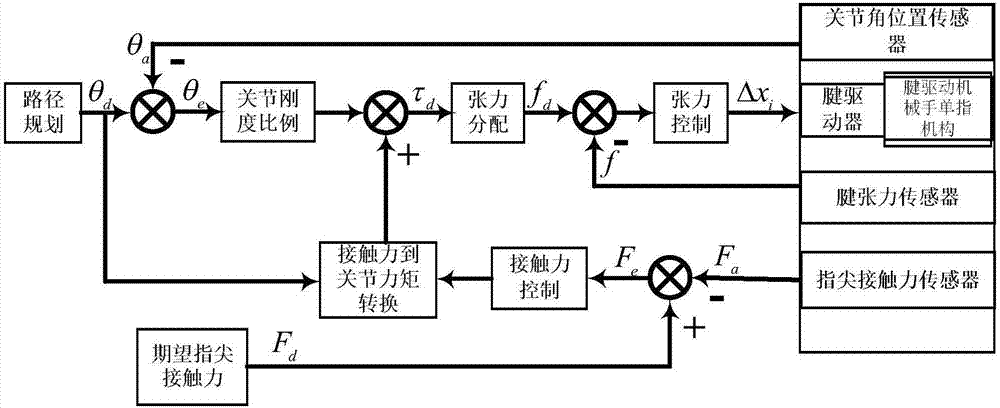
本发明涉及机器人控制技术,尤其是一种腱驱动机械手的操作控制方法和装置,特别是基于腱张力约束下腱驱动型多关节机械手、机械臂等操作机构的控制方法。
背景技术:
:机械手为模仿手/臂特定功能的一种自动机械,因此泛指机械臂、末端执行器、灵巧手手指等多关节多连杆操作机构。腱驱动型机械手是利用腱绳进行传动的机械手,允许驱动器放置于机械手结构体的外部,可以减小机械手体积和重量,从而提高了机械手的灵巧性,同时也在驱动器选型方面给机构设计者提供了更多灵活性。由于腱只可以传递张力,因此为了获得完全独立的自由度控制,必须要保证驱动器的数量多于自由度的个数。有多种腱配置方式,在配置合理的情况下,n+1型腱能够独立控制n个自由度,同时保证腱具有正张力。该腱配置方式简化了机构,但由于这种方式在减少腱绳数量的同时引入了关节位置和腱绳的耦合问题,因此控制器的设计非常复杂。在装配应用中机械手需要与非结构环境物理接触,因此机械手的力矩控制能力非常重要。研究者们提出多种控制策略来解决耦合腱驱动机械手的力矩控制问题。这些控制策略由张力分配算法和控制律两部分组成。张力分配算法是确定一组腱张力的过程,目的是产生期望的一组关节力矩,同时解决驱动的冗余问题。该冗余可以生成张力的零空间,用来保证所有腱具有正张力。目前已有的控制律根据是否使用腱张力反馈进行分类。无腱张力反馈的控制方法包括计算力矩法、其它能够预测或估计系统参数的智能方法,这些方法对于能够精确建模运动和力矩关系的系统是可行的,但机械手需要抓握或操作的是各种可能的物体,其接触表面特性差别很大,因此这些方法只能获得粗略的腱张力控制,经常产生更高的内张力,导致腱的磨损,增加摩擦力降低性能,因此这些方法难以实现精确的操作。采用张力反馈的腱空间控制器忽略腱的动力学,利用张力分配算法将期望的关节力矩转换为期望的腱张力,然后为每根腱使用独立的张力调节器。然而采用该种方式的控制器在手指动力学中引入了瞬态耦合,即某个关节的控制或扰动可能导致另一个关节的不期望的响应。总之,相对于传统的齿轮传动,腱驱动机械手的设计难点在于设计合适的控制器使其能够按照期望的轨迹运动及期望的接触力抓取物体同时保证腱的张力保持在期望的范围之内。腱只能传递张力,而且有一定的延迟,此外,机构对腱的摩擦以及腱的其它未建模动力学等因素也都影响着腱驱动机械手操作控制算法的设计。现有的控制算法,仍不能完全满足腱驱动机械手有效控制接触力和接触位置同时保持腱张力处于合适的约束范围的要求。技术实现要素:发明目的:本发明的目的:针对腱驱动机械手,提供一种力和位置控制方法和设备,该方法能够提高系统末端操作的位置和力控制性能,减小从自由空间到约束空间的冲击;同时通过约束腱张力,降低腱的磨损,提高其寿命,最终该方法能够有效的实现腱驱动机械手的操作控制,提高机械手的操作灵巧性和寿命。本发明采用的技术方案:一种腱驱动机械手腱张力约束接触力位操作控制方法和装置,实现方法包括有如下步骤:步骤1,由路径规划模块进行机械手单指自由空间中的关节角位置路径规划;由操作对象特性及其相对位置规划灵巧手单指运动期望的接触力;并且设定腱张力约束范围和接触力阈值;步骤2,由接触力传感器测量得到的接触力值与接触力阈值比较确定灵巧手和物体之间的接触状态,若接触力值小于接触力阈值说明机械手位于自由空间,设置输出接触力偏差fe为0;否则由比较器比较期望指尖接触力和实际指尖接触力传感器所测接触力之间的差别得到约束空间接触力偏差fe。