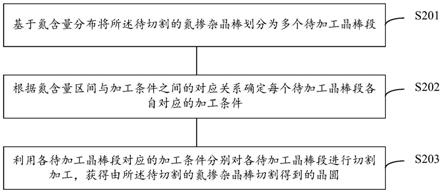
1.本发明实施例涉及晶圆制造技术领域,尤其涉及一种改善氮掺杂晶圆翘曲度的加工方法和系统。
背景技术:2.目前,在大尺寸的半导体级单晶硅片的工艺过程中,通常采用直拉(czochralski)法拉制的单晶硅棒(也可以在一些示例中被称之为晶棒或硅棒)。直拉法包括使由石英制成的坩埚中多晶硅熔化以获得硅熔体,将单晶种浸入硅熔体中,以及连续地提升晶种移动离开硅熔体表面,由此在移动过程中相界面处生长出单晶硅棒。
3.在拉制单晶硅棒的常规方案中,通常会利用氮掺杂技术将微量氮掺入单晶硅晶体,从而能够抑制对集成电路质量产生严重影响的空洞型(cop)缺陷以提高集成电路的成品率;还能够促进直拉单晶硅棒中的氧沉淀和二次诱生缺陷,在后续切割所得到的硅片表面有源区生成高质量的洁净区,以利于集成电路器件制备过程中的金属杂质吸除;而且还可以提高硅片机械强度。
4.目前在利用氮掺杂技术拉制晶棒的过程中,由于氮的分凝系数很小,导致出现偏析现象,从而导致在沿晶棒轴向方向的各位置氮浓度不一致,举例来说,晶棒尾部的含氮量通常会大于晶体头部的含氮量。此外,由于氮掺杂单晶硅所实现的效果程度通常由氮的浓度来决定,因此,晶棒在轴向方向上各位置将会由于氮浓度的不同而体现出不同机械强度,从而在切割工艺过程中出现翘曲的现象。
技术实现要素:5.有鉴于此,本发明实施例期望提供一种改善氮掺杂晶圆翘曲度的加工方法和系统;能够将氮掺杂晶棒进行切割以获得平坦度良好且均一的晶圆。
6.本发明实施例的技术方案是这样实现的:
7.第一方面,本发明实施例提供了一种改善氮掺杂晶圆翘曲度的加工方法,所述方法包括:
8.基于氮含量分布将所述待切割的氮掺杂晶棒划分为多个待加工晶棒段;其中,每个待加工晶棒段均对应于一氮含量区间;
9.根据氮含量区间与加工条件之间的对应关系确定每个待加工晶棒段各自对应的加工条件;其中,所述加工条件使得能够避免对应的待加工晶棒段经由线切割而发生翘曲现象;
10.利用各所述待加工晶棒段对应的加工条件分别对各所述待加工晶棒段进行切割加工,获得由所述待切割的氮掺杂晶棒切割得到的晶圆。
11.第二方面,本发明实施例提供了一种改善氮掺杂晶圆翘曲度的加工系统,所述系统包括:划分部分、确定部分和加工部分;其中,
12.所述划分部分,用于基于氮含量分布将所述待切割的氮掺杂晶棒划分为多个待加
工晶棒段;其中,每个待加工晶棒段均对应于一氮含量区间;
13.所述确定部分,用于根据氮含量区间与加工条件之间的对应关系确定每个待加工晶棒段各自对应的加工条件;其中,所述加工条件使得能够避免对应的待加工晶棒段经由线切割而发生翘曲现象;
14.所述加工部分,用于利用各所述待加工晶棒段对应各所述加工条件分别对各所述待加工晶棒段进行切割加工,获得由所述待切割的氮掺杂晶棒切割得到的晶圆。
15.本发明实施例提供了一种改善氮掺杂晶圆翘曲度的加工方法和系统;将待切割的氮掺杂晶棒按照氮含量区间划分为不同的待加工晶棒段,对于各待加工晶棒段分别确定能够避免翘曲现象的加工条件后,按照相应的加工条件对各自对应的待加工晶棒段进行切割加工,从而获得平坦度良好且均一的晶圆,降低了翘曲现象的发生概率。
附图说明
16.图1为本发明实施例提供的一种氮掺杂单晶硅棒的氮含量分布示意图;
17.图2为本发明实施例提供的改善氮掺杂晶圆翘曲度的加工方法流程示意图;
18.图3为本发明实施例提供的由氮掺杂晶棒切割所得到的待加工晶棒段示意图;
19.图4为本发明实施例提供的多线切割装置组成示意图;
20.图5为本发明实施例提供的效果对比示意图;
21.图6为本发明实施例提供的一种改善氮掺杂晶圆翘曲度的加工系统组成示意图;
