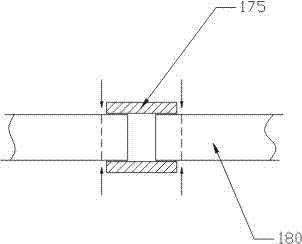
本发明涉及核裂变反应堆及其运行的方法。
背景技术:地球上已知可利用的重核裂变的核素转化组合有两组U-238/Pu-239和Th-232/U-233,相对应的主要核原料分别是:前者对应天然铀、核废料(包括贫铀),后者对应的是钍。除开核聚变能,已知地球上钍铀所含的能量远大于其它矿物能源储量的总和,其中钍储量比铀大4倍。如果采用快堆,核燃料利用率可以提高到60-70%,乐观的估计认为全球可利用钍铀资源可以维持人类2万年以上的全部能源需求。但目前的主力核电技术-压水堆的燃料利用率只有区区0.17%(以天然铀计算),产生的核废料量大,还有高压爆炸的危险性。显然压水堆不能作为未来核电的发展方向,核电行业越来越认同以快堆为主的先进核电的开发,以气冷堆和铅冷堆为代表的第四代核电技术开始崭露头角,以ADS和钍反应堆为推手的第五代核电技术的研究与开发也在悄然进行中。U-238/Pu-239的转化在快堆中已不是问题,但Th-232/U-233的转化就不同了,中间产物Pa-233衰变成U-233的半衰期长达27天,完全衰变需要300天,对反应堆来说这个时间太长,给反应堆的运行和控制带来困难。初装主燃料U-233的获取很困难,主要原因是:钍基乏燃料的γ射线强;乏燃料中烧结的钍基氧化物极难溶解;反应堆运行过程中堆芯中积累的Pa-233易俘获中子转化为不易裂变元素,会降低U-233的产率。这些难题迄今没有得到有效的解决,虽然采用加速器散裂中子源照射Th-232获取U-233也是好的途径,但因高能质子加速器成本及能耗太高,且难以长时间稳定运行,不宜大规模推广。一般认为最好的解决途径是反应堆在线提取中间产物Pa-233。在钍能发展过程中,最令人难忘的是“氟化钍熔盐堆”,氟化钍熔盐堆试验中曾经尝试在线提取钍/铀转化的中间产物Pa-233。遗憾的是这一卓越的核反应堆超越了材料学的极限,最耐熔盐腐蚀的特制Hastelloy-N合金在运行中也发生了危险的回路晶间腐蚀。目前攻克熔盐堆的材料腐蚀难题的可能性依然渺茫,即使将来攻克了材料腐蚀难题,高昂的材料和运行成本也将成为难以逾越的沟坎。熔盐堆还存在两个弱点:一回路熔盐承担的功能过多,多功能捆绑导致相互制约;高放射性且成分复杂的一回路熔盐必须频繁进行高耗能的纯化处理,在线熔盐管理复杂且自耗能大。二十世纪五、六十年代,美国阿贡实验室R.AVERY等人提出并研发过快-热中子耦合增殖反应堆,堆芯包括快中子能谱堆芯和热中子能谱堆芯,快中子能谱堆芯以饱和水蒸汽作慢化剂,以获取较硬的中子能谱,热中子能谱堆芯以加压水做慢化剂。中国学者张育曼和李玉崙在2008年提出过类似设计的水冷双区增殖核反应堆。一九六〇年代,为了提高核电站热效率、节省核燃料,美国通用电气公司(GE)研发过在沸水堆内产生饱和蒸汽,使堆芯产生较硬的中子能谱,形成快-热中子混合能谱型反应堆。严格来讲,这些设计的堆芯都使用水或者水蒸汽作慢化剂,快中子量少,能谱仍然属于热中子范畴,由于工程难度大于压水堆,经济性不高,至今均未得到工程实施。如果进一步拓展“快-热中子耦合核反应”的研究,也许能找到开发另类核电技术的新途径。快中子堆芯是否能进行快-热中子耦合核反应?是否能将慢化剂与快中子堆芯隔离?是否能解除慢化剂和冷却剂的功能捆绑?是否可以在堆芯外使用慢化剂提高快堆的核反应效率?是否能降低核反应容器内的物理条件,并实施增殖燃料在线提取?迄今为止,没有查阅到关于在快堆内使用慢化剂或以快中子堆芯为主体的快-热中子耦合核反应堆的相关文献。
技术实现要素:“钍增殖燃料在线提取”与“钍/铀高效转化及安全分离”问题由来已久,六十多年以来一直是制约“钍核反应堆”研究与开发的关键技术瓶颈,成为一大世纪难题。本发明的目的是为上述难题以及目前核电技术的一些缺陷提供一种解决方案。本发明涉及快堆型耦合核反应,该核反应是以快中子堆芯为主体的快-热中子耦合核反应,其具体实施方法是:(一)、将反应堆主容器拆分为相互完全隔离的裂变池和慢化池;慢化池内置慢化剂;裂变池内设置堆芯,堆芯具有快中子堆芯特性;将慢化剂与主冷却剂分离,裂变池和堆芯无慢化剂,主冷却剂通过裂变池而不通过慢化池。(二)、将裂变池和慢化池相互镶嵌或可移动式组合,使两者结构和功能耦合;在裂变池和慢化池之间设置隔热层,阻隔两者的热交换,使慢化池控制在接近常温常压的状态。(三)、允许中子穿过裂变池和慢化池之间的构造,使裂变池与慢化池能进行中子交换并进行耦合核反应,堆芯产生的快中子和从慢化池内反射进入裂变池的慢化中子可使堆芯同时进行快中子和慢化中子(包含热中子和中能中子)引发的耦合核反应,裂变池具有快中子反应堆的特性和功能,慢化池内可进行热中子核反应(如热中子俘获反应)。(四)、优化反应堆主容器结构和材料,在反应堆主容器侧壁设置大面积薄壁构造的中子交换窗口,在保证结构强度的同时增加中子交换效率。(五)、在慢化池设置耦合核控系统,利用耦合核反应实施耦合核控和非能动停堆。利用慢化剂的慢化中子功能和慢化剂的可控性或慢化池的可控性位移,通过改变裂变池和慢化池之间的中子交换控制堆芯的反应性;停堆时运用非能动方法使慢化池快速排出慢化液或快速位移慢化池,慢化池失去中子慢化功能,终止慢化池向堆芯输送慢化中子,堆芯反应性快速下降导致链式裂变反应不能维持,从而实现非能动停堆。(六)、利用热中子核反应的高效性,在慢化池接近常温常压的条件下,实施核燃料增殖和增殖燃料的在线提取,在反应堆外实现Pa-233/U-233转化以及Th-232/U-233的分离。在慢化池设置可在线更换燃料的增殖燃料系统,初始增殖燃料原料只含一种核素Th-232,只进行Th-232的热中子俘获核反应,避免Pa-233和U-233俘获中子造成的中子和有效核燃料的双重损耗,提高增殖效率和中子利用率;慢化池物理条件温和,在线提取增殖燃料没有难度,后期的核素分离简单,只需进行Th-232/U-233两个元素非此即彼的简单分离。(七)、优化堆芯设计,如采用烛式堆芯设计,提高核反应效率和燃耗率。(八)、将反应堆主容器低矮化、简单化、低成本化和模块化,实施裂变池的整体更换或实施裂变池模块一次性退役(裂变池随堆芯更换而退役),提高维修效率和整体安全性。(九)、将反应堆主要部件模块化,使反应堆可拆分和组合。反应堆模块的拆分与重组的难点主要表现在管道的拆分与重组。采用易重组的套管连接和拆分方法,简化反应堆模块的拆分和重组。套管连接与拆分方法采用垂直套接或非垂直套接或非垂直转垂直套接。垂直套接:连接套管较长,可多次重复使用,下方管头为固定管头,上方管头为可拆分管头,两个管头在同一垂直轴心上,以垂直吊装进行安装。初次连接前,预先将连接套管焊接在下管头上,连接时上管头对准并少许插入连接套管后焊接,焊接面朝上操作简单且焊接效果最佳;拆分时只需在连接套管上端的焊接处下方切割分离,连接套管稍许减短;重组时清理连接套管内的残留物,上管头相比前次适当加长,重复前次的连接流程即可。非垂直套接:非垂直套接以水平管道连接为主,以垂直吊装进行安装,连接在拆分模块上的管头为可拆分管头,对应的另一管头为固定管头;连接套管较短为一次性部件,以后按需要逐次加长连接套管或适量加长可拆分管头。连接时预先在固定管头上套上连接套管但暂不焊接,滑动连接套管露出固定管头,两管头对齐后套上连接套管,然后分别焊接两端。拆分时需切割掉整个连接套管,重新组合时换上长度合适的新连接套管,重复前次的连接流程即可。非垂直套接的焊接难度高,焊接效果不易保证。非垂直转垂直套接:连接的两个管道为非垂直管道,将需连接的两个管头以弯头分别转化为同轴心的垂直管头,固定管头在下,可拆分管头在上,其后的连接、拆分和重组方法与垂直套接相同。本发明涉及一种快堆型耦合核反应堆,其主要特征为:(一)、反应堆主容器包括相互耦合并彼此隔离的裂变池和慢化池;慢化池内置慢化剂,裂变池内置堆芯,堆芯具有快中子堆芯特性;慢化剂与主冷却剂分离,慢化剂不进入裂变池;主冷却剂不进入慢化池。(二)、裂变池与慢化池完全隔离,两者之间设置隔热层阻隔热交换,隔热层为真空构造或填充隔热材料。(三)、裂变池与慢化池能进行中子交换但不进行热交换。(四)、主冷却剂为特定的液态金属或熔盐,特别是铅或铅铋共晶。(五)、慢化池填充慢化剂,慢化剂为固态慢化剂或液态慢化剂。固态慢化剂为石墨或铍化合物,特别是石墨。液态慢化剂为重水或重水溶液或轻水或轻水溶液,特别是重水。填充液态慢化剂的慢化池设置慢化剂回路。(六)、裂变池和慢化池组合形成主容器耦合构造,主容器耦合构造为单慢化池内置耦合结构或单慢化池外置耦合结构或双慢化池耦合结构。单慢化池内置耦合结构是慢化池位于反应堆中心为桶状池型构造,裂变池位于慢化池外侧呈环状池型构造。单慢化池外置耦合结构是裂变池位于反应堆中心为桶状池型构造,慢化池位于裂变池外侧呈环状池型构造或筒状构造。双慢化池耦合结构是内慢化池位于反应堆中心为桶状池型构造,外慢化池位于外侧为环状池型构造,裂变池位于内外慢化池之间为环状池型构造。(七)、主容器耦合构造可设置为可拆分的组合式结构。(八)、反应堆主容器外周可设置主容器外壳,主容器外壳为一个加厚的池型金属壳体,裂变池和慢化池放置并固定在主容器外壳之内。本发明涉及的快堆型耦合核反应堆分6大部分进行说明:反应堆主容器;堆芯与燃料元件;慢化液回路及核控系统;增殖燃料系统;其他设施;快堆型耦合核反应堆类型。反应堆主容器反应堆主容器包括裂变池、慢化池和主容器外壳。快堆型耦合核反应堆主容器(特别是裂变池)侧壁可设置大面积中子交换窗口,中子交换窗口为薄壁构造,薄壁构造为框架蒙皮结构或薄壁筋板结构。框架蒙皮结构是在中子交换区域的侧壁部分设置框架,在框架上设置薄板蒙皮,框架蒙皮结构以外的主容器部分可采用非薄壁构造,如底板、靠近底部和顶部的侧壁可采用厚壁构造。薄壁筋板结构是侧壁以薄壁为主体,薄壁上设置筋板加固。框架蒙皮结构或薄壁筋板结构可以一次性整体构建。主容器侧壁垂直对称位置可设置主筋板或主框架,吊装承力由主筋板或主框架承担。在主容器承力大的位置可设置特别的加固结构,如主冷却剂出口处设置或加强筋板或加强框架。裂变池侧壁与慢化池侧壁之间设置侧壁隔热层,侧壁隔热层材料为固体颗粒;裂变池侧壁与慢化池侧壁通过侧壁隔热层传递侧向压力形成相互侧向支撑,类似于轮胎的外胎对内胎的支撑。裂变池结构材料难以达到很高的中子透明度,需要采用薄壁构造;慢化池和隔热层可以选用很高中子透明度的材料,相对较厚的慢化池可以对裂变池侧壁起到侧向支撑作用。侧壁隔热层的固体颗粒可以选择蜂窝状颗粒或蜂窝状球粒或空心球粒或实心球粒或实心颗粒,其中以不规则的蜂窝状颗粒最佳,其核密度小,不易流动,易填装和吸除。