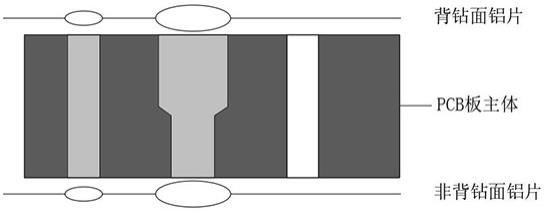
1.本发明涉及pcb板引线钻断技术领域,具体为一种树脂塞孔铝片二合一制作方法。
背景技术:2.各大供应商为了提供更好的产品来达到显示器需要提供的逐行或者隔行扫描的信号为观众带来无限的视觉享受;在pcb的精密度要求越来越高,从以前的低端通孔板转换成多层控深钻+树脂塞孔板,在品质要求和制作工艺都要求比较难。
技术实现要素:3.本发明提供一种具有产品品质好、生产工艺简化及生产效率高的树脂塞孔铝片二合一制作方法。
4.为了实现上述目的,通过以下技术方案实现。
5.一种树脂塞孔铝片二合一制作方法,适用于钻有通孔和背钻孔的pcb板的树脂塞孔,所述方法为将所述pcb板的背钻面和非背钻面的塞孔铝片为完全一样的两片板的塞孔方法。
6.本发明树脂塞孔铝片二合一制作方法,将传统的应用于pcb板上下在的不同的塞孔铝片设计为完全相同中的两块铝片的技术方案,使塞孔作业工序,上下铝片不会出现装反的情况,进而有效避免现有技术中因贴装时不容易,出现装反,进而导致塞孔一次不饱满,造成重复返工塞孔还不能保证塞孔的饱满度情况。
7.进一步地,所述的树脂塞孔铝片二合一制作方法,包括如下步骤,s1:铝片工程资料设计,以背钻孔为设计依据进行铝片钻孔工程资料设计;s2:铝片制作,根据s1步骤中设计的铝片工程资料进行钻孔生产铝片,生产铝片时直接一次生产出两张同样的铝片;s3:树脂塞孔,将s2步骤中制得的两张同样的铝片分别贴在pcb板的背钻面和非背钻面,然后从pcb板的背钻面和非背钻面同步向背钻孔进行树脂塞孔。
8.本发明树脂塞孔铝片二合一制作的方法,s步骤的铝片工程资料设计,其中,钻孔资料以背钻孔为依据进行设计,使铝片上钻孔大小与背钻孔相匹配和适应,为2步骤中铝片的生产提供基础和保障,s2步骤中一次生产出两张同样的铝片,确保装贴在pcb板上下两面的铝片是一样的,有效解决现有技术中因两片铝片不一样而出现的装反的情况,在铝片装贴完成后,s3步骤分别从pcb板的上下两面的铝片孔处向背钻孔进行灌树脂,完成树脂塞孔,该种作业方式使树脂塞孔饱满,返工率小,有效提升生产效率。
9.进一步地,s1步骤以背钻孔直径大小为基础,通过增加补偿的方法进行设计铝片工程资料,即是采用正常的直径+补偿的方法设计,该种方法为常规补偿设计方法,作业人员已经熟知,方便、高效。
10.进一步地,s2步骤前,还包括钻带制作,所述钻带制作时在料号位置设置标识。钻带的制作,用于确保铝片工程资料的设计,为铝片钻孔生产提供基础和保障。
11.进一步地,s2步骤中,还包括钻出与pcb板上通孔相对应的钻孔。
12.进一步地,s3步骤完成后,将pcb板放入烘烤工序进行烤板,使塞孔固化。
13.进一步地,烤板后,pcb板进入研磨工序进行研磨,使板面无树脂残留。
14.本发明树脂塞孔铝片二合一制作方法及方法与现有技术相比,具有如下有益效果:第一、产效率高,本发明方法采用一次直接生产出两张同样的铝片,减少了多次换机资料上传铝片的工序,降低了铝片工具生产备工具的准备时间,而且有效解决现有技术中因两片铝片不一样而出现的装反的情况,返工率小,大大提升了生产效率;第二、生产工艺简化,本发明方法采用一次直接生产出两张同样的铝片,减少了多次换机资料上传铝片的工序,使生产工艺得到简化;第三、产品品质好,本发明树脂塞孔铝片二合一制作的方法,s步骤的铝片工程资料设计,其中,钻孔资料以背钻孔为依据进行设计,使铝片上钻孔大小与背钻孔相匹配和适应,为s2步骤中铝片的生产提供基础和保障,s2步骤中一次生产出两张同样的铝片,确保装贴在pcb板上下两面的铝片是一样的,s3步骤分别从pcb板的上下两面的铝片孔处向背钻孔进行灌树脂,完成树脂塞孔,该种作业方式使树脂塞孔饱满,产品品质好。
附图说明
15.图1为本发明树脂塞孔铝片二合一制作方法的状态示意图。
具体实施方式
16.下面将结合具体实施例及附图对本发明树脂塞孔铝片二合一制作方法作进一步详细描述。
17.一种树脂塞孔铝片二合一制作方法,适用于钻有通孔和背钻孔的pcb板的树脂塞孔,所述方法为将所述pcb板的背钻面和非背钻面的塞孔铝片为完全一样的两片板的塞孔方法。
