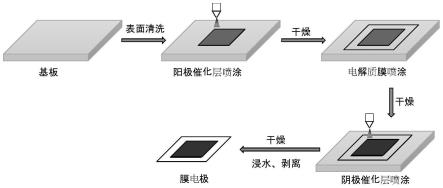
1.本发明属于膜电极技术领域,具体涉及一种膜电极的制备方法及膜电极。
背景技术:2.可再生能源的快速发展使其“间歇性”的缺点在大规模应用中成为日益突出的问题。通过电转气技术比如水电解将可再生能源所发的电转化为氢气,可以大大增强电力系统的灵活性从而提高可再生能源的消纳能力。因此电转气技术正成为可再生能源发展和应用的重要方向。固体聚合物电解质水电解制氢技术具备快速启停优势,同时具有环境友好、产氢纯度高、能量效率高、易于维护等优点,能匹配可再生能源发电的波动性,逐步成为电转气制氢主流技术。以聚合物电解质(pem)电解水制氢为例,目前pem水电解制氢已迈入10mw级别示范应用阶段,100mw级别的pem电解槽也正在开发。
3.膜电极组件(membrane electrode assembly,mea)是固体聚合物电解质水电解装置的核心部件,主要由固体聚合物电解质膜(离子交换膜)、催化剂、气体扩散层三个关键材料和边框组成。传统的膜电极组件制备方法可分为两大类:气体扩散电极法(gas diffusion electrode,gde)和催化剂涂覆膜法(catalyst coated membrane,ccm)。与gde相比,ccm使用固体聚合物电解质膜的核心材料作为离子传导相,降低了催化层与聚合物电解质膜之间的质子传输阻力,增加了催化剂和聚合物电解质的接触面积,在一定程度上提高了膜电极的性能以及催化剂的利用率和耐久性,因此是当今主流的燃料电池膜电极商业制备方法。
4.但是,由于ccm的催化层与聚合物电解质膜的溶胀性的差别和水电解特殊的工作环境(长时间在强酸、高电压的水环境下运行,反应产生氢气、氧气等对催化层的冲刷),易导致催化层与聚合物电解质膜的剥离,从而增加催化层与聚合物电解质膜之间的接触电阻,降低质子传导能力,影响膜电极的寿命。
5.若采用较高的热压温度和压力虽然会增强催化层与膜之间的接触界面,但由于离子聚合物较差的耐高温性能和催化层相对较低的结构强度,高温高压会破坏离子聚合物的离子传导性能和催化层的多孔结构,从而降低膜电极的性能和寿命。
技术实现要素:6.因此,本发明要解决的技术问题在于克服采用现有技术制得的膜电极催化层与聚合物电解质膜易剥离、导致膜电极性能和寿命降低的缺陷,从而提供一种膜电极的制备方法及膜电极。
7.为此,本发明提供了以下技术方案。
8.一种膜电极的制备方法,包括以下步骤:
9.步骤1、将阳极催化剂、离子聚合物悬浮液、第一溶剂混合,得混合液a,将所述混合液a涂覆在基板上,制备阳极催化层;
10.步骤2、将离子聚合物悬浮液与第二溶剂混合,得混合液b,在所述阳极催化层上原
位涂覆混合液b,制得聚合物电解质膜;
11.步骤3、将阴极催化剂、离子聚合物悬浮液、第三溶剂混合混合,得混合液c,将所述混合液c涂覆在所述聚合物电解质膜上,制备阴极催化层。
12.进一步的,所述步骤1满足条件(1)-(4)中的至少一项:
13.(1)所述阳极催化层中,离子聚合物的负载量为阳极催化剂负载量的50%到100%;
14.(2)所述阳极催化层中,所述阳极催化剂的负载量为0.4~3mg/cm2;
15.(3)将阳极催化剂、离子聚合物悬浮液、第一溶剂混合后,进行超声水浴分散,得到混合液a;
16.可选地,所述超声水浴分散时间为10~60min;
17.(4)将所述混合液a涂覆在基板上后,进行干燥,所述干燥温度为0-200℃、时间为1s-48h。
