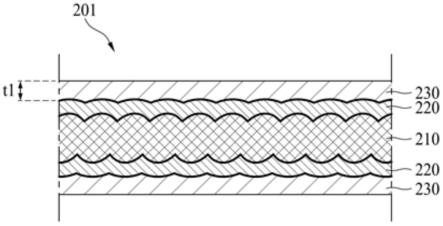
1.本发明涉及一种能够减轻轮胎重量的具有减轻重量的橡胶增强材料、该橡胶增强材料的制备方法和包括这种橡胶增强材料的轮胎。
背景技术:2.随着汽车性能的提高和道路条件的改善,要求轮胎在汽车高速行驶期间保持稳定性和耐久性。并且,考虑到环境问题、能源问题和燃料效率等,需要一种具有减轻的重量并仍然具有优异的耐久性的轮胎。作为满足这种要求的一个解决方案,对用作轮胎的橡胶增强材料的轮胎帘线的研究正在积极地进行。
3.轮胎帘线可以根据所使用的部位和功能来划分。例如,轮胎帘线可以主要分成通常支撑轮胎的胎体、承受载荷并防止随着高速行驶而变形的带束层以及防止带束层变形的冠带层(参见图1)。
4.作为用于轮胎帘线的材料,作为实例可以提到尼龙、人造丝、芳纶和聚酯等。
5.通常,为了与橡胶结合,将轮胎帘线与橡胶组分一起滚压。即,在轮胎的制造过程中包括滚压工艺。然而,在轮胎的制造过程中应用滚压工艺以结合轮胎帘线与橡胶的情况下,工艺成本可能会增加,并且由于滚压,轮胎的密度可能会增加超过必要水平,因此,轮胎的重量可能会不必要地增加。
6.在将橡胶滚压在轮胎帘线中的过程中,一般使用固体橡胶。然而,难以将通过滚压固体橡胶形成的产品制备成200μm以下、具体地5μm至30μm的薄膜形式,并且在将这种产品用作橡胶增强材料的情况下,轮胎的厚度和重量可能会增加。
7.近来,为了轮胎的超轻重量和增强材料的轻量,轮胎制造公司一直尝试降低橡胶层的厚度。滚动阻力(r/r)与轮胎的重量相关,并且对汽车的燃料消耗和二氧化碳的排放有重大影响。例如,随着滚动阻力(r/r)变大,在汽车行驶期间需要的能量也增加。并且,对汽车转动、倾斜和加速的阻力与汽车的重量相关。因此,对通过减轻轮胎重量来减轻汽车的重量、由此降低能耗的研究正在进行。
技术实现要素:8.[技术问题]
[0009]
本发明的一个目的是提供一种具有薄的厚度并仍然具有优异的耐久性的橡胶增强材料。
[0010]
本发明的另一目的是提供一种具有薄的厚度并仍然优异的耐久性的橡胶增强材料的制备方法。
[0011]
本发明的又一目的是提供一种包括所述橡胶增强材料的轮胎。
[0012]
[技术方案]
[0013]
根据本发明的一个实施方案,提供一种橡胶增强材料,包括:
[0014]
纤维基底;
[0015]
位于所述纤维基底上的粘合层;和
[0016]
位于所述粘合层上的橡胶复合物层,
[0017]
其中,所述橡胶复合物层的厚度为2μm至200μm,t50值为150秒至220秒,并且t90值为300秒至350秒。
[0018]
在本文中,t50值是根据astm d2084标准试验方法通过流变仪测量的,达到橡胶复合物层的最大交联密度的50%所需要的时间(秒),并且t90值是达到最大交联密度的90%所需要的时间(秒)。
[0019]
根据本发明的另一实施方案,提供一种所述橡胶增强材料的制备方法,包括以下步骤:
[0020]
制备纤维基底,
[0021]
在所述纤维基底上形成粘合层;和
[0022]
在所述粘合层上涂布橡胶复合物溶液并热处理以在所述粘合层上形成橡胶复合物层,
[0023]
其中,所述橡胶复合物溶液通过在50℃至110℃和30rpm至50rpm下加入所述橡胶复合物溶液中包含的一种组分,并在搅拌的同时依序混合其它组分30秒至120秒而制得。
[0024]
根据本发明的又一实施方案,提供一种包括所述橡胶增强材料的轮胎。
[0025]
在下文中,将详细说明根据本发明的实施方案的橡胶增强材料、所述橡胶增强材料的制备方法以及包括所述橡胶增强材料的轮胎。
[0026]
除非另有定义,否则本文中使用的所有技术术语和科学术语具有与本领域普通技术人员一般理解的含义相同的含义。本文中使用的术语仅用于有效地说明特定的实施方案,并且不旨在限制本发明。
[0027]
单数表达包括其复数表达,除非明确说明或者根据上下文显然并非意在这样做。
[0028]
如本文中所使用的,术语“包括”意在指明存在所实践的特征、数目、步骤、结构元件或它们的组合,并不意在排除存在或加入一个或多个其它的特征、数目、步骤、结构元件或它们的组合的可能性。
[0029]
虽然可以对本发明进行各种改变,并且本发明可以具有各种形式,但是在下面将详细地说明和解释具体的实例。然而,应当理解,这些不意在将本发明限制于特定的公开内容,并且在不背离本发明的精神和技术范围的情况下,本发明包括其所有的改变、等同或替代。
[0030]
并且,在两个部件的位置关系通过“上”、“上方”、“下”、“下方”和“旁边”等来说明的情况下,除非使用表述“正好”或“直接”,否则其它部件可以位于这两个部件之间。
[0031]
并且,在时间顺序通过“之后”、“随后”、“接下来”和“之前”等来说明的情况下,除非使用表述“正好”或“直接”,否则可以包括不连续的情况。
[0032]
并且,用语“至少一个”应当被理解为包括从一个或多个相关项目呈现的所有组合。
[0033]
并且,包括例如“第一”和“第二”等序数的术语仅用于将一个结构元件与其它的结构元件区分开。例如,第一结构元件可以被称为第二结构元件,类似地,第二结构元件可以被称为第一结构元件,而不背离本发明的权利范围。
[0034]
i.橡胶增强材料
[0035]
根据本发明的一个实施方案,提供一种橡胶增强材料,包括:
