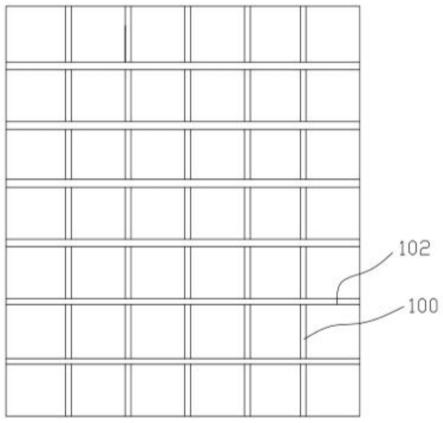
1.本发明属于光伏板组件技术领域,特别是涉及石墨烯导热光伏板组件制备方法及石墨烯导热光伏板组件。
背景技术:2.双玻光伏组件主要包括中部的光伏电池片,上层玻璃、下层玻璃,上层玻璃与下层玻璃直接设置有封装材料,通过封装材料将光伏电池片固定在上层玻璃以及下层玻璃之间;钢化玻璃材质作为顶层材料具有成本低、坚固、稳定、高透明度、防水和气体等特点得到广泛的应用,但是钢化玻璃透光率低,一般在初始透光率在90%左右,使用一段时间后有灰尘遮挡透光率会大幅下降,同时是热的不良导体,热阻系数大,夏天气温较高时,组件温度可达到七八十摄氏度,降低光伏组件的发电效率;以上问题使光伏组件发电效率严重下降,且很难清洁;石墨烯是一种高导热材料,目前,将石墨烯与光伏组件散热结合的问题研究有很多,但是仅仅是在光伏组件的玻璃上涂覆或者沉积一层石墨烯。
3.cn104916711b公开了将将普通玻璃浸没在石墨烯分散液中30-60秒钟后,把玻璃捞出并风干,然后将玻璃放入钢化炉进行加热,再将玻璃进行快速冷却室温,用干燥的冷空气迅速吹扫玻璃的两面,分为急冷时段和冷却时段,最后冷却至室温,制作出石墨烯钢化玻璃,通过这种技术工艺将石墨烯涂层附着在玻璃上,制得的产品虽然能增加漫射,减少反射效果,增加透光玻璃的透光量,且石墨烯膜层具有高亲水性,使光伏玻璃具自清洁功能,同时石墨烯可以降低热阻和光触媒效应,一定程度上提高光伏组件发电效率;但是存在下述缺陷:首先,通过浸渍的方法让石墨烯分散液附着在玻璃上,由于石墨烯与玻璃表面仅仅通过范德华力结合,光伏组件在运输过程中难免会相互摩擦,因此薄膜很容易被摩擦脱落,造成薄膜缺陷;另外,由于玻璃是不良导体,因此,即使在玻璃的上下表面上均附着石墨烯层,而两石墨烯层之间存在玻璃层,导致热量无法顺畅的由玻璃内表面散发至玻璃外表面,热量集聚,即纵向散热效率不高,继而导致光伏电池片热量无法即使散出,散热效率提高不够显著;
技术实现要素:4.本发明的目的在于提供石墨烯导热光伏板组件制备方法及石墨烯导热光伏板组件,以解决上述背景技术中提出的问题。
5.为解决此技术问题,本发明的技术方案是:
6.石墨烯导热光伏板组件制备方法,包括如下步骤:
7.s1:在前板玻璃及背板玻璃上对应光伏电池片的区域利用激光扫描进行穿透打孔形成第一导热微孔;
8.s2:在背板玻璃上成形后三维导热石墨烯网膜;
9.s3:取封装胶膜,在封装胶膜的上下表面喷涂石墨烯分散液并风干;
10.s4:在封装胶膜上印刷网格状的石墨烯铝浆图案;石墨烯铝浆图案中形成用于放
置光伏电池片的放置区域;
11.s5:取一印刷有石墨烯铝浆图案的封装胶膜,将若干组焊接好的光伏电池片依次规则排列放置在该封装胶膜的放置区域上;
12.s6:取一步骤s2中未印刷石墨烯铝浆图案的封装胶膜,将其覆盖在步骤s4的光伏电池片上,再将组件放置在背板玻璃上,并在其上方放置前板玻璃,然后抽真空热压,使上层封装胶膜和下层封装胶膜固化,得到光伏组件;
13.s7:激光打孔;沿各光伏电池片间的间隙,通过激光依次穿透前板玻璃、上层封装胶膜、石墨烯铝浆图案、下层封装胶膜以及背板玻璃,形成第二导热微孔;