固体颗粒成分具有坚固、耐热、高热阻和对中子透明的特性,如二氧化硅、硅铝氧化物、氧化锆或氧化铝,其中二氧化硅性价比最高。如果使用球粒则需在侧壁隔热层最上部增设压紧装置限制隔热材料移动,防止裂变池变形;压紧装置结构包括压紧弹簧、压块和弹簧固定器。裂变池底部设置承重隔热层,承重隔热层为块状固体,具有坚固、耐热的特性,如隔热陶瓷块,承重隔热层材料对中子透明性没有要求,具有吸收中子能力的材料可能更好,可起到底部中子屏蔽作用,可采用廉价的非核级材料。裂变池顶盖或慢化池顶盖可采用密封剂进行密封,传统的法兰盘密封不仅笨重体积大而且要求精度高,不适应于镶嵌紧密的裂变池和慢化池的顶盖密封。顶盖采用密封剂密封可简化密封结构,减轻主容器顶盖的重量。密封剂为金属密封剂或密封胶,金属密封剂为易熔金属或者易熔合金,特别是重金属及其合金。密封胶只适合低温型容器,如慢化池。容器侧壁上缘设置环状沟槽,环状沟槽的内缘高于外缘防止密封剂落入容器内,容器顶盖外缘向下设置环状裙板。顶盖与侧壁的密封结构可设置锁紧装置,防止顶盖被内部压力冲开,锁紧装置为螺纹构造或螺栓构造或弹力卡具;封盖时先在环状沟槽内均匀填充适量的液态密封剂,在密封剂凝固前将环状裙板插入环状沟槽内,再扣紧锁紧装置,密封剂凝固即形成密封构造;金属密封剂凝固使顶盖与侧壁形成牢固的密封结构,分离时加热密封结构使金属密封剂熔化即可;采用易熔金属的密封结构可设置加热装置。裂变池选择重金属密封剂,慢化池选择耐温耐腐蚀的密封硅胶。设置有薄壁构造的裂变池需要尽量减轻顶盖重量,当裂变池顶部设置有裂变池气室时,裂变池顶盖不受主冷却剂腐蚀的影响可重复使用,可采用轻质高强度材料,如钛合金。慢化池材料选择中子透明度高的金属,如铝、铝合金、锆合金、铝锆合金、铝钛合金、锆铌合金、镍铝合金。其中铝基金属材料性价比最高,能满足慢化池低温低压条件下的耐水蚀要求。为了进一步提高铝基金属的耐水蚀性,铝或铝合金的慢化池表面可以镀上耐水蚀金属,耐水蚀金属为锆或镍或钛。堆芯与燃料元件堆芯与燃料元件的内容包括:堆芯特性与结构;燃料内胆;闭式燃料棒;棒束闭式燃料组件;套管闭式燃料组件;开口式燃料棒;棒束开口式燃料组件;套管开口式燃料组件;排气构件(含无阀排气构件和有阀排气构件);燃料组件和燃料棒的固定与定位;燃料化学成分与物理形态。堆芯特性与结构:快堆型耦合核反应堆的裂变池内设置耦合堆芯,其具有快中子堆芯的特性。耦合堆芯为固态堆芯,由燃料棒组件构成,燃料棒组件由燃料棒组合构成,燃料棒内可设置燃料内胆,燃料填充进燃料内胆或燃料棒。燃料组件为棒束燃料组件或套管燃料组件,棒束燃料组件无主套管,套管燃料组件有主套管。燃料棒为闭式燃料棒或开口式燃料棒,闭式燃料棒构成棒束闭式燃料组件或套管闭式燃料组件;开口式燃料棒构成棒束开口式燃料组件或套管开口式燃料组件。耦合堆芯边缘可以进行补缺,使堆芯边缘趋近完整。棒束闭式燃料组件、套管闭式燃料组件、棒束开口式燃料组件或套管开口式燃料组件四种燃料棒组件可分别有相对应的半形组件或异形组件,半形组件或异形组件对堆芯边缘的缺刻进行补缺。半形组件横切面是对应的组件横切面的对角线切分的一半,异形组件横切面可以是任意形状,形状的选择取决于补缺效果。堆芯下方设置堆芯底座,堆芯固定在堆芯底座上,堆芯底座则固定在裂变池底板上,堆芯主要由裂变池底板承力,以此降低裂变池侧壁的承力。耦合堆芯可设计为烛式堆芯;烛式堆芯从下往上逐步燃烧,初装易裂变核素主要分布于堆芯燃料区下方,其浓度梯度是下高上低,上部燃料通过增殖反应累积,其累积速度与燃烧区上移速度相适应,堆芯燃耗率是越往下部越高,这种堆芯易裂变核素初装量比较节省,堆芯寿命长,总燃耗深度大。耦合堆芯设置二种或三种特性的径向分区。二种特性的径向分区:靠近慢化池的区域为耦合区,远离慢化池的为快谱区。三种特性的径向分区:在耦合区与快谱区之间增设缓冲区增强堆芯安全性;耦合区同时进行热中子和快中子核反应,其燃料成分配比接近于热中子堆芯;快谱区进行快中子核反应,其燃料成分配比接近于快中子堆芯;缓冲区燃料成分配比特性由堆芯安全性设计确定。特殊堆型的堆芯外围可增设转换燃料区或屏蔽区。燃料内胆:快堆型耦合核反应堆采用燃料棒组件堆芯,传统的燃料棒是燃料直接填充进燃料棒内。燃料内胆是燃料的包裹体,以整体形式填充进燃料棒内,隔离燃料与燃料棒。燃料内胆最先承受燃料的应力和腐蚀,保护燃料棒包壳管。燃料内胆是密封件,可以单独长期存放。燃料内胆主体包括内胆管、底塞、顶塞、填充物、压紧弹簧、注气孔或注气管。燃料内胆外径略小于燃料棒包壳管内径,预留燃料膨胀空间。内胆管为燃料内胆的包壳,内胆管两端由底塞和顶塞密封。顶塞设置有注气孔或注气管,燃料内胆内设置填充物和压紧弹簧,填充物包括燃料。注气孔或注气管供抽气或注气或排气之用,注气孔为孔状,注气管为短管状;注气孔或注气管可设置为自开式密封结构,在完成注气后进行密封。燃料内胆在升温或升压或升温加升压后,注气孔或注气管自行开口排气;自开式密封结构为可爆裂构造或可熔密封塞。可爆裂构造:注气管可爆裂,爆裂类型为低强度材料爆裂或低强度结构爆裂;低强度材料是注气管材质为低强度材料或受热后强度变低的材料,当燃料内胆温度升高内部气压增高,注气管受压爆裂自行开口排气;低强度结构是注气管上设置爆裂槽,爆裂槽处注气管壁很薄,气压差使爆裂槽形成裂缝,注气管开裂排气。可熔密封塞:可熔密封塞在升温后可熔化,可由单一密封剂或多种密封剂构成;多种密封剂是多种熔点不同的密封剂,密封塞外层熔点低于内层,密封时外层密封剂相当于钎焊料,堆芯启动升温后密封塞受热完全熔化,注气孔开通排气。燃料内胆顶端可增设防护罩,防护罩为指套管状或帽状,防护罩上布有孔隙供气体交流,防护罩设置于注气孔或注气管外。在燃料内胆完成注气密封后,指套管状防护罩直接焊接在顶塞顶端;在燃料内胆填装进燃料棒时,帽状防护罩由燃料棒压紧弹簧固定在顶塞之上。防护罩防止爆裂物或喷溅物接触燃料棒包壳管;燃料棒或燃料内胆可填充传热介质,如氦气、钠。闭式燃料棒:闭式燃料棒是传统燃料棒的闭式结构,闭式燃料棒的主体结构为两端封闭的棒状包壳管构造,闭式燃料棒主体包括下端塞、包壳管、压紧弹簧、上端塞、填充物或燃料内胆。上端塞和下端塞密封包壳管两端,包壳管内有长的气腔,气腔位于上部或下部,填充物或燃料内胆上设置压紧弹簧;燃料棒或燃料内胆内的填充物设置相同,核素填充物分三个区,从下往上分别为:下转换区、燃料区和上转换区,转换区只初装可转换核素,燃料区初装有易裂变核素。棒束闭式燃料组件:棒束闭式燃料组件主体包括下管座、棒束底栅板、骨架管、定位格架、闭式燃料棒和上管座。骨架管、定位格架和上下管座共同构成燃料棒组件的骨架,多个定位格架固定在骨架管束上,骨架管两端与上下管座固定。骨架管为两型,第一型是贯通空管,可用作导向管(如测量用导向管);第二型是实管,实管两端焊接有端塞,端塞与上下管座固定,管内设置有可转换燃料、压紧弹簧和较短的气腔,实管相当于转换燃料棒。燃料棒从定位格架中穿过并被约束定位;燃料棒固定在棒束底栅板上,棒束底栅板固定在下管座上端或者固定在骨架管上。下管座设置有定位插销或插销孔与堆芯底栅板定位,下管座设置有固定构造(如螺栓构造)将组件固定在堆芯底栅板上。上管座有定位插销与堆芯顶栅板上的插销孔定位。套管闭式燃料组件:套管闭式燃料组件主体包括管脚、棒束底栅板、主套管和闭式燃料棒。管脚设置有密封构造防漏流,管脚还设置有固定构造(如螺栓构造)与堆芯底栅板固定,管脚上有多个冷却剂入孔和控制漏流量的结构,主套管下端与管脚连接,燃料棒位于主套管内,燃料棒之上可增设上屏蔽体,燃料棒中段定位采用网格定位或绕丝定位,燃料棒底端与棒束底栅板固定,棒束底栅板固定在主套管下端或管脚上端,主套管顶端设置有吊装操作头和冷却剂出口,主套管外侧上部设置有垫块维持组件之间的距离。开口式燃料棒:开口式燃料棒及其组件与传统燃料棒及其组件的最明显不同之处是上部设置有排气构造。开口式燃料棒主体结构为底端封闭和顶端开口的棒状包壳管构造,顶端开口处设置有排气细管。开口式燃料棒主体包括下端塞、包壳管、压紧弹簧、上端塞、排气细管、填充物或燃料内胆。燃料棒两端分别焊接有端塞,底端由下端塞密封,上端塞上设置开口,开口处焊接有排气细管,裂变气体由排气细管排出。开口式燃料棒无气腔或有较短的上气腔,填充物或燃料内胆上设置压紧弹簧;燃料棒或燃料内胆内的填充物设置相同,核素填充物分三个区,从下往上分别为下转换区、燃料区和上转换区,上下转换区只初装可转换核素,燃料区初装有易裂变核素。燃料棒填充物可增设一个或两个屏蔽区,屏蔽区设置中子吸收体屏蔽剩余中子,增加堆芯轴向屏蔽功能。设置一个屏蔽区:在填充物最上部设置一个上屏蔽区;设置两个屏蔽区:在填充物的最下部设置下屏蔽区和上部设置上屏蔽区。燃料棒填充物可增设吸附区,吸附区填充蜂窝状固态吸附剂吸附裂变挥发物,吸附区位于上转换区与上屏蔽区之间或者位于填充物最上端,吸附区与上屏蔽区可以交换位置。燃料棒填充物从下往上可有六种分区组合:下转换区-燃料区-上转换区;下转换区-燃料区-上转换区-吸附区;下转换区-燃料区-上转换区-上屏蔽区;下转换区-燃料区-上转换区-吸附区-上屏蔽区;下屏蔽区-下转换区-燃料区-上转换区-上屏蔽区;下屏蔽区-下转换区-燃料区-上转换区-吸附区-上屏蔽区。棒束开口式燃料组件:棒束开口式燃料组件主体包括下管座、棒束底栅板、骨架管、定位格架、开口式燃料棒、上管座和排气构件。骨架管、定位格架和上下管座共同构成燃料组件的骨架,多个定位格架固定在骨架管束上,骨架管两端与上下管座固定。骨架管分两型,第一型是贯通空管,可用作导向管(如核测用导向管);第二型是实管,实管两端焊接有端塞,通过端塞与上下管座固定,实管内设置有可转换燃料、压紧弹簧和较短的气腔,实管相当于转换燃料棒。燃料棒从定位格架中穿过并被约束定位,燃料棒下端固定在棒束底栅板上,棒束底栅板固定在下管座上端或者固定在骨架管上。套管开口式燃料组件:套管开口式燃料组件主体包括管脚、棒束底栅板、主套管、开口式燃料棒和排气构件。管脚设置有密封构造防漏流,管脚还设置有固定构造(如螺栓构造)与堆芯底栅板固定,管脚上有多个冷却剂入孔和控制漏流量的结构。燃料棒中段定位采用网格定位或绕丝定位,燃料棒底端与棒束底栅板固定,棒束底栅板固定在主套管下端或管脚上端。主套管外侧上部可设置垫块维持组件之间的距离。开口式燃料棒组件可设置棒束顶栅板。棒束顶栅板固定在燃料组件主体的上端,即上管座内或主套管上端,棒束顶栅板上设置有定位孔和冷却剂孔,排气细管穿过棒束顶栅板上的定位孔使燃料棒被定位,燃料棒上端塞和棒束顶栅板间设置防振弹簧,防振弹簧套在排气细管基部。需要顶端定位的排气细管基部可适当加粗加厚,增强抗外力的强度。排气构件:开口式燃料棒组件的上部设置排气构件,排气构件下端与燃料组件主体连接。