[0036]
纤维基底;
[0037]
位于所述纤维基底上的粘合层;和
[0038]
位于所述粘合层上的橡胶复合物层,
[0039]
其中,所述橡胶复合物层的厚度为2μm至200μm,t50值为150秒至220秒,t90值为300秒至350秒。
[0040]
(其中t50值是根据astm d2084标准试验方法通过流变仪测量的达到橡胶复合物层的最大交联密度的50%所需要的时间(秒),并且t90值是达到最大交联密度的90%所需要的时间(秒))。
[0041]
作为本发明人的连续研究的结果,证实包括上述性质的橡胶复合物层的橡胶增强材料具有薄的厚度并且仍然表现出优异的耐久性。
[0042]
由于上述实施方案的橡胶增强材料包括所述橡胶复合物层并且表现出均匀的性质,并仍然具有优异的与橡胶的粘合强度,因此在轮胎的制造过程中无需通过滚压工艺也可以与橡胶牢固地结合。因此,所述橡胶增强剂能够降低轮胎制造成本,并且防止由于滚压引起的轮胎的密度和重量不必要的增加。
[0043]
并且,由于所述橡胶增强材料具有与橡胶优异的粘合强度,因此在制造生胎时可以降低气穴(air pocket),从而降低轮胎的缺陷率。
[0044]
由于所述橡胶增强材料具有薄的厚度,因此其满足为了轮胎的超轻重量而降低橡胶层的厚度的要求。此外,所述橡胶增强材料可以降低滚动阻力,并且能够改善汽车的燃料效率。具体地,所述橡胶增强材料能够改善电动车辆的燃料效率和行驶性能。
[0045]
图2和图4分别是根据本发明一个实施例的橡胶增强材料(201、301)的示意性横截面视图。
[0046]
所述橡胶增强材料(201、301)包括纤维基底(210、110)、位于所述纤维基底(210、110)上的粘合层(220)和位于所述粘合层(220)上的橡胶复合物层(230)。
[0047]
根据本发明的实施方案,所述纤维基底可以包括例如合股纱线(110)的纤维纱线和用经纱和纬纱编织的织物基底(210)中的至少一种。
[0048]
所述纤维纱线可以为由一根或多根初捻纱线(111、112)复捻而形成的合股纱线(110)。该初捻纱线可以包括选自尼龙、人造丝、芳纶、聚酯和棉中的一种或多种材料。
[0049]
所述合股纱线包括由不同材料的初捻纱线复捻而形成的混合合股纱线。例如,混合合股纱线可以包括初捻尼龙纱线和初捻芳纶纱线。
[0050]
参照图3,合股纱线(110)包括初捻纱线1(111)和初捻纱线2(112),其中所述初捻纱线1(111)与所述初捻纱线2(112)复捻在一起。所述初捻纱线1(111)具有第一加捻方向,所述初捻纱线2(112)具有第二加捻方向,并且所述初捻纱线1(111)与所述初捻纱线2(112)以第三加捻方向复捻在一起。在本文中,第二加捻方向可以与第一加捻方向相同,并且第三加捻方向可以与第一加捻方向相反。然而,加捻方向不限于此。第一捻数与第二捻数可以彼此相同或不同。所述初捻纱线1(111)与所述初捻纱线2(112)可以分别具有例如150tpm(每米的捻数)至500tpm的捻数。
[0051]
在所述织物基底(210)中,经纱和纬纱可以分别包括选自尼龙、人造丝、芳纶、聚酯
和棉中的一种或多种材料。
[0052]
优选地,经纱可以包括选自尼龙、人造丝、芳纶和聚酯中的一种或多种材料。并且优选地,纬纱可以包括选自尼龙、人造丝、芳纶、聚酯和棉中的一种或多种材料。
[0053]
同时,所述橡胶增强材料(201、301)包括位于所述纤维基底(210、110)上的粘合层(220)。
[0054]
所述粘合层包含间苯二酚-甲醛-胶乳(rfl)。
[0055]
例如,粘合层(220)可以由包含间苯二酚-甲醛-胶乳(rfl)和溶剂的粘合剂涂料溶液形成。
[0056]
间苯二酚-甲醛-胶乳起到粘合剂组分的作用。间苯二酚-甲醛-胶乳尤其改善纤维基底(210、110)与橡胶组分之间的亲和力和粘合强度。由此,粘合层(220)改善纤维基底(210、110)与橡胶复合物层(230)之间的内粘合强度,并且改善橡胶增强材料(201、301)与橡胶(例如,胎面等)之间的外粘合强度。
[0057]
由此,纤维基底(210、110)与橡胶复合物层(230)可以稳定地彼此贴附而不分离,从而降低在轮胎(101)的制造过程中的缺陷率。
[0058]
同时,所述橡胶增强材料(201、301)包括位于粘合层(220)上的橡胶复合物层(230)。
[0059]
橡胶复合物层(230)可以包含选自天然橡胶和合成橡胶中的一种或多种弹性聚合物。
[0060]
橡胶复合物层(230)可以通过在粘合层(220)上涂布包含所述弹性聚合物的液体橡胶复合物溶液来形成。由此,所述橡胶增强材料(201、301)可以具有薄的厚度的橡胶复合物层(230),该厚度难以通过使用固体橡胶的滚压工艺来实现。由于橡胶复合物层(230)的厚度变薄,因此可以有助于将包括橡胶复合物层(230)的橡胶增强材料(201、301)和包括橡胶增强材料(201、301)的轮胎的重量减轻。
[0061]
所述橡胶复合物层(230)可以由包含弹性聚合物、硫、硫化促进剂和硫化延迟剂的橡胶复合物溶液形成。
[0062]
所述弹性聚合物可以为选自天然橡胶和合成橡胶中的一种或多种橡胶。例如,弹性聚合物可以为选自天然橡胶(nr)、苯乙烯-丁二烯橡胶(sbr)、丁二烯橡胶(br)、氯丁二烯橡胶(cr)、异丁烯橡胶(ibr)、异戊二烯橡胶(ir)、丁腈橡胶(nbr)、丁基橡胶和氯丁橡胶中的一种或多种橡胶。
