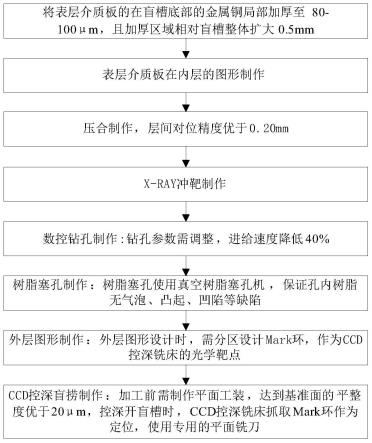
1.本发明涉及多层微波pcb产品技术领域,具体为表层介质板盲槽底部含金属化孔的多层微波板的制作方法。
背景技术:2.传统多层微波板的盲槽内含有图形,盲槽与槽内图形和金属化孔分别属于两张不同的介质板上,一般通过盲槽底部预先钻孔、制作内层图形、压合得到所述结构,其可加工性较好。针对在表层介质板上含盲槽且盲槽内含塞孔的金属化孔和金属图形的多层微波电路板,传统的制作方法无法实现,该产品结构的具体特征如下:
3.(1)在一张介质板上开盲槽,盲槽底部为金属图形;
4.(2)盲槽内含金属化孔与槽底金属图形相连,该金属化孔需塞孔;
5.(3)盲槽周围的表面图形为高精度的微带线,且微带线与盲槽距离≤0.075mm;
6.(4)产品对塞孔质量要求高,槽底平整度要求高;
7.(5)盲槽深度公差要求高:
±
35μm。
8.以某款八层微波产品为例,盲槽1-2(非传统的盲槽1-3)内含有盲孔2-8的特殊结构设计,其叠层图如图2所示,盲槽结构的俯视图如图3所示。
9.本发明所述针对多层微波板的特殊设计结构:盲槽与槽内图形和金属化孔均属于同一张的介质板上,且产品质量要求高。若采用传统的方案:整体压合+co2激光开盲槽+盲槽和盲孔金属化的制作方案,则无法实现金属化孔塞孔和高平整度的要求;若采用传统的方案:通孔金属化+塞孔+co2激光开盲槽,则盲槽内的金属化孔内填充物受损产生凹陷,槽底平整度无法保证,且盲槽内残留金属铜柱;同时传统机械铣加工,无法保证盲槽与外层微带线距离≤0.075mm的高精度要求,无法满足盲槽深度
±
35μm的高精度要求。为了解决了所述多层微波的特殊结构无法实现的问题,本发明提出了一种全新的制作方法,可实现盲槽内金属图形完整、平整度高,盲槽内金属化孔与金属图形可靠连接,盲槽与表面微带线对位精度高,做到了全新特殊结构设计的多层微波电路板的可靠工艺实现。
技术实现要素:10.针对现有技术的不足,本发明提供了表层介质板盲槽底部含金属化孔的多层微波板的制作方法,解决了针对多层微波板的特殊设计结构:盲槽与槽内图形和金属化孔均属于同一张的介质板上,且产品质量要求高,传统工艺无法实现的问题。
11.为实现以上目的,本发明通过以下技术方案予以实现:表层介质板盲槽底部含金属化孔的多层微波板的制作方法:包括以下步骤:
12.步骤a:采用图形电镀工艺,将表层介质板在盲槽底部的金属铜局部加厚;
13.步骤b:表层介质板在内层的图形制作完成后,开展整体压合制作;
14.步骤c:压合完成后,开展x-ray冲靶、数控钻孔制作;
15.步骤d:钻孔完成后,开展孔金属化、塞孔制作;
16.步骤e:塞孔完成后,开展外层图形制作;
17.步骤f:外层图形制作完成后,开展ccd控深铣床开盲槽制作。
18.作为本发明进一步的方案:所述盲槽底部的金属铜局部加厚至80-100μm,且加厚区域相对盲槽整体扩大0.5mm。
19.作为本发明进一步的方案:所述压合对位精度需优于0.20mm。
20.作为本发明进一步的方案:所述局部镀铜加厚区域的钻孔参数需调整,进给速度降低40%。
21.作为本发明进一步的方案:所述塞孔需使用真空塞孔机,保证孔内无气泡、凸起、凹陷等缺陷。
22.作为本发明进一步的方案:所述外层图形设计时,需分区域设计mark环,作为ccd控深铣床的光学靶点,实现xy平面的涨缩、偏转角度动态补偿,为盲槽与微带线高精度对位做好准备。
23.作为本发明进一步的方案:所述控深铣床开盲槽面前,使用真空吸附台面需制作专用平面工装,达到基准面的平整度≤20μm;控深盲槽加工时,ccd控深铣床抓取图形的mark环作为定位,同时使用专用的平面铣刀,实现盲槽深度公差
