/min球磨,然后高温300~450℃烧结,即合成li3ps4;
74.制备所述70li2s
·
30p2s5按照如下方法:将原料li2s、p2s5根据7:3的摩尔比进行500-600rpm/min球磨,然后高温200~350℃烧结,即合成70li2s
·
30p2s5;
75.制备所述li
11
si2p1s
12
按照如下方法:将原料li2s、p2s5、sis2根据摩尔比进行500rp-600m/min球磨,然后高温400~600℃烧结,合成得到所述li
11
si2p1s
12
;
76.制备所述li
10
gep2s
12
,按照如下方法:将原料li2s、p2s5、ges2根据摩尔比进行500-600rpm/min球磨,然后高温400~600℃烧结,合成得到所述li
11
si2p1s
12
。
77.进一步地,为了使柔性的负极与固态电解质层更有效的接触,优选以下石墨的形状和包覆形式,所述石墨的形状为粒状、磷片状、片状和块状中的至少一种;
78.所述固态电解质在所述石墨表面以面包覆和/或点包覆的形式存在。
79.上述的复合材料中,所述固态电解质包覆的石墨的质量百分含量为85%~95%,硫化物固态电解质的质量百分含量为5~15%。
80.为了制备上述的复合材料,按照包括如下步骤进行:
81.将所述固态电解质加入到无水乙醇中,得到第一混合溶液;
82.将所述石墨加入所述第一混合溶液中,进行超声分散处理,得到第二混合溶液;
83.将所述第二混合溶液在70~85℃进行加热,蒸干无水乙醇,得到所述复合材料。
84.每0.1克所述硫化物固态电解质与每1~20ml所述无水乙醇混合。
85.本技术还提供了一种负极,所述负极包括粘接剂、导电剂、第一固态电解质以及上述的复合材料。在本技术中,第一固态电解质的种类和固态电解质的种类相同。
86.所述负极具体由如下质量百分含量的组分制成,以负极质量的总量为100%计:
87.复合材料占85%~95%;
88.粘结剂占0.5%~2%;
89.导电剂占3%~10%;第一固态电解质占1~8%。
90.本技术还提供了上述负极的制备方法,包括如下步骤:1)将所述复合材料、所述粘结剂、所述导电剂、所述第一固态电解质按照比例进行球磨混合,得到球磨后的混合原料;
91.2)对所述球磨后的混合原料进行辊压,即得到所述负极。
92.上述的制备方法中,步骤1)中所述球磨的转速可为200-350rpm/min,球磨时间可为30-60min;
93.为了提供足够的剪切力使粘结剂纤维化,所述球磨在氧化锆球磨罐中采用直径可为2~10mm的氧化锆球进行;
94.在步骤2)中为了得到所需的负极的厚度,通过控制辊压机的上辊与下辊之间的间距实现,所述辊压机的上辊与下辊之间的间距可为100μm~300μm;
95.为了使制备的负极支撑性能更好,优化以下辊压的参数实现,辊速可为1-3m/min。
96.本技术还提供了一种固态电池,包括正极、固态电解质层和上述负极。其中固态电解质层中包含有第二固态电解质,第二固态电解质和第一固态电解质以及包覆层中的固态电解质种类相同。
97.在另一实施例中,包覆层中的固态电解质、负极中的第一固态电解质和固态电解质层中的第二固态电解质具有不同颗粒dv50和不同比表面积,其中,颗粒dv50由大到小依次为固态电解质层中的第二固态电解质、包覆层中的固态电解质、负极中的第一固态电解质。负极中的第一固态电解质的颗粒为纳米级,其dv50为5~35nm,其比表面积为200~350m2/g;第二固态电解质的颗粒dv50为8~15μm,比表面积为12~28m2/g;包覆层中的固态电解质的颗粒为纳米级,其dv50为50~150nm,比表面积为80~130m2/g。负极中的第一固态电解质的颗粒dv50最小,其可以有效填充在复合材料之间,提高负极的锂离子传导和电子传导性能。固态电解质层中的第二固态电解质作为锂离子传输的场所,若第二固态电解质的dv50过大,则引起锂离子扩散路径过长,而若其dv50过小,则容易引起副反应的发生,都不利于电池性能的发挥。