22.图7为本发明实施例提供的另一种改善氮掺杂晶圆翘曲度的加工系统组成示意图。
具体实施方式
23.下面将结合本发明实施例中的附图,对本发明实施例中的技术方案进行清楚、完整地描述。
24.对于固液界面来说,杂质在不同相中的溶解度不同,因此,造成杂质在界面两边材料中分布的浓度是不同的,这就是杂质分凝现象,杂质分凝作用的大小通常用分凝系数来描述。对于直拉法拉制单晶硅棒的过程中,硅熔体与单晶硅棒就形成了固液界面;若将氮元素视为杂质,那么在考虑熔体对流对溶质分凝的影响时,利用伯顿(burton)近似后,能够获得杂质分凝的有效分凝系数如式1所示:
[0025][0026]
其中,c
s
表示固相杂质浓度;c
l
表示熔体内部的杂质浓度;k0表示杂质的平衡分凝系数,在本发明实施例中,将氮元素视为杂质,该值优选为7
×
10
‑4。
[0027]
由上式可知,氮的有效分凝系数通常是很小的,那么在通过直拉法拉制单晶硅棒的过程中,随着晶棒的提拉,氮元素会沿晶棒的轴向方向出现偏析现象,最终造成整个晶棒沿轴向方向的氮元素浓度不一致,通常表现为如图1所示,氮含量由晶棒尾部至晶棒头部逐渐降低,具体来说,晶棒尾部的含氮量将明显大于晶棒头部的含氮量。由于氮含量与机械强度呈正向的相关关系,那么基于上述偏析现象的产生,晶棒各部分的机械强度也相应于氮含量的变化而出现差异,比如,晶棒后端部分的氮含量要大于前端部分,那么晶棒后端部分
的机械强度也会明显大于前端部分的机械强度。如此,在对整个氮掺杂单晶硅棒进行线切割或者多线切割时,若对氮掺杂单晶硅棒整体按照相同的加工条件进行加工,则会因为晶棒后端部分的机械强度较大,并且切割钢线的进给量不足,从而造成在加工过程中产生的热量无法及时散失,此时聚集的热量会导致晶棒后端部分切割所得的晶圆产生较为严重的翘曲现象。
[0028]
基于以上之阐述,本发明实施例期望提供一种能够改善氮掺杂晶圆翘曲度的加工方案,通过针对氮掺杂单晶硅棒整体的氮含量情况,分别采用不同的线切割加工条件进行,从而提升切割效率,降低翘曲现象的发生概率,获得平坦度良好且均一的晶圆。基于此,参见图2,其示出了本发明实施例提供的一种改善氮掺杂晶圆翘曲度的加工方法,该方法可以包括:
[0029]
s201:基于氮含量分布将所述待切割的氮掺杂晶棒划分为多个待加工晶棒段;其中,每个待加工晶棒段均对应于一氮含量区间;
[0030]
s202:根据氮含量区间与加工条件之间的对应关系确定每个待加工晶棒段各自对应的加工条件;其中,所述加工条件以使得能够避免对应的待加工晶棒段经由线切割而发生翘曲现象;
[0031]
s203:利用各待加工晶棒段对应的加工条件分别对各待加工晶棒段进行切割加工,获得由所述待切割的氮掺杂晶棒切割得到的晶圆。
[0032]
通过图2所示的技术方案,将待切割的氮掺杂晶棒按照氮含量区间划分为不同的待加工晶棒段,对于各待加工晶棒段分别确定能够避免翘曲现象的加工条件后,按照相应的加工条件对各自对应的待加工晶棒段进行切割加工,从而获得平坦度良好且均一的晶圆,降低了翘曲现象的发生概率。
[0033]
对于图2所示的技术方案,在一些可能的实现方式中,在执行步骤s201之前,所述方法还可以包括:检测待切割的氮掺杂晶棒的氮含量分布。
[0034]
对于上述实现方式,在一些示例中,所述检测待切割的氮掺杂晶棒的氮含量分布,包括:
[0035]
沿所述待切割的氮掺杂晶棒的轴向方向的多个轴向采样位置分别对应采集检测样品;
[0036]
将每个检测样品消除热施主后进行迅速降温,利用傅立叶变换红外光谱仪ftir检测降温后每个检测样品对应的氮含量,以获得用于表征所述待切割的氮掺杂晶棒的氮含量分布的所述各轴向采样位置的氮含量。
[0037]