14.s8:在第二导热微孔以及前板玻璃的第一导热微孔,分多次刮涂碳纤维束-石墨烯/光固化透明树脂填料,且在每次刮涂后采用磁性排列装置对前板玻璃的第一导热微孔以及第二导热微孔内的磁性石墨烯包裹碳纤维束填料进行定向排列后固化,当前板玻璃的第一导热微孔以及第二导热微孔内碳纤维束-石墨烯/光固化透明树脂填料与对应孔顶面在同一平面上时;在前板玻璃上喷涂石墨烯分散液,风干后固化,石墨烯分散液与碳纤维束-石墨烯/光固化透明树脂填料交联形成均匀的前三维导热石墨烯膜网膜。
15.优选的,步骤s1中对前板玻璃及背板玻璃进行第一导热微孔打孔的方法包括如下子步骤:
16.s11:在前板玻璃及背板玻璃上绘制纵向间隔线,纵向间隔线的宽度略大于两相邻光伏电池片之间的横向间距;
17.两相邻纵向间隔线之间的距离略大于光伏电池片的宽度;
18.s12:在前板玻璃及背板玻璃上绘制横向间隔线,横向间隔线的宽度略大于两相邻光伏电池片之间的纵向间距;
19.两相邻横向间隔线之间的距离略大于光伏电池片的高度;
20.s13:通过激光打孔机在由纵向间隔线与横向间隔线围成的网格区域内进行打孔。
21.优选的,步骤s2中在背板玻璃上成形后三维导热石墨烯网膜的方法,包括如下步骤:
22.s21:配制碳纤维束-石墨烯/光固化透明树脂填料;
23.s22:在背板玻璃上分多次刮涂步骤s21中制得碳纤维束-石墨烯/光固化透明树脂填料,并采用磁吸排列装置对进行定向排列,固化形成纵向导热层;
24.s23:在纵向导热层顶部填料固化前,在背板玻璃的表面喷涂石墨烯分散液风干并固化后,背板玻璃表面石墨烯层与纵向导热层交联形成后三维导热石墨烯网膜。
25.优选的,配制碳纤维束-石墨烯/光固化透明树脂填料的方法包括如下子步骤:
26.s211:碳纤维的磁负载;
27.s212:制得石墨烯分散液:将hummers方法制备的氧化石墨烯加入dmf,超声分散剥离,得分散均匀的氧化石墨烯/dmf溶液,在溶液中加入肼进行还原,得到石墨烯/dmf溶液;
28.s213:将石墨烯/dmf通过油浴加热,加入磁负载的碳纤维束,超声波震荡12-24h得到碳纤维束-石墨烯悬浮液;
29.s214:按照透明低聚物与溶剂的质量比例为1:1,将透明低聚物溶解于溶剂中,用频率为35-45khz的超声波清洗仪进行超声处理24h;
30.s215:将步骤s213制得的碳纤维束-石墨烯悬浮液与步骤s214制得的透明低聚物/
溶剂混合物相互混合,用频率为35-45khz的超声波清洗仪超声15-36h;
31.s216:将步骤s215中制备的混合溶液在20-40℃下磁力搅拌,并加入光引发剂/溶剂溶液,所述光引发剂与光固化树脂的质量比为0.01-0.1,一直搅拌到溶剂全部挥发完,得到碳纤维束-石墨烯/光固化透明树脂填料;
32.步骤s211中,碳纤维的磁负载采用三氯化铁溶液和氯化亚铁溶液进行碳纤维的磁负载此为现有技术,在此不再赘述。
33.优选的,包括输送平台,所述输送平台包括两侧的输送链条,两侧所述输送链条上设置有玻璃夹持装置,所述玻璃夹持装置包括玻璃放置平台,玻璃放置平台两侧部上方设置有阻挡部,所述阻挡部与玻璃放置平台两侧部之间形成夹持腔,沿玻璃输送方向依次设置刮涂装置、磁性排列装置以及固化箱,磁吸排列装置包括设置在玻璃放置平台的上下方向上的上磁吸排列装置,及下磁吸排列装置,所述上磁吸排列装置与下磁吸排列装置可远离或靠近所述玻璃放置平台,所述上磁吸排列装置包括设置在输送平台上方的安装顶架,所述安装顶架上固定有第一气缸,所述第一气缸的活塞杆上设置有第一电磁体,所述下磁吸排列装置包括设置在所述输送平台的下方的安装底架,所述安装底架上固定有第二气缸,所述第二气缸的活塞杆上设置有第二电磁体。所述刮涂装置包括通过滑块连接在安装顶架上的第三气缸,所述第三气缸的活塞杆上固定有刮板,还包括固定在安装顶架上的第四气缸,第四气缸活塞杆与第三气缸固定连接,通过所述第四气缸推动所述第三气缸沿所述安装顶杆横向运动。
