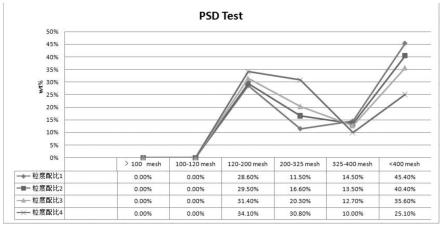
一种磁导率
μ
为9的铁硅软磁粉芯及其制备方法
技术领域
1.本发明属于软磁材料技术领域,具体涉及一种磁导率μ为9的铁硅软磁粉芯及其制备方法。
背景技术:2.铁硅软磁粉芯材料具有优异的dc偏流特性,高达16000高斯的饱和磁通密度,良好的温度稳定性和高储能。铁硅软磁粉芯特别适合家电、ups电源、光伏逆变器以及新能源汽车(obc),风力、水利发电等领域。最近几年国家提倡碳达峰碳中和带动新能源行业的快速崛起,有力地促进软磁材料的快速发展。
3.目前,铁硅粉末生产工艺主要分为气雾化、水雾化和机械破碎法三种。机械破碎法由于无法满足市场性能要求,已经退出市场。水雾化铁硅粉末由于形状不规则(图1),表面棱角多,对粉末绝缘包覆的要求也越高,同时压制过程棱角相互挤压,绝缘层容易破坏,从而造成磁芯损耗高;然而气雾化铁硅粉末成球形状(图2),粉末氧含量比较好控制,做出来的磁芯直流叠加高,损耗低。
4.专利号cn102543345b发明专利公开了铁硅铝软磁粉芯的制造方法。该工艺需要将粉末加热到然后倒入磷酸钝化液进行钝化,虽然绝缘工艺简单,生产效率高,但是无法做更低磁导率。
5.因此,如何开发出一种磁导率低,直流偏置性能好,特别适合于大电流电力设备使用的铁硅软磁粉芯是本领域技术人员亟待解决的技术难题。
技术实现要素:6.有鉴于此,本发明是为了克服现有技术中存在的上述不足,提供一种磁导率μ为9的铁硅软磁粉芯制备方法,采用本方法制得的铁硅软磁粉芯损耗低,直流偏置性能好。
7.为了实现上述目的,本发明所采取的技术方案是:
8.一种磁导率μ为9的铁硅软磁粉芯,所述铁硅软磁粉芯是由铁硅粉末按照粒度配比,并经一次绝缘包覆、粉末热处理、二次绝缘包覆、压制成型、磁芯热处理和表面涂装制得;其中,
9.所述铁硅粉末的粒度配比为:-120~+200目占34.1%,-200~+325目占30.8%,-325~+400目占10%,-400目以下占25.1%。
10.需要说明的是,由于粉末颗粒越粗压缩比越小,粉末填充越小,压制磁芯的高度就越高,以致磁导率升高;反之粉末越细压缩比越大,压制磁芯高度越小,以致磁导率降低。
11.可选地,所述铁硅软磁芯采用的是气雾化铁硅粉末,且所述铁硅粉末中硅的含量为5%~6%,余量为铁。
12.可选地,所述绝缘包覆采用磷酸、酒精、水,高岭土、硅酸钾、木质素,以在铁硅粉末表面形成磷酸盐,硅酸盐、硅氧化物绝缘层。
13.此外,本发明还请求保护一种如上述磁导率μ为9的铁硅软磁粉芯的制备方法,具
体包括如下步骤:
14.1)一次绝缘包覆:将气雾化铁硅粉末混合均匀,倒入磷酸、酒精、水的混合绝缘液体,待粉末化学反应完成后进行加热炒干,备用;
15.2)粉末热处理:将经步骤1)一次绝缘包覆后的铁硅粉末在隧道炉中进行热处理,并通入第一保护气体进行保护,备用;
16.3)二次绝缘包覆:把经步骤2)热处理后的粉末倒入绝缘设备中,加入高岭土并搅拌均匀,再加入硅酸钾、水、木质素进行加热炒干,备用;
17.4)压制成型:在经步骤3)绝缘后的粉末中加入脱模剂,进行压制成型,备用;
18.5)磁芯热处理:将步骤4)压制成型的磁芯放入氮气气氛中进行烧结,随后磁芯表面采用环氧树脂粉进行旋涂,即制备得到所述磁导率μ为9的铁硅软磁粉芯。
