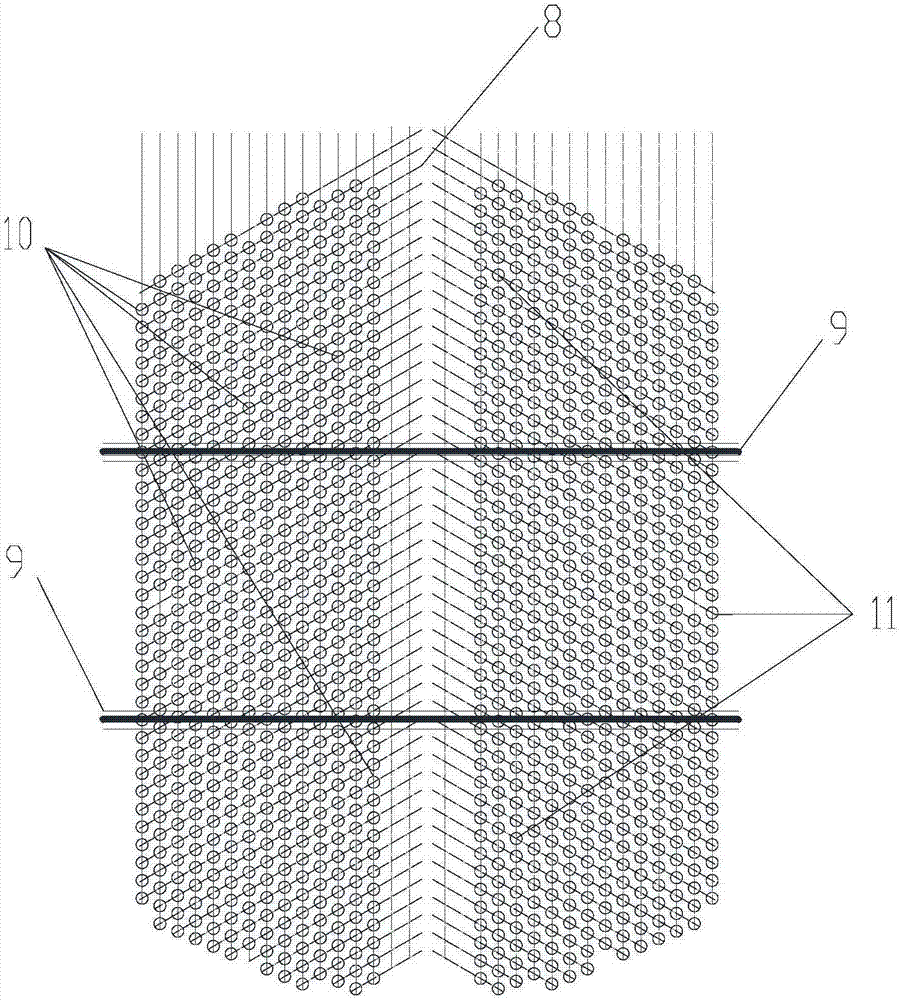
本发明涉及一种百万千瓦级核电站关键技术,特别是涉及一种核电站反应堆余热排出系统泄漏的检测方法。
背景技术:核安全的主要问题是要在任何情况下能够保证燃料持续冷却。正常运行情况下燃料产生的能量由一回路通过蒸汽发生器向二回路传热来导出。反应堆停闭以后,核功率虽然消失,但是由裂变碎片及它的衰变物的衰变产生的剩余功率却缓慢下降。为导出剩余功率,最初会由一回路冷却,当一回路不能够再运行时,则由反应堆余热排出系统(RRA系统)保证反应堆的冷却。如图1所示,反应堆余热排出系统中的主要装置是大型管式换热器,有立式或卧式,由换热器壳体(A流体侧)1、U型传热管2、管板3、位于换热器壳体1侧的进出口水管4、位于传热管侧(B流体侧)的进出口水管5、水室壳体(管箱)6、封头等部件组成。水室壳体由隔板7分为两个空间,两个空间与U型传热管进出口分别联通。隔板7与管板3的中心轴紧密相连,确保流体完全通过U型传热管2在换热器内单向流动。该换热器经过运行后往往带有放射性,如果发生泄漏,不仅会对安全生产、稳定运行等带来重大忧患,还会有工作人员意外放射性照射及环境污染风险。然而,核岛内热交换器泄漏点定位受环境空间限制及放射性工作环境影响,实施难度较大,对于换热器的缺陷处理为重要瓶颈。核电站内核岛换热器查漏技术在本项目建立前一直被国外所掌握和控制,其核岛大型换热器查漏主要实施在蒸汽发生器检漏上,对于类似于RRA系统(反应堆余热排出系统)换热器的查漏实施先例甚少,国内更是没有先例。解决RRA系统换热器是否泄漏的判定问题及漏点定位问题必须依靠自主研发查漏方法。常规的换热器氦气查漏方法为:大空间加压,小空间检测,优点在于小空间有利于泄漏氦气的聚集,空间内结构简单便于操作,有利于残存氦气的清理,对查漏复现性条件建立比较有利。而RRA系统换热器已经安装于现场,管道错综复杂,且经过一个循环的运行,RRA系统侧(B流体侧)已经具有放射性。如果用常规的氦气查漏方法,在空间较小的RRA系统侧(B流体侧)检测有较大的沾污及内污染风险。RRA系统换热器为立式安装,较大的设备冷却水系统(RRI系统)空间位于较小的RRA系统空间上方,由于氦气质量较轻,仅次于氢气,泄漏后聚集在换热器的传热管内不利于取样检测。用常规的查漏方法已经难以判断换热器是否泄漏。目前国内尚没有成熟的适用于核电站核岛现场带有放射性的大型管式换热器氦气查漏技术。
