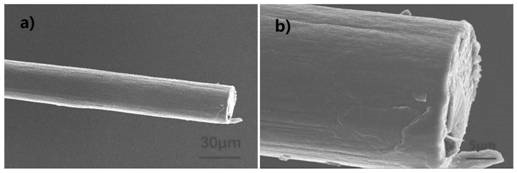
本发明涉及动物蛋白再生纤维
技术领域:
,更具体地,涉及一种角蛋白纺丝原液及其制备的角蛋白再生纤维。
背景技术:
:随着环境污染的加剧和自然资源的消耗,将废弃物回收并制备成再生材料得到了日益广泛的重视。羊毛作为一种高端的纺织品原料,穿着舒适性、保温性和透气性良好。然而,在洗毛、梳理、精梳和纺纱等纺织加工过程,每年会产生数以千吨的废弃羊毛。另外,羊肉生产过程中也会产生大量短而粗的废弃羊毛,只能作为垃圾被填埋或焚烧。在自然资源紧缺、合成纤维无法满足日益增长的高档动物纤维纺织品需求的背景下,回收废弃羊毛并将其开发成可作为纺织品应用的再生动物蛋白纤维,必将产生巨大的经济效益和环境效益。传统溶解羊毛的方法往往需要采用浓度高达42%~50%的尿素或溴化锂等溶剂,以破坏羊毛角蛋白分子间大量存在的氢键,同时调节溶液的ph值为碱性,并加入少量的十二烷基硫酸钠与角蛋白形成胶束以制备稳定的溶液。该方法制备的溶液中角蛋白浓度比较低(一般只有5%),无法满足直接纺丝的需求。如果提高浓度,角蛋白难以充分溶解,影响再生纤维的力学性能。为了制备满足纺丝要求的高浓度角蛋白纺丝液,一般羊毛溶解后还需要分离去除溶液中不溶解的羊毛残渣,然后通过透析或者调节等电点等方法除去尿素或溴化锂等小分子,以上两步纯化工艺都会导致角蛋白的损失,最高只能回收约70%的角蛋白。提纯的角蛋白还需再溶解成纺丝液,才能进行下一步的纺丝工艺。可见,现有技术通过回收羊毛制备的角蛋白纺丝原液方法复杂,需要经过溶解、提纯、再溶解等过程,原料损失严重。而且,通过纺丝得到的角蛋白再生纤维力学性能较差,无法同时满足强度和韧性的要求。例如,中国专利申请cn103205861a公开了一种羊毛角蛋白纺丝液,采用采用硫化钠/尿素/十二烷基硫酸钠方法溶解羊毛,其制备角蛋白纺丝原液的方法较为复杂,而且纺丝得到的角蛋白再生纤维力学性能较差。因此,需要开发出制备方法较为简单、有利于提高角蛋白再生纤维力学性能的角蛋白纺丝原液。技术实现要素:本发明为克服上述现有技术所述的制备方法复杂、纺丝得到的角蛋白再生纤维力学性能较差的缺陷,提供一种角蛋白纺丝原液,提供的角蛋白纺丝原液制备方法较为简单,能够直接制备出高浓度和粘度的纺丝原液,直接应用于湿法纺丝,而且能够减少角蛋白主链的破坏,不含尿素或溴化锂,有利于提高制得的角蛋白再生纤维力学性能,获得良好的强度和韧性。本发明的另一目的在于提供一种角蛋白再生纤维。为解决上述技术问题,本发明采用的技术方案是:一种角蛋白纺丝原液,由如下重量份数的原料在水中反应制备得到:所述蛋白质变性剂为十二烷基苯磺酸钠、十六烷基硫酸钠或十二烷基硫酸钠中的一种或几种。所述羊毛可以为废弃羊毛。发明人研究发现,现有技术采用尿素或溴化锂来溶解羊毛时,需要在高温条件下进行,碱性环境、高浓度的尿素和溴化锂都会在一定程度上破坏角蛋白主链,降低角蛋白分子量。角蛋白分子量降低,使得纺丝得到的角蛋白再生纤维力学性能较差,无法同时满足强度和韧性的要求。