19.可选地,步骤1)中,所述磷酸的用量为铁硅粉末重量的5~8%,酒精的用量为铁硅粉末重量的8%,水的用量为铁硅粉末重量的11%,加热温度控制在130℃以下,具体为100℃~130℃。
20.可选地,步骤2)中,热处理温度为700℃~800℃,保温时间为30~120min;及所述第一保护气体至少为氮气、氢气中的一种。
21.可选地,步骤3)中,所述高岭土的用量为铁硅粉末重量的8%~10%,木质素的用量为铁硅粉末重量的1%,硅酸钾的用量为铁硅粉末重量的8%~10%,水的用量为铁硅粉末重量的12%,且加热温度控制在100~130℃之间。
22.可选地,步骤4)中,所述脱模剂为微晶蜡或硬脂酸锌,及所述脱模剂的用量为铁硅粉末重量的0.2~0.4%;且压制成型的压力为18~22t/cm2。
23.可选地,步骤5)中,氮气流量为6m3/h,烧结温度为700℃~780℃,保温时间为30~120min。
24.经由上述的技术方案可知,与现有技术相比,本发明公开提供的一种磁导率μ为9的铁硅软磁粉芯及其制备方法,具有如下优异效果:
25.(1)本发明中绝缘工序简单,生产效率高,可进行大批量生产,制备过程节能环保,所制得的产品性能优异;且磁芯具有极高的直流偏置性能以及优异的功率损耗,产品性能处于行业领先水平。
26.(2)本发明采用粗细粉末进行粒度配比,其中-120目到+200目占34.1%,-200目到+325目占30.8%,-325目到+400目占10%,-400目以下占25.1%,粗细搭配的好处能够提高磁芯的致密度,降低磁芯的孔隙率,能有效的降低磁芯损耗。
附图说明
27.为了更清楚地说明本发明实施例或现有技术中的技术方案,下面将对实施例或现有技术描述中所需要使用的附图作简单地介绍,显而易见地,下面描述中的附图仅仅是本发明的实施例,对于本领域普通技术人员来讲,在不付出创造性劳动的前提下,还可以根据提供的附图获得其他的附图。
28.图1为水雾化铁硅粉末的sem图。
29.图2为气雾化铁硅粉末的sem图。
30.图3为粒度配比关系图。
具体实施方式
31.下面将结合本发明实施例及说明书附图,对本发明实施例中的技术方案进行清楚、完整地描述,显然,所描述的实施例仅仅是本发明一部分实施例,而不是全部的实施例。基于本发明中的实施例,本领域普通技术人员在没有做出创造性劳动前提下所获得的所有其他实施例,都属于本发明保护的范围。
32.为了更好地理解本发明,下面结合实施例对本发明的技术方案做进一步的说明。
33.实施例1
34.1)取气雾化铁硅粉末,其中硅的含量为5%~6%,铁硅粉末粒度配比为,-120目到+200目占34.1%,-200目到+325目占30.8%,-325目到+400目占10%,-400目以下占25.1%,按照以上比例将粉末混合均匀;
35.2)一次绝缘:将混合好的铁硅粉末倒入绝缘设备中,然后倒入磷酸、酒精、水的混合绝缘液体,当铁硅粉末和磷酸绝缘液体完成化学反应后,进行加热翻炒至干燥;其中磷酸的用量为铁硅粉末重量的7%,酒精的用量为铁硅粉末重量的8%,水的用量为铁硅粉末重量的11%,加热温度控制在100~130℃之间;
36.3)绝缘粉末热处理:将一次绝缘包覆后的铁硅粉末在隧道炉中进行热处理,先通入第氮气,20min后再通入氢气;于750℃条件下进行热处理,保温时间为50min;其中氮气流量设置为6m3/h,氢气流量设置为2.5m3/h;