技术实现要素:本发明的目的是在核电站现场判定商运核电站核岛内大型管式换热器是否泄漏,及对泄漏的换热器进行漏点定位,以便对换热器的泄漏缺陷进行处理。本发明目的通过以下技术方案予以实现:核电站反应堆余热排出系统泄漏的检测方法,它包括以下步骤:换热器壳体内侧及传热管干燥条件建立步骤:在商运核电站中,大型管式换热器经过运行后,设备本身带有水份,进行氦气查漏前需先对水份进行烘干,即对换热器壳体内侧(A流体侧)及U型传热管进行干燥,防止设备上存有水膜,影响气体穿过,干燥可使用热空气建立通风实现,干燥条件为无明显水迹存在。换热器壳体及传热管保压条件建立步骤:干燥条件建立后,可实施换热器查漏工作,根据管式换热器的结构可进行换热器壳体内(A流体侧)充氦气、U型传热管外(B流体侧)检测或U型传热管内(B流体侧)充氦气、换热器壳体外侧(A流体侧)检测两种方案,优选换热器壳体内充氦气、U型传热管外检测方案,优点在于:检测过程中发现换热器存在泄漏,可直接利用保压条件进行漏点定位,节省查漏时间。利用换热器壳体内充氦气、U型传热管外检测方案,需先将换热器壳体侧(A流体侧)壁上的开口部分全部封堵,仅保留氦气注入口用于氦气注入,并在氦气注入口安装氦气注入管线及阀门,氦气注入管线上安装有压力表,用以监测换热器壳体内氦气压力;开口部分封堵后,先通过氦气注入管线向换热器壳体内充入空气至1bar.g,然后关闭阀门并等待至少10分钟,优选30分钟,观察壳内压力有无明显下降,如压力没有下降则换热器壳体密封条件良好,可继续实施查漏步骤;如压力明显下降,则可能存在封堵密封不良,需对封堵位置重新封堵处理。所述封堵使用的是专用盲板加密封垫密封。U型传热管管板分区贴膜步骤:换热器壳体及U型传热管保压条件建立后,对U型传热管的管板进行分区,根据管板面积大小,将U型传热管管板分成至少两个区域,优先三个区域,同一U型传热管的进口和出口均位于同一区域内;做好分区后,对每个管板区域分别用薄膜粘贴覆盖;换热器壳体内充压保压步骤:管板粘贴薄膜后,开始向换热器壳体换热器壳体内充氦气;通过换热器壳体换热器壳体上的氦气注入管线向换热器壳体内充入氦气至1bar.g,充氦完毕后,用氦气质谱仪检查换热器法兰、阀门、盲板等接口处有无氦气泄漏,如有泄漏,可通过紧固、更换密封垫等措施进行消漏处理;处理后,继续向换热器壳体内充氦气至压力大于或等于换热器额定设计的工作压力;管板分区查漏步骤:充氦完毕后,对管板贴膜各区域用氦气质谱仪检查有无氦气泄漏;检查时遵循由上到下的顺序对各个区域进行检查,以防止掀开薄膜时如交界处薄膜翘起,又有下方区域泄漏,氦气会污染上部区域造成误判;持续检测6小时以上,如各个区域未发现氦气泄漏,则表明U型传热管密封良好无泄漏,查漏结束;在检测过程中,如发现某区域有氦气迹象,则表明此区域内存在U型传热管泄漏,需进行漏点定位;漏点定位步骤:确定泄漏U型传热管存在的区域后,对泄漏的区域进一步分为两个1/2子区域,按照管板分区查漏的方法进一步缩小泄漏区域;对泄漏区域重新贴膜前,利用抽风装置将U型传热管内气体吸走,以排走子区域内被氦气污染的U型传热管内的氦气以及降低泄漏U型传热管中氦气的浓度;以此类推,逐步缩小泄漏U型传热管区域;当无法进一步缩小泄漏区域时,用薄膜单独粘贴剩余子区域内的U型传热管,对每一根U型传热管进行单独检查,直到找到最终漏点。