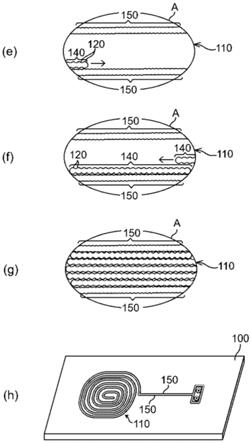
1.本发明涉及一种电路成型部件以及电子设备,特别地,涉及一种电气制品、通信终端、存储卡用转接头、光插头、光元件模块、电连接器、车辆等具有电子电路的各种各样的电路成型部件以及电子设备。
背景技术:2.在专利文献1中,公开了一种具有天线电路的存储卡用转接头。该天线电路,能够在通过导电镀覆而形成的立体电路成型部件(mid)中构成基础电路,并且通过由立体电路成型部件构成转接头本体的一部分或全部,从而能够对应于存储卡的种类适宜地设计转接头本体的形状。
3.专利文献1:日本特开2006-318217号公报
技术实现要素:4.发明要解决的技术问题
5.但是,在专利文献1中,没有公开任何关于电路成型部件的具体的内容,其是如何构成的,或者,具有什么样的结构等内容,无法通过阅读专利文献1得知。进一步,该电路成型部件,具有何种程度的性能,根据专利文献1也无法把握。
6.本发明要解决的技术问题是,提供一种在基材上具有自由度地、并且以高密合性形成金属层的电路成型部件。
7.另外,本发明要解决的技术问题是,提供一种具备这种电路成型部件的电气制品、通信终端、存储卡用转接头、光插头、光元件模块、电连接器、车辆等具有电子电路的各种各样的电子设备。
8.解决技术问题的方法
9.为了解决上述技术问题,本发明提供一种在基材的加工区域中形成有金属层的电路成型部件,在所述加工区域中,连续地多个凹部,各个凹部分别具有多个孔。
10.所述加工区域,其宽度与相对于所述基材的表面的最深深度的比率为10:1~6:1。
11.所述加工区域可以形成为:宽度在20μm~200μm的范围,相对于所述基材的表面的最深深度在2μm~30μm的范围内。
12.所述金属层,能够在所述加工区域内通过镀覆法进行层叠从而形成,在这种情况下,在进行层叠时与成为金属层的金属进行反应的催化剂,附着在所述孔以及凹部中。
13.如权利要求1所述的电路成型部件,所述多个凹部中的相互邻接的凹部的中心间的距离,是0.01mm~0.2mm。
14.能够使用在所述基材内不含金属材料的基材。
15.另外,本发明的电子设备,具备上述的电路成型部件。
附图说明
16.图1是本发明的实施方式的电路成型部件300的外观图。
17.图2是图1所示的电路成型部件300的制造步骤图。
18.图3是图1所示的电路成型部件300的制造步骤图。
19.图4是在图1所示的基材100上以高密合度形成金属层200的说明图。
20.图5是构成如图3(e)所示的填充线(hatch line)140的凹部120的侧面的sem照片。
21.图6是示出图3(g)所示的加工区域110的平面的sem照片。
22.图7是示出图1的金属层200的平面的sem照片。
23.图8是图1的金属层200的断面的sem照片。
24.附图标记说明
25.100
ꢀꢀꢀ
基材
26.110
ꢀꢀꢀ
加工区域
27.120
ꢀꢀꢀ
凹部
28.130
ꢀꢀꢀ
孔
29.140
ꢀꢀꢀ
填充线
30.150
ꢀꢀꢀ
轮廓线
31.200
ꢀꢀꢀ
金属层
32.300
ꢀꢀꢀ
电路成型部件
具体实施方式
33.以下,参照附图,说明本发明的实施方式。需要留意的点是,在各图中,为了容易理解发明,存在按照与实际不同的尺寸等绘制的位置。
34.图1是本发明的实施方式的电路成型部件300的外观图。在图1中,示出了电路成型部件300,其具备热可塑性树脂或热硬化性树脂等的基材100,和在基材100的加工区域110(图2(c))内形成的金属层200。
35.这里,示出了将电路成型部件300用作天线的示例,但是电路成型部件300除了天线以外,能够用于实现各种电子电路。另外,金属层200,能够根据电路成型部件300的用途布置其形状,进而,也能够根据具备电路成型部件300的电子设备的用途布置其形状,其材料的选择也能够有较高的自由度。
