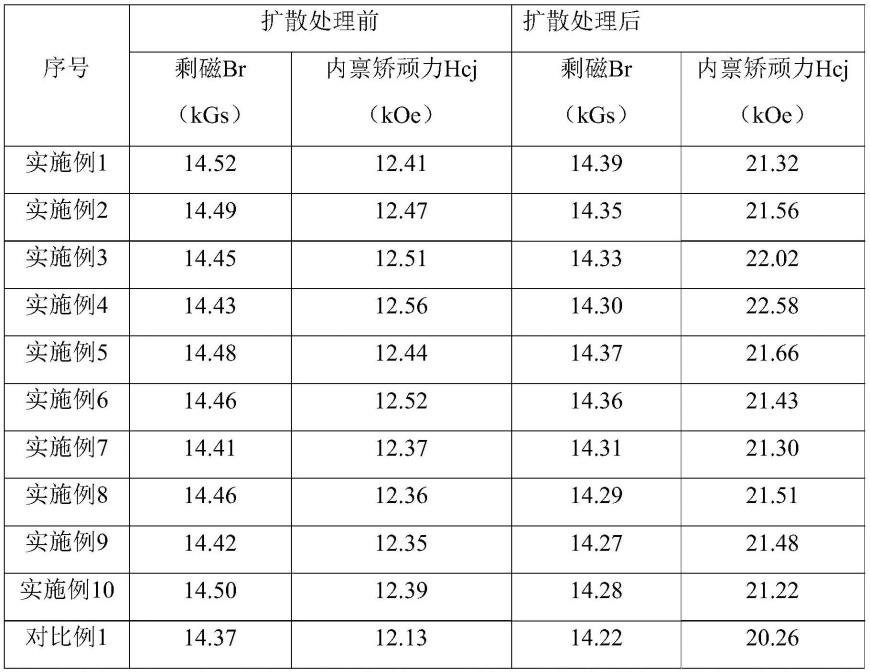
1.本发明涉及永磁材料技术领域,提供一种烧结钕铁硼永磁体及其制备方法。
背景技术:2.烧结钕铁硼永磁材料具有优异的磁性能,广泛应用于电子、电力机械、医疗器械、玩具、包装、五金机械、航天航空等领域,较常见的有永磁电机、扬声器、磁选机、计算机磁盘驱动器、磁共振成像设备仪表等。为了得到具有更高矫顽力与磁通量的永磁体,并且减小重稀土元素的掺杂量,采用晶界扩散(dy、tb、dy/tb单质或化合物)工艺已成为越来越多生产企业的选择。
3.如何提高烧结钕铁硼永磁材料的晶界扩散效果,得到具有更高矫顽力与磁通量的永磁体,成为了一个重要课题。晶界扩散技术核心的三个因素主要包括扩散源成分、附着扩散工艺和被扩散的钕铁硼基体。至今扩散相关的研究主要集中于前两者,但是关于扩散前基体材料的成分和结构状态对晶界扩散的影响研究却寥寥可数。
技术实现要素:4.鉴于此,本发明提出一种烧结钕铁硼永磁材料的制备方法,用该方法制备的烧结钕铁硼永磁材料经过晶界扩散处理后能够等到更高的矫顽力。
5.本技术提供了一种烧结钕铁硼永磁体的制备方法,包括以下步骤:获取钕铁硼氢破粉和镨铝铜氢破粉;在无氧条件下,对钕铁硼氢破粉和镨铝铜氢破粉进行气流磨处理,得到气流磨粉料;在氧含量≤500ppm的条件下,使气流磨粉料依次进行压制定型和等静压处理,得到钕铁硼生坯;对钕铁硼生坯依次进行真空烧结和回火处理,得到烧结钕铁硼永磁体。
6.进一步地,钕铁硼氢破粉的原料包括以下重量百分比的组分:pr-nd或nd:28.5%~30.5%、b:0.85%~0.95%、cu:0.01%~0.1%、ga:0.05%~0.15%、co:0.1%~0.5%、zr:0.1%~0.3%、余量为fe。
7.进一步地,镨铝铜氢破粉采用以下方法制得:将镨单质、铝单质和铜单质进行第一熔炼速凝甩带处理,得到镨铝铜合金甩带片;将镨铝铜合金甩带片进行第一氢破处理,得到镨铝铜氢破粉;钕铁硼氢破粉采用以下方法制得:将钕铁硼磁体原料进行第二熔炼速凝甩带处理,得到钕铁硼甩带片;将钕铁硼甩带片经过第二氢破处理,得到钕铁硼氢破粉;优选地,镨单质、铝单质和铜单质的原子百分比为:pr:60~80%、al:10~20%、cu:10~20%;优选地,钕铁硼甩带片和镨铝铜合金甩带片的预设平均厚度为3
±
0.5mm。
8.进一步地,第一氢破处理过程和第二氢破处理过程中,吸氢压力分别独立地选自0.08~0.15mpa,脱氢的温度分别独立地选自540~590℃。
9.进一步地,气流磨处理过程中,镨铝铜氢破粉的比例为1~10wt%。
10.进一步地,气流磨处理过程中,气流磨的研磨气体压力为500~700kpa,气流磨的分级轮转速为3800~5000rpm。
11.进一步地,在进行压制定型过程之前,烧结钕铁硼永磁体的制备方法还包括:对气流磨粉料进行预取向,然后使经预取向过程后得到的气流磨粉料与第一润滑剂混合后进行压制定型过程;优选地,预取向过程中采用的取向装置由电磁感应线圈制成,施加的取向磁场为0.8~1.5t。
12.进一步地,压制定型过程的磁场强度为1.5~5t,等静压处理过程的压力为150~300mpa;真空烧结过程的温度为980~1070℃,烧结时间为2~20h。
13.进一步地,回火处理过程包括:第一回火过程和第二回火过程;优选地,第一回火过程的温度为780~920℃,时间为2~5h;优选地,第二回火过程的温度为440~550℃,时间为2~8h。
14.本技术的另一方面还提供了一种烧结钕铁硼永磁体,该烧结钕铁硼永磁体采用本技术提供的烧结钕铁硼永磁体的制备方法制得。