34.优选的,步骤s22中,在背板玻璃上分多次刮涂步骤s21中制得碳纤维束-石墨烯/光固化透明树脂填料,并采用磁吸排列装置对进行定向排列,固化形成纵向导热层的方法包括如下步骤:
35.s221:将背板玻璃放置在玻璃放置平台上,并通过玻璃夹持装置夹持固定;
36.s222:通过刮涂装置对背板玻璃进行刮涂步骤s21中制得碳纤维束-石墨烯/光固化透明树脂填料,将刮涂后的微孔玻璃骨架静置10-15s,静置后,第一导热微孔内的填料高度低于背板玻璃第一导热微孔高度;并输送至磁性排列装置内,此时,第一磁体与第二磁体均向靠近直至第一磁体贴合在微孔玻璃骨架的顶面上,第二磁体贴合在玻璃放置平台的底面上,对背板玻璃孔隙内的石墨烯包裹碳纤维束进行磁吸排列,磁吸排列时间为4s-15s;
37.s223:将完成步骤s222的背板玻璃输送至固化箱中进行固化;
38.s224:重复步骤s221-步骤s222动作继续在第一定向导热层上叠加成形若干第二定向导热层,其中第二定向导热层的高度与第一定向导热层的高度之和低于背板玻璃第一导热微孔的高度;
39.s224:在背板玻璃上刮涂碳纤维素-石墨烯光固化填料至与背板玻璃第一导热微孔的顶面在同一平面上,将背板重新输送至磁性排列装置内,此时,第一磁体与第二磁体均向背板玻璃靠近直至第一磁体与背板玻璃顶面的距离为1-15nm,第二磁体贴合在玻璃放置平台的底面上,对背板玻璃孔隙内的石墨烯包裹碳纤维束进行磁吸排列,磁吸排列时间为4s-10s;完成填料的定向排列。
40.本发明采用多次涂覆的方法,使得单次涂覆后,背板玻璃内被石墨烯包裹的碳纤维素由于数量小,不易发生聚集,继而容易被定型排列,另外,经过固化后形成基体再次进行涂覆,使得石墨烯包裹碳纤维束涂料在固化后基体的上方进行定向排列,从而使得被石
墨烯包裹的碳纤维素达到纵向的延伸,如此,可提高其在背板玻璃孔隙内的连续。
41.优选的,封装胶膜为eva封装胶膜。
42.优选的,网格状的石墨烯铝浆印刷图案包括横向印刷线,横向印刷线的宽度略大于两相邻光伏电池片之间的纵向间距;两相邻横向印刷线之间的距离略大于光伏电池片的高度;还包括纵向印刷线,纵向印刷线与横向印刷线呈十字排列形成若干用于放置光伏电池片的放置区域,纵向印刷线的宽度略大于两相邻光伏电池片之间的横向间距;两相邻纵向印刷线之间的距离略大于光伏电池片的宽度。
43.优选的,石墨烯铝浆图案线条的高度与光伏电池片的高度相同。
44.优选的,石墨烯铝浆采用如下方法制备,包括如下步骤:
45.s41:将石墨烯粉体和球磨介质机械分散后置于球磨机中球磨,再经过滤、洗涤、干燥,制得石墨烯粉体;
46.s42:浆料组分混合,将有机载体置于高速分散机中,搅拌的同时将石墨烯粉体分散于有机载体中,分批加入铝粉,搅拌均匀,得混合浆料;
47.s43:研磨混合浆料,调节浆料粘度后制得成品。
48.本发明还提供一种技术方案,墨烯导热光伏板组件,包括若干组焊接好的光伏电池片,各电池片之间形成有石墨烯铝浆层,所述电池片及石墨烯铝浆层的上下方向上设置有封装胶膜层,所述封装胶膜层的外表面上喷涂形成有石墨烯层形成芯体,还包括前板玻璃以及背板玻璃,所述前板玻璃以及背板玻璃分别复合在芯体的上下表面上;所述前板玻璃以及背板玻璃内形成有若干第一纵向导热层,相邻光伏电池片之间形成有第二纵向导热层,所述第二纵向导热层贯穿前板玻璃、上层封装胶膜、石墨烯铝浆图案、下层封装胶膜以及背板玻璃。