进一步的,在所述的U型传热管管板分区贴膜步骤中,每根U型传热管的进口和出口对称分布在管板中心轴两侧,管板分区时,将U型传热管沿垂直管板中心轴分为至少两个区域,优选分为三个区域。进一步的,在所述的U型传热管管板分区贴膜步骤中,分区时在管板及管板图上分别做好标记。进一步的,在所述的U型传热管管板分区贴膜步骤中,每个区域内的U型传热管数量满足提高查漏效率要求,即尽量减少查漏次数,又有利于后续缩小查漏范围。进一步的,在所述的U型传热管管板分区贴膜步骤中,每个区域覆盖的薄膜均向相邻区域上的至少一排U型传热管管口延伸,并粘贴在该排U型传热管管口所在的管板上,以防止查漏时遗漏U型传热管。优选向相邻区域上的一排U型传热管管口延伸,并粘贴在该排U型传热管管口所在的管板上。进一步的,在所述的换热器壳体内充压保压步骤中,充入氦气的浓度为50%以上;充氦气后换热器壳体内压力大于或等于换热器额定设计的工作压力。进一步的,在所述的管板分区查漏步骤中,每间隔30分钟对管板贴膜各区域用氦气质谱仪检查有无氦气泄漏,持续检查24小时。进一步的,在所述的管板分区查漏步骤中,检查时,掀开薄膜,并遵循由上到下、由左到右或由右到左的顺序对各个区域进行检查。进一步的,在换热器壳体内侧及传热管干燥条件建立步骤之前,先构建换热器的SAS(空气隔离间)微负压隔离空间,排风装置安装在空间的顶部,换热器置于该空间内;SAS微负压隔离空间设一个供人员进出的门,门上挂有门帘。进一步的,用整片塑料将SAS微负压隔离空间分成两个隔离区域,其中第一区域与U型传热管进口联通,第二区域与U型传热管出口联通;SAS微负压隔离空间的门位于第一区域,排风装置位于第二区域。SAS隔离空间是为防止放射性气体、灰尘扩散而搭建的微负压空间,换热器沾染有放射性物质的部件(管板、换热器壳体等)均置于SAS微负压隔离空间内。SAS微负压隔离空间类似简易房结构,由塑料布、金属管骨架搭建而成,在其顶部安装有排风装置,排风装置通过软管将SAS微负压隔离空间内的气体排放到维修厂房气体处理系统。SAS微负压隔离空间除留有供人员进出的“门”外,无其它开口。人员进出“门”上挂有塑料门帘,以进一步减少SAS微负压隔离空间内空气向外部流通。在漏点定位过程中,需要将泄漏区域的薄膜掀开,因此造成泄漏的U型传热管内的氦气扩散到SAS微负压隔离空间内。同时泄漏传热管内的氦气还会扩散到被同一片薄膜覆盖的U型传热管内。为进一步缩小查漏范围,需要将U型传热管内及SAS微负压隔离空间内的氦气清除。此时,需要利用SAS微负压隔离空间的结构特点,用整片塑料将SAS微负压隔离空间分成两个隔离区域,一个区域与U型传热管进口联通,另外一个区域与U型传热管出口联通。SAS微负压隔离空间的“门”位于U型传热管进口侧,SAS微负压隔离空间的排风装置位于U型传热管出口侧。