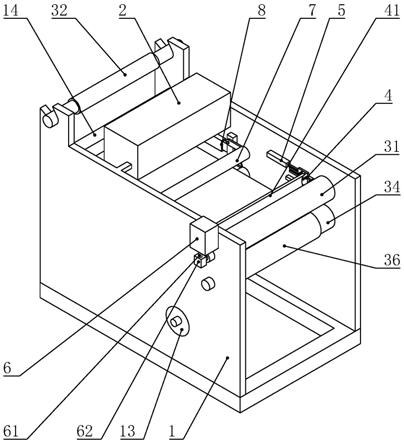
[0001]
本发明涉及印刷工艺领域,更具体地说,它涉及一种镭射印刷工艺。
背景技术:[0002]
印刷是将原稿经各种工序用油墨转移到纸张、纺织品、塑料品、皮革、pvc、pc等材料表面上,进行批量复制的技术。在进行印刷时,需要将油墨先附着在某一承印物上,先在该承印物上绘制图案或文字,再将图案转印到印刷物上,印刷物如纸张、纸板、塑料纸等,承印物如滚筒等。在镭射印刷的过程中,由于镭射膜作为印刷物,油墨组成的图案难以附着在镭射膜上,导致印刷的图案容易重影模糊。
技术实现要素:[0003]
针对现有技术存在的不足,本发明的目的在于提供一种镭射印刷工艺,该工艺使得图案清晰地印刷在镭射膜上。
[0004]
为实现上述目的,本发明提供了如下技术方案:镭射印刷工艺,
[0005]
s1、放卷,将带有转印膜的卷筒安装在机架上;
[0006]
s2、印刷,印刷装置用油墨将需要印刷的图案绘制到转印膜上;
[0007]
s3、加热,电磁加热装置将转印膜加热,以间接加热油墨;
[0008]
s4、放纸,附着有镭射膜的纸张依次放置在输送带上;
[0009]
s5、压合,压合装置将转印膜与纸张压合,使转印膜上的图案转印到镭射膜上;
[0010]
其中压合装置安装在机架上,压合装置包括有第一压合辊、第二压合辊和驱动装置,第一压合辊用于引导转印膜,第二压合辊设置在输送带的内侧,当使用时,驱动装置带动第一压合辊和第二压合辊相向移动,第一压合辊将转印膜压在输送带上,第二压合辊支撑输送带,以使图案转印到镭射膜上。
[0011]
本发明进一步设置为:驱动装置包括有压合架和压合杆,压合架和压合杆均固定连接在机架上,压合架上设置有导向孔,并转动连接有上连接板和下连接板,第一压合辊转动连接在上连接板上第二压合辊转动连接在下连接板上,压合杆上设置有伸缩杆,伸缩杆穿过导向孔,并转动连接有第一驱动板和第二驱动板,第一驱动板转动连接在上连接板上,第二驱动板的一端转动连接在下连接板上,当使用时,压合杆带动伸缩杆回移,使第一驱动板和第二驱动板分别带动上连接板和下连接板相向转动,以带动第一压合辊和第二压合辊相向移动。
[0012]
本发明进一步设置为:电磁加热装置包括有电磁罩和用于引导转印膜的第一输送辊,第一输送辊转动连接在机架上,第一输送辊内设置有容纳流动介质的加热腔,电磁罩用于发出电磁场,以加热该流动介质,从而将第一输送辊加热,并间接加热转印膜,机架上安装有调节装置,并转动连接有第二输送辊,卷筒套设在第二输送辊上,电磁罩安装在调节装置上,调节装置带动电磁罩移动,以调节电磁罩与第一输送辊之间的间距。
[0013]
本发明进一步设置为:调节装置包括有滑块、第一驱动杆和第二驱动杆,机架上还
安装有滑轨,滑轨沿长度方向设置有滑槽,滑块与滑槽滑动连接,第一驱动杆安装在机架上,并且其伸缩端连接在滑块上,以使滑块沿滑槽移动,电磁罩的一端转动连接在滑块上,第二驱动杆安装在滑块上,第二驱动杆的伸缩端转动连接在电磁罩上,以带动电磁罩转动,滑块上设置有两个限位块,两个限位块分别设置在电磁罩的两侧上,机架上还安装有传感器,传感器用于感应电磁罩的位置和角度,并分别与第一驱动杆和第二驱动杆电连接,以控制第一驱动杆和第二驱动杆。
[0014]
本发明进一步设置为:第一输送辊上安装有过压保护装置,过压保护装置包括有排气管,排气管的下端连接有转动接头,转动接头与第一输送辊转动连接,以使排气管和加热腔相连通。
[0015]
本发明进一步设置为:排气管的上端连接有冷凝器,冷凝器内设置有多个冷凝板,冷凝器的下端连接有导液管,导液管与排气管相连,并设置有止回阀。