发明人研究进一步研究发现,在不使用尿素或溴化锂等试剂破坏氢键的情况下,仅仅通过适当提高十二烷基硫酸钠等表面活性剂的用量,用作蛋白质变性剂,配合还原剂,即可充分溶解羊毛,能够制备出浓度高达20%、可直接用于湿法纺丝的羊毛角蛋白溶液。在羊毛溶解过程中,利用十二烷基硫酸钠等作为表面活性剂,其亲水端-so4-2可与角蛋白分子形成氢键,与角蛋白本身结构中的氢键形成竞争关系,从而达到破坏羊毛内部的氢键作用,而疏水端则与角蛋白中油性基团形成疏水作用,瓦解角蛋白内部疏水区结构,使还原剂进一步进入羊毛内部破坏二硫键,充分溶解羊毛。而角蛋白溶解后,表面活性剂通过疏水作用与角蛋白形成胶束,充分暴露角蛋白中的亲水基团和表面活性剂的亲水端,从而大大提高角蛋白在水中的溶解度。本发明根据纺丝工艺要求,通过充分溶解废弃羊毛制得高浓度(高达20%)角蛋白溶液,可不经任何提纯处理,溶解液可全部作为纺丝液直接用于制备再生纤维,避免了传统方法中角蛋白溶液浓度低、因提纯处理所带来的原料损失、资源浪费和繁杂工艺等问题,实现了废弃羊毛的高效回收利用。而且,本发明能够减少角蛋白主链的破坏,不含尿素或溴化锂,有利于提高制得的角蛋白再生纤维力学性能。得到的角蛋白溶解液配合适量的增韧剂得到纺丝原液,纺丝后进行常规的后交联处理,即获得具有良好的强度和韧性的角蛋白再生纤维。优选地,所述蛋白质变性剂为4~10份。优选地,羊毛与水的质量比为1∶3~8.45。优选地,所述反应的温度为60~80℃,反应时间为12~24h。优选地,所述蛋白质变性剂为十二烷基硫酸钠。优选地,所述还原剂为二硫苏糖醇、巯基乙酸、硫化钠或硼氢化钠中的一种或几种。优选地,所述还原剂为二硫苏糖醇和/或巯基乙酸。优选地,所述增韧剂为聚乙烯醇、羟丙基纤维素或聚轮烷接枝聚己内酯中一种或几种。优选地,所述聚乙烯醇的分子量mw为31000~50000g/mol。优选地,所述羟丙基纤维素的取代度为60~66%。优选地,所述聚轮烷接枝聚己内酯的分子量mw为300000~400000g/mol。可选地,所述聚轮烷接枝聚己内酯中,聚己内酯的含量为75wt%。所述聚轮烷接枝聚己内酯的原料可以为分子量mw为3000g/mol的聚己内酯。所述聚轮烷接枝聚己内酯可通过市售得到。本发明还保护一种角蛋白再生纤维,所述角蛋白再生纤维由上述角蛋白纺丝原液通过湿法纺丝、再进行后交联处理得到。所述湿法纺丝的步骤为:将上述角蛋白纺丝原液脱气泡后,以氯化铵饱和溶液为凝固浴,纺丝制得初生纤维。所述后交联处理的步骤为:将所述初生纤维浸泡在戊二醛的水溶液中,交联完成后,洗涤、干燥,得到所述角蛋白再生纤维。所述后交联的温度可以为室温。所述戊二醛的水溶液的浓度可以为5%。所述后交联处理的浸泡的时间可以为1~2min。与现有技术相比,本发明的有益效果是:本发明无需使用尿素或溴化锂等试剂,能够直接制备得到符合纺丝工艺要求的高浓度角蛋白原液,可不经任何提纯处理,直接用于纺丝制备再生纤维,角蛋白纺丝原液制备方法较为简单。避免了传统方法中角蛋白溶液浓度低、因提纯处理所带来的原料损失、资源浪费和繁杂工艺等问题,实现了废弃羊毛的高效回收利用。而且本发明能够减少角蛋白主链的破坏,不含尿素或溴化锂,有利于提高制得的角蛋白再生纤维力学性能。