当排风装置启动时,空气通过SAS微负压隔离空间入口进入U型传热管进口侧,流过U型传热管,通过U型传热管出口侧、排风装置排出整个查漏空间,此过程将没有泄漏但被氦气污染的U型传热管内的氦气清除。本发明的核电站反应堆余热排出系统泄漏的检测方法,是利用分区方法及氦气质谱查漏技术排除未泄漏的传热管,逐步缩小查漏范围;利用SAS微负压隔离空间特点建立更优的查漏条件,通过排风机建立传热管内空气流动,达到消除氦气对查漏区域的干扰,最终实现对泄漏传热管的定位。相对于其它查漏技术,具有泄漏定性准确、漏点定位精确,对系统及设备无影响等优势,并且可根据质谱仪示值变化,定性确定有无泄漏,排除人为误判。该技术适用于所有核电站大型管式换热器泄漏定性及漏点定位,适用于设备出厂鉴定及设备运行后缺陷查找。相对于其它无损检测方式,该方法可判断换热器传热管及管板焊缝泄漏与否。附图说明图1为核电站反应堆余热排出系统大型管式换热器结构示意图;图2为管板分区示意图。具体实施方式实施例一如图1所示,本实施例的核电站反应堆余热排出系统泄漏的检测方法,它包括以下步骤:换热器壳体1内侧及U型传热管2干燥条件建立步骤:干燥条件为无明显水迹存在;换热器壳体1及U型传热管2保压条件建立步骤:干燥条件建立后,可实施换热器查漏工作,根据管式换热器的结构选择换热器壳体1内充氦气、U型传热管2外检测方案。先在换热器壳体1侧壁上保留一个开口,其余开口部分全部封堵,该保留的开口作为氦气注入口用于氦气注入,并在氦气注入口安装氦气注入管线及阀门,氦气注入管线上安装有压力表,用以监测壳体内氦气压力;其余开口部分封堵后,先通过氦气注入管线向换热器壳体1内充入空气至1bar.g,然后关闭阀门并等待10~30分钟,观察换热器壳体1内压力有无明显下降,如压力没有下降则壳体密封条件良好,可继续实施查漏步骤;如压力明显下降,则可能存在封堵密封不良,需对封堵位置重新封堵处理;所述封堵使用的是专用盲板加密封垫密封。U型传热管管板3分区贴膜步骤:换热器壳体1及U型传热管2保压条件建立后,对U型传热管2的管板3进行分区,根据管板3面积大小,将管板3分成两个区域,同一U型传热管2的进口和出口均位于同一区域内;做好分区后,对每个管板区域分别用薄膜粘贴覆盖;换热器壳体1内充压保压步骤:管板3粘贴薄膜后,开始向换热器壳体1内充氦气;通过换热器壳体1上的氦气注入管线向壳体内充入氦气,充氦气后换热器壳体1内压力大于或等于换热器额定设计的工作压力;充氦完毕后,用氦气质谱仪检查换热器法兰、阀门、盲板等接口处有无氦气泄漏,如有泄漏需进行消漏处理;管板分区查漏步骤:充氦完毕后,对管板3的贴膜各区域用氦气质谱仪检查有无氦气泄漏;检查时遵循由上到下的顺序对各个区域进行检查,以在防止掀开薄膜时,如果交界处薄膜翘起,同时下方区域有泄漏的情况下,氦气会污染上部