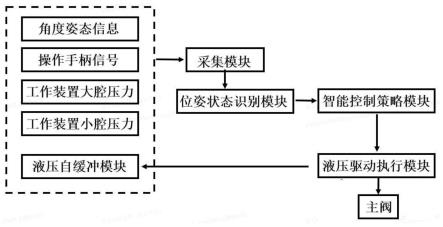
1.本发明涉及一种液压柔性自缓冲智能控制系统及挖掘机,属于挖掘机电液控制领域。
背景技术:2.挖掘机主要用于矿山开采,进行矿产资源的开挖回填等工作,具有工作循环时间短,强度大等特点。挖掘机由动臂、斗杆和铲斗协同工作,完成挖掘动作,因而不可避免的反复出现启动停止动作。传统的挖掘机依靠液压油缸的机械缓冲来实现,但是不能较好的解决冲击问题,工作装置的冲击会传递至整机,造成操作舒适性差,操作难度高,结构件使用寿命短等问题。通过延长液压主阀的关闭周期,可以实现降低冲击的效果,但同时会造成动作存在延迟的问题,降低操作舒适感。
技术实现要素:3.针对上述现有技术存在的问题,本发明提供一种液压柔性自缓冲智能控制系统及挖掘机,解决现有工作装置停止时的整机冲击问题,确保挖掘机操作的柔顺性及平稳性,延长结构件的使用寿命,提升可靠性。
4.为了实现上述目的,本发明采用的一种液压柔性自缓冲智能控制系统,包括:
5.采集模块,其用于采集挖掘机角度姿态信号、工作装置的油缸大腔小腔压力信号、操作手柄信号、液压自缓冲模块压力信号,并将采集到的各信息传输至位姿状态识别模块;
6.位姿状态识别模块,其用于识别出挖掘机当前的位姿状态,结合挖掘机操作手柄信号,依据姿态库,计算所需解决的冲击系数,同时结合挖掘机工作装置的油缸大腔、小腔的压力信号,修正所需解决的冲击系数,并传递至智能控制策略模块;
7.智能控制策略模块,其用于依据冲击系数,计算液压自缓冲模块中比例阀控制电流,同时修正主阀控制策略;
8.液压驱动执行模块,其用于控制挖掘机主阀及液压自缓冲模块。
9.作为改进,所述的角度姿态信号包括工作装置动臂、斗杆及铲斗的角度信息。
10.作为改进,所述的液压自缓冲模块,通过在工作装置的动臂、斗杆及铲斗的大腔小腔之间,安装具有电磁比例阀的连通装置,实现大腔小腔液压油的比例双向连通。
11.作为改进,所述冲击系数用于衡量挖掘机当前状态下,驱动液压自缓冲模块电流的大小。
12.作为改进,所述的采集模块能同步采集挖掘机角度、压力及can信号,且采集数据采用智能算法进行处理。
13.作为进一步的改进,所述智能算法包括算术平均法、模糊控制算法、神经网络算法、蚁群算法或卡尔曼滤波器方法中的一种或者几种。
14.作为改进,所述操作手柄信号包括动臂上升、动臂下降、斗杆外摆、斗杆内收、铲斗外摆及铲斗内收信号,取值在0-1000。
15.作为改进,所述液压自缓冲模块压力信号包括动臂阀前、动臂阀后、斗杆阀前、斗杆阀后、铲斗阀前及铲斗阀后的压力信号,取值在0-50mpa。
16.作为改进,当液压自缓冲模块的阀前和阀后压力相等后,切断液压自缓冲模块,同时减慢阀芯关闭速度。
17.另外,本发明还提供了一种挖掘机,所述挖掘机上安装有所述的液压柔性自缓冲智能控制系统。
18.与现有技术相比,本发明的液压柔性自缓冲智能控制系统,在满足挖掘机高效作业的前提下,降低工作停止冲击,保证挖掘机操作的柔顺性及平稳性,降低了操作难度,延长了结构件的使用寿命,提升了挖掘机的可靠性及智能化水平。
附图说明
19.图1是本发明的控制流程图;
20.图2是本发明的液压自缓冲模块原理图;
21.图3是本发明的位姿计算示意图;
22.图4是本发明的液压自缓冲模块的控制策略图。
具体实施方式
23.为使本发明的目的、技术方案和优点更加清楚明了,下面对本发明进行进一步详细说明。但是应该理解,此处所描述的具体实施例仅仅用以解释本发明,并不用于限制本发明的范围。
24.除非另有定义,本文所使用的所有的技术术语和科学术语与属于本发明的技术领域的技术人员通常理解的含义相同,本文中在本发明的说明书中所使用的术语只是为了描述具体的实施例的目的,不是旨在于限制本发明。
25.如图1所示,一种液压柔性自缓冲智能控制系统,包括:
26.采集模块,用于采集挖掘机角度姿态信号,工作装置的油缸大腔、小腔压力信号,操作手柄信号,及液压自缓冲模块压力信号,并将采集信息传输至位姿状态识别模块;
27.位姿状态识别模块,用于识别出挖掘机当前的位姿状态,结合挖掘机操作手柄信号,依据姿态库,计算所需解决的冲击系数,同时结合挖掘机工作装置的油缸大腔、小腔的压力信号,修正所需解决的冲击系数,并传递至智能控制策略模块;