需要说明的是,通过上述实现方式,能够获取到整根待切割的氮掺杂晶棒的氮含量分布。以图1所示为例,可以通过设置合适的氮含量阈值将氮含量分布划分为3个区间,分别如图1中所示被标记为i、ii和iii;其中,i区间对应于整根待切割氮掺杂晶棒的头部部分,iii区间对应于整根待切割的氮掺杂晶棒的尾部部分,ii区间则对应于整根待切割的氮掺杂晶棒的中间部分。相应于被标记的氮分布区间,可以将待切割的氮掺杂晶棒划分为3个部分,具体来说,如图3所示,可以将待切割的氮掺杂晶棒通过切割的方式得到3个待加工晶棒段,由于每个待加工晶棒段均对应于一个氮含量分布区间,因此,在本实施例中,各待加工晶棒段的标识可以被标记为与对应的氮含量分布区间的标记一致,即被标记为i、ii和iii。对于图3所示的3个待加工晶棒段来说,对应于待切割氮掺杂晶棒的头部部分的待加工
晶棒段i,其氮含量是最低的;对应于待切割氮掺杂晶棒尾部部分的待加工晶棒段iii,其氮含量是最高的;对应于待切割氮掺杂晶棒中间部分的待加工晶棒段ii,其氮含量介于待加工晶棒段i的氮含量与待加工晶棒段iii的氮含量之间。
[0038]
对于图2所示的技术方案,在一些可能的实现方式中,所述根据氮含量区间与加工条件之间的对应关系确定每个待加工晶棒段各自对应的加工条件,包括:
[0039]
针对每个待加工晶棒段,在线切割过程中分别采集设定的多个径向位置处的温度值;
[0040]
根据各待加工晶棒段在相同径向位置处的温度值确定各待加工晶棒段之间的温度差;
[0041]
基于各待加工晶棒段之间的温度差确定各待加工晶棒段对应的钢线进给量,以使得除位于所述待切割的氮掺杂晶棒首部以外的待加工晶棒段的加工温度与位于所述待切割的氮掺杂晶棒首部的待加工晶棒段的加工温度一致。
[0042]
对于上述实现方式,在一些示例中,在所述各待加工晶棒段中,位于所述待切割的氮掺杂晶棒首部的待加工晶棒段对应的钢线进给量小于除位于所述待切割的氮掺杂晶棒首部以外的待加工晶棒段对应的钢线进给量。
[0043]
针对上述实现方式及其示例,具体来说,结合前述图3所示的3个待加工晶棒段为例,由于各待加工晶棒段的氮含量不一致,并结合氮含量与机械强度之间的正相关关系,可以获知:待加工晶棒段i的机械强度弱于待加工晶棒段ii的机械强度,待加工晶棒段iii的机械强度则是3个待加工晶棒段中最高的。如果在进行线切割或多线切割的过程中,对这3根待加工晶棒段均采用适配待加工晶棒段i的加工条件进行切割加工,那么就会由于待加工晶棒段ii和待加工晶棒段iii机械强度过大而产生过多的热量造成加工温度升高,形成与待加工晶棒段i的加工温度的温度差,从而增加由待加工晶棒段ii和待加工晶棒段iii切割所得的硅片发生翘曲现象的概率。为了避免翘曲现象发生,就需要对该温度差进行弥补。详细来说,对于待加工晶棒段i、待加工晶棒段ii和待加工晶棒段iii,由首部沿待切割的氮掺杂晶棒轴向选取330mm、1060mm和1730mm位置分别对应于待加工晶棒段i、待加工晶棒段ii和待加工晶棒段iii进行径向采集温度的位置。具体可以均在各自的径向位置76mm、151.35mm以及259.11mm处分别采集切割过程的温度。如图3所示,在待加工晶棒段i的径向位置76mm、151.35mm以及259.11mm处分别采集温度值为a、b、c;在待加工晶棒段ii的径向位置76mm、151.35mm以及259.11mm处分别采集温度值为a’、b’、c’;在待加工晶棒段iii的径向位置76mm、151.35mm以及259.11mm处分别采集温度值为a”、b”、c”。随后,根据上述采集到的温度值,计算各待加工晶棒段之间的温度差,在本实施例中,也就是计算待加工晶棒段i和待加工晶棒段ii之间的温度差以及待加工晶棒段ii和待加工晶棒段iii之间的温度差。具体温度差的计算结果如表1所示:
[0044]
表1
[0045][0046]
其中,δt1表示待加工晶棒段i和待加工晶棒段ii之间的温度差;δt2表示待加工晶棒段ii和待加工晶棒段iii之间的温度差。
[0047]
通过表1所得到的数据,为了弥补加工过程中的温度差,需要调整各待加工晶棒段的加工条件,以使得待加工晶棒段ii和待加工晶棒段iii的加工温度与待加工晶棒段i的加工温度一致,避免因为机械强度大以及切割产热多发生硅片翘曲现象。在本发明实施例中,加工条件具体优选为加工时的钢线进给量。结合图3以及前述内容,待加工晶棒段i、待加工晶棒段ii和待加工晶棒段iii由于氮含量逐渐升高从而机械强度也相应提升,那么为了使得在切割加工过程中的加工温度均保持在对待加工晶棒段i进行切割时的加工温度,本发明实施例通过提升待加工晶棒段ii和待加工晶棒段iii的钢线进给量来保持加工温度。详细来说,以钢线的进给比例表征钢线进给量,待加工晶棒段i、待加工晶棒段ii和待加工晶棒段iii对应的钢线进给量如表2所示:
[0048]
表2
[0049]
待加工晶棒段标识iiiiii钢线进给量180%200%220%
[0050]
对于上述钢线进给量这一概念,在本实施例中详细来说,在一个加工周期cycle time内,设定最初的给线量是x,收线量是y,此时的钢线进给量是x
‑
y,进给比例视为100%;在同样的一个cycle time内,若设定的给线量是2x
‑
y,收线量是y,那么钢线进给量为2*(x
‑
y),进给比例则为200%;若设定给线量是3x
‑
2y,收线量是y,那么钢线进给量为3*(x
‑
y),进给比例则为300%,以此类推。
[0051]
根据以上阐述,在获得表2所示的待加工晶棒段i、待加工晶棒段ii和待加工晶棒段iii分别对应的钢线进给量之后,以图4所示的多线切割装置为例,在图4中,该装置包括放线轴1、收线轴2、导轮3、晶棒进给台5和钢线6,在利用图4所示的装置对待切割的氮掺杂晶棒4进行切割过程中,当切割硬度较小的待加工晶棒段i时,控制放线轴1的钢线供给量为较小值,如表2中的180%;当待加工晶棒段i加工完成后,将硬度居中的待加工晶棒段ii粘贴至图4中晶棒进给台5上,在切割待加工晶棒段ii时,控制放线轴1的钢线供给量较大于切割待加工晶棒段i的钢线进给量,如表2中的200%;当待加工晶棒段ii加工完成后,将硬度最高的待加工晶棒段iii粘贴至图4中晶棒进给台5上,在切割硬度较大的待加工晶棒段iii
时,控制放线轴1的钢线供给量最大,如表2中的220%。可以理解地,此时新钢线的供给量大,可以即使带走机械加工产生的热量,避免因温度过高,使得切割的硅片发生严重翘曲,从而极大的降低了出现温度差的概率。
[0052]
通过上述技术方案及其实现方式和示例对钢线进给量进行调整之后切割所得到的晶圆挠曲度warp品质与目前常规方案中使用同一加工条件而不调整钢线进给量进行切割所得到的晶圆warp品质相比,如图5所示,图中横坐标为待切割的氮掺杂晶棒的位置,纵坐标为晶圆的warp值,单位为微米(μm)。图5中的纯黑色实心点表示对钢线进给量进行调整之后的warp;灰色实心点表示不调整钢线进给量的warp,由图5中可以看出,采用本发明实施例的技术方案,相较于常规方案,能够获得平坦度更为良好且均一的晶圆,降低了翘曲现象的发生概率。
[0053]
基于前述技术方案相同的发明构思,参见图6,其示出了本发明实施例提供的一种改善氮掺杂晶圆翘曲度的加工系统60,该系统60包括:划分部分601、确定部分602和加工部分603;其中,
[0054]
所述划分部分601,用于基于氮含量分布将所述待切割的氮掺杂晶棒划分为多个待加工晶棒段;其中,每个待加工晶棒段均对应于一氮含量区间;
