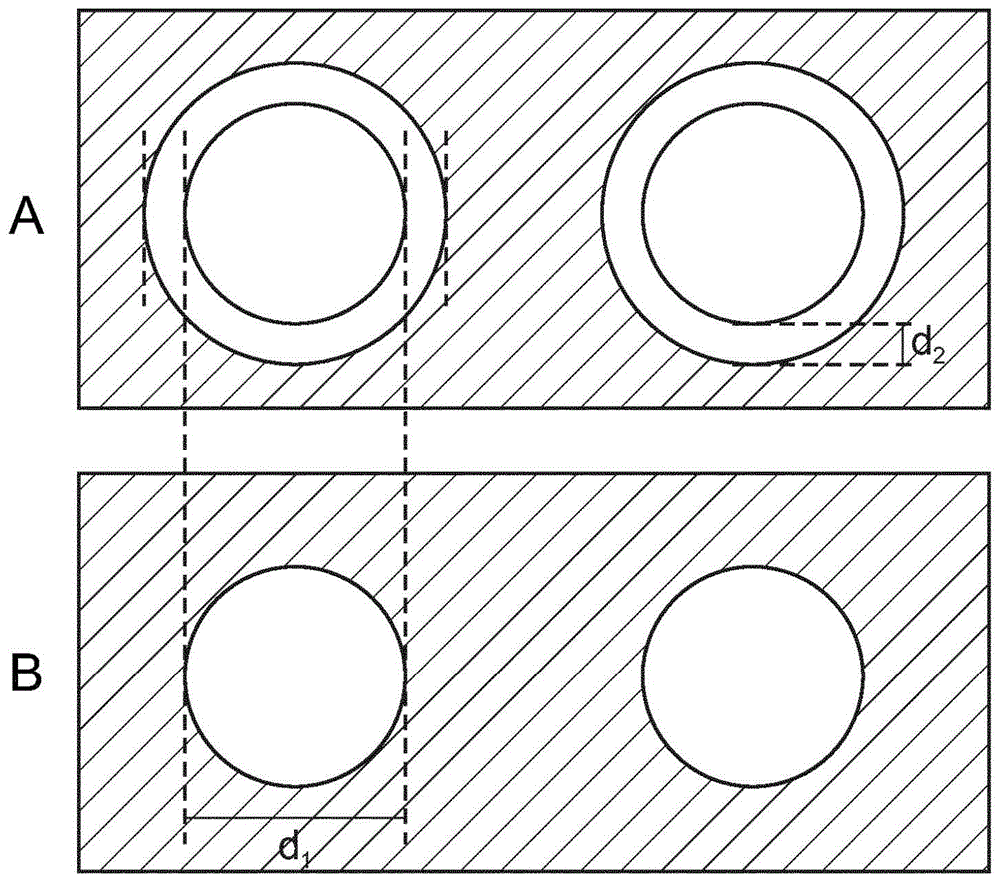
本发明涉及一种用于制造印刷电路板(pcb)的方法及一种印刷电路板。
背景技术:
:pcb为用于在其至少一个表面上安装例如集成电路(ic)、电阻器、开关等等的电气零件以便获得印刷电路板组合件(pcba)的薄板。在pcb的制造过程期间,通常在不导电、绝缘衬底/层上形成铜电路系统,所述衬底/层通常是由环氧树脂或聚酰亚胺树脂制成。最常见的不导电衬底/层为玻璃强化环氧树脂层压物,商业上被称为fr-4。为了获得多层pcb,通常形成不导电、绝缘衬底/层与其导电铜电路系统的堆叠以获得单件式产品。通常,在pcb制造期间(尤其是在制造多层pcb期间),利用永久性的两种特定类型的不导电、绝缘衬底/层:(i)前述不导电、绝缘衬底/层,也被称为堆积层、预浸体、内层、绝缘层等等,其在多层pcb内形成电路系统之间的不导电、绝缘衬底/层;及(ii)防焊剂(常常也被称作阻焊剂、外层等等),其在多层及非多层pcb中覆盖及保护最外电路系统。防焊剂在其聚合(也被称为固化或硬化)之后为完全聚合的永久性不导电材料层,其覆盖最外不导电衬底/层的表面及其大多数铜电路系统。防焊剂经图案化以完全地覆盖电路系统,但意图暴露以供焊接的铜电路系统的那些部分除外。在此类区域中,防焊剂通常展现开口,例如垫开口。通常,在第一步骤中,由光可成像组成物形成防焊剂,光可成像组成物涂覆至不导电衬底/层的表面以形成光可成像覆盖层。在第二步骤中,在使光可成像覆盖层于通常70℃至80℃的范围内的温度下短暂预聚合之后,通常将光可成像覆盖层曝光于光化辐射,光化辐射是借助于模板或原图而图案化。在曝光之后,在显影剂溶液(有机溶剂、水溶液或半水溶液)中使光可成像覆盖层显影,这会洗掉覆盖层的未曝光部分。然后,余留具有开口的光可成像覆盖层,其在通常150℃至200℃的范围内的温度下完全地聚合以形成不导电、完全聚合、图案化且永久性的防焊剂,所述防焊剂意图保护pcb的外表面上的电路系统达所述电路系统的整个使用期限。然后,使pcb经受焊接过程,且将金属或金属合金沉积至所述开口中。典型程序为借助于无电金属沉积而从含有金属的电解质当中进行金属沉积。通常沉积的金属为锡。然而,根据我们自己的实验,此类含有金属的电解质常常展示尤其在开口的边缘处渗入不导电、完全聚合、图案化且永久性的防焊剂的趋势。因此,在开口附近,金属有时沉积于防焊剂下方,主要在防焊剂与铜电路系统表面之间。假定开口周围的防焊剂与铜电路系统的相应铜表面之间的不充分粘着(及伴随的特定分层)为此渗入的原因。us5,484,688a在其说明书摘要中揭示“一种用于经结构化印刷电路板的图案化金属化物的方法,其中经完全结构化印刷电路板被覆盖有阻焊层,焊料接触部位保持敞开,阻焊层在使得发生以下情形的条件下被加热:尚未发生完全硬化且印刷电路板的铜表面几乎未氧化,在暴露的焊料接触部位处从水浴当中沉积金属,且在金属沉积操作之后将阻焊层加热足够长的时间以达到足够高的温度,使得整个阻焊层完全地硬化。不完全预硬化步骤防止溶液在金属化操作中渗入于阻焊层下方且由此松释其粘着”。us5,484,688a中所揭示的方法为两步骤方法,包含在焊接之前的防焊剂的预聚合步骤及在焊接之后的后聚合步骤,以便获得完全聚合、图案化且永久性的防焊剂。根据us5,484,688a中的技术方案7及8,“阻焊层[…][是]在金属沉积操作之前被加热”,分别“在排除氧的情况下”及“在保护性气体气氛下”。然而,在若干实际原因当中,两步骤热聚合非常不为pcb制造者所期望。第一,市售的防焊剂及防焊剂材料未被特性化及特定用于两步骤热聚合。因为防焊剂通常在单一热处理步骤中完全地聚合,所以对于相应预聚合及后聚合步骤未界定个别温度范围。此类额外规范对于各防焊剂必须被各自个别地实行及确定。第二,具有例如在自动化焊接过程中处置的仅预聚合防焊剂的pcb易遭受由例如输送机滚筒的机械硬/固体组件造成的刮痕及伤痕。防焊剂聚合(硬化)得越少,在自动化焊接过程期间损坏防焊剂的风险越高。这会容易增加有缺陷物品的数目。此外,防焊剂正变得越来越薄(例如层厚度为20μm或更小)且因此更易遭受机械缺陷。第三,由于水或其它溶剂的并入,未完全聚合的防焊剂趋向于增加其体积。此类所谓的后膨胀是不当的(且通常仅在防焊剂未完全地聚合时才会发生),尤其是对于细线电路系统,这是由于防焊剂中的开口的尺寸改变及非定域化。第四,两步骤热聚合通常需要用于预聚合的第一加热单元及用于后聚合的额外加热单元。然而,此类加热单元布置是不当的,这是由于额外成本及流线化原因。wo2009/125845a1揭示一种用于制造柔性配线板的方法。在所述方法中,在氧浓度不大于1体积%的气氛下执行用于使构成聚酰亚胺层的聚酰亚胺化合物与交联剂反应的热处理,在聚酰亚胺层上已通过曝光及碱性显影处理而形成预定图案。在不大于1体积%的极低氧含量中的热处理可防止不仅在导体电路的暴露表面中的颜色改变,而且在导体与聚酰亚胺层之间的界面中的颜色改变,且可防止聚酰亚胺层在镀敷之后发生上升。为了另外增加防焊剂与铜电路系统表面之间的粘着,各种铜表面处理(有时也被称为增加剥落强度的表面处理)为我们所知。在wo2012/005722a1的技术方案1中,“[揭示]处理金属表面以促进金属表面与有机材料之间的粘着的方法,其特征在于:在金属表面上形成金属氧化物层,且通过金属氧化物与表面改性剂化合物之间的自限制反应来控制金属氧化物层的形成”。此反应包含铜表面的氧化及后续还原反应。根据实例2及5,此反应分别应用于堆积层及防焊剂。然而,所述堆积层及防焊剂的聚合是在存在环境空气的情况下实行。相似于防焊剂应用,在多层pcb制造期间发生分层趋势及粘着问题且其针对堆积层应用已被观测到。简单地说,通过交替地堆叠堆积层及铜电路系统来形成多层pcb。堆积层将铜电路系统彼此电气绝缘且此外提供稳定性。