区域造成误判;持续检测6~24小时,如各个区域未发现氦气泄漏,则表明U型传热管2密封良好无泄漏,查漏结束;在检测过程中,如发现某区域有氦气迹象,则表明此区域内存在U型传热管2泄漏,需进行漏点定位;漏点定位步骤:确定泄漏U型传热管2存在的区域后,对泄漏的区域进一步分为两个1/2子区域,按照管板分区查漏的方法进一步缩小泄漏区域;对泄漏区域重新贴膜前,利用抽风装置将U型传热管2内气体吸走,以排走子区域内被氦气污染的U型传热管2内的氦气,以及降低泄漏的U型传热管2中氦气的浓度;以此类推,逐步缩小泄漏的U型传热管2区域;当无法进一步缩小泄漏区域时,用薄膜单独粘贴剩余子区域内的U型传热管2,对每一根U型传热管2进行单独检查,直到找到最终漏点。实施例二如图1~2所示,与实施例一相比,本实施例的核电站反应堆余热排出系统泄漏的检测方法各步骤具有以下不同:在所述的U型传热管管板3分区贴膜步骤中,每根U型传热管2一进一出的两个管口对称分布在管板中心轴8两侧,管板分区时,将U型传热管2沿垂直管板中心轴8分为三个区域,以使每个区域内的U型传热管2数量满足提高查漏效率要求,即尽量减少查漏次数,又有利于后续缩小查漏范围;分区时在管板3及管板图上分别做好标记;每个区域覆盖的薄膜均向相邻区域上的一排或两排U型传热管2的管口延伸,并粘贴在该排U型传热管2管口所在的管板3上,构成重叠区9,以防止查漏时遗漏U型传热管2。在所述的换热器壳体1内充压保压步骤中,充入氦气的浓度为50%以上;先将换热器壳体1内氦气压力充至1bar.g,用氦气质谱仪检查换热器法兰、阀门、盲板等接口处有无氦气泄漏,如有泄漏,可通过紧固、更换密封垫等措施进行消漏处理,此过程可以节省接口处初步查漏消漏时间;处理后继续向壳体内充氦气至压力大于或等于换热器额定设计的工作压力。在所述的管板分区查漏步骤中,检查时遵循由上到下、由左到右的顺序对各个区域进行检查;每间隔30分钟对管板3的贴膜各区域用氦气质谱仪检查有无氦气泄漏,持续检查24小时;检查时,掀开薄膜,并遵循以管板中心轴8为基准,由上到下或由左到右或由右到左的顺序对各个区域进行检查。实施例三与实施例二相比,本实施例的核电站反应堆余热排出系统泄漏的检测方法各步骤具有以下不同:在换热器壳体1内侧及U型传热管2干燥条件建立步骤之前,先构建换热器的SAS微负压隔离空间,排风装置安装在空间的顶部,换热器置于该空间内;SAS微负压隔离空间设一个供人员进出的门,门上挂有门帘。并且用整片塑料将SAS微负压隔离空间分成两个隔离区域,其中第一区域与U型传热管进口10联通,第二区域与U型传热管出口11联通;SAS微负压隔离空间的门位于第一区域,排风装置位于第二区域。本发明并不限于以上实施方式,应当指出,对于本技术领域的普通技术人员来说,在不脱离本发明原理的前提下,还可以做出若干变通,这些变通也属于本发明的保护范围。