接触力控制模块根据偏差计算控制量,然后接触力到关节力矩转换模块根据当前期望关节角位置将其转换为关节力矩;期望的关节角位置θd与手指的实际关节角位置θa进行比较得到关节角位置误差θe=θd-θa。然后通过关节刚度比例模块将关节角位置误差转化为关节力矩。两个关节力矩求和,其结果进一步由张力分配模块计算得到期望腱张力。然后由比较器比较期望腱张力和实际腱张力的差别,根据这个偏差由张力控制模块基于合适的控制律把张力的偏差转化为位置的偏差,输入到腱驱动器进行控制。步骤1所述的机械手自由空间中的关节角位置路径规划可采用一般多关节机械臂的关节角位置路径规划方法进行,如抛物线过渡的线性插值方法等,得到期望的关节角轨迹,由路径规划模块实现。步骤1中所述的接触力阈值由接触力传感器的噪声特性确定,高于该阈值说明接触物体。步骤2中所述为两种情况,接触力值小于接触力阈值情况下,设置输出接触力偏差fe为0;大于接触力阈值情况下,输出接触力偏差fe为实际接触力传感器测量值和期望的接触力值之间的差。步骤2中关节角位置偏差通过关节刚度比例模块,接触力偏差通过接触力控制模块、接触力到关节力矩转换模块转换为关节力矩后求和,并且通过能够实现张力约束的张力分配算法转化为腱张力期望值。接触力控制模块可由通常的控制算法实现,接触力到关节力矩转换模块由正运动学计算的雅克比矩阵实现。步骤2中张力分配模块将两关节力矩求和值转换为腱空间的力,具体考虑了腱张力约束,保证腱张力处于一个根据实际需求设定的最小和最大正值之间。最小值保证腱绳处于张紧状态,最大值由实际中采用腱绳的材质的张力限制决定,保护腱绳不被拉断和减小磨损。步骤2中张力控制模块将腱张力转换为位置偏差,输入到腱驱动器,拉动腱绳实现期望运动,具体可以由通用的控制算法实现。腱驱动机械手系统主要由控制器、腱驱动器、腱张力传感器、腱绳、腱驱动机械手机构、指尖接触力传感器、对应各关节的关节角位置传感器组成。关节角位置传感器固定在腱驱动机械手机构的各个关节上,指尖接触力传感器位于指尖。其中控制器包括前述步骤所述的包括路径规划模块、关节刚度比例模块、张力分配模块、接触力到关节力矩转换模块、接触力控制模块、张力控制模块。控制器接收来自关节角位置传感器、腱张力传感器、指尖接触力传感器的信息,然后控制各模块按照前面所提步骤运行,通过操作处理把张力控制模块的输出作为腱位置偏差输入到腱驱动器。腱驱动器包括无刷直流电机和把旋转运动转换为直线运动的滚珠丝杠、螺母等组件,根据输入的位置偏差驱动腱绳拉伸,驱动机械手单指机构相应运动,实现所需的位置和力的调整。