37.4)二次绝缘:将热处理冷却后的铁硅粉末再次倒入绝缘设备中.添加高岭土搅拌均匀,再加入硅酸钾、木质素和水的混合绝缘液体,进行加热翻炒至干燥;其中高岭土的用量为铁硅粉末重量的8%,木质素的用量为铁硅粉末重量的1%,硅酸钾的用量为铁硅粉末重量的8%,水的用量为铁镍粉末重量的12%,加热温度控制在100~130℃之间;
38.5)压制成型:压制成型前加入铁硅粉末重量0.3%的硬脂酸锌作为脱模剂,混合均匀后压制成26.9mm*14.8mm*11.1mm的磁环.成型压力采用20吨/平方厘米压制;将成型后的磁芯放入热处理炉,通入氮气在760℃下保温50min,然后自然冷却,其中氮气流量设置为6m3/h;
39.6)在磁环表面用环氧树脂粉末进行旋涂,固化后得到磁导率μ为9的铁硅软磁粉芯。经检测得到的铁硅软磁粉芯的磁性能如表1所示。
40.实施例2
41.1)取气雾化铁硅粉末,其中硅的含量为5%~6%,铁硅粉末粒度配比为,-120目到+200目占34.1%,-200目到+325目占30.8%,-325目到+400目占10%,-400目以下占25.1%,按照以上比例将粉末混合均匀;
42.2)一次绝缘:将混合好的铁硅粉末倒入绝缘设备中,然后倒入磷酸、酒精、水的混合绝缘液体.当铁硅粉末和磷酸绝缘液体完成化学反应后,进行加热翻炒至干燥;其中磷酸的用量为铁硅粉末重量的7%,酒精的用量为铁硅粉末重量的8%,水的用量为铁硅粉末重量的11%,加热温度控制在100~130℃之间;
43.3)绝缘粉末热处理:将一次绝缘包覆后的铁硅粉末在隧道炉中进行热处理,先通入第氮气,20min后再通入氢气;于770℃条件下进行热处理,保温时间为50min;其中氮气流量设置为6m3/h,氢气流量设置为2.5m3/h;
44.4)二次绝缘:将热处理冷却后的铁硅粉末再次倒入绝缘设备中.添加高岭土搅拌
均匀,再加入硅酸钾、木质素和水的混合绝缘液体,进行加热翻炒至干燥;其中高岭土的用量为铁硅粉末重量的9%,木质素的用量为铁硅粉末重量的1%,硅酸钾的用量为铁硅粉末重量的7%,水的用量为铁镍粉末重量的12%,加热温度控制在100~130℃之间;
45.5)压制成型:压制成型前加入铁硅粉末重量0.3%的硬脂酸锌作为脱模剂,混合均匀后压制成26.9mm*14.8mm*11.1mm的磁环,成型压力采用19吨/平方厘米压制;将成型后的磁芯放入热处理炉,通入氮气在740℃下保温50min,然后自然冷却,其中氮气流量设置为6m3/h;
46.6)在磁环表面用环氧树脂粉末进行旋涂,固化后得到磁导率μ为9的铁硅软磁粉芯。经检测得到的铁硅软磁粉芯的磁性能如表1所示。
47.实施例3
48.1)取气雾化铁硅粉末,其中硅的含量为5%~6%,铁硅粉末粒度配比为,-120目到+200目占34.1%,-200目到+325目占30.8%,-325目到+400目占10%,-400目以下占25.1%,按照以上比例将粉末混合均;
49.2)一次绝缘:将混合好的铁硅粉末倒入绝缘设备中,然后倒入磷酸、酒精、水的混合绝缘液体.当铁硅粉末和磷酸绝缘液体完成化学反应后,进行加热翻炒至干燥;其中磷酸的用量为铁硅粉末重量的8%,酒精的用量为铁硅粉末重量的8%,水的用量为铁硅粉末重量的11%,加热温度控制在100~130℃之间;
