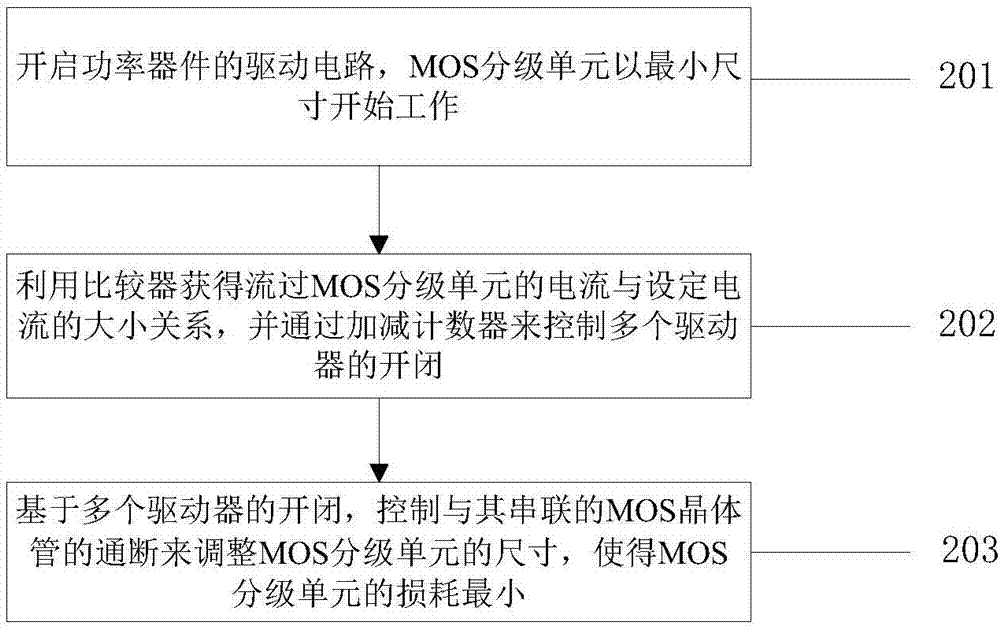
本发明属于集成电路领域,更具体地,涉及一种功率器件的驱动电路及方法。
背景技术:
:在电源类电路中,尤其是开关电源类电路中,如开关型降压(BUCK),开关型升压(BOOST),还有马达驱动、D类音频放大器等,都需要驱动一个功率管。原来的驱动设计方法都是根据功率、效率及成本的需求,设定好一下固定Rdson值的MOS,无论这个MOS是P型还是N型的。为了便于说明问题,在这里,我仅以驱动N型MOS管为例。在大功率的方案中,通常要求这个Rdson非常小,比如10毫欧,这就意味着MOS管的面积相当大。而且,通常P型MOS管的面积还会是N型的2~3倍。面积大,也就意味着寄生的栅源电容很大,为了提升整个系统的电源转换效率,就得降低各种损耗。在传统的集成电路系统中,MOS管的尺寸固定,在优化系统效率的时候,只有一个电流点的MOS管的损耗是最小的。假设这个最小MOS管的损耗的电流点为最大电流时,那么当系统负载变化,进入中载,或者轻载时,这个损耗将增大,系统效率必将降低。因此,有必要提供一种功率器件的驱动电路,可以根据负载电流的变化来调整MOS的尺寸,用以降低损耗。技术实现要素:本发明通过提供一种功率器件的驱动电路,能够根据负载电流的不同来调整功率器件MOS管的尺寸,以实现系统效率在不同的负载下效率能够达到多点优化,而不是目前的仅单点优化。根据本发明的一方面,提出了一种功率器件的驱动电路,该电路包括:驱动单元,所述驱动单元包括多个相互并联的驱动器,所述驱动单元依据驱动信号分别控制每一个驱动器的开闭;MOS分级单元,其输入端电性连接于所述驱动单元的输出端,所述MOS分级单元包括多个MOS晶体管,每个所述MOS晶体管均与一个所述驱动器串联,所述多个MOS晶体管的尺寸具有线性比例关系;比较单元,其输入端电性连接于所述MOS分级单元的输出端,所述比较单元用于比较流过所述MOS分级单元的负载电流与设定电流的大小关系,输出二进制信号;计数器,其输入端通信连接于所述比较单元的输出端,接收所述二进制信号,并依据所述二进制信号生成驱动信号,其输出端通信连接于所述驱动单元的输入端,将所述驱动信号传输至所述驱动单元。优选地,所述MOS晶体管的栅极连接于所述驱动单元的输出端,所述MOS晶体管的源极连接于地电位,所述MOS晶体管的漏极连接于所述比较单元的输入端。优选地,所述比较单元包括第一比较器和第二比较器,所述第一比较器的同相输入端和所述第二比较器的反向输入端连接于所述多个晶体管的漏极,用于获得MOS晶体管的漏源电压;所述第一比较器的反向输入端和所述第二比较器的同相输入端连接于稳压器,用于获取参考电压。优选地,基于所述MOS晶体管的漏源电压,表征所述负载电流。优选地,所述比较单元比较流过所述MOS分级单元的负载电流与设定电流的大小关系,输出二进制信号包括:当所述负载电流大于所述设定电流时,所述第一比较器输出的所述二进制信号为1,所述第二比较器输出的所述二进制信号为0;当所述负载电流小于所述设定电流时,所述第一比较器输出的所述二进制信号为0,所述第二比较器输出的所述二进制信号为1。优选地,所述计数器为加减计数器。