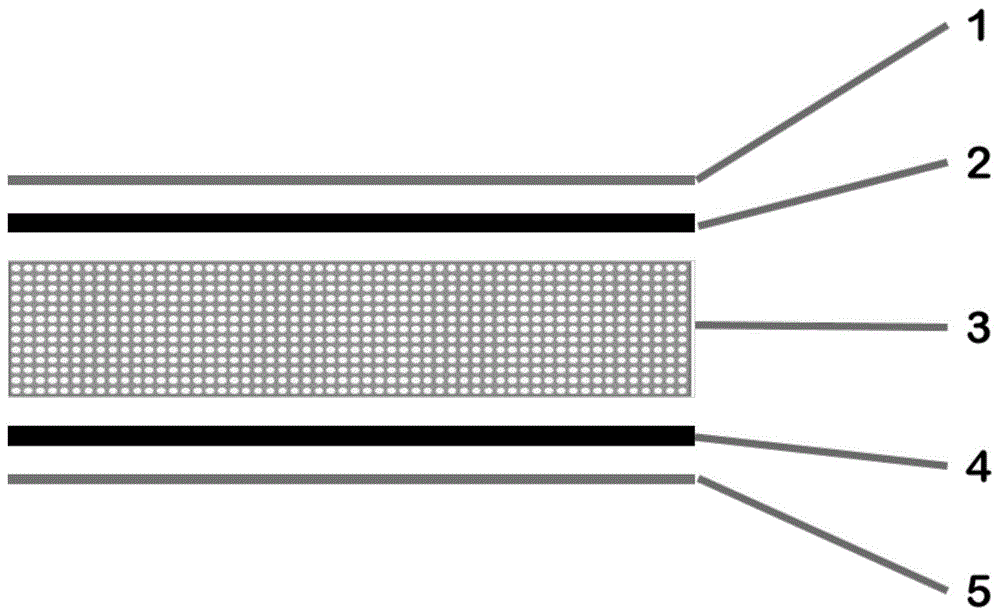
本发明涉及聚丙烯材料
技术领域:
,尤其涉及一种高强度环保微孔发泡聚丙烯复合材料及其制备方法。
背景技术:
:聚丙烯树脂(pp)是一种常见的通用塑料,其具有低密度、高化学稳定性、高耐热、易加工成型等优点,因此在家用电器、汽车制造业等领域有广泛的应用。但随着各领域对材料的机械及环保性能要求的逐渐提高,普通的聚丙烯材料无法继续满足应用需求。目前使用长玻纤增强聚丙烯的机械性能是比较有效的,常规增强方法是将长玻纤与熔融状态聚丙烯混合制备复合材料。但此方法要求聚丙烯具有较高流动性以满足浸润工艺要求,并且材料制作过程中容易出现浮纤现象,即长玻纤与聚丙烯分离而浮于表面。除此以外,长玻纤聚丙烯复合材料由于玻纤的应力集中效应,造成聚合物熔体在发泡过程中破裂,并且较低的熔体强度下容易在发泡过程中发生气体逃逸,造成泡孔破裂,严重影响成品材料的机械性能,这种情况下制备的复合材料性能甚至不如普通的聚丙烯材料。采用超临界流体物理发泡的微孔发泡聚丙烯,生产过程中环保无毒、无任何化学反应及化学残留,同时也是一种新型轻量化材料。其具有微小的泡孔尺寸和均匀的形貌分布,赋予了材料优异的抗冲击性能,是承载应用的理想选择。但在某些对机械性能要求较高的领域,如汽车零部件制造业,其机械强度仍不能满足要求。技术实现要素:本发明的目的在于提供一种用微孔发泡聚丙烯制备的高强度环保复合材料,以解决目前市面上常见的长玻纤增强聚丙烯树脂机械性能交叉,voc含量高的问题,旨在提供一种环保、轻量化、高强度的微孔发泡聚丙烯复合材料。为了解决上述问题,本发明提供了一种用微孔发泡聚丙烯制备的高强度环保复合材料,所述高强度环保复合材料由依次覆盖叠加的第一层无纺布、第一层gmt薄片、芯层mpp、第二层gmt薄片和第二层无纺布组成,且相邻两层之间相互粘结。作为本发明的一种优选,所述第一层无纺布通过单面撒粉或贴膜并经过热处理附在第一层gmt薄片上,所述第二层无纺布通过单面撒粉或贴膜并经过热处理附在第二层gmt薄片上,所述第一层gmt薄片与第二层gmt薄片通过热处理附在所述芯层mpp上。作为本发明的一种优选,第一层gmt薄片是在与第一层无纺布复合后,再通过蒸汽模压工艺附在了芯层mpp上,第二层gmt薄片也经过与第一层gmt薄片相同的处理工艺后附在了芯层mpp上。作为本发明的一种优选,本发明一种用微孔发泡聚丙烯制备的高强度环保复合材料的具体制备工艺如下:将无纺布(或针刺地毯、起绒地毯、簇绒地毯等材料)通过热处理粘合工艺附在gmt薄片上,得到背附无纺布的gmt薄片。将两张背附无纺布的gmt薄片包裹一片mpp片材,然后将包裹后的这组材料放进蒸汽模具进行模压处理。蒸汽模压完成后,在gmt薄片处于熔融状态时将材料转移至冷却模具进行冷却定型,定型完成后获得最终的聚丙烯复合材料。作为本发明的一种优选,所述无纺布的可选克重范围是100—200克/平方米。作为本发明的一种优选,所述无纺布可根据实际需求替换为特定的毯面,如针刺地毯、起绒地毯、簇绒地毯等。作为本发明的一种优选,所述gmt薄片的厚度范围是0.5—1.5毫米。作为本发明的一种优选,所述gmt薄片内部玻璃纤维的长度范围是40—60毫米。作为本发明的一种创新,所述gmt薄片与mpp的粘合不会添加任何胶水,而是将gmt薄片含有的聚丙烯在熔融后充当粘合剂。作为本发明的一种优选,所述熔融状态的gmt薄片由于其在空气中能够快速冷却的特性,故在制备过程中暴露在空气中的时间应尽可能减少,并尽量不超过10秒。