49.上述技术方案,本发明的有益效果是:
50.本发明对背板玻璃、前板玻璃第一导热微孔以及第二导热微孔孔隙内导热填料进行定向排列,使得孔隙内由底部至顶部形成连续的导热路线,并在背板玻璃、前板玻璃上形成石墨烯薄膜且与纵向导热路线交联形成三维导热网络,一方面提高表面石墨烯薄膜的结合力;另外产品导热系数能够提高50%以上;且多次固化磁吸排列方式使得导热填料相比于现有的定向排列技术其更稳定,更均匀;另外在封装胶膜上印刷网格状的石墨烯铝浆图案,光伏电池片的热量通过石墨烯铝浆图案传导至第二导热微孔,并在封装胶膜上形成石墨烯层,使得内部热量更容易被导出,导热系数进一步提高。
附图说明
51.图1是本发明中前板玻璃的结构示意图;
52.图2是本发明中石墨烯导热光伏板组件局部结构示意图;
53.图3是本发明中磁吸设备结构示意图;
54.图4是本发明中玻璃夹持装置的结构示意图;
55.图5是本发明中实施例1的光伏组件玻璃在橡皮擦拭实验前后的拉曼光谱图;
56.图6是本发明中对比例2的光伏组件玻璃在橡皮擦拭实验前后的拉曼光谱图。
具体实施方式
57.如图1-6所示,为了进一步解释本发明的技术方案,下面通过具体实施例来对本发明进行详细阐述。
58.实施例1
59.石墨烯导热光伏板组件制备方法,包括如下步骤:
60.s1:在前板玻璃及背板玻璃上对应光伏电池片的区域利用激光扫描进行穿透打孔形成第一导热微孔;本实施例此环节中包括如下子步骤:s11:在前板玻璃及背板玻璃上绘制纵向间隔线100,纵向间隔线的宽度略大于两相邻光伏电池片之间的横向间距,本实施列中,纵向间隔线的宽度为1.5cm;两相邻纵向间隔线之间的距离略大于光伏电池片的宽度,本实施列中,两相邻纵向间隔线之间的距离为18.5cm;s12:在前板玻璃及背板玻璃上绘制横向间隔线101,横向间隔线的宽度略大于两相邻光伏电池片之间的纵向间距,本实施列中,横向间隔线的宽度为1.5cm;两相邻横向间隔线之间的距离略大于光伏电池片的高度,本实施列中,两相邻横向间隔线之间的距离为18.5cm;s13:通过激光打孔机在由纵向间隔线与横向间隔线围成的网格区域内进行打孔,各个孔按照横向及纵向阵列排列,孔间距为3cm,孔径为2mm。
61.s2:在背板玻璃上成形后三维导热石墨烯网膜;包括如下步骤:
62.s21:配制碳纤维束-石墨烯/光固化透明树脂填料;其包括以下子步骤:s211:碳纤维的磁负载,碳纤维的磁负载采用三氯化铁溶液和氯化亚铁溶液进行碳纤维的磁负载此为现有技术,在此不再赘述;s212:制得石墨烯分散液:将hummers方法制备的氧化石墨烯加入dmf,超声分散剥离,得分散均匀的氧化石墨烯/dmf溶液,氧化石墨烯/dmf溶液的质量比例为1:25,在溶液中加入肼进行还原,肼与氧化石墨烯的质量比列为1:1.5,得到石墨烯/dmf溶液;s213:将石墨烯/dmf通过油浴加热,加入磁负载的碳纤维束,碳纤维束与石墨烯的质量比为1:5;超声波震荡12-24h得到碳纤维束-石墨烯悬浮液;s214:按照高透明环氧树脂与四氢呋喃溶液的质量比例为1:1,将高透明环氧树脂溶解于四氢呋喃溶液中,用频率为35-45khz的超声波清洗仪进行超声处理24h;s215:将步骤s213制得的碳纤维束-石墨烯悬浮液与步骤s214制得的高透明环氧树脂/四氢呋喃溶液混合物相互混合,用频率为35-45khz的超声波清洗仪超声15-36h;s216:将步骤s215中制备的混合溶液在20-40℃下磁力搅拌,并加入光引发剂/溶剂溶液,所述光引发剂与光固化树脂的质量比为0.01-0.1,一直搅拌到溶剂全部挥发完,得到碳纤维束-石墨烯/光固化透明树脂填料。