得到的角蛋白溶解液配合适量的增韧剂得到纺丝原液,纺丝后进行常规的后交联处理,即可制备出力学性能优越(具有良好的强度和韧性)、以羊毛角蛋白为主要基体材料的再生动物蛋白纤维。附图说明图1为本发明实施例1制备的角蛋白再生纤维的sem图片。图2为本发明实施例1制备的角蛋白再生纤维的xrd谱图。具体实施方式下面结合具体实施方式对本发明作进一步的说明。实施例中的原料均可通过市售得到;实施例及对比例中,聚乙烯醇购自sigma-aldrich西格玛奥德里奇(上海)贸易有限公司型号363138,分子量mw为31000~50000g/mol,水解度98~99%;羟丙基纤维素购自上海生工生物工程有限公司a600519,取代度60~66%;聚轮烷接枝聚己内酯购自天津微瑞超分子材料科技有限公司,型号u111562g,分子量300000~400000g/mol,pcl含量为75%。除非特别说明,本发明采用的试剂、方法和设备为本
技术领域:
常规试剂、方法和设备。实施例1本实施例提供一种角蛋白纺丝原液,以及通过湿法纺丝得到的角蛋白再生纤维。该角蛋白纺丝原液的制备方法如下:在氮气保护下,将20g废弃羊毛、10g十二烷基苯磺酸钠、5g二硫苏糖醇和62.5g蒸馏水加入到带有冷凝回流装置和搅拌磁子的三口瓶中,80℃下高速搅拌回流24h。当羊毛充分溶解后,加入2.5g羟丙基纤维素,停止加热使其自然降至室温并保持充分搅拌,得到浅灰色羊毛角蛋白纺丝原液。该角蛋白再生纤维的制备方法如下:将得到的纺丝原液在1000rpm的转速下离心10min进行脱气泡处理,以氯化铵饱和溶液为凝固浴,通过湿法纺丝制得初生纤维。然后在室温下将初生纤维浸泡在5%的戊二醛水溶液中进行1~2min的后交联处理,取出交联的再生纤维并用蒸馏水洗涤干净,自然风干,得到羊毛角蛋白含量为88.9%的再生纤维。实施例2本实施例提供一种角蛋白纺丝原液,以及通过湿法纺丝得到的角蛋白再生纤维。该角蛋白纺丝原液的制备方法如下:在氮气保护下,将20g废弃羊毛、10g十六烷基硫酸钠、5g二硫苏糖醇和62.5g蒸馏水加入到带有冷凝回流装置和搅拌磁子的三口瓶中,80℃下高速搅拌回流24h。当羊毛充分溶解后,加入2.5g羟丙基纤维素,停止加热使其自然降至室温并保持充分搅拌,得到浅灰色羊毛角蛋白纺丝原液。该角蛋白再生纤维的制备方法如下:将得到的纺丝原液在1000rpm的转速下离心10min进行脱气泡处理,以氯化铵饱和溶液为凝固浴,通过湿法纺丝制得初生纤维。然后在室温下将初生纤维浸泡在5%的戊二醛水溶液中进行1~2min的后交联处理,取出交联的再生纤维并用蒸馏水洗涤干净,自然风干,得到羊毛角蛋白含量为88.9%的再生纤维。实施例3本实施例提供一种角蛋白纺丝原液,以及通过湿法纺丝得到的角蛋白再生纤维。该角蛋白纺丝原液的制备方法如下:在氮气保护下,将20g废弃羊毛、10g十二烷基硫酸钠、5g二硫苏糖醇和62.5g蒸馏水加入到带有冷凝回流装置和搅拌磁子的三口瓶中,80℃下高速搅拌回流24h。当羊毛充分溶解后,加入2.5g羟丙基纤维素,停止加热使其自然降至室温并保持充分搅拌,得到浅灰色羊毛角蛋白纺丝原液。