18.本发明树脂塞孔铝片二合一制作方法,将传统的应用于pcb板上下面的不同的塞孔铝片设计为完全相同中的两块铝片的技术方案,使塞孔作业工序,上下铝片不会出现装反的情况,进而有效避免现有技术中因贴装时不容易,出现装反,进而导致塞孔一次不饱满,造成重复返工塞孔还不能保证塞孔的饱满度情况。
19.有背钻塞孔板的孔俩头的孔径大小不一样,现有技术中,设计对应面的大小孔对应铝片在贴网版的时候现场容易贴反,撕掉重新贴铝片容易变形报废。第一次塞未背钻孔,第二次塞背钻孔,烤完板磨完板以后才发现塞孔不饱满,重新补塞孔+烤板。而本发明改善以后只要正反面各塞一次烤完磨完板就可以达到要求,大大提高了效率。
20.本发明树脂塞孔铝片二合一制作方法,现有技术中,因pcb板上下面的塞孔铝片上的孔分别与相对应的背钻孔及背面的非背钻孔大小相适应,不仅造成易装反的情况出现,而且其导致装反后其背钻面的塞孔效果差,进而使整个塞孔的饱满度不够好。本发明更改后,将上下面的塞孔统一为孔大小均与背钻孔大小相适应的塞孔,进行该更改后,其塞孔大小与背钻面的背钻孔大小相适应,且大于非背钻面的孔,使没有背钻的一面孔小下树脂更多,进入孔的也更多,塞孔效果会更好,进而提升整个塞孔的饱满度,使整个塞孔的饱满度
会更好。
21.进一步地,所述的树脂塞孔铝片二合一制作方法,包括如下步骤,s1:铝片工程资料设计,以背钻孔为设计依据进行铝片钻孔工程资料设计;s2:铝片制作,根据s1步骤中设计的铝片工程资料进行钻孔生产铝片,生产铝片时直接一次生产出两张同样的铝片;s3:树脂塞孔,将s2步骤中制得的两张同样的铝片分别贴在pcb板的背钻面和非背钻面,然后从pcb板的背钻面和非背钻面同步向背钻孔进行树脂塞孔。
22.本发明树脂塞孔铝片二合一制作的方法,s步骤的铝片工程资料设计,其中,钻孔资料以背钻孔为依据进行设计,使铝片上钻孔大小与背钻孔相匹配和适应,为2步骤中铝片的生产提供基础和保障,s2步骤中一次生产出两张同样的铝片,确保装贴在pcb板上下两面的铝片是一样的,有效解决现有技术中因两片铝片不一样而出现的装反的情况,在铝片装贴完成后,s3步骤分别从pcb板的上下两面的铝片孔处同步向背钻孔进行灌树脂,完成树脂塞孔,该种作业方式使树脂塞孔饱满,返工率小,有效提升生产效率。
23.进一步地,s1步骤以背钻孔直径大小为基础,通过增加补偿的方法进行设计铝片工程资料,即是采用正常的直径+补偿的方法设计,该种方法为常规补偿设计方法,作业人员已经熟知,方便、高效。
24.进一步地,s2步骤前,还包括钻带制作,所述钻带制作时在料号位置设置标识。钻带的制作,用于确保铝片工程资料的设计,为铝片钻孔生产提供基础和保障。
25.进一步地,s2步骤中,还包括钻出与pcb板上通孔相对应的钻孔。
26.进一步地,s3步骤完成后,将pcb板放入烘烤工序进行烤板,使塞孔固化。
27.进一步地,烤板后,pcb板进入研磨工序进行研磨,使板面无树脂残留。
28.本发明树脂塞孔铝片二合一制作方法及方法与现有技术相比,具有如下有益效果:第一、产效率高,本发明方法采用一次直接生产出两张同样的铝片,减少了多次换机资料上传铝片的工序,降低了铝片工具生产备工具的准备时间,而且有效解决现有技术中因两片铝片不一样而出现的装反的情况,返工率小,大大提升了生产效率;第二、生产工艺简化,本发明方法采用一次直接生产出两张同样的铝片,减少了多次换机资料上传铝片的工序,使生产工艺得到简化;第三、产品品质好,本发明树脂塞孔铝片二合一制作的方法,s步骤的铝片工程资料设计,其中,钻孔资料以背钻孔为依据进行设计,使铝片上钻孔大小与背钻孔相匹配和适应,为s2步骤中铝片的生产提供基础和保障,s2步骤中一次生产出两张同样的铝片,确保装贴在pcb板上下两面的铝片是一样的,s3步骤分别从pcb板的上下两面的铝片孔处向背钻孔进行灌树脂,完成树脂塞孔,该种作业方式使树脂塞孔饱满,产品品质好。
29.上述实施例仅为本发明的具体实施例,其描述较为具体和详细,但并不能因此而理解为对本发明专利范围的限制。应当指出的是,对于本领域的普通技术人员来说,在不脱离本发明构思的前提下,还可以做出若干变形和改进,这些显而易见的替换形式均属于本发明的保护范围。