然而,在明确界定的位置处形成通孔,其使一个层的电路系统与其它层的一个或多于一个电路系统电气连接。此类通孔是例如通过使用激光、等离子体、光方法或常规钻孔而形成。通常,堆积层被真空层压至相应不导电衬底/层上且覆盖所述衬底/层的铜电路系统。堆积层随后被按压且经受第一热处理步骤以获得充分预聚合的堆积层。通常应用170℃至200℃的范围内的温度达大约30分钟。常见的是在具有热清洁空气的烘箱中,即,在存在分子氧的情况下应用此热处理。在所述第一热处理步骤之后,预聚合的堆积层处于用于图案化,尤其是用于通孔形成的条件下。然后,堆积层的表面及通孔表面通常被去污且基本上处于用于在多层pcb中形成下一铜电路系统的条件下。实行形成下一铜电路系统的过程,例如借助于以下各者:(i)减色过程,通常始于层压铜箔;(ii)半加成过程(sap)或高级修改半加成过程(amsap),通常始于无电沉积的铜层;及(iii)全加成过程(fap),始于形成用于选择性地沉积铜的临时、经结构化光阻层。在这些过程之中,通常应用sap,尤其是用于制造高密度pcb。在sap中,在第二热处理步骤之前将铜层无电沉积至堆积层表面上,第二热处理步骤通常是在100℃至150℃的范围内的温度下实行达至少30分钟(常常也被称作干燥步骤)。在此热处理步骤中,将热应用于预聚合、铜镀敷的堆积层。在下一步骤中,将临时、光敏性不导电材料层(光阻层)形成至无电沉积的铜层上,随后图案化以形成开口,且固化。然后,将额外铜沉积至开口中。在最后步骤中,移除临时、光敏性层及残余铜层。因此,形成了下一层的铜电路系统。必需的是,在多层pcb的使用期限期间不发生分层。因此,期望铜电路系统与堆积层之间的粘着尽可能地高且在pcb的使用期限期间余留。根据我们自己的实验,堆积层有时遭受以下缺点:不充分粘着会在铜表面与堆积层之间的界面处引起分层,在应力测试之后形成凸泡,且在盲微通孔(bmv)附近形成楔形空隙。技术实现要素:因此,本发明的目标是克服前述缺点,尤其是提供一种用于制造pcb的改善型方法,其-可在多层pcb中同等地应用于两种类型的永久性及不导电覆盖层,即,防焊剂及堆积层,-防止金属渗入于永久性及不导电覆盖层与铜表面之间,且同时-增加(改善)铜表面与覆盖层之间的粘着,尤其是在使用极薄覆盖层的情况下,且通常-较快、较不复杂且较可靠(例如引起制造缺陷较少的物品)。具体实施方式前述目标是通过一种用于制造印刷电路板的方法而解决,所述方法包括按下列次序的步骤:(i)提供不导电衬底,其在至少一个表面上具有-铜电路系统,其具有铜表面,其中所述铜表面是-通过(a)氧化及后续还原反应及/或(b)附着至所述铜表面的有机化合物予以化学处理,-永久性、不导电、未完全聚合的覆盖层,其至少部分地覆盖所述铜表面,(ii)在140℃至250℃的范围内的温度下于某一气氛中热处理具有所述永久性、不导电、未完全聚合的覆盖层的所述衬底,所述气氛含有以所述气氛的总体积计为100000ppm或更小的量的分子氧,使得获得具有永久性、不导电覆盖层的衬底,所述覆盖层相较于步骤(i)更多地聚合,限制条件为:-在步骤(i)之后,但在将任何金属或金属合金沉积至所述永久性、不导电、未完全聚合的覆盖层上之前,实行步骤(ii),且-在步骤(ii)中,如果所述覆盖层为防焊剂,那么在仅一个单一热处理步骤中完全地聚合所述永久性、不导电、未完全聚合的覆盖层。我们自己的实验已展示出,本发明的方法(如贯穿本文所定义)在防焊剂应用中赫然防止渗入(尤其是锡渗入),且在经受高度加速应力测试(hast,96小时,130℃,85%rh)之后的堆积层应用中显著地引起良好的粘着。假定本发明的方法在最大可能程度上防止在制造pcb期间的铜电路系统的铜表面的氧化。根据本发明的方法的步骤(i),提供不导电衬底。在所提供的不导电衬底的至少一个表面上,所述衬底具有-铜电路系统,其具有铜表面,及-永久性、不导电、未完全聚合的覆盖层,其至少部分地覆盖所述铜表面。此外,所述铜表面为经化学处理的铜表面。换句话说,具有此类铜表面的所提供的不导电衬底已经展现此经化学处理的铜表面,所述铜表面被至少部分地覆盖有所述覆盖层。此类经化学处理的铜表面的特征为铜表面的表面改性,被表达为精细且薄的化学处理层,其分别对覆盖层增加粘着及剥落强度。如果化学处理包含氧化及后续还原反应(在本发明的方法中被称作(a)),那么铜表面中的第一层铜原子被转化。通常,转化是自限制的。如果化学处理个别地或另外包含附着有机化合物的化学处理(在本发明的方法中被称作(b)),那么有机化合物层直接附着至铜表面的铜原子或在(a)之后获得的氧化且随后还原的铜原子/铜离子。化学处理层包含经转化铜原子及有机化合物层两者。通常,包含经转化铜原子及/或所述有机化合物的化学处理层可通过以下各者予以研究、分析及测量:傅立叶变换红外光谱法(ft-ir)、聚焦离子束高分辨率扫描电子显微法(fib高分辨率sem)、x射线光电子光谱法(xps),及穿透电子显微法(tem)。优选地,在相应样本的竖直横截面中实行分析。更优选地,借助于fib高分辨率sem来测定化学处理层厚度。然而,在一些状况下,优选的是制造相应衬底,这意味着如针对步骤(i)所定义的化学处理是作为本发明的方法的部分而实行。在此状况下,根据本发明的用于制造印刷电路板的方法是优选的,其包括按下列次序的步骤:(i)提供不导电衬底,其在至少一个表面上具有-铜电路系统,其具有铜表面,包含以下子步骤:(i-a)通过(a)氧化及后续还原反应及/或(b)有机化合物来化学处理所述铜表面,从而将所述化合物附着至所述铜表面,(i-b)运用永久性、不导电、未完全聚合的覆盖层来至少部分地覆盖在(i-a)之后获得的所述铜表面,(ii)在140℃至250℃的范围内的温度下于某一气氛中热处理具有所述永久性、不导电、未完全聚合的覆盖层的所述衬底,所述气氛含有以所述气氛的总体积计为100000ppm或更小的量的分子氧,使得获得具有永久性、不导电覆盖层的衬底,所述覆盖层相较于步骤(i-b)更多地聚合,限制条件为:-在步骤(i-b)之后,但在将任何金属或金属合金沉积至所述永久性、不导电、未完全聚合的覆盖层上之前,实行步骤(ii),且-在步骤(ii)中,如果所述覆盖层为防焊剂,那么在仅一个单一热处理步骤中完全地聚合所述永久性、不导电、未完全聚合的覆盖层。