该角蛋白再生纤维的制备方法如下:将得到的纺丝原液在1000rpm的转速下离心10min进行脱气泡处理,以氯化铵饱和溶液为凝固浴,通过湿法纺丝制得初生纤维。然后在室温下将初生纤维浸泡在5%的戊二醛水溶液中进行1~2min的后交联处理,取出交联的再生纤维并用蒸馏水洗涤干净,自然风干,得到羊毛角蛋白含量为88.9%的再生纤维。实施例4本实施例提供一种角蛋白纺丝原液,以及通过湿法纺丝得到的角蛋白再生纤维。该角蛋白纺丝原液的制备方法如下:在氮气保护下,将20g废弃羊毛、10g十二烷基硫酸钠、5g二硫苏糖醇和60g蒸馏水加入到带有冷凝回流装置和搅拌磁子的三口瓶中,80℃下高速搅拌回流24h。当羊毛充分溶解后,加入5g羟丙基纤维素,停止加热使其自然降至室温并保持充分搅拌,得到浅灰色羊毛角蛋白纺丝原液。该角蛋白再生纤维的制备方法如下:将得到的纺丝原液在1000rpm的转速下离心10min进行脱气泡处理,以氯化铵饱和溶液为凝固浴,通过湿法纺丝制得初生纤维。然后在室温下将初生纤维浸泡在5%的戊二醛水溶液中进行1~2min的后交联处理,取出交联的再生纤维并用蒸馏水洗涤干净,自然风干,得到羊毛角蛋白含量为80.0%的再生纤维。实施例5本实施例提供一种角蛋白纺丝原液,以及通过湿法纺丝得到的角蛋白再生纤维。该角蛋白纺丝原液的制备方法如下:在氮气保护下,将20g废弃羊毛、10g十二烷基硫酸钠、5g二硫苏糖醇和64g蒸馏水加入到带有冷凝回流装置和搅拌磁子的三口瓶中,80℃下高速搅拌回流24h。当羊毛充分溶解后,加入1g羟丙基纤维素,停止加热使其自然降至室温并保持充分搅拌,得到浅灰色羊毛角蛋白纺丝原液。该角蛋白再生纤维的制备方法如下:将得到的纺丝原液在1000rpm的转速下离心10min进行脱气泡处理,以氯化铵饱和溶液为凝固浴,通过湿法纺丝制得初生纤维。然后在室温下将初生纤维浸泡在5%的戊二醛水溶液中进行1~2min的后交联处理,取出交联的再生纤维并用蒸馏水洗涤干净,自然风干,得到羊毛角蛋白含量为95.2%的再生纤维。实施例6本实施例提供一种角蛋白纺丝原液,以及通过湿法纺丝得到的角蛋白再生纤维。该角蛋白纺丝原液的制备方法如下:在氮气保护下,将15g废弃羊毛、4g十二烷基硫酸钠、2g二硫苏糖醇和76.5g蒸馏水加入到带有冷凝回流装置和搅拌磁子的三口瓶中,80℃下高速搅拌回流18h。当羊毛充分溶解后,加入2.5g羟丙基纤维素,停止加热使其自然降至室温并保持充分搅拌,得到浅灰色羊毛角蛋白纺丝原液。该角蛋白再生纤维的制备方法如下:将得到的纺丝原液在1000rpm的转速下离心10min进行脱气泡处理,以氯化铵饱和溶液为凝固浴,通过湿法纺丝制得初生纤维。然后在室温下将初生纤维浸泡在5%的戊二醛水溶液中进行1~2min的后交联处理,取出交联的再生纤维并用蒸馏水洗涤干净,自然风干,得到羊毛角蛋白含量为85.7%的再生纤维。实施例7本实施例提供一种角蛋白纺丝原液,以及通过湿法纺丝得到的角蛋白再生纤维。该角蛋白纺丝原液的制备方法如下:在氮气保护下,将10g废弃羊毛、2g十二烷基硫酸钠、1g二硫苏糖醇和84.5g蒸馏水加入到带有冷凝回流装置和搅拌磁子的三口瓶中,60℃下高速搅拌回流12h。