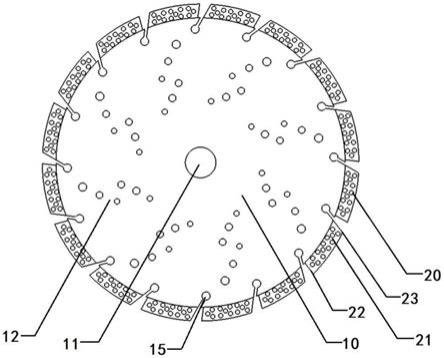
1.本发明涉及金刚石工具的技术领域,更具体地说,本发明涉及一种高性能金刚石圆锯片及其制备方法。
背景技术:2.金刚石圆锯片广泛应用于建筑、桥梁、路面等的机械加工,其中包括石材、混凝土等脆硬材料的切割。在当今高速发展经济的大背景下,低碳环保已经成为大势所趋,基础建设离不开金刚石锯片,由于在浇筑混凝土路面和工程施工过程中随着用工成本的提高和耗材成本的增加,开发节能高效的切割工具的需求越来越迫切,为此开发了各种异型结构、不同厚度的金刚石刀头,虽然异型金刚石刀头在理论上能够提高切割效率和速度,但对于烧结金刚石刀头的抗弯强度、冲击韧性等性能指标提出了更高的要求。
技术实现要素:3.为解决现有技术中存在的上述技术问题,本发明的目的在于提供一种高效节能的高性能金刚石圆锯片及其制备方法。
4.本发明的第一方面提供了一种高性能金刚石圆锯片,包括圆盘基体,圆盘基体外周的边缘上固定有多个金刚石刀头,所述金刚石刀头沿着圆盘基体的圆周方向的侧表面具有相同的倾斜方向;其特征在于:所述金刚石刀头由金属粉末和金刚石颗粒通过冷压成型并热压烧结而成,而所述金属粉末由25~35wt%的cusn合金粉、20~30wt%的fecocu合金粉、3~11wt%的ni粉、1~5wt%的sn粉和余量的fe粉组成;其中,所述金刚石刀头的前表面和后表面上设置有多个圆孔槽,所述圆孔槽的侧壁与所述金刚石刀头的前表面和后表面垂直设置,并且所述多个圆孔槽的底表面的面积之和占所述金刚石刀头的前表面或后表面的正投影面积的15~50%。
5.优选地,所述多个圆孔槽的底表面的面积之和占所述金刚石刀头的前表面或后表面的正投影面积的25~35%。
6.其中,所述金刚石刀头的前表面上的圆孔槽的深度与所述金刚石刀头的后表面上的圆孔槽的深度相同。
7.其中,所述热压烧结的温度为780~850℃,压力为20~30mpa。
8.其中,所述金刚石刀头的抗弯强度大于1200mpa,抗冲击韧性大于22.0j/cm2。
9.本发明的第二方面提供了一种高性能金刚石圆锯片的制备方法,包括以下步骤:
10.(1)将金刚石颗粒和金属粉末混合均后装模后冷压成型得到前表面和后表面上具有多个圆孔槽的金刚石刀头坯体;所述金刚石刀头坯体通过热压烧结得到所述金刚石刀头;并且所述金属粉末由25~35wt%的cusn合金粉、20~30wt%的fecocu合金粉、3~11wt%的ni粉、1~5wt%的sn粉和余量的fe粉组成;
11.(2)将金刚石刀头设置在所述圆盘基体周围相应位置上,通过焊接使所述金刚石刀头和圆盘基体焊接在一起。
12.优选地,所述多个圆孔槽的底表面的面积之和占所述金刚石刀头的前表面或后表面的正投影面积的25~35%。
13.其中,所述金刚石刀头的前表面上的圆孔槽的深度与所述金刚石刀头的后表面上的圆孔槽的深度相同。
14.其中,所述热压烧结的温度为780~850℃,压力为20~30mpa。
15.其中,所述金刚石刀头的抗弯强度大于1200mpa,抗冲击韧性大于22.0j/cm2。
16.与现有技术相比,本发明的高性能金刚石圆锯片及其制备方法具有以下有益效果:
17.本发明的高性能金刚石圆锯片中的金刚石刀头具有优异的抗弯强度和抗冲击韧性,能够适应异型刀头设计;并且通过刀头的优化设计使得锯片切割时,接触面有更多的排屑槽,在切割混凝土、花岗岩时带走更多的砂砾,碎屑,降低切割阻力,同时可以提高散热能力,使刀头可以保持温度不过热,刀头不会钝化,切割锋利度,最终达到事半功倍,提高切割效率,降低材料消耗。本发明的高性能金刚石圆锯片主要用于钢筋混凝土墙面的开孔,切割,以及工程桥梁的切割维护,与现有的市售产品相比,能够显著降低材料消耗,节约材料成本。
附图说明
18.图1为本发明的高性能金刚石圆锯片的平面结构示意图。
具体实施方式
19.以下结合附图对本发明的原理和特征进行描述,所举实例只用于解释本发明,并非用于限定本发明的范围。在下列段落中参照附图以举例方式更具体地描述本发明。根据下面说明和权利要求书,本发明的优点和特征将更清楚。需说明的是,附图均采用非常简化的形式且均使用非精准的比例,仅用以方便、明晰地辅助说明本发明实施例的目的。