[0063]
所述橡胶复合物溶液可以还包含选自胶溶剂、炭黑、加工油、活化剂、抗老化剂、石油树脂和抗氧化剂中的一种或多种添加剂。
[0064]
所述橡胶复合物溶液可以包含选自甲苯、石脑油、甲醇、二甲苯和四氢呋喃中的至少一种溶剂。
[0065]
所述橡胶复合物层(230)的厚度(t1)可以为2μm至200μm,或5μm至150μm,或5μm至100μm,或5μm至50μm,或10μm至40μm,或20μm至40μm。
[0066]
如图2中所示,所述橡胶复合物层(230)的厚度(t1)测量为自邻接粘合层(220)的橡胶复合物层(230)的一侧至位于粘合层(220)相对侧上的橡胶复合物层(230)的另一侧的最长距离。
[0067]
在现有的橡胶增强材料中,在纤维基底上滚压橡胶基底以形成橡胶层,因此,橡胶
层的厚度一般为1mm以上,或者至少0.8mm以上。
[0068]
相反,由于橡胶复合物层(230)由橡胶复合物溶液形成,因此其可以具有200μm以下的薄的厚度。因此,橡胶增强材料(201、301)的整个厚度会变薄,此外,包括橡胶增强材料(201、301)的轮胎(101)的厚度可以变薄。
[0069]
如果橡胶复合物层(230)的厚度太薄,则橡胶复合物层(230)可能不具有足够的压敏粘合性和粘合强度,因此,在制造轮胎时缺陷率可能增加,并且轮胎的耐久性可能劣化。因此,优选橡胶复合物层(230)的厚度(t1)为2μm以上,或5μm以上,或10μm以上,或20μm以上。
[0070]
然而,如果橡胶复合物层(230)的厚度太厚,则可能不适合本发明提供具有薄厚度的橡胶增强材料(201、301)的目的。具体地,如果橡胶复合物层(230)的厚度太厚,则在溶剂的蒸发过程中在橡胶复合物层(230)中可能形成气泡,因此,橡胶增强材料(201、301)会难以具有均匀的厚度。并且,在应用所述橡胶增强材料(201、301)的轮胎中可能产生气穴,因此,轮胎质量会劣化,并且缺陷率会增加。此外,涂布操作应当进行数次,以便形成厚的橡胶复合物层(230),因此,工艺效率会劣化。因此,优选橡胶复合物层(230)的厚度(t1)为200μm以下、或150μm以下、或100μm以下、或50μm以下、或40μm以下。
[0071]
具体地,所述橡胶复合物层(230)可以具有150秒至220秒的t50值和300秒至350秒的t90值。
[0072]
在本文中,t50值是根据astm d2084标准试验方法通过流变仪测量的达到橡胶复合物层的最大交联密度的50%所需要的时间(秒),并且t90值是达到最大交联密度的90%所需要的时间(秒)。t90值意指最佳的硫化时间,并且t50值意指硫化一半的时间。
[0073]
硫化特性例如t50值和t90值可以使用本领域中常用的任何方法来测量。例如,所述硫化特性可以使用流变仪(所谓的“硫化仪”)来测量。所述硫化特性可以参照文献《matador rubber s.r.o(2007)test methods of rubber materials and products.vert,pp.71-76》来测量。
[0074]
根据本发明的实施方案,为了橡胶复合物层(230)要以适宜的硫化速度形成以均一地表现出在本发明中作为目标的性质(具体地,优异的粘合性质),优选t90值为300秒以上并且t50值为150秒以上。如果t90值和t50值太小,则橡胶的硫化起始时间可能过快,因此,粘合强度可能由于早硫化而降低。
[0075]
然而,如果形成橡胶复合物层(230)的最佳硫化时间和硫化一半的时间过度延长,则可能产生非硫化。因此,优选t90值为350秒以下并且t50值为220秒以下。
[0076]
优选地,橡胶复合物层(230)的t90值可以为300秒至350秒,或305秒至345秒,或305秒至340秒,或310秒至340秒。另外,橡胶复合物层(230)的t50值可以为150秒至220秒,或160秒至220秒,或170秒至210秒,或180秒至210秒。
[0077]
同时,根据消防安全标准(kfs 440)的静电标准,要求汽车轮胎具有小于1.0
×
109ohm/sq的固有表面电阻以防止汽车静电安全事故。
[0078]
根据本发明的实施方案,所述橡胶复合物层(230)可以具有4.0
×
108ohm/sq至8.0
×
108ohm/sq的固有表面电阻,从而表现出满足上述标准的静电性质。
[0079]
优选地,所述橡胶复合物层(230)可以具有4.0
×
108ohm/sq至8.0
×
108ohm/sq、或4.1
×
108ohm/sq至7.8
×
108ohm/sq、或4.2
×
108ohm/sq至7.5
×
108ohm/sq的固有表面电阻。
[0080]
根据本发明的实施方案,所述橡胶复合物层(230)可以具有优异的粘合性质。粘合性质可以由粘合强度来表示。例如,根据astm d4393标准试验方法,所述橡胶复合物层(230)可以表现出17.0n/英寸以上、或17.0n/英寸至17.5n/英寸的粘合强度。于此,粘合强度是通过剥离试验方法(十字头速度:125mm/min)使用instron夹具(grip,cat.no.2712-041)测得的值。
[0081]
