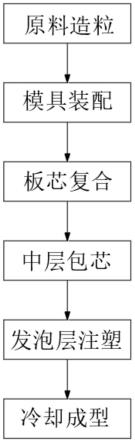
1.本发明涉及包芯板材的加工制备技术领域,具体为微发泡防木塑包芯板材及其制备方法。
背景技术:2.现有的微发泡板材大多采用塑料为原料进行制备,通过注塑的方式实现成型加工。
3.然而在加工过程中,由于塑料的注塑内压不足,尤其是对于面积较大的板材,导致其内部经常产生注塑气孔,影响板材的成型质量,同时由于板材呈微发泡状态,在长时间的磨损和静止过程中,容易出现内腔氧化的情况,进而造成塑料产生木塑情况,严重影响板材的使用寿命。
技术实现要素:4.本发明的目的在于提供微发泡防木塑包芯板材及其制备方法,以解决大面积板材的注塑和质量问题。
5.为实现上述目的,本发明提供如下技术方案:
6.微发泡防木塑包芯板材,所述包芯板材包括发泡层、包芯层和板芯,所述发泡层和包芯层均为聚丙烯塑料注塑成型,所述板芯为木屑、聚丙烯和粘接剂填充而成。
7.优选的,所述包芯层包裹在板芯的外层,所述发泡层包裹在包芯层的外壁,发泡层的厚度小于板芯厚度的二分之一,包芯层的厚度大于发泡层的厚度。
8.一种根据上述的微发泡防木塑包芯板材实现的制备方法,所述制备方法包含以下步骤:
9.原料造粒,取质量比为1:2的聚丙烯塑料和木屑作为原料,通过破碎机进行破碎,得到粉末状的混合原料,再将原料添加粘接剂混合成粘稠状,通过造粒机对粘稠状原料进行造粒;
10.模具装配,根据制备的板件尺寸,制备三层相互套接的空心模具,分别为内层、外层,中层;
11.板芯复合,将内层模具进行加热,颗粒状的原料干燥后,填充在内层板状模具的内腔中,通过液压机进行高压挤压;
12.中层包芯,板芯挤压成型后,并取下内层模具,在中层模具内腔中注塑熔融状态的聚丙烯塑料,形成包芯层;
13.发泡层注塑,在聚丙烯塑料原料中加入发泡剂,充分混合均匀后,带包芯层冷却中80-100摄氏度时,取下中层模具,将混合有发泡剂的聚丙烯塑料原料注塑浇筑在外层模具的内腔中。
14.冷却成型,待外层注塑成型后,冷却至室温,脱去外层模具,得到完整的五层复合结构的包芯板材。
15.优选的,所述造粒机对混合的粘稠状造粒后的颗粒外径为1-3mm,破碎机的破碎转速为2000r/min,破碎后的粉末颗粒为0.1-0.25mm级。
16.优选的,所述内层模具的加热采用循环热风加热或红外线辐射加热,加热的温度为80-100摄氏度,加热挤压的时间为30-45min。
17.优选的,所述包芯层的注塑压力为1-1.5mpa,所述发泡层的注塑压力为1.5-2mpa。
18.优选的,所述中层模具注塑时,板芯的温度为50-80摄氏度.