18.进一步的,所述步骤2满足以下条件中的至少一项:
19.(1)制得的聚合物电解质膜的厚度为10-200μm;
20.(2)涂覆混合液b后,进行干燥;所述干燥温度为0-200℃、时间为1s-48h;
21.(3)第二溶剂包括异丙醇和水,所述异丙醇与水的质量比例为(2~8):1。
22.进一步的,所述步骤3满足以下条件中的至少一项:
23.(1)阴极催化层中,阴极催化剂的负载量为0.05~3mg/cm2;
24.(2)涂覆混合液c后,进行干燥,所述干燥温度为0-200℃、时间为1s-48h。
25.进一步的,所述阳极催化剂为ir、pt、ru、pd、au、cu、ni、sn、ag中的一种或两种以上的合金,或者其氧化物;和/或
26.阴极催化剂为ir、pt、ru、pd、au、cu、ni、sn、ag中的一种或两种以上的合金,或者其氧化物。
27.进一步的,所述步骤1~步骤3中的涂覆采用喷涂;
28.可选地,为气体雾化喷涂或超声辅助雾化喷涂。
29.进一步的,所述基板材料为金属板、聚四氟乙烯、玻璃、聚碳酸酯或云母板。
30.进一步的,所述离子聚合物悬浮液中,离子聚合物的质量含量为5%~10%;
31.所述离子聚合物为nafion树脂、阴离子聚合物as-4或a201。
32.离子聚合物的种类视水电解运行的体系而定,阴离子聚合物和者阳离子聚合物分别应用于阴离子交换膜和质子交换膜水电解的膜电极。
33.进一步的,第一溶剂包括水、异丙醇、正丙醇、甲醇、乙醇中的一种或多种;
34.第二溶剂包括水、异丙醇、正丙醇、甲醇、乙醇中的一种或多种;
35.第三溶剂包括水、异丙醇、正丙醇、甲醇、乙醇中的一种或多种。
36.根据上述膜电极的制备方法制得的膜电极。
37.基板使用前,对其进行清洗去除表面附着物。
38.待阴极催化层干燥后,将基板和得到的膜电极整体浸入水中、或者在基板上用水直接浸透膜电极将膜电极从基板上取下,也可不用水浸透,直接将膜电极从基板上直接取下。
39.本发明技术方案,具有如下优点:
40.1.本发明提供的膜电极的制备方法,包括以下步骤:步骤1、将阳极催化剂、离子聚合物悬浮液、第一溶剂混合,得混合液a,将所述混合液a涂覆在基板上,制备阳极催化层;步骤2、将离子聚合物悬浮液与第二溶剂混合,得混合液b,在所述阳极催化层上原位涂覆混合液b,制得聚合物电解质膜;步骤3、将阴极催化剂、离子聚合物悬浮液、第三溶剂混合混合,得混合液c,将所述混合液c涂覆在所述聚合物电解质膜上,制备阴极催化层。
41.本发明先在基板上制备阳极催化层,再在所述阳极催化层上原位涂覆离子聚合物悬浮液制备聚合物电解质膜,在阳极催化层上直接原位铸膜,液相的良好流动性其部分渗透进阳极催化层,这样在铸膜完成以后阳极催化层与聚合物电解质膜之间的接触面积可以大大提高,从而有效地降低离子传导阻力,进一步改善催化剂的利用率,降低过电压,提高膜电极的性能。同时,由于一部分聚合物电解质膜渗透到了阳极催化层里,这样在水电解装置运行过程中,嵌入到阳极催化层孔隙中的部分聚合物电解质膜可以起到固定作用,防止阳极催化层与聚合物电解质膜的剥离,实现膜电极的长寿命运行。
42.本发明相对于目前的催化剂涂覆膜法,这种原位铸膜工艺可以在阳极使用一半或者更低的催化剂负载量,降低成本。无需额外基建设备,可与目前的催化剂涂覆膜法采用相同的设备,易于推广。阳极催化剂层直接镀在基板上,可保证膜电极的平整度。
