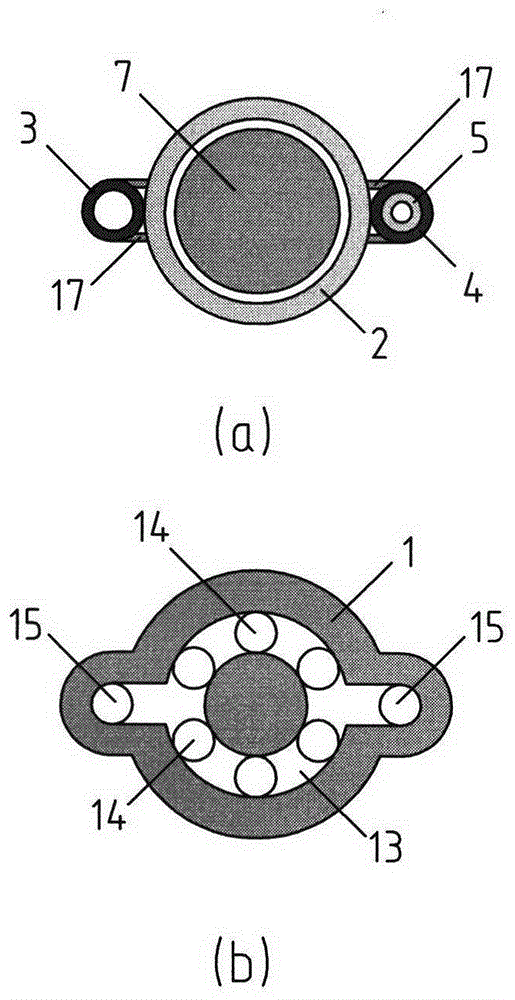
本发明涉及沉管压灌桩全过程施工使用的一种组合桩管及其使用方法,属于桩基础施工技术领域。
背景技术:申请号为201110172486.3、申请日为2011年6月24日、申请人为毕建东的中国发明专利:沉管灌注桩全过程施工方法及其专用装置(以下简称为:201110172486.3专利),提出了沉管压灌桩的概念,做法是:沉管到位后,上拔桩管的同时,通过灌注管泵送混凝土,插入钢筋笼后成桩;并给出了试桩、测桩的方法及其专用装置。201110172486.3专利所存在的问题或可优化的地方是:(1)泵送混凝土是用地面上的混凝土泵,通过输送管,包括向上的输送管,将混凝土输送到灌注管上口,路线较长,弯曲较多,容易造成堵管。在锤击的过程中,如不将输送管、灌注管断开,向上的输送管中的混凝土中的石子受振下沉堵管,处理麻烦,影响效率,浪费混凝土;如将输送管、灌注管断开,将造成反复断、接,亦很麻烦。最严重的问题是:因较难有效排气,不易保证混凝土质量——这是压灌桩的通病,桩承载力越高,这个问题越突出。(2)需要单独设置拔管装置,如用油缸静力拔管,或用振动装置振动拔管,因此,桩机构造较为复杂,成本相对较高;上拔桩管、同时泵送混凝土,难以保证拔管与泵送混凝土的速度匹配,控制难度较大,易造成断桩。(3)内锤直接打击桩管下板,冲击应力较高,贯入效率较低。
技术实现要素:为进一步降低沉管压灌桩成本、提高质量和效率,结合沉管压灌桩的特点,以201110172486.3专利为技术基础,本发明提供了沉管压灌桩全过程施工方法使用的一种组合桩管及其使用方法。1.组合桩管本发明提供的沉管压灌桩全过程施工方法使用的组合桩管为由沉管系统、混凝土压灌系统和端阻力检测系统组合而成的桩管。如图1、图2和图3所示,其构成如下:1.1主管2与动力总成6、容积约1m3的料斗9为同心且等外径的圆形,主管2在动力总成6下,容积约1m3的料斗9在动力总成6上,用螺纹连接或焊接成为整体;1.2主管2、动力总成6、料斗9外的一侧,通过连接板17与圆形的灌注管3焊接;另一侧通过连接板17与圆形的排气管4焊接;1.3下板1为外形略大于主管2与灌注管3、排气管4用连接板17焊好后的外形的柱形台体,两侧有与灌注管3、排气管4同心且等内径的圆孔15;1.4下板1上部有与主管2同心且等内径的凹入,凹入内有缓冲垫12;下部上有水平通道13,下有竖直通道14;1.5水平通道13的水平截面为与主管2同心的圆环形,并与圆孔15连通;水平通道13的竖直截面为圆形;1.6数量不少于两个的竖直通道14的水平截面为圆形,上与水平通道13连通,下通到下板1底面,沿水平通道13的环向均匀分布;1.7主管2、灌注管3、排气管4下端周边与下板1焊接;1.8灌注管3上端有排气阀10,排气管4上端有排气阀11;1.9排气管4内套有圆管形的压杆5;压杆5上端与排气阀11螺纹连接,下端插入下板1的圆孔15内;1.10动力总成6下端,通过钢丝绳8,与置于主管2内的、圆柱形的内锤7相连;动力总成6上端,通过穿过容积约1m3的料斗9侧壁的连接管16,与灌注管3相连;1.11动力总成6下可驱动内锤7,通过缓冲垫12,锤击下板1;上可振动料斗9内的混凝土,并通过连接管16,向灌注管3泵送混凝土。2.垫板用组合桩管进行全过程施工需用图4所示的垫板,其构成如下:2.1外形不小于下板1的薄钢板21;2.2薄钢板21底面焊有与下板1的圆孔15、竖直通道14同心、直径略大的圆形厚钢板22;2.3薄钢板21顶面焊有能套进下板1两侧圆孔15或竖直通道14内的、数量不少于两个且对称布置的圆形定位环23。3.