36.作为能够用作基材100的树脂的示例,可列举:abs(acrylonitrile butadiene styrene:丙烯腈丁二烯苯乙烯),pc(polycarbonate:聚碳酸酯),ppc(polypropylene carbonate:聚丙烯碳酸酯),ppe(polyphenylene ether:聚苯醚),m-ppe(modified-polyphenylene etheer:改性聚苯醚),lcp(liquid crystal polymer:液晶聚合物),pbt(poly-butyleneterephthalate:聚对苯二甲酸丁二醇酯),tpe(thermoplastic elastomer:热塑性弹性体),ppo(polyphenylene oxide:聚苯醚),peek(polyetheretherketone:聚醚醚酮),pct(polycyclo hexylene dimethylene eterephthalate:聚环己二甲基对苯二甲酸酯)等。需要说明的是,在5g等的高频率电路的情况下,可以选择lcp、coc(环状烯烃共聚物)、sps(间规聚苯乙烯)、pom(聚缩醛)、pi(聚酰亚胺)、ptfe(聚四氟乙烯)等的低介电正切的原材料。
37.另外,基材100,能够将上述各树脂的成分中的若干种进行适当组合。或者,基材100,例如,还能够以相对于总重量为5wt%~50wt%的方式含有玻璃纤维等的非导电填料,或含有5wt%~50wt%的锡粒子、铜粒子、锑粒子等。这种填料等,与使用图4在下文描述的孔130的情况相同,能够帮助提高基材100与金属层200的密合性。
38.进一步,基材100的材料,除了树脂以外,也能够选用纤维、纸、皮、石英玻璃等的非导电体。也就是说,基材100的材料,只要能够在电子电路中使用即可,能够从现有的用于基材的材料中选择。
39.金属层200,例如,能够以3μm~100μm的厚度形成。在本实施方式中,能够通过镀覆法,涂覆法、喷涂法形成金属层200。金属层200,能够选用铜、银、金、铂、镍或它们的合金作为材料。虽然在本实施方式中,对采用无电解镀覆的示例进行说明,但是也能够采用电镀覆、熔融镀覆、真空镀覆等。
40.图2~图3是图1所示的电路成型部件300的制造步骤图。
41.首先,准备作为加工对象的基材100(图2(a))。这里,基材100,对采用射出成形用聚碳酸酯树脂制成基材的例子进行说明。为了形成金属层200而对基材100进行加工的方法,能够采用:激光照射、冲压模具、模塑成型等,在本实施方式中,对通过激光照射来加工基材100的示例进行说明。
42.需要说明的是,激光的种类不限,能够使用固体激光、液体激光、气体激光、半导体激光、纤维激光等各种介质的激光。
43.接着,对基材100连续地进行激光照射以形成轮廓线150,该轮廓线150是想要形成金属层200的区域的外缘(图2(b))。激光照射的条件,能够根据基材100的硬度、电路成型部件300的用途等进行适当选择,作为一个示例,可以选用如下条件:构成轮廓线150的凹部120的底面部的直径大致为10μm~100μm、高度为2μm~30μm。
44.具体地,激光照射的条件能够是:波长为355nm~2000nm(例如,1064nm),透镜孔径为100mm~420mm(例如,254mm),最大功率为10w~30w(例如,20w),脉冲为4ns~200ns,频率为5khz~500khz。需要说明的是,例如在选用聚酰亚胺薄膜作为基材100的情况下,能够采用532nm的波长,例如在选用透明聚碳酸酯作为基材100的情况下,能够采用355nm的波长。
45.基材100,当被照射激光时,其被照射的点(及其附近)会因激光热而熔解。因此,在基材100上,在激光点处形成凹部120。形成了第1个凹部120之后,便使基材100与激光照射装置以300mm/sec~2500mm/sec的相对的移动速度沿着线状进行移动,形成与该凹部120相邻的凹部120。
46.需要说明的是,凹部120的形状,可以是略穹顶状,除此之外,也可以是大致圆锥状或大致棱锥状。另外,基材100与激光照射装置的移动速度越慢,则相互邻接的凹部120的中心间距离越短而越像u字槽,在采用冲压模具、模塑成型等的情况下,也能够形成v字槽。因此,在本说明书中使用的用语“凹部”,也包括u字槽、v字槽这样的槽。
47.另外,关注构成轮廓线150的凹部120和与之邻接的凹部120,以两者的略圆形的底面的面积例如彼此重叠50%~90%的方式,以相对较细的间距(pitch)照射激光。通常,基材100的耐热温度越高越好,这样就越能增加相互邻接的凹部120的重叠比例,因此可以提高激光的功率等。