在进一步的实施例中,一种腱驱动机械手腱张力约束末端力位操作控制方法,包括如下步骤:步骤1,规划机械手单指自由空间中的关节角位置路径,规划灵巧手单指运动期望的接触力;设定腱张力约束范围和接触力阈值;步骤2,测量接触力值并将其与接触力阈值比较,以确定灵巧手和物体之间的接触状态;若接触力值小于接触力阈值,则机械手位于自由空间,设置输出接触力偏差fe为0;否则,比较期望指尖接触力和实际指尖接触力传感器所测接触力之间的差别得到约束空间接触力偏差fe;根据偏差计算控制量并结合当前期望关节角位置将其转换为关节力矩;期望的关节角位置θd与手指的实际关节角位置θa进行比较得到关节角位置误差θe=θr-θd;将所述关节角位置误差转化为关节力矩;两个关节力矩求和,其结果进一步计算得到期望腱张力;比较期望腱张力和实际腱张力的偏差,根据这个偏差并基于合适的控制律把张力的偏差转化为位置的偏差,输入到腱驱动器进行控制。进一步的,提供一种腱驱动机械手单指系统,包括:控制器,路径规划模块、关节刚度比例模块、张力分配模块、接触力到关节力矩转换模块、接触力控制模块和张力控制模块;腱驱动器,包括无刷直流电机和把旋转运动转换为直线运动的滚珠丝杠组件,根据输入的位置偏差驱动腱绳拉伸,驱动机械手单指机构相应运动,实现所需的位置和力的调整;腱张力传感器,安装在键上,腱的一端连接在相应指节上,另一端连接在腱驱动器上;腱绳,腱驱动机械手单指机构,包括基座、近指节、中指节和远指节;采用n+1型腱驱动方式,具有3个独立自由度,其中远指节通过一个连杆机构与中指节耦合,以实现绕侧摆关节、基关节和中关节的旋转运动;指尖接触力传感器,固定在远指节上;关节角位置传感器,固定在腱驱动单指机构的各个关节上;腱张力传感器、关节角位置传感器和指尖接触力传感器采集的信息发送给控制器,控制器发送控制指令给腱驱动器。本发明的有益效果:本发明设计了一种满足腱张力约束的腱驱动机械手末端操作控制方法,该方法能够根据规划的接触力实现稳定的抓取,提高系统末端操作的位置和力控制性能,并且一定程度上减轻机械手接触物体时的冲击;通过约束腱张力,降低腱的磨损,提高系统的寿命。该方法可进一步应用于以腱为传动方式的多关节机械臂、灵巧手单指等多关节多连杆机构中,因此该实现方法具有广阔的应用前景。附图说明图1是腱驱动型机械手单指系统组成图。图2是腱驱动机械手单指腱张力约束笛卡尔空间阻抗控制框图。图3是单指坐标系示意图。其中,各附图标记如下:1,控制器;2,腱驱动器;3,腱绳;4,腱张力传感器;5,腱驱动机械手单指机构;6,关节角位置传感器;7,指尖接触力传感器;11,侧摆关节;12基关节;13,中关节;14,连杆;15,基座;16,近指节;17,中指节;18,远指节。具体实施方式在机械手泛指机械臂、末端执行器、灵巧手手指等多关节多连杆操作机构,这儿主要采用了基于腱驱动的灵巧手单手指的柔顺控制为例结合附图说明腱驱动机械手力和位置控制方法的具体实施方法。但并不因此将本发明限制在实施范围之内。如图1所示,腱驱动机械手单指系统主要由控制器1、腱驱动器2、腱张力传感器4、腱绳3、腱驱动机械手单指机构5、指尖接触力传感器7、对应各关节的关节角位置传感器6组成。腱驱动机械手单指机构由基座15、近指节16、中指节17和远指节18组成,采用“n+1”型腱驱动方式,具有3个独立自由度,其中远指节通过一个连杆14机构与中指节耦合,主要实现绕侧摆关节11、基关节12和中关节13的旋转运动。关节角位置传感器6固定在腱驱动单指机构的各个关节上。每一根腱上都装有腱张力传感器4,腱的一端连接在相应指节上,另一端连接在腱驱动器2上。