试桩方法使用组合桩管试桩的具体步骤如下:3.1组合桩管对位压在桩点位置的垫板上;3.2用动力总成6,通过钢丝绳8,驱动内锤7,通过缓冲垫12,锤击下板1,组合桩管整体下沉,至预定的锤击贯入度后,停止锤击;3.3拧下排气阀11,下压压杆5,得到压杆5下的桩端阻力;3.4如果桩端阻力满足要求,结束;如果桩端阻力未达到要求,再锤击,达到新定锤击贯入度,再测桩端阻力,直到桩端阻力满足要求为止。4.做桩方法使用组合桩管做桩的具体步骤如下:4.1组合桩管对位压在桩点位置的垫板上;4.2用动力总成6,通过钢丝绳8,驱动内锤7,通过缓冲垫12,锤击下板1,组合桩管整体下沉,至试桩确定的锤击贯入度后,停止锤击;4.3用动力总成6,将容积约1m3的料斗9内的混凝土,通过连接管16、灌注管3,泵送到下板1下部,进而通过水平通道13,进入竖直通道14,同时用桩架上的起吊装置上吊组合桩管;随着泵送压力的加大,组合桩管顶起;期间,混凝土中的空气,通过排气阀10、排气阀11排出;4.4当有混凝土中的水泥浆从组合桩管外侧冒出时,降低压力继续泵送混凝土,至组合桩管底面出地面为止;4.5旁移组合桩管,让出桩位后,按已有方法将钢筋笼插入混凝土中,结束。5.测桩方法使用组合桩管测桩分桩端阻力检测和桩侧阻力检测,为成桩前检测。5.1桩端阻力检测的具体步骤如下:5.1.1组合桩管对位压在桩点位置的垫板上;5.1.2用动力总成6,通过钢丝绳8,驱动内锤7,通过缓冲垫12,锤击下板1,组合桩管整体下沉,至试桩确定的锤击贯入度后,停止锤击;5.1.3拧下排气阀11,下压压杆5,得到压杆5下的桩端阻力;5.1.4如果桩端阻力满足要求,合格;如果桩端阻力未达到要求,不合格。5.2桩侧阻力检测的具体步骤如下:5.2.1检测完桩端阻力后,用缓凝混凝土,按做桩方法将组合桩管顶起一定高度后,停止泵送混凝土;5.2.2整体下压组合桩管,得到桩侧阻力;5.2.3如果桩侧阻力满足要求,合格;接续进行泵送混凝土、插钢筋笼操作,成桩;5.2.4如果桩侧阻力未达到要求,不合格。从上述可看出组合桩管及垫板的如下特点:(1)动力总成6、内锤7、钢丝绳8、缓冲垫12、主管2和下板1组成了组合桩管的沉管系统。缓冲垫12可采用盘绕钢丝绳、碟簧或赛钢板(聚甲醛板)以及机油拌砂或土等。(2)动力总成6、灌注管3、排气管4、下板1以及容积约1m3的料斗9、排气阀10、排气阀11和连接管16组成了组合桩管的混凝土压灌系统;利用泵送混凝土的压力,该系统同时可完成顶管功能。(3)压杆5、排气管4组成了组合桩管的端阻力检测系统;端阻力检测是依照201110172486.3专利中的小面积法,用下压压杆5完成的;排气管4在此起到保证压杆5受压稳定的作用。(4)动力总成6具有驱动内锤7和振动、泵送混凝土的功能;其振动功能可排出容积约1m3的料斗9中的混凝土中的空气。(5)如果仅用灌注管3顶管,因其水平截面积较小,所需的混凝土泵送压力会相当大;下板1下部特殊设计的水平通道13和竖直通道14,目的是解决混凝土泵送压力问题,同时要保证下板1的抗锤击能力。(6)灌注管3、排气管4以及排气阀10、排气阀11,可排出最初泵送混凝土时,灌注管3中的空气,以及正常泵送混凝土期间,混凝土在容积约1m3的料斗9中未完全排出的空气。(7)垫板:垫板的作用:一是将下板1底面与土隔离,使下板1底面不粘土,保证混凝土质量;二是封堵下板1底面的竖直通道14和圆孔15,防止水、土进入。定位环23可固定垫板与下板1的相对位置。试桩、做桩或测桩后,垫板留在桩底。有益效果与201110172486.3专利相比,本发明提供的组合桩管,将沉管系统、混凝土压灌系统和端阻力检测系统有机组合在一起,顶管与混凝土灌注两项需求合二为一,完成包括试桩、做桩和测桩在内的沉管压灌桩的全过程施工,设备简单,控制容易,不易堵管,节省混凝土,利于保证混凝土质量、提高施工效率。