43.2.本发明提供的膜电极的制备方法,所述步骤1满足条件(1)-(4)中的至少一项:(1)所述阳极催化层中,离子聚合物的负载量为阳极催化剂负载量的50%到100%;(2)所述阳极催化层中,所述阳极催化剂的负载量为0.4~3mg/cm2;(3)将阳极催化剂、离子聚合物悬浮液、第一溶剂混合后,进行超声水浴分散,得到混合液a;(4)将所述混合液a涂覆在基板上后,进行干燥,所述干燥温度为0-200℃、时间为1s-48h。
44.本发明通过对第一离子聚合物与阳极催化剂的负载量、分散条件、干燥温度的限定,保证步骤2中进行原位铸膜的聚合物电解质膜能够部分渗透进催化层增强接触界面,顺利形成稳定的结构。
45.本发明将催化剂涂覆膜工艺和铸膜工艺相结合,设计了一种用于固体聚合物电解质水电解的膜电极及其制备技术。制备的固体聚合物电解质可以实现部分嵌入到催化层孔隙里,能够大大提高催化层与电解质膜之间的接触面积和接触强度,可以有效降低膜电极的过电压,并实现长寿命运行。该方法可以用于制备质子交换膜水电解的膜电极,也可以用于碱性固体阴离子交换膜水电解的膜电极。采用原位铸膜法制备的膜电极可以显著提高电解装置的性能和寿命从而降低制氢的成本。基于该类原位铸膜法制备的膜电极具有广阔的市场前景。
附图说明
46.为了更清楚地说明本发明具体实施方式或现有技术中的技术方案,下面将对具体实施方式或现有技术描述中所需要使用的附图作简单地介绍,显而易见地,下面描述中的附图是本发明的一些实施方式,对于本领域普通技术人员来讲,在不付出创造性劳动的前提下,还可以根据这些附图获得其他的附图。
47.图1是实施例1的工艺流程图。
具体实施方式
48.提供下述实施例是为了更好地进一步理解本发明,并不局限于所述最佳实施方式,不对本发明的内容和保护范围构成限制,任何人在本发明的启示下或是将本发明与其他现有技术的特征进行组合而得出的任何与本发明相同或相近似的产品,均落在本发明的保护范围之内。
49.实施例中未注明具体实验步骤或条件者,按照本领域内的文献所描述的常规实验步骤的操作或条件即可进行。所用试剂或仪器未注明生产厂商者,均为可以通过市购获得的常规试剂产品。
50.实施例1
51.本实施例提供了一种膜电极的制备方法,制备尺寸10cm
×
10cm、有效膜电极面积为5cm
×
5cm,应用于质子交换膜水电解的膜电极。
52.制备方法如图1所示,包括以下步骤:
53.(1)准备厚度为5mm,尺寸为20cm
×
20cm的玻璃作为制备膜电极的基板。用丙酮和去离子水清洗玻璃基板,去除表面附着物。
54.(2)将12.5毫克ir黑催化剂(一般喷涂过程中会有20%的损耗)分散到3.8g异丙醇、0.95g水(异丙醇与水的比例为4:1)和0.27ml 5wt%nafion悬浮液的混合溶剂中,利用超声水浴分散30分钟。然后利用超声喷雾法将ir黑悬浮液均匀地喷涂到玻璃上,喷涂面积为5cm
×
5cm。扣除20%的损耗,ir的负载量为0.4mg/cm2。喷涂后在120℃干燥2小时,得到玻璃上负载的ir阳极催化层。
55.(3)将约4.76ml 5wt%nafion悬浮液与66.34g异丙醇16.58g水混合后,利用超声水浴分散30分钟。然后利用超声喷雾法均匀地喷涂到(2)中得到的负载有ir催化层的玻璃上。喷涂面积为10cm
×
10cm,扣除20%的损耗,nafion的负载量为1.75mg/cm2。喷涂后在120℃干燥2小时,得到玻璃上覆盖ir阳极催化层的nafion质子交换膜,厚度约为10微米。