15.本发明中,在气流磨制粉阶段前,加入镨铝铜合金氢破粉制备烧结钕铁硼磁体。镨的加入后能够取代晶粒表面的nd,并形成(nd,pr)2fe
14
b相,这能够增强主相的各向异性场。同时铝和铜的加入使得钕铁硼磁体烧结后,其晶界相的流动性和浸润性增强,进而使晶界扩散的dy、tb、dy/tb等更加连续地富集在晶界相中,更好地包裹主相晶粒,从而使其矫顽力增量获得提高。
具体实施方式
16.本技术提供了一种烧结钕铁硼永磁体的制备方法,包括以下步骤:获取钕铁硼氢破粉和镨铝铜氢破粉;在无氧条件下,对钕铁硼氢破粉和镨铝铜氢破粉进行气流磨处理,得到气流磨粉料;在氧含量≤500ppm的条件下,使气流磨粉料依次进行压制定型和等静压处理,得到钕铁硼生坯;对钕铁硼生坯依次进行真空烧结和回火处理,得到烧结钕铁硼永磁体。
17.本发明中,在气流磨制粉阶段前,加入镨铝铜合金氢破粉制备烧结钕铁硼磁体。镨的加入后能够取代晶粒表面的nd,并形成(nd,pr)2fe
14
b相,这能够增强主相的各向异性场。同时铝和铜的加入使得钕铁硼磁体烧结后,其晶界相的流动性和浸润性增强,进而使晶界扩散的dy、tb、dy/tb等更加连续地富集在晶界相中,更好地包裹主相晶粒,从而使其矫顽力增量获得提高。
18.在一种优选的实施例中,钕铁硼氢破粉的原料包括以下重量百分比的组分:pr-nd或nd:28.5%~30.5%、b:0.85%~0.95%、cu:0.01%~0.1%、ga:0.05%~0.15%、co:0.1%~0.5%、zr:0.1%~0.3%、余量为fe。钕铁硼氢破粉的组成包括但不限于上述范围,而将其限定在上述范围内有利于进一步增强其制得的钕铁硼氢破粉的磁性能。
19.镨铝铜氢破粉和钕铁硼氢破粉可以采用本领域常用的方法制得,比如,镨铝铜氢破粉采用以下方法制得:将镨单质、铝单质和铜单质进行第一熔炼速凝甩带处理,得到镨铝铜合金甩带片;将镨铝铜合金甩带片进行第一氢破处理,得到镨铝铜氢破粉;钕铁硼氢破粉采用以下方法制得:将钕铁硼磁体原料进行第二熔炼速凝甩带处理,得到钕铁硼甩带片;将钕铁硼甩带片经过第二氢破处理,得到钕铁硼氢破粉。
20.优选地,镨单质、铝单质和铜单质的原子百分比为:pr:60~80%、al:10~20%、cu:10~20%。相比于其他原子百分比,镨单质、铝单质和铜单质的原子百分比为上述范围
时,镨元素在晶相中分散地更加均匀,从而有利于进一步增强主相的各向异性场,同时矫顽力进一步等到增强。
21.优选地,钕铁硼甩带片和镨铝铜合金甩带片的预设平均厚度为3
±
0.5mm。将两种甩带的预设平均厚度设置在上述范围,有利于提高富钕相分散均匀性,同时抑制α-fe出现,提高后续制得的烧结永磁材料的矫顽力和剩磁。
22.在一种优选的实施例中,第一氢破处理过程和第二氢破处理过程中,吸氢压力分别独立地选自0.08~0.15mpa,脱氢的温度分别独立地选自540~590℃。氢破处理过程中,吸氢反应的压力和脱氢温度包括但不限于上述范围,而将其限定在上述范围内有利于进一步提高吸氢粉粒径的均匀性,从而能够进一步提高烧结永磁材料的磁性能。
23.在一种优选的实施例中,气流磨处理过程中,镨铝铜氢破粉的比例为1~10wt%。相比于其他范围,将镨铝铜氢破粉的比例限定在上述范围内有利于形成更多的(nd,pr)2fe
14
b相,从而进一步增强主相的各向异性场;同时还能够进一步提高晶相的流动性和浸润性增强,从而进一步提高其矫顽力。