98.本技术还提供了一种用电设备,该用电设备包括上述的固态电池,其中固态电池作为用电设备的供电电源。
99.下面结合实施例和附图对本技术作详细描述。
100.实施例1
101.1、复合材料的制备:
102.(1)将0.415g li6ps5cl(简称为lpsc)分散在50ml无水乙醇中,形成第一混合溶液;
103.(2)将4.585g dv50为4μm的石墨分散在第一混合溶液中,超声分散处理1h,形成第二混合溶液;
104.(3)将第二混合溶液进行80℃真空干燥,蒸干无水乙醇,获得li6ps5cl包覆石墨(lpsc@gr)的复合材料,其中复合材料中石墨含量占91.7%,li6ps5cl含量占8.3%,包覆层的厚度为120nm。
105.2、负极的制备:
106.(1)将以上制得的复合材料、粘结剂(ptfe)、导电剂(石墨烯)、lpsc按照比例90:1:4:5共5g进行称量,将称量好的原料放入氧化锆球磨罐中,然后再加入50g直径为10mm的氧化锆球进行球磨,其中球磨转速为200rpm/min,球磨时间30min。
107.(2)球磨后的原料利用辊压机进行辊压,调整上辊与下辊之间的间距为100μm,调整辊速为1m/min,经过裁剪冷压,获得厚度为100μm的负极。
108.3、固态电池的制备
109.(1)固态电解质片的制备
110.将硫化物固态电解质(lpsc)置于模具中,通过施加压力10mpa,制备成厚度为100μm、直径为10mm的固态电解质片。
111.(2)正极的制备
112.在手套箱中,按照质量比70:30称取正极材料lno@ncm622与硫化物固态电解质(lpsc),研磨混合均匀,其中lno@ncm622指的是linbo3包覆lini2co2mn2o2,且在正极材料中linbo3的包覆量为0.5%~1%。称取混合后的物料20mg置于直径10mm的固态电池模具中,施加10mpa的压力,得到正极压片,侧放置直径10mm的涂炭铝箔圆片作为集流体,得到正极。
113.(3)固态电池的制备
114.将上述正极3、固态电解质片(即硫化物固态电解质层)2、负极1组装成固态电池(固态电池的结构参见图2)。
115.实施例2
116.与本技术实施例1相同,不同的是,复合材料的制备过程中,加入0.325g li6ps5cl和4.675g石墨,制备得到的复合材料中石墨含量占93.5%,li6ps5cl的含量占6.5%,包覆层的厚度为85nm。
117.实施例3、
118.与本技术实施例1相同,不同的是,复合材料的制备过程中,加入0.25g li6ps5cl和4.75g石墨,制备得到的复合材料中石墨含量占95%,li6ps5cl的含量占5%,包覆层的厚度为50nm。
119.实施例4、
120.与本技术实施例1相同,不同的是,复合材料的制备过程中,加入0.375g li6ps5cl和4.625g石墨,制备得到的复合材料中石墨含量占92.5%,li6ps5cl的含量占7.5%,包覆层的厚度为100nm。
121.实施例5、
122.与本技术实施例1相同,不同的是,复合材料的制备过程中,加入0.75g li6ps5cl和4.25g石墨,制备得到的复合材料中石墨含量占85%,li6ps5cl的含量占15%,包覆层的厚度为150nm。
123.实施例6
124.与本技术实施例1相同,不同的是,复合材料的制备过程中,石墨dv50为2μm。
125.实施例7
126.与本技术实施例1相同,不同的是,复合材料的制备过程中,石墨dv50为5μm。
127.实施例8
128.与本技术实施例1相同,不同的是,复合材料的制备过程中,石墨dv50为6μm。