63.s22:在背板玻璃上分三次刮涂步骤s21中制得碳纤维束-石墨烯/光固化透明树脂填料,并采用磁吸排列装置对进行定向排列,固化形成纵向导热层;
64.具体的,涉及的设备包括输送平台200,所述输送平台包括两侧的输送链条201,两侧所述输送链条上设置有玻璃夹持装置,所述玻璃夹持装置包括玻璃放置平台202,玻璃放置平台两侧部上方设置有阻挡部203,所述阻挡部与玻璃放置平台两侧部之间形成夹持腔204,沿玻璃输送方向依次设置刮涂装置205、磁性排列装置206以及固化箱207,磁吸排列装置包括设置在玻璃放置平台的上下方向上的上磁吸排列装置,及下磁吸排列装置,所述上磁吸排列装置与下磁吸排列装置可远离或靠近所述玻璃放置平台,所述上磁吸排列装置包括设置在输送平台上方的安装顶架210,所述安装顶架上固定有第一气缸211,所述第一气缸的活塞杆上设置有第一电磁体212,所述下磁吸排列装置包括设置在所述输送平台的下
方的安装底架213,所述安装底架上固定有第二气缸214,所述第二气缸的活塞杆上设置有第二电磁体215。所述刮涂装置包括通过滑块连接在安装顶架上的第三气缸216,所述第三气缸的活塞杆上固定有刮板217,还包括固定在安装顶架上的第四气缸218,第四气缸活塞杆与第三气缸固定连接,通过所述第四气缸推动所述第三气缸沿所述安装顶杆横向运动。
65.且本实施例形成纵向导热层的方法包括如下步骤:s221:将背板玻璃放置在玻璃放置平台上,并通过玻璃夹持装置夹持固定;s222:通过刮涂装置对背板玻璃进行刮涂步骤s21中制得碳纤维束-石墨烯/光固化透明树脂填料,将刮涂后的微孔玻璃骨架静置10-15s,静置后,第一导热微孔内的填料高度为背板玻璃第一导热微孔高度的三分之一;并输送至磁性排列装置内,此时,第一磁体与第二磁体均向靠近直至第一磁体贴合在微孔玻璃骨架的顶面上,第二磁体贴合在玻璃放置平台的底面上,对背板玻璃孔隙内的石墨烯包裹碳纤维束进行磁吸排列,磁吸排列时间为4s-15s;s223:将完成步骤s222的背板玻璃输送至固化箱中进行固化;s224:重复步骤s221-步骤s222动作继续在第一定向导热层上叠加成形一第二定向导热层,其中第二定向导热层的高度与第一定向导热层的高度之和为背板玻璃第一导热微孔的高度的三分之二;s224:在背板玻璃上刮涂碳纤维素-石墨烯光固化填料至与背板玻璃第一导热微孔的顶面在同一平面上,将背板重新输送至磁性排列装置内,此时,第一磁体与第二磁体均向背板玻璃靠近直至第一磁体与背板玻璃顶面的距离为1-15nm,第二磁体贴合在玻璃放置平台的底面上,对背板玻璃孔隙内的石墨烯包裹碳纤维束进行磁吸排列,磁吸排列时间为4s-10s;完成填料的定向排列。
66.s23:在纵向导热层顶部填料固化前,在背板玻璃的表面喷涂石墨烯分散液风干并固化后,背板玻璃表面石墨烯层与纵向导热层交联形成后三维导热石墨烯网膜。
67.s3:取封装胶膜,封装胶膜为eva封装胶膜,在封装胶膜的上下表面喷涂石墨烯分散液并风干;石墨烯分散液采用s212制得的石墨烯/dmf溶液;