当羊毛充分溶解后,加入2.5g羟丙基纤维素,停止加热使其自然降至室温并保持充分搅拌,得到浅灰色羊毛角蛋白纺丝原液。该角蛋白再生纤维的制备方法如下:将得到的纺丝原液在1000rpm的转速下离心10min进行脱气泡处理,以氯化铵饱和溶液为凝固浴,通过湿法纺丝制得初生纤维。然后在室温下将初生纤维浸泡在5%的戊二醛水溶液中进行1~2min的后交联处理,取出交联的再生纤维并用蒸馏水洗涤干净,自然风干,得到羊毛角蛋白含量为80.0%的再生纤维。实施例8本实施例提供一种角蛋白纺丝原液,以及通过湿法纺丝得到的角蛋白再生纤维。该角蛋白纺丝原液的制备方法如下:在氮气保护下,将20g废弃羊毛、10g十二烷基硫酸钠、5g巯基乙酸和62.5g蒸馏水加入到带有冷凝回流装置和搅拌磁子的三口瓶中,80℃下高速搅拌回流24h。当羊毛充分溶解后,加入2.5g羟丙基纤维素,停止加热使其自然降至室温并保持充分搅拌,得到浅灰色羊毛角蛋白纺丝原液。该角蛋白再生纤维的制备方法如下:将得到的纺丝原液在1000rpm的转速下离心10min进行脱气泡处理,以氯化铵饱和溶液为凝固浴,通过湿法纺丝制得初生纤维。然后在室温下将初生纤维浸泡在5%的戊二醛水溶液中进行1~2min的后交联处理,取出交联的再生纤维并用蒸馏水洗涤干净,自然风干,得到羊毛角蛋白含量为88.9%的再生纤维。实施例9本实施例提供一种角蛋白纺丝原液,以及通过湿法纺丝得到的角蛋白再生纤维。该角蛋白纺丝原液的制备方法如下:在氮气保护下,将20g废弃羊毛、10g十二烷基硫酸钠、5g硫化钠和62.5g蒸馏水加入到带有冷凝回流装置和搅拌磁子的三口瓶中,80℃下高速搅拌回流24h。当羊毛充分溶解后,加入2.5g羟丙基纤维素,停止加热使其自然降至室温并保持充分搅拌,得到浅灰色羊毛角蛋白纺丝原液。该角蛋白再生纤维的制备方法如下:将得到的纺丝原液在1000rpm的转速下离心10min进行脱气泡处理,以氯化铵饱和溶液为凝固浴,通过湿法纺丝制得初生纤维。然后在室温下将初生纤维浸泡在5%的戊二醛水溶液中进行1~2min的后交联处理,取出交联的再生纤维并用蒸馏水洗涤干净,自然风干,得到羊毛角蛋白含量为88.9%的再生纤维。实施例10本实施例提供一种角蛋白纺丝原液,以及通过湿法纺丝得到的角蛋白再生纤维。该角蛋白纺丝原液的制备方法如下:在氮气保护下,将20g废弃羊毛、10g十二烷基硫酸钠、5g硼氢化钠和62.5g蒸馏水加入到带有冷凝回流装置和搅拌磁子的三口瓶中,80℃下高速搅拌回流24h。当羊毛充分溶解后,加入2.5g羟丙基纤维素,停止加热使其自然降至室温并保持充分搅拌,得到浅灰色羊毛角蛋白纺丝原液。该角蛋白再生纤维的制备方法如下:将得到的纺丝原液在1000rpm的转速下离心10min进行脱气泡处理,以氯化铵饱和溶液为凝固浴,通过湿法纺丝制得初生纤维。然后在室温下将初生纤维浸泡在5%的戊二醛水溶液中进行1~2min的后交联处理,取出交联的再生纤维并用蒸馏水洗涤干净,自然风干,得到羊毛角蛋白含量为88.9%的再生纤维。