48.图2(c)中,示出了图2(b)所示的区域a的放大图。图2(c)中,标记有箭头以示出凹
部120的形成方向。如图2(c)所示,相互邻接的凹部120,以相当高的程度重叠。因此,当关注刚形成的凹部120时,虽然在箭头的前侧(图面右侧)存在画出凹部120的底面的边界线,但是在箭头的后侧(图面左侧)画出凹部120的底面的边界线已经发生熔解因而不存在。
49.之后,在想要形成轮廓线150的位置连续地照射激光,完成轮廓线150(图2(d))。如已经叙述的,轮廓线150是指想要形成金属层200的区域的外缘,因此被轮廓线150封闭的区域成为加工区域110。
50.需要说明的是,加工区域110,虽然取决于电路成型部件300的用途
·
规模,但是对于线状的区域来说,例如形成为,宽度在20μm~200μm的范围内,最深深度在2μm~30μm的范围内。即,加工区域110,宽度与最深深度的比率为10:1~6:1。
51.以下,为了对加工区域110中的加工状态进行详细说明,暂且关注区域a的放大位置以进行说明。
52.当轮廓线150的形成结束时,开始对加工区域110全面地进行激光照射。在本实施方式中,在加工区域110中,连续地且线状地进行激光照射。将如此形成的连续的凹部120,称作填充线140。
53.用于形成填充线140的激光照射条件,可以与形成轮廓线150的情况相同,但是为了提高基材100与金属层200的密合性,在填充线140中相互邻接的凹部120,就底面的面积而言,以不重叠或相互重叠20%以下的方式,使用相对较粗的间距照射激光(图3(e))。
54.这里,示出了填充线140中相互邻接的凹部120以10%左右重叠的状态。然而,即使在填充线140中按照相互邻接的凹部120的底面不会重叠的条件照射激光,这些凹部120之间的区域也会因激光照射而熔解,在大多数情况下等于进行了加工。
55.需要说明的是,虽然在图3(e)中示出了,在不与轮廓线150重叠的状态下的、第1行的填充线140,但是填充线140中的凹部120,也能够在与轮廓线150重叠的状态下形成。
56.若继续在填充线140中进行凹部120的形成,则可最终完成第1行的填充线140。在本实施方式中,当第1行的填充线140完成后,隔着1行填充线140的间隔,形成第3行的填充线140(图3(f))。
57.即,在本实施方式中,在第2行的填充线140的形成之前,先形成第3行的填充线140。需要说明的是,相互邻接的填充线140的中心间距离,能够设为0.01mm~0.2mm。
58.在本实施方式中,像这样,形成奇数行的填充线140之后,形成偶数行的填充线140。通过这样,不会在刚熔解且为相对高温的区域中形成凹部120,能够避免后续形成的凹部120的形状变形。特别地,在选用热可塑性树脂作为基材100的材料的情况下,很有效。
59.然而,在填充线140相对较长的情况下等,已熔解的位置会被外部空气冷却,因此,并不必须在形成奇数行的填充线140之后形成偶数行的填充线140。
60.若继续在填充线140中形成凹部120,则可形成整行的填充线140(图3(g))。之后,虽然没有图示,但是例如在与各行的填充线140正交的方向上形成第1列的填充线140,接着,例如形成第3列、第5列这样的奇数列的填充线140,之后,形成偶数列的填充线140。
61.像这样,当整行整列的填充线140的形成结束时,在加工区域110中全面地形成了多个凹部10,加工处理结束(图3(h))。然而,并非必须在行方向和列方向这样的彼此不同的方向上形成填充线140,能够仅仅在一个方向上形成填充线140,即,仅仅在行方向上形成填充线140。
62.在这种情况下,使在行列方向上相互邻接的凹部120的中心间距离,大致为凹部120的直径,或者,也可以使得在行列方向上相互邻接的凹部120的底面重叠5%~15%左右。
63.另外,需要注意的是,轮廓线150以及填充线140,均不限于形成为直线状,也包括形成为曲线状。具体地,如图3(h)所示,加工区域110中包括漩涡状部分,因此在该部分形成的轮廓线150以及填充线140是曲线状。
64.在本实施方式中,在图3(e)以及图3(f)中,示出了相对于轮廓线150平行地形成各行的填充线140的示例,但是各填充线140的形成方向,不一定必须相对于轮廓线150平行。