在所述橡胶复合物层(230)的粘合强度为17.0n/英寸以上的情况下,所述橡胶增强材料可以附着至橡胶上而不会在轮胎制造过程中损耗(running down),因此,轮胎制造过程可以稳定地进行。在所述橡胶复合物层(230)的粘合强度小于17.0n/英寸的情况下,由于在轮胎制造过程中橡胶增强材料的损耗,可能产生缺陷,并且在制造生胎时,可能产生气穴并且轮胎缺陷率可能会增加。
[0082]
根据上述实施方案的橡胶增强材料(201、301)可以应用于轮胎的冠带层(90)、带束层(50)和胎体(70)中的至少一个。
[0083]
ii.橡胶增强材料的制备方法
[0084]
根据本发明的另一实施方案,提供一种所述橡胶增强材料的制备方法,包括以下步骤:
[0085]
制备纤维基底;
[0086]
在所述纤维基底上形成粘合层;和
[0087]
在所述粘合层上涂布橡胶复合物溶液并热处理以在所述粘合层上形成橡胶复合物层,
[0088]
其中,所述橡胶复合物溶液通过在50℃至110℃和30rpm至50rpm的条件下加入所述橡胶复合物溶液中包含的一种组分,并且在搅拌的同时依序混合其它组分30秒至120秒而制得。
[0089]
对于纤维基底(210)的细节描述,应用“i.橡胶增强材料”的说明。
[0090]
进行在纤维基底(210、110)上形成粘合层(220)的步骤。
[0091]
所述粘合层(220)可以由包含间苯二酚-甲醛-胶乳(rfl)和溶剂的粘合剂涂料溶液形成。
[0092]
例如,粘合剂涂布溶液可以通过将纤维基底(210、110)浸没在粘合剂涂料溶液中而涂布在纤维基底(210、110)上。或者,浸没工艺可以通过使纤维基底(210、110)穿过粘合剂涂料溶液来实现。这种浸没可以在能够控制张力、浸没时间和温度的浸没装置中进行。
[0093]
另外,粘合剂涂布溶液可以通过使用刮刀或涂布机涂布,或者通过使用喷雾器喷涂,而涂布在纤维基底(210、110)上。
[0094]
形成粘合层(220)的步骤可以还包括在纤维基底(210、110)上涂布粘合剂涂料溶液,并在130℃至250℃下热处理80秒至120秒。该热处理可以在用于热处理的常规设备中进行。通过热处理,间苯二酚-甲醛-胶乳(rfl)可以固化或固定以形成粘合层(220)。通过这种热处理,可以更稳定地形成粘合层(220)。
[0095]
随后,进行将橡胶复合物溶液涂覆在粘合层(220)上并热处理以在粘合层(220)上形成橡胶复合物层(230)的步骤。
[0096]
所述橡胶复合物溶液可以包含弹性聚合物、硫、硫化促进剂和硫化延迟剂。
[0097]
所述弹性聚合物可以为选自天然橡胶和合成橡胶中的一种或多种橡胶。例如,弹
性聚合物可以为选自天然橡胶(nr)、苯乙烯丁二烯橡胶(sbr)、丁二烯橡胶(br)、氯丁二烯橡胶(cr)、异丁烯橡胶(ibr)、异戊二烯橡胶(ir)、丁腈橡胶(nbr)、丁基橡胶和氯丁橡胶中的一种或多种橡胶。
[0098]
根据本发明的实施方案,优选所述橡胶复合物溶液包含60至70phr(每百份橡胶的份数)的天然橡胶、30至40phr的苯乙烯-丁二烯橡胶、1至5phr的硫、1至5phr的硫化促进剂和0.1至0.5phr的硫化延迟剂。
[0099]
即,为了形成具有均匀厚度和性质的橡胶复合物层(230),优选所述橡胶复合物溶液包含上述含量范围的组分。不满足上述含量范围的橡胶复合物溶液可能无法涂布至均匀的厚度,因此,会引发疲劳性能的劣化。并且,如果不满足上述含量范围,则所述橡胶复合物层(230)可能不具有150秒至220秒的t50值和300秒至350秒的t90值,从而导致粘合性质的劣化。
[0100]
对硫化促进剂和硫化延迟剂的种类不具体限制。可以应用本领域中可以用作硫化促进剂和硫化延迟剂的任何复合物。作为非限制性的实例,可以应用n-叔丁基-2-苯并噻唑-次磺酰胺(tbbs)和1,3-二苯胍(dpg)等作为硫化促进剂,可以应用n-(环己基硫代)邻苯二甲酰亚胺等作为硫化延迟剂。
[0101]
具体地,为了形成具有非常薄的厚度并且仍然均匀地分散构成组分的橡胶复合物层(230),需要在制备橡胶复合物溶液的过程中加入每一组分之后确立温度、搅拌速度和搅拌时间。
[0102]
根据本发明的实施方案,优选通过在50℃至110℃和30rpm至50rpm下加入橡胶复合物溶液中包含的一种组分、然后在搅拌的同时依序混合其它组分30秒至120秒来制备橡胶复合物溶液。
[0103]
在橡胶复合物溶液的制备过程是在小于50℃的温度下、或以小于30rpm的搅拌速度、或搅拌时间小于30秒进行的情况下,可能难以获得高度分散的橡胶复合物溶液。在橡胶复合物溶液中包含的组分未均匀分散的情况下,橡胶复合物溶液不会涂布至均匀的厚度,因此会引发疲劳性能和粘合性质的劣化。
[0104]
然而,在橡胶复合物溶液的制备过程是在大于110℃的温度下、或以大于50rpm的搅拌速度、或搅拌时间大于120秒进行的情况下,橡胶复合物层可能不具有150秒至220秒的t50值和300秒至350秒的t90值,并且可能不能得到最佳水平的粘合性质。
[0105]
为了制备橡胶复合物溶液,可以使用常用的混合装置,例如螺旋桨型搅拌机。当使用混合装置时,可以考虑搅拌机的直径、介质的密度和传递至介质的搅拌力等来调节搅拌速度。作为非限制的实例,在本发明的制备实例中,容量为10l的螺旋桨型搅拌机(容器直径100cm,螺旋桨直径80cm,螺旋桨长度120cm)用于制备所述橡胶复合物溶液。
