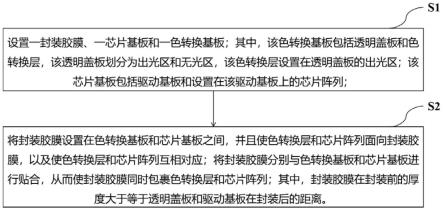
1.本发明涉及发光二极管的技术领域,特别是涉及一种显示模组的制备方法及一种显示模组。
背景技术:2.微型发光二极管(micro-led,μ-led)是指将微米级的发光二极管(led)芯片组装到驱动电路板上所形成的发光阵列,是一种主动发光的矩阵式显示技术,其具有亮度高、饱和度高、响应速度快、结构轻薄、寿命长等特性,在微显示产品、ar(增强现实)/vr(虚拟现实)、光通信、固态照明和军事航天等各领域都有着极其重要的应用。
3.目前,micro-led显示模组主要有两种实现方式:三色rgb法和色转换法。其中,三色rgb法需要巨量转移rgb三原色led芯片,存在着工艺难度大、制备成本高和红光芯片效率低等问题,难以满足市场需求;色转换法是以单色的micro-led芯片阵列为发光源、采用纳米荧光粉或量子点(quantum dots,qd)为色转换层的彩色转换技术,其具有与半导体工艺兼容的特性,可实现高分辨图形化,为显示模组的量产提供了另一种有效途径。
4.与发光效率不理想、光色质量较差的荧光材料相比,qd材料具有发光波长可调、显色性高、色纯度好、色域广等优异的发光性能,有利于提升显示模组的发光性能。请参阅图1,其为现有技术中一种micro-led显示模组的结构示意图,其包括色转换基板1、芯片基板2以及将色转换基板1和芯片基板2贴合在一起的框胶3;其中,色转换基板1包括第一基板以及设置在第一基板上的色转换层12,芯片基板2包括第二基板以及设置在第二基板上的芯片阵列22,色转换层12和芯片阵列22相向设置且互相对应;框胶3设置在色转换层12和芯片阵列22的四周,并通过自身的粘性使第一基板和第二基板贴合。然而,仅采用框胶3进行封装的结构,往往存在着气密性不够而被空气中的水分和氧气入侵,使得qd表面的有机配体发生化学反应而猝灭,导致显示模组的发光性能下降;同时,芯片阵列22在持续发光过程中会产生较多热量,容易造成qd表面的有机配体脱落,导致qd的表面缺陷增多,发光效率降低。综上,qd材料存在热稳定性差、抗水氧能力差的问题,严重制约了qd材料在micro-led领域的实际应用
技术实现要素:5.基于此,本发明的目的在于,提供一种显示模组的制备方法,其通过优化micro-led显示模组的封装结构来克服qd材料热稳定性差、抗水氧能力差的问题。
6.本发明的技术效果是如下技术方案实现的:
7.一种显示模组的制备方法,包括步骤:
8.s1:设置一封装胶膜、一芯片基板和一色转换基板;其中,所述色转换基板包括透明盖板和色转换层,所述透明盖板划分为出光区和无光区,所述色转换层设置在所述透明盖板的出光区;所述芯片基板包括驱动基板和设置在所述驱动基板上的芯片阵列;
9.s2:将所述封装胶膜设置在所述色转换基板和所述芯片基板之间,并且使所述色
转换层和所述芯片阵列面向所述封装胶膜,以及使所述色转换层和所述芯片阵列互相对应;将封装胶膜分别与所述色转换基板和所述芯片基板进行贴合,从而使所述封装胶膜包裹所述色转换层和所述芯片阵列;其中,所述封装胶膜在封装前的厚度大于等于所述透明盖板和所述驱动基板在封装后的厚度。
10.本发明所述的显示模组的制备方法,将封装胶膜分别与色转换基板和芯片基板进行对位贴合,不仅能够包裹住qdcc层,避免水氧对qd材料的侵袭,而且该封装胶膜能够将qdcc层和芯片阵列完全隔离,起到非常好的隔热降温效果。该制备方法具有工艺简单、可行性高、制备成本低的优点,有利于实现了对芯片阵列和色转换层的有效保护,并且提高了显示模组的发光性能和使用寿命。
11.进一步地,步骤s2具体为:
12.首先将所述封装胶膜与所述芯片基板进行贴合,使得所述封装胶膜包裹所述芯片阵列;然后使所述色转换基板带有色转换层的一侧面向封装后的芯片基板,并且使所述色转换层与所述芯片阵列互相对应;将所述色转换基板和封装后的芯片基板进行贴合,使得所述封装胶膜包裹所述色转换层。