排气构件主体包括约束部和排气主管。排气构件下部为约束部,约束部为套管形或喇叭形或爪形;套管形约束部上端可设置约束部承接板,约束部承接板设置有冷却剂出孔和衔接其他部件的固定构造;排气构件上部是排气主管。排气主管顶端设置泄压阀或者不设置泄压阀;设置泄压阀的排气构件为有阀排气构件,不设置泄压阀的排气构件为无阀排气构件。排气构件外侧可设置吊装操作头。无阀排气构件:无阀排气构件主体包括约束部、排气细管集束和排气主管,排气细管经简单约束成紧密的排气细管集束后直接套入排气主管,排气细管在排气主管内可以伸缩。有阀排气构件:有阀排气构件主体包括约束部、密封套管、排气细管集束、密封头、排气主管和泄压阀。泄压阀设置在排气主管顶端,有阀排气构件内排气细管在约束部先经旋曲约束后,其上端部分再约束成紧密的排气细管集束,即排气细管在约束部区段内为松散的旋曲状态,被扭曲的排气细管有类似弹簧的功能,有一定屈伸功能缓冲燃料棒变形应力,并满足燃料棒辐照伸长的需求。密封套管下端与约束部上端固定,密封套管内套入排气细管集束,两者在顶端整体密封(如钎焊密封)后构成可排气的密封头,排气主管再与密封套管密封固定,使裂变气体只能通过排气主管和泄压阀排出。钎焊料一般难于满足耐高温和抗腐蚀的高需求,钎焊密封的密封头需要与主冷却剂隔离,适当加长密封套管,灌注主冷却剂时密封套管内会留存潴留气体,这部分不能排出的潴留气体成为密封头与主冷却剂的隔离层。排气主管上设置有注气孔或注气管,燃料组件制造完成后进行抽真空和注气处理并封闭注气孔或注气管。密封头采用钎焊密封,其工艺流程为:燃料棒制作完成后抽真空并封闭排气细管末端(如感应加热后机械压封),封闭排气细管前可根据需要灌注检测气体,排气细管长度以顶端略长于密封套管顶端为宜→完成燃料棒气密性和探伤检查→完成燃料棒组件的主体组装→对排气细管进行退火并旋曲约束其下部→再约束排气细管上部形成紧密的排气细管集束→焊接约束部与密封套管连接处→连接约束部与燃料组件主体并使排气细管集束套进密封套管→用金属丝塞紧排气细管之间的缝隙→密封处进行表面处理→加热焊料池至焊料熔化(焊料熔点高于主冷却剂最高运行温度)→倒立燃料棒组件,将密封处插入焊料池内合适深度,待焊液充分浸入后取出冷却凝固成密封头→整理打磨抛光密封套管→切割掉密封头的最末端,整理打磨排气细管端口,确保每根排气细管畅通。泄压阀:有阀排气构件顶端设置泄压阀,泄压阀为弹簧型泄压阀或易熔重金属泄压阀或双泄压阀。有阀排气构件的排气主管内可设置排气吸附区,排气吸附区包括吸附体定位器、吸附体和吸附体压紧弹簧。吸附体为布有筛孔的棒状盒体,其内填充吸附剂。吸附体定位器为定位弹簧或弹性卡具,防止吸附体位移。吸附体压紧弹簧压紧吸附体,防气流冲击和位移。弹簧型泄压阀:弹簧型泄压阀为圆柱状,其主体包括阀壳体、下阀体、上阀体、弹簧、弹簧定位头和压紧螺丝。阀壳体为圆筒状,下阀体侧面与阀壳体固定并密封;下阀体与上阀体为凸凹面对应的阀门结构,凸凹面紧贴可实现密封,凸凹面分开可实现排气泄压;下凸上凹的对应结构有利于气体冲刷掉凝结物,阀体不易结垢;下阀体正中设置通气孔,上阀体侧边设置通气孔;上阀体上端与弹簧连接,弹簧上端连接有弹簧定位头,压紧螺丝向下压紧弹簧定位头,压紧螺丝与阀壳体上端以螺纹固定,弹簧定位头和压紧螺丝设置通气孔供气体排出。易熔重金属型泄压阀:易熔重金属型泄压阀的阀门功能由液态重金属替代,易熔重金属型泄压阀包括环形凹槽、帽盖、易熔重金属和防脱堵头。帽盖即为上阀体,为盲管形,环形凹槽为下阀体,帽盖与环形凹槽形成有间隙的镶嵌构造,环形凹槽的间隙内填充易熔重金属,易熔重金属为密封剂,防脱堵头防止帽盖被内部高压气流冲脱,如防脱螺丝。易熔重金属型泄压阀的工作温度在易熔重金属的熔点之上,低于工作温度时凝固的重金属相当于焊料起固定和密封作用;在泄压时压差力推动气体穿过重金属液体构成的U型通道,压力差由重金属液体的比重和高度决定。环形凹槽可为单体构件或复体构件,单体构件的环形凹槽即下阀体为环形凹槽状整体;复体构件的环形凹槽由阀壳体、下阀体和中心气管焊接密封后构成。双泄压阀:双泄压阀是开口式燃料组件顶端串联两个泄压阀,下方泄压阀为易熔重金属型泄压阀,上方为弹簧型泄压阀,其下阀体可作为易熔重金属型泄压阀的防脱堵头。双泄压阀的优点是密封效果好,低温时凝固的重金属能彻底密封,高温时双泄压阀起双保险作用,重金属液体还可以吸收裂变气体中的挥发物,防止阀体结垢,增加弹簧型泄压阀的可靠性。燃料组件和燃料棒的固定与定位:快堆型耦合核反应堆主冷却剂主要采用重金属,堆芯的浮力很大,燃料棒和燃料组件适合采用在底部固定和在顶部定位。底部固定有利于抗主冷却剂浮力和上冲力,燃料组件的受力向上可降低燃料棒及组件的弯曲变形。顶部定位限定径向位置,燃料棒和燃料组件仍然可以垂直位移,以满足材料辐照伸长的需求。燃料组件固定与定位方式:可以采用堆芯底栅板固定,燃料组件的下管座或管脚与堆芯底栅板固定,如螺栓固定;燃料组件顶部可采用堆芯顶栅板定位,闭式燃料棒组件以上端的定位销与堆芯顶栅板进行定位。开口式燃料棒组件以排气主管上端穿过堆芯顶栅板的定位孔进行定位,排气主管与堆芯顶栅板之间设置或不设置防振弹簧。设置防振弹簧:排气主管上设置定簧凸圈,防振弹簧套在排气主管上,防振弹簧下端抵在定簧凸圈上,防振弹簧上端顶住堆芯顶栅板,防振弹簧可防止燃料组件振动,也能满足组件辐照伸长。燃料棒固定方式:燃料组件下部设置有棒束底栅板,燃料棒固定在棒束底栅板上,固定方式可为螺纹固定或焊接固定或镶嵌式固定。螺纹固定:燃料棒下端塞端部与棒束底栅板设置用于定位的凸台、凹槽和用于固定的螺孔,先镶嵌凸台和凹槽定位(可防止燃料棒旋转松动)再用螺钉进行螺纹固定;另外一种构造是燃料棒下端塞端部与棒束底栅板相互设置对应的螺丝和螺孔进行螺纹固定。焊接固定:燃料棒下端塞端部设置槽口,棒束底栅板的条形栅板插入下端塞的槽口再焊接固定。镶嵌式固定:燃料棒下端塞端部设置键槽,棒束底栅板上设置相对应的棒束导轨,棒束导轨滑进键槽进行镶嵌式固定。燃料化学成分与物理形态:快堆型耦合核反应堆可以采用传统的氧化物陶瓷燃料也可以采用先进陶瓷燃料,如氮化物或碳化物或硅化物燃料;可以采用芯块燃料,也可采用颗粒燃料。燃料内胆更适宜直接填充颗粒燃料,可以解决先进陶瓷燃料不易烧结成型的难题,燃料内胆可约束颗粒燃料自烧结成型。燃料颗粒与内胆管接触紧密,内胆管承受最先的膨胀应力,当燃料逐渐膨胀到最大直径后,燃料内胆与包壳管被压紧在一起,传热效率增加,整体传热效率优于芯块燃料,有利降低燃料棒温度。最初的传热可依靠气体或液体传热介质,如氦气或钠。燃料内胆将燃料与包壳管隔离,减轻了包壳管所受应力和腐蚀,包壳管不易破裂,有利延长燃料棒寿命。燃料内胆使燃料棒包壳管内壁受到隔离保护,根据内胆管和包壳管的功能和所处环境不同,两者可以采用不同的材质,朝不同的方向优化。开口式燃料棒比闭式燃料棒更适宜采用先进核燃料,开口式燃料棒可以采用高热导率的氮化物或碳化物或硅化物燃料可以降低燃料芯块温度,还可避免某些裂变产物对包壳管的腐蚀,如氧化铯;开口式燃料棒自行排气可以解决氮化物燃料产气量过高的难题。更重要的是氮化物或碳化物或硅化物燃料是解决钍基乏燃料后处理难题的途径,因为烧结的钍基氧化物极难溶解,溶解时必须在强酸溶液中添加氢氟酸,会造成设施的严重腐蚀。慢化液回路及核控系统慢化液回路及核控系统的内容包括:慢化液回路;慢化池液位核控系统;阻隔屏核控系统。慢化池填充液态慢化剂,慢化池设置有慢化液回路,慢化液由慢化液冷却器冷却;反应堆设置核控系统调控堆芯功率和执行停堆操作,核控系统为慢化池液位核控系统或阻隔屏核控系统或慢化池位移核控系统或控制棒核控系统;慢化池液位核控系统设置在特定的慢化液回路中,其慢化液回路为单向慢化液回路,慢化液始终从慢化池顶部输入;慢化池液位核控系统通过调控慢化池内慢化剂的液位高度来改变中子交换和中子能谱,从而达到调控堆芯反应性的目的,并在紧急情况下自动执行非能动停堆;单向慢化液回路中慢化液没有充满慢化池,反应堆移动可引起慢化液波动,慢化池液位核控系统不适应于移动型反应堆;阻隔屏核控系统包括特定的慢化液回路和阻隔屏机构,其慢化液回路为变向慢化液回路,正常运行时慢化液从慢化池底部输入顶部输出,慢化池内充满慢化液,不受反应堆移动影响;停堆期间慢化液变向为从慢化池顶部输入,慢化池不积存慢化液;阻隔屏核控系统通过阻隔中子交换的方式调控堆芯反应性,其没有慢化液波动,适宜于移动型反应堆,也可用于固定型反应堆。慢化池位移核控系统是整体移动慢化池,通过改变慢化池与裂变池的耦合结构,使中子交换和耦合核反应改变,从而调控堆芯反应性;慢化池位移核控系统适合微型或小型核反应堆,特别是空间核反应堆。慢化池液位核控系统:慢化池液位核控系统采用单向慢化液回路。单向慢化液回路从慢化池顶部输入慢化液,其主体包括慢化池、储液池、慢化液、输液泵、输液管、喷液器、回流管和慢化液冷却器。单向慢化液回路由输液泵推动,其循环路径是:储液池→输液泵→喷液器→慢化池→回流管→慢化液冷却器→储液池。储液池位置低于慢化池,慢化液依靠重力回流,储液池与慢化池的落差越大回流势能越大。输液管上设置有输液泵,输液泵定量向慢化池供应慢化液,输液管一头连接储液池底部,另一头连接慢化池上部的喷液器,喷液器主体为一个设置有喷嘴的容器或管件(如中空的栅格板状容器或网状管道或分枝状管道),其功能是以喷淋或喷雾方式将慢化液分散到慢化池内各个器件表面,慢化液从上向下流淌带走器件上的热量。回流管为大口径管道,以满足快速停堆的要求;慢化液冷却器是慢化液的冷却和控温装置,其设置在储液池内或者之外。慢化池内须冷却的部件表面可设置丝网,丝网减缓慢化液流淌速度,帮助慢化液在部件表面均匀分布,并防止慢化液飞溅。慢化池液位核控系统主体包括单向慢化液回路、气体平衡管和液流控制机构。气体平衡管连通慢化池顶部和储液池顶部,平衡两池的气压。液流控制机构包括液流控制器、停堆阀、监测装置及控制线路;液流控制器为单个电动调节阀或由多个电动调节阀组成,其功能是精确调节慢化池液位;停堆阀为常闭状态,停堆期间开启,停堆阀可为一个或多个串联的大口径常闭电动阀门;监测装置包括慢化剂液位监测装置和温度传感器。慢化池液位核控系统正常运行时,输液泵将慢化液泵入慢化池,喷液器分散慢化液到各器件表面向下流淌并积存于慢化池内,慢化液靠重力通过液流控制器以一定的流量经回流管回流到储液池,并由慢化液冷却器冷却和控温。停堆时,启动停堆程序或切断停堆阀的供电,常闭的停堆阀自动开启,慢化池内的慢化液通过大口径的停堆阀快速回流进储液池,慢化池不积存慢化液,热中子和热中子裂变反应基本消失,堆芯反应性剧降,以此达到非能动停堆目的;停堆期间慢化液回路继续执行冷却功能;慢化池液位核控系统的工作流程:(一)、反应堆功率调控:由液流控制器执行,调节慢化池内慢化剂液面高度→改变中子交换和中子能谱→调控堆芯功率。