[0106]
优选地,温度、搅拌速度和搅拌时间可以根据橡胶复合物溶液中包含的组分的性质来调节。
[0107]
作为非限制的实例,橡胶复合物溶液可以如下制备:
[0108]
在60℃至70℃的温度下,在以30至40rpm搅拌下,混合60至70phr的天然橡胶100秒至120秒(步骤(a)),
[0109]
向步骤(a)的包含混合物的组合物中加入30至40phr的苯乙烯-丁二烯橡胶,然后在100℃至110℃的温度下,在以30rpm至40rpm搅拌下,使它们混合30秒至60秒(步骤(b)),
[0110]
向步骤(b)的包含混合物的组合物中加入1至5phr的硫和0.5至2.5phr的第一硫化促进剂,然后在50℃至60℃的温度下,在以30至40rpm搅拌下,使它们混合30秒至60秒(步骤(c)),和
[0111]
向步骤(c)的包含混合物的组合物中加入0.5至2.5phr的第二硫化促进剂和0.1至0.5phr的硫化延迟剂,然后在70℃至80℃的温度下,在以40至45rpm搅拌下,使它们混合30秒至60秒(步骤(d))。
[0112]
同时,所述橡胶复合物溶液可以还包含本领域中常用的添加剂。
[0113]
例如,所述橡胶复合物溶液可以还包含选自胶溶剂、炭黑、加工油、活化剂、抗老化剂、石油树脂和抗氧化剂中的一种或多种添加剂。
[0114]
对胶溶剂、炭黑、加工油、活化剂、抗老化剂、石油树脂和抗氧化剂的种类不具体限制。可以应用本领域中可以用作添加剂的任何化合物。作为非限制的实例,可以使用2,2'-二苯甲酰氨基二苯基二硫化物等作为胶溶剂;可以使用氧化锌(zno)和硬脂酸等作为活化剂;可以使用聚合的2,2,4-三甲基-1,2-二氢喹啉(tmdq)和n-(1,3-二甲基丁基)-n'-苯基-对苯二胺(6ppd)等作为抗老化剂;并且可以使用蜡等作为抗氧化剂。
[0115]
作为非限制的实例,还包含添加剂的橡胶复合物溶液可以如下制备:
[0116]
在60℃至70℃的温度下,在以30至40rpm搅拌下,混合60至70phr的天然橡胶和0.1至0.5phr的胶溶剂100秒至120秒(步骤(1)),
[0117]
向步骤(1)的包含混合物的组合物中加入30至40phr的苯乙烯-丁二烯橡胶,然后在100℃至110℃的温度下,在以30rpm至40rpm搅拌下,使它们混合30秒至60秒(步骤(2)),
[0118]
向步骤(2)的包含混合物的组合物中加入50至55phr的炭黑和5至10phr的加工油,然后在90℃至100℃的温度下,在以25rpm至35rpm搅拌下,混合30秒至60秒(步骤(3)),
[0119]
向步骤(3)的包含混合物的组合物中加入5至10phr的活化剂和0.5至2.5phr的第一抗老化剂,然后在100℃至110℃的温度下,在以35rpm至45rpm搅拌下,混合30秒至60秒(步骤(4)),
[0120]
向步骤(4)的包含混合物的组合物中加入5至10phr的石油树脂、0.5至2.5phr的第二抗老化剂和1至5phr的抗氧化剂,然后在90℃至100℃的温度下,在以30rpm至40rpm搅拌下,混合30秒至60秒(步骤(5)),
[0121]
向步骤(5)的包含混合物的组合物中加入1至5phr的硫和0.5至2.5phr的第一硫化促进剂,然后在50℃至60℃的温度下,在以30rpm至40rpm搅拌下,使它们混合30秒至60秒(步骤(6)),和
[0122]
向步骤(6)的包含混合物的组合物中加入0.5至2.5phr的第二硫化促进剂和0.1至0.5phr的硫化延迟剂,然后在70℃至80℃的温度下,在以40至45rpm搅拌下,使它们混合30秒至60秒(步骤(7))。
[0123]
所述橡胶复合物溶液可以还包含可以溶解弹性聚合物的溶剂。例如,所述溶剂可以包括选自甲苯、石脑油、甲醇、二甲苯和四氢呋喃中的至少一种。
[0124]
对在粘合层(220)上涂布所述橡胶复合物溶液的方法不具体限制,并且可以应用已知的涂布方法。
[0125]
例如,为了形成橡胶复合物层(230),可以将其上形成有粘合层(220)的纤维基底(210、110)浸没在橡胶复合物溶液中。通过浸没,所述橡胶复合物溶液可以涂布在粘合层
(220)上。
[0126]
作为涂布方法,可以应用凹版涂布法、微凹版涂布法和逗点涂布法(comma coating)等。例如,通过使用逗点涂布机进行逗点涂布,所述橡胶复合物溶液可以涂布在粘合层(220)上。于此,涂布可以在能够蒸发溶剂的温度下,例如,在65℃至100℃的温度下进行。
[0127]
在粘合层(220)上涂布所述橡胶复合物溶液之后,进一步进行热处理。热处理可以在用于热处理的常规设备中进行。对于热处理,可以在50℃至160℃的温度下施加热量30秒至150秒。
[0128]
每单位面积涂布的橡胶复合物溶液的量可以为75g/m2至300g/m2、或100g/m2至200g/m2。通过将粘合层(220)的每单位面积涂布的橡胶复合物溶液的量控制在上述范围内,可以制备具有薄的厚度并且仍然具有优异的粘合性质和耐久性的橡胶增强材料(201、301)。
[0129]
所述橡胶复合物层(230)的厚度(t1)可以为2μm至200μm、或5μm至150μm、或5μm至100μm、或5μm至50μm、或10μm至40μm、或20μm至40μm。