24.在一种优选的实施例中,气流磨处理过程中,气流磨的研磨气体压力为500~700kpa,气流磨的分级轮转速为3800~5000rpm。将气流磨的研磨气体压力和气流磨的分级轮转速限定在上述范围内有利于提高气流磨粉的粒径均匀性。
25.为了抑制真空熔炼过程中表面氧化、脱碳、合金元素贫化、渗氢、渗氧、垂直褶皱和裂纹等现象出现,在一种优选的实施例中,在进行压制定型过程之前,烧结钕铁硼永磁体的制备方法还包括:对气流磨粉料进行预取向,然后使经预取向过程后得到的气流磨粉料与第一润滑剂混合后进行压制定型过程。
26.预取向过程有利于提高烧结钕铁硼永磁体的剩磁。优选地,预取向过程中采用的取向装置由电磁感应线圈制成,施加的取向磁场为0.8~1.5t。预取向过程的取向磁场包括但不限于上述范围,而将其限定在上述范围内有利于使烧结钕铁硼永磁体中晶粒的较好的取向度和剩磁,同时又具有优异的内矫顽力值。
27.为了进一步提高气流磨粉料颗粒的粒径均匀性,优选地,在气流磨处理过程之前,使钕铁硼氢破粉和镨铝铜氢破粉与第二润滑剂和/或乳化剂混合。更优选地,上述添加剂的添加量为钕铁硼氢破粉和镨铝铜氢破粉的0.01~0.08wt%。
28.上述第一润滑剂和第二润滑剂包括但不限于硬脂酸锌和/或硬脂酸钙,乳化剂包括但不限于聚乙二醇辛烷。优选地,钕铁硼氢破粉和镨铝铜氢破粉及添加剂的混合时间为10-60min。在一种优选的实施例中,气流磨粉料的平均粒度smd为2.3~2.9μm,d90/d10≤5.2;例如钕铁硼细粉的平均粒度smd为2.58μm、2.75μm。
29.优选地,压制定型过程的磁场强度为1.5~5t,等静压处理过程的压力为150~300mpa。压制定型过程的磁场强度和等静压处理过程的压力包括但不限于上述范围,而将其限定在上述范围内有利于进一步提高压坯密度(3.8~4.2g/cm3),进而有利于进一步提高烧结钕铁硼磁体的磁场强度。
30.在一种优选的实施例中,真空烧结过程的温度为980~1070℃,烧结时间为2~20h。真空烧结过程的温度和烧结时间包括但不限于上述范围,而将其限定在上述范围内有利于进一步提高富钕相在晶界间的分散均匀性,提高其磁性能。
31.需要将等经静压处理后的钕铁硼压坯放置于拨料箱中进行剥料和摆盒,其中,剥
料时的氧含量不高于500ppm,能减少o2的干预,避免重稀土元素的一定量的氧化,保证主相整体占比较高,有利于促进磁体性能的进一步提升。
32.在一种优选的实施例中,回火处理过程包括:第一回火过程和第二回火过程。采用二级回火过程有利于提高烧结钕铁硼永磁体的矫顽力。优选地,第一回火过程的温度为780~920℃,时间为2~5h;优选地,第二回火过程的温度为440~550℃,时间为2~8h。第一回火过程和第二回火过程的温度和时间包括但不限于上述范围,而将其限定在上述范围内有利于进一步提高富钕相在晶界间的分散均匀性,从而有利于更进一步提高烧结钕铁硼永磁体的矫顽力。
33.本技术的另一方面还提供了一种烧结钕铁硼永磁体,该烧结钕铁硼永磁体采用本技术提供的烧结钕铁硼永磁体的制备方法制得。
34.采用本技术提供的方法制得的烧结钕铁硼永磁体中主相具有较好各向异性和较高的矫顽力值。
35.下面将结合具体实施例,更加详细地描述本发明。
36.实施例1
37.按照重量百分比pr-nd 29.5%、b 0.94%、cu 0.05%、ga 0.1%、co 0.3%、zr 0.15%、余量为fe的比例称取原料,通过真空速凝法制备钕铁硼铸片,其中钕铁硼甩带片平均厚度3
±
0.5mm;
38.使用氮气保护的密封装置盛放、运输钕铁硼铸片至氢爆装置进行第一氢破处理,吸氢压力为0.1mpa,脱氢温度为580℃,得到钕铁硼氢破粉,平均粒度在10~20μm;