指尖接触力传感器7固定在远指节18上,腱张力传感器4、关节角位置传感器6和指尖接触力传感器7采集的信息发送给控制器,控制器发送控制指令给腱驱动器。如图1所示,腱驱动单指机械手系统的控制器1包括路径规划模块、关节刚度比例模块、张力分配模块、接触力到关节力矩转换模块、接触力控制模块、张力控制模块。控制器接收来自关节角位置传感器、腱张力传感器、指尖接触力传感器的信息,然后控制各模块按照前面所提步骤运行,通过操作处理把张力控制模块的输出作为腱位置偏差输入到腱驱动器。腱驱动器包括无刷直流电机和把旋转运动转换为直线运动的滚珠丝杠、螺母等组件,根据输入的位置偏差驱动腱绳拉伸,驱动机械手单指机构相应运动,实现所需的位置和力的调整。图2控制器中路径规划模块根据手指指尖当前位置和物体的期望接触点确定从初始点到接触点的期望关节角位置θd;关节刚度比例模块将关节角位置误差转化为关节力矩;接触力到关节力矩转换模块通过力雅可比矩阵把规划的接触力转换为关节力矩;张力分配模块将前述两个模块输出求和后的关节力矩转换为腱空间的力。腱张力比较器比较期望腱张力和实际腱张力的差别,根据这个偏差张力控制模块计算位置偏差对机械手单手指的腱位置进行修正,输出量δxi作为腱端的速度输入到腱驱动器中。腱驱动器有4个输入端为位置控制器输出的腱端速度量v;控制器的输入量为4个关节角位置传感器给出的角位移量θa、腱张力传感器张力值f、指尖接触力传感器三维力输入。对于当前的腱驱动机械手单指系统,变量θd、θa、θe、f、fd、δx都是四维的列向量,τd为三维的列向量。因为腱只能传递张力,因此单独的位置控制很难保证腱张力时刻大于0,而且腱本身有一定的柔韧性,对力的传递有迟滞性。控制器在初始时刻时,给腱绳施加力fi≥fmin保证腱在初始时刻具有预张紧。具体地,控制器各模块按照如下具体步骤运行。步骤1,由路径规划模块进行机械手单指自由空间中的关节角位置路径规划;输入由操作对象特性规划得到灵巧手单指运动期望的接触力;并且设定腱张力约束范围和接触力阈值。步骤2,根据接触力传感器测量得到的接触力值与接触力阈值比较确定灵巧手和物体之间的接触状态,若接触力值小于接触力阈值说明机械手位于自由空间,设置输出接触力偏差fe为0;否则由比较器比较期望指尖接触力和实际指尖接触力传感器所测接触力之间的差别得到约束空间接触力偏差fe。接触力控制模块根据偏差计算控制量,然后接触力到关节力矩转换模块将其转化为当前期望关节角位置下的关节力矩;期望的关节角位置θd与手指的实际关节角位置θa进行比较得到关节角位置误差θe=θd-θa。然后通过关节刚度比例模块将关节角位置误差转化为关节力矩。两个关节力矩求和,进一步由张力分配模块计算得到期望腱张力。然后由比较器比较期望腱张力和实际腱张力的差别,根据这个偏差由张力控制模块基于合适的控制律把张力的偏差转化为位置的偏差,输入到腱驱动器进行控制。控制器各模块的具体实现如下:1)路径规划模块机械手手指运动路径规划是指根据手指指尖当前位置和物体的期望接触点确定从初始点到接触点的运动轨迹。目前路径规划主要分为:笛卡尔空间的路径规划和关节空间的路径规划。对于多关节的手指,指尖的笛卡尔空间运动轨迹很难用时间的变量表示,并且计算比较复杂。相比而言,在关节空间,除了耦合关节外,其他的关节的角位移都是相对独立的,可以分别进行路径规划,规划的方程相对简单而且计算量小、实时性好,所以这里采用了关节空间的路径规划。