[0016]
本发明进一步设置为:冷凝器连接有干燥器,干燥器内设置有用于吸收介质的干燥剂。
[0017]
本发明进一步设置为:干燥器上安装有排气阀,排气阀上设置有排气口,并转动连接有压杆,排气口滑动连接有阀芯,并安装有调节座,阀芯设置有滑孔,压杆穿过滑孔,并连接有配重,调节座上设置有用于供阀芯插入的限位槽,并螺纹连接有调节杆,限位槽内设置有弹簧,弹簧的下端连接在阀芯上,弹簧的上端连接有调节块,调节杆的下端伸入限位槽内,并与调节块转动连接。
[0018]
本发明进一步设置为:机架上还转动连接有第三输送辊和第四输送辊,输送带套设在第三输送辊和第四输送辊上,输送带设置在第一输送辊的下方。
[0019]
本发明进一步设置为:机架上还安装有用于带动第一输送辊和第三输送辊转动的伺服电机和多个用于引导转印膜的导引辊,伺服电机分别与第一输送辊和第三输送辊链连接或带连接,以带动转印膜和输送带同步转动。
[0020]
综上所述,本发明具有以下有益效果:驱动装置带动第一压合辊和第二压合辊相向移动,第一压合辊和第二压合辊分别从两侧挤压转印膜和输送带,将转印膜贴合在输送带上,通过双面挤压的方式,使得转印膜和输送带上的纸张贴合紧密,确保将转印膜上的图案完整地转印到纸张上附着的镭射膜上,从而保证印刷效果。并且通过电磁加热装置加热转印膜上的油墨,从而降低油墨中的含水量,使得油墨不易掉落,并且图案不易变形,便于通过压合固定在纸张上,使得转印到镭射膜上的图案清晰。而且电磁加热装置升温快,有利于提高生产效率。
附图说明
[0021]
图1为印刷装置的立体结构示意图;
[0022]
图2为机架的连接结构示意图;
[0023]
图3为双辊压合装置的立体结构示意图;
[0024]
图4为调节装置的立体结构示意图;
[0025]
图5为过压保护装置的立体结构示意图;
[0026]
图6为图5的a放大图。
具体实施方式
[0027]
下面结合附图和实施例,对本发明进一步详细说明。其中相同的零部件用相同的附图标记表示。需要说明的是,下面描述中使用的词语“前”、“后”、“左”、“右”、“上”和“下”指的是附图中的方向,词语“底面”和“顶面”、“内”和“外”分别指的是朝向或远离特定部件几何中心的方向。
[0028]
参照图1-6所示,镭射印刷工艺,
[0029]
s1、放卷,将带有转印膜的卷筒安装在机架1上;
[0030]
s2、印刷,印刷装置2用油墨将需要印刷的图案绘制到转印膜上;
[0031]
s3、加热,电磁加热装置4将转印膜加热,以间接加热油墨;
[0032]
s4、放纸,附着有镭射膜的纸张依次放置在输送带36上;
[0033]
s5、压合,压合装置7将转印膜与纸张压合,使转印膜上的图案转印到镭射膜上;
[0034]
其中压合装置7安装在机架1上,压合装置7包括有第一压合辊71、第二压合辊72和驱动装置8,第一压合辊71用于引导转印膜,第二压合辊72设置在输送带36的内侧,当使用时,驱动装置8带动第一压合辊71和第二压合辊72相向移动,第一压合辊71将转印膜压在输送带36上,第二压合辊72支撑输送带36,以使图案转印到镭射膜上。
[0035]
通过上述方案,驱动装置8带动第一压合辊71和第二压合辊72相向移动,第一压合辊71和第二压合辊72分别从两侧挤压转印膜和输送带36,将转印膜贴合在输送带36上,通过双面挤压的方式,使得转印膜和输送带36上的纸张贴合紧密,确保将转印膜上的图案完整地转印到纸张上附着的镭射膜上,从而保证印刷效果。并且通过电磁加热装置4加热转印膜上的油墨,从而降低油墨中的含水量,使得油墨不易掉落,并且图案不易变形,便于通过压合固定在纸张上,使得转印到镭射膜上的图案清晰。而且电磁加热装置4升温快,有利于提高生产效率。