13.进一步地,步骤s2具体为:
14.首先将所述封装胶膜与所述色转换基板进行贴合,使得所述封装胶膜包裹所述色转换层;然后使所述芯片基板带有芯片阵列的一侧面向封装后的色转换基板,并且使所述芯片阵列与所述色转换层互相对应;将所述芯片基板和封装后的色转换基板进行贴合,使得所述封装胶膜包裹所述芯片阵列。
15.进一步地,步骤s2具体为:
16.首先将所述封装胶膜设置在所述色转换基板和所述芯片基板之间,并且使所述色转换层和所述芯片阵列互相对应;然后同时将所述封装胶膜与所述色转换基板和所述芯片基板进行贴合,使得所述封装胶膜同时包裹所述色转换层和所述芯片阵列。
17.进一步地,所述封装胶膜的透光率大于90%、耐热温度大于100℃、水汽透过率小于10-2
g/(m2·
24h),并且上下表面均有粘性。
18.进一步地,在步骤s2之前还包括步骤:在所述封装胶膜的一表面形成一阻光墙;所述封装胶膜与所述芯片基板贴合后,所述阻光墙嵌入所述芯片阵列之间。
19.进一步地,在步骤s2之前还包括步骤:在所述透光盖板的无光区形成一挡光墙。
20.进一步地,在步骤s2之前还包括步骤:在所述挡光墙上形成一遮光墙。
21.进一步地,所述芯片阵列中的每一个芯片均包括由上至下层叠设置的缓冲层、n型传输层、发光层、p型传输层和电极层;所述阻光墙的高度大于等于所述芯片的发光层的厚度,并且小于等于所述芯片阵列的高度;所述封装胶膜与所述芯片基板贴合后,所述阻光墙的底面不高于所述芯片的发光层。
22.进一步地,所述阻光墙的侧面设有凸台,所述凸台的外缘直径大于相邻两个芯片的距离。
23.本发明还提供了一种显示模组,其包括层叠设置的色转换基板、封装胶膜和芯片基板;所述色转换基板包括透明盖板和色转换层,所述透明盖板划分为出光区和无光区,所述色转换层设置于所述透明盖板的出光区;所述芯片基板包括驱动基板和设置在所述驱动基板表面的芯片阵列,并且所述芯片阵列与所述色转换层互相对应;所述封装胶膜设置在
所述色转换层和所述芯片阵列之间,并且同时包裹所述色转换层和所述芯片阵列。
24.进一步地,所述封装胶膜的透光率大于等于90%、耐热温度大于等于100℃、水汽透过率小于10-2
g/(m2·
24h),并且上下表面均有粘性。
25.进一步地,还包括一阻光墙,所述阻光墙设置在所述封装胶膜面向所述芯片阵列的一侧并且嵌入所述芯片阵列之间;所述芯片阵列中的每一个芯片均包括由上至下层叠设置的缓冲层、n型传输层、发光层、p型传输层和电极层;所述阻光墙的高度大于等于所述芯片的发光层的厚度,并且小于等于所述芯片阵列的高度;所述阻光墙的底面不高于所述芯片的发光层;所述阻光墙的侧面设有凸台,所述凸台的外缘直径大于相邻两个芯片的距离。
26.进一步地,还包括一挡光墙,所述挡光墙设置在所述透光盖板的无光区。
27.进一步地,还包括一遮光墙,所述遮光墙设置在所述挡光墙与所述封装胶膜之间。
28.与现有技术相比,本发明提供的一种显示模组的制备方法和一种显示模组,将封装胶膜分别与色转换基板和芯片基板进行对位贴合,使封装胶膜同时包裹色转换层和芯片阵列,不仅能够有效阻挡水氧入侵对芯片阵列和色转换层的不良影响,而且能避免芯片阵列发光时散发的热量对色转换层产生不利影响;同时,该封装胶膜具有一定的柔性,可以在外力冲击时起到良好的缓冲作用,降低显示模组的机械损伤,延长其使用寿命。进一步地,本发明还设计了阻光墙、挡光墙和遮光墙的结构,既能防止芯片和色转换层的侧向串光,又能提高显示模组的发光亮度和对比度。该显示模组的制备方法具有工艺简单、可行性高、制备成本低的优点,有利于实现了对芯片阵列和色转换层的有效保护,并且提高了显示模组的发光性能和使用寿命。