机械手自由空间中的关节角位置路径规划可采用一般多关节机械臂的关节角位置路径规划类似的方法进行,如抛物线过渡的线性插值方法、三次多项式路径规划等等。本实施方案采用抛物线过渡的线性插值方法,该方法具有运动特性好,易于实现等优点。规划的方程为:式中θd0是关节的初始角位移,θdf是关节最后到达的期望角位移,tf是到达期望位置的时间,a是加速度。在实际中,先估计环境的笛卡尔位置,然后通过逆运运学解出各关节所要到达的角位移,最后根据式(1)对手指各关节进行路径规划。2)接触力到关节力矩转换模块根据操作物体特性及相对指尖位置,由指尖接触力fc,可通过雅克比矩阵j计算出使手指指尖在接触到物体并保持静态平衡时所需的关节力矩τd1:τd1=jtfc(2)雅可比矩阵反映了关节空间速度到指尖笛卡尔空间速度的映射关系,同时也反映了指尖接触力到关节力矩的映射关系[41]。在正向运动学的基础上,我们可以求取手指的雅可比矩阵。正向运动学是根据关节角求手指末端在基座坐标系下的位置和姿态。由d-h参数描述,建立单指坐标系如图3所示,zi轴沿关节i的运动轴方向;xi轴沿着zi轴和zi+1轴的公法线,指向下一个关节;yi轴由xi轴和zi轴按照右手直角坐标系法则来确定。为了简化模型,基座坐标系o0x0y0z0和基关节坐标系o1x1y1z1方向一致,指尖坐标系otxtytzt和顶关节坐标系o4x4y4z4方向一致。按照建立的单指坐标系和各个指节的长度,单指的d-h参数如表1所示。表1全驱动手指单指d-h参数关节ai-1αi-1diθi1l000θ12l1900θ23l200θ34l300θ4tl4000其中l0、l1、l2、l3、l4为固定的手指指节长度,其值为:l0=21mm、l1=9mm、l2=45mm、l3=30mm、l4=21mm。θ1、θ2、θ3、θ4为可变的关节角:侧摆关节角、基关节角、中关节角和远关节角。根据d-h参数可得单指6个坐标系之间的变换矩阵为:确定了单指6个坐标系中相邻坐标系之间的齐次坐标变换矩阵后,即可求得指尖坐标系otxtytzt相对于基座坐标系o0x0y0z0的位置和姿态为:其中cosθ23代表cos(θ2+θ3),cosθ234代表cos(θ2+θ3+θ4)。根据齐次变换矩阵的定义可知矩阵的第四列的前三行即为指尖末端在基座坐标系o0x0y0z0中的笛卡尔坐标:这样由已知的手指关节角θ1、θ2、θ3、θ4即可得到指尖末端在基座坐标系o0x0y0z0中的笛卡尔位置。对xt、yt、zt求θ1、θ2、θ3、θ4的偏导数即可得到雅可比矩阵j:3)接触力控制模块接触力控制模块主要是通过设计合适的控制器以满足待定的性能要求。控制器可以采用不同的控制算法(如滑模变结构、pid、神经网络、模糊以及它们的组合算法等)构建。其中,pid控制具有原理简单、易于实现,鲁棒性强和适应范围广等特点,是一种应用广泛的控制规律。本实施方案采用了一个pid控制器:式中,fe=fd-fa,kp1为比例环节系数,ki1为积分环节系数,kd1为微分环节系数,d/dt微分算子。前述控制算法滑模变结构、神经网络、模糊以及它们的组合算法等也可实现类似的控制功能。