[0130]
同时,在橡胶复合物层(230)形成之后,可以任选地进行切割步骤。切割步骤是根据需要或根据使用目的将以板的形式制备的橡胶增强材料(201、301)进行切割的步骤。所述切割可以使用常用的切割刀或加热刀进行。
[0131]
通过上述方法制备的橡胶增强材料(201、301)可以卷绕在卷绕机上。
[0132]
iii.轮胎
[0133]
根据本发明的又一实施方案,提供一种包括上述橡胶增强材料的轮胎。
[0134]
图1是根据本发明一个实施例的轮胎(101)的局部剖视图。
[0135]
参照图1,轮胎(101)包括胎面(10)、胎肩(20)、胎侧(30)、胎圈(40)、带束层(50)、气密层(60)、胎体(70)和冠带层(90)。
[0136]
胎面(10)是直接接触路面的部分。胎面(10)是贴附至冠带层(90)外侧的坚固橡胶层,并且由具有优异耐磨性的橡胶组成。胎面(10)行使将汽车的驱动力和制动力传递至地面的直接功能。在胎面(10)区域中,形成凹槽(80)。
[0137]
胎肩(20)是边缘部分,并且与胎侧(30)连接。除胎侧(30)之外,胎肩(20)也是轮胎最薄弱部分中的一个。
[0138]
胎侧(30)是轮胎(101)的连接胎面(10)和胎圈(40)的侧部,并且其保护胎体(70)并为轮胎提供侧边稳定性。
[0139]
胎圈(40)是其中包括卷绕胎体(70)端部的钢丝的区域,其中钢丝涂布有橡胶并覆盖帘线。胎圈(40)用于将轮胎(101)装配并固定至轮缘。
[0140]
带束层(50)是位于胎面(10)与胎体(70)之间的覆盖层(coat layer)。带束层(50)用于防止由外部冲击或外部状况对内部构件例如胎体(70)造成的损坏,并且其维持胎面(10)的形状为平的,由此维持轮胎(101)与路面的接触在最佳状况。带束层(50)可以包含根据本发明的实施方案的橡胶增强材料(201)(参见图2)。
[0141]
气密层(60)在无内胎轮胎中用于代替内胎,并且由具有几乎没有透气性或无透气性的特殊橡胶制成。气密层(60)防止轮胎(101)中填充的空气泄漏。
[0142]
胎体(70)是由高强度合成纤维制成的帘线的重合片材形成,并且是用于形成轮胎
(101)的骨架的重要部分。胎体(70)用于承受施加于轮胎(101)的负载和冲击并且维持气压。胎体(70)可以包含根据本发明的实施方案的橡胶增强材料(201)。
[0143]
凹槽(80)是指在胎面区域中的大空隙。凹槽(80)用于在湿路面上行驶时增大排水能力和用于改善抓地力。
[0144]
冠带层(90)是胎面(10)下面的保护层,并且保护内部的其它构件。冠带层(90)必须应用于高速行驶的车辆。具体地,随着车辆的行驶速度增大,轮胎的带束层部分变形使乘坐舒适性劣化,因此,冠带层(90)防止带束层部分变形的重要性提高。冠带层(90)可以包含根据本发明的实施方案的橡胶增强材料(201)。
[0145]
根据本发明的一个实施方案的轮胎(101)包括橡胶增强材料(201)。所述橡胶增强材料(201)可以应用于冠带层(90)、带束层(50)和胎体(70)中的至少一个。
[0146]
[有益效果]
[0147]
根据本发明,提供具有薄的厚度和轻重量并且仍然具有优异耐久性的橡胶增强材料。所述增强材料不仅减轻轮胎的重量,而且能够实现改善的滚动阻力。
附图说明
[0148]
图1是根据本发明一个实施例的轮胎的局部剖视图。
[0149]
图2是根据本发明一个实施例的橡胶增强材料的示意性横截面视图。
[0150]
图3是合股纱线的示意图。
[0151]
图4是根据本发明另一实施例的橡胶增强材料的示意性横截面视图。
[0152]
[附图标记说明]
[0153]
10:胎面
[0154]
20:胎肩
[0155]
30:胎侧
[0156]
40:胎圈
[0157]
50:带束层
[0158]
60:气密层
[0159]
70:胎体
[0160]
80:凹槽
[0161]
90:冠带层
[0162]
101:轮胎
[0163]
110:合股纱线
[0164]
111:初捻纱线1
[0165]
112:初捻纱线2
[0166]
201、301:橡胶增强材料
[0167]
210:织物基底
[0168]
220:粘合层
[0169]
230:橡胶复合物层
具体实施方式
[0170]
在下文中,给出优选的实施例以用于更好地理解本发明。然而,给出这些实施例仅作为本发明的举例说明,而本发明不局限于此。
[0171]
制备例1
[0172]
根据下面步骤(1)至步骤(7),制备橡胶复合物溶液。
[0173]
为了制备橡胶复合物溶液,使用容量为10l的螺旋桨型搅拌机(容器直径100cm,螺旋桨直径80cm,螺旋桨长度120cm,型号名称super-mix mr203,由hado co.,ltd.制造)。
[0174]
在70℃的温度下,在以40rpm搅拌下,将60phr的天然橡胶(根据tsr分类标准为20级,sir20)和0.1phr的胶溶剂(struktol a86)混合120秒[步骤(1)]。
[0175]
向在步骤(1)中获得的混合物中,加入40phr的苯乙烯-丁二烯橡胶(sbr-1502),然后在110℃的温度下在以40rpm搅拌下,使它们混合60秒[步骤(2)]。