28.智能控制策略模块,用于依据冲击系数,计算液压自缓冲模块中比例阀控制电流,同时修正主阀控制策略;
29.液压驱动执行模块,用于控制挖掘机主阀及液压自缓冲模块。
30.作为实施例的改进,如图2所示,所述液压自缓冲模块,通过在工作装置的动臂、斗杆及铲斗的大腔a和小腔b之间,安装包括连通管路及电磁比例阀的连通装置c,控制系统可以改变驱动电流的大小,实现管路的通断和连接大小,降低高压腔压力。该连通装置c不具备单向阀或单向节流装置,不具备油箱回油功能。
31.作为实施例的改进,如图1所示,采集模块主要采集操作手柄信号、工作装置大腔信号、工作装置小腔信号、液压自缓冲模块压力及角度姿态信号;
32.操作手柄信号主要包括动臂上升、动臂下降、斗杆外摆、斗杆内收、铲斗外摆及铲
斗内收等六个动作的行程can信号,取值在0-1000;
33.工作装置大腔、小腔信号主要为动臂大腔、动臂小腔、斗杆大腔、斗杆小腔、铲斗大腔及铲斗小腔等六个压力信号的模拟量信号,取值在0-50mpa;
34.液压自缓冲模块的压力信号主要为动臂阀前、动臂阀后、斗杆阀前、斗杆阀后、铲斗阀前及铲斗阀后等六个压力信号的模拟量信号,取值在0-50mpa;
35.角度姿态信号主要包括动臂、斗杆和铲斗的角度信息。
36.作为实施例的改进,采集模块用于对挖掘机的操作手柄信号、工作装置大腔信号、工作装置小腔信号、液压自缓冲模块压力及角度姿态信号进行滤波处理,去除干扰数据,滤波办法主要采用算数平均值滤波,滑动平均值滤波和卡尔曼滤波器等。
37.作为实施例的改进,所述的位姿状态识别模块,以铲斗齿尖末端位置为例,依据动臂、斗杆和铲斗的角度信息为基础,推导变换矩阵,获得工作装置运动学模型,计算铲斗齿尖末端的位置和姿态矩阵。
38.如图3所示,动臂与地面夹角θ1,斗杆与地面夹角θ2,铲斗与地面的夹角为θ3,坐标原点至动臂根部铰点距离为α0,动臂铰点间距离为α1,斗杆铰点间距离为α2,铲斗铰点间距离为α3;
39.由各个倾角传感器1测量的倾角值推导关节角:
[0040][0041]
其中动臂转角为斗杆转角为铲斗转角为
[0042]
进而构建工作装置运动学方程:
[0043][0044]
进而推算齿尖末端位置:
[0045][0046]
其中,x为铲斗斗齿x坐标值,y为铲斗斗齿y坐标值,z为铲斗斗齿z坐标值,ξ为铲斗姿态。
[0047]
进一步的,依据工作装置各关节的位姿,结合手柄动作信息,查表姿态库,计算所需解决的初始冲击系数δ1,姿态库依据工作装置的重力,分解至油缸的作用力,计算初始冲击系数。
[0048]
如表1所示,动臂在各角度下的初始冲击系数:
[0049]
表1动臂的初始冲击系数
[0050][0051]
同时,结合挖掘机工作装置的油缸大腔、小腔压力信号对初始冲击系数δ1进行修正,得到冲击系数δ。
[0052]
其修正方法如公式4):
[0053]
δ=δ1*(p
b-ps)/p
max
公式4);
[0054]
其中,pb为大腔压力,ps为小腔压力,p
max
p为液压系统溢流压力。
[0055]
进一步的,位姿状态识别模块将计算所得冲击系数δ传递至智能控制策略模块,其中δ取值范围为0~100%。
[0056]
智能控制策略模块依据冲击系数,设定液压自缓冲模块驱动电流,其电流值i如公式5):
[0057]
i=if+δ*(i
max-if)公式5);
[0058]
其中if为自缓冲模块启动电流,i
max
为自缓冲模块最大电流。
[0059]
进一步的,智能控制策略模块依据驱动电流,设定加载方式,具体加载时间由实验确定,实现大腔小腔缓慢连通,同时改变主阀控制策略,加快阀芯关闭速度。
[0060]
当液压自缓冲模块的阀前和阀后压力相等后,切断液压自缓冲模块,同时减慢阀芯关闭速度,恢复正常的主阀控制策略。控制策略如图4所示。
[0061]
智能控制策略模块通过液压驱动执行模块,实现对液压自缓冲模块和主阀的控制。
[0062]
以上所述仅是本发明的优选实施方式,应当指出:对于本技术领域的普通技术人员来说,在不脱离本发明原理的前提下,还可以做出若干改进和润饰,这些改进和润饰也应视为本发明的保护范围。