50.3)绝缘粉末热处理:将一次绝缘包覆后的铁硅粉末在隧道炉中进行热处理,先通入第氮气,20min后再通入氢气;于760℃条件下进行热处理,保温时间为50min;其中氮气流量设置为6m3/h,氢气流量设置为2.5m3/h;
51.4)二次绝缘:将热处理冷却后的铁硅粉末再次倒入绝缘设备中.添加高岭土搅拌均匀,再加入硅酸钾、木质素和水的混合绝缘液体,进行加热翻炒至干燥;其中高岭土的用量为铁硅粉末重量的8%,木质素的用量为铁硅粉末重量的1%,硅酸钾的用量为铁硅粉末重量的7%,水的用量为铁镍粉末重量的12%,加热温度控制在100~130℃之间;
52.5)压制成型:压制成型前加入铁硅粉末重量0.4%的硬脂酸锌作为脱模剂,混合均匀后压制成26.9mm*14.8mm*11.1mm的磁环.成型压力采用20吨/平方厘米压制;将成型后的磁芯放入热处理炉,通入氮气在740℃下保温50min,然后自然冷却,其中氮气流量设置为6m3/h;
53.6)在磁环表面用环氧树脂粉末进行旋涂,固化后得到磁导率μ为9的铁硅软磁粉芯。经检测得到的铁硅软磁粉芯的磁性能如表1所示。
54.实施例4
55.1)取气雾化铁硅粉末,其中硅的含量为5%~6%,铁硅粉末粒度配比为,-120目到+200目占34.1%,-200目到+325目占30.8%,-325目到+400目占10%,-400目以下占25.1%,按照以上比例将粉末混合均匀;
56.2)一次绝缘:将混合好的铁硅粉末倒入绝缘设备中,然后倒入磷酸、酒精、水的混合绝缘液体.当铁硅粉末和磷酸绝缘液体完成化学反应后,进行加热翻炒至干燥;其中磷酸的用量为铁硅粉末重量的5%,酒精的用量为铁硅粉末重量的8%,水的用量为铁硅粉末重量的11%,加热温度控制在100~130℃之间;
57.3)绝缘粉末热处理:将一次绝缘包覆后的铁硅粉末在隧道炉中进行热处理,先通
入第氮气,20min后再通入氢气。于740℃条件下进行热处理,保温时间为50min;其中氮气流量设置为6m3/h,氢气流量设置为2.5m3/h;
58.4)二次绝缘:将热处理冷却后的铁硅粉末再次倒入绝缘设备中.添加高岭土搅拌均匀,再加入硅酸钾、木质素和水的混合绝缘液体,进行加热翻炒至干燥;其中高岭土的用量为铁硅粉末重量的10%,木质素的用量为铁硅粉末重量的1%,硅酸钾的用量为铁硅粉末重量的10%,水的用量为铁镍粉末重量的12%,加热温度控制在100~130℃之间;
59.5)压制成型前加入铁硅粉末重量0.4%的硬脂酸锌作为脱模剂,混合均匀后压制成26.9mm*14.8mm*11.1mm的磁环.成型压力采用22吨/平方厘米压制.将成型后的磁芯放入热处理炉,通入氮气在780℃下保温50min,然后自然冷却,其中氮气流量设置为6m3/h;
60.6)在磁环表面用环氧树脂粉末进行旋涂,固化后得到磁导率μ为9的铁硅软磁粉芯。经检测得到的铁硅软磁粉芯的磁性能如表1所示。
61.实施例5
62.1)取气雾化铁硅粉末,其中硅的含量为5%~6%,铁硅粉末粒度配比为,-120目到+200目占34.1%,-200目到+325目占30.8%,-325目到+400目占10%,-400目以下占25.1%,按照以上比例将粉末混合均匀;