29.为了更好地理解和实施,下面结合附图详细说明本发明。
附图说明
30.图1为背景技术中一种micro-led显示模组的结构示意图;
31.图2为本发明提供的一种显示模组的制备方法的步骤示意图;
32.图3为本发明实施例1提供的一种显示模组的制备方法的步骤示意图;
33.图4为本发明实施例1提供的一种显示模组的制备方法的流程示意图;
34.图5为本发明实施例1提供的一种显示模组的结构示意图;
35.图6为本发明实施例2提供的一种显示模组的制备方法的步骤示意图;
36.图7为本发明实施例2提供的一种显示模组的制备方法的流程示意图;
37.图8为本发明实施例3提供的一种显示模组的制备方法的步骤示意图;
38.图9为本发明实施例3提供的一种显示模组的制备方法的流程示意图;
39.图10为本发明实施例4提供的阻光墙的形成方法的流程示意图;
40.图11为本发明实施例4提供的一种显示模组的结构示意图。
41.附图标记:色转换基板1,透光盖板11,出光区11a,无光区11b,色转换层12,芯片基板2,驱动基板21,芯片阵列22,框胶3,封装胶膜4,阻光墙5,第一阻光墙51,第二阻光墙52,挡光墙6,遮光墙7,第一掩膜81,第二掩膜82。
具体实施方式
42.现有技术中,基于量子点色转换(quantum dots color conversion,qdcc)层的
micro-led显示模组在工作一段时间后,经常会出现发光亮度逐渐下降,甚至完全不发光的情况,其原因在于该显示模组的封装结构存在着气密性较低和隔热性较差的缺陷,无法阻隔水氧和高温对qd材料的影响,导致qd材料失效,显示模组发光性能降低。基于此,本发明对显示模组的封装结构进行优化,采用一种耐热性高、水氧阻隔能力强、透光性高、双面有粘性的封装胶膜作为封装材料,将该封装胶膜分别与色转换基板和芯片基板进行对位贴合,不仅能够包裹住qdcc层,避免水氧对qd材料的侵袭,而且该封装胶膜能够将qdcc层和芯片阵列完全隔离,起到非常好的隔热降温效果。请参阅图2,其为本发明提供的一种显示模组的制备方法的步骤示意图,该制备方法包括步骤:
43.s1:设置一封装胶膜4、一芯片基板2和一色转换基板1;其中,该色转换基板1包括透明盖板11和色转换层12,该透明盖板11划分为出光区11a和无光区11b,该色转换层12设置在透明盖板11的出光区;该芯片基板2包括驱动基板21和设置在该驱动基板21上的芯片阵列22;
44.s2:将封装胶膜4设置在色转换基板1和芯片基板2之间,并且使色转换层12和芯片阵列22面向封装胶膜4,以及使色转换层12和芯片阵列22互相对应;将封装胶膜4分别与色转换基板1和芯片基板2进行贴合,从而使封装胶膜4同时包裹色转换层12和芯片阵列22;其中,封装胶膜4在封装前的厚度大于等于透明盖板和驱动基板21在封装后的距离。
45.为使本发明的目的、技术方案和优点更加清楚,下面通过具体的实施例作进行说明。
46.实施例1
47.请参阅图3和图4,其中,图3为本实施例提供的一种显示模组的制备方法的步骤示意图,图4为本实施例提供的一种显示模组的制备方法的流程示意图。该显示模组的制备方法包括步骤:
48.s111:设置一封装胶膜4,在该封装胶膜4的一表面形成阻光墙5;
49.现有技术中,显示模组封装时常采用液态的环氧树脂封装胶、聚氨酯封装胶和有机硅树脂封装胶,并通过旋涂或喷墨打印等工艺覆盖在色转换层12的表面,然后通过加热烘烤或紫外线照射的方式进行固化,但这些方式制备的封装层可能存在厚度较薄、致密性较差、胶体容易产生气泡等问题,并且制备工艺较为繁琐,投入成本较高。因此,本实施例直接采用成型的封装胶膜4作为封装材料,避免液态胶水涂覆和固化过程中气密性、透光性难以控制的问题。