19.优选的,所述粘接剂采用环氧树脂ab胶,在搅拌前加入环氧树脂a胶,当搅拌混合均匀后,准备复合压铸时,再加入环氧树脂b胶。
20.与现有技术相比,本发明的有益效果是:
21.本发明通过设置分层的包芯板材,从而通过压铸板芯,达到提高板材强度的目的,通过设置包芯层,实现对板芯进行注塑包裹,提供平整的板材外壁,利用带有发泡剂的发泡层,形成微发泡状态的外壁,同时限定了发泡层的厚度,避免发泡间隙较深造成深度氧化,提高了对板材外壁的保护。
附图说明
22.图1为本发明的制备流程图;
具体实施方式
23.下面将结合本发明实施例中的附图,对本发明实施例中的技术方案进行清楚、完整地描述,显然,所描述的实施例仅仅是本发明一部分实施例,而不是全部的实施例。基于本发明中的实施例,本领域普通技术人员在没有做出创造性劳动前提下所获得的所有其他实施例,都属于本发明保护的范围。
24.请参阅图1,本发明提供一种技术方案:
25.实施例1:
26.微发泡防木塑包芯板材,包芯板材包括发泡层、包芯层和板芯,发泡层和包芯层均为聚丙烯塑料注塑成型,板芯为木屑、聚丙烯和粘接剂填充而成,包芯层包裹在板芯的外层,发泡层包裹在包芯层的外壁,发泡层的厚度小于板芯厚度的二分之一,包芯层的厚度大于发泡层的厚度。
27.一种根据上述的微发泡防木塑包芯板材实现的制备方法,制备方法包含以下步骤:原料造粒、模具装配、板芯复合、中层包芯、发泡层注塑和冷却成型。
28.s1:取质量比为1:2的聚丙烯塑料和木屑作为原料,通过破碎机进行破碎,得到粉末状的混合原料,再将原料添加粘接剂混合成粘稠状,通过造粒机对粘稠状原料进行造粒;
29.s2:根据制备的板件尺寸,制备三层相互套接的空心模具,分别为内层、外层,中层;
30.s3:将内层模具进行加热,颗粒状的原料干燥后,填充在内层板状模具的内腔中,通过液压机进行高压挤压;
31.s4:板芯挤压成型后,并取下内层模具,在中层模具内腔中注塑熔融状态的聚丙烯塑料,形成包芯层;
32.s5:在聚丙烯塑料原料中加入发泡剂,充分混合均匀后,带包芯层冷却中80摄氏度
时,取下中层模具,将混合有发泡剂的聚丙烯塑料原料注塑浇筑在外层模具的内腔中。
33.s6:待外层注塑成型后,冷却至室温,脱去外层模具,得到完整的五层复合结构的包芯板材。
34.其中:造粒机对混合的粘稠状造粒后的颗粒外径为1mm,破碎机的破碎转速为2000r/min,破碎后的粉末颗粒为0.1mm级;内层模具的加热采用循环热风加热或红外线辐射加热,加热的温度为80摄氏度,加热挤压的时间为30-45min;包芯层的注塑压力为1mpa,发泡层的注塑压力为1.5mpa;中层模具注塑时,板芯的温度为50摄氏度;粘接剂采用环氧树脂ab胶,在搅拌前加入环氧树脂a胶,当搅拌混合均匀后,准备复合压铸时,再加入环氧树脂b胶。
35.实施例2:
36.微发泡防木塑包芯板材,包芯板材包括发泡层、包芯层和板芯,发泡层和包芯层均为聚丙烯塑料注塑成型,板芯为木屑、聚丙烯和粘接剂填充而成,包芯层包裹在板芯的外层,发泡层包裹在包芯层的外壁,发泡层的厚度小于板芯厚度的二分之一,包芯层的厚度大于发泡层的厚度。
37.一种根据上述的微发泡防木塑包芯板材实现的制备方法,制备方法包含以下步骤:原料造粒、模具装配、板芯复合、中层包芯、发泡层注塑和冷却成型。
38.s1:取质量比为1:2的聚丙烯塑料和木屑作为原料,通过破碎机进行破碎,得到粉末状的混合原料,再将原料添加粘接剂混合成粘稠状,通过造粒机对粘稠状原料进行造粒;
39.s2:根据制备的板件尺寸,制备三层相互套接的空心模具,分别为内层、外层,中层;
40.s3:将内层模具进行加热,颗粒状的原料干燥后,填充在内层板状模具的内腔中,通过液压机进行高压挤压;
41.s4:板芯挤压成型后,并取下内层模具,在中层模具内腔中注塑熔融状态的聚丙烯塑料,形成包芯层;
42.s5:在聚丙烯塑料原料中加入发泡剂,充分混合均匀后,带包芯层冷却中80-100摄氏度时,取下中层模具,将混合有发泡剂的聚丙烯塑料原料注塑浇筑在外层模具的内腔中。
43.s6:待外层注塑成型后,冷却至室温,脱去外层模具,得到完整的五层复合结构的包芯板材。