(二)、停堆操作:启动停堆程序或切断停堆阀的电源→停堆阀自动开启→慢化液经大口径停堆阀快速回流入储液箱→慢化池缺失慢化液而失去中子慢化功能→热中子裂变反应被终止→堆芯不能维持链式反应而停堆。(三)、停堆冷却:停堆阀处于断电开启状态→输液泵继续运行→慢化液回路继续循环→喷液器向慢化池内各部件喷洒慢化剂并进行冷却→慢化液经停堆阀快速回流入储液箱,慢化液不能积存于慢化池内。(四)、慢化池液位核控系统的恢复:关闭停堆操作或恢复停堆阀的供电→停堆阀处于关闭状态→慢化液经液流控制器回流到储液池→调节液流控制器使慢化池液位保持在适宜高度。阻隔屏核控系统:阻隔屏核控系统采用变向慢化液回路。变向慢化液回路主体包括慢化池、储液池、慢化液、输液管、输液泵、上输液管、上输液阀、下输液管、下输液阀、喷液器、上回流管、下回流管、下回流阀和慢化液冷却器。变向慢化液回路的慢化液由输液泵输运,正常运行期由输液泵提供输运慢化液的全部动力;停堆期增加重力回流,储液池与慢化池的落差越大回流势能越大。输液管下端连通储液箱底部,输液管上设置有输液泵,输液泵之上分出上输液管和下输液管。上输液管接通喷液器,喷液器主体为一个设置有喷嘴的容器或管件(如中空的栅格板状容器或网状管道或分枝状管道),慢化液通过喷液器将慢化液分散到慢化池内各个器件表面,慢化液从上向下流淌带走器件上的热量。下输液管接通慢化池底部;下回流管为大口径管道,以满足快速停堆的要求。下输液阀为常开状态,停堆期间关闭,下输液阀可为常开电动阀门。上输液阀和下回流阀为常闭状态,停堆期间开启,上输液阀和下回流阀可为常闭电动阀门。正常运行时的循环路径是:储液池→输液管→输液泵→下输液阀→下输液管→慢化池→上回流管→慢化液冷却器→储液池。停堆期间的循环路径是:储液池→输液管→输液泵→上输液阀→上输液管→喷液器→慢化池→下回流阀→下回流管→慢化液冷却器→储液池。停堆期间的上回流管功能转化为气体平衡,平衡慢化池和储液池内的气压。慢化池内需冷却的部件表面可设置丝网,丝网减缓慢化液流淌速度,帮助慢化液在部件表面均匀分布,并防止慢化液飞溅。阻隔屏核控系统主体包括变向慢化液回路和阻隔屏机构;阻隔屏机构主体包括阻隔屏驱动器、传动带、上导杆、密封滑套、密封环、阻隔屏、下导杆和下导向管。阻隔屏设置在靠近裂变池的慢化池一侧,阻隔屏为下部分叉的筒形或弧形板体,分叉口设置下导杆,阻隔屏上部设置上导杆。密封滑套设置在慢化池顶盖上或者慢化池上承板上,密封滑套内设置密封环和滑动构造,上导杆可在密封滑套内滑动;下导杆滑行并定位于下导向管内,下导向管设置有漏液孔。阻隔屏具有阻隔热中子或全部中子的功能,阻隔屏驱动器驱动阻隔屏上下运动,移动阻隔屏改变主容器内中子分布和中子交换,以此改变堆芯反应性和调控堆芯功率。停堆操作由变向慢化液回路执行,启动停堆程序或切断阀门的供电,常开的下输液阀关闭,常闭的上输液阀和下回流阀自动开启,慢化液通过下回流管快速流入储液池,储液池的气体通过上回流管进入慢化池平衡两池气压,慢化池不能积存慢化液,热中子和热中子裂变反应消失,堆芯反应性剧降,以此达到非能动停堆目的;正常运行时慢化液从下往上循环,慢化池内充满慢化液,冷却功能高效;停堆期间慢化液回路变向为从上往下循环,慢化液在各器件表面流淌能继续执行冷却功能。增殖燃料系统增殖燃料系统的内容包括:增殖棒系统;增殖燃料的分离提纯。慢化池中设置增殖燃料系统,增殖燃料系统由慢化液冷却。增殖燃料系统为浸泡式增殖燃料系统或隔离式增殖燃料系统。浸泡式增殖燃料系统的增殖燃料原料(可转换核素)浸泡在慢化液中,慢化液行使溶剂功能溶解增殖燃料中的部分核素,通过慢化液回路带出反应堆,并在反应堆外被在线分离提取。浸泡式增殖燃料系统构造复杂,还增加了慢化液的功能负载,慢化液成分复杂腐蚀性强,对慢化池结构材料要求高,会导致慢化液回路结垢,对慢化液回路产生负面影响,运行难度较大。隔离式增殖燃料系统为增殖棒系统,增殖燃料填装在增殖棒内,增殖燃料与慢化剂隔离;隔离式的增殖棒系统构造简单效率高,慢化液纯度高、功能单一、稳定性高。增殖棒系统:增殖棒系统主体包括慢化液回路、增殖棒、增殖棒套管、套管格架、换棒机构和附属装置。增殖棒为两端密封的棒状包壳管构造,其内填装增殖燃料原料(可转换核素)。增殖棒套管为指套管,是增殖棒与慢化池之间的隔离套管,固定在慢化池顶盖或慢化池上承板或慢化池底板上,其开口端在慢化池之外,增殖棒套管与固定面接合处为密封构造。增殖棒套管隔离增殖棒和慢化液,便于增殖棒的在线更换,其长短和截面形状与增殖棒相互适应。套管格架加固增殖棒套管防止变形。增殖棒和增殖棒套管的管材部分选用对中子透明度高的材料,如铝基或锆基金属材料。换棒机构是增殖棒的在线更换设施,换棒机构可设置在慢化池上方或者下方,在慢化池上方有阻挡物(如管道等)的换棒障碍区域,选择下方换棒方式或者设置替代物取代增殖棒;替代物无需在线更换,只须在慢化池开盖时更换,替代物可为二次中子源组件或反射棒或反应棒,二次中子源组件用于反应堆下次启动或新堆启动,反应棒用于制造人造元素。增殖棒系统的换棒机构可设置对增殖棒的定位功能和自动换棒功能。附属装置包括温度检测装置,温度传感器内置于增殖棒内,当增殖棒内温度高过正常值时,表明增殖棒内有裂变反应发生,U-233的含量已达到可提取的范围,此棒必须更换;为了增加增殖棒和增殖棒套管的散热效果,可以在增殖棒套管内或者增殖棒内填充导热液。在慢化池上方通过的主冷却剂输出管以及其他管道对在线更换增殖棒有影响,其设置方法是:(一)、降低慢化池整体高度,主冷却剂输出管直接从慢化池顶盖上方通过。(二)、只降低主冷却剂输出管经过的慢化池局部区域的高度,此区域形成封闭的“U”形区,主冷却剂输出管位于“U”形区内,慢化池顶盖被“U”形区隔断不连续。(三)、为减少主冷却剂输出管对在线更换增殖棒的影响,可将相关的主冷却剂输出管区段设计为侧扁形出口及侧扁形管道,减少遮挡面积。增殖棒包括底端塞或底板、包壳管、填充物、温度传感器和顶端部。下端由底端塞或底板密封,上端由顶端部密封,顶端部上设置操作头供换棒机构抓取。初始填充物(增殖燃料原料)为钍化合物,温度传感器置于填充物中。增殖棒为重复性使用构件或一次性构件,重复性增殖棒可以多次使用,底端塞和顶端部可以从包壳管上分离,包壳管与底端塞和顶端部以螺纹连接并密封。增殖燃料的分离提纯:增殖燃料的分离提纯采用一种难溶化合物分离流程:利用某类钍化合物比铀化合物惰性的特性进行分离,增殖燃料原料为难溶钍化合物,这种难溶钍化合物转化的铀化合物是可溶的。所述的难溶化合物是针对某种特定的溶剂而言,因此难溶钍化合物有多种;溶剂可以是水或酸液或碱液或有机溶剂,难溶钍化合物为结晶体二氧化钍或氢氧化钍或钍盐或钍酸盐或有机钍化合物。难溶钍化合物分离流程:增殖棒内难溶钍化合物接受中子辐射→在线提取出的增殖棒放置储藏室(9-11个月)待Pa-233充分衰变为U-233→从增殖棒中取出增殖燃料并进行粉碎→从增殖棒中取出增殖燃料并进行粉碎→粉碎后的增殖燃料投入溶解池,充分搅拌后澄清→分离溶液和沉淀;沉淀物经干燥后得到Th-232化合物;分离出的溶液进行溶质和溶剂分离,溶质分离物经干燥得到U-233化合物。增殖燃料的分离提纯采用一种可溶化合物分离流程:增殖燃料原料为可溶钍化合物,这种可溶钍化合物转化的铀化合物也是可溶的。所述的可溶化合物是针对某种特定的溶剂而言,因此可溶钍化合物有多种;溶剂可以是水或酸液或碱液或有机溶剂,可溶钍化合物为非结晶二氧化钍或氢氧化钍或钍盐或钍酸盐或有机钍化合物。可溶钍化合物分离流程:增殖棒内难溶钍化合物接受中子辐射→在线提取出的增殖棒放置储藏室(9-11个月)待Pa-233充分衰变为U-233→从增殖棒中取出增殖燃料并进行粉碎→粉碎后的增殖燃料投入溶解池,搅拌溶解→增殖燃料溶液→从溶液中萃取U-233;从萃取液中分离溶质再干燥得到U-233化合物;从萃取后的剩液中分离溶质再干燥得到Th-232化合物。其他设施其他设施的内容包括:主冷却剂辅助加热保温装置;主冷却剂氧控系统;裂变池气室及裂变气体净化系统;余热排出系统;中子源机构和核测装置。主冷却剂辅助加热保温装置:主冷却剂为液态重金属,特别是铅或铅铋共晶;主回路即主冷却剂回路,主回路可设置主冷却剂辅助加热保温装置,主冷却剂辅助加热保温装置设置在裂变池底部和循环管道上其功能是熔化凝固的主冷却剂和预防主冷却剂凝固。主冷却剂氧控系统:液态重金属对金属材料有一定的溶解腐蚀性,最有效的防腐蚀方法是以氧控技术保持金属表面氧化膜的完整性,现有资料显示,在严格控制铅铋液体中含氧量的条件下,某些不锈钢表面的保护性氧化膜能长时间完好无损。主回路设置氧控系统,可降低主冷却剂对材料的腐蚀,氧控系统为气相氧控系统或固相氧控系统。氧控系统的测氧探头可选用氧化锆氧传感器。气相氧控系统:气相氧控系统主体包括氧控气体回路、气体扩散装置、气泵和检控装置。氧控气体回路包括气体调配室和循环气道,气体调配室将氧控气体成分调配到合适的比例;气体扩散装置为主冷却剂流经的管道或容器,可含有搅拌装置,气体扩散装置可由主循环泵或主循环管或裂变池气室替代;气泵将氧控气体鼓入气体扩散装置,氧控气体均匀分散到主冷却剂内,少量溶解后的剩余气体再回到气体调配室重新调配。检控装置检测主回路含氧量和氧控气体回路中的气体成分比例,并指令气体调配室调控各气体成分。气相氧控系统可采用三元气体组合,三元气体包括氧化性气体、还原性气体和载体气体;氧化性气体可选用水蒸气或氧气或二氧化碳,水蒸气最易调控;还原气体可选用氢气或一氧化碳,以氢气最合适,氢气可以还原过量的重金属氧化物有利清除固态杂质;载体气体可选用氩气,氩气性价比最高;三元气体组合可以选用H2O/H2/Ar或O2/H2/Ar或CO2/CO/Ar;比较可行的是H2O/H2/Ar组合,含低浓度氢气的H2/Ar通入可调温度的水中获取水蒸气含量可调的H2O/H2/Ar。固相氧控系统:固相氧控系统主体包括质量交换器和检控装置。质量交换器为填装有氧化物固体颗粒的容器型装置,可设置在主回路的支路上,氧化物固体颗粒可以少量溶解在主冷却剂中,如氧化铅PbO;主冷却剂流经质量交换器在氧化物固体颗粒上进行溶质交换,即进行固相反应的氧化物溶解和溶质沉积。检控装置包括温控器和流量控制器,检控装置检测和调节流经氧化物固体颗粒的主冷却剂的温度或流速或支路开通时间,通过控制氧化物溶解和析出过程来调控主冷却剂中的含氧量。支路动力可由主回路射流压差提供。固相氧控系统可增添一个旁路设置氢化物溶解装置协调主回路氧含量的调控,氢化物溶解装置可设置在与质量交换器相对的主回路的另一端。