[0055]
所述确定部分602,用于根据氮含量区间与加工条件之间的对应关系确定每个待加工晶棒段各自对应的加工条件;其中,所述加工条件使得能够避免对应的待加工晶棒段经由线切割而发生翘曲现象;
[0056]
所述加工部分603,用于利用各所述待加工晶棒段对应各所述加工条件分别对各所述待加工晶棒段进行切割加工,获得由所述待切割的氮掺杂晶棒切割得到的晶圆。
[0057]
具体来说,所述加工部分603,具体可以为前述图4所示的多线切割装置,本发明实施例对此不做赘述。
[0058]
在一些示例中,如图7所示,所述确定部分602,包括采集设备6021和数据处理设备6022;其中,
[0059]
所述采集设备6021,用于针对每个待加工晶棒段,在线切割过程中分别采集设定的多个径向位置处的温度值;
[0060]
所述数据处理设备6022,用于根据各待加工晶棒段在相同径向位置处的温度值确定各待加工晶棒段之间的温度差;以及,
[0061]
基于各待加工晶棒段之间的温度差确定各待加工晶棒段对应的钢线进给量,以使得除位于所述待切割的氮掺杂晶棒首部以外的待加工晶棒段的加工温度与位于所述待切割的氮掺杂晶棒首部的待加工晶棒段的加工温度一致。
[0062]
在一些示例中,所述划分部分601,用于将所述待切割的氮掺杂晶棒基于氮含量分布切割为多个待加工晶棒段。
[0063]
在一些示例中,如图7所示,所述系统60还包括检测部分604,经配置为:检测所述待切割的氮掺杂晶棒的氮含量分布。
[0064]
可以理解地,在本实施例中,“部分”可以是部分电路、部分处理器、部分程序或软件等等,当然也可以是单元,还可以是模块也可以是非模块化的。
[0065]
另外,在本实施例中的各组成部分可以集成在一个处理单元中,也可以是各个单元单独物理存在,也可以两个或两个以上单元集成在一个单元中。上述集成的单元既可以
采用硬件的形式实现,也可以采用软件功能模块的形式实现。
[0066]
所述集成的单元如果以软件功能模块的形式实现并非作为独立的产品进行销售或使用时,可以存储在一个计算机可读取存储介质中,基于这样的理解,本实施例的技术方案本质上或者说对现有技术做出贡献的部分或者该技术方案的全部或部分可以以软件产品的形式体现出来,该计算机软件产品存储在一个存储介质中,包括若干指令用以使得一台计算机设备(可以是个人计算机,服务器,或者网络设备等)或processor(处理器)执行本实施例所述方法的全部或部分步骤。而前述的存储介质包括:u盘、移动硬盘、只读存储器(rom,read only memory)、随机存取存储器(ram,random access memory)、磁碟或者光盘等各种可以存储程序代码的介质。
[0067]
因此,本实施例提供了一种计算机存储介质,所述计算机存储介质存储有改善氮掺杂晶圆翘曲度的加工程序,所述改善氮掺杂晶圆翘曲度的加工程序被至少一个处理器执行时实现上述技术方案中所述改善氮掺杂晶圆翘曲度的加工方法步骤。
[0068]
可以理解地,上述改善氮掺杂晶圆翘曲度的加工装置60的示例性技术方案,与前述改善氮掺杂晶圆翘曲度的加工方法的技术方案属于同一构思,因此,上述对于改善氮掺杂晶圆翘曲度的加工装置60的技术方案未详细描述的细节内容,均可以参见前述改善氮掺杂晶圆翘曲度的加工方法的技术方案的描述。本发明实施例对此不做赘述。
[0069]
需要说明的是:本发明实施例所记载的技术方案之间,在不冲突的情况下,可以任意组合。
[0070]
以上所述,仅为本发明的具体实施方式,但本发明的保护范围并不局限于此,任何熟悉本技术领域的技术人员在本发明揭露的技术范围内,可轻易想到变化或替换,都应涵盖在本发明的保护范围之内。因此,本发明的保护范围应以所述权利要求的保护范围为准。