56.(4)将3.13毫克pt/c催化剂(pt/c催化剂中pt占50wt%)分散到0.95g异丙醇、0.24g水和0.062g 5wt%nafion悬浮液的混合溶剂中,利用超声水浴分散30分钟。然后利用超声喷雾法将pt/c悬浮液均匀地喷涂到(3)中得到的nafion质子交换膜上,喷涂面积为5cm
×
5cm,完全覆盖膜下方的阳极催化层。扣除20%的损耗,pt的负载量为0.05mg/cm2。喷涂后在120℃干燥2小时,得到nafion质子交换膜上负载的pt/c阴极催化层。
57.(5)将(4)中得到的负载有膜电极的玻璃置于去离子水中室温浸泡30分钟,利用nafion的吸水膨胀效用使膜电极从玻璃板上自动剥离。在60℃干燥2小时后得到最终的膜电极。
58.实施例2
59.本实施例提供了一种膜电极的制备方法,制备尺寸10cm
×
10cm、有效膜电极面积为5cm
×
5cm应用于质子交换膜水电解的膜电极。
60.(1)准备厚度为5mm,尺寸为20cm
×
20cm的玻璃作为制备膜电极的基板。用丙酮和去离子水清洗玻璃基板,去除表面附着物。
61.(2)将20毫克iro2催化剂(喷涂过程中会有20%的损耗)分散到6.08g异丙醇、1.52g水(比例为4:1)和0.4g 5wt%nafion悬浮液的混合溶剂中,利用超声水浴分散30分钟。然后利用超声喷雾法将iro2悬浮液均匀地喷涂到玻璃上,喷涂面积为5cm
×
5cm。扣除
20%的损耗,iro2的负载量为0.64mg/cm2。喷涂后在120℃干燥2小时,得到玻璃上负载的pt阳极催化层。
62.(3)将约25ml 5wt%nafion悬浮液与443.26g异丙醇和87.1g水混合后,利用超声水浴分散30分钟。然后利用超声喷雾法均匀地喷涂到(2)中得到的负载有iro2催化层的玻璃上。喷涂面积为10cm
×
10cm,扣除20%的损耗,nafion的负载量为9.21mg/cm2。喷涂后在120℃干燥1小时,得到玻璃上覆盖iro2阳极催化层的nafion质子交换膜,厚度约为10微米。
63.(4)将3.13毫克pt催化剂分散到0.96g异丙醇、0.24g水和0.063 5wt%nafion悬浮液的混合溶剂中,利用超声水浴分散30分钟。然后利用超声喷雾法将pt/c悬浮液均匀地喷涂到(3)中得到的nafion膜上,喷涂面积为5cm
×
5cm,完全覆盖膜下方的阳极催化剂层。扣除20%的损耗,pt的负载量为0.1mg/cm2。喷涂后在120℃干燥2小时,得到nafion膜上负载的pt/c阴极催化层。
64.(5)将(4)中得到的负载有膜电极的玻璃置于去离子水中室温浸泡30分钟,利用nafion的吸水膨胀效用使膜电极从玻璃板上自动剥离。在60℃干燥2小时后得到最终的膜电极。
65.实施例3
66.本实施例提供了一种膜电极的制备方法,制备尺寸10cm
×
10cm、有效膜电极面积为5cm
×
5cm应用于质子交换膜水电解的膜电极。
67.(1)准备厚度为5mm,尺寸为20cm
×
20cm的玻璃作为制备膜电极的基板。用丙酮和去离子水清洗玻璃基板,去除表面附着物。
68.(2)将80毫克ruir催化剂(假设喷涂过程中会有20%的损耗)分散到24.32g异丙醇、6.08g水和1.6g 5wt%nafion悬浮液的混合溶剂中,利用超声水浴分散30分钟。然后利用超声喷雾法将ruir悬浮液均匀地喷涂到玻璃上,喷涂面积为5cm
×
5cm。扣除20%的损耗,ruir的负载量为2.56mg/cm2。喷涂后在120℃干燥2小时,得到玻璃上负载的ruir阳极催化层。