[0036]
作为改进的一种具体实施方式,驱动装置8包括有压合架81和压合杆82,压合架81和压合杆82均固定连接在机架1上,压合架81上设置有导向孔811,并转动连接有上连接板83和下连接板84,第一压合辊71转动连接在上连接板83上第二压合辊72转动连接在下连接板84上,压合杆82上设置有伸缩杆821,伸缩杆821穿过导向孔811,并转动连接有第一驱动板85和第二驱动板86,第一驱动板85转动连接在上连接板83上,第二驱动板86的一端转动连接在下连接板84上,当使用时,压合杆82带动伸缩杆821回移,使第一驱动板85和第二驱动板86分别带动上连接板83和下连接板84相向转动,以带动第一压合辊71和第二压合辊72相向移动。
[0037]
通过上述方案,压合杆82带动伸缩杆821回移,导向孔811引导伸缩杆821平稳移动,使第一驱动板85和第二驱动板86分别带动上连接板83和下连接板84相向转动,以带动第一压合辊71和第二压合辊72相向移动,第一压合辊71和第二压合辊72分别从两侧同时挤压转印膜和输送带36,通过挤压使得转印膜和纸张贴合紧密,确保将转印膜上的图案完整地转印到镭射膜上。
[0038]
作为改进的一种具体实施方式,电磁加热装置4包括有电磁罩41和用于引导转印膜的第一输送辊31,第一输送辊31转动连接在机架1上,第一输送辊31内设置有容纳流动介质的加热腔311,电磁罩41用于发出电磁场,以加热该流动介质,从而将第一输送辊31加热,并间接加热转印膜,机架1上安装有调节装置5,并转动连接有第二输送辊32,卷筒套设在第
二输送辊32上,电磁罩41安装在调节装置5上,调节装置5带动电磁罩41移动,以调节电磁罩41与第一输送辊31之间的间距。
[0039]
通过上述方案,电磁罩41发出电磁场将第一输送辊31内的流动介质快速加热,从而通过流动介质将金属制成的第一输送辊31快速加热,以间接加热转印膜,使得热量均匀散热,通过均匀加热转印膜上的油墨,从而降低油墨的含水量,使得图案不易变形,并且便于在加热后通过压合固定在纸张上,使得在图案清晰地转印到纸张上,转印后由于散热将油墨中的水分快速蒸发,保证图案清晰。通过调节装置5带动电磁罩41移动,以调节电磁罩41与第一输送辊31之间的间距,从而调节加热的温度和温度升降的速度,保证均匀加热或快速升降温,以获得更好地加热效果。当需要清洁第一输送辊31时,能够将电磁罩41移开,也便于清理维护。
[0040]
作为改进的一种具体实施方式,调节装置5包括有滑块51、第一驱动杆52和第二驱动杆53,机架1上还安装有滑轨11,滑轨11沿长度方向设置有滑槽111,滑块51与滑槽111滑动连接,第一驱动杆52安装在机架1上,并且其伸缩端连接在滑块51上,以使滑块51沿滑槽111移动,电磁罩41的一端转动连接在滑块51上,第二驱动杆53安装在滑块51上,第二驱动杆53的伸缩端转动连接在电磁罩41上,以带动电磁罩41转动,滑块51上设置有两个限位块511,两个限位块511分别设置在电磁罩41的两侧上,机架1上还安装有传感器12,传感器12用于感应电磁罩41的位置和角度,并分别与第一驱动杆52和第二驱动杆53电连接,以控制第一驱动杆52和第二驱动杆53。
[0041]
通过上述方案,滑轨11水平设置,第一驱动杆52推动滑块51沿滑槽111水平移动,第二驱动杆53带动电磁罩41绕转动连接处转动,两个限位块511使得电磁罩41在一定角度内转动,并且通过传感器12控制第一驱动杆52和第二驱动杆53,避免电磁罩41与第一输送辊31碰撞,保护各个零部件,避免损坏。并且通过传感器12控制电磁罩41的位置和角度,从而达到控制加热效果的作用。