[0176]
向在步骤(2)中获得的混合物中,加入50phr的炭黑(n330)和6phr的加工油(石蜡类,p-2,michang),然后在100℃的温度下,在以35rpm搅拌下,使它们混合60秒[步骤(3)]。
[0177]
向在步骤(3)中获得的混合物中,加入5phr的第一活化剂(zno)、2phr的第二活化剂(硬脂酸)和1.5phr的第一抗老化剂(tmdq),然后,在110℃的温度下,在以45rpm搅拌下,使它们混合60秒[步骤(4)]。
[0178]
向在步骤(4)中获得的混合物中,加入7phr的石油树脂(p-90)、1phr的第二抗老化剂(6ppd)和2.5phr的抗氧化剂(蜡),然后在100℃的温度下,在以40rpm搅拌下,使它们混合60秒[步骤(5)]。
[0179]
将在步骤(5)中获得的混合物在室温(25℃)下放置2小时,然后混合。随后,在70℃的温度下,在以40rpm搅拌下,使其混合120秒[步骤(5.5)]。
[0180]
向在步骤(5.5)中获得的混合物中,加入3.4phr的硫和0.85phr的第一硫化促进剂(tbbs),然后在60℃的温度下,在以40rpm搅拌下,使它们混合30秒[步骤(6)]。
[0181]
向在步骤(6)中获得的混合物中,加入0.6phr的第二硫化促进剂(dpg)和0.2phr的硫化延迟剂(n-(环己基硫代)邻苯二甲酰亚胺),然后在80℃的温度下,在以45rpm搅拌下,使它们混合30秒[步骤(7)]。
[0182]
制备例2
[0183]
除了在步骤(1)、步骤(2)、步骤(6)和步骤(7)中的温度如下改变以外,通过与制备例1相同的方法制备橡胶复合物溶液。
[0184]-步骤(1):60℃
[0185]-步骤(2):110℃
[0186]-步骤(6):50℃
[0187]-步骤(7):70℃
[0188]
制备例3
[0189]
除了在步骤(1)、步骤(2)、步骤(6)和步骤(7)中的搅拌速度如下改变以外,通过与制备例1相同的方法制备橡胶复合物溶液。
[0190]-步骤(1):35rpm
[0191]-步骤(2):35rpm
[0192]-步骤(6):30rpm
[0193]-步骤(7):40rpm
[0194]
制备例4
[0195]
除了在步骤(1)、步骤(2)、步骤(6)和步骤(7)中的混合时间如下改变以外,通过与制备例1相同的方法制备橡胶复合物溶液。
[0196]-步骤(1):100秒
[0197]-步骤(2):45秒
[0198]-步骤(6):60秒
[0199]-步骤(7):60秒
[0200]
制备例5
[0201]
除了在步骤(1)、步骤(2)和步骤(3)中的天然橡胶、苯乙烯-丁二烯橡胶和炭黑的含量如下改变以外,通过与制备例1相同的方法制备橡胶复合物溶液。
[0202]-步骤(1):天然橡胶70phr
[0203]-步骤(2):苯乙烯-丁二烯橡胶phr
[0204]-步骤(3):炭黑55phr
[0205]
比较制备例1
[0206]
除了在步骤(6)和步骤(7)中的温度如下改变以外,通过与制备例1相同的方法制备橡胶复合物溶液。
[0207]-步骤(6):45℃
[0208]-步骤(7):70℃
[0209]
比较制备例2
[0210]
除了在步骤(1)、步骤(2)、步骤(6)和步骤(7)中的温度如下改变以外,通过与制备例1相同的方法制备橡胶复合物溶液。
[0211]-步骤(1):75℃
[0212]-步骤(2):120℃
[0213]-步骤(6):70℃
[0214]-步骤(7):90℃
[0215]
比较制备例3
[0216]
除了在步骤(1)、步骤(2)、步骤(6)和步骤(7)中的搅拌速度(rpm)如下改变以外,通过与制备例1相同的方法制备橡胶复合物溶液。
[0217]-步骤(1):25rpm
[0218]-步骤(2):35rpm
[0219]-步骤(6):35rpm
[0220]-步骤(7):40rpm
[0221]
比较制备例4
[0222]
除了在步骤(1)、步骤(2)、步骤(6)和步骤(7)中的搅拌速度(rpm)如下改变以外,通过与制备例1相同的方法制备橡胶复合物溶液。
[0223]-步骤(1):45rpm
[0224]-步骤(2):40rpm
[0225]-步骤(6):45rpm
[0226]-步骤(7):55rpm
[0227]
比较制备例5
[0228]
除了在步骤(1)、步骤(2)、步骤(6)和步骤(7)中的混合时间如下改变以外,通过与制备例1相同的方法制备橡胶复合物溶液。
[0229]-步骤(1):100秒
[0230]-步骤(2):120秒
[0231]-步骤(6):150秒
[0232]-步骤(7):60秒
[0233]
实施例1至实施例5
[0234]
(1)织物基底的制备
[0235]
制备1260de的尼龙长丝(初捻纱线1)和1500de的芳纶长丝(初捻纱线2)。使用捻线机(cable corder),同时进行长丝1和长丝2的初捻(逆时针方向)和复捻(顺时针方向),以制备具有300tpm捻数的合股纱线(110)。
[0236]
使用合股纱线(110)作为经纱和使用棉纱作为纬纱,编织织物以制备厚度为0.04mm的织物基底(210)。
[0237]
(2)粘合层的形成
[0238]