优选地,所述MOS分级单元包括:所述MOS分级单元包括第一MOS晶体管、第二MOS晶体管和第三MOS晶体管,所述第一MOS晶体管、第二MOS晶体管和第三MOS晶体管的尺寸比例为1:2:4。根据本发明的另一方面,提出了一种功率器件的驱动方法,该方法包括如下步骤:开启功率器件的驱动电路,MOS分级单元以最小尺寸开始工作;利用比较器获得流过所述MOS分级单元的电流与设定电流的大小关系,并通过加减计数器来控制多个驱动器的开闭;基于所述多个驱动器的开闭,控制与其串联的MOS晶体管的通断来调整所述MOS分级单元的尺寸,使得所述MOS分级单元的损耗最小。优选地,所述MOS分级单元的损耗为所有的MOS晶体管的损耗之和。优选地,所述MOS晶体管的损耗包括开关损耗和导通损耗,表示为:Ploss=f×Cgs×Vgs2+Id2×Rdson(1)其中,Ploss表示为MOS晶体管的损耗;f为开关频率,Cgs为栅源电容,Vgs为栅源电压;Id为漏极电流,Rdson为导通源漏电阻,Cgs×Rdson=Z,Z为常数。本发明的有益效果在于:将流过MOS分级单元的电流与设定电流进行对比,并基于对比结果,通过加减计数器来控制多个驱动器的开闭,进而控制了与驱动器串联的MOS晶体管的通断,从而调整了MOS分级单元的尺寸,使得MOS分级单元的损耗最小,使得系统效率在不同的负载下效率能够达到多点优化。本发明的其它特征和优点将在随后具体实施方式部分予以详细说明。附图说明通过结合附图对本发明示例性实施方式进行更详细的描述,本发明的上述以及其它目的、特征和优势将变得更加明显,其中,在本发明示例性实施方式中,相同的参考标号通常代表相同部件。图1示出了根据本发明的一个实施例的功率器件的驱动电路原理图。图2示出了根据本发明的功率器件的驱动方法的流程图。具体实施方式下面将更详细地描述本发明的优选实施方式。虽然以下描述了本发明的优选实施方式,然而应该理解,可以以各种形式实现本发明而不应被这里阐述的实施方式所限制。相反,提供这些实施方式是为了使本发明更加透彻和完整,并且能够将本发明的范围完整地传达给本领域的技术人员。实施例1图1示出了根据本发明的一个实施例的功率器件的驱动电路原理图。如图1所示,根据本发明的功率器件的驱动电路包括:驱动单元101,驱动单元101包括多个相互并联的驱动器,驱动单元101依据驱动信号分别控制每一个驱动器的开闭;MOS分级单元102,其输入端电性连接于驱动单元101的输出端,MOS分级单元102包括多个MOS晶体管,每个MOS晶体管均与一个驱动器串联,多个MOS晶体管的尺寸具有线性比例关系;比较单元103,其输入端电性连接于MOS分级单元102的输出端,比较单元103用于比较流过MOS分级单元102的负载电流与设定电流的大小关系,输出二进制信号;计数器104,其输入端通信连接于比较单元103的输出端,接收二进制信号,并依据二进制信号生成驱动信号,其输出端通信连接于驱动单元101的输入端,将驱动信号传输至驱动单元101。该实施例通过提供一种功率器件的驱动电路,能够根据负载电流的不同来调整功率器件MOS管的尺寸,以实现系统效率在不同的负载下效率能够达到多点优化,而不是目前的仅单点优化。在一个示例中,MOS晶体管的栅极连接于驱动单元101的输出端,MOS晶体管的源极连接于地电位,MOS晶体管的漏极连接于比较单元103的输入端。