换句话说,本发明的方法是优选的,其中步骤(i)进行以下操作:(i)提供不导电衬底,其在至少一个表面上具有-铜电路系统,其具有铜表面,(i-a)通过(a)氧化及后续还原反应及/或(b)有机化合物来化学处理所述铜表面,从而将所述化合物附着至所述铜表面,(i-b)运用永久性、不导电、未完全聚合的覆盖层来至少部分地覆盖在(i-a)之后获得的所述铜表面。优选地,在步骤(i-a)之前,在清洁步骤中清洁铜表面,更优选地在蚀刻清洁步骤中清洁铜表面。在此类蚀刻清洁步骤中,优选地使用清洁溶液,其优选地含有一种或多于一种酸及/或一种或多于一种氧化剂。优选地,使用无机酸与过氧化氢的混合物。优选的无机酸为硫酸。在步骤(i)(包含上述子步骤(i-a)及(i-b))之后,铜电路系统由于处理步骤而展现包括化学处理层的铜表面。步骤(i)中的术语“氧化及后续还原”是指基于氧化反应及后续还原反应的化学转化过程及其转化产物。如果在本发明的方法的步骤(i)中存在/实行(a)及(b)两者,那么首先实行(a),即,在(b)之前。因此,如果实行(a)及(b),那么根据(b)的有机化合物主要附着至铜,铜处于主要还原状态下。优选地通过选自由以下各者组成的群组的一种或多于一种氧化剂来实行氧化反应:绿泥石,包含亚氯酸;次氯酸盐,包含次氯酸;过氧化物,包含过氧化氢;高锰酸盐;过氯酸盐,包含过氯酸;过硫酸盐,包含过氧化单硫酸盐、过氧二硫酸盐及其相关酸;及臭氧。优选地通过选自由有机还原剂及无机还原剂组成的群组、优选地选自由以下各者组成的群组的一种或多于一种还原剂来实行还原反应:醛,包含甲醛;硼氢化物;硼烷;及经取代的硼烷。在氧化反应之后,铜主要以氧化数+2而存在;在还原反应之后主要以氧化数0而存在,但由于cu-(0)的立即再氧化,特定量的呈氧化数+1的铜是不可避免的。然而,呈氧化数0的铜是优选的。因此,含有呈氧化数0及+1的铜的混合物通常在还原反应之后存在于化学处理层中。因此,本发明的方法(如上文所定义,优选地如定义为优选的)是优选的,其中在步骤(i)(a)中,通过以下操作来化学处理所述铜表面:将cu-(0)氧化成cu-(i)及cu-(ii)且随后在所述铜表面中还原所述cu-(i)及cu-(ii),使得产生cu-(0)。如之前所提及,在还原反应之后,主要产生cu-(0)。含有呈氧化数±0及+1的铜的混合物形成化学处理层或化学处理层至少含有所述混合物。术语“后续”/“随后”表示在氧化反应之后基本上立即的还原反应。在一些状况下,优选的是在还原反应之前包含冲洗或调节步骤。在(a)之后获得无蚀刻的表面粗化(也被称为非蚀刻表面粗化)。尽管有此粗化效应,但相较于常规蚀刻方法,表面相对光滑,常规蚀刻方法通常引起极明显的表面粗化或甚至引起表面毁坏;通常包含更改导体形貌。相反地,(a)中所定义的铜表面改性在深度上通常不会超过200纳米且因此被称作纳米结构化表面或纳米经结构化表面。因此,本发明的方法(如上文所定义,优选地如定义为优选的)是优选的,其中步骤(i)中的铜表面包括铜表面上的化学处理层,其中90%或更大的处理层的厚度为500nm或更小,优选地为300nm或更小,更优选地为180nm或更小,甚至更优选地为150nm或更小,最优选地,90%或更大的处理层的厚度在50nm至100nm的范围内。优选地,这些参数是在处理层的竖直横截面中测定。在此类横截面中,处理层的面积是优选地通过积分而测定,其中以横截面中的处理层的总面积计,90%或更大的面积对应于未超过例如500nm的层厚度。本发明的方法(如上文所定义,优选地如定义为优选的)是甚至更优选的,其中步骤(i)中的所述铜表面包括所述铜表面上的化学处理层,所述处理层的最大厚度为500nm或更小,优选地为300nm或更小,更优选地为180nm或更小,甚至更优选地为150nm或更小,最优选地,所述处理层的最大厚度在20nm至100nm的范围内。如果存在/实行(a),那么本发明的方法(如上文所定义,优选地如定义为优选的)是优选的,其中氧化且随后还原的铜表面展现经转化铜层,其最大层厚度为200nm或更小,优选地为160nm或更小,更优选地,其最大层厚度为120nm或更小,甚至更优选地,其最大层厚度为100nm或更小,最优选地,其最大层厚度为50nm或更小。根据我们自己的实验,此类纳米经结构化表面提供各种优点。用于高频应用中的pcb得益于此类比较光滑的表面,这是由于减低的信号损耗。此外,相较于常规的严苛蚀刻方法,铜表面上仅微量的金属铜涉及到转化反应,从而导致电路系统中的金属铜的损耗减低。另外,获得了极好的粘着。因此,在本发明的方法中,优选的是实行至少(a),更优选地为(a)及(b)。根据(b),将有机化合物附着至铜表面。“经附着(attached)”,相应地,“附着(attaching)”,意思是形成络合物、粘着、吸附,使得获得有机化合物与铜表面的物理化学键合。因此,经附着的有机化合物不能容易通过在常见的冲洗及清洗条件下的冲洗或清洗而移除。本发明的方法(如上文所定义,优选地如定义为优选的)是优选的,其中附着至铜表面的有机化合物为粘着促进剂及/或与cu-(i)形成络合物的化合物,优选地为硅烷基粘着促进剂及/或与cu-(i)形成络合物的化合物。本发明的方法(如上文所定义,优选地如定义为优选的)是优选的,其中所述有机化合物为选自由以下各者组成的群组的一种或多于一种化合物:唑、硅烷、唑-硅烷-混成物,及其组合。这包含多于一种唑的混合物、多于一种硅烷的混合物、含有一种或多于一种唑及一种或多于一种硅烷的混合物。