63.2)一次绝缘:将混合好的铁硅粉末倒入绝缘设备中,然后倒入磷酸、酒精、水的混合绝缘液体.当铁硅粉末和磷酸绝缘液体完成化学反应后,进行加热翻炒至干燥;其中磷酸的用量为铁硅粉末重量的6%,酒精的用量为铁硅粉末重量的8%,水的用量为铁硅粉末重量的11%,加热温度控制在100~130℃之间;
64.3)绝缘粉末热处理:将一次绝缘包覆后的铁硅粉末在隧道炉中进行热处理,先通入第氮气,20min后再通入氢气。于750℃条件下进行热处理,保温时间为50min。其中氮气流量设置为6m3/h,氢气流量设置为2.5m3/h;
65.4)二次绝缘:将热处理冷却后的铁硅粉末再次倒入绝缘设备中.添加高岭土搅拌均匀,再加入硅酸钾、木质素和水的混合绝缘液体,进行加热翻炒至干燥;其中高岭土的用量为铁硅粉末重量的9%,木质素的用量为铁硅粉末重量的1%,硅酸钾的用量为铁硅粉末重量的9%,水的用量为铁镍粉末重量的12%,加热温度控制在100~130℃之间;
66.5)压制成型:压制成型前加入铁硅粉末重量0.3%的硬脂酸锌作为脱模剂,混合均匀后压制成26.9mm*14.8mm*11.1mm的磁环.成型压力采用21吨/平方厘米压制;将成型后的磁芯放入热处理炉,通入氮气在760℃下保温50min,然后自然冷却,其中氮气流量设置为6m3/h;
67.6)在磁环表面用环氧树脂粉末进行旋涂,固化后得到磁导率μ为9的铁硅软磁粉芯。经检测得到的铁硅软磁粉芯的磁性能如表1所示。
68.表1实施例1-实施例5得到的铁硅软磁粉芯的磁性能
[0069][0070]
由表1可知,使用本方法制备的磁导率μ为9的铁硅软磁粉芯,直流偏置性能200oe条件下为90%以上;功率损耗在100khz,30mt下为300mw/cm3左右,性能处于行业的领先水平。
[0071]
实施例6
[0072]
1)取气雾化铁硅粉末,其中硅的含量为5%~6%,铁硅粉末粒度配比为,-120目到+200目占34.1%,-200目到+325目占30.8%,-325目到+400目占10%,-400目以下占25.1%,按照以上比例将粉末混合均匀;
[0073]
2)一次绝缘:将混合好的铁硅粉末倒入绝缘设备中,然后倒入磷酸、酒精、水的混合绝缘液体.当铁硅粉末和磷酸绝缘液体完成化学反应后,进行加热翻炒至干燥;其中磷酸的用量为铁硅粉末重量的6%,酒精的用量为铁硅粉末重量的8%,水的用量为铁硅粉末重量的11%,加热温度控制在100~130℃之间;
[0074]
3)绝缘粉末热处理:将一次绝缘包覆后的铁硅粉末在隧道炉中进行热处理,先通入第氮气,20min后再通入氢气。于740℃条件下进行热处理,保温时间为50min。其中氮气流量设置为4m3/h,氢气流量设置为2.5m3/h;
[0075]
4)二次绝缘:将热处理冷却后的铁硅粉末再次倒入绝缘设备中.添加高岭土搅拌均匀,再加入硅酸钾、木质素和水的混合绝缘液体,进行加热翻炒至干燥;其中高岭土的用量为铁硅粉末重量的9%,木质素的用量为铁硅粉末重量的1%,硅酸钾的用量为铁硅粉末重量的9%,水的用量为铁镍粉末重量的12%,加热温度控制在100~130℃之间;
[0076]
5)压制成型:压制成型前加入铁硅粉末重量0.3%的硬脂酸锌作为脱模剂,混合均匀后压制成26.9mm*14.8mm*11.1mm的磁环.成型压力采用18,19,20,21,22吨/平方厘米压制;将成型后的磁芯放入热处理炉,通入氮气在740℃下保温50min,然后自然冷却,其中氮气流量设置为6m3/h;
[0077]