68.s4:在封装胶膜上印刷网格状的石墨烯铝浆图案;网格状的石墨烯铝浆印刷图案包括横向印刷线,横向印刷线的宽度略大于两相邻光伏电池片之间的纵向间距;两相邻横向印刷线之间的距离略大于光伏电池片的高度;还包括纵向印刷线,纵向印刷线与横向印刷线呈十字排列形成若干用于放置光伏电池片的放置区域,纵向印刷线的宽度略大于两相邻光伏电池片之间的横向间距;两相邻纵向印刷线之间的距离略大于光伏电池片的宽度,石墨烯铝浆图案线条的高度与光伏电池片的高度相同,石墨烯铝浆采用如下方法制备,包括如下步骤:s41:将石墨烯粉体和球磨介质机械分散后置于球磨机中球磨,再经过滤、洗涤、干燥,制得石墨烯粉体;s42:浆料组分混合,将有机载体置于高速分散机中,搅拌的同时将石墨烯粉体分散于有机载体中,分批加入铝粉,搅拌均匀,得混合浆料;s43:研磨混合浆料,调节浆料粘度后制得成品。
69.s5:取一印刷有石墨烯铝浆图案的封装胶膜,将若干组焊接好的光伏电池片依次规则排列放置在该封装胶膜的放置区域上;
70.s6:取一步骤s2中未印刷石墨烯铝浆图案的封装胶膜,将其覆盖在光伏电池片上,再将组件放置在背板玻璃上,并在其上方放置前板玻璃,然后抽真空热压,使上层封装胶膜和下层封装胶膜固化,得到光伏组件;
71.s7:激光打孔;沿各光伏电池片间的间隙,通过激光依次穿透前板玻璃、上层封装胶膜、石墨烯铝浆图案、下层封装胶膜以及背板玻璃,形成第二导热微孔;
72.s8:在第二导热微孔以及前板玻璃的第一导热微孔,分三次刮涂碳纤维束-石墨烯/光固化透明树脂填料,且在每次刮涂后采用磁性排列装置对前板玻璃的第一导热微孔以及第二导热微孔内的磁性石墨烯包裹碳纤维束填料进行定向排列后固化,当前板玻璃的第一导热微孔以及第二导热微孔内碳纤维束-石墨烯/光固化透明树脂填料与对应孔顶面在同一平面上时;在前板玻璃上喷涂石墨烯分散液,风干后固化,石墨烯分散液与碳纤维束-石墨烯/光固化透明树脂填料交联形成均匀的前三维导热石墨烯膜网膜,本实施例中具体的方法与背板玻璃的后三维导热石墨烯膜网膜相同,在此不再赘述。
73.实施例2
74.与实施例1的区别在于:步骤s1中各个孔按照横向及纵向阵列排列,孔间距为3cm,孔径为4mm;
75.实施例3
76.与实施例1的区别在于:步骤s1中各个孔按照横向及纵向阵列排列,孔间距为3cm,孔径为6mm;
77.实施例4
78.与实施例1的区别在于:步骤s1中各个孔按照横向及纵向阵列排列,孔间距为3cm,孔径为8mm;
79.实施例5
80.与实施例3的区别在于:步骤s1中各个孔按照横向及纵向阵列排列,孔间距为2cm,孔径为6mm;
81.实施例6
82.与实施例3的区别在于:步骤s1中各个孔按照横向及纵向阵列排列,孔间距为4cm,孔径为6mm;
83.实施例7
84.与实施例3的区别在于:步骤s3中的封装胶膜为eva封装胶膜,未在封装胶膜的上下表面喷涂石墨烯分散液;
85.对比例1
86.本实施例中其余步骤与实施例3相同,区别在于:在背板玻璃及前板玻璃内部形成纵向导热通道时,采用一次刮涂完成并固化一次成型导热通道。
87.对比例2
88.本实施例中其余步骤与实施例3相同,区别在于:同时只在背板玻璃以及前板玻璃的表面采用喷涂的方式形成石墨烯薄膜,而在背板玻璃及前板玻璃内部未形成纵向导热通道。
89.对比例3
90.本实施例中采用普通的eva封装胶膜作为粘结层,未在其表面喷涂石墨烯分散液形成石墨烯薄膜;以及未在封装胶膜上印刷网格状的石墨烯铝浆图案;同时只在背板玻璃以及前板玻璃的表面采用喷涂的方式形成石墨烯薄膜,而在背板玻璃及前板玻璃内部未形成纵向导热通道。