69.(3)将约50ml 5wt%nafion悬浮液与696.8g异丙醇和174.2g水混合后,利用超声水浴分散30分钟。然后利用超声喷雾法均匀地喷涂到(2)中得到的负载有ruir催化层的玻璃上。喷涂面积为10cm
×
10cm,扣除20%的损耗,nafion的负载量为18.42mg/cm2。喷涂后在120℃干燥2小时,得到玻璃上覆盖ruir阳极催化层的nafion质子交换膜,厚度约为100微米。
70.(4)将9.39毫克pt/c催化剂(pt/c催化剂中pt占50wt%)分散到2.85g异丙醇、0.71g水和0.19g 5wt%nafion悬浮液的混合溶剂中,利用超声水浴分散30分钟。然后利用超声喷雾法将pt/c悬浮液均匀地喷涂到(3)中得到的nafion膜上,喷涂面积为5cm
×
5cm,完全覆盖膜下方的阳极催化剂层。扣除20%的损耗,pt的负载量为0.15mg/cm2。喷涂后在120℃干燥2小时,得到nafion膜上负载的pt/c阴极催化层。
71.(5)将(4)中得到的负载有膜电极的玻璃置于去离子水中室温浸泡30分钟,利用nafion的吸水膨胀效用使膜电极从玻璃板上自动剥离。在60℃干燥2小时后得到最终的膜电极。
72.实施例4
73.本实施例提供了一种膜电极的制备方法,制备尺寸10cm
×
10cm、有效膜电极面积
为5cm
×
5cm应用于质子交换膜水电解的膜电极。
74.(1)准备厚度为5mm,尺寸为20cm
×
20cm的玻璃作为制备膜电极的基板。用丙酮和去离子水清洗玻璃基板,去除表面附着物。
75.(2)将50毫克ptruir黑催化剂(假设喷涂过程中会有20%的损耗)分散到15.2g异丙醇、3.8g水和1g 5wt%nafion悬浮液的混合溶剂中,利用超声水浴分散30分钟。然后利用超声喷雾法将ptruir黑悬浮液均匀地喷涂到玻璃上,喷涂面积为5cm x 5cm。扣除20%的损耗,ptruir的负载量为1.6mg/cm2。喷涂后在120℃干燥2小时,得到玻璃上负载的ptruir阳极催化层。
76.(3)将约50ml 5wt%nafion悬浮液与696.8g异丙醇和174.2g水混合后,利用超声水浴分散30分钟。然后利用超声喷雾法均匀地喷涂到(2)中得到的负载有ptruir催化层的玻璃上。喷涂面积为10cm
×
10cm,扣除20%的损耗,nafion的负载量为42mg/cm2。喷涂后在150℃干燥2小时,得到玻璃上覆盖ptruir阳极催化层的nafion质子交换膜,厚度约为200微米。
77.(4)将31毫克pt催化剂分散到31g异丙醇、7.75g水和0.4g 5wt%nafion悬浮液的混合溶剂中,利用超声水浴分散30分钟。然后利用超声喷雾法将pt/c悬浮液均匀地喷涂到(3)中得到的nafion膜上,喷涂面积为5cm
×
5cm,完全覆盖膜下方的阳极催化剂层。扣除20%的损耗,pt的负载量为1mg/cm2。喷涂后在120℃干燥2小时,得到nafion膜上负载的pt/c阴极催化层。
78.(5)将(4)中得到的负载有膜电极的玻璃置于去离子水中室温浸泡30分钟,利用nafion的吸水膨胀效用使膜电极从玻璃板上自动剥离。在60℃干燥2小时后得到最终的膜电极。
79.显然,上述实施例仅仅是为清楚地说明所作的举例,而并非对实施方式的限定。对于所属领域的普通技术人员来说,在上述说明的基础上还可以做出其它不同形式的变化或变动。这里无需也无法对所有的实施方式予以穷举。而由此所引申出的显而易见的变化或变动仍处于本发明创造的保护范围之中。