实施例11本实施例提供一种角蛋白纺丝原液,以及通过湿法纺丝得到的角蛋白再生纤维。该角蛋白纺丝原液的制备方法如下:在氮气保护下,将20g废弃羊毛、10g十二烷基硫酸钠、5g二硫苏糖醇和60g蒸馏水加入到带有冷凝回流装置和搅拌磁子的三口瓶中,80℃下高速搅拌回流24h。当羊毛充分溶解后,加入5g聚乙烯醇,停止加热使其自然降至室温并保持充分搅拌,得到浅灰色羊毛角蛋白纺丝原液。该角蛋白再生纤维的制备方法如下:将得到的纺丝原液在1000rpm的转速下离心10min进行脱气泡处理,以氯化铵饱和溶液为凝固浴,通过湿法纺丝制得初生纤维。然后在室温下将初生纤维浸泡在5%的戊二醛水溶液中进行1~2min的后交联处理,取出交联的再生纤维并用蒸馏水洗涤干净,自然风干,得到羊毛角蛋白含量为80.0%的再生纤维。实施例12本实施例提供一种角蛋白纺丝原液,以及通过湿法纺丝得到的角蛋白再生纤维。该角蛋白纺丝原液的制备方法如下:在氮气保护下,将20g废弃羊毛、10g十二烷基硫酸钠、5g二硫苏糖醇和60g蒸馏水加入到带有冷凝回流装置和搅拌磁子的三口瓶中,80℃下高速搅拌回流24h。当羊毛充分溶解后,加入5g聚轮烷接枝聚己内酯,停止加热使其自然降至室温并保持充分搅拌,得到浅灰色羊毛角蛋白纺丝原液。该角蛋白再生纤维的制备方法如下:将得到的纺丝原液在1000rpm的转速下离心10min进行脱气泡处理,以氯化铵饱和溶液为凝固浴,通过湿法纺丝制得初生纤维。然后在室温下将初生纤维浸泡在5%的戊二醛水溶液中进行1min的后交联处理,取出交联的再生纤维并用蒸馏水洗涤干净,自然风干,得到羊毛角蛋白含量为80.0%的再生纤维。对比例1本对比例提供一种角蛋白纺丝原液,以及通过湿法纺丝得到的角蛋白再生纤维。该角蛋白纺丝原液的制备方法如下:在氮气保护下,将20g废弃羊毛、29g尿素、2g十二烷基硫酸钠、5g二硫苏糖醇和41.5g蒸馏水加入到带有冷凝回流装置和搅拌磁子的三口瓶中,80℃下高速搅拌回流24h。当羊毛充分溶解后,加入2.5g羟丙基纤维素,停止加热使其自然降至室温并保持充分搅拌,得到浅灰色溶解不充分糊状羊毛角蛋白纺丝原液。该角蛋白再生纤维的制备方法如下:将得到的纺丝原液在1000rpm的转速下离心10min进行脱气泡处理,以氯化铵饱和溶液为凝固浴,通过湿法纺丝制得初生纤维。然后在室温下将初生纤维浸泡在5%的戊二醛水溶液中进行1~2min的后交联处理,取出交联的再生纤维并用蒸馏水洗涤干净,自然风干,得到羊毛角蛋白含量为88.9%的再生纤维。对比例2本对比例提供一种角蛋白纺丝原液,以及通过湿法纺丝得到的角蛋白再生纤维。该角蛋白纺丝原液的制备方法如下:在氮气保护下,将20g废弃羊毛、35g溴化锂、2g十二烷基硫酸钠、5g二硫苏糖醇和35.5g蒸馏水加入到带有冷凝回流装置和搅拌磁子的三口瓶中,80℃下高速搅拌回流24h。当羊毛充分溶解后,加入2.5g羟丙基纤维素,停止加热使其自然降至室温并保持充分搅拌,得到浅灰色溶解不充分糊状羊毛角蛋白纺丝原液。该角蛋白再生纤维的制备方法如下:将得到的纺丝原液在1000rpm的转速下离心10min进行脱气泡处理,以氯化铵饱和溶液为凝固浴,通过湿法纺丝制得初生纤维。