本发明提供的组合桩管中设有缓冲垫,内锤锤击下板时,可降低组合桩管各部位应力,提高贯入效率。综上所述,本发明较201110172486.3专利,具有更好的技术、经济效益。附图说明图1是组合桩管构成示意图;图2是图1的横剖面示意图,其中:图a是内锤7部位横剖面示意图,图b是下板1的水平通道13部位横剖面示意图;图3是图1中的下板1轴测示意图,其中:图a是顶面下看轴测示意图;图b是底面上看轴测示意图;图4是垫板构成示意图,其中:图a是平面示意图,图b是剖面示意图。具体实施方式某建筑工程场地,自上而下的土层:2m厚杂填土,8m厚可塑状态粉质粘土,2m厚全风化泥岩,2m厚强风化泥岩,以下为中风化泥岩。设计桩径800mm,桩长16m,桩端持力层为中风化泥岩,单桩极限承载力2100t,其中:桩端极限阻力1700t,桩侧极限阻力400t。组合桩管基本数据:主管2外径800mm,壁厚30mm,高12m;灌注管3、排气管4、连接管16外径133mm,壁厚10mm;压杆5外径113mm,壁厚10mm;下板1周边大出主管2、灌注管3、排气管4焊好后的相应外形20mm,高度500mm,两侧圆孔15直径113mm;下板1上部凹入直径740mm,深度200mm;水平通道13水平向圆环形外径740mm,内径514mm;水平通道13竖向为圆形,直径113mm,中心距下板1底面150mm;六个竖直通道14沿水平通道13环向均匀分布,直径113mm;动力总成6外径800mm,高5m,总功率200kW,用液压方式驱动内锤7,最高频率每分钟50次,最低频率每分钟20次;动力总成6用液压方式泵送混凝土,最大压力25MPa,最大流量每小时100立方米;内锤7直径700mm,长6m,重18t;缓冲垫12为圆形赛钢板,直径720mm,厚150mm;容积约1m3的料斗9外径800mm,壁厚10mm,高2.5m。组合桩管总高度为20m。垫板基本数据:薄钢板21:厚3mm,周边较下板1周边大出10mm;厚钢板22:厚20mm,直径133mm;定位环23:外径103mm,内径83mm,高20mm。1.试桩:(1)组合桩管对位压在桩点位置的垫板上,开始锤击,最大落距2.0m;当最后10锤平均贯入度不大于10mm时,停止锤击,此时组合桩管入土深度约15.5m;(2)拧下排气阀11,下压压杆5,得到压杆5下的桩端阻力为55t,换算至全截面桩端极限阻力为1370t,未达到要求;(3)再锤击,当最后10锤平均贯入度不大于5mm时,停止锤击,此时组合桩管入土深度约16.5m;(4)再下压压杆5,得到压杆5下的桩端极限阻力为69t,换算至全截面桩端极限阻力为1720t,满足要求,试桩结束。2.做桩:(1)按试桩的步骤,达到预定的锤击贯入度——最后10锤平均贯入度不大于5mm,停止锤击,组合桩管入土深度在16~17m;(2)通过灌注管3,以最大20MPa的压力泵送C80混凝土,同时用桩架上的起吊装置上吊组合桩管;当组合桩管上移约8m时,组合桩管周边冒浆;(3)降低压力继续泵送混凝土,至组合桩管底面出地面为止;(4)旁移组合桩管,让出桩位后,按已有方法将钢筋笼插入混凝土中,结束。3.测桩:(1)按试桩方法的步骤,达到预定的锤击贯入度,停止锤击;(2)检测桩端阻力:下压压杆5,得出压杆5下的桩端极限阻力为70t,换算至全截面桩端极限阻力为1750t,满足要求;(3)检测桩侧阻力:通过灌注管3,以最大20MPa的压力泵送C80缓凝混凝土;当组合桩管上顶约100mm时,暂停泵送混凝土;然后,整体下压组合桩管,检测桩侧极限阻力为410t,满足要求;(4)接续进行泵送混凝土、插钢筋笼等步骤的操作,成桩。