唑-硅烷-混成物为例如唑部分与硅烷部分的共价连接(也被称为硅烷化唑)。步骤(i)包含至少部分地由永久性、不导电、未完全聚合的覆盖层覆盖的铜表面,这意味着铜表面优选地与所述覆盖层层压。相应层压过程通常是在真空及常常显著地低于140℃的上升温度下实行。优选的是本发明的方法(如上文所定义,优选地如定义为优选的),其中步骤(i)中的所述永久性、不导电、未完全聚合的覆盖层是选自由防焊剂及堆积层组成的群组,优选地为防焊剂。因此,在一些状况下,本发明的方法是优选的(如上文所定义,优选地如定义为优选的),其中步骤(i)中的永久性、不导电、未完全聚合的覆盖层为防焊剂,优选地为如贯穿本文所描述的防焊剂。然而,在其它状况下,本发明的方法是优选的(如上文所定义,优选地定义为优选的),其中步骤(i)中的永久性、不导电、未完全聚合的覆盖层为堆积层,优选地为如贯穿本文所描述的堆积层。术语“至少部分地覆盖”表示:在一些状况下,铜表面的相异区域未被覆盖,以便形成开口,例如接触垫。这在覆盖层为防焊剂的情况下尤其适用。因此,在一些状况下,本发明的方法(如上文所描述,优选地如描述为优选的)是优选的,其中步骤(i)中的永久性、不导电、未完全聚合的覆盖层展现暴露铜表面的区域的开口。然而,优选的是大部分铜表面是由覆盖层覆盖,优选地,至少80%的铜表面是由覆盖层覆盖。术语“永久性”表示在本发明的方法期间或在本发明的方法之后并不意图移除整个覆盖层。覆盖层并非临时覆盖层,而是最优选地保持达pcb的整个使用期限。然而,所述术语并不排除永久性覆盖层的不同的临时条件。在一些状况下,优选的是通过本发明的方法(如上文所描述的方法,优选地如描述为优选的)而制造的印刷电路板为多层印刷电路板。在此状况下,在本发明的方法的第一循环中,步骤(i)中的永久性、不导电、未完全聚合的覆盖层为堆积层,其在本发明的方法的后续第二循环中形成步骤(i)的不导电衬底的基础。因此,本发明的方法(如上文所描述,优选地如描述为优选的)是优选的,其中步骤(i)中的永久性、不导电、未完全聚合的覆盖层为堆积层,优选地为无铜层的堆积层,更优选地为无金属层的堆积层。为了在后续第二循环中针对步骤(i)形成在至少一个表面上具有铜电路系统的不导电衬底,使无铜层的堆积层在第一循环的步骤(ii)之后经受铜金属化过程,以便形成具有铜表面的相应铜电路系统。此类步骤序列对于半加成过程是典型的,且我们自己的实验已展示出本发明的方法在此类步骤序列中尤其有益。相较于含有金属层的堆积层,无金属层的堆积层通常更易遭受氧渗透。在后一状况下,金属层通常减低通过堆积层的氧渗透且因此自然地减低在后续热处理步骤期间的铜表面上的铜氧化的风险。因此,本发明的方法在无金属层的堆积层的状况下有利地减低铜表面上的铜氧化的风险且显著地增加粘着属性(对于关于铜氧化的其它细节,参见下文)。如本发明的方法的步骤(i)中所定义的不导电衬底在一些状况下优选地为核心衬底,其通常为堆积多层pcb的基础及起点。通常,核心衬底包括玻璃布强化纤维材料及在外部上的铜层。优选地,此类核心衬底另外包括选自由以下各者组成的群组的一群或多于一群填料粒子:sio2、al2o3、tio2、zro2。此类核心衬底并非堆积层。优选地,在本发明的方法中,步骤(i)中的覆盖层不包括填料纤维,优选地不包括玻璃纤维。代替地,本发明的方法(如上文所描述,优选地如描述为优选的)是优选的,其中根据步骤(i)的覆盖层包括填料粒子,优选地为选自由以下各者组成的群组的一群或多于一群填料粒子:sio2、al2o3、tio2、zro2,最优选地为sio2。本发明的方法(如上文所描述,优选地如描述为优选的)是优选的,其中步骤(i)中的所述永久性、不导电、未完全聚合的覆盖层独立地为干膜或液体。术语“独立地”表示:举例来说,如果在制造pcb期间使用多于一个覆盖层,那么堆积层可被用作干膜,但防焊剂可被提供为液体。所属领域技术人员知道,在此上下文中的液体覆盖层并非完全地为液体,但展现在此
技术领域:
中是典型的特定粘度。同样地,所属领域技术人员知道,干膜并非完全地干燥,而是含有特定量的典型溶剂。根据本发明的方法(如上文所定义,优选地定义为优选的)是优选的,其中步骤(i)中的覆盖层为干膜防焊剂或液体防焊剂。通常,在所属领域中同等地利用干膜防焊剂以及液体防焊剂。如果步骤(i)中的覆盖层为堆积层,那么根据本发明的方法(如上文所定义,优选地定义为优选的)是优选的,其中步骤(i)中的覆盖层为干膜堆积层。后者包含例如光可成像电介质(pid)作为堆积层,其被光结构化。然而,还已开发了液体堆积层且其可应用于本发明的方法中。通常,防焊剂是透明的。这允许所属领域技术人员快速地且定性地确定防焊剂下方的铜表面的氧化。在不存在氧化的情况下观测到典型的金属铜色,其中在存在氧化的情况下观测到典型的深色/深棕色。因此,根据本发明的方法(如上文所定义,优选地定义为优选的)是优选的,其中步骤(i)中的永久性、不导电、未完全聚合的覆盖层是透明的。通常,堆积层不是透明的。然而,作为堆积层的前述光可成像电介质展现至少特定程度的透明度,其可用以确定铜表面的氧化。根据本发明的方法(如上文所定义,优选地定义为优选的)是优选的,其中步骤(i)中的所述永久性、不导电、未完全聚合的覆盖层的层厚度为50μm或更小,优选地为40μm或更小,更优选地为33μm或更小,甚至更优选地为28μm或更小,最优选地为22μm或更小。如果覆盖层为堆积层,那么根据本发明的方法是优选的,其中步骤(i)中的堆积层的层厚度为50μm或更小,优选地为33μm或更小,更优选地为21μm或更小,甚至更优选地为15μm或更小,最优选地为10μm或更小。如果覆盖层为防焊剂,那么根据本发明的方法是优选的,其中步骤(i)中的防焊剂的层厚度为50μm或更小,优选地为40μm或更小,更优选地为33μm或更小,甚至更优选地为28μm或更小,最优选地为22μm或更小。