6)在磁环表面用环氧树脂粉末进行旋涂,固化后得到磁导率μ为9的铁硅软磁粉芯。经检测得到的铁硅软磁粉芯的磁性能如表2所示,通过测试性能可以看出,压力越大磁芯的损耗越低,直流叠加也越好。
[0078]
表2不同压力压制得到的铁硅软磁粉芯的磁性能
[0079][0080]
由表2可知,相同的绝缘包覆工艺,相同条件下的热处理温度,当压力越大时磁芯的磁导率μ值越高,同时直流叠加和损耗也越好;且在模具所能承受压力范围内,压力越大磁芯性能越好。
[0081]
实施例7
[0082]
1)取气雾化铁硅粉末,其中硅的含量为5%~6%,铁硅粉末粒度配比为,-120目到+200目占34.1%,-200目到+325目占30.8%,-325目到+400目占10%,-400目以下占25.1%,按照以上比例将粉末混合均;
[0083]
2)一次绝缘:将混合好的铁硅粉末倒入绝缘设备中,然后倒入磷酸、酒精、水的混合绝缘液体.当铁硅粉末和磷酸绝缘液体完成化学反应后,进行加热翻炒至干燥;其中磷酸的用量为铁硅粉末重量的7%,酒精的用量为铁硅粉末重量的7%,水的用量为铁硅粉末重量的4%,加热温度控制在100~130℃之间;
[0084]
3)绝缘粉末热处理:将一次绝缘包覆后的铁硅粉末在隧道炉中进行热处理,先通入第氮气,20min后再通入氢气;于740℃条件下进行热处理,保温时间为50min;其中氮气流量设置为6m3/h,氢气流量设置为2.5m3/h;
[0085]
4)二次绝缘:将热处理冷却后的铁硅粉末再次倒入绝缘设备中.添加高岭土搅拌均匀,再加入硅酸钾、木质素和水的混合绝缘液体,进行加热翻炒至干燥;其中高岭土的用量为铁硅粉末重量的5%,木质素的用量为铁硅粉末重量的1%,硅酸钾的用量为铁硅粉末重量的6%,水的用量为铁镍粉末重量的10%,加热温度控制在100~130℃之间;
[0086]
5)压制成型:压制成型前加入铁硅粉末重量0.4%的硬脂酸锌作为脱模剂,混合均匀后压制成26.9mm*14.8mm*11.1mm的磁环.成型压力采用21吨/平方厘米压制;将成型后的磁芯放入热处理炉,通入氮气分别在680℃,720℃,740℃,760℃,780℃下保温50min,然后自然冷却,其中氮气流量设置为6m3/h;
[0087]
6)在磁环表面用环氧树脂粉末进行旋涂,固化后得到磁导率μ为9的铁硅软磁粉芯。经检测得到的铁硅软磁粉芯的磁性能如表3所示。
[0088]
表3不同退火温度得到的铁硅软磁粉芯的磁性能
[0089][0090]
由表3可知,相同的绝缘包覆工艺,相同的压力,当热处理温度越高时磁芯磁导率越高,同时直流叠加和损耗开始变差;当热处理温度越低时,磁导率越低,同时直流叠加变好,但是损耗也开始变差;且热处理温度在720℃~740℃之间损耗和直流叠加性能最好。
[0091]
此外,粒度配比与粉末压缩比间存在的关系,如下表4和表5所示。
[0092]
表4
[0093][0094]
表5
[0095][0096]
对所公开实施例的上述说明,使本领域专业技术人员能够实现或使用本发明。对这些实施例的多种修改对本领域的专业技术人员来说将是显而易见的,本文中所定义的一般原理可以在不脱离本发明的精神或范围的情况下,在其它实施例中实现。因此,本发明将
不会被限制于本文所示的这些实施例,而是要符合与本文所公开的原理和新颖特点相一致的最宽的范围。