20.如图1所示,本发明的高性能金刚石圆锯片,包括圆盘基体10,圆盘基体10外周的边缘上通过激光焊接固定有多个金刚石刀头20,所述圆盘基体10的直径可根据要求,设计为100mm~300mm,所述金刚石刀头20的个数为6~20个。相邻的金刚石刀头20之间的圆盘基体10上设置有与所述相邻的金刚石刀头20之间的间隙邻接的排屑槽15,所述圆盘基体10的中心设置有安装孔11。所述金刚石刀头20的前表面和后表面上设置有多个圆孔槽21,在本发明中,所述圆孔槽21的侧壁与所述金刚石刀头20的前表面或后表面垂直设置,通过垂直设置能够更好的发挥容屑和排屑能力,切割时能带走更多的砂砾,碎屑,降低切割阻力,保证切割的锋利程度,而且所述多个圆孔槽的底表面的面积之和占所述金刚石刀头的前表面或后表面的正投影面积的15~50%,既能够发挥排屑和散热能力,在高速切割时能够带走由刀头与材料切割产生的热量并且顺利排屑,而且在能够保证在圆孔槽垂直设置的情形下,高速切割条件下的稳定性,防止崩裂。优选地,所述多个圆孔槽的底表面的面积之和占所述金刚石刀头的前表面或后表面的正投影面积的25~35%,可以使得锯片可以更加流畅的完成切割,保证切割效果。本发明中,金刚石刀头由金属粉末和金刚石颗粒通过冷压成型并热压烧结而成,热压烧结的温度为780~850℃,压力为20~30mpa。所述金属粉末由25~35wt%的cusn合金粉、20~30wt%的fecocu合金粉、3~11wt%的ni粉、1~5wt%的sn粉和
余量的fe粉组成,上述合金粉末在780~850℃,压力为20~30mpa的烧结条件下,胎体的致密度能够达到97%以上,具有优异的抗弯强度和抗冲击韧性,所述金刚石刀头的抗弯强度大于1250mpa,抗冲击韧性大于22.0j/cm2。在本发明中,为了降低冷压模具的设计成本和制造成本,所有的金刚石刀头均具有相同的结构和尺寸,而且金刚石刀头的前表面上的圆孔槽的深度与所述金刚石刀头的后表面上的圆孔槽的深度相同,所述圆孔槽的深度为所述金刚石刀头厚度的1/5~1/20,优选地,所述圆孔槽的深度为所述金刚石刀头厚度的1/5~1/10。在本发明中,所述圆盘基体10上设置有多个散热孔阵列12,所述散热孔阵列12靠近所述圆盘基体10的外圆区域,在切割过程中,外圆区域离金刚石刀头更近,可以更好的提高风流量来散热,在高速切割时,圆盘基体不会因集聚热量过多而导致发热软化变形,提高安全性。
21.本发明的高性能金刚石圆锯片的制造工序如下:
22.1.基体加工
23.根据图纸要求,将钢板淬火热处理,回火,激光切割形状,回火,磨平面,磨内孔,磨外圆,去毛刺。
24.2.金刚石刀头制备
25.根据具体使用要求,选取金属结合剂,致孔剂(液体石蜡)和金刚石颗粒混合均匀,然后通过冷压成型得到表面具有箭头槽齿的金刚石刀头坯体,热压烧结,砂轮砂带打磨制做金刚石刀头;所述金属粉末由25~35wt%的cusn合金粉、20~30wt%的fecocu合金粉、3~11wt%的ni粉、1~5wt%的sn粉和余量的fe粉组成;所述热压烧结的温度为780~850℃,压力为20~30mpa。
26.3.激光焊接
27.将刀头与基体一起放在按图纸要求相应的基体位置上,将激光焊接机的光点调整到刀头与基体合适的位置,启动激光焊接机焊接,使刀头和基体在激光穿透的瞬间焊接在一起,然后以600n/mm2强度标准对每个金刚石刀头进行焊接强度检测。
28.4.打磨、喷漆、检验
29.将焊接后箭头齿激光焊接锯片先将刀头内侧面喷砂,然后用专用砂轮打磨金刚石刀头的工作面,并使金刚石暴露出来,将焊接后箭头齿激光焊接锯片用磨光机打磨基体表面光亮,然后以600n/mm2强度标准对每个金刚石刀头进行安全焊接强度检测,不合格返工,合格则进行表面喷漆,烘干,以防止表面生锈,最后丝印,激光打标,包装,入库。
30.实施例1