我们自己的实验展示出,展现层厚度为30μm或更小,尤其为20μm或更小的防焊剂以及堆积层在热处理步骤期间非常易遭受氧渗透。因此,本发明的方法尤其有益于极薄覆盖层,尤其是低于30μm。在许多状况下,防焊剂以及堆积层含有环氧化合物。通常,这些化合物在步骤(ii)时经历剧烈的结构改变,从而导致在步骤(ii)之后获得的覆盖层更多地聚合或甚至完全地聚合。因此,根据本发明的方法(如上文所定义,优选地定义为优选的)是优选的,其中步骤(i)中的所述永久性、不导电、未完全聚合的覆盖层包括环氧化合物。然而,在一些状况下,本发明的方法(如上文所定义,优选地定义为优选的)是优选的,其中步骤(i)中的覆盖层为包括至少一种化合物的堆积层,所述化合物是选自由以下各者组成的化合物的群:环氧化合物、聚酰亚胺、氰酸酯、双马来酰亚胺-三嗪化合物、聚丙烯醚及聚烯烃,优选地,步骤(i)中的覆盖层为包括环氧化合物的堆积层。通常且在所属领域中常见的是,在环境空气(即,具有大约78体积%的氮及大约21体积%的氧的环境气氛,其等于以环境空气的总组成物计为210000ppm的氧)下实行防焊剂及堆积层的聚合。氧为环境空气的普遍的氧化化合物,其在热处理步骤期间造成不当的铜氧化。假定此不当的氧化会显著地减低铜表面与防焊剂/堆积层之间的粘着。此外,经氧化的铜促进渗入。因此,在本发明的方法中,用于步骤(ii)中的气氛含有以所述气氛的总体积计为100000ppm(10体积%)或更小的量的分子氧。这包含没有其它不当的氧化化合物以不当的量而存在。步骤(ii)中的所述气氛为低反应性且非常优选地为惰性的气氛。因此,本发明的方法(如上文所定义,优选地定义为优选的)是优选的,其中所述气氛中的分子氧的所述量为50000ppm(5体积%)或更小,优选地为10000ppm(1体积%)或更小,更优选地为1000(0.1体积%)ppm或更小,甚至更优选地为100ppm(0.01体积%)或更小,最优选地为10ppm(0.001体积%)或更小,甚至最优选地为5ppm(0.0005体积%)或更小。优选的是本发明的方法(如上文所定义,优选地定义为优选的),其中步骤(ii)中的所述气氛为惰性气体,优选地为选自由以下各者组成的群组的惰性气体:氮、二氧化碳、稀有惰性气体及其混合物;更优选地为选自由以下各者组成的群组的惰性气体:氮、二氧化碳、氦、氩及其混合物;最优选地,所述惰性气体为氮。更优选地,气氛为气态氮,其中以气氛的总体积计,氮含量大于99.0体积%,优选地,氮含量大于99.5体积%,更优选地,氮含量大于99.8体积%,甚至更优选地,氮含量大于99.9体积%,最优选地,氮含量大于99.99体积%。在一些状况下,根据本发明的方法(如上文所定义,优选地如定义为优选的)是优选的,其中根据步骤(ii)的气氛替代地为真空。在此类状况下,环境空气被抽空,而非由一种或多于一种惰性气体替换。真空的总体积形成气氛。然而,在本发明的方法中,应用一种或多于一种惰性气体是优选的。因此,在一些状况下,优选的是在本发明的方法的步骤(ii)中不应用真空。优选的是本发明的方法(如上文所定义,优选地定义为优选的),其中步骤(ii)中的所述温度在142℃至220℃的范围内,优选地在145℃至210℃的范围内,更优选地在150℃至205℃的范围内。根据我们自己的实验,上述优选温度针对覆盖层、防焊剂以及堆积层提供最佳聚合。优选地,将如上文所描述的温度及气氛应用于合适的烘箱或固化装置中。通常,烘箱及固化装置分别在本发明的步骤(ii)中测定气氛的总体积。如果覆盖层为防焊剂,那么防焊剂在本发明的方法的步骤(ii)中于一个单一步骤中完全地聚合。这意味着热驱动聚合不中断。换句话说,完全聚合是在仅一个单一热处理步骤(单步骤聚合)中实行。此外,这意味着运用焊料金属或焊料金属合金的金属化是在防焊剂完全地聚合之后实行。如果覆盖层为堆积层,那么通常期望在后续(例如第二)热处理步骤中完全地聚合堆积层。然而,术语“相较于步骤(i)更多地聚合”意味着获得至少显著的聚合增加,优选地至少在通过较少聚合的堆积层的分子氧渗透显著地缩减且后续金属化可安全地实行的程度上。本发明的方法(如上文所定义,优选地定义为优选的)是优选的,其中步骤(ii)实行达至少10分钟,优选地达至少20分钟,更优选地达至少30分钟。小于10分钟的热处理常常会产生相较于步骤(i)不充分地聚合的永久性、不导电覆盖层。此类不充分聚合常常会在后续制造步骤期间于覆盖层中造成机械缺陷。根据本发明的方法(如上文所描述,优选地如描述为优选的)是优选的,其中步骤(ii)实行高达180分钟,优选地高达120分钟,更优选地高达90分钟。超过180分钟的热处理在大多数状况下不是必要的。在180分钟之后,聚合对于其它制造步骤(例如对于堆积层)是充分的,或覆盖层完全地聚合,且因此不能实现进一步聚合(例如对于防焊剂)。尤其优选的是根据本发明的方法(如上文所描述,优选地如描述为优选的),其中步骤(ii)实行达20至180分钟,优选地达20至150分钟。根据我们的实验,本发明的方法相较于在存在环境空气的情况下实行但在其它方面与本发明的方法相同的方法提供了显著的粘着增加。粘着常常是通过剥落强度测试而定量。优选的剥落强度测试被描述于下文的实例章节中。在此类测试中,测定为了将覆盖层与铜表面分离所需要的强度。优选的是根据本发明的方法(如上文所描述,优选地如描述为优选的),其中用于将覆盖层与铜表面分离的剥落强度(优选地在如贯穿本文所定义的hast条件之后)相较于用于相同地将此类覆盖层与相应铜表面分离的剥落强度增加了至少10%,至相应铜表面上的覆盖层是获自步骤(ii)中在存在环境空气的情况下实行但在其它方面与本发明的方法相同的方法,优选地增加了至少30%,更优选地增加了至少50%,甚至更优选地增加了至少70%,最优选地增加了至少100%。