50.为了确保封装胶膜4能同时包裹芯片阵列22和色转换层12并实现更好的保护效果,封装胶膜4在封装前的厚度d1应大于等于封装后驱动基板21和透光盖板11之间的距离d3,并且封装胶膜4还需要满足下述条件:透光率大于等于90%、耐热温度大于等于100℃、水汽透过率小于10-2
g/(m2·
24h),并且上下表面均有粘性,其可以为oca(光学胶,optically clear adhesive)胶膜、eva(聚乙烯-聚醋酸乙烯酯,polyethylene vinylacetate)胶膜、poe(聚烯足弹性体,polyolefin elastomer)胶膜、pvb(聚乙烯醇缩丁醛,polyvinyl butyral)胶膜或tpu(热塑性聚氨酯橡胶,thermoplastic polyurethanes)胶膜等。其中,oca胶膜具有无色透明、光透过率高(一般为92~99%)、耐热温度大于130℃、胶结强度良好、可在室温或低温下固化、固化收缩小等优点,因此本实施例优选oca胶膜为封装胶膜4。
51.oca胶膜通常包括一亚克力胶体层以及贴合该亚克力胶体层上下表面的离型膜,使用时需要撕去离型膜,并将亚克力胶体层直接贴合在芯片基板2或色转换基板1的表面,然后在室温或25~40℃的低温条件下进行固化。需要注意的是,oca胶膜封装前的厚度指的是亚克力胶体层的厚度。
52.可选的,封装胶膜4混有增散射颗粒,如sio2或al2o3颗粒,可以通过增加芯片阵列22发出的光的散射,提升显示模组的发光性能。
53.为防止芯片侧向串光,本实施例在封装胶膜4的一表面形成阻光墙5,其形成方法具体为:通过光刻工艺在封装胶膜4的一表面形成掩膜,该掩膜在驱动基板21上的垂直投影大于等于芯片阵列22在驱动基板21上的垂直投影;在未被掩膜覆盖的封装胶膜4表面填充阻光墙5;除去掩膜。所述阻光墙5可以为反光墙或吸光墙,本实施例优选为能够提高芯片出光亮度的反光墙;具体地,可以通过蒸镀工艺在未被掩膜覆盖的封装胶膜4表面形成分布式布拉格反射镜(distributed bragg reflector,dbr)的结构,从而形成反光的阻光墙5;其中,分布式布拉格反射镜是由高折射率薄膜和低折射率薄膜堆叠而成,例如tio2/al2o3、tio2/sio2、ta2o5/al2o3、hfo2/sio2等。
54.阻光墙5的宽度小于等于相邻两个芯片的距离;在本实施例中,阻光墙5的宽度小于相邻两个芯片的距离,芯片阵列22与阻光墙5之间形成一定的间隙,使得封装胶膜4在被挤压发生形变时能够进入并填充该间隙,减少对芯片阵列22的挤压应力。
55.s112:设置一芯片基板2;其中,该芯片基板2包括驱动基板21和设置在驱动基板21上的芯片阵列22;将带有阻光墙5的封装胶膜4与该芯片基板2进行对位贴合,并且使该阻光墙5嵌入芯片阵列22中,从而使封装胶膜4包裹该芯片阵列22;
56.所述驱动基板21为表面设有驱动电路的基板,其可以为印刷电路板(printed circuit board,pcb)、硅基板、透明玻璃基板和柔性基板等。芯片阵列22中的每个芯片均包括由上至下层叠设置的缓冲层、n型传输层、发光层、p型传输层和电极层,并且通过预置锡膏技术、金属共晶键合技术或微管技术使电极层与驱动基板21键合。
57.通过对位设备使封装胶膜4带有阻光墙5的一侧面向芯片基板2带有芯片阵列22的一侧,并且使阻光墙5面向芯片阵列22之间的空位;将封装胶膜4贴覆在芯片基板2的表面,然后利用治具在封装胶膜4没有阻光墙5的一侧进行低温热压贴合或常温压合,使阻光墙5嵌入至芯片阵列22中,从而使封装胶膜4包裹住芯片阵列22,且封装胶膜4的边缘紧密贴合在芯片阵列22周围的驱动基板21上。随着治具和驱动基板21的不断挤压,封装胶膜逐渐扩张变薄,使得芯片基板1封装后,驱动基板21的上表面到封装胶膜4的顶面的距离d2小于封装胶膜在封装前的厚度d1。