具体地,MOS晶体管与驱动器是一一对应的,MOS晶体管的栅极连接到驱动单元101的输出端,通过控制驱动器的开闭即可控制MOS晶体管的通断,进而实现了对MOS分级单元102尺寸的调整。在一个示例中,比较单元103包括第一比较器C1和第二比较器C2,第一比较器C1的同相输入端和第二比较器C2的反向输入端连接于多个晶体管的漏极,用于获得MOS晶体管的漏源电压;第一比较器C1的反向输入端和第二比较器C2的同相输入端连接于稳压器,用于获取参考电压。具体地,晶体管的源极连接于地电位,第一比较器C1的同相输入端和第二比较器C2的反向输入端连接于多个晶体管的漏极,检测MOS管的漏源电压,比较器用于比较漏源电压和参考电压的大小。在一个示例中,基于MOS晶体管的漏源电压,表征负载电流。具体地,通过检测MOS管的漏源电压来检测负载电流的变化。在一个示例中,比较单元103比较流过MOS分级单元102的负载电流与设定电流的大小关系,输出二进制信号包括:当负载电流大于设定电流时,第一比较器C1输出的二进制信号为1,第二比较器C2输出的二进制信号为0;当负载电流小于设定电流时,第一比较器C1输出的二进制信号为0,第二比较器C2输出的二进制信号为1。具体地,当负载电流大于设定电流时,第一比较器C1输出的二进制信号为1,第二比较器C2输出的二进制信号为0,计数器104的控制输出端发出的新的驱动信号,驱动单元101根据驱动信号分别控制每一个驱动器的开闭,从而使得MOS分级单元102的尺寸增加;当负载电流小于设定电流时,第一比较器C1输出的二进制信号为0,第二比较器C2输出的二进制信号为1,计数器104的控制输出端发出的新的驱动信号,驱动单元101根据驱动信号分别控制每一个驱动器的开闭,从而使得MOS分级单元102的尺寸减小。在一个示例中,计数器104为加减计数器。具体地,加减计数器又叫可逆计数器,是可以进行正向和反向计数的计数器,从而可以调整输出的驱动信号的改变,从而调整MOS分级单元102尺寸的变化。在一个示例中,MOS分级单元102包括:MOS分级单元102包括第一MOS晶体管M1、第二MOS晶体管M2和第三MOS晶体管M3,第一MOS晶体管M1、第二MOS晶体管M2和第三MOS晶体管M3的尺寸比例为1:2:4。在图1中,驱动单元101包括3个驱动器,分别是第一驱动器N1、第二驱动器N2和第三驱动器N3,MOS分级单元102包括3个MOS晶体管,分别是第一MOS晶体管M1、第二MOS晶体管M2和第三MOS晶体管M3,MOS分级单元102的尺寸记为1,那么第一MOS晶体管M1占MOS分级单元102尺寸的比例为1/7,第二MOS晶体管M2为2/7,第三MOS晶体管M3为4/7,3个MOS晶体管可以将细分为7个均等的级别,第一驱动器N1的输出端连接第一MOS晶体管M1的栅极,第二驱动器N2的输出端连接第二MOS晶体管M2的栅极,第三驱动器N3的输出端连接第三MOS晶体管M3的栅极。本领域技术人员应当理解,本实施例中的比例及分级级数只是其中一个例子,可以此二进制的形式继续细化,比如4个MOS晶体管尺寸比例为为1:2:4:8,将MOS分级单元的尺寸分为15个级别,任何采用本发明中的方法,针对特定系统对比例进行优化的比例和分级数,也应该视为在本发明的保护之内。