39.按照原子百分比pr 70%、al 10%、cu 20%,将其转换为相应重量的比例称取原材料,通过真空速凝法制备钕铁硼铸片,其中钕铁硼甩带片平均厚度3
±
0.5mm,并通过上述步骤进行第二氢破处理,得到镨铝铜氢破粉,平均粒度在8~15μm;
40.将两种氢破粗粉按照95:5的重量比例混合,向氢碎粉混合物中添加占其0.05wt%的硬脂酸锌进行一次混合,然后将一次混合物经过气流磨,得到平均粒度smd=2.5μm的气流磨细粉;
41.向气流磨细粉中加入0.3%的硬脂酸锌进行二次混合后,在磁场强度为2.0t的压机上制备得到成型生坯,并进行等静压;之后将成型生坯于真空烧结炉中烧结,烧结温度为1050℃,保温时间8h,第一回火过程的温度为850℃,保温时间为3h,第二回火过程的温度为500℃,保温时间为5h,第二回火过程保温结束后,使用氮气冷却,得到烧结钕铁硼磁体。
42.实施例2
43.与实施例1的区别在于:制备镨铝铜氢破粉的过程中,按照原子百分比pr 70%、al 15%、cu 15%称取原材料。
44.实施例3
45.与实施例1的区别在于:制备镨铝铜氢破粉的过程中,按照原子百分比pr 70%、al 20%、cu 10%称取原材料。
46.实施例4
47.与实施例1的区别在于:制备镨铝铜氢破粉的过程中,按照原子百分比pr 70%、al 20%、cu 10%称取原材料;且气流磨处理过程中,钕铁硼氢破粉和镨铝铜氢破粉的重量比为92:8。
48.实施例5
49.与实施例1的区别在于:制备镨铝铜氢破粉的过程中,按照原子百分比pr 70%、al 20%、cu 10%称取原材料;且气流磨处理过程中,钕铁硼氢破粉和镨铝铜氢破粉的重量比为97:3。
50.实施例6
51.与实施例1的区别在于:制备镨铝铜氢破粉的过程中,按照原子百分比pr 60%、al 20%、cu 20%称取原材料。
52.实施例7
53.与实施例1的区别在于:制备镨铝铜氢破粉的过程中,按照原子百分比pr 50%、al 25%、cu 25%称取原材料。
54.实施例8
55.与实施例1的区别在于:制备镨铝铜氢破粉的过程中,按照原子百分比pr 70%、al 20%、cu 10%称取原材料;且气流磨处理过程中,钕铁硼氢破粉和镨铝铜氢破粉的重量比为99:1。
56.实施例9
57.与实施例1的区别在于:制备镨铝铜氢破粉的过程中,按照原子百分比pr 70%、al 20%、cu 10%称取原材料;且气流磨处理过程中,钕铁硼氢破粉和镨铝铜氢破粉的重量比为99.5:0.5。
58.实施例10
59.与实施例1的区别为:第一氢破处理过程和第二氢破处理过程的吸氢压力均为0.2mpa,脱氢温度均为500℃。
60.对比例1
61.与实施例1的区别在于:钕铁硼磁体的制备过程中没有加入上述镨铝铜氢破粉。
62.性能测试:
63.将上述所有钕铁硼磁体取样,制作成18mm
×
24mm
×
4mm的磁片,测试其磁性能。用pvd法在样品表面沉积一层8μm后的tb镀层,进行扩散工艺处理,一级扩散温度为900℃,保温时间为16h,二级扩散温度为500,保温时间为4h。测试扩散后样品的磁性能。测试结果见表1。
64.表1
[0065][0066]
从上表数据可知,加入镨铝铜合金粗粉后,制备出的烧结钕铁硼材料,其晶界扩散后矫顽力增幅更强;镨铝铜合金中铝与铜的比例变化以及镨铝铜粗粉占比也会影响扩散后的磁性能。
[0067]
以上所述,仅是本发明的较佳实施例,并非对本发明作任何限制,凡是根据本发明技术实质对以上实施例所作的任何简单修改、变更以及等效变换,均仍属于本发明技术方案的保护范围。