作为本发明的一种优选,所述mpp由于其内部含有大量微小的泡孔,在受到外力时能够变形来耗散能量,故微孔发泡聚丙烯能够在实现轻量化的前提下提高其抗冲击性能。作为本发明的一种优选,所述mpp在其发泡过程是完全的物理发泡,无任何化学添加剂,所以mpp是一种新型绿色环保材料。作为本发明的一种优选,所述mpp的发泡倍率范围是10—20倍。作为本发明的一种优选,所述mpp的厚度选择范围是10—30毫米。作为本发明的一种改进,所述mpp可根据实际需求对某一方面性能的特殊要求,添加不同种类的添加剂来达到要求的标准,如阻燃剂、抗氧化剂、着色剂等。作为本发明的一种优选,所述蒸汽模压工艺的模具温度范围是160—180℃。作为本发明的一种优选,所述蒸汽模压工艺的蒸汽喷射时间为10秒。作为本发明的一种优选,所述蒸汽模压工艺的保压时间范围是10—20秒。作为本发明的一种优选,所述蒸汽模压工艺的蒸汽抽气时间为20秒。作为本发明的一种优选,所述蒸汽模压工艺的蒸汽压力约为0.8兆帕。作为本发明的一种优选,所述冷却模具的保压时间范围是40—60秒。作为本发明的一种优选,所述无纺布与gmt薄片的复合可以在蒸汽模具中跟gmt薄片与mpp的复合同时进行,此时生产工艺变成了蒸汽模压处理和冷却定型两个步骤,生产工艺进一步简化。该技术方案具有以下有益的技术效果:(1)本发明在制备或使用过程中产生的废料可回收利用,是一种可回收材料。(2)本发明制备出了能够实现轻量化的高强度复合材料。(3)本发明具有很强的可调整范围,能够根据不同的应用场景有针对性的选择不同的工艺参数或原料,制备出符合要求的复合材料,配方组分选择范围大,能够显著提高产品的竞争力。(4)本发明生产工艺简单,生产流程耗时短,适合大批量生产。(5)采用本技术方案制备的聚丙烯复合材料,与同类材料相比具有更高的机械强度,优异的抗冲击性能使其能够满足承载应用的要求。同时mpp作为微孔发泡材料使其重量更轻,达到了轻量化的要求。该制备过程中未使用任何胶水,故能够通过严格的voc排放测试,增强了该复合材料在家用电器、汽车零部件等领域的应用前景。附图说明图1是本发明的结构示意图;标注说明:1、第一层无纺布,2、第一层gmt薄片3、芯层mpp,4、第二层gmt薄片,5、第二层无纺布。具体实施方式以下结合具体实施例,对本发明做进一步描述。以下所提供的实施例并非用以限制本发明所涵盖的范围,所描述的步骤也不是用以限制其执行顺序。本领域技术人员结合现有公知常识对本发明做显而易见的改进,亦落入本发明要求的保护范围之内。如图1所示,图1是本发明的结构示意图,本发明的一种用微孔发泡聚丙烯制备的高强度环保复合材料包括从上至下依次叠加的第一层无纺布1、第一层gmt薄片2、芯层mpp3、第二层gmt薄片4、第二层无纺布5。实施例1(1)将克重为150克的无纺布单面撒粉,然后通过热处理将无纺布附在gmt薄片(厚度1毫米,玻纤长度50毫米)上;(2)将背附无纺布的gmt薄片与mpp(发泡倍率为15倍,厚度19毫米)按图1示顺序排列,然后将材料放进蒸汽模具中进行蒸汽模压工艺,工艺参数如表1;(3)将蒸汽模压完的材料转移至冷却模具,冷却定型50秒后取出,得到微孔发泡聚丙烯复合材料。实施例2(1)将克重为100克的无纺布单面撒粉,然后通过热处理将无纺布附在gmt薄片(厚度0.8毫米,玻纤长度40毫米)上;(2)将背附无纺布的gmt薄片与mpp(发泡倍率为10倍,厚度14毫米)按图1示顺序排列,然后将材料放进蒸汽模具中进行蒸汽模压工艺,工艺参数如表1;(3)将蒸汽模压完的材料转移至冷却模具,冷却定型40秒后取出,得到微孔发泡聚丙烯复合材料。