加减计数器有三个输出控制端,分别为Q1,Q2和Q3,分别与驱动信号G1,G2和G3对应,控制第一驱动器N1、第二驱动器N2和第三驱动器N3的通断,如表1所示。表1Q3\G3Q2\G2Q1\G1总的MOS尺寸可导通部分0001A/7M20011A/7M20102A/7M30113A/7M2,M31004A/7M41015A/7M2,M41106A/7M3,M4111AM2,M3,M4开启功率器件的驱动电路,MOS分级单元102以最小尺寸开始工作,如图1所示,此时加减计数器的输出为0,此时第一MOS晶体管在工作,第一MOS晶体管M1占MOS分级单元102尺寸的比例为1/7;利用比较器获得流过MOS分级单元102的负载电流与设定电流的大小关系,并通过加减计数器来控制多个驱动器的开闭,本领域技术人员应理解,上面检测电流的方法只是其中之一,其它任何检测电流的方法,如通过串联电阻,采样MOS等,都不影响本发明的实施;基于多个驱动器的开闭,控制与其串联的MOS晶体管的通断来调整MOS分级单元102的尺寸,使得MOS分级单元102的损耗最小。由实施例可以得出,除了通过调整MOS尺寸减小损耗、提高效率外,还有3个方面可以降低损耗,提高转换效率:1)在电流变小时,由于MOS尺寸变小,Rdson增大,那么,在开关管进行导通与关断时的直通损耗也将减小;2)由于每个驱动器都有可能被关断(每个周期都不导通),那么驱动他们的损耗也会减小,尤其是大功率的系统中,这几个驱动的自己损耗也是不小的;3)在大功率系统中,MOS的尺寸大,Rdson非常小,如10毫欧,其实,这10毫欧应该还包括MOS管的本征Rdson_int(比如5毫欧),金属连线的等效电阻Rm(比如5毫欧)。假设电流减半,Rdson加倍,如变成20毫欧,由于金属连线的等效电阻将不变,还是5毫欧,那么MOS管的本征Rdson_int将变成了15毫欧,那么,MOS管的面积不是只有原来一半,而是可以只要原来的三分之一,也就Cgs可以减小三分之一,这时减小驱动,那效果更可观。本实施例将流过MOS分级单元的电流与设定电流进行对比,并基于对比结果,通过加减计数器来控制多个驱动器的开闭,进而控制了与驱动器串联的MOS晶体管的通断,从而调整了MOS分级单元的尺寸,使得MOS分级单元的损耗最小,使得系统效率在不同的负载下效率能够达到多点优化。实施例2图2示出了根据本发明的功率器件的驱动方法的流程图。如图2所示,根据本发明的实施例,提供了一种功率器件的驱动方法,该方法包括如下步骤:步骤201,开启功率器件的驱动电路,MOS分级单元以最小尺寸开始工作;步骤202,利用比较器获得流过MOS分级单元的电流与设定电流的大小关系,并通过加减计数器来控制多个驱动器的开闭;步骤203,基于多个驱动器的开闭,控制与其串联的MOS晶体管的通断来调整MOS分级单元的尺寸,使得MOS分级单元的损耗最小。在一个示例中,MOS分级单元的损耗为所有的MOS晶体管的损耗之和。在一个示例中,所述MOS晶体管的损耗包括开关损耗和导通损耗,表示为:Ploss=f×Cgs×Vgs2+Id2×Rdson(1)其中,Ploss表示为MOS晶体管的损耗;f为开关频率,Cgs为栅源电容,Vgs为栅源电压;Id为漏极电流,Rdson为导通源漏电阻,Cgs×Rdson=Z,Z为常数。在此需要说明的是,漏极电流即为负载电流,下面提到的负载电流均是指漏极电流。