65.因此,例如,可以在相对于轮廓线150的延伸方向,例如成30
°
、45
°
、60
°
、90
°
之类的所需的角度的方向上,形成各行的填充线140,进一步,也可以在相对于各行的填充线,例如成30
°
、45
°
、60
°
、90
°
之类的所需要的角度的方向上,形成各列的填充线140。
66.另外,各填充线140,不限于在多个凹部120以行列状的方式彼此直交的状态下形成填充线140,例如,也可以在多个凹部120呈千鸟状或者蜂窝状地进行排列的状态下形成填充线140。
67.当对基材100的激光处理结束时,熔解时剥落而成为微粒的基材100的一部分,会附着于基材100的表面。因此,例如,使用超声波清洗机清洗基材100,或者使用吹气枪对基材100吹射空气,从基材100上除去微粒。
68.图4是对在图1所示的基材100上以较高的密合度形成金属层200的情况进行说明的图。如图4所示,凹部120具有呈不规则的形状的多个孔130。各孔130,在为了形成凹部120而照射激光时发生熔解,因而产生。
69.在本实施方式中,在基材100上形成金属层200之前,进行在下文说明的前处理。在该前处理的一个步骤中,与成为金属层200的镀覆材料相对应的催化剂,不仅附着于凹部120,还附着于各孔130。
70.因此,镀覆材料与附着在凹部120以及各孔130中的催化剂进行反应且进行层叠,从而形成金属层200,并且即使对所完成的金属层200沿剥离的方向施加应力,由于成为不规则的形状的各孔130可得到锚定效果,因此金属层200难以从基材100剥离。
71.也就是说,在本实施方式中,在形成不规则的形状的各孔130的条件下形成凹部120,通过该孔130的形状发挥锚定效果,从而得到对基材100具有较高的密合度的金属层200。
72.因此,在采用通过激光照射形成凹部120的方法的情况下,也就是说,在采用通过冲压模具或模塑成型形成凹部120的方法的情况下,为了能够形成与凹部120以及孔130对应的部分,使用具有与其对应的形状的模具。
73.接着,对为了在基材100上形成金属层200而进行的前处理进行说明。前处理,因基材100以及金属层200的原材料等而不同,这里,对金属层200的材料选用镍铜的情况下的典型例进行说明。前处理,包括在下文中说明的表面处理、中和处理、附着处理、活性化处理。
74.在表面处理中,进行碱性蚀刻处理以使基材100的表面粗化。表面处理,在对200ml~400ml的高浓度(例如,98%)氢氧化钠添加1l纯水而形成约1l的混合液的液槽中,将基材100含浸1分钟~20分钟(例如,5分钟)。此时,混合液的温度,例如,能够是50℃~70℃左右。之后,从液槽中取出基材100,清洗干净。
75.在中和处理中,使用酸对基材100的表面的碱性状态进行中和。中和处理,例如在对50ml~200ml的35%浓度的盐酸添加1l纯水而形成的约1l的混合液的液槽中,将基材100例如含浸1分钟~5分钟。此时,混合液的温度,例如,能够是10℃~25℃左右。之后,从液槽中取出基材100,清洗干净。
76.在附着处理中,使催化剂附着,该催化剂与想要通过对基材100进行镀覆而层叠的金属相对应。附着处理,例如,在对3ml~10ml的锡、5ml~15ml的盐酸,30ml~150ml的硫酸钯添加1l纯水而形成的约1l的混合液的液槽中,将基材100例如含浸1分钟~10分钟。此时,混合液的温度,例如,能够是10℃~25℃左右。之后,从液槽中取出基材100,清洗干净。
77.或者,附着处理,例如,在对60ml~200ml的锡、150ml~300ml的盐酸、10ml~450ml的氯化钯添加1l纯水而形成的约1l的混合液的液槽中,将基材100例如含浸1分钟~10分钟。此时,混合液的温度,例如,能够是10℃~25℃左右。之后,将基材100从液槽中取出,清洗干净。
78.在活性化处理中,使附着于基材100的催化剂活性化。活性化处理,例如在对10ml~50ml的盐酸、10ml~50ml的过氧化氢、30ml~100ml的硫酸添加1l纯水而形成的约1l的混合液的液槽中,将基材100例如含浸数秒钟~10分钟。此时,混合液的温度,例如,能够是10℃~25℃左右。之后,将基材100从液槽中取出,清洗干净。