129.实施例9
130.与本技术实施例1相同,不同的是,复合材料的制备过程中,石墨dv50为8μm。
131.实施例10
132.与本技术实施例1相同,不同的是,复合材料的制备过程中,石墨dv50为1μm。
133.实施例11
134.与本技术实施例1相同,不同的是,复合材料的制备过程中,石墨dv50为10μm。
135.实施例12
136.与本技术实施例1相同,不同的是,负极的制备中,调整上辊与下辊之间的间距为125μm,获得厚度为125μm的负极。
137.实施例13
138.与本技术实施例1相同,不同的是,负极的制备中,调整上辊与下辊之间的间距为200μm,获得厚度为200μm的负极。
139.实施例14
140.与本技术实施例1相同,不同的是,负极的制备中,调整上辊与下辊之间的间距为300μm,获得厚度为300μm的负极。
141.实施例15
142.与本技术实施例1相同,不同的是,负极的制备中,调整上辊与下辊之间的间距为75μm,获得厚度为75μm的负极。
143.实施例16
144.与本技术实施例1相同,不同的是,负极的制备中,调整上辊与下辊之间的间距为350μm,获得厚度为350μm的负极。
145.申请实施例17
146.与本技术实施例5相同,不同的是,复合材料的制备中:硫化物固态电解质为li3ps4(简称lps),获得li3ps4包覆的石墨(lps@gr)。
147.负极的制备步骤中:
148.步骤(2)调整上辊与下辊之间的间距为200μm,调整辊速为1m/min,获得厚度为200μm的负极。
149.在固态电池的制备步骤中:
150.不同之处为硫化物固态电解质为lps。
151.实施例18
152.与本技术实施例1相同,不同的是,复合材料的制备步骤中:
153.0.5g硫化物固态电解质li
10
gep2s
12
(简称lgps);4.5g dv50为10μm石墨,获得li
10
gep2s
12
包覆的石墨(lgps@gr)(其石墨的质量百分含量为90%,lgps的质量百分比含量为10%),其中lgps层的厚度为125nm。
154.负极的制备步骤中:
155.步骤(2)调整上辊与下辊之间的间距为150μm,获得厚度为150μm的负极。
156.固态电池的制备步骤中:
157.不同之处为硫化物固态电解质为lgps。
158.实施例19
159.与本技术实施例1相同,不同的是,硫化物固态电解质为70li2s
·
30p2s5。
160.实施例20
161.与本技术实施例1相同,不同的是,硫化物固态电解质为li
11
si2p1s
12
。
162.实施例21
163.1、复合材料的制备步骤:
164.(1)将0.75g硫化物固态电解质li6ps5cl分散在45ml n-甲基吡咯烷酮(nmp)中,形成第一混合溶液;
165.(2)将4.25g dv50为5μm石墨分散在溶液a中,超声处理1h,形成第二混合溶液;
166.(3)将第二混合溶液进行80℃真空干燥,获得li6ps5cl包覆的石墨(lpsc@gr)(其石墨的含量为85%,li6ps5cl的含量占15%),其中lpsc层的厚度为150nm。
167.2、负极的制备步骤:
168.与本技术实施例1相同,不同的是,步骤(1)中加入40g直径为10mm的氧化锆球进行球磨,其中球磨转速为200rpm/min,球磨时间30min。
169.步骤(2)调整上辊与下辊之间的间距为300μm,调整辊速为1m/min,获得厚度为300μm的负极。
170.实施例22
171.与本技术实施例1相同,不同的是,
172.1、复合材料的制备过程中,0.6g硫化物固态电解质li6ps5cl,4.4g dv50为10μm的石墨,获得li6ps5cl包覆的石墨(lpsc@gr),其中lpsc层的厚度为130nm。
173.2、负极的制备:
174.(1)加入40g直径为10mm的氧化锆球进行球磨。
175.(2)调整上辊与下辊之间的间距为150μm,调整辊速为1m/min,获得厚度为150μm的负极。
176.实施例23
177.1、复合材料的制备:将licl、incl3和石墨在水中分散均匀后,经过60℃加热搅拌蒸发掉水分,得到li3incl6包覆石墨的复合材料。其中复合材料的石墨dv50为4μm,石墨含量占91.7%,li3incl6含量占8.3%,包覆层的厚度为120nm。
178.2、负极的制备与实施例1相同。
179.3、固态电池的制备:与实施例相同,不同的是固态电解质为li3incl6。
180.实施例24
181.1、负极材料的制备,将质量比为1:2的al2o3、li2co3经过球磨均匀混合后,在真空管式炉中以800℃进行高温锻烧10h,冷却后得到lialo2,将质量比为1:9的lialo2、石墨均匀分散在无水乙醇中,蒸干无水乙醇获得负极材料前驱体,载真空管式炉中以400℃对负极材料前驱体进行烧结,获得lialo2包覆石墨的负极材料。其中复合材料的石墨dv50为4μm,石墨含量占91.7%,lialo2含量占8.3%,包覆层的厚度为120nm。
182.2、负极的制备与实施例1相同。
183.3、固态电池的制备:与实施例1相同,不同的是固态电解质为lialo2。
184.对比例1
185.与实施例1不同的是,负极材料制备过程中,将0.415g li6ps5cl和4.585g的石墨,替换为5g的石墨,制备得到不具有硫化物固态电解质包覆层的石墨负极材料。
186.将实施例1-24、对比例1所制备得到的复合材料和负极的相关参数记录在表1中,并将所制备得到的固态电池进行全电池性能测试,测试方法为:利用新威测试柜对固态电池进行倍率充电与倍率放电。电池测试倍率为0.1c,工作电压范围2.75-4.3v,循环100圈。
187.对上述固态电池测试数据进行汇总,得到表2。
188.表1
[0189][0190][0191]
表2固态电池的性能测试结果
[0192][0193]
通过对比表1中不同参数的考察,比较表2中固态电池的性能结果可知:
[0194]
1、根据上述实施例1-24、对比例1的测试数据可见,与包覆有固态电解质的复合材料相比,不进行固态电解质包覆的负极材料,其固态电池的测试性能显著下降,表现为首效仅为62.2%,100圈循环保持率仅为71.3,其原因是当不具有固态电解质包覆时,固态电池中的负极活性材料(石墨)无法与固态电解质充分接触,导致无法确保固态电解质很好地浸润到石墨材料中,从而极大地影响了负极活性材料的首效发挥,以及影响固态电池的循环稳定性。在本技术中,由于固态电解质作为锂离子传输的通道,所以当固态电解质和石墨的接触性能差时,会降低石墨的容量发挥,引起首效的下降,所以可以通过首效的大小体现固态电解质与石墨接触性能的好坏。
[0195]
2、通过上述实施例1-5的测试数据可见,固态电解质的百分含量可以影响固态电池电化学性能,当固态电解质的含量为6.5~8.3%,固态电池的充放电首效在84.2~85.5%之间,100圈容量保持率在92.2~98.5%之间。申请
[0196]
3、通过上述实施例1和实施例6-11中不同石墨dv50数据考察可知,本技术实施例1、6-9与实施例10-11对比可知,复合材料中石墨的粒径dv50可为2~8μm,其制备得到固态电池的性能优于实施例10-11制备的,由此可知石墨粒径过大或过小导致接触不充分,从而
影响界面处的锂离子传输。
[0197]
4、通过实施例1-22与实施例22-23的测试数据可见,采用硫化物固态电解质制成的固态电池,相对于采用卤化物固态电解质和氧化物固态电解质制成的电池,具有更优的电化学性能,原因在于硫化物固态电解质的电导率大于卤化物固态电解质和氧化物固态电解质。