对于此类剥落强度测试,考虑由铜表面与覆盖层之间的界面引起的剥落强度。优选的是本发明的方法(如上文所定义,优选地定义为优选的)另外包括在步骤(ii)之后的以下步骤:(iii)将一种或多于一种金属或金属合金至少部分地沉积至(a)所述覆盖层或(b)未由所述覆盖层覆盖的所述铜表面上。如果本发明的方法中的覆盖层为防焊剂,那么铜表面未由防焊剂完全地覆盖。通常,防焊剂含有提供对铜电路系统的铜表面的界定区域的接近的开口。这些开口随后被填充有焊料金属,最优选地为锡,以便产生用于将铜电路系统与电气零件电气连接的接触垫。本发明的方法(如上文所定义,优选地定义为优选的)是优选的,其中将一种或多于一种金属或金属合金沉积至未由覆盖层覆盖的铜表面上是在防焊剂完全地聚合之后实行。如果本发明的方法中的覆盖层为堆积层,那么优选地利用无金属层的堆积层(参见上文)。在此状况下,金属晶种层、优选地为钯晶种层在步骤(iii)中沉积至在步骤(ii)之后获得的经热处理的堆积层上。因此,金属晶种层的沉积是在步骤(ii)之后执行。此类金属晶种层优选地为用于铜的无电沉积的起点。在其它步骤序列中,铜电路系统形成于堆积层上。因此获得在至少一个表面上具有铜电路系统的不导电衬底,铜电路系统具有铜表面,不导电衬底已准备用于如本发明的方法的步骤(i)中所定义的化学处理。在一些状况下,堆积层的完全或彻底聚合优选地是在金属晶种层被沉积或整个铜电路系统被形成之后实行。在此优选状况下,堆积层的完全或彻底聚合是在含有一定量的分子氧的气氛中执行,如本发明的方法的步骤(ii)中所定义,或在含有环境空气的气氛中执行。堆积层在存在环境空气的情况下的此类完全或彻底聚合未必是有害的。已通过本发明的方法而获得的高度聚合显著地防止了分子氧迁移。此外,由于金属层沉积至堆积层上而另外显著地防止了所述分子氧迁移。优选的是本发明的方法(如上文所定义,优选地定义为优选的),其中一种或多于一种金属独立地为选自由以下各者组成的群组的金属:锡、镍、金、钯、铜及银;相应地,一种或多于一种金属合金独立地包括选自由以下各者组成的群组的金属:锡、镍、金、钯、铜及银。如果步骤(i)中的覆盖层为堆积层,那么一种或多于一种金属独立地为选自由钯及铜组成的群组的金属,相应地,一种或多于一种铜合金独立地包括选自由钯及铜组成的群组的金属。如果步骤(i)中的覆盖层为防焊剂,那么一种或多于一种金属独立地为选自由以下各者组成的群组的金属,相应地,一种或多于一种铜合金独立地包括选自由以下各者组成的群组的金属:锡、镍、金、钯及银,更优选地选自由锡及镍组成的群组。本发明的方法的益处为未观测到前述金属的渗入,尤其是锡的渗入。这是值得注意的,这是因为锡作为焊接金属的沉积会需要严苛条件且容易引起渗入。本发明的方法利用由经化学处理的铜表面(即,增加剥落强度的表面处理)及在气氛中的后续热处理的组合引起的极好的粘着,所述气氛含有以所述气氛的总体积计为100000ppm或更小的量(优选地更小,更优选地如上文针对本发明的方法所定义)的分子氧。我们的实验结果展示出此组合出人意料地产生了协同效应(参见实例章节)。尤其对于极薄覆盖层,本发明的方法展示了出人意料地良好的结果。印刷电路板为高度复杂的电子零件且需要满足高标准及需求。根据我们的实验,根据本发明的方法(如上文所定义,优选地定义为优选的)而制造的印刷电路板尤其在常见的hast(96小时,130℃,85%rh,参见实例章节)中展示了极好的结果。本发明的方法(如上文所定义,优选地定义为优选的)用于制造印刷电路板。如上文所提及,获得了覆盖层与铜表面之间的极好的粘着。此外,对于防焊剂及堆积层未观测到渗入。因此,本发明还涉及一种印刷电路板,其包括-不导电衬底,其在至少一个表面上具有铜电路系统,所述铜电路系统具有铜表面,其中所述衬底的所述表面及所述铜表面被至少部分地覆盖有防焊剂,所述防焊剂是-透明的,且-层厚度为20μm或更小,优选地为15μm或更小,最优选地为10μm或更小,其中在所述防焊剂下方的所述铜表面-为金属铜色,且-展现最大层厚度为200nm或更小的经转化铜层。关于本发明的方法的前述特征同样地适用于本发明的印刷电路板(如上文所定义)。术语“金属铜色”表示金属铜的典型亮色,但不为氧化铜的典型颜色,其为显著深褐色。所属领域技术人员能够区分在防焊剂下方的金属铜及氧化铜。通过以下非限制性实例来进一步阐释本发明。实例a:防焊剂应用:样本制备样本1至6(各自包括若干相同试样)被制备如下(对于概述,另外参见以下表1):步骤(i):提供不导电衬底,其在至少一个表面上具有铜电路系统,铜电路系统具有铜表面:使用铜箔(150mm×75mm×35μm)来表示在至少一个表面上具有的铜电路系统具有铜表面的不导电衬底。清洁铜表面:在第一步骤中,通过使用硫酸/h2o2溶液来蚀刻清洁所有铜箔的铜表面,所述溶液含有180ml/lsoftcleanuc168、200ml/lcupraetch起始剂、75ml/lhydrox(全部为atotech的产品),及545ml/l去离子水,以获得经蚀刻清洁的铜箔。蚀刻清洁会移除重氧化物及其它化合物,例如防锈剂及/或表面活性剂。在蚀刻清洁之后,运用冷水来冲洗经蚀刻清洁的铜箔达大约两分钟。因此获得了经蚀刻清洁及冲洗的铜箔。未进一步处理用于样本1(比较样本,未根据本发明)的铜箔的铜表面且随后使其经受层压防焊剂(参见下文)。在第二步骤中,进一步处理用于样本2至6的铜箔的铜表面。子步骤(i-a);化学处理铜表面:(b)通过有机化合物(硅烷):将用于样本2至4的铜箔在25℃下浸润至含有1重量%的硅烷且以乙醇及去离子水为溶剂的涂布溶液中达60秒。涂布溶液的ph值为5(运用乙酸进行调节)。已制备了三种不同的涂布溶液,各自含有不同的硅烷:对于样本2:5-[[3-(三甲氧基硅基)丙基]硫基]-1,3,4-噻二唑-2(3h)-硫酮对于样本3:5-[[3-(三甲氧基硅基)丙基]硫基]-1,3,4-噻二唑-2-胺对于样本4:5-[[3-(三甲氧基硅基)丙基]硫基]-4h-1,2,4-三唑-3-胺然后干燥所得的铜箔。