Cgs×Rdson=Z是MOS晶体管的物理特性,结合公式(1)可得,当且仅当f×Cgs×Vgs2=Id2×Rdson的时候,Ploss可取得最小值。也就是说,在优化系统效率的时候,固定的MOS尺寸,只有一个电流点的Ploss是最小的,记这个最小的损耗为Ploss0,那么Ploss0=f×Cgs0×Vgs2+I02×Rdson0,那么当系统负载变化,进入中载,或者轻载时,这个损耗将增大,系统效率必将降低。因此,考虑提出一种功率器件的驱动方法,能够根据负载电流的不同来调整功率器件MOS管的尺寸。为了便于说明本发明的方法,我们通过检测MOS管的漏源电压Vds来检测负载电流的变化,而且调整MOS管尺寸的目标是维护Vds不变为一个常数。在传统的集成电路系统中,MOS管的尺寸固定,当负载电流变小为I1时,栅源电容和Rdson值不变,此时的损耗表示为:Ploss1a=f×Cgs0×Vgs2+I12×Rdson0(2)其中,f为开关频率;Cgs0为栅源电容;Vgs为栅源电压;Rdson0为漏极电流为I0时的导通源漏电阻。采用本发明提出的方法,负载电流变小为I1时,根据MOS晶体管的物理特性可得,此时的损耗为:Ploss1b=f×Cgs1×Vgs2+I12×Rdson1(3)其中,f为开关频率;Cgs1为栅源电容;Vgs为栅源电压;Rdson1为漏极电流为I1时的导通源漏电阻。根据MOS晶体管的物理特性,可得,Cgs0×Rdson0=Cgs1×Rdson1=Z(4)其中,Cgs0为漏极电流为I0时的栅源电容;Rdson0为漏极电流为I0时的导通源漏电阻;Cgs1为漏极电流为I1时的栅源电容;Rdson1为漏极电流为I1时的导通源漏电阻,Z为常数。将公式(4)代入到公式(3)中,可得:利用公式(2)和公式(5),比较这两个损耗,可得:令可得因为f×Cgs0×Vgs2=I02×Rdson0,所以两者之间的损耗差值Δ可化简为:其中,Δ为损耗差值,I0为负载电流;Rdson0为漏极电流为I0时的导通源漏电阻。由公式(8)可以看出,Δ≥0,当且仅当I1=I0时,Δ=0,也即本发明所采取的方法,损耗一定会小于传统的方法。如果MOS管的尺寸能够与每一个负载电流点,都能够有一个一一对应的尺寸,那么系统的效率将会在整个负载范围内,都能够得到一个最佳的效率。但是由于电路成本及MOS管设计的离散性,决定的MOS管的尺寸在实际设计中很难做成一个连续变化的,但是可以细分成几个级别,细分的级别越多,越可以近似都认为连续,实现最佳效率的负载点也就越多。本实施例将流过MOS分级单元的电流与设定电流进行对比,并基于对比结果,通过加减计数器来控制多个驱动器的开闭,进而控制了与驱动器串联的MOS晶体管的通断,从而调整了MOS分级单元的尺寸,使得MOS分级单元的损耗最小,使得系统效率在不同的负载下效率能够达到多点优化。本领域技术人员应理解,上面对本发明的实施例的描述的目的仅为了示例性地说明本发明的实施例的有益效果,并不意在将本发明的实施例限制于所给出的任何示例。以上已经描述了本发明的各实施例,上述说明是示例性的,并非穷尽性的,并且也不限于所披露的各实施例。在不偏离所说明的各实施例的范围和精神的情况下,对于本
技术领域:
的普通技术人员来说许多修改和变更都是显而易见的。当前第1页1 2 3