91.实验结果:沿石墨烯包裹碳纤维束长度排列方向对实施例1-7,以及对比例1-2产品测试热导率;热导率使用c-therm tci仪器采用astm d7984标准测试高导热石墨烯散热
材料的导热系数。
92.测试结果如表1所示。
93.表1
94.组别导热系数(w/mk)实施例1723实施例2745实施例3845实施例4923实施例51033实施例6738实施例7665对比例1616对比例2477对比例3416
95.透光率测定:
96.表2
97.组别可见光透光率,%实施例387实施例565实施例693
98.由表1可知,通过对背板玻璃孔隙内石墨烯包裹碳纤维束进行定向排列,使得石墨烯包裹碳纤维束在背板玻璃孔隙内由底部至顶部形成连续的导热路线,其导热系数能够提高50%以上;大程度提升了光伏组件的导热性能;
99.对比实施例1-实施例4,可知,随着背板玻璃,前板玻璃孔径的增大,光伏组件的导热系数先增大后趋于平缓,证明玻璃孔隙孔径为6mm时,碳纤维束-石墨烯/光固化透明树脂填料更易于流平于孔隙内,石墨烯包裹碳纤维束分散性更佳,易提高整体产品的排列效果;
100.对比实施例3及实施例5,6,可知,孔间距越小,产物导热系数越高,然而由表2可知其透光率将有所降低;由此,孔间距最佳为3cm。
101.对比实施例1与对比例1,可知,多次固化磁吸排列方式使得石墨烯包裹碳纤维束较一次成型其导热路线更加连续,以提高其导热性能;对比实施例1与对比例2,可知,背板玻璃及前板玻璃内部形成纵向导热通道可以显著提高光伏组件的导热效率,对比对比例2与对比例3,可知,eva封装胶膜作为粘结层,在其表面喷涂石墨烯分散液形成石墨烯薄膜;以及在封装胶膜上印刷网格状的石墨烯铝浆图案;可以提高光伏组件的导热效率。
102.本测试例用于表征实施例1和对比例2的石墨烯薄膜与玻璃的界面结合力。
103.对实施例1和对比例2的光伏组件前玻璃板进行橡皮擦拭实验。测试方法为用4b橡皮以相同的力度分别对实施例1和对比例2的光伏组件前玻璃板样品表面来回擦拭10次;测定擦拭前后待测样品的面电阻以及拉曼(raman)信号;
[0104][0105]
经分析可知,实施例1中形成的三维导热石墨烯膜网膜玻璃在擦拭前后raman信号无显著变化,与擦拭前相比,该样品在擦拭后只在2d值有所减小,面电阻有微小增加,表明玻璃表面的石墨烯层的结构无显著变化;而对比例2的光伏组件前板玻璃在擦拭前后raman信号有较大变化,与擦拭前相比,样品在擦拭后石墨烯相对于基底的信号强度显著减弱,2d峰几乎消失不见,面电阻显示无导电性,表明玻璃表面的石墨烯层在擦拭过程中受到严重破坏。此定性实验说明,形成的三维导热石墨烯膜网膜与玻璃基底间结合力的提升。
[0106]
本发明的目的还在于提供一种由上述方法制得的墨烯导热光伏板组件,包括若干组焊接好的光伏电池片400,各电池片之间形成有石墨烯铝浆层401,所述电池片及石墨烯铝浆层的上下方向上设置有封装胶膜层402,所述封装胶膜层的外表面上喷涂形成有石墨烯层形成芯体,还包括前板玻璃404以及背板玻璃405,所述前板玻璃以及背板玻璃分别复合在芯体的上下表面上;所述前板玻璃以及背板玻璃内形成有若干第一纵向导热层406,相邻光伏电池片之间形成有第二纵向导热层407,所述第二纵向导热层贯穿前板玻璃、上层封装胶膜、石墨烯铝浆图案、下层封装胶膜以及背板玻璃。