因此获得了用于样本2至4的经硅烷化及干燥的铜箔。随后使这些铜箔经受层压防焊剂(参见下文)。(a)通过氧化及后续还原:在蚀刻清洁之后,通过氧化及后续还原反应来化学处理用于样本5及6的铜箔的铜表面。第一,将用于样本5及6的铜箔在50℃下浸润至含有15.5ml/lnovabondit稳定剂(atotech)的调节溶液中达30秒。调节剂使铜表面在ph值及电化电位方面稳定。因此获得了用于样本5及6的经调节铜箔。第二,在包括100ml/lnovabondit102(atotech)及15.5ml/lnovabondit稳定剂(atotech)的氧化溶液中处理经调节铜箔。处理是在70℃下实行,从而导致cu(0)至cu(i/ii)氧化物的均一且自限制的转化,最终在铜表面上形成了经转化铜的针型层,其最大层厚度小于180nm。在氧化反应之后,运用冷水来冲洗经氧化的铜箔。第三,使经氧化及冲洗的铜箔与包括20ml/lnovabondit还原剂(atotech)及5ml/lnovabondit稳定剂的还原溶液接触。接触是在35℃下实行达5分钟,从而引起还原反应。还原反应将cu(i/ii)物种转化成cu(0),由此增强了铜表面对化学物质(例如来自环境及/或后续金属化过程)的稳定性。在还原反应之后,运用冷水来冲洗铜箔达大约两分钟。因此获得了经还原及冲洗的铜箔。随后使用于样本5的铜箔经受层压防焊剂(参见下文)。在还原反应之后,使用于样本6的经还原及冲洗的铜箔浸润至保护剂溶液中达一分钟,所述溶液为去离子水中的10ml/lnovabondit保护剂mk(atotech)。基本上,浸润至保护剂溶液中是任选的。其在实行时将有机化合物附着至经氧化且随后还原的铜表面,以便避免经还原铜的再氧化(对应于如上文所定义的子步骤(i-a)中的(b))。在浸润之后,运用冷水来冲洗用于样本6的铜箔达大约两分钟且随后干燥。因此获得了用于样本6的经保护及冲洗的铜箔。随后使这些铜箔经受层压防焊剂(参见下文)。子步骤(i-b);运用覆盖层来覆盖铜表面:在第一层压步骤中,在黄光下于洁净室中通过使用真空层压机(dynachemva7124-hp6)将干膜型光可成像防焊剂(永久性、不导电、未完全聚合、含有丙烯酸酯及环氧化合物的覆盖层)真空层压至所有六个样本的铜表面上,其中室温在20至25℃的范围内且相对湿度为50至60%。各防焊剂的层厚度为20μm且因此易遭受分子氧渗透。用于真空层压的条件如下:第一步骤:100℃,真空:在3hpa下30秒,压力:在0,5mpa下30秒,第二步骤:80℃,压力:在8kgf/cm2下60秒在层压之后,获得了经层压铜箔。在热处理之前,借助于uv灯以光化方式预聚合经层压铜箔,其中所施加的总曝光能量为1000mj/cm2。在此步骤中,尤其聚合丙烯酸酯化合物。因此,对于各样本获得了具有永久性、不导电、未完全聚合的防焊剂的铜箔。表1,用于防焊剂应用的样本设计的概观*“硅烷处理”通过有机化合物来化学处理铜表面(将硅烷附着至经蚀刻清洁的铜表面)**“保护剂处理”通过有机化合物来化学处理铜表面(将保护剂化合物附着至经氧化且随后还原的铜原子/铜离子)步骤(ii),热处理衬底:在各样本中,使至少一个试样经受以下两个热处理步骤中的一者:-在160℃下使用常规热空气对流烘箱(heraeus烘箱ut6200)处理达60分钟(未根据本发明的方法产生样本,而是产生比较实例)经受此类热处理的样本在下文中另外缩写为“+o2”(例如样本1,+o2),这指示其热处理是在存在环境空气的情况下进行。-在160℃下于展现气氛的烘箱(atvpep-603)中处理达60分钟,所述气氛含有以小于5ppm的量的分子氧经受此热处理的样本在下文中缩写为“-o2”(例如样本1,-o2),这指示其热处理是在惰性气氛中进行。“-o2”样本可根据本发明或比较实例,这取决于铜表面是否被化学处理。在各热处理步骤中,未完全聚合的防焊剂在所述热处理期间完全地聚合且在仅一个单一热处理步骤中聚合,即,不中断热驱动聚合(单步骤聚合)。在此步骤中,尤其聚合环氧化合物。经由剥落强度测试的防焊剂粘着评估:对于在热处理之后获得的各样本(1至6)(包含“+o2”及“-o2”),测定剥落强度:(1)直接在如上文所描述的热处理之后(也被称为初始剥落强度),(2)在96小时hast之后(hast条件:130℃,85%rh,hast腔室:ehs-221m)。为了测定剥落强度,已通过将相应铜箔粘着至刚性板(大小与铜箔相同)而从各试样制备了若干条带型片段,使得刚性板面对完全聚合的防焊剂。因此获得了具有结构上加强的防焊剂的铜箔。然后,将各加强铜箔切割成所述条带型片段(10×100mm,铣刀(millingcutter),walterlemmenccd)。使条带型片段经受剥落力测量机器(roellzwickz010)以独立地评估将铜箔与其相应的结构上加强的防焊剂分层所需要的剥落强度(角度:90°,速度:50毫米/分钟)。通常,避免分层所需要的剥落强度越高,粘着越好。以下表2中概述了剥落强度测试的结果。表2,用于防焊剂应用的剥落强度,以n/cm为单位整个样本1以及所有样本2至6—+o2—为未根据本发明的比较实例。所有样本2至6—-o2—符合本发明的方法。根据表2,样本1的剥落强度值最低。样本1—-o2—是基于us5,484,688a中所揭示的教示,其中防焊剂在单步骤聚合中完全地聚合。如果使用惰性氮气氛(-o2)以代替环境空气(+o2),那么对于样本1根本未观测到剥落强度增加(参见“在热处理之后”)或至少未获得显著剥落强度增加(参见“在hast之后”)。因此,在惰性氮气氛中仅仅于铜表面(其未通过增加剥落强度的表面处理予以处理)上聚合防焊剂并不足以获得良好的粘着。