4)关节刚度比例模块关节角位置误差转化为期望的关节力矩τd,采用刚度控制器:τd1=k(θd-θa)(6)其中k为对角型刚度矩阵。5)腱张力分配模块由于腱只传递张力,为了避免腱在运动过程中出现松弛,引入腱张力控制器确保腱张力的正定性。腱张力控制器算法的基础是n个关节力矩τ和n+1个腱张力f之间的关系:其中t表示腱的内部张力;r∈r3*3是由三个独立关节的半径组成的对角阵;b表示腱的结构矩阵;wt正交于rb的行空间且正定。系统中腱张力可控的充要条件为p可逆,要求rb行满秩。由式(7)可以得到:令p-1=[aa]设定腱张力取值范围[fminfmax],fmin保证腱始终处于绷紧的状态,fmax保护腱不超负荷。令ai和ai分别代表a的行向量和a的列向量。腱张力分配算法的步骤如下。a)首先根据fmin确定t的取值,则有:fi=aiτ+ait≥fmin(10)b)其次将内部张力值t代入张力分配等式(9);c)令fl为张力中最小的元素,fh为张力中的最大元素;d)确定是否张力f1,...,fn超过上界fmax,如果fh≤fmax,表明没有超界,给各根腱分配张力f1,...,fn+1并结束分配过程。e)如果出现fh>fmax,则采用比例缩放的方式构造一个新的方程:由前述过程中得到的fl和fh及其对应位置处相关参量计算得到式(11)中参量:d=(ahal-alah)τf)令fl为利用(12)式所计算出的张力最小的元素,fh为其中的张力最大元素,g)若如果fh≤fmax,并且fl>fmin,给各根腱分配张力f1,...,fn+1,并结束分配过程;否则,重新进行e)、f)、g)过程,直到满足要求为止。6)张力控制模块通过设计合适的控制器以满足待定的张力控制精度要求。如上所述,控制器可以采用不同的控制算法构建。其中,pid控制具有原理简单、易于实现,鲁棒性强和适应范围广等特点。本实施方案采用了一个pd控制器,如下:式中,kp2为比例环节系数,fd为期望腱张力,f为腱张力传感器测量所得到的实际腱张力,kd2为微分环节系数,d/dt为微分算子。由机构参数可以确定相应的映射矩阵;根据具体的性能指标要求,可以确定相应的控制器参数。下面是具体实施实例的一组相关参数设置。根据如图2中所示腱的排列可以得出结构矩阵b,进而得到腱映射矩阵p,如下:同时根据任务要求及腱的特性设置腱张力范围fmin=8n,fmax=200n。具体腱驱动机械手系统的控制器采用了通用pc、数据采集卡结合电机驱动器来实现,另外以嵌入式处理器、dsp等为运算核心结合信号调理和电机驱动的控制器结构形式也是可行的。根据上述结构参数,进行张力控制器的pd参数和接触力控制pid参数调节。采用该方法所实现系统获得了良好的性能,该方法能够提高系统末端操作力控制精度,减小从自由空间到约束空间的冲击;同时通过约束腱张力,降低腱的磨损,提高其寿命,最终能够有效的实现腱驱动机械手的操作控制,提高机械手的操作灵巧性和寿命。该方法可进一步应用于以腱为传动方式的多关节操作臂、末端执行器等机构中,因此该实现方法和装置具有广阔的应用前景。需要说明的是,在上述具体实施方式中所描述的各个具体技术特征,在不矛盾的情况下,可以通过任何合适的方式进行组合。为了避免不必要的重复,本发明对各种可能的组合方式不再另行说明。当前第1页12