然后在室温下将初生纤维浸泡在5%的戊二醛水溶液中进行1~2min的后交联处理,取出交联的再生纤维并用蒸馏水洗涤干净,自然风干,得到羊毛角蛋白含量为88.9%再生纤维。对比例3本对比例提供一种角蛋白纺丝原液,以及通过湿法纺丝得到的角蛋白再生纤维。该角蛋白纺丝原液的制备方法如下:在氮气保护下,将20g废弃羊毛、10g十二烷基硫酸钠、5g二硫苏糖醇和65g蒸馏水加入到带有冷凝回流装置和搅拌磁子的三口瓶中,80℃下高速搅拌回流24h。当羊毛充分溶解后,停止加热使其自然降至室温并保持充分搅拌,得到浅灰色羊毛角蛋白纺丝原液。该角蛋白再生纤维的制备方法如下:将得到的纺丝原液在1000rpm的转速下离心10min进行脱气泡处理,以氯化铵饱和溶液为凝固浴,通过湿法纺丝制得初生纤维。然后在室温下将初生纤维浸泡在5%的戊二醛水溶液中进行1~2min的后交联处理,取出交联的再生纤维并用蒸馏水洗涤干净,自然风干,得到羊毛角蛋白含量为100%的再生纤维。对比例4本对比例提供一种角蛋白纺丝原液,以及通过湿法纺丝得到的角蛋白再生纤维。该角蛋白纺丝原液的制备方法如下:在氮气保护下,将20g废弃羊毛、10g十二烷基硫酸钠、5g二硫苏糖醇和62.5g蒸馏水加入到带有冷凝回流装置和搅拌磁子的三口瓶中,80℃下高速搅拌回流24h。当羊毛充分溶解后,加入2.5g羟丙基纤维素,停止加热使其自然降至室温并保持充分搅拌,得到浅灰色羊毛角蛋白纺丝原液。该角蛋白再生纤维的制备方法如下:将得到的纺丝原液在1000rpm的转速下离心10min进行脱气泡处理,以氯化铵饱和溶液为凝固浴,通过湿法纺丝制得初生纤维。然后将初生纤维用蒸馏水洗涤干净,自然风干,得到羊毛角蛋白含量为88.9%的再生纤维。对比例5本对比例提供一种角蛋白纺丝原液,以及通过湿法纺丝得到的角蛋白再生纤维。该角蛋白纺丝原液的制备方法如下:在氮气保护下,将10g废弃羊毛、36.25g尿素、2.5g二硫苏糖醇和50g蒸馏水加入到带有冷凝回流装置和搅拌磁子的三口瓶中,80℃下高速搅拌回流24h。当羊毛充分溶解后,加入1.25g羟丙基纤维素,停止加热使其自然降至室温并保持充分搅拌,得到浅灰色羊毛角蛋白纺丝原液。该角蛋白再生纤维的制备方法如下:将得到的纺丝原液在1000rpm的转速下离心10min进行脱气泡处理,以氯化铵饱和溶液为凝固浴,通过湿法纺丝制得初生纤维。然后在室温下将初生纤维浸泡在5%的戊二醛水溶液中进行1~2min的后交联处理,取出交联的再生纤维并用蒸馏水洗涤干净,自然风干,得到羊毛角蛋白含量为88.9%的再生纤维。测试方法力学性能测试:使用标准iso11566,间距为25mm,拉伸速率为5mm.min-1。每个样品测量平行测试50个根试样;测试得到拉伸强度和断裂伸长率。形貌测试:sem形貌表征使用hitachi型号s-4800,纤维表面喷镀铂金,加速电压为10kv。xrd测试:xrd测试由d8advancex-射线衍射仪进行测试(waxr,cukαradiation,λ=0.154nm,扫描范围=5-80°,扫描速度10°min-1,brukercorporation,genrmany)。