裂变池气室和裂变气体净化系统:固定型反应堆的裂变池顶部可设置裂变池气室,裂变池中产生的气体或开口式燃料棒排出的裂变气体可以排到裂变池气室。采用开口式燃料棒组件的裂变池可以设置双层裂变池气室,开口式燃料棒组件的排气主管穿过堆芯顶栅板,堆芯顶栅板将裂变池气室分隔为裂变池上气室和裂变池下气室。反应堆可设置裂变气体净化系统,裂变气体净化系统为气体循环净化系统,功能是冷却部件和去除具有化学活性和核活化性的裂变气体成分,如碘、氙、溴、铯。裂变气体净化系统为闭合气体循环回路,裂变气体净化系统主体包括裂变池气室、抽气泵、气体净化冷却室、废气罐、配气罐、气体调配室、送气泵、流量控制阀和监控装置。裂变气体在气体净化冷却室被冷却和净化,多余的净化气体被压入废气罐储存,气体调配室将根据需要调取配气罐(如氧气罐、氢气罐、氩气罐)中的气体,使调配的气体成分达到特殊要求,如含氧量。双层裂变池气室内的气体流向是:循环气体先进入裂变池下气室,再通过两气室之间的间隙进入裂变池上气室,然后排出裂变池;从下往上流动的循环气体带走裂变气体并阻挡裂变气体接触主冷却剂,防止有害气体污染主冷却剂。裂变气体净化系统的工作流程为:裂变池气室→抽气泵→气体净化冷却室→气体调配室→送气泵→气体流量控制阀→裂变池气室。反应堆余热排出系统:反应堆设置小循环泵余热排出装置和应急非能动余热排出系统。在停堆后小循环泵余热排出装置取代主循环系统将堆内余热排出。应急非能动余热排出系统:当停堆期间小循环泵余热排出装置因故障不能工作,反应堆立即启用应急非能动余热排出系统。应急非能动余热排出系统的位置高于主容器,最初的运行动力为重力,随后的动力来自蒸汽。应急非能动余热排出系统主体包括载热液箱、冷却水箱、真空室、流量控制阀、启动阀和管道。位置高度是:真空室最高,冷却水箱次之,再其次为载热液箱,裂变池最低。载热液箱储存纯水或者水溶液,水溶液可含有中子吸收剂,如含硼水溶液。冷却水箱储存冷却水,冷却水量取决于设定的余热排出量。真空室在最初时起吸除主容器和回路中的的气体的功能,真空室连通一根吸气管和一根排液管,吸气管连接冷凝管的末端,排液管连接载热液箱。流量控制阀为常闭状态,通常设定为一个流量定值,也可以通过控制线路调节大小,流量控制阀可为常闭电动阀门;其余阀门均为启动阀,正常运行时启动阀处于关闭状态,所有通道被切断,应急时启动阀处于开启状态,启动阀可为常闭电动阀门;启动阀全部开启后,反应堆余热以水蒸汽形式非能动排出裂变池。整个系统有两个回路:一个回路是气体回路,另一个回路是水-汽回路;非能动余热排出系统的工作流程是:(一)、启动程序:反应堆停堆→小循环泵余热排出系统不能正常工作→启动应急非能动余热排出系统。(二)、气体回路工作流程:真空室一次性吸除主容器和管道内的气体,裂变池气室→蒸汽管→冷凝管→真空室←排液管←载热液箱。(三)、水-汽回路工作流程:载热液箱→载热液→流量控制阀→裂变池气室→分散到主冷却剂表面→水蒸汽→蒸汽管→冷凝管→冷凝水→载热液箱。中子源机构和核测装置:中子源机构和核测装置可以设置在裂变池或者慢化池,以设置在裂变池底部或慢化池顶部为宜。裂变池条件严酷需设置能与主冷却剂隔离的指套管,中子源机构或核测装置以插件插入指套管内。慢化池条件温和可采用密封构造,中子源机构或核测装置可直接接触慢化剂。裂变池底部可设置中子源机构,中子源机构主体包括中子源组件、中子源冷却器、中子源套管、滑动套管和中子源驱动器。中子源套管为中子源组件与主冷却剂的隔离套管,中子源套管和滑动套管连通并在在同一中心线上,两者固定在裂变池底板上,前者位于裂变池内,后者位于裂变池外,除两者之外中子源机构的其余部分均可从裂变池上在线分离;中子源套管的横截面形状可以与堆芯燃料组件相适应,如六边形。中子源组件为柱状密封构造,其基部为光滑的滑动部分,中子源组件内部设置中子源和冷却剂循环通道;中子源冷却器冷却中子源组件,中子源冷却器为气体或液体冷却回路,冷却剂可从中子源组件中心进入再从周边回流。中子源驱动器的功能是驱动中子源组件在滑动套管内滑动,中子源组件的滑动方式是上下运动,中子源驱动器可以是电机驱动的简易的升降台(如液压式、螺杆式、齿条式)或复杂的电磁驱动器。裂变池底部设置中子源机构可以简化裂变池构造,降低裂变池高度,降低反应堆制造难度。慢化池顶部可设置慢化池中子源机构,慢化池中子源机构主体包括中子源组件、密封滑套、密封环和中子源驱动器。密封滑套固定在慢化池顶盖上,中子源组件外壳为光滑的圆柱形密封容器,其内设置有中子源。中子源组件与密封滑套中形成可滑动的密封构造,中子源驱动器驱动中子源组件在密封滑套内运动,中子源驱动器为起吊装置或电磁驱动装置。中子源组件由慢化剂直接冷却,中子源组件内可充填导热液或导热气体增强冷却效果。中子源组件释放的中子在慢化池慢化为热中子,热中子交换进入裂变池引发堆芯裂变反应。慢化池内的装置均由慢化液冷却,慢化池内的插件(如增殖棒)与隔离套管之间的间隙可填充导热液提高冷却效率。快堆型耦合核反应堆类型快堆型耦合核反应堆类型的内容包括:双慢化池耦合核反应堆;单慢化池外置耦合核反应堆;单慢化池内置耦合核反应堆;空间耦合核反应堆。双慢化池耦合核反应堆:双慢化池耦合核反应堆为中型以上的固定型反应堆,适用于电站、供热和海水淡化。反应堆主容器为双慢化池耦合结构,主容器为可拆分组合式构造,有主容器外壳。反应堆拥有内外双慢化池,内慢化池位于反应堆中心为桶状池型构造,外慢化池位于反应堆外侧为环状池型构造;裂变池位于两慢化池中间为环状池型构造。裂变池内外侧壁均设置有大面积薄壁构造的中子交换窗。裂变池顶盖密封采用金属密封剂进行密封,金属密封剂为易熔重金属合金。裂变池设置有裂变池气室,裂变池顶盖采用高强度轻质顶盖。慢化池顶盖采用密封硅胶进行密封。主冷却剂为铅或铅铋合金,堆芯为燃料棒堆芯,燃料组件可为开口式燃料棒组件或闭式燃料棒组件,开口式燃料组件优于闭式燃料棒组件,可以降低裂变池高度。慢化剂为重水,慢化池设置有慢化液回路。外慢化池专司燃料增殖,设置为增殖棒系统,可在线提取增殖燃料,生产U-233核燃料。内慢化池专司核控,其设置为慢化池液位核控系统。停堆时内外双慢化池同时快速排出慢化液,反应堆因慢化功能缺失不能维持链式反应而停堆。单慢化池外置耦合核反应堆:单慢化池外置耦合核反应堆为多样性反应堆类型,规模可以从小型到大型,可以为固定堆也可以为移动堆。反应堆主容器为可拆分组合式构造,有主容器外壳。主容器为单慢化池外置耦合结构,裂变池位于中心为桶状池型构造,慢化池位于裂变池外侧呈环状池型构造。裂变池侧壁设置有大面积薄壁构造的中子交换窗。裂变池顶盖采用金属密封剂进行密封,金属密封剂为易熔重金属合金。慢化池顶盖采用硅胶进行密封。主冷却剂为铅或铅铋合金,堆芯为燃料棒堆芯。慢化剂为重水,慢化池设置有慢化液回路,慢化池设置增殖棒系统,可在线提取增殖燃料,生产U-233核燃料。固定型单慢化池外置耦合核反应堆的堆芯可采用开口式燃料组件或闭式燃料组件,核控系统采用慢化池液位核控系统。移动型单慢化池外置耦合核反应堆的堆芯采用闭式燃料组件,核控系统采用阻隔屏核控系统。单慢化池内置耦合核反应堆:单慢化池内置耦合核反应堆为简化的小型或微型反应堆,热交换器与反应堆合并为一体。反应堆主容器为单慢化池内置耦合结构,慢化池位于反应堆中心为桶状池型构造,慢化剂为重水或轻水;裂变池位于慢化池外侧呈环状池型构造。裂变池内侧壁设置有大面积薄壁结构的中子交换窗。主冷却剂为铅或铅铋合金,固定堆裂变池可设置裂变池气室;堆芯可采用闭式燃料棒组件或开口式燃料棒组件(固定堆),堆芯外周可设置转换燃料区,堆芯外侧设置有屏蔽区。慢化池设置慢化池液位核控系统(固定堆)或阻隔屏核控系统(移动堆)。中子源机构设置在裂变池或慢化池内。反应堆外侧设置热交换池,热交换池的内侧和裂变池外侧共用一个传热壁,传热壁外侧设置传热管,主冷却剂在传热管和裂变池内循环,传热管和传热壁上设置有散热片,传热管和传热壁共同导出堆芯热量。热交换池相当于一、二回路热交换器,二回路冷却剂为水。一回路设置排爆管和爆破阀,当发生水泄漏进入传热管并进入集流室时,水汽化为蒸汽,比重很轻的蒸汽向上进入排爆管,爆破阀受压破膜排出水蒸气,能防止水或蒸汽进入堆芯。水泄漏进入裂变池气室时,裂变池顶盖上设置的排爆管和爆破阀也能排出水蒸气。裂变池内可设置导流板。一回路设置或者不设置主循环泵。一回路设置主循环泵:主冷却剂靠强制循环。一回路不设置主循环泵:主冷却剂靠自循环。单慢化池内置耦合核反应堆的热交换效率不高,适宜作为出水温度要求不太高的核能装置。空间耦合核反应堆:反应堆为无主容器外壳的微型或小型空间核动力装置,反应堆径向可不设置屏蔽构造。主容器为单慢化池外置耦合结构,裂变池位于中心为桶状,慢化池位于外侧为环形筒状,慢化剂为石墨,填充在筒状慢化池中;反应堆采用慢化池位移核控系统,慢化池不接触裂变池,慢化池以裂变池为中心进行轴向移动。主冷却剂为液态金属,特别是液态碱金属,如锂-7,堆芯主体由闭式燃料棒组件构成,裂变池可设置导流管。裂变池热能由液态金属传导给热电转换装置。慢化池位移核控系统行使中子慢化和核控功能,慢化池位移核控系统包括慢化池和慢化池驱动机构。慢化池驱动机构主体包括慢化池驱动器、离合器、中心导杆和回弹装置。中心导杆轴向固定在裂变池底板中心,正常运行时离合器与中心导杆啮合,慢化池驱动器沿着中心导杆运动和定位。慢化池驱动器可为步进或旋转电机,中心导杆为螺杆,电机转子轴心为空心状,中心导杆从电机转子轴心穿过,电机转子环绕中心导杆旋转。正常运行时,离合器与中心导杆啮合,电机推动慢化池驱动机构沿着中心导杆运动和定位。停堆时,离合器与中心导杆分离,回弹装置将慢化池拉回或推回远端,即慢化池远离裂变池,堆芯因缺乏慢化中子致反应性下降而停堆。回弹装置的弹力由弹簧提供。本发明的技术优势在于:(一)、快堆型耦合核反应堆主冷却剂可采用化学性质稳定的液态重金属,特别是铅或铅铋共晶,主容器在常压下运行,反应堆具有固有安全性。(二)、快堆型耦合核反应堆的主容器拆分为相互耦合但彼此完全隔离的裂变池和慢化池,两者之间设置隔热层,解除了慢化剂与主冷却剂的功能捆绑,裂变池和慢化池可各自朝最有利的方向优化。反应堆主要部件可拆分和组合,可实施模块化设计。其主容器可采用耗材少的薄壁构造。裂变池和慢化池分别采用廉价的铁素合金和铝合金,工程难度和制造成本均低。(三)、快堆型耦合核反应堆在堆芯外使用慢化剂,在快中子堆芯中实现快-热中子耦合核反应,核反应效率比快堆大幅提高,堆芯易裂变核素的含量可以显著降低。与其他快堆相比,昂贵的易裂变核素的初装量下降,燃料增殖效率提高,可以使核燃料增殖的“倍周期”缩短。