±
35μm、盲槽与微带线距离≤0.075mm的高精度要求,实现控深开盲槽可控加工。
24.本发明与现有技术相比具备以下有益效果:针对在表层介质板上含盲槽且盲槽内含塞孔的金属化孔和金属图形,解决了所述多层微波的特殊结构无法实现的问题,且盲槽内金属图形完整、平整度高,盲槽内金属化孔与金属图形可靠连接,盲槽与表面微带线对位精度高,做到了全新特殊结构电路板的可靠工艺实现。
附图说明
25.图1为本发明的工艺流程图;
26.图2为八层微波产品的叠层图;
27.图3为八层微波产品盲槽结构的俯视图;
28.图4为表层介质板的在盲槽底部的金属铜局部加厚示意图。
具体实施方式
29.为更进一步阐述本发明为实现预定发明目的所采取的技术手段及功效,以下结合附图及较佳实施例,对依据本发明的具体实施方式、结构、特征及其功效,详细说明如后。
30.请参阅图1-4,本发明提供一种技术方案:表层介质板盲槽底部含金属化孔的多层微波板的制作方法,包括以下步骤:
31.步骤a:采用图形电镀工艺,将表层介质板在盲槽底部的金属铜局部加厚;
32.步骤b:表层介质板在内层的图形制作完成后,开展整体压合制作;
33.步骤c:压合完成后,开展x-ray冲靶、数控钻孔制作;
34.步骤d:钻孔完成后,开展孔金属化、塞孔制作;
35.步骤e:塞孔完成后,开展外层图形制作;
36.步骤f:外层图形制作完成后,开展ccd控深铣床开盲槽制作。
37.盲槽底部的金属铜局部加厚至80-100μm,且加厚区域相对盲槽整体扩大0.5mm。
38.压合对位精度需优于0.20mm。
39.局部镀铜加厚区域的钻孔参数需调整,进给速度降低40%。
40.塞孔需使用真空塞孔机,保证孔内无气泡、凸起、凹陷等缺陷。
41.外层图形设计时,需分区域设计mark环,作为ccd控深铣床的光学靶点,实现xy平面的涨缩、偏转角度动态补偿,为盲槽与微带线高精度对位做好准备。
42.控深铣床开盲槽面前,使用真空吸附台面需制作专用平面工装,达到基准面的平整度≤20μm;控深盲槽加工时,ccd控深铣床抓取图形的mark环作为定位,同时使用专用的平面铣刀,实现盲槽深度公差
±
35μm、盲槽与微带线距离≤0.075mm的高精度要求,实现控深开盲槽可控加工。
43.将表层介质板在盲槽底部的金属铜局部加厚至80-100μm,且加厚区域相对盲槽整体扩大0.5mm;表层介质板在内层的图形制作完成后,开展整体压合,压合的压合对位精度需优于0.20mm;x-ray冲靶完成后,开展数控钻孔制作,局部镀铜加厚区域的钻孔参数需调整,进给速度降低40%;通孔金属化后,开展塞孔制作,塞孔需使用真空塞孔机,保证孔内无气泡、凸起、凹陷等缺陷;外层图形设计时,需分区域设计mark环,作为ccd控深铣床的光学靶点,实现xy平面的涨缩、偏转角度动态补偿,为盲槽与微带线高精度对位做好准备;外层图形制作完成后,控深铣床开盲槽面前,使用真空吸附台面需制作专用平面工装,达到基准面的平整度≤20μm;控深盲槽加工时,ccd控深铣床抓取图形的mark环作为定位,同时使用专用的平面铣刀,实现盲槽深度公差
±
35μm、盲槽与微带线距离≤0.075mm的高精度要求,实现控深开盲槽可控加工。最终做到了全新特殊结构设计的多层微波电路板的可靠工艺实现。
44.以上所述,仅是本发明的较佳实施例而已,并非对本发明作任何形式上的限制,虽然本发明已以较佳实施例揭示如上,然而并非用以限定本发明,任何本领域技术人员,在不脱离本发明技术方案范围内,当可利用上述揭示的技术内容做出些许更动或修饰为等同变化的等效实施例,但凡是未脱离本发明技术方案内容,依据本发明的技术实质对以上实施例所作的任何简介修改、等同变化与修饰,均仍属于本发明技术方案的范围内。