31.将坯料淬火热处理,回火,根据图纸要求,激光切割加工得到中心具有安装孔且直径为300mm的圆盘基体坯料,在圆盘基体的外边缘加工出16个排屑槽并加工出散热孔阵列,回火,磨平面,磨内孔,磨外圆,去毛刺;取cusn合金粉25重量份,fecocu合金粉30重量份,镍粉6重量份,锡粉3重量份,和铁粉36重量份,放入混料桶中混30分钟后,添加金刚石2重量份,继续混料3小时后将粉料加入模具中冷压成型,得到的坯体的前表面和后表面上对称设置有多个圆孔槽,圆孔槽的深度为金刚石刀头厚度的1/10,所述前表面或后表面上的多个圆孔槽的底表面的面积之和占所述金刚石刀头的前表面或后表面的正投影面积的约30%。随后进行热压烧结,热压烧结温度为810℃,压力为28mpa,保温时间为100秒,然后采用砂轮砂带打磨刀头,将刀头与基体一起放在按图纸要求相应的基体位置上,将激光焊接机的光
点调整到刀头与基体合适的位置,启动激光焊接机焊接,使上述制备的16个金刚石刀头和基体在激光穿透的瞬间焊接在一起,以600n/mm2强度标准对每个金刚石刀头进行焊接强度检测,再采用高频焊接护齿,焊接后将箭头齿激光焊接锯片用磨光机打磨基体表面光亮,然后用砂轮打磨金刚石刀头的工作面,并使金刚石暴露出来,然后进行表面喷漆,烘干,以防止表面生锈,最后以600n/mm2强度标准对每个金刚石刀头进行焊接强度检测,不合格返工,合格则进行表面喷漆,烘干,以防止表面生锈,最后丝印,激光打标,包装,入库。
32.实施例2
33.将坯料淬火热处理,回火,根据图纸要求,激光切割加工得到中心具有安装孔且直径为300mm的圆盘基体坯料,在圆盘基体的外边缘加工出16个排屑槽并加工出散热孔阵列,回火,磨平面,磨内孔,磨外圆,去毛刺;取cusn合金粉30重量份,fecocu合金粉40重量份,镍粉5重量份,锡粉5重量份,和铁粉20重量份,放入混料桶中混30分钟后,添加金刚石2重量份继续混料3小时后将粉料灌入模具中冷压成型得到的坯体的前表面和后表面上对称设置有多个圆孔槽,圆孔槽的深度为金刚石刀头厚度的1/10,所述前表面或后表面上的多个圆孔槽的底表面的面积之和占所述金刚石刀头的前表面或后表面的正投影面积的约30%。随后进行热压烧结,热压烧结温度为810℃,压力为28mpa,保温时间为100秒,然后采用砂轮砂带打磨刀头,将刀头与基体一起放在按图纸要求相应的基体位置上,将激光焊接机的光点调整到刀头与基体合适的位置,启动激光焊接机焊接,使上述制备的16个金刚石刀头和基体在激光穿透的瞬间焊接在一起,以600n/mm2强度标准对每个金刚石刀头进行焊接强度检测,再采用高频焊接护齿,焊接后将箭头齿激光焊接锯片用磨光机打磨基体表面光亮,然后用砂轮打磨金刚石刀头的工作面,并使金刚石暴露出来,然后进行表面喷漆,烘干,以防止表面生锈,最后以600n/mm2强度标准对每个金刚石刀头进行焊接强度检测,不合格返工,合格则进行表面喷漆,烘干,以防止表面生锈,最后丝印,激光打标,包装,入库。
34.对比例1
35.与实施例1相比,区别在于对比例1中坯体的前表面和后表面为平面。
36.对比例2
37.与实施例2相比,区别在于对比例1中坯体的前表面和后表面为平面。
38.实施例1和2中制备的金刚石刀头参照gb/t 5318
‑
1985测量抗冲击韧性(a
k
),参照gb/t5319
‑
2002测量抗弯强度,结果记录在表1中。
39.表1
[0040] 实施例1实施例2抗冲击韧性(j/cm2)22.524.3抗弯强度(mpa)13101270
[0041]
按照jb/t3235
‑
1999人造金刚石烧结体磨耗比测定方法对实施例1
‑
2以及对比例1
‑
3进行测试,结果记录在表2中。
[0042]
表2
[0043] 实施例1实施例2对比例1对比例2磨耗比(
×
104)1.391.331.030.98
[0044]
对于本领域的普通技术人员而言,具体实施例只是对本发明进行了示例性描述,显然本发明具体实现并不受上述方式的限制,只要采用了本发明的方法构思及技术方案进
行的各种非实质性的改进,均在本发明的保护范围之内。