(四)、慢化池内可接近常温常压,可无难度地的延伸慢化池功能。慢化池可增加燃料增殖、耦合核控和核测的功能。(五)、快堆型耦合核反应堆可采用慢化池液位核控系统,可快速控制全部剩余反应性,不需要控制棒、调节棒、屏蔽棒和化学控制。裂变池径向不需要中子屏蔽件,反应堆整体使用的中子吸收剂少,既可以节省设备材料费用,还可以减少堆内中子损耗,提高中子经济性。可以省去昂贵复杂且难于驾驭的控制棒驱动机构,可卸掉裂变池一半左右的重量和功能负载,简化裂变池和堆芯的构造,降低裂变池高度,裂变池仅相当于堆芯吊篮。可实施裂变池整体更换或一次性退役(随堆芯更换而退役),提高维修安全性和维修效率。(六)、在慢化池可实施燃料增殖和增殖燃料的在线提取,实现Pa-233/U-233堆外转化,减少Pa-233的负面影响。Th-232的热中子俘获截面比快中子高19倍,慢化池增殖燃料只含单一核素Th-232,初始只进行单一高效的Th-232热中子俘获反应,易裂变核素的俘获反应造成的核燃料和中子的双损耗可以忽略,所以慢化池内增殖燃料的中子利用率高。慢化池增殖燃料成分单一,转化后的增殖燃料最终需要分离的化学元素只有Th-232和U-233,即非此即彼,核素分离简单。慢化池中生产的U-233核燃料不含发射高能γ射线的Th-228子体,因此慢化池中生产的U-233核燃料是安全的,不需要代价高昂的防护γ射线的设施及生产工艺。堆芯内的钍基乏燃料仍然有高能γ射线,可以通过提高堆芯燃耗,增加慢化池生产U-233核燃料的比重来解决,可以使乏燃料后处理频次(即闭环次数)大幅减少,甚至有可能省去。(七)、快堆型耦合核反应堆可采用“烛式堆芯”,可与慢化池液位核控系统相匹配,两者都支持从下往上的逐步燃烧方式,“烛式堆芯”初装易裂变核素主要分布于堆芯燃料区下方,其浓度梯是下高上低,上部燃料通过增殖反应累积,其累积速度与燃烧区上移速度相适应,堆芯燃耗率是越往下部越高,这种堆芯易裂变核素初装量比较节省,堆芯寿命长,总燃耗深度大。(八)、简化的裂变池使堆芯可以采用开口式燃料棒组件,开口式燃料棒能减少中子损耗,降低燃料棒内压,延长燃料棒包壳管的寿命,提高堆芯燃耗率。开口式燃料棒为高导热率先进陶瓷燃料(如氮化物、碳化物、硅化物燃料)的运用创造了条件,可克服氮化物燃料易高温分解释放氮气的缺陷。更重要的是先进陶瓷燃料是解决钍基乏燃料后处理难题的最佳途径,这是因为烧结的钍基氧化物极难溶解,溶解时必须在强酸溶液中添加氢氟酸,会造成设施的严重腐蚀。(九)、快堆型耦合核反应堆核原料以廉价的Th-232为主,其次为核废料。堆芯中心既适合燃烧U-233、U-235和Pu-239,还适合燃烧超铀元素,可以为压水堆核废料提供一个解决途径。利用廉价的钍和核废料,燃料成本降低,核资源的利用率提高,全球核裂变能的可持续期限可增长到万年以上。附图说明图1垂直连接套管拆装示意图;图2非垂直连接套管拆装示意图;图3非垂直转垂直连接套管拆装示意图;图4框架蒙皮结构主容器示意图;图5薄壁筋板结构主容器示意图;图6主容器顶盖密封剂密封构造示意图;图7双慢化池耦合核反应堆纵剖面图;图8双慢化池耦合核反应堆横剖面图;图9单慢化池外置耦合核反应堆纵剖面图;图10单慢化池外置耦合核反应堆横剖面图;图11单慢化池内置耦合核反应堆纵剖面图;图12单慢化池内置耦合核反应堆横剖面图;图13空间耦合核反应堆纵剖面图;图14空间耦合核反应堆横剖面图;图15防护罩为指套管状的燃料内胆示意图;图16防护罩为帽状的燃料内胆示意图;图17填装燃料内胆的开口式燃料棒示意图;图18开口式燃料棒及螺纹连接示意图;图19螺纹连接的燃料棒底端塞结构图;图20焊接连接的燃料棒底端塞结构图;图21镶嵌连接的燃料棒底端塞结构图;图22棒束开口式燃料组件示意图;图23套管开口式燃料组件示意图;图24无阀排气构件纵剖面示意图;图25无阀排气构件(爪式)俯视图;图26有阀排气构件纵剖面示意图;图27弹簧式泄压阀纵剖面图;图28易熔重金属泄压阀纵剖面图;图29双泄压阀纵剖面图;图30闭式燃料棒及螺纹连接示意图;图31棒束闭式燃料组件示意图;图32套管闭式燃料组件示意图;图33裂变气体净化系统示意图;图34裂变气体净化系统工作流程图;图35主冷却剂气相氧控示意图;图36主冷却剂固相氧控示意图;图37慢化池液位核控系统示意图;图38阻隔屏核控系统示意图;图39筒形阻隔屏结构图;图40弧形阻隔屏结构图;图41裂变池底部中子源机构示意图;图42慢化池顶部中子源机构示意图;图43应急非能动余热排出系统示意图;图44难溶增殖燃料提取分离流程图;图45可溶增殖燃料提取分离流程图。图中标注与名称对照:101主容器外壳;132蒙皮;133框架;142薄壁;143筋板;150容器侧壁;151容器顶盖;152环状沟槽;153环状裙板;154密封剂;155锁紧装置;175连接套管;176固定管头;177可拆分管头;178上管头;179下管头;180管头;201裂变池;202裂变池顶盖;203裂变池侧壁;205裂变池底板;209保温层;211侧壁隔热层;212承重隔热层;221裂变池气室;222裂变池上气室;223裂变池下气室;231主冷却剂进口;232主冷却剂出口;233导流管;234导流板;235主循环泵;236主循环管;250堆芯;251堆芯底座;255堆芯顶栅板;256堆芯底栅板;258屏蔽区;281气体调配室;282气体扩散装置;283气泵;285质量交换器;286氧化物固体颗粒;287温控器;289流量控制器;301慢化池;302内慢化池;303外慢化池;305慢化池顶盖;306慢化池侧壁;307慢化池底板;365增殖棒;366增殖棒套管;367套管格架;400中子源;401中子源机构;411中子源组件;413中子源驱动器;415中子源套管;426滑动套管;427密封滑套;429冷却剂泵;431中子源冷却器;501热交换池侧壁;502热交换池;503传热壁;504传热管;505散热片;507集流室;508排爆管;509爆破阀;511进水管;512出水管;553慢化池驱动器;555中心导杆;558弹簧;601储液池;602慢化液冷却器;605液流控制器;611停堆阀;631喷液器;632输液泵;633输液管;635回流管;638气体平衡管;655上输液管;656上输液阀;661下输液管;662下输液阀;663上回流管;665下回流管;666下回流阀;681阻隔屏;682阻隔屏驱动器;683传动带;685上导杆;691密封环;695下导杆;696下导管;700开口式燃料棒;703燃料内胆;705内胆管;707底塞;708顶塞;709注气孔;710注气管;711防护罩;712下转换区;713燃料区;714上转换区;717气腔;721压紧弹簧;722填充物;725下端塞;726上端塞;728包壳管;729排气细管;731排气细管集束;732密封套管;734凸台;735凹槽;737螺钉;738螺孔;742槽口;743焊接点;747键槽;751约束部;752潴留气体;753密封头;754爪状连接;755排气主管;756注气孔;757泄压阀;759冷却剂出孔;761约束部承接板;765吸附体;766吸附体定位器;767吸附体压紧弹簧;771开口式燃料棒;772棒束顶栅板;773棒束底栅板;774上管座;775下管座;776骨架管;777定位格架;778顶部定位格架;779底部定位格架;781固定螺杆;782定位插销;785管脚;786冷却剂入孔;787密封体;788固定螺纹;789主套管;791垫块;795闭式燃料棒;811阀壳体;812下阀体;813上阀体;814弹簧;815弹簧定位头;816压紧螺丝;818通气孔;822帽盖;825易熔重金属;827防脱堵头;831中心气管;912抽气泵;913气体净化冷却室;914气体调配室;915配气罐;916废气罐;917送气泵;918气体流量控制阀;931载热液箱;932冷却水箱;933冷凝管;934真空室;935吸气管;936排液管;937流量控制阀;938启动阀;939蒸汽管。具体实施方式下面结合附图和具体实施方式对本发明做进一步的详细描述。实施例一:快堆型耦合核反应的实施方法如图9和图10所示:将反应堆主容器拆分为相互完全隔离的裂变池201和慢化池301,裂变池内设置堆芯250,堆芯具有快中子堆芯特性,慢化池301内置慢化剂。将裂变池201与慢化池301相互镶嵌或可移动式组合,使两者结构和功能耦合,在裂变池201和慢化池301之间设置隔热层,阻隔两者的热交换,使慢化池301可控制在接近常温常压的状态;将慢化剂与主冷却剂分离,两者在结构和功能上不再捆绑,裂变池201和堆芯250无慢化剂,主冷却剂通过裂变池201而不通过慢化池301;允许中子穿过裂变池201和慢化池301之间的构造,使裂变池201与慢化池301能进行中子交换并进行耦合核反应,堆芯产生的快中子和从慢化池301内反射进入裂变池201的慢化中子可使堆芯同时进行快中子和慢化中子(包括热中子和中能中子)引发的耦合核反应,裂变池201具有快中子反应堆的特性和功能,慢化池301内可进行热中子核反应(如热中子俘获反应)。在慢化池301设置耦合核控系统,利用耦合核反应实施耦合核控和非能动停堆;利用慢化剂的慢化中子功能和慢化剂的可控性或慢化池的可控性位移,通过改变裂变池201和慢化池301之间的中子交换控制堆芯250的反应性;停堆时使慢化池301失去中子慢化功能,终止慢化池301向堆芯250输送慢化中子,堆芯反应性快速下降导致链式裂变反应不能维持,从而实现非能动停堆。利用热中子核反应的高效性,在慢化池接近常温常压的条件下,实施核燃料增殖和增殖燃料的在线提取,在反应堆外实现Pa-233/U-233转化以及Th-232/U-233的分离;在慢化池301设置可在线更换燃料的增殖燃料系统,初始增殖燃料原料只含一种核素Th-232,只进行Th-232的热中子俘获核反应,避免或降低Pa-233和U-233俘获中子造成的中子和有效核燃料的双重损耗,提高增殖效率和中子利用率高。慢化池物理条件温和,在线提取增殖燃料没有难度,后期的核素分离简单,只需进行Th-232/U-233两个元素非此即彼的简单分离。优化燃料元件和堆芯设计(如采用烛式堆芯设计),提高核反应效率和燃耗率。如图4和图5所示,优化反应堆主容器材料和结构,在反应堆主容器侧壁设置大面积薄壁构造的中子交换窗口,在保证结构强度的同时增加中子交换效率。将反应堆主容器低矮化、简单化、低成本化和模块化,实施裂变池的整体更换或实施裂变池模块一次性退役(裂变池随堆芯更换而退役),提高维修效率和整体安全性。将反应堆主要部件模块化,使反应堆可拆分和组合。