实施例3(1)将克重为200克的无纺布单面贴膜,然后通过热处理将无纺布附在gmt薄片(厚度1.5毫米,玻纤长度60毫米)上;(2)将背附无纺布的gmt薄片与mpp(发泡倍率为15倍,厚度17毫米)按图1示顺序排列,然后将材料放进蒸汽模具中进行蒸汽模压工艺,工艺参数如表1;(3)将蒸汽模压完的材料转移至冷却模具,冷却定型60秒后取出,得到微孔发泡聚丙烯复合材料。实施例4(1)将无纺布(克重为150克)和毯面(克重为300克)进行单面撒粉;(2)将无纺布、毯面、gmt和mpp(发泡倍率为20倍,厚度19毫米)按照毯面-gmt-mpp-gmt-无纺布的顺序排列,然后将材料放进蒸汽模具中进行蒸汽模压工艺,工艺参数如表2;(3)将蒸汽模压完的材料转移至冷却模具,冷却定型60秒后取出,得到微孔发泡聚丙烯复合材料。实施例1-4的由本发明制得的一种用微孔发泡聚丙烯制备的高强度环保复合材料的工艺参数测定,测试标准:气味测试标准:q/jlyj7110538d-2018、voc测试标准:q/jlyj7110274b-2014,为如下表所示:表2:本发明实施例的各项反应条件、参数对实施例1所制备的环保复合材料与常规的phc/pp六角蜂窝材料进行了voc相关参数的测定,所测得的数据如下表所示:表2:本发明实施例与其他材料voc测试:表3:本发明实施例复合材料的强度测试:注:“15p”表明所用mpp材料的物理发泡倍率;“10mm”表明该材料的厚度。表4:同尺寸mpp材料与phc材料的重量/克重对比表5:同尺寸mpp材料与pp六角蜂窝、phc的力学性能对比:拉伸断裂应力/mpa弯曲最大载荷/mpa弯曲模量/mpampp3.62.5400pp六角蜂窝32.3185phc641000通过上述若干的测试,从表2的测试中,我们对本发明制得的复合材料与phc材料以及pp六角蜂窝材料进行了voc指数的测定,测定的范围包括各大有害气体以及气味等,从表2中可以看出,本发明制备所得的符合材料在各方面均优于phc材料以及pp六角蜂窝材料,在气味上也与之相似,也无刺鼻性气味;在表3的测试中,我们对不同厚度的本发明制得的复合材料进行了弯曲强度、弯曲模量以及拉伸强度的测试,mpp材料的物理发泡率为15p以及20p,厚度为10/14/19mm,在测试中,mpp材料的发泡倍率为15p时强度较高,而整体复合材料的强度是mpp材料的上下两层决定的,因此mpp较薄时材料的强度会稍高,实际选用时mpp材料的厚度为10-30mm均可。表4的测试比较了在常规聚丙烯复合材料中使用的phc材料与本发明所使用的mpp材料在同尺寸时的克重以及重量的对比,本发明所采用的mpp材料在同尺寸在的相较于phc材料减轻了30%以上。表5的测试中我们选用了mpp材料与pp六角蜂窝、phc进行力学性能对比,测试对比中各材料的长宽均相等,发现本发明采用的mpp材料尽管力学性能稍劣于phc材料,但相较于pp六角蜂窝材料还是具有全面的优势的。综上所述的,本发明所制得的复合材料追求环保、轻量化、高强度,而mpp材料有着不俗的强度以及较为轻量化的优势,因此本发明将其应用至聚丙烯复合材料中,本发明最终制备得到的聚丙烯符合材料voc含量低、强度高且质量相对较轻,且本发明生产工艺简单,生产流程耗时短,适合大批量生产,能够大批量的应用于汽车领域,具有较好的商业前景。上述说明示出并描述了发明的若干优选实施例,但如前述,应当理解本发明并非局限于本文所披露的形式,不应看作是对其他实施例的排除,而可用于各种其他组合、修改和环境,并能够在本文所述发明构想范围内,通过上述教导或相关领域的技术或知识进行改动。而本领域人员所进行的改动和变化不脱离本发明的精神和范围,则都应在本发明所附权利要求的保护范围内。当前第1页12