样本2至6经历增加剥落强度的表面处理(实例5及6是基于wo2012/005722a1中所揭示的教示予以处理)。根据表2,样本1至6—+o2(在热处理之后)—的剥落强度从1.27(样本1,无增加剥落强度的表面处理)增加至高达4.76(样本6)。在hast之后获得了相似结果;从0.11(样本1)至高达1.80(样本6)。甚至在存在环境空气的情况下仍获得了此剥落强度增加,且其来源于表面处理。然而,通过组合(1.)增加剥落强度的表面处理(优选地包含氧化及后续还原反应)及(2.)在惰性气氛中的热处理而实现了出人意料的额外剥落强度增加。表2展示出(1.)及(2.)的组合展现协同效应。在组合(1.)及(2.)之后获得的剥落强度超过对于(1.)及(2.)个别地所获得的剥落浓度的总和。表2中的结果展示出惰性氮气氛协同地增加了增加剥落强度的表面处理的效应。此外,避免了如us5,484,688a中所揭示的两步骤过程。经由渗入测试(锡焊接)的防焊剂粘着评估:如上文在章节a下所略述而制备其它六个样本,其中本质差异为使用覆铜层压物(coppercladlaminate;ccl)以代替铜箔。此外,在层压防焊剂之后,实行防焊剂的图案化以便在防焊剂中获得开口,其开口直径为大约200μm。出于此目的,将与防焊剂层压的ccl对准至光掩模上且随后在环境温度下曝光于光化辐射(使用接触曝光单元exm-1201-f02),其曝光能量为500mj/cm2,以获得具有选择性预聚合的防焊剂的样本。使防焊剂在包括大约1重量%的无水碳酸钠的含水显影剂溶液中显影,运用水进行冲洗,且随后经受如上文所描述的热处理。因此获得了具有永久性、图案化、不导电、完全聚合的防焊剂的样本。将样本首先通过使用硫酸基清洁溶液(proselectsf,atotech)在50℃下清洁达5分钟且随后运用水进行冲洗。接下来,将暴露于开口中的铜表面在30℃下借助于100g/l铜活化剂bc65(atotech)的微蚀刻溶液进行微蚀刻(蚀刻深度为大约1μm),且随后运用水进行冲洗。然后,在两步骤程序中,将锡在焊接过程中沉积于所述暴露铜表面上。首先,实行浸润至22℃沉积溶液(stannatech,atotech)中达1分钟,随后浸润至相同但展现75℃温度的溶液中达15分钟。然后,运用水来冲洗相应样本。最后,获得了锡焊接样本。通过光显微法(olympusbx50)来研究渗入质量。样本1展示了在焊接过程期间由于针对所有试样的严苛锡焊接条件而引起的防焊剂与铜表面的严重分层。可能没有足够的锡沉积至开口中;因此,未实行微观研究。样本2至6—+o2—频繁地展示了在防焊剂与铜表面之间的不当的锡渗入,其中对于样本2至6—-o2,未观测到此类渗入。在图1的a及b中,锡焊接开口被示意性地描绘为直径d1为大约200μm的白色圆形。未渗入的防焊剂被描绘为阴影区域。防焊剂下方渗入的锡被描绘为具有宽度d2(d2在大约25至35μm的范围内)的环带。图2中展示对应的原始图。图1的a示意性地展示如针对样本6—+o2—所观测到的锡渗入。与此对比,针对样本6—-o2—未观测到锡渗入,如图1的b所展示。针对样本2至5已获得了相似结果(数据未被展示)。根据本发明的方法而制造的印刷电路板允许没有锡渗入的锡焊接,尤其是用于厚度为20μm或更小的防焊剂。此外,防止渗入,尤其是在锡的情况下,似乎并不仅仅关于粘着的问题。结果展示出,(1.)增加剥落强度的表面处理(优选地包含氧化及后续还原反应)及(2.)在惰性氮气氛(小于5ppm分子氧)中的热处理的前述组合不仅改善了粘着,而且另外防止了渗入(甚至对于展现比较低的剥落强度值的样本;比较表1的样本2至4与样本5及6)。对于极薄防焊剂(尤其是20μm或更小)尤其如此,所述防焊剂趋向于分子氧渗透。样本2至6—-o2—也通过了标准带测试(结果未被展示)b:堆积层应用:对于堆积层应用,已制备了两个额外样本(样本7及8)。这些样本是相似地如上文在项目a下对于防焊剂应用所略述而制备,其中使用防焊剂以代替堆积层且此外具有以下差异:-在各层压步骤中,层压参数是如上文所描述,但其中本质差异为在第二步骤中应用100℃,-热处理实行如下(对于两者:在存在环境空气的情况下及在小于5ppm分子氧的惰性气体(氮)下):在150℃至180℃的范围内的温度下60分钟,随后在200℃下60分钟在数个测试系列中主要测试20μm的典型的含环氧树脂的堆积层。另外,对于相同的含环氧树脂但展现40μm的厚度的堆积层获得了数个结果。表3,用于堆积层应用的样本设计的概观样本蚀刻清洁硅烷处理氧化反应还原反应保护剂处理堆积层7是否否否否是8是否是是是是在热处理之后及在hast(如上文所定义的hast)之后已再次测定了剥落强度。表4中概述了剥落强度结果。表4,用于堆积层应用的剥落强度,以n/cm为单位样本7为比较实例;不存在增加剥落强度的表面处理。在存在环境空气(+o2)的情况下,基本上未获得粘着(剥落强度为0.1至0.3)。所有样本8—+o2—不包含在气氛中的热处理,所述气氛含有100000ppm或更小(以所述气氛的总体积计)的量的分子氧,且因此也未根据本发明。相反地,所有样本8—-o2—是根据本发明。如表4中清楚地所展示,对于样本7以及样本8两者,针对-o2所获得的剥落强度相较于针对+o2所获得的剥落强度显著地增加。在样本8中实行的增加剥落强度的表面处理会增加惰性氮气氛的正面效应。再者,(1.)增加剥落强度的表面处理(优选地包含氧化及后续还原反应)及(2.)在惰性气氛中的热处理的组合出人意料地且协同地增加了剥落强度。有趣的是,样本8—40μm—甚至在存在环境空气(+o2)的情况下仍展示相对高的剥落强度。尽管在各状况下在惰性氮气氛中观测到显著的剥落强度增加(参见样本8—-o2),但此实例展示出40μm堆积层相较于20μm堆积层固有地较不易遭受分子氧渗透。因此,本发明的方法尤其有益于厚度小于40μm的堆积层。当前第1页12