反应堆模块的拆分与重组的难点主要表现在管道的拆分与重组。采用易重组的套管连接和拆分方法,简化反应堆模块的拆分和重组,套管连接与拆分方法为垂直套接或非垂直套接或非垂直转垂直套接。如图1所示,垂直套接:连接套管175较长可多次重复使用,下方管头为固定管头176,上方管头为可拆分管头177,两个管头在同一垂直轴心上,以垂直吊装进行安装;初次连接前,预先将连接套管175焊接在下管头179上,连接时上管头178对准并少许插入连接套管175后焊接,焊接面朝上操作简单且焊接效果最佳;拆分时只需在连接套管175上端的焊接处下方切割分离,连接套管175稍许减短;重组时清理连接套管175内的残留物,上管头相比前次适当加长,重复前次的连接流程即可。如图2所示,非垂直套接:非垂直套接以水平管道连接为主,以垂直吊装进行安装,连接在拆分模块上的管头为可拆分管头177,对应的另一管头为固定管头176,连接套管175较短为一次性部件,以后按需要逐次加长连接套管175或适量加长可拆分管头177;连接时预先在固定管头176上套上连接套管175但暂不焊接,滑动连接套管175露出固定管头176,两管头对齐后套上连接套管175,然后分别焊接两端;拆分时需切割掉整个连接套管175,重新组合时换上长度合适的新连接套管175,重复前次的连接流程即可;非垂直套接的焊接难度高,焊接效果不易保证。如图3所示,非垂直转垂直套接:连接的两个管道为非垂直管道,将需连接的两个管头以弯头分别转化为同轴心的垂直管头,固定管头176在下,可拆分管头177在上,其后的连接、拆分和重组方法与垂直套接相同。实施例二:双慢化池耦合核反应堆如图7、图8所示,双慢化池耦合核反应堆为中型以上的固定型反应堆,适用于电站、供热和海水淡化。反应堆主容器为双慢化池耦合结构,主容器为可拆分组合式构造,有主容器外壳101。反应堆拥有内外双慢化池,内慢化池302位于反应堆中心为桶状池型构造,外慢化池303位于反应堆外侧为环状池型构造;裂变池201位于两慢化池中间为环状池型构造。裂变池201内外侧壁均设置有大面积薄壁构造的中子交换窗。裂变池顶盖密封采用金属密封剂进行密封,金属密封剂为易熔重金属合金,裂变池顶盖采用高强度轻质顶盖。慢化池顶盖采用密封硅胶进行密封。主冷却剂为铅或铅铋合金,堆芯为燃料棒堆芯,燃料组件可为开口式燃料棒组件或闭式燃料棒组件,开口式燃料组件优于闭式燃料棒组件,可以降低裂变池高度。慢化剂为重水,慢化池设置有慢化液回路。外慢化池303专司燃料增殖,设置为增殖棒系统,可在线提取增殖燃料,生产U-233核燃料。内慢化池302专司核控,其设置为慢化池液位核控系统。停堆时内外双慢化池同时快速排出慢化液,反应堆因慢化功能缺失而停堆。实施例三:固定型单慢化池外置耦合核反应堆如图9、图10所示,固定型单慢化池外置耦合核反应堆为小型到大型的反应堆,适用于电站、供热和海水淡化。主容器为可拆分组合式构造,有主容器外壳101。反应堆主容器为单慢化池外置耦合结构,裂变池位于中心为桶状池型构造,慢化池位于裂变池外侧呈环状池型构造。裂变池201外侧壁设置有大面积薄壁构造的中子交换窗。裂变池顶盖采用金属密封剂进行密封,金属密封剂为易熔重金属合金,裂变池顶盖采用高强度轻质顶盖。慢化池顶盖采用密封硅胶进行密封。主冷却剂为铅或铅铋合金,堆芯为燃料棒堆芯,燃料组件可为开口式燃料棒组件或闭式燃料棒组件,开口式燃料棒组件优于闭式燃料棒组件,可以降低裂变池高度。慢化剂为重水,慢化液回路为单向慢化液回路,核控系统为慢化池液位核控系统;停堆时慢化池快速排出慢化液,反应堆因慢化功能缺失而停堆。慢化池设置有增殖棒系统,可在线提取增殖燃料,生产U-233核燃料。实施例四:移动型单慢化池外置耦合核反应堆如图9、图10所示,移动型单慢化池外置快堆型耦合核反应堆为微型或小型核动力装置,如舰船动力。与实施例六大部分相同,所不同的是:燃料组件为闭式燃料棒组件;慢化池301设置变向慢化液回路,核控系统为阻隔屏核控系统。实施例五:单慢化池内置耦合核反应堆如图11、图12所示,单慢化池内置耦合核反应堆为简化的小型或微型核反应堆,热交换器与反应堆合并为一体。反应堆主容器为单慢化池内置耦合结构,慢化池301位于反应堆中心为桶状池型构造,慢化剂为重水或轻水。裂变池201位于慢化池301外侧呈环状池型构造。裂变池内侧壁203设置有大面积薄壁结构的中子交换窗。主冷却剂为铅或铅铋合金,裂变池可设置裂变池气室;堆芯采用固体燃料棒堆芯,堆芯外周可设置转换燃料区,堆芯外侧设置有屏蔽区258。慢化池设置慢化池液位核控系统(固定堆)或阻隔屏核控系统(移动堆);中子源机构401设置在裂变池或慢化池内。反应堆外侧设置热交换池502,热交换池的内侧和裂变池外侧共用一个传热壁503,传热壁503外侧设置传热管504,主冷却剂在传热管504和裂变池201内循环,传热管504和传热壁503上设置有散热片505,传热管504和传热壁503共同导出堆芯热量。热交换池502相当于一、二回路热交换器,二回路冷却剂为水;一回路设置排爆管508和爆破阀509,当发生水泄漏进入传热管504并进入集流室507时,水汽化为蒸汽,比重很轻的蒸汽向上进入排爆管508,爆破阀509受压破膜排出水蒸气,能防止水或蒸汽进入堆芯;水泄漏进入裂变池气室221时,裂变池顶盖202上设置的排爆管508和爆破阀509也能排出水蒸气。裂变池内可设置导流板234;一回路设置或者不设置主循环泵;一回路设置主循环泵235:主冷却剂靠强制循环;一回路不设置主循环泵:主冷却剂靠自循环。实施例六:空间耦合核反应堆如图13、图14所示,反应堆为无主容器外壳的微型或小型空间核动力装置,反应堆径向省略屏蔽构造,减轻重量。主容器为单慢化池外置耦合结构,裂变池201位于中心为桶状,慢化池301位于外侧为环形筒状,慢化剂为石墨,填充在筒状慢化池中;反应堆采用慢化池位移核控系统,慢化池301不接触裂变池201,慢化池301以裂变池201为中心进行轴向移动。主冷却剂为液态金属,特别是液态碱金属,如锂-7,堆芯250主体由闭式燃料棒组件构成,裂变池可设置导流管233。裂变池201热能由液态金属传导给热电转换装置。慢化池位移核控系统行使中子慢化和核控功能,慢化池位移核控系统包括慢化池301和慢化池驱动机构。慢化池驱动机构主体包括慢化池驱动器553、离合器、中心导杆555和回弹装置;中心导杆555轴向固定在裂变池底板205中心。慢化池驱动器553为步进或旋转电机,中心导杆555为螺杆,电机转子轴心为空心状,中心导杆555从电机转子轴心穿过,电机转子环绕中心导杆555旋转。正常运行时,离合器与中心导杆555啮合,电机推动慢化池驱动机构沿着中心导杆555运动和定位;停堆时,离合器与中心导杆555分离,回弹装置将慢化池301拉回或推回远端,即慢化池301远离裂变池201,堆芯因缺乏慢化中子致反应性下降而停堆。实施例七:侧壁设置有大面积中子交换窗口的核反应堆裂变池传统的反应堆主容器只有一个,主容器不设中子交换窗,但设置屏蔽件阻止中子向外泄漏,主容器结构采用均匀厚实结构。上述实施例中所述的大面积中子交换窗口是非均匀结构,在本实施例中详细说明。如图4和图5所示,快堆型耦合核反应堆主容器侧壁203可设置大面积中子交换窗口增加中子交换量,中子交换窗口一般设置在裂变池侧壁203。将裂变池侧壁进行中子交换的区域设置为薄壁构造,形成中子交换窗口。薄壁构造采用框架蒙皮结构或薄壁筋板结构。框架蒙皮结构是在中子交换区域的侧壁部分设置框架133,框架上设置薄板蒙皮132,框架蒙皮结构以外的裂变池部分可采用非薄壁构造,如底板、靠近底部和顶部的侧壁采用厚壁构造。薄壁筋板结构是侧壁以薄壁142为主体,薄壁142上设置筋板143加固。框架蒙皮结构或薄壁筋板结构可以一次性整体构建。裂变池侧壁垂直对称位置设置主框架或主筋板,吊装承力由主框架或主筋板承担。在裂变池承力大的位置设置特别的加固结构,如主冷却剂出口处设置加强框架或加强筋板。裂变池侧壁上缘设置为密封构造可与裂变池顶盖进行密封,构成密闭的裂变池201主容器。实施例八:内置于燃料棒的燃料内胆快堆型耦合核反应堆采用燃料棒组件堆芯,传统的燃料棒是燃料直接填充进燃料棒内。燃料内胆703是燃料的包裹体,以整体形式填充进燃料棒内,隔离燃料与燃料棒。燃料内胆703最先承受燃料的应力和腐蚀,保护燃料棒包壳管728。燃料内胆703是密封件,可以单独长期存放。如图15、图16和图17所示,燃料内胆703主体包括内胆管705、底塞707、顶塞708、填充物722、压紧弹簧721、注气孔709或注气管710。燃料内胆703外径略小于燃料棒包壳管728内径,预留燃料膨胀空间。内胆管705为燃料内胆703的包壳,内胆管705两端由底塞707和顶塞708密封。顶塞708设置有注气孔709或注气管710。燃料内胆内设置填充物(包括燃料)和压紧弹簧721,注气孔709或注气管710供抽气或注气或排气之用;注气孔709为孔状,注气管710为短管状,注气孔709或注气管710可设置为自开式密封结构,在完成注气后进行密封。燃料内胆703在升温或升压或升温加升压后,注气孔709或注气管710自行开口排气,自开式密封结构为可爆裂构造或可熔密封塞。可爆裂构造:注气管710可爆裂,爆裂类型为低强度材料爆裂或低强度结构爆裂。低强度材料是注气管710材质为低强度材料或受热后强度变低的材料,当燃料内胆703温度升高内部气压增高,注气管710受压爆裂自行开口排气;低强度结构是注气管710上设置爆裂槽,爆裂槽处注气管壁很薄,气压差使爆裂槽形成裂缝,注气管710开裂排气。可熔密封塞:可熔密封塞在升温后可熔化,可由单一密封剂或多种密封剂构成,多种密封剂是多种熔点不同的密封剂,密封塞外层熔点低于内层,密封时外层密封剂相当于钎焊料,堆芯启动升温后密封塞受热完全熔化,注气孔709开通排气。燃料内胆703顶端可增设防护罩711,防护罩711为指套管状或帽状,防护罩711上布有孔隙供气体交流,防护罩711设置于注气孔709或注气管710外。在燃料内胆703完成注气密封后,指套管状防护罩711直接焊接在顶塞708顶端;在燃料内胆703填装进燃料棒时,帽状防护罩711由燃料棒压紧弹簧固定在顶塞708之上。防护罩711防止爆裂物或喷溅物接触燃料棒包壳管728;燃料棒或燃料内胆703可填充传热介质,如氦气、钠。燃料内胆703更适宜直接填充颗粒燃料,可以解决先进陶瓷燃料不易烧结成型的难题,燃料内胆703可约束颗粒燃料自烧结成型。燃料颗粒与内胆管705接触紧密,内胆管705承受最先的膨胀应力,当燃料逐渐膨胀到最大直径后,燃料内胆703与包壳管728被压紧在一起,传热效率增加,整体传热效率优于芯块燃料,有利降低燃料棒温度。