44.其中:造粒机对混合的粘稠状造粒后的颗粒外径为2mm,破碎机的破碎转速为2000r/min,破碎后的粉末颗粒为0.25mm级;内层模具的加热采用循环热风加热或红外线辐射加热,加热的温度为100摄氏度,加热挤压的时间为30-45min;包芯层的注塑压力为1.5mpa,发泡层的注塑压力为2mpa;中层模具注塑时,板芯的温度为80摄氏度;粘接剂采用环氧树脂ab胶,在搅拌前加入环氧树脂a胶,当搅拌混合均匀后,准备复合压铸时,再加入环氧树脂b胶。
45.实施例3:
46.微发泡防木塑包芯板材,包芯板材包括发泡层、包芯层和板芯,发泡层和包芯层均为聚丙烯塑料注塑成型,板芯为木屑、聚丙烯和粘接剂填充而成,包芯层包裹在板芯的外层,发泡层包裹在包芯层的外壁,发泡层的厚度小于板芯厚度的二分之一,包芯层的厚度大于发泡层的厚度。
47.一种根据上述的微发泡防木塑包芯板材实现的制备方法,制备方法包含以下步骤:原料造粒、模具装配、板芯复合、中层包芯、发泡层注塑和冷却成型。
48.s1:取质量比为1:2的聚丙烯塑料和木屑作为原料,通过破碎机进行破碎,得到粉末状的混合原料,再将原料添加粘接剂混合成粘稠状,通过造粒机对粘稠状原料进行造粒;
49.s2:根据制备的板件尺寸,制备三层相互套接的空心模具,分别为内层、外层,中层;
50.s3:将内层模具进行加热,颗粒状的原料干燥后,填充在内层板状模具的内腔中,通过液压机进行高压挤压;
51.s4:板芯挤压成型后,并取下内层模具,在中层模具内腔中注塑熔融状态的聚丙烯塑料,形成包芯层;
52.s5:在聚丙烯塑料原料中加入发泡剂,充分混合均匀后,带包芯层冷却中80-100摄氏度时,取下中层模具,将混合有发泡剂的聚丙烯塑料原料注塑浇筑在外层模具的内腔中。
53.s6:待外层注塑成型后,冷却至室温,脱去外层模具,得到完整的五层复合结构的包芯板材。
54.其中:造粒机对混合的粘稠状造粒后的颗粒外径为3mm,破碎机的破碎转速为2000r/min,破碎后的粉末颗粒为0.15mm级;内层模具的加热采用循环热风加热或红外线辐射加热,加热的温度为90摄氏度,加热挤压的时间为30-45min;包芯层的注塑压力为1.2mpa,发泡层的注塑压力为1.7mpa;中层模具注塑时,板芯的温度为65摄氏度;粘接剂采用环氧树脂ab胶,在搅拌前加入环氧树脂a胶,当搅拌混合均匀后,准备复合压铸时,再加入环氧树脂b胶。
55.对比例1:
56.采用添加发泡剂的聚丙烯塑料原料在注塑压力为2mpa的压力下注塑实心成型。
57.对比例2:
58.在实施例1的基础上,取质量比为1:1的聚丙烯塑料和木屑作为原料,制备包芯板材;
59.对比例3:
60.在实施例1的基础上,在板芯和包芯层冷却后注塑加工。
[0061] 塑木比注塑温度注塑压力板材截面成型质量实施例11:280/501/1.5mpa强度高,分层不明显实施例21:2100/801.5/12mpa分层明显,强度高实施例31:290/651.2/1.7mpa强度高,分层错位对比例11:0 2mpa截面气孔多,强度低对比例21:180/501/1.5mpa无分层,结构强度差对比例31:2室温1/1.5mpa截面上多组温度应力间隙
[0062]
综上:
[0063]
通过实施例1与对比例1相较,采用分层注塑并包芯加工的方式,减小了板材截面内腔中的气孔量,提高了强度;
[0064]
通过实施例1与对比例2,聚丙烯塑料和木屑的质量配比,影响其板芯的成型强度;
[0065]
通过实施例1与对比例3相较,通过保持注塑前板芯或包芯层的温度,有助于减小
温度差,降低温度应力的产生,提高了成型质量;
[0066]
通过三组实施例相较,在温差越小,注塑压力越大的条件下,分层注塑的成型质量最佳,分层明显,避免相互熔融混合,提高了板材的成型质量和结构强度。
[0067]
尽管已经示出和描述了本发明的实施例,对于本领域的普通技术人员而言,可以理解在不脱离本发明的原理和精神的情况下可以对这些实施例进行多种变化、修改、替换和变型,本发明的范围由所附权利要求及其等同物限定。