58.为满足防止芯片侧向串光的功能,该阻光墙5的高度应大于等于芯片的发光层的厚度,并且阻光墙5的高度小于等于芯片阵列22的高度;阻光墙5嵌入芯片阵列22后,阻光墙5的底面不高于芯片发光层的下表面。在本实施例中,阻光墙5的高度低于芯片阵列22的高度且大于芯片的缓冲层、n型传输层和发光层的总高度,有利于在实现防串光效果的前提下,降低形成阻光墙5的工艺难度和制造成本。
59.s121:设置一色转换基板1;其中,该色转换基板1包括透光盖板11和色转换层12,该透光盖板11划分为出光区和无光区,该色转换层12设置在透光盖板11的出光区;在透明盖板的无光区上形成挡光墙6;
60.所述透光盖板11可以为透明的玻璃基板、陶瓷基板或聚合物基板,其可以划分为出光区11a和无光区11b,并且出光区11a与芯片基板2在驱动基板21上的垂直投影保持一致。所述色转换层12填充有红色qd油墨、绿色qd油墨、蓝色qd油墨和透明油墨中的至少一种;其中,红色qd油墨、绿色qd油墨和蓝色qd油墨有含有不同浓度的qd材料的uv光固树脂制成,透明油墨由透明的uv光固树脂制成;在实际应用中,可根据最终的显示需求在透光盖板11的出光区11a按预设的图案填充不同颜色的油墨。
61.为防止色转换层12的侧向串光,本实施例在透明盖板11的无光区11b形成挡光墙6,并且该挡光墙6的高度大于等于色转换层12的高度。挡光墙6的形成方法具体为:在透光盖板11的出光区11a形成色转换层12后,直接通过光刻、旋涂或喷墨打印工艺在透明盖板11的无光区11b形成挡光墙6;或者,先在透光盖板11的出光区11a形成一牺牲层,然后通过光刻、旋涂或喷墨打印工艺在透明盖板11的无光区11b形成挡光墙6,接着除去牺牲层,并在透光盖板11的出光区11a上形成色转换层12。所述挡光墙6可以为反光墙或吸光墙,本实施例优选为能够提高显示模组对比度的吸光墙,其由混有炭黑颗粒的光固树脂制成的黑色油墨制成。
62.s122:在挡光墙6上形成遮光墙7;
63.所述遮光墙7也可以为反光墙或吸光墙,本实施例优选为能够进一步提高芯片出光亮度的反光墙,并同样为采用蒸镀工艺在挡光墙6上形成dbr反射镜结构。其中,遮光墙7的高度小于等于色转换层12和芯片阵列22在封装后的距离,并且遮光墙7的宽度也小于等于相邻两个芯片的间隙,防止在压合过程中其对芯片阵列22造成挤压甚至机械损伤。由于阻光墙5的高度低于芯片阵列22的高度,本实施例的遮光墙7的高度应略小于色转换层12和芯片阵列22在封装后的距离,并将遮光墙7和阻光墙5在封装后的距离控制在1~2μm,这样可以尽可能减小封装后遮光墙7和阻光墙5之间的缝隙,提高防串光效果。
64.s130:使色转换基板1带有色转换层12的一侧面向封装后的芯片基板2,并且色转换层12与芯片阵列22互相对应;将色转换基板1与封装后的芯片基板2进行压合,从而使封装胶膜4同时包裹色转换层12、遮光墙7和挡光墙6。
65.将色转换基板1设置在封装后的芯片基板2上方,并且使色转换基板1带有色转换层12、挡光墙6和遮光墙7的一侧面向芯片基板2带有芯片阵列22并贴覆有封装胶膜4的一侧;然后通过对位设备调整色转换基板1和芯片基板2的相对位置,使得色转换层12与芯片阵列22互相对应、以及挡光墙6和遮光墙7与阻光墙5互相对应;利用治具在色转换基板1顶面进行下压,封装胶膜4进一步被挤压并扩张变薄,使得封装胶膜4同时包裹住色转换层12、遮光墙7和挡光墙6,并且封装胶膜4的边缘紧密贴合于驱动基板21和透明盖板11之间,最终形成具有良好气密性和隔热性的显示模组。此时,驱动基板21和透明盖板的距离d3不仅小于封装胶膜4在封装前的厚度d1,而且还小于步骤112中驱动基板11上表面到封装胶膜4顶面的距离d2,即有d3<d2<d1。
66.通过步骤s111~s130制备得到的显示模组的结构示意图如图5所示。