[0042]
作为改进的一种具体实施方式,第一输送辊31上安装有过压保护装置6,过压保护装置6包括有排气管61,排气管61的下端连接有转动接头62,转动接头62与第一输送辊31转动连接,以使排气管61和加热腔311相连通。
[0043]
通过上述方案,排气管61将加热腔311内由于升温导致膨胀的空气排出。转动接头62将转动的第一输送辊31与固定的排气管61连接,并且避免气体泄漏。
[0044]
作为改进的一种具体实施方式,排气管61的上端连接有冷凝器63,冷凝器63内设置有多个冷凝板631,冷凝器63的下端连接有导液管632,导液管632与排气管61相连,并设置有止回阀633。
[0045]
通过上述方案,冷凝器63将过热的空气中的液体在冷凝板631冷凝,液体汇集在冷凝器63的下端,并通过导液管632送入排气管61,以回流到加热腔311内,从而起到回收的作用,回收循环能充分利用资源,有利于降低生产成本,并且能够长时间生产,减少维护。止回阀633避免液体逆流,也避免液体堆积。
[0046]
作为改进的一种具体实施方式,冷凝器63连接有干燥器64,干燥器64内设置有用于吸收介质的干燥剂。
[0047]
通过上述方案,干燥器6干燥剂4将排出的空气中气化的介质吸收,避免污染空气,生产更为环保。
[0048]
作为改进的一种具体实施方式,干燥器64上安装有排气阀65,排气阀65上设置有排气口651,并转动连接有压杆652,排气口651滑动连接有阀芯653,并安装有调节座66,阀芯653设置有滑孔655,压杆652穿过滑孔655,并连接有配重654,调节座66上设置有用于供阀芯653插入的限位槽661,并螺纹连接有调节杆662,限位槽661内设置有弹簧663,弹簧663的下端连接在阀芯653上,弹簧663的上端连接有调节块664,调节杆662的下端伸入限位槽661内,并与调节块664转动连接。
[0049]
通过上述方案,配重654设置在压杆652上,下压阀芯653,使得阀芯653将排气口651封闭,从而使得干燥器64以及与其相通的冷凝器63和加热腔311的内部形成高压,以便于提高沸点,从而使得流动介质能够更高效地被使用。还可以通过转动调节杆662,调节弹簧下压阀芯653的力,微调气压,并且通过重新配置配重654,改变内部的气压。
[0050]
作为改进的一种具体实施方式,机架1上还转动连接有第三输送辊34和第四输送辊35,输送带36套设在第三输送辊34和第四输送辊35上,输送带36设置在第一输送辊31的下方。
[0051]
通过上述方案,第三输送辊34和第四输送辊35支撑输送带36,使得输送带36展平,便于平稳输送纸张。印刷装置2、第一输送辊31和输送带36从上到下依次设置,便于缩短生产线。
[0052]
作为改进的一种具体实施方式,机架1上还安装有用于带动第一输送辊31和第三输送辊34转动的伺服电机13和多个用于引导转印膜的导引辊14,伺服电机13分别与第一输送辊31和第三输送辊34链连接或带连接,以带动转印膜和输送带36同步转动。
[0053]
通过上述方案,伺服电机13便于控制第一输送辊31和输送带36的转速,并且同步转动有利于准确地将图案转印到镭射膜上。
[0054]
以上所述仅是本发明的优选实施方式,本发明的保护范围并不仅局限于上述实施例,凡属于本发明思路下的技术方案均属于本发明的保护范围。应当指出,对于本技术领域的普通技术人员来说,在不脱离本发明原理前提下的若干改进和润饰,这些改进和润饰也应视为本发明的保护范围。