最初的传热可依靠气体或液态传热介质,如氦气或钠。燃料内胆703将燃料与包壳管728隔离,减轻了包壳管728所受应力和腐蚀,包壳管728不易破裂,有利延长燃料棒寿命。燃料内胆703使燃料棒包壳管728内壁受到隔离保护,根据内胆管705和包壳管728的功能和所处环境不同,两者可以采用不同的材质,朝不同的方向优化。实施例九:开口式燃料棒简化的快堆型耦合核反应堆的裂变池只相当于堆芯吊篮,裂变池上部可设置裂变池气室221,堆芯可以采用开口式燃料棒组件,燃料组件的排气口可以伸出到裂变池气室221,排出的裂变气体可以不接触主冷却剂。如图17和图18所示,开口式燃料棒组件由开口式燃料棒700组合构成;开口式燃料棒700主体结构为底端封闭和顶端开口的棒状包壳管构造,顶端开口处设置有排气细管729。开口式燃料棒700主体包括下端塞725、包壳管728、压紧弹簧721、上端塞726、排气细管729、填充物722或燃料内胆703。燃料棒两端分别焊接有端塞,底端由下端塞725密封,上端塞726上设置开口,开口处焊接有排气细管729,裂变气体由排气细管729排出,开口式燃料棒700无气腔或有较短的上气腔717,填充物722或燃料内胆703上设置压紧弹簧721;燃料棒或燃料内胆703内的填充物722设置相同,填充物722中核素段可分三个区,从下往上分别为下转换区712、燃料区713和上转换区714,上下转换区只初装可转换核素,燃料区713初装有易裂变核素。燃料棒填充物增设一个或两个屏蔽区,屏蔽区设置中子吸收体屏蔽剩余中子,增加堆芯轴向屏蔽功能。设置一个屏蔽区:在填充物最上部设置一个上屏蔽区。设置两个屏蔽区:在填充物的最下部设置下屏蔽区和上部设置上屏蔽区。燃料棒填充物722增设吸附区,吸附区填充蜂窝状固态吸附剂吸附裂变挥发物,吸附区位于上转换区714与上屏蔽区之间或者位于填充物722最上端,吸附区与上屏蔽区可以交换位置。燃料棒填充物从下往上有六种基本分区组合:下转换区-燃料区-上转换区;下转换区-燃料区-上转换区-吸附区;下转换区-燃料区-上转换区-上屏蔽区;下转换区-燃料区-上转换区-吸附区-上屏蔽区;下屏蔽区-下转换区-燃料区-上转换区-上屏蔽区;下屏蔽区-下转换区-燃料区-上转换区-吸附区-上屏蔽区。实施例十:开口式燃料棒组件开口式燃料棒组件由开口式燃料棒700组合构成,开口式燃料棒组件为棒束开口式燃料组件或套管开口式燃料组件;棒束开口式燃料组件无主套管,套管开口式燃料组件有主套管789。开口式燃料组件上部设置有排气构件。如图22所示,棒束开口式燃料组件:棒束开口式燃料组件包括下管座775、棒束底栅板773、骨架管776、定位格架777、开口式燃料棒700、上管座774和排气构件;骨架管776、定位格架777和上下管座共同构成燃料组件的骨架,多个定位格架固定在骨架管束上,骨架管776两端与上下管座固定。骨架管776分两型,第一型是贯通空管,可用作导向管(如核测用导向管);第二型是实管,实管两端焊接有端塞,通过端塞与上下管座固定,实管内设置有可转换燃料、压紧弹簧和较短的气腔,实管相当于转换燃料棒。燃料棒从定位格架777中穿过并被约束定位。燃料棒下端固定在棒束底栅板773上,棒束底栅板773固定在下管座775上端或者固定在骨架管776上。如图23所示,套管开口式燃料组件:套管开口式燃料组件包括管脚785、棒束底栅板773、主套管789、开口式燃料棒700和排气构件。管脚785设置有密封构造防漏流,管脚785还设置有固定构造(如螺栓构造)与堆芯底栅板256固定,管脚785上有多个冷却剂入孔786和控制漏流量的结构。燃料棒底端与棒束底栅板773固定,棒束底栅板773固定在主套管789下端或管脚785上端。液态重金属主冷却剂浮力很大,燃料棒和燃料组件都必须采用下端固定。如图18、图19、图20和图21所示,燃料棒底部固定:燃料组件下部设置有棒束底栅板773,燃料棒固定在棒束底栅板773上,固定方式为螺纹固定或焊接固定或镶嵌式固定。螺纹固定:下端塞725端部与棒束底栅板773设置用于定位的凸台734、凹槽735和用于固定的螺孔738,先镶嵌凸台734和凹槽735定位(可防止燃料棒旋转松动)再用螺钉737进行螺纹固定;另外一种构造是燃料棒下端塞725端部与棒束底栅板773相互设置对应的螺丝和螺孔738进行螺纹固定。焊接固定:燃料棒下端塞725端部设置槽口742,棒束底栅板773的条形栅板插入下端塞725的槽口742再焊接固定。镶嵌式固定:燃料棒下端塞725端部设置键槽747,棒束底栅板上设置相对应的棒束导轨,棒束导轨滑进键槽747进行镶嵌式固定。燃料棒顶端定位:开口式燃料棒组件可以设置棒束顶栅板772进行燃料棒顶端定位,棒束顶栅板772固定在燃料组件主体的上端,即上管座774内或主套管789上端;棒束顶栅板772上设置有定位孔和冷却剂孔,排气细管729穿过棒束顶栅板772上的定位孔使燃料棒被定位,燃料棒上端塞726和棒束顶栅板772间设置防振弹簧,防振弹簧套在排气细管729基部。需要顶端定位的燃料棒排气细管729基部可适当加粗加厚,增强抗外力的强度。燃料组件固定:燃料棒组件的下管座775或管脚785与堆芯底栅板256固定(如螺栓构造)。燃料组件顶部可采用堆芯顶栅板255定位,开口式燃料棒组件以排气主管755上端穿过堆芯顶栅板255的定位孔进行定位。排气构件:开口式燃料棒组件的上部设置排气构件,排气构件主体包括约束部751和排气主管755。约束部751位于排气构件下部并与燃料组件主体连接,约束部751为套管形或喇叭形或爪形。排气构件上部是排气主管755,排气主管755顶端可设置泄压阀757或者不设置泄压阀;设置泄压阀757的排气构件为有阀排气构件,不设置泄压阀的排气构件为无阀排气构件。如图24所示,无阀排气构件:无阀排气构件包括约束部751、排气细管集束731和排气主管755,排气细管729经简单约束成紧密的排气细管集束731后直接套入排气主管755,排气细管729在排气主管755内可以伸缩,排气主管755外侧可设置吊装操作头。如图26所示,有阀排气构件:有阀排气构件主体包括约束部751、密封套管732、排气细管集束731、密封头753、排气主管755和泄压阀757。泄压阀757设置在排气主管755顶端,有阀排气构件内排气细管729在约束部751先经旋曲约束后,其上端部分再约束成紧密的排气细管集束731,即排气细管729在约束部751区段内为松散的旋曲状态,被扭曲的排气细管729有类似弹簧的功能,有一定屈伸功能缓冲燃料棒变形应力,并满足燃料棒辐照伸长的需求。密封套管732下端与约束部751上端固定,密封套管732内套入排气细管集束731,两者在顶端整体密封(如钎焊密封)后构成可排气的密封头753,排气主管755再与密封套管732密封固定,使裂变气体只能通过排气主管755和泄压阀757排出。钎焊料一般难于满足耐高温和抗腐蚀的高需求,钎焊密封的密封头753需要与主冷却剂隔离,适当加长密封套管732,灌注主冷却剂时密封套管732内会留存潴留气体752,这部分不能排出的潴留气体752成为密封头753与主冷却剂的隔离层。排气主管755上设置有注气孔756或注气管,燃料组件制造完成后进行抽真空和注气处理并封闭注气孔756或注气管。密封头753采用钎焊密封,其工艺流程为:燃料棒制作完成后抽真空并封闭排气细管末端(如感应加热后机械压封),封闭排气细管729前可根据需要灌注检测气体,排气细管729长度以顶端略长于密封套管732顶端为宜→完成燃料棒气密性和探伤检查→完成燃料棒组件的主体组装→对排气细管729进行退火并旋曲约束其下部→再约束排气细管729上部形成紧密的排气细管集束731→焊接约束部751与密封套管732连接处→连接约束部与燃料组件主体并使排气细管集束731套进密封套管732→用金属丝塞紧排气细管之间的缝隙→密封处进行表面处理→加热焊料池至焊料熔化(焊料熔点高于主冷却剂最高运行温度)→倒立燃料棒组件,将密封处插入焊料池内合适深度,待焊液充分浸入后取出冷却凝固成密封头753→整理打磨抛光密封套管732→切割掉密封头753的最末端,整理打磨排气细管729端口,确保每根排气细管729畅通。泄压阀:有阀排气构件顶端设置泄压阀757,泄压阀757为弹簧型泄压阀或易熔重金属泄压阀或双泄压阀;有阀排气构件的排气主管755内可设置排气吸附区,排气吸附区包括吸附体定位器766、吸附体765和吸附体压紧弹簧767。吸附体765为布有筛孔的棒状盒体,其内填充吸附剂。吸附体定位器766为定位弹簧或弹性卡具,防止吸附体765位移。吸附体压紧弹簧767压紧吸附体765,防气流冲击和位移。如图27所示,弹簧型泄压阀:弹簧型泄压阀为圆柱状,其包括阀壳体811、下阀体812、上阀体813、弹簧814、弹簧定位头815和压紧螺丝816;阀壳体为圆筒状,下阀体812侧面与阀壳体811固定并密封。下阀体812与上阀体813为凸凹面对应的阀门结构,凸凹面紧贴可实现密封,凸凹面分开可实现排气泄压;下凸上凹的对应结构有利于气体冲刷掉凝结物,阀体不易结垢。下阀体812正中设置通气孔818,上阀体813侧边设置通气孔818。上阀体813上端与弹簧连接,弹簧上端连接有弹簧定位头815,压紧螺丝816向下压紧弹簧定位头815,压紧螺丝816与阀壳体811上端以螺纹固定,弹簧定位头815和压紧螺丝816设置通气孔818供气体排出。如图28所示,易熔重金属型泄压阀:易熔重金属型泄压阀的阀门功能由液态重金属替代,易熔重金属型泄压阀包括环形凹槽、帽盖822、易熔重金属825和防脱堵头827。帽盖822即为上阀体,为盲管形,环形凹槽为下阀体,帽盖822与环形凹槽形成有间隙的镶嵌构造,环形凹槽的间隙内填充易熔重金属825,易熔重金属825为密封剂,防脱堵头827防止帽盖822被内部高压气流冲脱,如防脱螺丝。易熔重金属型泄压阀的工作温度在易熔重金属的熔点之上,低于工作温度时凝固的重金属相当于焊料起固定和密封作用,在泄压时压差力推动气体穿过重金属液体825构成的U型通道,压力差由重金属液体的比重和高度决定,环形凹槽为单体构件或复体构件,单体构件的环形凹槽即下阀体为环形凹槽状整体,复体构件的环形凹槽由阀壳体811、下阀体812和中心气管831焊接密封后构成。如图29所示,双泄压阀:双泄压阀是开口式燃料组件顶端串联两个泄压阀,下方泄压阀为易熔重金属型泄压阀,上方为弹簧型泄压阀,其下阀体812可作为易熔重金属型泄压阀的防脱堵头827。双泄压阀的优点是密封效果好,低温时凝固的重金属能彻底密封,高温时双泄压阀起双保险作用,重金属液体还可以吸收裂变气体中的挥发物,防止阀体结垢,增加弹簧型泄压阀的可靠性。