67.作为本实施例的一个补充,所述遮光墙7的形成并不一定要限制在步骤s121之后,其可以在步骤s130之前的任一阶段形成。例如,在步骤s112获得封装后的芯片基板2之后,在封装胶膜4表面与阻光墙5相对的位置形成遮光墙7;或者,在步骤s111中,在形成阻光墙5之前或之后,在封装胶膜4的一表面形成遮光墙7。此外,步骤s111~s112和步骤s121~s122
在步骤s130之前分别执行,并没有严格的先后顺序之分。
68.实施例2
69.本实施例与实施例1的主要区别在于先将封装胶膜4与色转换基板1对位贴合,然后将封装后的色转换基板1与芯片基板2进行对位贴合。
70.请参阅图6和图7,其中,图6为本实施例提供的一种显示模组的制备方法的步骤示意图,图7为本实施例提供的一种显示模组的制备方法的流程示意图。该显示模组的制备方法包括步骤:
71.s210:设置一封装胶膜4,在该封装胶膜4的一表面形成阻光墙5;
72.s221:设置一色转换基板1;其中,该色转换基板1包括透光盖板11和色转换层12,该透光盖板11划分为出光区11a和无光区11b,该色转换层12设置在该透光盖板11的出光区11a;在透光盖板11的无光区形成挡光墙6;
73.s222:在挡光墙6上形成遮光墙7;
74.其中,步骤s210和步骤s221~s222在步骤s230前分别执行;
75.s230:使封装胶膜4没有阻光墙5的一侧面向该色转换基板1带有色转换层12的一侧,并且使阻光墙5与遮光墙7和挡光墙6互相对应;将封装胶膜4与色转换基板1进行压合,使得封装胶膜4同时包裹色转换层12、遮光墙7和挡光墙6;
76.s240:设置一芯片基板2,其中,该芯片基板2包括驱动基板21和设置在驱动基板21上的芯片阵列22;使芯片基板2带有芯片阵列22的一侧面向封装后的色转换基板1,然后将芯片基板2与封装后的色转换基板1进行压合,使得封装胶膜4表面的阻光墙5嵌入芯片阵列22中,从而使封装胶膜4包裹芯片阵列22。
77.与实施例1不同的是,本实施例的阻光墙5的高度等于芯片阵列22的高度,有利于避免阻光墙5在芯片阵列22之间过度嵌入而无法实现防串光的功能;此时,遮光墙7的高度可以小于色转换层17并且嵌入芯片阵列22,并使得遮光墙7和阻光墙5在封装后的距离为1~2μm。
78.作为本实施例的一个补充,所述遮光墙7的形成并不一定要限制在步骤s221之后,其可以在步骤s230之前的任一阶段形成。
79.实施例3
80.本实施例与实施例1~2的区别在于将封装胶膜4同时与色转换基板1和芯片基板2进行对位贴合。
81.请参阅图8和图9,其中,图8为本实施例提供的一种显示模组的制备方法的步骤示意图,图9为本实施例提供的一种显示模组的制备方法的流程示意图。该显示模组的制备方法包括步骤:
82.s310:设置一封装胶膜4,在该封装胶膜4的一表面形成阻光墙5;
83.s321:设置一色转换基板1;其中,该色转换基板1包括透光盖板11和色转换层12,该透光盖板11划分为出光区11a和无光区11b,该色转换层12设置在该透光盖板11的出光区11a;在透光盖板11的无光区11b形成挡光墙6;
84.s322:在挡光墙6上形成遮光墙7;
85.其中,步骤s310和步骤s321~s322在步骤s330前分别执行,并且所述遮光墙7的形成可以在步骤s330之前的任一阶段形成。
86.s330:设置一芯片基板2,其中,该芯片基板2包括驱动基板21和设置在驱动基板21上的芯片阵列22;将封装胶膜4设置在色转换基板1和芯片基板2之间,并且使色转换层12和芯片阵列22面向封装胶膜4,以及使色转换层12和芯片阵列22互相对应;将色转换基板1、封装胶膜4和芯片基板2同时进行压合,使得封装胶膜4同时包裹色转换层12、遮光墙7、挡光墙6和芯片阵列22。