将织物基底(210)浸入包含15重量%的间苯二酚-甲醛-胶乳(rfl)和85重量%的溶剂(水,h2o)的粘合剂涂料溶液中,然后在150℃下热处理100秒以形成粘合层(220)。
[0239]
(3)橡胶复合物层的形成
[0240]
随后,使用逗点涂布机,以120g/m2至130g/m2的每单位面积涂布量在粘合层(220)上涂布各制备例的橡胶复合物溶液,然后在70℃的温度下蒸发溶剂,以制备其中形成有橡胶复合物层(230)的橡胶增强材料(201)。
[0241]
(4)切割
[0242]
将橡胶增强材料(201)切割为10mm的宽度,从而制备用于冠带层(90)的橡胶增强材料。对于切割,使用切割刀。
[0243]
(5)轮胎的制造
[0244]
将切割的橡胶增强材料用于制造205/55r16标准轮胎。为了制造轮胎,使用包括1300de/2股hmls轮胎帘线的帘布层(body ply)和钢丝帘线带束层(steel cord belt)。
[0245]
具体地,将用于帘布层的橡胶层压在气密层橡胶上,层压胎圈钢丝和带束层部,然后应用上面制备的橡胶增强材料,并且依序形成用于形成胎面部、胎肩部和胎侧部的橡胶层,以制造生胎。将生胎放入硫化模具中,并且在170℃下硫化15分钟以制造轮胎。
[0246]
比较例1至比较例5
[0247]
除了在形成橡胶复合物层时在比较制备例中得到的每种橡胶复合物溶液用作橡胶复合物溶液以外,通过与实施例1至实施例5相同的方法制备橡胶增强材料和包括所述橡胶增强材料的轮胎。
[0248]
实验例
[0249]
(1)厚度
[0250]
在根据实施例和比较例的每种橡胶增强材料中,使用mitutoyo corporation的游
标卡尺测量纤维基底和橡胶复合物层的厚度(t1)。
[0251]
(2)橡胶复合物层的硫化特性(t50、t90)
[0252]
从根据实施例和比较例的每种橡胶增强材料中收集橡胶复合物层的样品。根据astm d2084标准试验方法,使用流变仪(mdr 2000,alpha technologies)测量样品的t50值和t90值。
[0253]
(3)粘合剂的压敏粘性
[0254]
根据astm d2979标准试验方法,在以下条件下测量橡胶复合物层的粘合剂的压敏粘性。
[0255]-气缸直径:10mm
[0256]-载荷:300gf
[0257]-剥离速度:5mm/min
[0258]-起始载荷:10gf
[0259]-试验开始时的载荷速度:10mm/min
[0260]-到达目标载荷速度:0.2mm/min
[0261]-保持时间:20s
[0262]
(4)粘合强度
[0263]
根据astm d4393标准试验方法,对橡胶复合物层的条带剥离粘合性进行试验。使用instron夹具(grip,cat.no.2712-041)以125mm/min的十字头速度进行试验。
[0264]
(5)疲劳强度保持率
[0265]
通过弯曲疲劳试验测量疲劳强度保持率。制备长度为30cm并且宽度为1英寸的试样。在170℃下进行硫化15分钟。在试验之前,将试样安装在弯曲疲劳试验机的滑轮上,然后在100℃下放置30分钟。此外,在150rpm、100℃和滑轮尺寸为1英寸的条件下将试样弯曲25,000个循环。于此,滑轮尺寸是指悬挂了试样的滑轮的直径。与运转之前的粘合强度相比,运转后的试样的粘合强度定义为疲劳强度保持率。
[0266]
(6)固有表面电阻
[0267]
对于制备的长度为30cm且宽度为1英寸的试样,使用电阻测量装置(型号名称:insulation tester 1550c,由fluke制造)测量固有表面电阻。
[0268]
[表1]
[0269][0270]
[表2]
[0271][0272]
参照表1和表2,证实,与使用比较制备例1至比较制备例5的橡胶复合物溶液形成的橡胶复合物层相比,使用制备例1至制备例5的每种橡胶复合物溶液形成的橡胶复合物层具有优异的硫化特性(t50、t90)、压敏粘合性和粘合强度,并且仍然具有高疲劳强度保持率和低的固有表面电阻。
[0273]
(7)轮胎的性质评价
[0274]
使用通过滚压工艺制备的轮胎帘线(使用由细度为840丹尼尔的尼龙制成的2股纱线作为经纱,经纱密度为25/英寸),制造205/60r16标准轮胎作为参考例。
[0275]
对于参考例和实施例1的轮胎,测量以下性质。实施例1的轮胎的性质值是基于参考例的性质值(100%)转换的值。
[0276]-材料重量:实施例1的橡胶增强材料和参考例的轮胎帘线的重量
[0277]-轮胎重量:实施例1和参考例的轮胎的重量
[0278]-高速行驶性能:根据us fmvss 139h标准试验方法测量
[0279]-耐久性i:根据us fmvss 139e标准试验方法测量
[0280]-耐久性ii:根据europe ece-r119标准试验方法测量
[0281]-滚动阻力(rrc):根据iso 28580标准试验方法测量
[0282]
[表3]
[0283]
轮胎实施例1(指数)参照例(指数)材料重量30100轮胎重量98100高速行驶性能102100耐久性i102100耐久性ii102100滚动阻力(rrc)102100
[0284]
参照表3,证实与参照例的轮胎相比,包括根据本发明的实施方案的橡胶增强材料的实施例1的轮胎具有轻量并且仍然具有优异的高速行驶性能、耐久性和滚动阻力。