测试结果本申请可根据纺丝工艺要求,在中性的条件下制备湿法纺丝所需要浓度和粘度的角蛋白溶液,从而无需纯化而直接用于纺丝。实施例1~12制备得到的角蛋白纺丝原液中角蛋白浓度高,其中实施例1~5和8~12的浓度高达20%。将实施例1~12的角蛋白纺丝原液通过纺丝,结合简单的后交联处理工艺,制备出力学性能优越、以羊毛角蛋白为主要基体材料(角蛋白含量大于88.9%)的再生动物蛋白纤维,纺丝和后处理工艺简单,操作简便。如表1所示,本申请实施例1~12制得的角蛋白再生纤维的拉伸强度均高于7cn/tex,断裂伸长率均高于20%,具有良好的力学性能。而现有技术中,一般纯角蛋白溶液的可纺性差,得到的再生材料力学性能低,使得羊毛角蛋白通常只能作为再生材料的次要组分。形貌测试结果:如图1所示,实施例1得到表面光滑,直径约为30微米的纤维长丝。xrd测试结果:图2中,9°代表α螺旋结构,20°代表β折叠,与原始羊毛相比,实施例1得到的再生纤维的α螺旋减少,β折叠有所增加。对比例1和对比例2为传统方法,需要采用高浓度的尿素、溴化锂等试剂,以破坏羊毛角蛋白分子间存在的大量氢键,还需要调节ph值为碱性,并加入少量的十二烷基硫酸钠与角蛋白形成胶束,才能制备出稳定的角蛋白溶液。溶液反应需要在高温条件下进行,碱性环境和高浓度的尿素或溴化锂都会在一定程度上破坏角蛋白主链,降低角蛋白分子量。此外,高浓度的尿素和溴化锂会直接影响再生纤维的凝固过程,降低再生纤维的力学性能。如表1所示,对比例1和对比例2的拉伸强度均不足。对比例3经过了后交联处理但没有使用增韧剂,虽然所得再生纤维的力学强度比较高,但是其韧性比较差。对比例4使用了增韧剂但没有交联,再生纤维的韧性有一定的改善,但是其力学强度很差,不能满足实用要求。对比例5在羊毛溶解过程中没有使用十二烷基硫酸钠等表面活性剂,则需要使用大量的尿素或溴化锂破坏氢键,尽管如此,依然不能得到高浓度充分溶解的角蛋白溶液,并且由于高浓度的尿素或溴化锂对再生纤维凝固过程的影响,降低了所制备的再生纤维的力学强度和韧性。表1实施例1~12及对比例1~5制得的角蛋白再生纤维的力学性能样品拉伸强度(cn/tex)断裂伸长率(%)实施例18.6841.09实施例28.5243.05实施例39.4439.72实施例47.0668.19实施例510.9822.72实施例67.6656.24实施例77.1863.02实施例88.5642.28实施例98.3435.42实施例108.2937.84实施例1110.8522.32实施例127.0264.54对比例14.7424.24对比例24.9830.74对比例312.554.40对比例40.5722.65对比例54.858.71显然,本发明的上述实施例仅仅是为清楚地说明本发明所作的举例,而并非是对本发明的实施方式的限定。对于所属领域的普通技术人员来说,在上述说明的基础上还可以做出其它不同形式的变化或变动。这里无需也无法对所有的实施方式予以穷举。凡在本发明的精神和原则之内所作的任何修改、等同替换和改进等,均应包含在本发明权利要求的保护范围之内。当前第1页12