87.实施例4
88.在实施例1~3中,阻光墙5的高度只需要大于芯片的发光层、n型传输层和缓冲层的总厚度,但是在色转换基板1和芯片基板2通过封装胶膜4贴合在一起的过程中,由于遮光墙7和色转换层12的挤压,封装胶膜4逐渐扩张变薄,容易陷进芯片阵列22之间的空位中,导致阻光墙5过度嵌入而无法阻挡芯片的侧向发光。为了克服这个问题,可以将阻光墙5的高度设置为大于等于芯片的高度,但过高的阻光墙5会造成工艺复杂繁琐、,投入成本过高,在实际生产过程中往往难以实现。为此,本实施例设计了一个侧面设有凸台的阻光墙5,其凸台的外缘直径大于相邻两个芯片的距离,能够在下压时卡住芯片的顶面,防止阻光墙的过度嵌入。
89.请参阅图10和图11,其中,图10为本实施例提供的阻光墙的形成方法的流程示意图,图11为本实施例提供的一种显示模组的结构示意图。该阻光墙5的形成方法具体为:通过光刻工艺在封装胶膜4的一表面形成第一掩膜81,该第一掩膜81在驱动基板21上的垂直投影小于芯片阵列22在驱动基板21上的垂直投影;在未被第一掩膜81覆盖的封装胶膜4表面填充第一阻光墙51;通过光刻工艺在第一掩膜81上形成第二掩膜82,该第二掩膜82在驱动基板21上的垂直投影大于等于芯片阵列22在驱动基板21上的垂直投影;在未第二掩膜82覆盖的第一阻光墙51表面填充第二阻光墙52;除去第一掩膜81和第二掩膜82,第一阻光墙51和第二阻光墙52结合形成一侧面设有凸台的阻光墙5。
90.在一个具体的应用场景中,封装前选用的封装胶膜4为oca胶膜,其厚度为25~30μm,并且长度、宽度均比色转换层12和芯片阵列22所在区域多20~50μm。色转换层12的厚度为3~4μm,芯片阵列22的高度为5~7μm;挡光墙6的高度也为3~4μm,即与色转换层12的厚度保持一致;遮光墙7的高度也为6~7μm。侧面设有凸台的阻光墙5的总高度为6~10μm,其中,第一阻光墙51的高度为2~3μm,第二阻光墙52的高度为4~7μm;在其他应用场景中,也可以选用侧面没有凸台的阻光墙5,则阻光墙5的高度为4~7μm。封装后,透光盖板11和驱动基板21的距离为19~25μm,阻光墙5和遮光墙7的距离为1~2μm,色转换层12和芯片阵列22的距离为8~10μm。根据显示模组的不同尺寸控制oca胶膜的厚度、长度和宽度,既能保证对位贴合后色转换层12和芯片阵列22之间预留一定的间距,又能保证oca胶膜的边缘和透明盖板11、驱动基板均紧密贴合,而其本身良好的粘接强度、阻水氧性能和耐热性能对显示模组起到良好的密封保护作用,不需要设置额外的阻水氧层、粘接层或保护层,并且其室温或低温固化的特性也不会对色转换层11和芯片阵列22造成不良影响,具有结构简单、易于实现、成本较低的优点。
91.与现有技术相比,本发明提供的一种显示模组的制备方法和一种显示模组,将封装胶膜4分别与色转换基板1和芯片基板2进行对位贴合,使封装胶膜同时包裹色转换层和芯片阵列,不仅能够有效阻挡水氧入侵对芯片阵列和色转换层的不良影响,而且能避免芯片阵列发光时散发的热量对色转换层产生不利影响;同时,该封装胶膜具有一定的柔性,可
以在外力冲击时起到良好的缓冲作用,降低显示模组的机械损伤,延长其使用寿命。进一步地,本发明还设计了阻光墙、挡光墙和遮光墙的结构,既能防止芯片和色转换层的侧向串光,又能提高显示模组的发光亮度和对比度。该显示模组的制备方法具有工艺简单、可行性高、制备成本低的优点,有利于实现了对芯片阵列和色转换层的有效保护,并且提高了显示模组的发光性能和使用寿命。
92.以上所述实施例仅表达了本发明的几种实施方式,其描述较为具体和详细,但并不能因此而理解为对发明专利范围的限制。应当指出的是,对于本领域的普通技术人员来说,在不脱离本发明构思的前提下,还可以做出若干变形和改进,这些都属于本发明的保护范围。