79.接着,对于无电解镀覆,以金属层200为铜层的情况为例进行说明。无电解镀覆处理,包括下文中说明的冲击镀覆处理、镀铜处理、镀镍处理、后处理、干燥处理。
80.在冲击镀覆处理中,在所需要的对300ml~350ml的无电解镍硼冲击镀覆液添加1l纯水而得到的约1l的、且ph调节为6.3~6.8的液体的液槽中,将基材100例如含浸数秒钟~10分钟。此时,混合液的温度,例如,能够是50℃~70℃左右。之后,将基材100从液槽中取出,清洗干净。需要留意的点是,冲击镀覆处理,不是必须进行的处理。
81.作为无电解镍硼冲击镀覆液,例如,能够使用以6%~10%的单乙醇胺、25%~35%的硫酸镍、1%~10%的氨和10%~20%的次磷酸的含有比例用纯水进行稀释的混合液。
82.在镀铜处理中,在所需要的对220ml~270ml的无电解铜镀覆液添加1l纯水而得到的约1l的混合液的液槽中,将基材100含浸例如2小时~3小时。此时,混合液的温度,例如,能够是40℃~55℃左右。之后,将基材100从液槽中取出,清洗干净。
83.作为无电解铜镀覆液,例如,能够使用以40~50%的氢氧化钠和6%~12%的硫酸铜的含有比例用纯水进行稀释的混合液。
84.在镀镍处理中,在所需要的对120ml~170ml的无电解镍镀覆液添加1l纯水而得到的约1l的、且ph调节为6.0~6.7的混合液的液槽中,将基材100含浸例如数秒~10分钟。此时,混合液的温度,例如,能够是40℃~55℃左右。之后,将基材100从液槽中取出,清洗干净。
85.作为无电解镍镀覆液,例如,能够使用以10%的乳酸、4%的氢氧化钠、45%的硫酸镍、20%的磷酸钠、4.5%的氢氧化钠和3%的苹果酸的含有比例用纯水进行稀释得到的混合液。
86.在后处理中,在所需要的对50ml~100ml的后处理液添加1l纯水而得到的约1l的混合液的液槽中,将基材100例如浸渍30秒钟~2分钟。此时,混合液的温度,例如,能够是30
℃~70℃左右。之后,将基材100从液槽中取出,清洗干净。
87.在干燥处理中,将基材100搬入未图示的干燥机中,在50℃~100℃的温度下干燥15分钟~60分钟。
88.图5,是构成如图3(e)所示的填充线140的凹部120的侧面的sem照片。图5(a)示出1000倍的放大照片,图5(b)示出2000倍的放大照片,图5(c)示出5000倍的放大照片,图5(d)示出10000倍的放大照片。
89.如图5(a)~图5(d)所示,可知在凹部120的侧面形成有多个孔130。各孔130,其形状不规则,因此大小也不规则,大致上,存在大量的开口尺寸为10μm~30μm左右的孔。
90.图6,是示出图3(g)所示的加工区域110的平面的sem照片。图6(a)示出200倍的放大照片,图6(b)示出1000倍的放大照片。这里示出了,彼此邻接的凹部120以基本上不会重叠的方式形成的状态。
91.如图6(a)以及图6(b)所示,在加工区域110中以行列状形成凹部120。按照条件实施激光照射,微细地观察可知,难以按照该条件有规则地形成凹部120,可知可形成约400μm的凹部120。
92.图7(a)以及图7(b),是示出图1的金属层200的平面的sem照片。图7(a)示出200倍的放大照片,图7(b)示出500倍的放大照片。如图7(a)以及图7(b)所示,可知在基材100的加工区域110的表面上全面地形成了金属层200。
93.图8(a)以及图8(b),是示出图1的金属层200的断面的sem照片。图8(a)示出200倍的放大照片,图8(b)示出500倍的放大照片。由图8(a)以及图8(b)可知,以约400μm的间距不隔着间隔而连续地形成了向下略穹顶状的凹部120。需要说明的是,为了得到在本发明书中记载的断面照片,使用ryobi公司制造的研磨机fg-18切断基材100。
94.另外,在各凹部120中,目视观察可知,存在相对于其表面沿着放射方向呈棘状的多个孔130。并且可知,由于金属层200位于各孔130中,因此金属层200与基材100的连接变得牢固。
95.如以上说明,根据本实施方式的电路成型部件300,能够在基材100上,具有自由度地、以较高的密合性形成金属层200。因此,电路成型部件300,能够用于各种各样的电气制品、通信终端、存储卡用转接头、光插头、光元件模块、电连接器、车辆等的电子电路中。